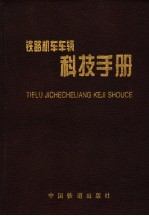
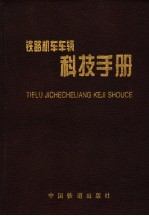
铁路机车车辆科技手册 第3卷 制造技术PDF电子书下载
- 电子书积分:21 积分如何计算积分?
- 作 者:张庆林主编;铁路机车车辆科技手册编委会编
- 出 版 社:北京:中国铁道出版社
- 出版年份:2002
- ISBN:7113047343
- 页数:778 页
第一章 铁路机车车辆制造技术概况 1
第一节 铁路机车车辆制造技术体系的形成和发展 2
产品制造技术的起步 2
体系的形成 3
发展阶段 4
技术创新阶段 5
第二节 铁路机车车辆制造技术展望 8
新型机车车辆的几项关键技术 8
机械制造技术的进展和发展趋势 8
机车车辆制造技术展望 10
新型机车车辆关键制造技术的研究与开发 11
第二章 企业工艺管理和产品工艺过程设计 13
第一节 企业工艺管理工作 13
机械制造工艺的基本概念 13
企业工艺管理的主要内容 14
第二节 产品工艺过程设计 16
产品结构工艺性审查 16
工艺方案设计 17
工艺技术选择 18
工艺路线设计与优化 18
工艺规程的设计 20
工艺定额的制订 21
工艺装备(专用设备)设计 22
第三节 产品工艺方案的技术经济分析 23
工艺方案技术经济分析的意义 23
工艺方案的技术分析 23
工艺方案的经济分析 24
第四节 工艺发展规划 25
工艺发展规划的主要功能 26
工艺发展规划的类型 26
编制工艺发展规划的基本原则 26
工艺发展规划的主要内容 27
工艺发展规划的管理和实施 28
第一章 概论 31
第一节 国内外铸造技术现状和发展趋势 31
金属熔炼 31
造型和制芯 32
砂处理 36
特种铸造 36
铸造技术的发展趋势 36
第二节 机车车辆工业铸造技术的发展 37
机车车辆工业铸造技术的发展概况 37
机车车辆工业铸造技术的发展方向 39
满足重载提速要求的新措施 41
第二章 铸造技术 42
第一节 熔炼 42
铸铁的熔炼 42
铸钢的熔炼 47
有色金属的熔炼 54
第二节 造型材料 60
原砂 60
粘结剂 61
附加物及辅助材料 63
型砂和芯砂 64
第三节 造型与制芯 66
铸型的分类 66
砂型铸造 66
第四节 落砂与清理 70
落砂 70
清理 71
第五节 旧砂再生 71
水玻璃砂的旧砂再生 71
树脂砂的旧砂再生 74
第六节 特种铸造 76
熔模铸造 76
金属型铸造 77
低压铸造 78
壳型铸造 79
压力铸造 80
陶瓷型铸造 80
离心铸造 82
消失模铸造 82
第三章 机车车辆产品典型零件铸造工艺 84
第一节 铸铁件铸造工艺 84
机车柴油机曲轴铸造 84
机车柴油机机体铸造 86
机车柴油机气缸盖铸造 88
机车柴油机活塞铸造 89
第二节 铸钢件铸造工艺 90
侧架铸造 90
摇枕铸造 91
车钩铸造 93
客车转向架构架铸造 94
整体铸钢车轮铸造 95
第四章 先进铸造技术在机车车辆产品制造中的应用 98
第一节 气冲造型生产线 98
造型线和砂处理 98
型砂 99
制芯系统 99
浇注系统与浇注 99
捅箱 99
第二节 迪砂造型生产线 99
造型机型号和规格 100
造型线组成 100
真空造型原理 100
造型 100
铸型输送系统 101
主要配套设备 101
造型线的特点 102
经济效益分析 102
第三节 树脂砂造型生产线 102
简介 102
树脂砂无箱造型生产线 103
树脂砂造型铸造柴油机机体 103
树脂砂造型铸造电力机车铸钢件 104
树脂砂造型铸造摇枕和侧架铸钢件 104
第四节 电渣熔铸柴油机曲轴 106
卧式分段熔铸法 106
立式一次成形法 106
第五节 ZN290型增压器轴承挤压铸造 107
挤压铸造工艺特点 107
挤压铸造工艺过程 108
附表2-1 机车车辆典型零件铸造工艺 110
附表2-2 先进铸造技术应用项目 110
附表2-3 铸造工艺主要设备 111
第一章 概论 113
第一节 焊接与切割原理及分类 113
简介 113
原理、分类及适用范围 113
第二节 机车车辆工业焊接与切割技术概况 114
机车车辆工业焊接与切割技术的现状 114
机车车辆工业焊接与切割技术的发展 115
第三节 焊接应力与变形 115
焊接应力与变形产生的原因 115
减少与消除焊接应力的措施 115
防止和矫正焊接变形的措施 117
消除机车转向架构架焊接应力的方法 121
第二章 焊接与切割工艺及装备 122
第一节 手工电弧焊 122
焊接接头和坡口形式 122
手工电弧焊设备及工具 123
焊条 124
焊接参数 126
第二节 熔化极气体保护焊 126
熔化极气体保护焊分类 127
保护气体 129
焊丝 130
工艺参数 131
第三节 埋弧焊 134
埋弧焊的技术特点 134
埋弧焊设备 134
埋弧焊焊丝与焊剂 135
埋弧焊焊接工艺 136
第四节 摩擦焊 138
摩擦焊的主要特点 138
摩擦焊机 139
摩擦焊工艺 139
第五节 电阻焊 141
电阻焊的特点 141
电阻焊设备 141
点焊和缝焊工艺参数选择 142
第六节 钎焊 143
钎焊方法 143
钎焊生产工艺 144
第七节 切割工艺及设备 144
氧乙炔切割 144
等离子弧切割 145
水下等离子弧切割 146
激光切割 148
第三章 机车车辆零部件焊接工艺 150
第一节 概述 150
第二节 机车零部件焊接工艺 150
内燃机车底架焊接工艺 150
东风5型内燃机车底架中梁焊接工艺 153
机车转向架构架焊接工艺 154
第三节 客车零部件焊接工艺 155
25型客车车体钢结构组焊工艺 155
铝合金车体制造技术 158
不锈钢客车车体焊接工艺 165
客车转向架(SW-160型)焊接工艺 166
第四节 货车零部件焊接工艺 169
货车底架组焊工艺 169
罐车罐体焊接工艺 173
货车转向架构架焊接工艺 175
棚车车顶钢结构焊接工艺 178
第五节 焊接设备与工装 180
客车铝合金车体自动焊接设备 180
MIG/MAG/CO2高性能多用途焊机 181
焊接烟尘净化器 181
装配—焊接夹具 181
车体钢结构焊接夹具通用化 183
附表3-1 焊接与切割工艺主要设备 187
第一章 概论 189
第一节 国内外锻压技术现状与发展趋势 189
国外锻压技术现状与发展趋势 189
国内锻压技术的发展 191
第二节 机车车辆工业锻压技术 191
机车车辆锻压技术的现状 191
机车车辆产品发展对锻压技术的要求 193
第二章 锻造 194
第一节 自由锻造 194
锤上自由锻 194
液压机上自由锻 194
变形程度对锻件的影响 195
锻造温度的控制 195
锻件的锻后冷却和热处理 195
第二节 模锻 197
锤上模锻 197
摩擦压力机上模锻 198
热模锻压力机上模锻 199
平锻机上模锻 199
第三章 冲压 202
第一节 冲压加工的工序 202
分离工序 202
变形工序 202
第二节 冲压加工 203
冲裁 203
弯曲 208
拉延 213
冲压工艺方案分析 216
冷挤压 220
第四章 锻压技术在机车车辆产品制造中的应用 225
第一节 全纤维曲轴锻造 225
全纤维曲轴锻造的特点 225
16V240ZJ型柴油机曲轴锻造 226
曲轴锻件毛坯尺寸的确定 226
设备 227
第二节 连杆锻造 228
技术条件 228
锻造工艺 228
设备 228
第三节 车轴锻造 230
简介 230
锻造工艺 230
设备 230
第四节 制动缸缸体的强力旋压加工 231
简介 231
毛坯制备 231
旋压工艺 231
设备 232
第五节 弹簧锻造 233
工艺 233
设备 233
第六节 机械压力机精锻 233
机械压力机精锻设备的特点 233
机械压力机精锻工艺的特点 234
精密锻造在机车车辆产品制造中的应用 234
第七节 离合器式螺旋压力机锻造 235
离合器式螺旋压力机的特点 236
离合器式螺旋压力机在机车车辆产品制造中的应用 236
第八节 电热镦锻 238
电热镦锻的特点 238
电热镦锻的应用 238
气门电热镦锻生产线 239
第九节 超塑性成形 239
材料的超塑性及超塑性成形 239
超塑性成形在机车车辆产品制造中的应用 240
超塑性锻造实例 241
第十节 温热挤压 241
挤压的种类 241
热挤压工艺的特点 241
温挤压特点及其应用 241
温热挤压实例 243
第十一节 电液锤 244
简介 244
电液锤的特点 245
第十二节 步冲机冲压 245
步冲机的特点 245
步冲机的类型 245
第十三节 型材拉弯 246
拉弯的基本原理 246
拉弯工艺的应用 247
第十四节 板料折弯 247
板料折弯和数控折弯技术 247
板料折弯工艺的应用 247
附表4-1 典型零件锻压工艺及先进技术应用 248
附表4-2 锻压剪冲工艺主要设备 249
第一章 概论 253
第一节 国内外热处理技术现状和发展趋势 253
热处理技术的现状与发展 253
我国热处理技术的发展目标 255
表面工程技术 255
第二节 机车车辆工业热处理及表面工程技术的发展方向 257
机车车辆工业热处理技术的发展方向 257
机车车辆工业表面工程技术的发展方向 257
第二章 热处理技术在机车车辆产品制造中的应用 258
第一节 通用热处理技术 258
热处理基础 258
几种通用的热处理技术 260
通用热处理技术在机车车辆工业中的应用 263
第二节 气体渗碳和可控气氛热处理 267
简介 267
可控气氛及其控制原理 267
齿轮的渗碳 269
渗碳技术的发展趋势 270
可控气氛多用炉 271
第三节 氮化技术 272
基本原理及特点 272
气体氮化和离子氮化技术 273
曲轴的氮化 274
盐浴氮碳共渗技术 277
盐浴氮碳共渗技术的应用 278
第四节 感应加热技术 280
基本原理和特点 280
从动齿轮的埋油感应淬火 281
曲轴的感应淬火和感应淬火机床 282
感应热处理技术的发展 284
第五节 激光热处理技术 284
基本原理和特点 284
激光热处理技术的应用 285
激光热处理技术的发展 286
第六节 真空热处理技术 287
真空加热和淬火技术 287
真空(低压)渗碳 288
真空热处理技术的应用 290
第七节 淬火冷却技术 293
特殊的淬火工艺 293
冷却过程和淬火介质 294
第八节 计算机技术在热处理中的应用 296
工艺过程的计算机控制 296
渗碳工艺的优化和自动控制系统 298
计算机查询系统 299
计算机模拟在热处理中的应用与发展 300
第三章 表面工程技术在机车车辆产品制造中的应用 303
第一节 电镀技术 303
原理及技术特点 303
电镀工艺及设备 303
第二节 磷化技术 314
原理及技术特点 314
磷化工艺及设备 314
应用实例 320
第三节 电刷镀技术 320
原理及技术特点 320
设备、工具及溶液 321
在机车车辆产品上的应用 327
第四节 氧乙炔焰粉末热喷涂喷焊技术 331
热喷涂基本原理及特点 331
设备与粉末 332
喷涂喷焊工艺 336
热喷涂喷焊技术的应用 341
第五节 等离子喷涂技术 344
基本原理和特点 344
等离子喷涂设备 344
等离子喷涂工艺 346
等离子喷涂技术的应用 347
第六节 电弧喷涂技术 349
基本原理及特点 349
电弧喷涂设备 349
电弧喷涂工艺 350
应用实例 351
第七节 喷丸强化技术及其应用 353
喷丸技术的基本原理及特点 353
喷丸设备及工艺 353
第八节 型钢板材表面防腐预处理技术 354
钢材抛丸预处理的除锈原理 354
QYS-3型抛丸预处理线及其应用 355
薄钢板抛丸预处理线 356
附表5-1 机车车辆零件应用表面工程技术实例 357
附表5-2 典型零件表面处理和先进技术应用项目 359
附表5-3 钢材预处理生产线 360
附表5-4 热处理工艺主要设备 361
第一章 概论 363
第一节 国内外机械加工技术的发展 363
发展概况 363
机械加工设备 364
刀具技术 365
夹具技术 366
计算机技术的应用 366
第二节 机车车辆工业机械加工技术的发展 369
发展概况 369
发展方向 369
第二章 通用机械加工技术 371
第一节 常用加工方法和加工设备 371
基本加工方式 371
机床分类 371
机床型号和主要参数 371
微电子技术在设备改造中的应用 376
第二节 机床夹具 377
定义、组成、分类 377
组合夹具 378
第三节 刀具技术 379
刀具在切削加工中的重要性 379
刀具材料 379
可转位刀具 380
刀具涂层技术 380
第三章 机车车辆零部件机械加工工艺 382
第一节 机车车辆走行部零部件加工工艺 382
货车轮轴加工生产线 382
机车转向架构架加工 385
车轴加工工艺 389
高速客车空心车轴的加工 390
轴箱加工 391
客车转向架(SW-160型)构架加工工艺 395
第二节 机车柴油机零部件加工工艺 397
柴油机机体加工 397
柴油机曲轴加工 400
柴油机钢顶铝裙活塞加工 402
柴油机气缸盖加工工艺 405
柴油机连杆加工工艺 410
柴油机气门生产线 411
柴油机喷油泵、喷油嘴(精密偶件)加工工艺 413
柴油机精密螺栓加工工艺 418
第三节 其他零件加工工艺 419
机车齿轮加工工艺及设备 419
增压器叶轮加工工艺 420
增压器涡轮叶片加工工艺 421
120型阀中间体加工工艺 422
第四节 特种加工技术 426
定义 426
常用的特种加工方法 426
电火花加工及应用 428
电解加工及应用 429
超声波加工及应用 430
激光加工及应用 430
第五节 数控技术及加工中心 431
数控技术 431
加工中心 433
第六节 专用机床与组合机床及其应用 435
专用机床的特点 435
组合机床的特点 436
专用加工设备的研制 437
活塞销孔加工组合机床 437
附表6-1 金属切削加工主要设备 441
第一章 概论 455
第一节 国内外理化检验与计量检测技术现状及发展趋势 455
分析化学技术 455
力学性能测试 456
金相检验 457
计量检测技术 458
无损检测技术 458
第二节 机车车辆工业理化检验与计量检测技术发展概况 461
化学及仪器分析 461
力学性能测试 461
金相检验 461
计量检测技术 461
无损检测技术 462
第二章 理化检验技术 463
第一节 化学分析 463
常规化学分析方法 463
仪器分析方法 464
钢中气体分析 469
第二节 金相检验 469
宏观检验 469
光学金相分析 470
图像分析技术 474
显微硬度测定 476
电子显微分析方法 477
第三节 力学性能及物理参数测试 479
常规力学性能试验 479
断裂性能测试 484
实物整体试验 485
残余应力测定 485
热性能测试 487
绝缘材料试验方法 488
涂料性能测试 489
第三章 计量检测技术 493
第一节 几何量计量 493
常用计量仪器 493
高精度及专用计量设备 496
铁路专用量具 497
在线检测 499
第二节 温度、电磁、力学计量 499
温度计量 499
电磁计量 501
力学计量 503
机车车辆产品主要专用计量器具 504
第四章 无损检测技术 507
第一节 磁粉检测 507
磁粉探伤原理 507
磁化方法 507
磁粉探伤方法 507
磁化规范 508
磁粉检测设备 509
磁粉探伤器材 510
第二节 超声波检测 512
超声波探伤基本原理 512
超声波探头和标准试块 516
第三节 射线检测 520
射线的产生 520
射线探伤原理 520
射线探伤设备 521
射线探伤器材 522
射线防护 523
第四节 涡流检测 523
涡流检测基本原理 523
涡流检测仪 524
检测用线圈 524
检测线圈的使用方式 525
对比试样 525
第五节 渗透检测 525
渗透探伤基本原理 525
渗透剂 525
显像剂 526
去除剂 527
渗透探伤的基本步骤 527
第五章 先进检测技术的应用 528
第一节 在理化检验中的应用 528
光电直读光谱技术 528
金属材料中气体分析 528
第二节 在测量中的应用 528
齿轮测量技术 528
曲轴形位公差检测 529
机体三孔同轴度检测 529
双边加载薄壁轴瓦半圆周长测量 529
轴承压装压力—位移连测 530
轴承不退轴动态质量检测 530
车轮踏面在加工中的自动检测 530
车轮踏面参数测量装置 531
数显轴径尺和轮径尺 531
机车车辆电子称重台 532
第三节 在探伤中的应用 532
车轴磁粉探伤 532
柴油机曲轴磁粉探伤 532
摇枕、侧架整体探伤 534
轮箍内部缺陷超声波探伤 534
涡流检测轴承滚子表面裂纹 535
气门表面渗透检测 537
第四节 清洁度检测 539
意义 539
分类 539
空气清洁度 539
测量内容 540
粉尘浓度测量方法 540
柴油机组装清洁度检测 541
轴承间清洁度检测 541
附表7-1 主要检测装备和仪器 543
第一章 概论 547
第一节 组装的基本概念 547
组装的含义 547
组装方法分类 547
第二节 组装工艺方案的基本要求 548
合理的工艺流程 548
良好的工作场地 548
必要的组装工艺装备 548
严格的检测及试验 549
油漆、美工和装潢要求 549
第二章 内燃机车组装技术 550
第一节 柴油机发电机组组装技术 550
喷油器组装技术 550
喷油泵组装技术 552
增压器组装技术 554
调速器组装技术 558
柴油机发电机组总组装 564
主要调整和检验项目 568
主要工艺装备 571
第二节 内燃机车总组装技术 572
组装前的准备 572
组装技术要求及工艺 572
主要工艺装备 575
组装后的试验 576
机车油漆 576
第三章 电力机车组装技术 577
第一节 电器屏柜组装 577
组装环境条件 577
组装技术要求 577
组装工艺流程与布线 579
检测及试验 581
第二节 转向架组装 582
转向架组装技术要求 582
各部件组装技术要求和组装工艺 583
转向架组装工艺流程及平面布置 585
检测及试验 586
第三节 电力机车总组装 586
组装技术条件 586
主要工序内容 587
工艺流程和布线 588
检测及试验 589
第四章 客车组装技术 592
第一节 转向架组装技术 592
SW-160型转向架结构 592
组装工艺 592
第二节 客车总组装技术 597
组装技术要求 597
总组装工艺 597
油漆与标记 601
检测及试验 604
第五章 货车组装技术 605
第一节 转向架组装技术 605
轮对组装 605
转向架总组装 605
第二节 货车总组装技术 608
组装技术要求 608
总组装工艺 608
主要工艺装备 610
第六章 牵引电机制造技术 612
第一节 概述 612
牵引电机的分类 612
牵引电机的特点 612
牵引电机的结构及系列 613
第二节 机座制造技术 622
简介 622
机座制造工艺 622
第三节 铁心制造技术 626
简介 626
铁心制造工艺 628
冲压设备与模具 629
第四节 换向器制造技术 631
简介 631
换向器制造工艺 632
第五节 线圈制造技术 634
简介 634
线圈制造工艺 636
线圈制造质量与下工序的关系 638
第六节 嵌线技术 639
工艺准备 639
直(脉)流电机电枢的嵌线 640
补偿绕组的嵌线 642
电枢线圈与升高片的焊接 642
转子的绑扎 643
直(脉)流电机电枢制造的质量要求 645
交流电机的嵌线 646
异步电机导条端板焊接 648
第七节 牵引电机的绝缘及绝缘处理工艺 650
牵引电机的绝缘结构 650
牵引电机常用绝缘材料 650
绝缘处理工艺 651
绝缘处理用的设备 651
绝缘处理的工艺过程 651
第八节 电机组装技术 653
直(脉)流牵引电动机总组装 653
同步牵引发电机总组装 660
异步牵引电动机总组装 662
第九节 牵引电机试验 663
简介 663
机车电机试验内容 664
测量仪器仪表 665
试验方法 665
机车电机试验设备 669
第一章 概论 671
第一节 机车车辆材料 671
金属材料 671
非金属材料 674
第二节 机车车辆材料的分类和选用原则 676
金属材料的分类 676
金属材料选用原则 676
非金属材料的分类及选用原则 677
第二章 金属材料 678
第一节 铁道车辆用主要金属材料 678
耐候钢 678
B级钢 679
C级钢 681
E级钢 684
奥贝球铁 686
第二节 铁道机车用主要金属材料 689
导磁铸钢 689
不锈钢 690
高温合金 692
Cr-Mo-Cu合金灰铸铁 697
球墨铸铁 698
硼铸铁 700
蠕墨铸铁 701
第三节 其他金属材料 703
制动闸瓦材料 703
柴油机轴瓦材料 708
第三章 非金属材料 712
第一节 塑料 712
塑料的特性 712
塑料的组成 712
常用塑料品种、性能及用途 713
塑料成形及加工方法 717
第二节 树脂基复合材料 718
分类 718
纤维类增强复合材料 719
功能型复合材料 720
阻燃塑料 720
第三节 胶粘剂和粘接技术 721
胶粘剂的组成 722
胶粘剂的分类 722
粘接技术 724
胶粘剂在机车车辆上的应用 724
第四节 橡胶及其制品 725
橡胶的特性及组成 725
橡胶的分类 726
橡胶制品的应用 726
第四章 油料和涂料 728
第一节 内燃机车用燃料 728
内燃机车燃油分类 728
内燃机车用轻柴油的牌号与性能指标 728
第二节 润滑油、润滑脂和冷却剂 729
内燃机车柴油机及增压器润滑油 729
电力机车变压器油 731
液力传动油 731
其他润滑油 732
润滑脂 732
冷却剂 734
第三节 机车车辆用涂料 735
涂料的作用 735
涂料的组成 735
涂料的分类 737
涂装技术 739
机、客车用涂料 740
货车用涂料 742
其他漆料 743
涂料在机车车辆上的应用 743
附表9-1 铁道机车主要零部件金属材料 745
附表9-2 铁道车辆主要零部件金属材料 747
附表9-3 合成材料在日本铁道车辆上的应用 748
附表9-4 合成材料在德国机车车辆上的应用 749
附表9-5 合成材料在我国铁道机车上的应用 750
附表9-6 合成材料在我国铁道车辆上的应用 751
附表9-7 常用塑料及树脂缩写代号和中文名称对照 752
第一章 计算机辅助设计CAD 753
第一节 CAD系统的组成与功能 753
CAD系统的组成 753
CAD系统的功能 753
CAD系统的应用效果 754
第二节 CAD系统的发展过程与趋势 754
CAD系统的发展过程 754
CAD系统的发展趋势 754
第二章 计算机辅助工程CAE 756
第一节 CAE的主要技术方法 756
动态设计技术 756
优化设计方法 757
可靠性设计 757
计算机仿真技术 757
第二节 CAE主流软件系统 758
CAE软件选择原则 758
有限元分析软件ANSYS 758
动力学仿真软件ADAMS 758
第三节 CAE应用实例 759
柴油机摇臂轴座裂纹分析 759
铁路凹底平车的结构轻量化 759
第三章 计算机辅助工艺过程设计CAPP 761
第一节 CAPP的含义与意义 761
计算机辅助工艺过程设计的含义 761
计算机辅助工艺过程设计的意义 761
第二节 CAPP的内容与步骤、方法 762
工艺过程设计的内容 762
工艺过程设计的步骤 762
工艺过程设计的方法 762
第三节 CAPP应用实例 762
冲压CAPP系统 762
机加工多模式CAPP系统 763
铸造工艺计算机辅助设计和凝固模拟分析系统 763
第四章 计算机辅助检测CAT 765
第一节 CAT系统的功能及组成 765
计算机辅助测试系统的功能 765
计算机辅助测试系统的组成 765
第二节 CAT应用实例 766
便携式动态测试系统 766
柴油机机体主轴承孔形位误差测量 766
光学金相显微镜的数码相机改造 766
第五章 计算机辅助制造CAM 767
第一节 数控加工编程 767
数控编程的内容与步骤 767
数控编程的方法及其发展 767
第二节 CAM在生产中的应用 768
逆向仿型加工系统 768
柴油机机体和气缸盖加工系统 768
数控弯管机和数控火焰切割机 768
印制电路板的CAM系统 768
第六章 计算机辅助管理MIS 770
第一节 MIS的开发应用 770
企业管理信息系统的定义 770
企业管理信息系统开发应用的目标 770
企业管理信息系统开发应用的原则和方法 771
第二节 MIS开发应用实例 771
微机网络管理信息系统 771
企业财务管理电算化 771
计算机辅助物资管理系统 772
资源需求计划MRPⅡ系统 772
第七章 计算机集成制造CIM 773
第一节 产品数据管理PDM 773
PDM应用背景 773
PDM应用实例 773
第二节 并行工程CE 774
并行工程应用背景 774
并行工程应用实例 774
第三节 计算机集成制造系统CIMS 775
第八章 计算机网络系统 776
第一节 中车公司广域网 776
广域网建设的意义 776
广域网技术方案 776
应用效果 777
第二节 LORIC国际互联网站 777
建立网站的意义 777
网站应用的效果 777
第三节 INTRANET企业网 777
Intranet的形成和发展 777
Intranet的组成和功能 778
Intranet企业网实例 778
- 《三毛传 你松开手我便落入茫茫宇宙》(中国)程碧 2019
- 《摄影构图超易上手》雷波著 2020
- 《超易上手 简谱与视唱入门教程 超适合零基础音乐爱好者》王凯编著 2020
- 《超易上手》于海力编著 2019
- 《更易上手弹古筝》舞雪歌云编著 2019
- 《铁路沿线大风风速智能预测理论》刘辉 2019
- 《黑板报手抄报即学即用一本就够》智典棒棒糖 2017
- 《水墨也软萌 超易上手的童趣国画》涂涂猫著 2019
- 《唯美手编 5 清爽的配色编织》(日本)日本宝库社 2019
- 《侨乡研究丛书 铁路华工的跨国生活 广东侨乡和北美铁路华工营的物质文化研究》谭金花,(美)芭芭拉·沃斯,(美)莱恩·肯尼迪编著 2019
- 《中国当代乡土小说文库 本乡本土》(中国)刘玉堂 2019
- 《异质性条件下技术创新最优市场结构研究 以中国高技术产业为例》千慧雄 2019
- 《中国铁路人 第三届现实主义网络文学征文大赛一等奖》恒传录著 2019
- 《莼江曲谱 2 中国昆曲博物馆藏稀见昆剧手抄曲谱汇编之一》郭腊梅主编;孙伊婷副主编;孙文明,孙伊婷编委;中国昆曲博物馆编 2018
- 《中国制造业绿色供应链发展研究报告》中国电子信息产业发展研究院 2019
- 《中国陈设艺术史》赵囡囡著 2019
- 《指向核心素养 北京十一学校名师教学设计 英语 七年级 上 配人教版》周志英总主编 2019
- 《《走近科学》精选丛书 中国UFO悬案调查》郭之文 2019
- 《清至民国中国西北戏剧经典唱段汇辑 第8卷》孔令纪 2018
- 《北京生态环境保护》《北京环境保护丛书》编委会编著 2018