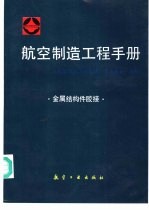
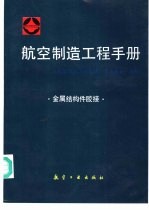
航空制造工程手册 金属结构件胶接PDF电子书下载
- 电子书积分:14 积分如何计算积分?
- 作 者:《航空制造工程手册》总编委会主编
- 出 版 社:北京:航空工业出版社
- 出版年份:1995
- ISBN:7800469085
- 页数:418 页
第1章 胶接概论 1
1.1 概述 1
1.1.1 金属胶接技术优缺点 1
目录 1
1.1.2 飞机金属胶接结构件分类 2
1.1.3 飞机金属胶接结构应用概况 3
1.2 飞机金属胶接工艺特点及使命 4
1.2.1 金属胶接工艺过程 4
1.2.2 飞机金属胶接工艺特点 4
1.3.1 现代飞机金属胶接技术水平标志 5
1.3.2 飞机金属胶接结构技术发展方向 5
1.2.3 飞机金属胶接工艺的使命 5
1.3 飞机金属胶接技术发展趋势 5
第2章 胶接体系 7
2.1 胶接接头的形成 7
2.1.1 胶接界面 7
2.1.1.1 胶接界面层的构成及特性 7
2.1.1.2 胶接界面效应及粘附力 7
2.1.2 胶粘剂的湿润 8
2.1.2.1 胶粘剂对被粘表面的湿润 8
2.1.2.2 影响胶接湿润的主要因素 9
2.1.3.1 固化方法 10
2.1.3 胶粘剂的固化 10
2.1.3.2 影响胶粘剂固化的主要因素 11
2.2 胶接接头的破坏 12
2.2.1 破坏机理 12
2.2.1.1 破坏位置 12
2.2.1.2 破坏特征 13
2.2.2 引起破坏的因素 13
2.3.1 先进胶接体系要素 15
2.3.2 先进胶接体系实现途径 15
2.3 先进胶接体系 15
第3章 胶接接头设计 17
3.1 胶接接头基本受力形式 17
3.2 胶接接头设计 18
3.2.1 胶接接头设计原则 18
3.2.1.1 按胶接特性设计接头 18
3.2.1.2 其他设计考虑 20
3.3 胶接接头形式 21
3.3.1 接头类型 21
3.3.2 典型胶接接头形式 21
3.3.3.1 飞机钣金胶接结构胶接接头 26
3.3.3 飞机典型结构胶接接头 26
3.3.3.2 飞机蜂窝胶接结构胶接接头 31
第4章 胶接材料的选择 34
4.1 选材原则及要求 34
4.1.1 选材原则 34
4.1.2 选材要求 34
4.1.3 选材程序 34
4.2.2 推荐的胶接用金属材料 35
4.2.2.2 国内推荐的金属材料 35
4.2.2.1 国外推荐的金属材料 35
4.2.1 选材附加要求 35
4.2 金属材料的选择 35
4.3 蜂窝芯材的选择 36
4.3.1 选材附加要求 36
4.3.2 芯材标准及选材 36
4.4 胶粘剂的选择 37
4.4.1 选材附加要求 37
4.4.2 国外推荐的金属胶接胶粘剂体系 37
4.4.3 国内推荐的金属胶接胶粘剂体系 38
4.5.2 推荐选用的密封剂 39
4.5.1 选材附加要求 39
4.5 密封防护材料的选择 39
第5章 结构胶粘剂 41
5.1 结构胶粘剂的分类及特性 41
5.1.1 结构胶粘剂的主要性能要求 42
5.1.1.1 美国军用规范对金属蜂窝结构胶粘剂要求 42
5.1.1.2 美国联邦规范对金属钣金结构胶粘剂要求 42
5.1.1.3 中国航标对金属钣金结构胶粘剂要求 42
5.1.1.4 中国航标对金属蜂窝结构胶粘剂要求 42
5.1.2.1 胶膜 47
5.1.2 结构胶粘剂的供应状态及使用特点 47
5.1.1.5 结构胶粘剂的重要性能 47
5.1.2.2 发泡胶 48
5.1.2.3 糊状胶 48
5.1.2.4 底胶 48
5.1.3 结构胶粘剂的化学类型及特性 48
5.1.3.1 改性酚醛胶粘剂 48
5.1.3.2 改性环氧胶粘剂 49
5.1.3.3 双马来酰亚胺胶粘剂 50
5.1.3.4 聚酰亚胺胶粘剂 50
5.2.1.2 主要力学性能及应用情况 51
5.2.1.1 基本组成、材料标准及工艺特性 51
5.2 可供选用的结构胶粘剂及其主要特性 51
5.2.1 国内常用结构胶粘剂 51
5.2.2 国外常用结构胶粘剂 70
5.2.2.1 基本组成、供应状态及工艺特性 70
5.2.2.2 主要力学性能 70
第6章 金属被粘物 82
6.1 金属被粘物要求 82
6.1.1 表面清洁度 82
6.1.3 线膨胀系数及电化学电位 83
6.1.3.1 线膨胀系数 83
6.1.2 表面粗糙度 83
6.1.3.2 电化学电位 84
6.1.4 胶粘剂匹配 85
6.2 可供选用的常用金属被粘物及其主要性能 85
6.2.1 可供选用的常用金属被粘物 85
6.2.1.1 国外常用铝合金 85
6.2.1.2 国内常用铝合金 86
6.2.1.3 其他合金 86
6.2.2 常用金属被粘物的主要力学性能 87
6.2.2.1 材料技术规范 87
6.2.2.2 主要力学性能 88
6.3 常用金属被粘物的固化温度及时间限制 90
第7章 铝蜂窝芯材 91
7.1 分类及要求 91
7.1.1 概述 91
7.1.1.1 芯材格形 91
7.1.1.2 通气孔及耐久性 92
7.1.1.3 芯材方向及标注 93
7.1.2 分类 93
7.1.3.1 物理性能 94
7.1.3 要求 94
7.1.3.2 力学性能 95
7.1.3.3 耐腐蚀性能 103
7.1.3.4 外观 103
7.1.3.5 颜色代号识别 104
7.1.3.6 验收或鉴定试验项目 104
7.2 可供选用的铝蜂窝芯材 105
7.2.1 国外可供选用的芯材及其性能 105
7.2.2 国内可供选用的芯材及其性能 109
7.2.2.1 SYL-3芯材的性能 110
7.2.2.2 BSC芯材的性能 113
7.2.2.3 其他芯材性能 116
第8章 密封防护材料 118
8.1 密封防护作用 118
8.2 密封防护材料分类及一般要求 119
8.2.1 密封防护材料分类 119
8.2.2 密封防护材料的一般要求 121
8.3 可供选择的密封防护材料 121
第9章 辅助材料 123
9.1 种类及用途 123
9.2.1.1 脱模材料分类 124
9.2.1.2 脱模材料选材 124
9.2 脱模材料 124
9.2.1 分类和选材 124
9.2.2 溶液类脱模材料 125
9.2.2.1 配制方法 125
9.2.2.2 技术指标 125
9.2.3 薄膜类脱模材料 125
9.2.3.1 聚四氟乙烯玻璃布 125
9.2.3.2 E3760和A5000薄膜 126
9.3 真空袋薄膜 127
9.2.3.3 单面涂压敏胶的脱模薄膜 127
9.4 有孔隔离膜 128
9.5 边挡材料 130
9.6 压力传递材料 130
9.7 透气材料 131
9.7.1 作用和选材 131
9.7.2 技术数据 131
9.8 压敏胶带 132
9.9 密封腻子 133
9.10 印痕薄膜层片 134
10.1.2 类别及用途 135
10.1.3 技术要求 135
第10章 胶接工艺装备 135
10.1.1 特点 135
10.1 特点、类别与要求 135
10.2 固化模胎 136
10.2.1 基本组成部分及功能 136
10.2.2 分类 137
10.2.3 技术要求 137
10.2.5 整体铸铝固化模胎(铸铝胎) 138
10.2.4.2 芯模 138
10.2.5.1 模体 138
10.2.4.1 模体 138
10.2.4 平板固化模胎(平板胎) 138
10.2.5.2 芯模 139
10.2.5.3 压紧机构 141
10.2.5.4 检验卡板 142
10.2.6 构架式固化模胎(构架胎) 143
10.2.6.1 特点 144
10.2.6.2 结构 144
10.3.1 分类 145
10.3 铣切模胎 145
10.3.2 技术要求 146
10.3.3 预变形法加工蜂窝零件的铣切模胎 146
10.3.3.1 用途 146
10.3.3.2 结构 146
10.3.3.3 型面加工依据 147
10.3.4 仿形或数控加工用的铣切模胎 148
10.4 装配及检验型架 148
10.4.1 装配型架 148
10.5.3 装配型架的选用原则 149
10.5.2 铣切模胎的选用原则 149
10.5 胶接工艺装备的选用原则 149
10.4.2 检验型架 149
10.5.1 固化模胎的选用原则 149
10.5.4 检验型架的选用原则 150
10.6 协调依据及容差分配 150
10.6.1 模线样板-标准样件法 150
10.6.2 CAD/CAM法 151
10.6.2.1 编制原则 151
10.6.3 协调误差 152
10.6.3.1 CAD/CAM法自身的误差 152
10.6.2.2 协调路线及若干有关问题 152
10.6.3.2 CAD/CAM法的协调误差 153
10.6.4 容差分配 153
10.7 工装鉴定及使用维护 153
10.7.1 胶接工装的鉴定 153
10.7.2 胶接工装的使用维护 154
第11章 胶接设备 155
11.1 铝蜂窝芯材制造专用设备 155
11.1.1 铝箔处理机 155
11.1.1.1 铝箔碱洗处理机 155
11.1.1.3 铝箔耐久处理机 157
11.1.1.2 铝箔耐蚀处理机 157
11.1.1.4 成形法制造芯材的铝箔处理机 158
11.1.1.5 铝箔处理机使用注意事项 159
11.1.2 成形法制造蜂窝芯材的设备 159
11.1.2.1 波形条成形机 159
11.1.2.2 波形条成形机使用注意事项 160
11.1.3 拉伸法制造蜂窝芯材的设备 160
11.1.3.1 铝箔涂胶机 161
11.1.3.2 蜂窝拉伸机 167
11.2 胶粘剂涂敷设备 169
11.2.1 底胶涂敷设备 169
11.2.1.1 空气喷涂装置 169
11.2.1.2 静电喷涂装置 170
11.2.2 胶膜贴敷设备 171
11.3 胶接固化设备 171
11.3.2 加热炉(箱) 172
11.3.1.3 使用注意事项 172
11.3.3.1 工作原理 172
11.3.3 热压罐 172
11.3.1.2 构件固化用热压机 172
11.3.1.1 箔层固化用热压机 172
11.3.1 热压机 172
11.3.3.2 分类 173
11.3.3.3 技术要求 173
11.3.3.4 结构组成及用途 174
11.3.3.5 热压罐微机控制 174
11.4 蜂窝芯材机械加工设备 175
11.4.1 锯床 175
11.4.2.3 靠模铣床 176
11.4.2.2 平面铣床 176
11.4.2.1 特点 176
11.4.2 蜂窝铣床 176
11.4.2.4 数控蜂窝铣床 177
第12章 胶接厂房技术要求 178
12.1 胶接厂房特点 178
12.1.1 重要性 178
12.1.2 胶接工序对厂房的特殊要求 178
12.2 国外对胶接厂房的要求 179
12.2.1 净化间要求 179
12.2.2 厂房清洁度要求 179
12.3 胶接厂房分类及要求 179
12.3.1 分类 179
12.3.2.1 环境要求 182
12.3.2 一类厂房(净化间)技术要求 182
12.3.2.2 设施要求 183
12.3.2.3 土建及暖通要求 183
12.3.2.4 消防、防爆及“三废”排放要求 184
12.3.2.5 其他要求 184
12.3.3 二类厂房技术要求 184
12.4.1.2 工艺布置内容 185
12.4.2.1 铝箔处理间 185
12.4.2 胶接工作间的工艺要求 185
12.4.1.1 胶接车间工艺布置的特点 185
12.4.1 工艺布置 185
12.4 胶接车间工艺要求 185
12.4.2.2 铝箔涂胶间 186
12.4.2.3 胶粘剂贮存间 186
12.4.2.4 配胶间 186
12.4.2.5 表面处理间 186
12.4.2.6 底胶喷涂间 186
12.4.2.7 胶膜粘贴间 186
12.4.2.9 胶接件固化间 187
12.4.2.8 胶接装配间 187
第13章 胶接技术安全和劳动保护 188
13.1 胶接作业防毒安全技术 188
13.1.1 主要毒物分级和危害 188
13.1.1.1 职业性接触毒物危害程度分级依据 188
13.1.1.2 职业性接触毒物的危害 188
13.1.2 安全技术措施 189
13.1.3 个人防护 190
13.1.4 中毒急救 190
13.2.2 主要易燃易爆物的贮存及灭火方法 191
13.2.2.1 贮存及灭火方法 191
13.2.1 主要易燃易爆物 191
13.2 防火防爆安全技术 191
13.2.2.2 隔离存放 192
13.2.3 安全技术措施 192
13.3 压力容器安全技术 193
13.3.1 安全检查内容和方法 193
13.3.2 安全附件 193
13.3.3 热压罐运行安全要求 194
13.4 废弃物处理 194
14.1.1 预装配目的 196
14.1.2 预装配程序及注意事项 196
14.1 目的及程序 196
第14章 胶接零件预装配 196
14.2 胶接零件技术要求 197
14.2.1 夹芯零件 197
14.2.2 其他零件 197
14.2.2.1 钣金成形零件 197
14.2.2.2 板弯型材零件 197
14.2.2.3 挤压型材零件 198
14.2.2.4 平板零件 198
14.3.1 配合技术要求 199
14.3 胶接零件预装配配合要求 199
14.2.3 其他要求 199
14.3.2 零件补充加工 201
14.4 校验膜法预装配 201
14.4.1 校验膜分类和要求 201
14.4.1.1 分类 201
14.4.1.2 要求 201
14.4.2 预装配应用 201
14.4.2.1 校验固化成形模具(或夹具) 201
14.4.2.2 大型复杂胶接构件预装配 201
15.1.2 分类 203
15.1.1 要求 203
第15章 胶接零件表面处理 203
15.1 要求及分类 203
15.1.3 注意事项 204
15.2 常用金属被粘物表面处理方法 204
15.2.1 铝合金 204
15.2.1.1 化学氧化处理法(FPL法) 204
15.2.1.2 铬酸阳极化法(CAA法) 205
15.2.1.3 磷酸阳极化法(PAA法) 205
15.2.2.1 分类 207
15.2.2.2 铬酸-氟化物阳极化法 207
15.2.2 钛合金 207
15.2.1.4 其他表面处理方法 207
15.2.2.3 NaTESi阳极化法 208
15.2.3 其他材料 208
15.2.3.1 镁合金 208
15.2.3.2 不锈钢 209
15.2.3.3 钢及铁合金 210
15.2.3.4 锌合金及镀锌金属 210
15.2.3.5 铜、黄铜及青铜 210
15.2.3.6 镍及其合金 211
15.2.3.7 钨及其合金 211
15.2.3.8 铝蜂窝芯材 211
16.1.1.1 胶粘剂调配 212
16.1.1 胶粘剂调配、贮存及启封 212
16.1.1.2 胶粘剂贮存及启封 212
第16章 胶粘剂涂敷 212
16.1 胶粘剂准备 212
16.1.2 胶液粘度测定 213
16.2 胶粘剂应用形式及涂敷方法 213
16.2.1 胶粘剂应用形式和底胶种类及作用 213
16.2.1.1 胶粘剂应用形式 213
16.2.1.2 底胶的作用 214
16.2.2 胶粘剂涂敷方法 214
16.2.2.1 胶液涂敷方法 214
16.3.1 喷涂特点 216
16.2.2.2 胶膜贴敷方法 216
16.3 底胶喷涂技术 216
16.3.2 喷涂方法 217
16.3.3 喷涂参数 218
16.4 常用胶粘剂涂敷工艺参数 220
16.4.1 国内常用胶粘剂涂敷工艺参数 220
16.4.2 国外常用胶粘剂涂敷工艺参数 221
17.1.2.1 封装目的 223
17.1.1 组装 223
17.1.2 真空袋封装 223
17.1 胶接构件组装及真空袋封装 223
第17章 胶接组装、固化及密封 223
17.1.2.2 热电偶的固定 224
17.1.2.3 真空袋封装注意事项 225
17.2 胶接构件的固化方法及参数 226
17.2.1 固化要素 226
17.2.1.1 固化压力 226
17.2.1.2 固化温度 227
17.2.1.3 固化工艺参数选择 227
17.2.2.2 工艺特点 228
17.2.2.1 工艺流程 228
17.2.2 热压机固化法 228
17.2.3 加热炉(烘房)固化法 229
17.2.3.1 低压胶接构件的特性 230
17.2.3.2 工艺流程及控制参数 230
17.2.3.3 工艺要求 230
17.2.4 热压罐固化法 231
17.2.4.1 热压罐固化法适用范围 231
17.2.4.2 工艺流程及注意事项 231
17.2.5 常用胶粘剂固化参数 232
17.2.5.1 板-板胶粘剂 232
17.2.5.4 点焊胶粘剂 233
17.2.5.3 发泡胶粘剂 233
17.2.5.2 板-芯胶粘剂 233
17.2.5.5 国外胶粘剂 234
17.3 胶接构件清理及密封防护 234
17.3.1 胶接构件的清理 234
17.3.1.1 卸模取件 234
17.3.1.2 表面清理 234
17.3.1.3 切除余量 235
17.3.2 密封防护 235
17.3.2.1 密封形式与要求 235
17.3.2.2 密封工艺 236
第18章 胶接修补 238
18.1 修补内容及要求 238
18.1.1 修补内容及意义 238
18.1.2 修补要求 238
18.2 胶接缺陷及损伤分类和修补方案 239
18.2.1 胶接缺陷及损伤分类 239
18.2.2 修补方案 240
18.3 修补材料及设施 241
18.3.1 修补材料 241
18.3.1.1 修补胶粘剂 241
18.3.1.2 蜂窝芯材 242
18.3.2 修补工具及设备 243
18.3.1.3 其他材料 243
18.4 修补工艺 244
18.4.1 修补方法 244
18.4.2 修补工艺典型操作 247
第19章 铝蜂窝芯材制造 253
19.1 概述 253
19.1.1 发展与应用 253
19.1.2 制造方案及特点 253
19.1.2.3 铝箔处理方法 254
19.1.2.4 制造方案比较 254
19.1.2.2 格子形状 254
19.1.2.1 铝箔厚度和芯材密度 254
19.2 成形法制造蜂窝芯材 255
19.2.1 工艺流程 255
19.2.2 制造方法 255
19.2.2.1 箔料分割 255
19.2.2.2 制通气孔及波形条成形 256
19.2.2.3 除油 257
19.2.2.4 涂胶 258
19.2.2.6 叠装 259
19.2.2.5 制叠装定位孔 259
19.3 拉伸法制造蜂窝芯材 260
19.3.1 工艺流程 260
19.3.2 制造方法 260
19.3.2.1 铝箔除油 260
19.3.2.2 涂胶 260
19.2.2.7 固化 260
19.3.2.3 制通气孔 262
19.3.2.4 切割下料 263
19.3.2.5 叠装固化 263
19.4 耐蚀蜂窝芯材的制造 264
19.4.1 铝箔耐蚀处理 264
19.3.2.6 叠层板下料 264
19.3.2.7 拉伸成形 264
19.4.2 普通芯材耐蚀处理 265
19.4.2.1 芯材耐蚀处理 265
19.4.2.2 耐蚀芯材性能 266
19.4.3 两种耐蚀芯材制造方法比较 267
19.5 耐久铝蜂窝芯材制造 267
19.5.1 铝箔耐久处理 267
19.5.2 耐久性与力学性能 268
19.6 机械加工 269
19.6.1.1 排样 270
19.6.1.2 条料加工 270
19.6.1.3 刀具 270
19.6.1 叠层板下料 270
19.6.2 芯材下料及拼接 271
19.6.2.1 下料 271
19.6.2.2 拼接 271
19.6.3 芯材型面加工 273
19.6.3.1 型面加工 273
19.6.3.2 加工用刀具 274
19.7.1 外观质量 275
19.6.3.3 夹芯固持方法 275
19.7 芯材检验 275
19.7.2 力学性能 276
第20章 蜂窝胶接结构制造 277
20.1 概述 277
20.1.1 典型结构及分类 277
20.1.2 工艺流程 277
20.1.2.1 零件制造 277
20.1.2.2 预装配 278
20.1.2.6 质量检验 279
20.1.2.5 装配、封装、固化及清理 279
20.1.2.3 胶接表面处理 279
20.1.2.4 涂敷胶粘剂 279
20.2 舵面类蜂窝结构件胶接 280
20.2.1 结构特点 280
20.2.2 芯材表面处理 281
20.2.3 工艺特点 281
20.2.4 实例 282
20.3 曲板、筒体类结构件胶接 283
20.3.1 结构特点 283
20.3.2 工艺特点 285
20.3.3 实例 286
20.3.4 层压或挤压边缘蜂窝夹层板的压制工艺 288
20.4 无孔蜂窝结构件胶接 289
20.4.1 结构特点及芯格内压变化 289
20.4.1.1 结构特点 289
20.4.1.2 芯格内压变化 290
20.4.2 工艺特点 290
20.4.3 实例 290
20.4.4 常见胶接缺陷、产生原因及预防措施 291
20.5.3 内嵌件固定法 292
20.5.2 预埋件固定法 292
20.5.1 嵌入件的分类 292
20.5 嵌入件及其固定法 292
20.5.4 实例 293
第21章 钣金胶接结构制造 294
21.1 概述 294
21.1.1 钣金胶接结构应用 294
21.1.2 钣金胶接结构分类 295
21.2 板-桁条结构件胶接 297
21.2.1 结构工艺特点 297
21.2.2 工艺流程及要点 298
21.2.3 胶接缺陷及产生原因 300
21.3 翼肋、翼梁结构件胶接 301
21.3.1 结构工艺特点 301
21.3.2 工艺流程及要点 302
21.3.3 胶接缺陷及产生原因 302
21.4 波骨板结构件胶接 302
21.4.1 结构工艺特点 302
21.4.2 工艺流程及要点 303
21.5 层板结构件胶接 304
21.5.1 结构工艺特点 304
21.4.3 胶接缺陷及产生原因 304
21.5.2 工艺流程及要点 305
21.5.3 胶接缺陷及产生原因 305
第22章 胶焊结构制造 307
22.1 概述 307
22.1.1 胶焊结构应用 307
22.2.1 铝合金胶焊件工艺流程 308
22.2.2 点焊前准备 308
22.2 先焊后胶制造法 308
22.1.2 胶焊结构工艺方案 308
22.2.3 点焊 309
22.2.4 注胶 310
22.2.5 固化及检验 311
22.2.6 常见胶接缺陷及产生原因 311
22.3 先胶后焊制造法 312
22.3.1 工艺流程 312
22.3.2 胶粘剂 312
22.3.3 工艺要点 314
23.2.1 结构形式 315
23.2 胶铆工艺 315
23.1 概述 315
第23章 胶铆及胶螺结构制造 315
23.2.2 工艺流程 316
23.2.2.1 胶接固化后铆接 316
23.2.2.2 胶接涂胶及铆接后固化 317
23.2.3 工艺过程注意事项 317
23.3 胶螺工艺 318
23.3.1 结构形式 318
23.3.2 工艺流程 319
23.4 密封防护 320
23.3.3 工艺过程注意事项 320
第24章 特种胶接结构制造 321
24.1 铝合金胶接复合层板 321
24.1.1 特性及应用 321
24.1.1.1 特性 321
24.1.1.2 应用 322
24.1.2 技术要求 322
24.1.2.1 复合层板种类 322
24.1.2.2 技术要求(国产铝复合层板) 323
24.1.3 胶接工艺 323
24.1.3.1 胶粘剂 323
24.1.4.1 基本力学性能 324
24.1.4 铝复合层板性能 324
24.1.3.2 工艺特点 324
24.1.4.2 剩余胶接强度 325
24.2 纤维增强铝合金胶接层板 325
24.2.1 特性、应用及发展动态 325
24.2.1.1 特性 326
24.2.1.2 应用 327
24.2.1.3 发展动态 327
24.2.2 品级、材料及性能 328
24.2.2.1 品级及组成 328
24.2.2.2 材料 329
24.2.2.3 性能 330
24.2.3 胶接工艺 331
24.2.3.1 工艺流程 331
24.2.3.2 制造工艺 332
24.3 前缘防冰结构胶接 332
24.3.1 结构形式 333
24.3.2 胶接工艺 333
24.3.3 故障及排除方法 334
24.4 芳纶纸蜂窝芯材结构胶接 335
24.4.1 芳纶纸蜂窝芯材性能 335
24.4.1.1 芳纶纸 335
24.4.1.2 国产芳纶纸蜂窝芯材性能 336
24.4.1.3 国外芳纶纸蜂窝芯材性能 337
24.4.2 胶接工艺 337
24.4.2.1 Nomex芯材零件制造 338
24.4.2.2 胶接表面制备 339
24.4.2.3 填充块胶接 339
24.4.2.4 胶接固化 339
24.5 消音蜂窝壁板制造 339
24.5.1 结构形式及应用 340
24.5.2 胶粘剂 340
24.5.3.2 蜂窝芯材贴膜及破膜法 341
24.5.3.1 铝面板制孔 341
24.5.3 胶接工艺 341
第25章 理化性能检测 343
25.1 胶粘剂理化性能检测 343
25.1.1 目的和范围 343
25.1.2 检测方法 343
25.2 密封防护材料理化性能检测 346
25.2.1 目的和范围 346
25.2.2 检测方法 346
25.2.3 密封腻子和液态密封垫理化性能检测标准 349
26.1 胶接件力学性能检测通用要求 350
第26章 胶接件力学性能检测 350
26.3 蜂窝结构胶接性能检测 351
26.4 胶接结构件力学性能试验 351
26.4.1 典型结构件力学性能试验 351
26.4.1.1 全高度夹层结构典型件的悬臂梁弯曲试验 351
26.2 板-板胶接性能检测 351
26.4.1.2 蜂窝夹层板的压缩稳定性试验 362
26.4.1.3 蜂窝夹层结构的剪切稳定性试验 362
26.4.1.6 蜂窝夹层结构压-剪复合与冲击联合试验 363
26.4.1.7 蜂窝夹层结构高-低-常温振动式验 363
26.4.1.5 蜂窝夹层结构压-剪复合与侧压联合试验 363
26.4.1.4 蜂窝夹层结构的压-剪复合试验 363
26.4.2 胶接部件试验 364
第27章 胶接接头耐应力环境性能试验 365
27.1 耐应力环境性能 365
27.2 钣-钣胶接接头耐应力环境试验 365
27.2.1 传统试验方法 365
27.2.1.1 静应力环境试验 365
27.2.1.2 循环应力环境试验 370
27.2.2 断裂力学试验方法 370
27.2.2.1 静应力环境断裂试验 372
27.3.1 蜂窝夹层试样试验 374
27.2.2.2 循环应力环境断裂试验 374
27.3 蜂窝结构胶接接头耐应力环境试验 374
27.3.2 蜂窝结构元件试验 376
第28章 胶接质量无损检测 378
28.1 任务 378
28.2 缺陷类型及产生原因 379
28.2.1 金属钣金胶接结构制造中的主要胶接缺陷 379
28.2.2 金属蜂窝胶接结构制造中的主要胶接缺陷 380
28.2.3 金属胶接结构使用中出现的主要缺陷 381
28.3.1 胶接表面质量检查 382
28.3 无损检测方法 382
28.3.2 目视检验 383
28.3.3 敲击法 384
28.3.4 声振检测 385
28.3.5 超声波检测 386
28.3.6 射线检测 388
28.3.7 激光全息照相 388
28.3.8 热学检测 389
28.3.9 声发射与应力波检测 390
28.4 常用胶接无损检测方法的选择 391
28.5.2 设备要求 392
28.5.1 人员要求 392
28.5 检测条件 392
28.5.3 标准试块 393
28.5.4 验收标准 393
28.5.4.1 对分离缺陷的要求 393
28.5.4.2 对群集状缺陷的要求 394
29.1.1 意义 395
29.1.1.1 确保安全性 395
29.1.1.2 减小分散性 395
29.1 意义及要求 395
第29章 胶接质量控制 395
29.1.2 胶接质量控制要求 396
29.1.2.1 总要求 396
29.1.2.2 胶接质量控制的基本要求 397
29.2 胶接生产要素的质量控制 398
29.2.1 厂房与环境的质量控制 398
29.2.2 胶接仪器、设备及装置的质量控制 398
29.2.2.1 一般要求 398
29.2.2.2 仪器、设备与装置的质量控制 398
29.2.2.3 工艺装备的质量控制 399
29.2.3.1 胶粘剂的质量控制 400
29.2.3 胶接用材料的质量控制 400
29.2.3.2 辅助材料的质量控制 401
29.2.4 胶接工艺过程的质量控制 401
29.2.5 胶接制品的质量控制 403
29.2.5.1 胶接随炉试件(胶接控制试件) 403
29.2.5.2 胶接制件质量检验 403
29.2.5.3 胶接制件首件鉴定 403
29.2.5.4 胶接制件抽件检验 404
29.2.6.4 特殊训练人员 405
29.2.6.3 重新考核 405
29.2.6.2 结构胶接特种工艺人员 405
29.2.6.1 结构胶接属特种工艺 405
29.2.6 从事结构胶接的人员素质要求 405
29.3 技术文件及管理控制 406
29.3.1 技术文件控制 406
29.3.2 管理控制 406
29.3.2.1 工艺能力鉴定 406
29.3.2.2 不合格品控制 406
29.3.2.3 胶接制件质量控制履历本 406
29.3.2.4 质量保证系统 407
第30章 胶接术语 408
参考文献 416
- 《市政工程基础》杨岚编著 2009
- 《联吡啶基钌光敏染料的结构与性能的理论研究》李明霞 2019
- 《异质性条件下技术创新最优市场结构研究 以中国高技术产业为例》千慧雄 2019
- 《工程静力学》王科盛主编 2019
- 《中国制造业绿色供应链发展研究报告》中国电子信息产业发展研究院 2019
- 《中央财政支持提升专业服务产业发展能力项目水利工程专业课程建设成果 设施农业工程技术》赵英编 2018
- 《Maya 2018完全实战技术手册》来阳编著 2019
- 《化学反应工程》许志美主编 2019
- 《绿色过程工程与清洁生产技术 张懿院士论文集精选 上》《绿色过程工程与清洁生产技术》编写组编 2019
- 《软件工程》齐治昌,谭庆平,宁洪编著 2019
- 《莼江曲谱 2 中国昆曲博物馆藏稀见昆剧手抄曲谱汇编之一》郭腊梅主编;孙伊婷副主编;孙文明,孙伊婷编委;中国昆曲博物馆编 2018
- 《指向核心素养 北京十一学校名师教学设计 英语 七年级 上 配人教版》周志英总主编 2019
- 《植物百科彩色图鉴 第2卷》植物百科彩色图鉴编委会主编 2012
- 《远去的老调》经典文库编委会编 2019
- 《北京生态环境保护》《北京环境保护丛书》编委会编著 2018
- 《莼江曲谱 1 中国昆曲博物馆藏稀见昆剧手抄曲谱汇编之一》郭腊梅主编;孙伊婷副主编;孙文明,孙伊婷编委;中国昆曲博物馆编 2018
- 《共和国日记 1964》《共和国日记》编委会编 2019
- 《中国地方艺文荟萃 华北东北卷 第1辑 3》《中国地方艺文荟萃》编委会编 2018
- 《绿色过程工程与清洁生产技术 张懿院士论文集精选 上》《绿色过程工程与清洁生产技术》编写组编 2019
- 《中国地方艺文荟萃 华北东北卷 第1辑 1》《中国地方艺文荟萃》编委会编 2018
- 《指向核心素养 北京十一学校名师教学设计 英语 七年级 上 配人教版》周志英总主编 2019
- 《北京生态环境保护》《北京环境保护丛书》编委会编著 2018
- 《指向核心素养 北京十一学校名师教学设计 英语 九年级 上 配人教版》周志英总主编 2019
- 《高等院校旅游专业系列教材 旅游企业岗位培训系列教材 新编北京导游英语》杨昆,鄢莉,谭明华 2019
- 《中国十大出版家》王震,贺越明著 1991
- 《近代民营出版机构的英语函授教育 以“商务、中华、开明”函授学校为个案 1915年-1946年版》丁伟 2017
- 《新工业时代 世界级工业家张毓强和他的“新石头记”》秦朔 2019
- 《智能制造高技能人才培养规划丛书 ABB工业机器人虚拟仿真教程》(中国)工控帮教研组 2019
- 《陶瓷工业节能减排技术丛书 陶瓷工业节能减排与污染综合治理》罗民华著 2017
- 《全国职业院校工业机器人技术专业规划教材 工业机器人现场编程》(中国)项万明 2019