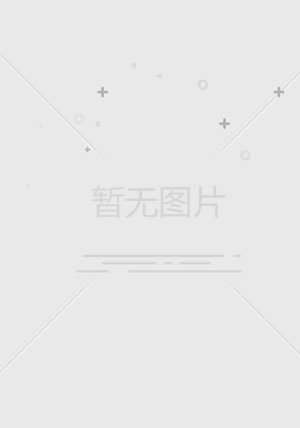
第1篇 切削加工 3
第1章 切削加工理论基础 3
1.1切削加工 3
1.1.1切削加工的优缺点 3
1.1.2切削加工类型 3
目录 3
1.1.3评价切削加工状况的基准 4
1.2刀具的几何形状及选择原则 4
1.2.1切削运动 4
1.2.2刀具切削部分的几何角度 5
1.2.3刀具切削角度的选择原则 7
1.3.1切屑的形成过程及种类 9
1.3切屑 9
1.3.2切削比、剪切角和剪切应变 10
1.3.3影响切屑形态的因素和断屑 12
1.4积屑瘤及其类似物 15
1.4.1积屑瘤及其类似物的种类 15
1.4.2积屑瘤对切削加工的影响及防止方法 15
1.5切削力 16
1.5.1车削的三个分力 16
1.5.2主切削力的理论公式 16
1.5.3影响切削力的因素 18
1.6.3温升对切削性能的影响 19
1.6.2影响前刀面平均温度的因素 19
1.6.4切削温度的测定方法 19
1.6.1切削热的产生与传出 19
1.6切削热与切削温度 19
1.6.5计算切削温度的实用公式 20
1.7切削加工中的振动 20
1.7.1引起受迫振动的原因及消减措施 21
1.7.2产生自激振动的原因及消除措施 21
1.8刀具磨损与耐用度 24
1.8.1刀具磨损的形态 24
1.8.2刀具磨损对切削加工的影响 25
1.8.3刀具磨钝标准 25
1.8.4刀具磨损的原因及减少磨损的措施 26
1.8.5刀具耐用度、影响因素及提高耐用度的方法 28
2.1影响加工精度的因素 30
第2章 切削加工质量 30
2.2提高加工精度的措施 33
2.3经济加工精度 34
2.4表面粗糙度的评定指标 43
2.4.1基本概念 43
2.4.2评定表面粗糙度的参数及其数值系列 45
2.5表面粗糙度的分级 46
2.5.1规定表面粗糙度要求的一般规则 47
2.5.2附加的评定表面粗糙度的参数和数值 47
2.5.3关于取样长度和评定长度的选用 48
2.6各种加工方法所能得到的表面粗糙度 49
2.7表面粗糙度与加工精度和配合之间的关系 54
第3章 冷却与润滑 58
3.1冷却润滑剂的作用 58
3.2冷却润滑剂的种类、配方和使用 59
3.3冷却润滑剂的添加剂 64
3.4冷却润滑剂的选用 65
第4章 毛坯选择和加工余量 68
4.1毛坯的选择 68
4.1.1选择毛坯时应考虑的问题 68
4.1.2毛坯种类及其制取方法的选择 68
4.2加工余量 69
4.2.1毛坯的切削加工余量 70
4.2.2切削加工的工序间余量 80
第5章 基准 89
5.1基准概述 89
5.2基准选择 90
5.4尺寸链计算实例 93
5.3基准间尺寸换算 93
5.5基准不同产生的误差分析 101
5.6基准不同实例 107
第6章 车削加工 110
6.1车刀 110
6.1.1刀具材料 110
6.1.2车刀几何角度及其选择 113
6.1.3可转位机夹车刀 117
6.1.4金刚石车刀 120
6.2普通车床加工 123
6.2.1普通车床类型及工作精度 123
6.2.2精密车床技术性能 124
6.2.3普通车床的切削用量 126
6.2.4车床装夹方法及装夹精度 133
6.2.5细长轴车削 135
6.2.6螺纹车削 137
6.2.7薄壁件车削 143
6.3精密车削 146
6.3.1虹面和镜面车削 146
6.3.2磁盘车削 148
6.3.3磁鼓加工 150
6.4常用的自动车床加工 150
6.4.1单轴纵切自动车床的调整设计 152
6.4.2单轴六角自动车床的调整设计 166
6.4.3在自动车床上进行成组加工 173
6.4.4特殊用途的车床 175
7.1.1铣刀的类型 178
7.1铣刀 178
第7章 铣削加工 178
7.1.2铣刀切削部分材料的选用 181
7.1.3铣刀直径及齿数的选择 182
7.1.4铣刀的几何角度及其选择 183
7.2铣床 186
7.2.1铣床的类型 186
7.2.2常用铣床的技术规格 187
7.3铣削工艺 191
7.3.1铣削方式 191
7.3.2铣削要素和切削层参数 193
7.3.3铣削力和铣削功率 199
7.3.4铣刀的磨损极限及耐用度 203
7.3.5提高铣削效率和质量的措施 207
7.3.6型面铣削 217
7.3.7分度头的使用 227
7.4精密机械刻划 232
7.4.1精密刻划刀具 232
7.4.2刻划设备 238
7.4.3刻划工艺 245
7.4.4刻度检验 248
第8章 钻削、镗削加工 256
8.1钻头、铰刀与镗刀 256
8.1.1麻花钻 256
8.1.2扩孔钻 266
8.1.3铰刀 267
8.1.4深孔钻 272
8.1.5镗刀 276
8.2钻床与镗床 280
8.2.1钻床 280
8.2.2镗床 284
8.3钻削、镗削 287
8.3.1钻孔 287
8.3.2铰削 301
8.3.3镗削 307
8.3.4电子工业常用材料的钻削、铰削和镗削 316
第9章 刨削、插削与拉削加工 324
9.1刨削加工 324
9.1.1加工范围与特点 324
9.1.2刨刀几何参数与刨削用量 324
9.1.3刨床 333
9.1.4工件的装夹 333
9.1.5精刨 335
9.1.6常用高效率刨刀 337
9.2插削加工 337
9.2.1插刀几何参数与插削用量 337
9.2.3工件的装夹 343
9.24矩形花键孔插刀 343
9.3拉削加工 345
9.3.1拉削特点与拉刀 345
9.3.2拉削余量与拉削方式 346
9.3.3拉刀切削部分的几何参数 348
9.3.4拉床 352
9.3.5拉削装置 353
9.3.6拉削工艺因素 353
9.3.7高速拉削 356
10.1外圆磨削 358
10.1.1外圆磨削方法 358
第10章 磨削加工 358
10.1.2磨削工艺参数 359
10.1.3外圆磨削实例 362
10.2内圆磨削 364
10.2.1内圆磨削方法 365
10.2.2内圆磨削工艺参数 366
10.2.3内圆磨削实例 366
10.3平面磨削 367
10.3.1平面磨削方法 368
10.3.2平面磨削工艺参数 369
10.3.3平面磨削实例 370
10.4无心磨削 370
10.4.1无心磨削方法 371
104.2无心磨削工艺参数 371
10.4.3无心磨削实例 374
10.5螺纹磨削 375
10.5.1螺纹磨削方法 375
10.5.2螺纹磨削工艺参数 377
10.5.3精密丝杠和滚珠丝杠的加工 378
10.6磨具、磨料与磨床 383
10.7常用难加工材料的磨削 395
10.7.1难加工材料的分类 395
10.7.2难加工材料磨削工艺特点 396
11.1.1研磨概述 401
第11章 表面精加工 401
11.1研磨 401
11.1.2研磨剂与研具 402
11.1.3研磨余量 408
11.1.4研磨方法 409
11.2抛光 411
11.2.1机械抛光 411
11.2.2液体抛光 412
11.2.3化学抛光 413
11.2.4电解抛光 414
11.3滚压 415
11.3.1滚压概述 415
11.4挤光 420
11.4.1挤光加工的精度与表面粗糙度 420
11.3.2表面滚压工具和滚压工艺 420
11.4.2挤光工具 421
11.5珩磨 424
11.5.1珩磨的工作原理和特点 424
11.5.2珩磨机床与珩磨头 425
11.5.3珩磨油石 426
11.5.4珩磨工艺参数 428
11.6超精加工 433
11.6.1超精加工的特点和应用 433
11.6.2超精加工工艺参数 434
11.6.3超精加工用油石的选择 435
11.6.4冷却润滑液 435
第12章 齿形加工 437
12.1常用齿形加工方法的分类及比较 437
12.2成形刀铣齿 438
12.3滚齿 438
9.2.2插床 442
12.4插齿 443
12.5剃齿 449
12.6磨齿 454
12.7刨齿 457
12.8螺旋锥齿轮加工 461
12.9珩齿、研齿和抛齿 464
第13章 钳工 469
13.1划线 469
13.2錾切 471
13.3锯割 471
13.4锉削 472
13.5弯曲 473
13.5.1毛坯长度的计算 473
13.5.2最小弯曲半径 476
13.6铆接 480
13.6.1铆钉和冲头 480
13.6.2铆钉直径、长度和钻孔直径 484
13.6.3铆接方法及工艺要求 485
13.7攻丝和套丝 486
13.7.1螺纹 486
13.7.2丝锥和绞杠 497
13.7.3攻丝方法 501
13.7.5套丝方法 504
13.7.4板牙和板牙架 504
13.8刮削 505
13.8.1刮削的作用及刮削余量 505
13.8.2刮刀 506
13.8.3显示剂和接触精度要求 508
13.8.4刮削方法 510
13.8.5刮削精度补偿 510
13.9装配工艺 511
13.9.1装配方法及组织形式 511
13.9.2装配过程中的钳工修配工作 512
13.9.3清洗 513
13.9.4平衡 518
13.9.5校正 521
13.9.6螺纹连接 526
13.9.7过盈连接 529
13.9.8典型部件的装配 531
第14章 切削加工自动化 544
14.1概述 544
14.2上料安装自动化 544
14.2.1上料装置的种类 545
14.2.2单件上料装置的组成 545
14.2.3料仓式上料装置 546
14.2.4自动定向料斗式上料装置 560
14.3单机自动化 565
14.3.1机床基本动作的机械化和自动化 565
14.3.2机床工作循环自动化 565
14.4切削加工的数字控制系统 570
14.4.1机床数字控制的通用标准 570
14.4.2数控装置 581
14.4.3数控机床的伺服系统 596
14.5计算机数字控制 599
14.5.1计算机数控系统 599
14.5.2微型单板计算机数控 601
14.6程序编制 606
14.6.1手工编程 606
14.6.2自动编程 610
14.6.3其他编程方法 623
第15章 精密测量 625
15.1概述 625
15.1.1测量的基本概念 625
15.1.2长度基准及尺寸传递系统 625
15.1.4测量误差及数据处理 626
15.1.3测量方法分类与基本度量指标 626
15.2.1游标量具及其主要指标 628
15.2通用量具量仪简介 628
15.2.2螺旋副量具及其主要指标 629
15.2.3通用机械式测微仪及其主要指标 631
15.2.4通用光学量仪 632
15.2.5三坐标测量机 635
15.3圆柱体测量 635
15.3.1圆柱体综合测量——量规法 635
15.3.2轴径的测量 638
15.3.3孔径的测量 639
15.4.1角度的通用基准——多面棱体及刻度盘 642
15.4.2角度和锥度的直接测量 642
15.4角度和锥度的测量 642
15.4.3角度或锥度的间接测量 644
15.5表面形状和位置误差的测量 646
15.5.1表面形状误差的测量 647
15.5.2表面位置误差的测量 653
15.6表面粗糙度的测量 656
15.6.1比较法 656
15.6.2光切法 657
15.6.3光波干涉法 657
15.6.4针描法 658
15.7螺纹测量 659
15.7.1螺纹量规 660
15.7.2外螺纹几何参数的测量 660
15.7.3内螺纹中径的测量 665
15.7.4丝杠的测量 666
15.8齿轮测量 667
15.8.1单面啮合综合测量 668
15.8.2双面啮合综合测量 669
15.8.3周节误差的测量 670
15.8.4齿圈径向跳动误差的测量 673
15.8.5公法线长度测量 674
15.8.6基节测量 674
15.8.7齿形测量 675
15.8.8齿厚偏差的测量 676
15.9新技术在精密测量中的应用 677
15.9.1光栅技术的应用 677
1.2.3脉冲电源 679
15.9.2激光技术的应用 679
15.9.3微机技术的应用 680
常用符号 683
第2篇 特种加工 689
概述 689
第1章 电火花成形加工 691
1.1电火花加工的原理、特点及分类 691
1.1.1电火花加工原理 691
1.1.2影响电蚀量的主要因素 692
1.1.3加工特点、应用范围及分类 694
1.2电火花成形加工机床 694
1.2.1电火花成形加工机床型号系列表示方法 694
1.2.2电火花成形加工机床的组成 696
1.3.1电火花成形加工的加工速度 700
1.3电火花成形加工的基本工艺规律 700
1.3.2电火花成形加工的电极相对损耗 702
1.3.3影响电火花成形加工精度的主要因素 706
1.3.4电火花加工的表面质量 709
1.4电火花穿孔加工工艺及应用 713
1.4.1电火花穿孔加工工艺 713
1.4.2电火花穿孔加工用工具电极 715
1.4.3电火花穿孔加工电规准的选择与转换 719
1.4.4排屑 720
1.4.5加工实例 720
1.5电火花型腔加工工艺及应用 722
1.5.1电火花型腔加工工艺 723
1.5.2电火花型腔加工用工具电极 725
1.5.3加工规准的选择、转换与平动量的分配 731
1.5.5加工实例 734
1.5.4排屑 734
第2章 电火花线切割加工 744
2.1电火花线切割加工的原理和特点 744
2.2电火花线切割加工机床 744
2.2.1电火花线切割加工机床的分类 744
2.2.2电火花线切割加工机床型号系列表示方法 745
2.2.3电火花线切割加工机床的主要部件 745
2.2.4机床本体 745
2.2.5工作液循环系统 755
2.2.6脉冲电源 756
2.2.7控制系统 761
2.2.8电火花线切割机床的使用条件 769
2.3.1电火花线切割加工工艺指标的评定 770
2.3电火花线切割加工的基本工艺规律 770
2.3.2工件材料与电极丝材料的基本特性 771
2.3.3工作液的种类及加工性能 773
2.3.4影响工艺指标的因素 773
2.4电火花线切割加工工艺及应用 783
2.4.1对工件图纸进行分析 783
2.4.2加工前的工艺准备 785
2.4.3工件的装夹与调整 785
2.4.4确定切割原则 789
2.4.5切割加工 790
2.4.6电火花线切割加工的工艺技巧 790
2.4.7电火花线切割加工的应用实例 796
2.5.1编程基本知识 801
2.5线切割机床数控程序编制 801
2.5.2CL六边形法 803
2.5.3PCPT线切割编程软件应用 812
2.5.4微型计算机在数控线切割编程中的应用 819
第3章 其他电火花加工 821
3.1电火花精密微细加工 821
3.1.1小孔电火花加工 821
3.1.2精密微细加工实例 837
3.2共轭回转式电火花加工 839
3.2.1共轭回转式电火花加工原理及应用范围 839
3.2.2共轭回转式电火花加工分类 840
3.3电火花磨削与电火花镗磨小孔 842
3.4.2电火花强化的物理化学过程 845
3.4.1电火花强化原理、作用及常用工具电极材料 845
3.4电火花强化 845
3.4.3电火花强化层特性及应用 846
3.4.4电火花强化的一般规律 847
3.4.5电火花强化设备及常用规范 849
3.5电火花刻字 851
3.6半导体材料及非导体材料的电火花加工 852
3.6.1半导体材料的电火花加工 852
3.6.2非导体材料的电火花加工 854
第4章 电化学加工 856
4.1电化学加工的原理、特点及分类 856
4.1.1电化学加工的基本原理 856
4.1.2加工特点、应用范围及分类 861
4.2.1电化学抛光设备 862
4.2电化学抛光 862
4.2.2电化学抛光的基本工艺规律 868
4.2.3电化学抛光工艺及应用 873
4.3电解加工 884
4.3.1电解加工设备 884
43.2电解加工的基本工艺规律 889
4.3.3电解加工工艺及应用 892
4.4电解磨削 906
4.4.1电解磨削设备 906
4.4.2电解磨削的基本工艺规律 907
4.4.3电解磨削工艺及应用 909
5.1超声加工的原理、特点及分类 913
5.1.1加工原理、特点及应用范围 913
第5章 超声加工 913
5.1.2超声加工的分类 914
5.2超声加工设备 914
5.2.1超声发生器 914
5.2.2声学部件 914
5.2.3设备本体 922
5.3超声加工的基本工艺规律 923
5.3.1超声加工的加工速度 923
5.3.2超声加工的加工精度 926
5.3.3超声加工的表面粗糙度 928
5.4超声加工的应用 928
5.4.1孔的超声加工 928
5.4.3超声抛光 929
5.4.2超声切断 929
5.4.4超声清洗 930
第6章 激光加工 932
6.1激光加工的原理和特点 932
6.1.1加工原理 932
6.1.2加工特点和应用范围 932
6.2激光加工设备 933
6.2.1激光器 933
6.2.2光学系统 939
6.2.3电气系统 940
6.2.4机械系统 942
6.3激光加工工艺及应用 942
6.3.1激光在材料加工上的应用 942
6.3.2激光在电子工业中的应用 951
- 《钒产业技术及应用》高峰,彭清静,华骏主编 2019
- 《现代水泥技术发展与应用论文集》天津水泥工业设计研究院有限公司编 2019
- 《异质性条件下技术创新最优市场结构研究 以中国高技术产业为例》千慧雄 2019
- 《Prometheus技术秘笈》百里燊 2019
- 《中央财政支持提升专业服务产业发展能力项目水利工程专业课程建设成果 设施农业工程技术》赵英编 2018
- 《药剂学实验操作技术》刘芳,高森主编 2019
- 《林下养蜂技术》罗文华,黄勇,刘佳霖主编 2017
- 《脱硝运行技术1000问》朱国宇编 2019
- 《催化剂制备过程技术》韩勇责任编辑;(中国)张继光 2019
- 《信息系统安全技术管理策略 信息安全经济学视角》赵柳榕著 2020