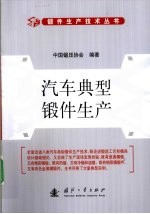
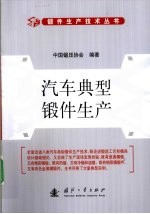
汽车典型锻件生产PDF电子书下载
- 电子书积分:13 积分如何计算积分?
- 作 者:赵一平主编
- 出 版 社:北京:国防工业出版社
- 出版年份:2009
- ISBN:9787118065503
- 页数:396 页
第一章 概论 1
1.1 概述 1
1.1.1 汽车工业拉动锻造行业快速发展 1
1.1.2 锻件在汽车上的分布 1
1.1.3 汽车锻件用原材料种类和生产准备 1
1.2 汽车锻件的锻造特点 3
1.2.1 生产的专业化、规模化 3
1.2.2 形状复杂,锻造工艺多样化 7
1.2.3 精度高,锻造成形精密化 8
1.2.4 组织性能要求高,材质和热处理技术不断提升 10
1.3 汽车典型锻件 10
1.3.1 锻件的分类 10
1.3.2 汽车典型锻件种类 11
1.3.3 汽车典型锻件工艺特性概述 11
1.4 汽车锻件的锻造工艺评估(综合分析) 15
1.4.1 工艺稳定,成形良好 15
1.4.2 工艺简单,劳动生产率高 15
1.4.3 材料利用率高 16
1.4.4 模具寿命高 16
1.5 汽车锻件生产技术的发展趋势 17
1.5.1 锻件组织性能要求不断提升 17
1.5.2 加速锻件生产的节能降耗 17
1.5.3 大力发展有色金属锻件 19
1.5.4 精密模锻技术持续快速发展 19
1.5.5 特种锻造技术保持良好发展势头 20
1.5.6 锻造新技术不断出现 21
1.5.7 锻模CAD/CAE/CAM一体化技术和锻模制造技术得到快速发展 21
第二章 曲轴类锻件生产技术 23
2.1 概述 23
2.1.1 曲轴铸改锻日趋明显 24
2.1.2 世界各国曲轴模锻件生产状况简述 24
2.1.3 曲轴模锻工艺流程 25
2.1.4 曲轴锻造生产线和自动生产线的设备组成 26
2.1.5 曲轴锻件的通用技术条件及曲轴锻坯技术协议 28
2.1.6 曲轴用原材料 30
2.2 曲轴模锻工艺 31
2.2.1 曲轴的分类 31
2.2.2 曲轴锻件图的制定 32
2.2.3 曲面分模曲轴分模面的走向 34
2.2.4 影响曲轴锻造工艺的主要因素 36
2.2.5 曲轴原材料规格选择和材料利用率 38
2.2.6 曲轴锻造生产工艺文件 39
2.3 曲轴模具的模膛设计和模具结构设计 41
2.3.1 终锻模膛设计 41
2.3.2 预锻模膛设计 42
2.3.3 切边模膛设计 44
2.3.4 热校正模膛设计 45
2.3.5 曲拐扭转模膛设计 45
2.3.6 弯曲模膛设计 47
2.3.7 三维造型设计曲轴模具 49
2.3.8 曲轴锻模的结构设计 51
2.3.9 曲轴模具使用寿命及模具材料 52
2.4 曲轴常见的锻造缺陷及其防止措施 55
2.4.1 充不满 55
2.4.2 折叠 57
2.4.3 变形 59
2.4.4 表面凹坑 62
2.5 曲轴锻件的热处理工艺及后续工序 63
2.5.1 曲轴锻件的热处理工艺 63
2.5.2 曲轴调质热处理生产作业规程 64
2.5.3 后续工序 65
2.6 曲轴模锻工艺及模具设计实例 65
2.6.1 QS四拐8平衡块平面分模曲轴工艺及模具设计 65
2.6.2 BPD六拐8平衡块曲面分模曲轴工艺及模具设计 74
参考文献 88
第三章 连杆类锻件生产技术 89
3.1 概述 89
3.2 连杆的分类 89
3.2.1 按材料分类 89
3.2.2 按结构分类 89
3.2.3 各类连杆的优缺点比较 90
3.3 连杆的原材料及其性能要求 90
3.4 连杆典型锻造工艺流程 92
3.4.1 连杆模锻件生产主要工艺方法 92
3.4.2 连杆典型完整锻造工艺流程 92
3.5 连杆锻造工艺及模具设计 100
3.5.1 锻件图的设计 100
3.5.2 锻造工艺方案确定 101
3.5.3 锻造成形力的计算 102
3.5.4 坯料的选择 103
3.5.5 模具设计 103
3.6 关键工序工艺技术要点及其分析与对策 110
3.6.1 辊锻工序工艺技术要点及其分析与对策 110
3.6.2 模锻工序工艺技术要点及其分析与对策 110
3.7 胀断连杆工艺介绍 111
3.7.1 胀断连杆材料及其性能要求 111
3.7.2 胀断连杆的加工特点 112
3.7.3 胀断连杆的锻造工艺特点 113
3.8 典型连杆模锻生产线配置 113
3.8.1 辊锻制坯—摩擦压力机模锻生产线配置 113
3.8.2 辊锻制坯—电液锤生产线 114
3.8.3 辊锻(楔横轧)制坯—机械压力机生产线 114
3.9 连杆锻件的质量控制 115
3.9.1 原材料的质量控制 115
3.9.2 下料工序的质量控制 115
3.9.3 中频感应加热的质量控制 115
3.9.4 锻造过程的质量控制 116
3.9.5 调质或控制冷却的质量控制 118
3.10 连杆锻件典型工艺的经济成本分析 119
参考文献 120
第四章 转向节锻件生产工艺 121
4.1 汽车构造对转向节的要求 121
4.2 转向节锻件结构类型与锻造工艺难度 122
4.2.1 转向节锻件形体要素描述 122
4.2.2 转向节锻件结构类型 122
4.2.3 转向节锻造的工艺难度 127
4.3 转向节锻件图设计中的几个问题 128
4.3.1 分模面 128
4.3.2 切削余量与余块 128
4.3.3 模锻斜度与过渡圆角 128
4.3.4 公差 129
4.3.5 技术要求 129
4.3.6 转向节锻件图实例 129
4.4 转向节锻件成形工艺 133
4.4.1 概述 133
4.4.2 转向节卧锻成形工艺 134
4.4.3 转向节立锻成形工艺 140
4.5 转向节锻模结构设计中的几个问题 153
4.5.1 分模面与锁扣 153
4.5.2 模膛布排 153
4.5.3 顶出机构设计 153
4.6 转向节锻造辅助工序与模具 155
4.6.1 切边与冲连皮 155
4.6.2 弯曲模设计 157
4.6.3 校正模设计 157
4.6.4 转向节锻件生产过程中的其他工序 157
4.7 典型转向节锻造生产线简介 158
参考文献 160
第五章 前轴类锻件生产工艺 162
5.1 概述 162
5.1.1 汽车前轴锻件的工艺特点 162
5.1.2 国外的前轴锻件生产技术的发展 162
5.1.3 国内前轴的生产工艺概况 164
5.2 前轴锤上模锻工艺 166
5.2.1 前轴锤上模锻工艺流程 166
5.2.2 前轴锤上模锻工艺设计 166
5.2.3 前轴的锤锻模设计 167
5.2.4 前轴切边模设计 169
5.2.5 前轴校正模设计 169
5.3 机械压力机上模锻前轴工艺与模具设计 169
5.3.1 机械压力机模锻工艺 169
5.3.2 终锻模膛及其模块设计 170
5.3.3 预锻模膛设计 171
5.3.4 弯曲模膛设计 171
5.3.5 机械压力机模锻前轴常见质量问题的解决方法 172
5.4 前轴成形辊锻工艺 173
5.4.1 前轴成形辊锻工艺流程 173
5.4.2 前轴成形辊锻的技术难点 174
5.4.3 前轴成形辊锻采取的技术措施 174
5.4.4 前轴成形辊锻工艺辊锻道次的确定 175
5.4.5 辊锻型槽的设计 176
5.4.6 各道次型槽纵向周期吻合问题 177
5.4.7 前滑计算及锻件长度控制 177
5.5 前轴精密辊锻—整体模锻工艺设计方法 178
5.5.1 主要工艺流程与工艺特点 178
5.5.2 前轴锻件的特点和热收缩率的选择 179
5.5.3 辊锻件图的确定 180
5.5.4 毛坯直径尺寸的选定 180
5.5.5 特征孔型设计 181
5.5.6 第3、2、1道辊锻件图设计 182
5.5.7 辊锻模具在辊锻机上的安装方式 183
5.5.8 精密辊锻前滑值的影响因素分析 184
5.5.9 辊锻模具图的设计 184
5.6 成形过程的数值模拟、物理模拟与工艺调试 184
5.6.1 有限元模型的建立 184
5.6.2 模拟结果及讨论 186
5.6.3 物理模拟的必要性 188
5.6.4 铅的物理性质及铅料的制作方法 188
5.6.5 用铅件代替热钢件进行模具调试的特点 189
5.6.6 工艺调试条件和过程 190
5.6.7 工艺调试中出现的问题与解决办法 191
5.7 前轴精密辊锻—整体模锻工艺应用示例 194
5.7.1 工艺流程的确定与设备选型 194
5.7.2 生产线设备平面布置图 196
5.7.3 生产线的建设情况、生产节拍和年生产能力 197
5.7.4 产品质量 197
5.7.5 节能节材效果和经济效益分析 198
参考文献 200
第六章 半轴类锻件生产技术 201
6.1 概述 201
6.1.1 顶镦的特点 201
6.1.2 半轴模锻工艺流程 201
6.1.3 半轴锻造生产线和锻造自动生产线的设备组成 202
6.1.4 半轴用原材料 204
6.2 顶镦(聚集)规则 204
6.2.1 圆棒料(坯料)的镦粗长度和镦粗比 204
6.2.2 自由顶镦规则 205
6.2.3 凹模内顶锻规则 205
6.2.4 凸模锥形模膛顶镦规则 206
6.2.5 电热镦粗 207
6.2.6 活动凹模顶镦制坯(聚料) 208
6.3 半轴顶镦工艺 208
6.3.1 半轴锻件图的制定 208
6.3.2 半轴顶镦力计算和平锻机规格选择 209
6.4 半轴模具的模膛及结构设计 210
6.4.1 凸模锥形顶镦模膛设计及模具结构设计 210
6.4.2 终锻模膛及模具结构设计 213
6.4.3 切边模膛设计及模具结构设计 215
6.4.4 平锻模具总体结构设计 217
6.5 MS后桥半轴顶镦工艺及模具设计 219
6.5. 1 锻件图设计 219
6.5.2 后桥半轴基本参数计算 219
6.5.3 半轴法兰盘工步图设计和计算 220
6.5.4 MS后桥半轴锻造压力计算及平锻机规格选择 221
6.5.5 半轴法兰盘平锻机顶镦模具设计(机械化模具) 222
第七章 齿轮类锻件生产工艺 224
7.1 概述 224
7.1.1 齿轮类锻件的分类 224
7.1.2 齿坯锻造工艺 224
7.1.3 齿轮精锻工艺 225
7.2 齿坯的开式模锻工艺 226
7.2.1 齿轮用钢材的锻造温度范围 226
7.2.2 齿轮坯开式模锻工艺 226
7.2.3 齿轮坯锤上模锻示例 227
7.2.4 齿轮坯机械压力机模锻工步示例 228
7.3 齿坯的闭式模锻工艺 228
7.3.1 齿坯闭式模锻工艺过程 228
7.3.2 预锻毛坯的形状和尺寸确定 229
7.3.3 齿坯闭式模锻的锻造力计算 231
7.3.4 齿坯闭式模锻设备选择 231
7.3.5 模具设计 232
7.4 齿坯的高速热镦锻技术 233
7.4.1 自动化高速热镦锻机生产线 233
7.4.2 高速热镦锻的工艺特点 234
7.4.3 高速热镦锻机工艺及模具结构 235
7.4.4 高速热镦锻齿坯的模锻工步 236
7.5 锥齿轮热精锻技术 237
7.5.1 直齿圆锥齿轮精锻工艺的适用性 237
7.5.2 热精锻直齿锥齿轮的精度标准 238
7.5.3 直齿锥齿轮热精锻工艺过程 241
7.5.4 直齿锥齿轮热精锻用模具 243
7.5.5 直齿锥齿轮热精锻设备 245
7.5.6 直齿锥齿轮粉末锻造工艺 247
7.5.7 螺旋锥齿轮的热精锻技术简介 248
7.6 锥齿轮的冷精锻技术 249
7.6.1 锥齿轮的闭塞冷锻技术 249
7.6.2 冷摆辗工艺 253
7.7 锥齿轮热锻(温锻)—冷锻复合成形技术 254
7.7.1 热锻—冷锻复合成形技术 254
7.7.2 热锻—冷锻复合成形技术概述 254
7.7.3 热锻—冷锻复合成形技术工艺过程与特点 255
7.7.4 热锻—冷锻复合成形技术其他应用 256
7.7.5 温锻—冷锻复合技术在国外的应用 258
7.7.6 温锻—冷锻复合技术在国内的应用现状 258
7.8 汽车同步器齿环的热精锻技术 260
7.8.1 汽车同步器齿环的工艺特点及其材质 260
7.8.2 同步器齿环工艺流程及锻件图的制定 260
7.8.3 同步器齿环的主要精度指标及其控制 260
7.8.4 同步器齿环锻造温度规范的选择及分析 261
7.8.5 模具结构及齿形设计 262
7.8.6 齿环精锻通用模架设计 263
7.9 直齿圆柱齿轮精锻技术 265
7.9.1 圆柱齿轮的挤压成形 265
7.9.2 汽车齿轮的分流锻造 266
参考文献 268
第八章 等速万向节锻件生产技术 269
8.1 概述 269
8.1.1 等速万向节在汽车传动中的作用 269
8.1.2 轿车等速万向节传动轴组成 269
8.1.3 等速万向节的类型及其结构 270
8.1.4 等速万向节锻件分类及材料 272
8.1.5 等速万向节锻造技术的发展和现状 274
8.2 等速万向节锻件生产技术 280
8.2.1 筒形壳和三柱槽壳的冷锻工艺 280
8.2.2 筒形壳和三柱槽壳的温—冷复合工艺 287
8.2.3 钟形壳的锻造工艺 299
8.2.4 星形套和三销架的闭塞冷锻工艺 308
8.3 等速万向节关键模具设计与制造 318
8.3.1 等速万向节壳体温锻模具设计与制造 318
8.3.2 等速万向节壳体冷精整模具设计与制造 327
8.3.3 星形套、三销架闭塞锻造模具设计与制造 330
8.4 等速万向节锻造用压力机 332
8.4.1 等速万向节温锻压力机 332
8.4.2 等速万向节热锻用压力机 337
8.4.3 等速万向节冷锻用压力机 338
8.5 等速万向节精密锻造今后发展 339
8.5.1 等速万向节壳体锻件倒角成形 339
8.5.2 控制冷却在温锻生产中的应用 340
8.5.3 钟形壳锻件高速热镦工艺 341
8.5.4 无磷化处理的冷精整工艺 342
参考文献 342
第九章 控制臂(悬臂)类铝锻件生产技术 343
9.1 概述 343
9.1.1 汽车轻量化促进汽车铝锻件生产的发展 343
9.1.2 铝及铝合金的分类 344
9.1.3 控制臂用6×××系铝合金的特点 345
9.1.4 铝锻件生产技术特点 347
9.1.5 控制臂在汽车上的部位和作用 347
9.2 控制臂的模锻工艺 349
9.2.1 控制臂的分类 349
9.2.2 铝合金锻件图的设计 353
9.2.3 流线设计与锻件质量 355
9.2.4 控制臂常用铝合金材料及其性能 358
9.2.5 影响控制臂锻造工艺的主要因素 358
9.3 控制臂铝合金锻件工艺流程和生产技术特点 359
9.3.1 工艺流程 359
9.3.2 坯料准备 360
9.3.3 加热 360
9.3.4 制坯 363
9.3.5 蚀洗与修伤 367
9.3.6 预锻 368
9.3.7 终锻 368
9.3.8 润滑 368
9.3.9 控制臂的切边、冲孔 369
9.3.10 控制臂铝合金锻件的热处理 369
9.3.11 矫正 370
9.3.12 铝合金锻件的质量检验 370
9.4 控制臂铝锻件模膛设计和模具结构 372
9.4.1 制坯 372
9.4.2 预锻模膛设计 372
9.4.3 终锻模设计 375
9.4.4 掏料模的设计 376
9.4.5 切边模与冲孔模设计 377
9.4.6 矫正模设计 378
9.4.7 锻模模架的设计 379
9.4.8 锻模使用寿命 381
9.5 锻造模具的材料 382
9.6 控制臂铝合金锻件的热处理 383
9.6.1 固溶温度 383
9.6.2 固溶加热方法及保温时间 383
9.6.3 固溶冷却 385
9.6.4 时效强化 385
9.6.5 铝合金锻造加热设备的技术要求 386
9.7 控制臂铝合金锻件常见缺陷与质量控制 388
9.7.1 锻件的常见主要缺陷 388
9.7.2 锻件的质量控制 391
9.8 控制臂模具设计实例 392
9.8.1 控制臂锻件的设计 392
9.8.2 控制臂锻模的设计 393
- 《危险化学品经营单位主要负责人和安全生产管理人员安全培训教材》李隆庭,徐一星主编 2012
- 《绿色过程工程与清洁生产技术 张懿院士论文集精选 上》《绿色过程工程与清洁生产技术》编写组编 2019
- 《润滑剂生产及应用》张远欣,王晓路主编 2012
- 《HSEQ与清洁生产》高峰编著 2019
- 《大气中典型二恶英类物质的氧化降解机理研究》张晨曦 2017
- 《洗涤剂生产工艺与技术》宋小平,韩长日主编 2019
- 《生活垃圾焚烧飞灰中典型污染物控制技术》朱芬芬等编著 2019
- 《典型地区居民汞、镉、砷、铅、铬环境总暴露研究报告》中国环境科学研究院著 2018
- 《皮革用化学品生产工艺与技术》宋小平,韩长日著 2018
- 《大众汽车维修资料全书 2008-2018款车型》瑞佩尔主编 2019
- 《断陷湖盆比较沉积学与油气储层》赵永胜等著 1996
- 《高考快速作文指导》张吉武,鲍志伸主编 2002
- 《建筑施工企业统计》杨淑芝主编 2008
- 《钒产业技术及应用》高峰,彭清静,华骏主编 2019
- 《近代旅游指南汇刊二编 16》王强主编 2017
- 《汉语词汇知识与习得研究》邢红兵主编 2019
- 《生物质甘油共气化制氢基础研究》赵丽霞 2019
- 《黄遵宪集 4》陈铮主编 2019
- 《孙诒让集 1》丁进主编 2016
- 《近代世界史文献丛编 19》王强主编 2017
- 《指向核心素养 北京十一学校名师教学设计 英语 七年级 上 配人教版》周志英总主编 2019
- 《北京生态环境保护》《北京环境保护丛书》编委会编著 2018
- 《指向核心素养 北京十一学校名师教学设计 英语 九年级 上 配人教版》周志英总主编 2019
- 《抗战三部曲 国防诗歌集》蒲风著 1937
- 《高等院校旅游专业系列教材 旅游企业岗位培训系列教材 新编北京导游英语》杨昆,鄢莉,谭明华 2019
- 《中国十大出版家》王震,贺越明著 1991
- 《近代民营出版机构的英语函授教育 以“商务、中华、开明”函授学校为个案 1915年-1946年版》丁伟 2017
- 《新工业时代 世界级工业家张毓强和他的“新石头记”》秦朔 2019
- 《智能制造高技能人才培养规划丛书 ABB工业机器人虚拟仿真教程》(中国)工控帮教研组 2019
- 《陶瓷工业节能减排技术丛书 陶瓷工业节能减排与污染综合治理》罗民华著 2017