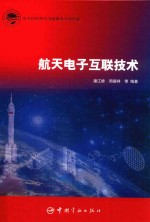
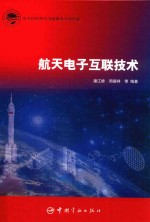
航天电子互联技术PDF电子书下载
- 电子书积分:13 积分如何计算积分?
- 作 者:潘江桥,周德祥编著
- 出 版 社:北京:中国宇航出版社
- 出版年份:2015
- ISBN:9787515910789
- 页数:361 页
第1章 概述 1
1.1 航天电子互联的概念 1
1.2 航天电子互联技术在航天制造技术领域的地位和作用 2
1.3 航天电子互联的发展简史 3
1.4 航天电子互联的技术展望 4
第2章 单片集成电路封装技术 7
2.1 概述 7
2.2 单片集成电路封装原材料 9
2.2.1 引线键合封装工艺原材料 10
2.2.2 CBGA/CCGA封装工艺原材料 12
2.2.3 倒装焊芯片封装工艺原材料 13
2.3 单芯片封装技术 14
2.3.1 内部互联 15
2.3.2 外部互联 23
2.4 集成电路封装设计 27
2.4.1 封装设计概述 27
2.4.2 封装设计内容 28
2.5 单片集成电路试验与检测 33
2.5.1 单片集成电路封装工艺过程检测 33
2.5.2 单片集成电路成品检验试验 38
2.5.3 单片集成电路可靠性验证 40
2.6 单片集成电路对电子产品装联的影响 45
2.6.1 集成电路内部互联材料对电装过程中焊接温度的要求 45
2.6.2 各种封装形式对电子产品装联的影响 46
2.7 典型故障 48
2.7.1 芯片粘接系统失效 48
2.7.2 互联系统失效 49
2.7.3 内部多余物引起的失效 53
2.7.4 电路封装的典型缺陷分析 54
2.8 航天特殊要求及禁忌 57
2.9 展望 57
2.9.1 面向高密度发展 57
2.9.2 面向系统级封装(SiP)技术的发展 57
2.9.3 从单芯片封装(Single Chip Package,SCP)向多芯片组件(MCM)发展 58
2.9.4 面向三维(Three Dimension,3D)微组装技术的发展 58
参考文献 59
第3章 混合集成电路互联技术 60
3.1 概述 60
3.2 混合集成电路封装原材料 60
3.2.1 基板材料 60
3.2.2 导体材料 62
3.2.3 介质材料 62
3.2.4 封装材料 63
3.3 混合集成电路基板制备技术 63
3.3.1 低/高温共烧陶瓷基板制备工艺 63
3.3.2 混合集成电路薄/厚膜制备工艺 65
3.4 混合集成电路的组装 69
3.4.1 混合集成电路的组装工艺流程 69
3.4.2 混合集成电路的组装工艺技术 69
3.4.3 多余物控制技术 71
3.4.4 混合集成电路水汽控制与检测 72
3.5 混合集成电路试验与检测 73
3.5.1 混合集成电路封装工艺在线检测 73
3.5.2 混合集成电路试验 74
3.6 典型故障 77
3.6.1 大腔体外壳平行缝焊漏气问题 77
3.6.2 电容立碑失效 78
3.7 混合集成电路对电子产品装联的影响 79
3.8 航天特殊要求及禁忌 79
3.9 展望 79
参考文献 81
第4章 微波组件组装技术 82
4.1 概述 82
4.2 微波组件主要材料 84
4.2.1 微波电路基板 84
4.2.2 微波组件壳体 87
4.2.3 微波组件载体基片 87
4.3 T/R组件组装技术 88
4.3.1 不含裸芯片的T/R组件组装技术 88
4.3.2 含裸芯片的T/R组件组装技术 91
4.4 T/R组件密封技术 97
4.4.1 胶粘剂密封 97
4.4.2 衬垫密封 98
4.4.3 玻璃金属封接 98
4.4.4 脉冲激光熔焊密封 100
4.5 T/R组件检测与测试 101
4.5.1 T/R组件发射电性能测试 101
4.5.2 T/R组件接收电性能测试 104
4.5.3 T/R组件自动测试系统 105
4.6 典型故障 106
4.6.1 案例1:耦合微带粘连 107
4.6.2 案例2:电容焊点断裂 107
4.6.3 案例3:尾丝不一致 108
4.7 航天特殊要求及禁忌 109
4.8 展望 109
参考文献 112
第5章 印制电路板制造技术 113
5.1 概述 113
5.2 基材 114
5.2.1 基材的选用 114
5.2.2 基材的分类 115
5.3 印制电路板制造工艺 118
5.3.1 典型工艺流程 118
5.3.2 主要工艺技术 119
5.4 印制电路板的检测 125
5.4.1 印制电路板的检测 125
5.4.2 印制电路板的试验 137
5.5 典型故障 143
5.5.1 案例1:印制电路板焊接后翘曲问题 143
5.5.2 案例2:印制电路板焊接后白斑问题 145
5.5.3 案例3:印制电路板过孔开路问题 146
5.6 印制电路板对电子产品装联的影响 147
5.6.1 设计工艺性对电装的影响 147
5.6.2 物理性能对电装的影响 148
5.6.3 化学性能对电装的影响 149
5.6.4 电气性能对电装的影响 149
5.6.5 玻璃化转变温度(Tg)对电装的影响 149
5.6.6 热膨胀系数(CTE)对电装的影响 150
5.7 航天特殊要求及禁忌 151
5.8 展望 152
参考文献 154
第6章 印制电路板组装件互联技术 155
6.1 概述 155
6.2 印制电路板组装件互联的通用要求 156
6.2.1 印制电路板 156
6.2.2 元器件要求 156
6.2.3 焊接材料 159
6.2.4 喷涂材料 161
6.2.5 粘固和灌封材料 161
6.2.6 环境要求 162
6.2.7 工具和设备要求 162
6.3 PCA组装前的预处理 162
6.3.1 镀金引线(焊端)除金 163
6.3.2 元器件搪锡 164
6.3.3 元器件引线成形 164
6.3.4 印制板预处理 165
6.3.5 元器件预烘 167
6.4 元器件安装 168
6.4.1 通孔插装技术(THT) 168
6.4.2 表面贴装技术(SMT) 169
6.4.3 混合安装技术(MMT) 172
6.5 焊接 172
6.5.1 软钎焊机理 172
6.5.2 焊接方法 175
6.5.3 典型元器件焊接 190
6.5.4 有铅无铅元器件混合焊接 192
6.6 清洗技术 195
6.6.1 印制电路板组装件污染物 195
6.6.2 清洗方法 196
6.6.3 清洗的质量控制 199
6.7 防护与加固 200
6.7.1 印制电路板组装件的防护涂覆 201
6.7.2 印制电路板组装件的加固 204
6.8 检测 211
6.8.1 元器件引线镀层检测 211
6.8.2 焊膏印刷质量检查 212
6.8.3 焊点缺陷检查 212
6.9 典型故障 215
6.9.1 案例1:焊点开裂 215
6.9.2 案例2:引线成形不足造成引线从本体处开裂 215
6.9.3 案例3:焊点虚焊 216
6.9.4 案例4:焊点桥连 217
6.9.5 案例5:印制板阻焊膜脱落 218
6.9.6 案例6:焊盘脱落 219
6.9.7 案例7:器件粘固不到位造成器件引线断裂 219
6.9.8 案例8:CBGA封装器件焊球与本体开裂 220
6.10 航天特殊要求及禁忌 221
6.10.1 焊接材料选用 221
6.10.2 端头处理工艺 222
6.10.3 引线成形工艺 222
6.10.4 元器件安装工艺 222
6.10.5 印制板组装件焊接工艺 223
6.10.6 清洗工艺 223
6.10.7 粘固工艺 223
6.10.8 印制板组装件修复与改装工艺 224
6.10.9 静电防护工艺 224
6.11 展望 224
6.11.1 导电胶互联技术 224
6.11.2 光电互联技术 225
6.11.3 微焊接技术 226
6.11.4 3D立体组装技术 226
参考文献 227
第7章 整机装联技术 228
7.1 概述 228
7.2 整机电气互联 228
7.2.1 星、箭载整机典型结构 229
7.2.2 地面整机结构 230
7.2.3 连接工艺 231
7.3 机械装配 253
7.3.1 星、箭载整机机械装配 253
7.3.2 地面机箱(柜)的机械装配 258
7.3.3 常用的安装紧固方式 261
7.4 整机防护与加固技术 271
7.4.1 产品的防护技术 271
7.4.2 整机产品的加固 273
7.5 检测 276
7.5.1 检测内容 277
7.5.2 检测环节 278
7.5.3 检测方法 278
7.5.4 重点检测项目 279
7.6 典型故障 279
7.6.1 案例1:减振器减振垫脱落问题 280
7.6.2 案例2:J7A型插座壳体锈蚀问题 280
7.6.3 案例3:某配电器印制板外引线压线导致绝缘下降问题 281
7.6.4 案例4:平台定位螺钉弯曲问题 281
7.6.5 案例5:灌胶工艺不细化造成三通接插件胶液不密实问题 282
7.6.6 案例6:某压力开关插座常开接触对不导通质量问题 283
7.7 航天特殊要求及禁忌 284
7.8 展望 284
参考文献 286
第8章 电子互联可靠性分析与验证 287
8.1 概述 287
8.2 电子产品工艺失效分析技术 288
8.2.1 失效分析的基本程序和方法 289
8.2.2 失效分析检测技术 292
8.3 电子产品筛选试验 294
8.3.1 振动试验 294
8.3.2 温度循环试验 300
8.3.3 老炼试验 305
8.4 可靠性验证试验 306
8.4.1 寿命试验 306
8.4.2 加速试验 311
8.4.3 环境试验 323
8.5 展望 333
参考文献 335
第9章 航天电子产品数字化制造技术 337
9.1 概述 337
9.2 航天电子产品数字化制造的主体构架 338
9.2.1 软件系统层 338
9.2.2 数据层 339
9.2.3 产品层 340
9.3 基于模型的数字化工艺 342
9.3.1 设计模型的转换 342
9.3.2 印制板模拟装配 343
9.3.3 整机模拟装配 344
9.3.4 线束模拟装配 346
9.4 数字化工艺仿真 346
9.4.1 SMT贴片仿真 346
9.4.2 集成电路焊接应力仿真 347
9.5 数字化制造模式 348
9.5.1 基于单元制造的车间制造执行系统 349
9.5.2 基于单元制造的MES作业执行管理 351
9.5.3 基于单元制造的MES质量管理 352
9.5.4 数据统计分析 353
9.6 展望 353
9.6.1 建立数字化协同模式 353
9.6.2 建立工艺知识专家系统 354
参考文献 355
附录 缩略语 356
- 《电子测量与仪器》人力资源和社会保障部教材办公室组织编写 2009
- 《钒产业技术及应用》高峰,彭清静,华骏主编 2019
- 《现代水泥技术发展与应用论文集》天津水泥工业设计研究院有限公司编 2019
- 《异质性条件下技术创新最优市场结构研究 以中国高技术产业为例》千慧雄 2019
- 《Prometheus技术秘笈》百里燊 2019
- 《少儿电子琴入门教程 双色图解版》灌木文化 2019
- 《中央财政支持提升专业服务产业发展能力项目水利工程专业课程建设成果 设施农业工程技术》赵英编 2018
- 《药剂学实验操作技术》刘芳,高森主编 2019
- 《林下养蜂技术》罗文华,黄勇,刘佳霖主编 2017
- 《脱硝运行技术1000问》朱国宇编 2019
- 《市政工程基础》杨岚编著 2009
- 《家畜百宝 猪、牛、羊、鸡的综合利用》山西省商业厅组织技术处编著 1959
- 《《道德经》200句》崇贤书院编著 2018
- 《高级英语阅读与听说教程》刘秀梅编著 2019
- 《计算机网络与通信基础》谢雨飞,田启川编著 2019
- 《海明威书信集:1917-1961 下》(美)海明威(Ernest Hemingway)著;潘小松译 2019
- 《看图自学吉他弹唱教程》陈飞编著 2019
- 《法语词汇认知联想记忆法》刘莲编著 2020
- 《培智学校义务教育实验教科书教师教学用书 生活适应 二年级 上》人民教育出版社,课程教材研究所,特殊教育课程教材研究中心编著 2019
- 《国家社科基金项目申报规范 技巧与案例 第3版 2020》文传浩,夏宇编著 2019
- 《中国当代乡土小说文库 本乡本土》(中国)刘玉堂 2019
- 《异质性条件下技术创新最优市场结构研究 以中国高技术产业为例》千慧雄 2019
- 《中国铁路人 第三届现实主义网络文学征文大赛一等奖》恒传录著 2019
- 《莼江曲谱 2 中国昆曲博物馆藏稀见昆剧手抄曲谱汇编之一》郭腊梅主编;孙伊婷副主编;孙文明,孙伊婷编委;中国昆曲博物馆编 2018
- 《中国制造业绿色供应链发展研究报告》中国电子信息产业发展研究院 2019
- 《中国陈设艺术史》赵囡囡著 2019
- 《指向核心素养 北京十一学校名师教学设计 英语 七年级 上 配人教版》周志英总主编 2019
- 《《走近科学》精选丛书 中国UFO悬案调查》郭之文 2019
- 《清至民国中国西北戏剧经典唱段汇辑 第8卷》孔令纪 2018
- 《北京生态环境保护》《北京环境保护丛书》编委会编著 2018