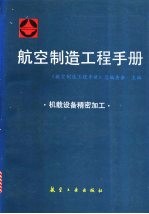
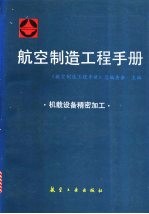
航空制造工程手册 机载设备精密加工PDF电子书下载
- 电子书积分:21 积分如何计算积分?
- 作 者:《航空制造工程手册》总编委会主编
- 出 版 社:北京:航空工业出版社
- 出版年份:1996
- ISBN:7800469522
- 页数:791 页
目 录 2
第1章精密车削 2
1.1精密车削设备及设备改造 2
1.1.1精密及高精度车床的工作精度 2
1.1.2车床精度对加工质量的影响 3
1.1.3普通车床的精化及改装 4
1.1.3.1普通车床的精化 4
1.1.3.2普通车床的改装 4
1.2精密车削刀具材料及刃磨 5
1.2.1精密车削刀具材料的应用 5
1.2.1.1精密车削刀具的切削性能要求 5
1.2.1.2刀具材料的主要机械、物理性能 6
1.2.1.3 刀具材料的使用性能及推荐用途 6
1.2.2.1高速钢刀具的刃磨 12
1.2.2刀具材料的刃磨 12
1.2.2.2硬质合金刀具的刃磨 14
1.2.2.3陶瓷材料刀具的刃磨 15
1.2.2.4超硬材料刀具的刃磨或研磨 16
1.3工件材料的切削加工性 19
1.3.1切削加工性概念及影响因素 19
1.3.1.1切削加工性的主要衡量方法 19
1.3.1.2刀具耐用度作加工性衡量指标 20
1.3.1.3材料性能作加工性衡量指标 20
1.3.2难切材料的切削加工性 21
1.3.2.1常用的难切材料 21
1.3.2.2难切材料的加工特点 22
1.3.2.3难切材料的切削加工性指标 23
1.3.2.4切削加工性的主要改善途径 23
1.3.3.1高速钢刀具材料的选用 24
1.3.3难切材料加工用的刀具材料选择 24
1.3.3.2硬质合金刀具材料的选用 25
1.3.3.3其他刀具材料的选用 25
1.3.4切削液的应用 25
1.3.4.1切削液的作用 25
1.3.4.2切削液的润滑作用及添加剂 26
1.3.4.3切削液中的其他添加剂 26
1.3.4.4切削液的分类 27
1.3.4.5常用切削液配方及选用 27
1.4外圆和端面精密车削 29
1.4.1车削的加工特点 29
1.4.2工件的装夹 30
1.4.2.1工件装夹的主要方式 30
1.4.3 外圆及端面精密车削的切削方式 31
1.4.2.2装夹方式对加工精度的影响 31
1.4.3.1高速及低速精密车削 32
1.4.3.2 采用滚压和挤压降低表面粗糙度 33
1.4.3.3大刃倾角车刀的切削加工 33
1.4.4外圆及端面车削刀具和几何角度 33
1.4.4.1车刀的结构 33
1.4.4.2 刀杆形状及尺寸 34
1.4.4.3硬质合金焊接车刀刀片及刀杆槽形 35
1.4.4.4硬质合金焊接车刀的镶焊 38
1.4.4.5硬质合金机夹重磨车刀的夹固形式 40
1.4.4.6硬质合金可转位车刀 41
1.4.4.7 硬质合金可转位车刀刀片 44
1.4.4.8陶瓷车刀刀片 51
1.4.4.9复合聚晶立方氮化硼刀片 51
1.4.4.10外圆及端面车削用车刀的几何角度 53
1.4.5.1 切削用量的选择原则和影响因素 58
1.4.5切削用量选择 58
1.4.5.2高速钢刀具的切削用量 59
1.4.5.3硬质合金刀具的切削用量 59
1.4.5.4其他材料刀具的切削用量 60
1.4.6加工中容易产生的问题及改善措施 61
1.4.6.1 加工精度误差及改善措施 61
1.4.6.2加工表面质量缺陷及改善措施 61
1.4.7加工实例 62
1.4.7.1 分油盘端面的精密车削 62
1.4.7.2弹簧管外圆的精密车削 63
1.5孔的精密车削 64
1.5.1精密孔的车削加工特点 65
1.5.1.1 精密孔车削用的刀具特点 65
1.5.2.1 钻孔工艺及应用范围 66
1.5.2钻孔及钻孔刀具 66
1.5.1.2精密孔车削的工艺特点 66
1.5.2.2钻孔刀具 68
1.5.2.3钻孔切削用量 73
1.5.2.4常见缺陷及改进措施 74
1.5.3车孔及车孔刀具 75
1.5.3.1 车孔工艺及应用范围 75
1.5.3.2内孔车刀结构 76
1.5.3.3 内孔车削的切削用量 77
1.5.4铰孔及铰孔刀具 77
1.5.4.1铰孔工艺及应用范围 77
1.5.4.2铰孔切削刀具及几何角度 78
1.5.4.3铰孔切削用量 84
1.5.4.4提高铰削质量的措施 85
1.5.5加工实例 86
1.5.5.1外筒衬套孔的精密车削 86
1.5.5.2线圈架孔的精密车削 87
1.5.5.3转子柱塞孔的精密车削 88
1.6球面的精密车削 89
1.6.1球面精密车削的加工特点 89
1.6.2球面车削的切削方法 91
1.6.2.1外球面的加工方法 91
1.6.2.2内球面的加工方法 92
1.6.3容易产生的缺陷及改善措施 92
1.6.3.1筒形刀加工外球面 92
1.6.3.2飞刀铣削外球面 93
1.6.3.3回转刀架加工外球面 94
1.6.3.4成形车刀加工内、外球面 94
1.6.3.5球面铰刀加工内球面 94
1.6.3.6单片铰刀加工内球面 95
1.6.4.1 电液伺服阀反馈杆小球面加工 96
1.6.4加工实例 96
1.6.4.2柱塞泵柱塞体外球面车削 97
1.6.4.3柱塞座内球面精密车削 97
1.7螺纹车削 98
1.7.1螺纹车削的加工特点 98
1.7.2螺纹车削的切削方法 99
1.7.2.1螺纹车削的分类 99
1.7.2.2普通螺纹车削进刀方法 100
1.7.2.3梯形及蜗杆螺纹的切削方法 100
1.7.2.4圆锥螺纹的切削方法 101
1.7.2.5 多头螺纹加工 101
1.7.2.6螺纹的旋风切削法 102
1.7.2.7 内螺纹的拉削加工 103
1.7.3螺纹车削刀具 103
1.7.3.1 螺纹车刀和螺纹梳刀 103
1.7.3.2 圆板牙 106
1.7.3.3 丝锥 107
1.7.4.1 螺纹车刀车削螺纹的切削用量 111
1.7.4螺纹加工的切削用量 111
1.7.4.2旋风切削螺纹的切削用量 112
1.7.4.3丝锥加工的切削速度 112
1.7.4.4圆板牙加工的切削速度 113
1.7.5螺纹加工容易产生的缺陷和改进措施 113
1.7.5.1螺纹车削 113
1.7.5.2丝锥及圆板牙加工螺纹 114
1.7.6拉削丝锥的加工实例 115
1.8内、外槽的精密车削 117
1.8.1加工特点 117
1.8.2 内、外槽车削的加工工艺 118
1.8.3精密车削内、外槽的刀具及几何角度 119
1.8.3.1 车削外槽用的刀具 119
1.8.3.3车削端面槽用的刀具 120
1.8.3.2车削内槽用的刀具 120
1.8.4内、外槽加工的切削用量 121
1.8.5 加工中容易产生的缺陷及改进措施 121
1.8.6加工实例 122
1.8.6.1外筒衬套内、外槽的精车 122
1.8.6.2线圈架端面密封槽的加工 123
1.9回转曲面的精密车削 124
1.9.1 回转曲面车削的切削方法 124
1.9.2成形车削 124
1.9.2.1 成形车削的切削方法及应用范围 124
1.9.2.2径向进给成形车削用的刀具 125
1.9.3仿形车削 127
1.9.3.1仿形车床 127
1.9.3.2车床的仿形附件 128
1.9.3.3仿形靠模的设计及要求 131
1.9.4.1数控车削的特点 135
1.9.4.2数控车削的编程步骤 135
1.9.4回转曲面的数控车削 135
1.9.4.3直线和圆弧组成旋转母线的编程 136
1.9.4.4可描述非圆曲线旋转母线的编程 137
1.9.4.5 列表曲线旋转母线的编程 137
1.9.4.6提高加工质量的途径 139
1.10精密单轴纵切自动车床加工 139
1.10.1航空仪表轴类零件及加工设备简介 139
1.10.2凸轮纵切自动车床加工 142
1.10.2.1 加工工艺过程优化设计原则 142
1.10.2.2凸轮的设计 152
1.10.2.3凸轮制造 163
1.10.2.4凸轮纵切自动车床的加工精度 164
1.10.3.1简介及加工原理 170
1.10.3数控纵切自动车床 170
1.10.3.2加工特点及加工精度分析 173
1.11超精密车削 175
1.11.1超精密车削的特点与应用 175
1.11.2超精密车削用的刀具 176
1.11.2.1超精密车削对刀具的要求 176
1.11.2.2天然金刚石刀具的特性 176
1.11.2.3天然金刚石刀具的设计和制造 177
1.11.2.4金刚石刀具适用的被加工材料 178
1.11.2.5超精密车削用的其他刀具材料 178
1.11.3超精密车床 178
1.11.3.1对超精密车床的主要要求 179
1.11.3.2超精密车床的关键部件 179
1.11.3.3超精密车床的驱动 180
1.11.4.2环境的温、湿度控制 181
1.11.4.1环境的空气净化 181
1.11.4超精密车削的环境要求 181
1.11.4.3环境的隔振与减振 182
1.11.4.4环境的其他条件要求 182
1.11.5 超精密车削的工艺特点 182
1.11.5.1车削时刀具磨损与工件表面质量 182
1.11.5.2车削时的积屑瘤 183
1.11.5.3其他切削参数对表面质量的影响 183
1.11.6超精密车削的发展 185
1.11.6.1超精密车削的发展趋势 185
1.11.6.2超精密车削的新课题 185
2.1.1 精密磨削表面的形成 186
2.1.1.1 精密磨削表面形成的特点 186
2.1.1.2影响磨削质量的主要因素 186
第2章精密磨削 186
2.1外圆精密磨削 186
2.1.2砂轮的选择 187
2.1.2.1砂轮特性及一般选择原则 187
2.1.2.2精密磨削砂轮的选择 190
2.1.3.1 砂轮静平衡的方法及注意事项 191
2.1.3.2砂轮的动态平衡原理及装置 191
2.1.3砂轮的平衡 191
2.1.2.3超硬磨料砂轮及其应用 191
2.1.4砂轮的修整 193
2.1.4.1修整工具 193
2.1.4.2修整用量的选择 194
2.1.5磨削用量的选择 194
2.1.6外圆精密磨削的工艺参数 195
2.1.7切削液选择及净化 195
2.1.7.1 切削液的选择及使用注意事项 195
2.1.8.3减少机床振动 197
2.1.8.2工作台低速运动的平稳性 197
2.1.7.2切削液的净化 197
2.1.8对机床的要求 197
2.1.8.1磨床的精度要求 197
2.1.9外圆精密磨削的中心孔要求 198
2.1.10表面缺陷和防止措施 198
2.1.11加工实例 200
2.2内圆精密磨削 201
2.2.1内圆磨头 202
2.2.1.1 内圆磨头的主要类型 202
2.2.1.2机械传动及电动磨头的调整和润滑 203
2.2.1.3 内圆磨头的使用注意事项 204
2.2.1.4 内圆磨头的技术改造 204
2.2.2砂轮杆 205
2.2.2.1砂轮杆的形式及增强措施 205
2.2.2.3精密内磨深孔用砂轮杆 207
2.2.2.2 磨削小孔时砂轮杆部直径的选择 207
2.2.3精密内磨用的砂轮 208
2.2.3.1砂轮特性的选择 208
2.2.3.2 砂轮直径及宽度的选择 208
2.2.4工件的装夹 209
2.2.5精密内磨削工艺参数的选 210
择 210
2.2.6常见的磨削缺陷及防止措施 210
2.2.7精密内磨削实例 211
2.2.7.1 阀套超深孔的精密磨削 211
2.2.7.2轴承外圈孔的精密磨削 212
2.3平面精密磨削 215
2.3.1平面精密磨削的特点 215
2.3.3工件的装夹 216
2.3.2.2工艺参数的选择 216
2.3.3.1采用电磁吸盘装夹工件 216
2.3.2.1磨削用量的选择原则 216
2.3.2 磨削用量的选择 216
2.3.3.2采用其他方法装夹工件 217
2.3.4平面精密磨削对机床的要求 218
2.3.5容易产生的缺陷和防止措施 218
2.3.5.1 一般工件易产生的缺陷和防止措施 218
2.3.5.2精密磨削薄片工件产生的变形和挠曲 219
2.3.6加工实例 219
2.4精密螺纹磨削 220
2.4.1精密螺纹磨削的加工方式、加工特点及其应用 221
2.4.2砂轮的使用 222
2.4.2.1砂轮特性的选择 222
2.4.2.3砂轮的修整 223
2.4.2.2砂轮的平衡及安装 223
2.4.3磨削用量的选择 224
2.4.4精密螺纹磨削时切削液的选择 225
2.4.5滚珠丝杠圆弧形螺纹磨削 225
2.4.5.1滚珠丝杠的主要要求 225
2.4.5.2砂轮圆弧的修整及修整夹具 226
2.4.6精密螺纹磨削的加工注意事项 228
2.4.6.1螺纹磨床的使用要求 228
2.4.6.2螺纹磨削时机床的调整要求 228
2.4.6.3磨削加工时的注意事项 229
2.4.7螺纹磨削时的常见缺陷及防止措施 229
2.4.8加工举例 230
2.5精密无心外圆磨削 230
2.5.1精密无心外圆磨削的加工方式 231
2.5.3精密无心外圆磨削的调整 233
2.5.3.1调整参数的选择 233
2.5.2砂轮的选择 233
2.5.3.2机床的调整 234
2.5.4 精密无心外圆磨削工艺参数的选择 235
2.5.4.1通磨工艺参数的选择 235
2.5.4.2 切入磨削工艺参数的选择 237
2.5.4.3其他工艺参数选择 238
2.5.5 磨削容易出现的缺陷及防止措施 238
2.6坐标磨削 239
2.6.1 坐标磨削的加工方式及加工要点 240
2.6.1.1 坐标磨削的加工方式 240
2.6.1.2 坐标磨削的加工要点 241
2.6.2数控坐标磨床的磨削方式 242
2.6.3砂轮规格及磨料与转速的关系 243
2.6.3.1 普通直径砂轮转速的选择 243
2.6.3.2小直径砂轮转速的选择 243
2.6.4数控坐标磨床磨削实例 244
2.7光学曲线磨削 245
2.7.1 光学曲线磨削的加工工艺 245
2.7.1.1光学曲线磨削的加工方式 245
2.7.1.2光学曲线磨削的磨削运动 246
2.7.1.3 内角与圆弧型面的磨削方法 246
2.7.2砂轮形状及磨削用量的选择 248
2.7.2.1常用砂轮形状及修整 248
2.7.2.2磨削用量的选择 249
2.7.3效控光学曲线磨削 249
2.7.4光学曲线磨削的放大图 250
2.7.5数控光学曲线磨床的磨削实例 251
2.8环形沟槽的磨削 253
2.8.1环形沟槽的磨削特点 253
2.8.2环形沟槽磨削用砂轮的修整 254
2.8.2.1砂轮的修整方法 254
2.8.2.2金属滚轮滚压修整成形砂轮 255
2.8.2.3金刚石滚轮修整成形砂轮 256
2.9缓进磨削 257
2.9.1缓进磨削的工艺特征及使用特点 257
2.9.1.1缓进磨削的工艺特征 257
2.9.1.2缓进磨削的使用特点 257
2.9.2缓进磨削对机床的要求 258
2.9.3缓进磨削砂轮的选择及修整 259
2.9.3.1缓进磨削对砂轮的要求 259
2.9.3.2缓进磨削砂轮的选择要点 259
2.9.3.3缓进磨削砂轮的修整 260
2.9.4缓进磨削的切削液及使用要求 261
2.9.4.1切削液的选用 261
2.9.4.2切削液的供给方式 261
2.9.6缓进磨削的工艺设计 262
2.9.6.1缓进磨削工艺的选择要点 262
2.9.5.1缓进磨削的应用范围 262
2.9.5.2缓进磨削的生产效率 262
2.9.5缓进磨削的应用范围和生产效率 262
2.9.6.2连续修整的缓进磨削 263
2.10径向和轴向配磨技术 263
2.10.1径向和轴向配磨的应用及精度 264
2.10.1.1径向和轴向配磨的应用范围 264
2.10.1.2径向和轴向精密配磨的加工精度 264
2.10.2径向和轴向配磨用的配磨磨床 265
2.10.3径向配磨的工作原理和配磨装置 266
2.10.3.1普通径向配磨的工作步骤 266
2.10.3.2径向自动配磨的工作原理 267
2.10.3.3径向自动配磨装置 268
2.10.4轴向配磨的工作原理和配磨装置 268
2.10.4.1轴向配磨的工作要求 268
2.10.4.2轴向配磨的测试 269
2.10.4.3轴向配磨的加工原理 271
2.10.4.4轴向配磨装置 273
2.10.5径向和轴向配磨的工艺要求 274
第3章精密珩磨 275
3.1珩磨加工的特点和原理 275
3.1.1珩磨加工的特点 275
3.1.2珩磨加工的基本原理 275
3.1.2.1强制式珩磨 276
3.1.2.2自由式珩磨 276
3.1.3珩磨的切削过程 277
3.1.3.1定压进给的珩磨过程 277
3.1.3.2定量进给的珩磨过程 277
3.2.2 内孔珩磨机的运动形式及进给方式 278
3.2.2.2 内孔珩磨机的进给方式 278
3.2.2.1 内孔珩磨机的运动形式 278
3.2.1珩磨机的类型 278
3.2珩磨机的类型及其应用 278
3.1.3.3定压-定量进给的珩磨过程 278
3.2.3珩磨机的选择 280
3.2.3.1珩磨机的选择原则 280
3.2.3.2国产小型珩磨机简介 281
3.3珩磨工具 281
3.3.1珩磨头 281
3.3.1.1 珩磨头的种类及结构形式 281
3.3.1.2通孔珩磨头的设计 285
3.3.2主轴接头及珩磨夹具 287
3.3.2.1主轴接头的结构 287
3.3.2.2珩磨夹具的结构 289
3.3.3珩磨头与珩磨工具的配置 289
3.4.1珩磨油石的特性及选择 290
3.4.1.1磨料的选择 290
3.4珩磨油石 290
3.4.1.2磨料粒度的选择 291
3.4.1.3珩磨油石硬度的选择 292
3.4.1.4珩磨油石结合剂的选择 292
3.4.1.5珩磨油石的组织和浓度选择 293
3.4.2珩磨油石的结构及制备 293
3.4.2.1珩磨油石的构造 293
3.4.2.2分体式珩磨油石的连接 294
3.4.2.3珩磨油石的修正 294
3.4.3超硬磨料珩磨油石的应用 295
3.4.3.1 人造金刚石珩磨油石的应用 295
3.4.3.2立方氮化硼珩磨油石的应用 296
3.5通孔珩磨工艺 296
3.5.2珩磨切削参数的选择 297
3.5.2.1珩磨的切削速度与交叉角 297
3.5.1.1珩磨余量的确定 297
3.5.1.2珩磨前尺寸的分组 297
3.5.1珩磨余量及尺寸分组 297
3.5.2.2珩磨切削参数对加工的影响 298
3.5.2.3珩磨压力的选择 299
3.5.3珩磨行程和越程量的调整 299
3.5.4特殊工件的珩磨 300
3.5.5通孔珩磨加工的注意事项 301
3.5.6珩磨切削液 301
3.5.6.1珩磨切削液的功用及使用要求 301
3.5.6.2珩磨切削液的选择及应用 302
3.5.7珩磨的尺寸控制 302
3.5.8通孔珩磨常见缺陷和消除措施 303
3.6.1.1油石在两端孔口的越程量不等 304
3.6盲孔珩磨工艺 304
3.6.1盲孔珩磨存在的主要技术关键 304
3.6.1.2油石的磨耗不均匀 305
3.6.1.3润滑条件差 305
3.6.2实现盲孔珩磨加工的途径 305
3.6.2.1改进珩磨机的结构 305
3.6.2.2改进油石结构 305
3.6.2.3改进珩磨工具的结构 305
3.7平面珩磨工艺 306
3.7.1平面珩磨的分类及加工原理 307
3.7.1.1双面平面珩磨 307
3.7.2.1双面平面珩磨的应用 308
3.7.3珩磨盘的要求及选择 308
3.7.2.2单面平面珩磨的应用 308
3.7.2平面珩磨的应用范围 308
3.7.1.2单面平面珩磨 308
3.7.4珩磨盘的修正 309
3.7.4.1金刚石笔修正法 309
3.7.4.2上、下珩磨盘对珩法 310
3.7.5工件在平面珩磨时的运动轨迹 310
3.7.5.1工件运动轨迹的确定原则 310
3.7.5.2平面珩磨传动装置的结构分类 311
3.7.5.3平面珩磨的运动轨迹及工作原理 311
3.7.6珩磨工艺参数的选择 313
3.7.6.1珩磨速度的选择 313
3.7.6.2偏心轴的偏心量选择 314
3.7.7平面珩磨的常见缺陷和解决措施 314
3.8珩磨加工技术的发展 315
3.8.2珩磨加工工艺的发展 316
3.8.1.3珩磨工艺加工效率的提高 316
3.8.2.2平顶珩磨工艺 316
3.8.2.1强力珩磨工艺 316
3.8.1.2珩磨工艺加工精度的提高 316
3.8.1.1珩磨工艺加工范围的扩大 316
3.8.1珩磨工艺加工效果的提高 316
3.8.2.3盲孔珩磨工艺 317
3.8.2.4顺序单行程珩磨工艺 317
3.8.3发展新型的超硬磨料 317
3.8.4发展新型的珩磨机床 318
3.8.5发展珩磨机床的自动测量和数控技术 318
第4章研磨 320
4.1研磨工作原理及特点 320
4.1.1研磨工作原理 320
4.1.1.1研磨分类及适用范围 320
4.1.1.2研磨机理 321
4.1.1.3研磨精度的形成原理 321
4.1.2.2研磨精度水平 322
4.1.2.1研磨特点 322
4.1.2研磨特点及精度水平 322
4.2研磨剂 323
4.2.1研磨剂的成分 323
4.2.1.1磨料及其选择 323
4.2.1.2附加液的选择 323
4.2.1.3辅助材料的种类 324
4.2.2研磨剂的配制 324
4.2.2.1研磨膏的配制 324
4.2.2.2研磨液的配制 326
4.2.2.3固体研磨剂的配制 327
4.3研具 327
4.3.1研具的作用及要求 327
4.3.2研具材料的选择及使用实例 328
4.3.2.1研具材料的种类及适用范围 328
4.3.3.1外圆柱面研磨器 329
4.3.3. 研具的设计 329
4.3.2.2铸铁研磨平板实例 329
4.3.3.2内圆柱面研磨器 331
4.3.3.3平面研磨用研磨平板 334
4.4研磨设备 335
4.4.1双盘研磨机 335
4.4.2外圆研磨机 335
4.4.3立式内、外圆研磨机 336
4.5圆柱面研磨工艺 336
4.5.1外圆柱面研磨工艺 336
4.5.1.1 工件结构形式及操作方法的选择 337
4.5.1.2外圆柱面的半机械研磨 338
4.5.1.3外圆柱面的机械研磨 340
4.5.2内孔研磨工艺 345
4.5.2.1 内孔的结构形式 345
4.5.2.2通孔研磨的工艺特点 346
4.5.2.3小孔研磨的工艺特点 347
4.5.2.4锥孔研磨的工艺特点 348
4.5.2.5盲孔研磨的工艺特点 348
4.5.2.6中心孔研磨的工艺特点 348
4.6平面研磨工艺 349
4.6.1平面的结构形式及操作方法的 349
选择 349
4.6.2 平面的手工研磨 350
4.6.2.1研磨平板的研磨及修整 351
4.6.2.2平面手工研磨的操作 352
4.6.3平面的机械研磨 352
4.6.4平面的振动研磨 353
4.6.4.1振动研磨机 353
4.6.4.2研磨用量 354
4.6.4.3常见故障及排除方法 354
4.7.2.2球面研磨的方法及应用 355
4.7.2球面研磨的加工方式 355
4.7.2.1球面研磨的工作运动 355
4.7球面研磨 355
4.7.1球面研磨的工艺特点 355
4.7.3球面研磨的研具 356
4.7.3.1圆筒形研具的设计 356
4.7.3.2圆柱形研具的设计 358
4.7.3.3成对研具的使用 358
4.7.3.4成形法研磨内球面的研具 358
4.7.3.5球面研具的材料选用 359
4.7.4球面研磨的精度和表面粗糙度 359
4.7.4.1研磨剂配方与表面粗糙度 359
4.7.4.2加工精度的影响因素 359
4.7.5.1柱塞体外球面的研磨 360
4.7.5.2柱塞座内球面的抛光 360
4.7.5加工实例 360
4.7.5.3柱塞体内球面的研磨 361
4.7.5.4颊板外球面的研磨 362
4.7.5.5端盖及圈偶件的研磨 362
4.7.5.6柱塞垫内球面的研磨 363
4.7.5.7柱塞头外球面的研磨 363
4.7.5.8反馈杆小球面的研磨 364
4.8硬质合金工件的研磨工艺 365
4.8.1圆柱面的研磨工艺 365
4.8.2平面研磨工艺 366
4.9研磨的常见故障及排除方法 367
4.9.1半干及湿研磨的常见故障及排除方法 367
4.9.2干研磨的常见故障及排除方法 369
4.10.2机械化学研磨法 370
4.10.2.1湿式机械化学研磨法 370
4.10.1超精密研磨的特点及应用 370
4.10超精密研磨工艺 370
4.10.2.2干式机械化学研磨法 371
4.10.3非接触研磨法 371
4.10.4磁力研磨法 372
4.10.4.1 利用磁性流体的磁力研磨 372
4.10.4.2利用磁性磨粒的磁力研磨法 374
第5章抛光 376
5.1磨料抛光的原理及分类 376
5.1.1磨料抛光的原理 376
5.1.2磨料抛光的类型及应用范围 376
5.2固结磨料抛光 377
5.2.1硬质合金轮抛光 378
5.2.1.1抛光原理 378
5.2.1.2抛光设备 378
5.2.1.3抛光的关键工装 379
5.2.1.4抛光磨头及抛光刃具 381
5.2.1.5抛光工艺条件 390
5.2.1.6合金轮抛光的加工特点 391
5.2.1.7 合金轮抛光的缺陷和排除方法 392
5.2.2固结磨料柔性磨具抛光 394
5.2.2.1抛光机理及特点 394
5.2.2.2砂布、砂纸抛光 394
5.2.2.3其它固结磨料柔性磨具 396
5.3自由磨料抛光 398
5.3.1 自由磨料抛光的加工原理及特点 398
5.3.1.1 自由磨料抛光的加工原理 398
5.3.1.2 自由磨料抛光的使用范围及特点 402
5.3.1.3 自由磨料抛光的注意事项 404
5.3.2抛光剂和抛光工艺的关系 405
5.3.2.1 磨料粒度和表面粗糙度值的关系 405
5.3.2.3添加剂及其作用 406
5.3.2.2磨料材质及其适用性 406
5.3.3常用抛光剂的配制及应用 407
5.3.4影响抛光表面质量的因素 411
第6章精冲 413
6.1精冲机理及应用 413
6.1.1精冲机理 413
6.1.2精冲过程 414
6.1.3精冲的精度及应用 415
6.2精冲件的工艺性 416
6.2.1精冲件的结构工艺性 416
6.2.1.1圆角半径 416
6.2.1.2环宽 417
6.2.1.3孔径及孔边距 417
6.2.1.4槽宽及槽边距 417
6.2.1.5齿轮模数 418
6.2.2.1压倒角 419
6.2.1.6窄悬臂和凸耳 419
6.2.2精冲复合工艺 419
6.2.2.2压沉孔 420
6.2.2.3压印 422
6.2.2.4半冲孔(冲盲孔) 423
6.2.2.5弯曲 424
6.2.2.6压扁 426
6.2.2.7浅拉延 427
6.2.2.8翻孔、起伏成形 427
6.2.3精冲件的质量 427
6.2.3.1尺寸精度 427
6.2.3.2剪切面质量 427
6.2.3.3剪切面垂直度 429
6.2.3.4平面度 429
6.2.3.8精冲件常见的缺陷及消除方法 430
6.2.3.7剪切面形变硬化层 430
6.2.3.5塌角 430
6.2.3.6毛刺 430
6.3精冲模具 432
6.3.1精冲模具结构 432
6.3.1.1普通压力机使用的精冲模具 432
6.3.1.2专用精冲压力机使用的模具 442
6.3.2精冲模具设计 447
6.3.2.1精冲模具的设计参数 447
6.3.2.2模具主要零、部件的结构设计 453
6.3.3精冲模具材料 463
6.3.3.1模具主要零件的材料选择 463
6.3.3.2模具材料的深冷处理 464
6.4精冲件材料 465
6.4.1精冲件的适用材料 465
6.4.1.1 钢材 466
6.4.1.2铜和铜合金 467
6.4.1.3铝和铝合金 468
6.4.2钢的球化退火 469
6.4.2.1常用的球化退火工艺 469
6.4.2.2加预热的球化退火工艺 469
6.5精冲设备 470
6.5.1精冲工艺对设备的要求 470
6.5.2 专用精冲压力机的类型和特点 471
6.5.2.1专用精冲压力机的类型 471
6.5.2.2专用精冲压力机的特点 473
6.6精冲润滑剂 476
6.6.1精冲润滑剂的作用 476
6.6.2常用的精冲润滑剂 476
6.7应用实例 477
6.7.1平板的精冲 477
6.7.1.2平板复合精冲模 479
6.7.1.1平板精冲的工艺性分析 479
6.7.1.3平板精冲的技术经济效果 483
6.7.2齿轮件精冲 484
6.7.2.1齿轮模数、材料及加工难度 484
6.7.2.2齿轮复合精冲模 484
6.7.2.3齿轮精冲的技术经济效果 486
6.7.3杠杆精冲件 486
6.7.3.1杠杆的精冲性能 487
6.7.3.2杠杆复合精冲模 487
6.7.3.3杠杆精冲的技术经济效果 489
6.8精冲模的计算机辅助设计及制造 489
6.8.1精冲模CAD/CAM的特点 489
6.8.2精冲模CAD/CAM的基本结构 489
6.8.3.1精冲件的图形输入 490
6.8.3精冲模CAD/CAM的应用 490
6.8.3.2工艺分析及计算 491
6.8.3.3模具结构的设计 491
6.8.3.4自动绘图和数控编程 491
第7章液压泵、液压马达精密偶件 492
加工工艺 492
7.1转子的加工工艺 492
7.1.1 转子的结构特点及技术要求 492
7.1.2转子加工工艺过程 493
7.1.3转子主要加工工艺及工艺分析 495
7.1.3.1转子的材料 495
7.1.3.2柱塞孔的加工工艺 495
7.1.3.3高精度大端面的加工工艺 497
7.1.3.4端面分油槽的加工工艺 498
7.1.3.5 中心内型孔的加工工艺 498
7.2.2柱塞加工工艺过程 499
7.2.1柱塞的结构特点及技术要求 499
7.2柱塞的加工工艺 499
7.2.3柱塞主要加工工艺及工艺分析 501
7.2.3.1柱塞外圆的精加工工艺 501
7.2.3.2柱塞外球面的加工工艺 503
7.2.3.3柱塞内球面的加工工艺 504
7.2.3.4柱塞深小孔的加工工艺 504
7.2.3.5柱塞的收口组合工艺 504
第8章 电液伺服阀典型零件加工工艺8.1滑阀偶件加工工艺 506
8.1.1 滑阀偶件的结构特点及技术要求 506
8.1.2阀套加工工艺过程 508
8.1.3阀套主要加工工艺及工艺难点分析 509
8.1.3.1 阀套的材料及其对工艺过程的影响 509
8.1.3.2阀套内孔加工工艺 509
8.1.3.3阀套矩形孔加工工艺 513
8.1.3.4电火花穿方孔的电极 515
8.1.3.5阀套内环槽加工工艺 516
8.1.4阀套内孔及工作边的测量 518
8.1.5阀芯加工工艺过程 519
8.1.6阀芯主要加工工艺及分析 520
8.1.6.1阀芯中心孔加工工艺 520
8.1.6.2阀芯中槽及均压槽加工工艺 521
8.1.6.3 阀芯外圆磨削及径向配磨工艺 521
8.1.6.4 阀芯工作边精磨及轴向配磨工艺 524
8.1.7滑阀偶件去毛刺工艺分析 528
8.1.7.1阀芯工作边去毛刺工艺 528
8.1.7.2阀套去毛刺工艺 529
8.2伺服阀壳体加工工艺 530
8.2.1伺服阀壳体的结构特点及技术要求 530
8.2.2壳体使用的材料 531
8.2.3壳体加工工艺 531
8.2.4.1粗加工配套孔的几种方法 532
8.2.4壳体关键工序加工方法分析 532
8.2.4.2精加工配套孔的几种方法 533
8.2.4.3油孔加工 534
8.2.5壳体加工中应注意的几个问题 534
8.3衔铁组件加工工艺 535
8.3.1衔铁组件的结构特点及技术要求 535
8.3.2衔铁加工工艺 536
8.3.3挡板加工工艺 538
8.3.4衔挡组件精加工工艺 539
8.3.5反馈杆加工工艺 540
8.3.5.1反馈杆小球的加工方法分析 541
8.3.5.2反馈杆小球的氮化及配研 543
8.3.6弹簧管加工工艺 543
8.3.6.1弹簧管薄壁部分的加工及刚度测量 544
8.3.6.2 弹簧管加工中易出现的问题 545
8.3.7衔铁组件组合工艺 546
8.4喷嘴、节流孔加工工艺 549
8.4.1 喷嘴、节流孔的结构特点及技术要求 549
8.4.2喷嘴、节流孔加工工艺过程 549
8.4.3喷嘴、节流孔主要加工工艺 550
8.4.3.1小孔的加工 550
8.4.3.2小孔去毛刺 550
8.4.3.3喷嘴、节流孔的配对 551
8.5电液伺服阀零组件的清洗与防锈 552
8.5.1清洗工作的重要性 552
8.5.2清洗方法、清洗液的选择及防锈措施 552
第9章舵机助力器精密零件加工工艺 554
9.1滑阀零件加工工艺 554
9.1.1 滑阀零件结构特点及技术要求 554
9.1.2滑阀零件加工工艺过程 556
9.1.3.1 阀芯主要加工工艺 557
9.1.3滑阀零件主要加工工艺 557
9.1.3.2副滑阀主要加工工艺 560
9.1.3.3套筒主要加工工艺 560
9.1.3.4滑阀偶件配套工艺 560
9.1.4滑阀零件工艺分析 561
9.1.4.1滑阀零件常用材料 561
9.1.4.2滑阀零件毛坯的选择 561
9.1.4.3滑阀零件重点工艺分析 561
9.1.5主要工艺装备及检测工具 562
9.2旋转阀加工工艺 563
9.2.1阀芯的加工工艺 563
9.2.1.1 阀芯的结构特点及技术要求 563
9.2.1.2阀芯加工工艺过程 564
9.2.1.3阀芯主要加工工艺 564
9.2.2副阀的加工工艺 566
9.2.2.1副阀的结构形式及技术要求 566
9.2.1.5阀芯加工主要工艺装备 566
9.2.1.4工艺分析 566
9.2.2.2副阀加工工艺过程 567
9.2.2.3副阀主要加工工艺 567
9.2.2.4工艺分析 568
9.2.2.5副阀加工的主要工艺装备 568
9.2.3内套的加工工艺 569
9.2.3.1 内套的结构形式及技术要求 569
9.2.3.2内套加工的工艺过程 569
9.2.3.3内套主要加工工艺 570
9.3 平板阀加工工艺 570
9.3.1 阀座及阀座组件的加工工艺 570
9.3.1.1 阀座的结构特点及技术要求 570
9.3.1.2阀座加工工艺过程 571
9.3.1.3阀座主要加工工艺 571
9.3.1.6 阀座组件的结构特点及技术要求 576
9.3.1.4工艺分析 576
9.3.1.5加工阀座的主要工艺装备 576
9.3.1.7阀座组件的工艺过程 577
9.3.1.8阀座组件主要加工工艺 577
9.3.1.9工艺分析 578
9.3.2阀板的加工及其配套工艺 578
9.3.2.1 阀板的结构特点及技术要求 578
9.3.2.2阀板加工工艺过程 579
9.3.2.3阀板主要加工工艺 579
9.3.2.4工艺分析 583
9.4活塞杆 584
9.4.1 活塞杆的结构形式和技术要求 584
9.4.2活塞杆零件、组件工艺过程 584
9.4.3活塞杆零件、组件主要加工工艺 585
9.4.4.1活塞杆毛坯的选择 586
9.4.4.2活塞杆加工工艺分析 586
9.4.4活塞杆工艺分析 586
9.4.4.3活塞杆主要工艺装备 587
9.5作动筒 587
9.5.1作动筒的结构形式和技术要求 587
9.5.2作动筒加工工艺过程 589
9.5.3作动筒主要加工工艺 590
9.5.4作动筒工艺分析 592
9.5.4.1作动筒毛坯及材料的选择 592
9.5.4.2作动筒加工工艺分析 592
9.5.4.3作动筒主要工艺装备 593
第10章惯性器件加工工艺 596
10.1常规陀螺框架加工工艺 596
10.1.1 陀螺框架的结构特点及技术要求 596
10.1.2陀螺框架的工艺过程 600
10.1.3典型陀螺框架的主要加工工艺 600
10.1.4.2加工难点及分析 601
10.1.4工艺分析 601
10.1.4.1毛坯及材料的选择 601
10.1.5主要工艺装备 603
10.1.6重要检测方法 604
10.1.7 陀螺框架在加工中容易出现的问题及其解决方法 606
10.2挠性接头加工工艺 607
10.2.1 挠性接头的结构特点及技术要求 607
10.2.2挠性接头零、组件工艺过程 608
10.2.3挠性接头主要加工工艺 609
10.2.4工艺分析 611
10.2.5主要工艺装备 613
10.2.6重要检测方法 614
10.2.7加工中容易出现的问题及其解决方法 615
10.3挠性杆加工工艺 615
10.3.1挠性杆的结构特点和技术要求 616
10.3.2挠性杆的工艺过程 617
10.3.3挠性杆的主要加工工艺及分析 618
10.3.4主要工艺装备 621
10.3.5重要的检测方法 623
10.4轴承保持器的加工工艺 623
10.4.1保持器材料 623
10.4.2保持器的加工 624
10.5导电环加工工艺 625
10.5.1 精密导电环的结构特点及技术要求 626
10.5.2导电环的制造工艺过程 627
10.5.3主要加工工艺 627
10.5.4工艺分析 629
10.5.5主要工艺装备 631
10.5.6检测方法 632
10.6.1 环架的结构特点和主要技术要求 633
10.5.7出现的问题及其解决方法 633
10.6平台环架加工工艺 633
10.6.2环架的加工工艺 635
10.6.3主要工艺装备 638
10.6.4重要的检测方法 638
10.6.5加工中容易出现的问题及其解决方法 639
10.7陀螺马达加工工艺 639
10.7.1零、组件结构特点及技术要求 640
10.7.2典型零件加工工艺过程 641
10.7.3工艺分析 641
10.7.4主要工艺装备 642
10.7.5检测方法 644
第11章雷达天线加工工艺 645
11.1抛物面雷达天线加工工艺 645
11.1.1结构特点及技术要求 645
11.1.3水压成形工艺过程 646
11.1.2几种基本成形方法的比较 646
11.1.4水压成形装置及主要加工工艺 647
11.1.5水压成形工艺分析 647
11.2标准波导组合平板缝阵天线加工工艺 648
11.2.1结构特点及技术要求 648
11.2.2工艺过程 649
11.2.3主要加工工艺 649
11.2.4工艺分析 651
11.3整体平板缝阵天线的加工工艺 651
11.3.1零件结构特点及技术要求 652
11.3.2工艺过程 652
11.3.3主要加工工艺 653
11.3.4工艺分析 653
11.3.4.1关键工序加工难点分析 653
11.4板材铆装结构平板缝阵天线 654
11.3.4.2工艺装备分析 654
11.3.4.3天线检测 654
11.4.1零、组件结构特点及技术要求 655
11.4.2底、面板加工工艺过程 656
11.4.3主要加工工艺 656
11.4.4天线装配与焊接 658
第12章仪表类精密零件加工工艺 659
12.1轴尖加工工艺 659
12.1.1各类轴尖的特点及技术要求 659
12.1.2轴尖的加工特点及工艺过程 660
12.1.2.1轴尖的加工特点 660
12.1.2.2单轴尖加工工艺过程 661
12.1.3轴尖的主要加工工艺 661
12.1.3.1整体单轴尖的主要加工工艺 661
12.1.3.2整体球轴尖的主要加工工艺 663
12.1.4轴尖加工的工艺分析 664
12.1.5轴尖的检验 666
12.2宝石轴承加工工艺 667
12.2.1宝石轴承的特点及应用 667
12.2.2宝石轴承的类型 668
12.2.3各类宝石轴承加工工艺过程 669
12.2.4宝石轴承的加工特点 669
12.2.5宝石轴承加工方法及主要设备 670
12.2.5.1宝石轴承毛坯的切割 670
12.2.5.2宝石轴承的平面加工 672
12.2.5.3宝石轴承的外圆磨削 673
12.2.5.4宝石轴承的内孔加工 674
12.2.5.5宝石轴承的槽加工 676
12.2.5.6宝石轴承的抛光 677
12.3.1仪表精密轴的主要类型及特点 678
12.3仪表精密轴类零件加工工艺 678
12.2.6宝石轴承的检验 678
12.3.2典型零件加工工艺 680
12.4磁滞环加工工艺 681
12.4.1磁滞环的技术要求 681
12.4.2磁滞环加工工艺过程 683
12.4.3磁滞环的工艺分析 684
12.5 磁粉离合器杯形转子的加工工艺 685
12.5.1 磁粉离合器杯形转子的结构特点及技术要求 685
12.5.2杯形转子加工工艺过程 686
12.5.3杯形转子的工艺分析 688
12.6加速度计中弹簧片的加工工艺 688
12.6.1 加速度计弹簧片的结构特点和技术要求 688
12.6.2弹簧片加工工艺过程 689
12.6.3弹簧片的主要加工工艺 690
12.6.4弹簧片的工艺分析 692
12.6.5 加速度计中弹簧片的温度冲击和机械振动时效 693
12.7定子、转子叠层的加工工艺 694
12.7.1 定子、转子叠层的工艺特点及技术要求 694
12.7.2定子、转子叠层加工的工艺过程 695
12.7.3定子、转子叠层的主要加工工艺 695
12.7.4定子、转子叠层的工艺分析 696
12.7.5叠层胶合强度的检验方法 697
12.7.6叠层的加工方法不当对传感器零位信号的危害 697
第13章仪表零件微小孔加工技术 699
13.1概述 699
13.2微小孔常规机械加工 704
13.2.1微小孔钻削加工 704
13.2.1.1微小孔钻具种类 704
13.2.1.2微小孔钻具主要几何参数的选择 706
13.2.1.3微小孔钻削用量的选择 707
13.2.2.1几种微小孔精镗刀介绍 709
13.2.2微小孔的镗削加工 709
13.2.2.2微小孔镗刀几何参数的选择 712
13.2.2.3微小孔镗削用量的选择 713
13.2.3微小孔的铰削加工 714
13.2.3.1 铰刀种类、特点及适用性指标 714
13.2.3.2铰刀几何参数及切削用量的选择 720
13.2.3.3提高微小孔铰削加工质量的技术措施 721
13.2.4微小孔拉削及挤压加工 725
13.2.4.1拉削加工 725
13.2.4.2挤压加工 726
13.2.5微小孔机械磨钻和拉抛加工 730
13.2.5.1机械磨钻 730
13.2.5.2微小孔拉抛工艺 731
13.3.1.2微小孔振动机械加工主要工艺效果及分析 734
13.3.1.1 微小孔振动机械加工的实质 734
13.3.1微小孔振动机械加工 734
13.3微小孔特种机械加工 734
13.3.1.3微小孔振动机械加工的类型及特点 735
13.3.1.4振动加工装置的类型及其频率范围 736
13.3.1.5微小孔振动加工的应用 736
13.3.2微小孔的超高速机械加工 740
13.3.2.1 微小孔的超高速机械加工简介 740
13.3.2.2微小孔深孔的超高速钻削加工 742
13.3.2.3微小孔超高速加工的应用实例 744
13.4仪表类典型零件微小孔加工工艺 745
13.4.1航空仪表用宝石轴承孔加工 745
13.4.2仪表轴类零件轴向中心微深孔加工 745
13.4.3仪表轴套类零件孔系加工 746
13.4.4仪表平板类零件孔系加工 746
14.1.1 振动筒压力传感器的结构及工作原理 747
14.1薄壁振动筒加工工艺 747
第14章其他航空精密零件加工工艺 747
14.1.2 振动筒的结构特点及技术要求 748
14.1.3振动筒加工工艺过程 749
14.1.4振动筒的主要加工工艺 749
14.1.5振动筒的加工工艺分析 750
14.1.5.1材料选择 750
14.1.5.2加工难点及分析 751
14.1.5.3加工质量控制及技术措施 751
14.1.5.4主要加工设备及工艺装备 751
14.1.5.5重要的检测方法 752
14.2浮筒类零件加工工艺 752
14.2.1 浮筒类零件的结构特点及技术要求 752
14.2.2浮筒类零件的加工工艺过程 753
14.2.3浮筒类零件的主要加工工艺 753
14.2.4.2定位基准及零件的装夹 754
14.2.4.1毛坯及材料的选择 754
14.2.4浮筒类零件加工工艺分析 754
14.2.4.3金刚石车刀在浮筒加工中的应用及车刀的参数 755
14.2.4.4浮筒类零件的检测 756
14.3环形电位器骨架的加工工艺 756
14.3.1骨架的结构特点及技术要求 756
14.3.2骨架的加工工艺过程 757
14.3.3骨架的主要加工工艺 758
14.3.4骨架加工工艺分析 759
14.3.4.1加工变形的控制 759
14.3.4.2切削刀具的选择 759
14.3.4.3 PCBN刀具的几何参数 761
14.3.4.4精车切削的加工参数 761
14.3.6.2浸绝缘清漆 762
14.3.6.1草酸阳极化 762
14.3.6绝缘处理 762
14.3.5稳定化处理 762
14.3.4.5 PCBN刀具的刃磨 762
14.3.4.6骨架几何精度的检测 762
14.4精密平板的加工工艺 764
14.4.1精密平板的结构特点及技术要求 764
14.4.2精密平板加工方法的选择 764
14.4.3精密平板加工应遵循的一般原则 765
14.4.4坐标镗削加工 765
14.4.4.1 坐标镗削加工的工艺过程 765
14.4.4.2 坐标镗削加工的主要加工工艺 766
14.4.5普通冲压、内孔整修加工 766
14.4.5.1 普通冲压、内孔整修加工工艺过程 766
14.4.5.2普通冲压、内孔整修加工的主要加工工艺 766
14.4.5.3整修模 768
14.4.5.4整修冲切力计算 771
14.4.5.6普通冲压、内孔整修加工精密平板实例 772
14.4.5.5 不能整修的孔的补充加工 772
14.4.6精冲、内孔整修加工 774
14.4.6.1精冲、内孔整修加工工艺过程 774
14.4.6.2精冲、内孔整修加工精密平板实例 774
14.5整体钛合金涡轮加工工艺 775
14.5.1 涡轮的结构及技术要求 775
14.5.2涡轮加工工艺过程 776
14.5.3涡轮的主要加工工艺 777
14.5.4涡轮加工工艺分析 781
14.5.4.1 材料的切削加工性及切削参数 781
14.5.4.2毛坯加工前下料问题及解决措施 782
14.5.4.3涡轮叶片的加工 783
14.5.4.4涡轮的静平衡及动平衡 788
参考文献 790
- 《市政工程基础》杨岚编著 2009
- 《工程静力学》王科盛主编 2019
- 《中国制造业绿色供应链发展研究报告》中国电子信息产业发展研究院 2019
- 《中央财政支持提升专业服务产业发展能力项目水利工程专业课程建设成果 设施农业工程技术》赵英编 2018
- 《Maya 2018完全实战技术手册》来阳编著 2019
- 《化学反应工程》许志美主编 2019
- 《绿色过程工程与清洁生产技术 张懿院士论文集精选 上》《绿色过程工程与清洁生产技术》编写组编 2019
- 《软件工程》齐治昌,谭庆平,宁洪编著 2019
- 《高等教育双机械基础课程系列教材 高等学校教材 机械设计课程设计手册 第5版》吴宗泽,罗圣国,高志,李威 2018
- 《化学工程与工艺专业实验指导》郭跃萍主编 2019
- 《莼江曲谱 2 中国昆曲博物馆藏稀见昆剧手抄曲谱汇编之一》郭腊梅主编;孙伊婷副主编;孙文明,孙伊婷编委;中国昆曲博物馆编 2018
- 《指向核心素养 北京十一学校名师教学设计 英语 七年级 上 配人教版》周志英总主编 2019
- 《植物百科彩色图鉴 第2卷》植物百科彩色图鉴编委会主编 2012
- 《远去的老调》经典文库编委会编 2019
- 《北京生态环境保护》《北京环境保护丛书》编委会编著 2018
- 《莼江曲谱 1 中国昆曲博物馆藏稀见昆剧手抄曲谱汇编之一》郭腊梅主编;孙伊婷副主编;孙文明,孙伊婷编委;中国昆曲博物馆编 2018
- 《共和国日记 1964》《共和国日记》编委会编 2019
- 《中国地方艺文荟萃 华北东北卷 第1辑 3》《中国地方艺文荟萃》编委会编 2018
- 《绿色过程工程与清洁生产技术 张懿院士论文集精选 上》《绿色过程工程与清洁生产技术》编写组编 2019
- 《中国地方艺文荟萃 华北东北卷 第1辑 1》《中国地方艺文荟萃》编委会编 2018
- 《指向核心素养 北京十一学校名师教学设计 英语 七年级 上 配人教版》周志英总主编 2019
- 《北京生态环境保护》《北京环境保护丛书》编委会编著 2018
- 《指向核心素养 北京十一学校名师教学设计 英语 九年级 上 配人教版》周志英总主编 2019
- 《高等院校旅游专业系列教材 旅游企业岗位培训系列教材 新编北京导游英语》杨昆,鄢莉,谭明华 2019
- 《中国十大出版家》王震,贺越明著 1991
- 《近代民营出版机构的英语函授教育 以“商务、中华、开明”函授学校为个案 1915年-1946年版》丁伟 2017
- 《新工业时代 世界级工业家张毓强和他的“新石头记”》秦朔 2019
- 《智能制造高技能人才培养规划丛书 ABB工业机器人虚拟仿真教程》(中国)工控帮教研组 2019
- 《陶瓷工业节能减排技术丛书 陶瓷工业节能减排与污染综合治理》罗民华著 2017
- 《全国职业院校工业机器人技术专业规划教材 工业机器人现场编程》(中国)项万明 2019