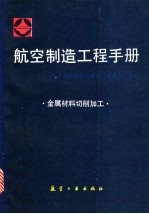
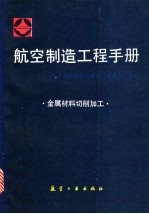
航空制造工程手册 金属材料切削加工PDF电子书下载
- 电子书积分:20 积分如何计算积分?
- 作 者:《航空制造工程手册》总编委会主编
- 出 版 社:北京:航空工业出版社
- 出版年份:1994
- ISBN:7800468291
- 页数:724 页
目 录 1
符号说明 1
第1章金属切削原理 1
1.1切削过程中的变形规律 1
1.1.1切削过程中的塑性变形 1
1.1.1.1变形区的划分 1
1.1.1.2剪切应变与变形系数 2
1.1.1.3切屑形成的几何和力学关系 2
1.1.1.4剪切角的理论公式 4
1.1.2剪切面的剪应力 5
1.1.3刀具前刀面的摩擦特性 6
1.1.4积屑瘤和鳞刺 7
1.1.4.1积屑瘤 7
1.1.4.2鳞刺 8
1.1.5斜角切削 9
1.1.5.1切屑流出方向 9
1.1.5.2刀具的实际工作角度 9
1.1.5.3有效剪切角 10
1.1.6难加工材料的切削变形规律 10
1.1.6.1钛合金 10
1.1.6.2高温合金 11
1.2.1切削分力 12
1.2.2切削力的经验公式 12
1.2切削力 12
1.2.3影响切削力的因素 13
1.2.4切削力的测量 14
1.2.4.1 八角环电阻式三向车削测力仪 14
1.2.4.2压电式测力仪 15
1.3切削热和切削温度 15
1.3.1切削热的产生与传出 15
1.3.1.1切削热的产生 15
1.3.2切削温度的经验公式 16
1.3.1.2切削热的传出 16
1.3.1.3刀具前后刀面的温度分布 16
1.3.3影响切削温度的因素 17
1.3.4切削温度的测量 18
1.3.4.1 人工热电偶测温法 18
1.3.4.2 自然热电偶测温法 18
1.3.4.3红外线测温法 19
1.4刀具的磨损及刀具寿命 19
1.4.1 刀具的磨损形态 19
1.4.2刀具的磨损机理 19
1.4.3刀具的磨损特性 21
1.4.4.1 切削高温合金的刀具磨损特点 22
1.4.4 切削难加工材料时的刀具磨损 22
1.4.4.2切削钛合金的刀具磨损特点 23
1.4.5刀具的磨钝标准 23
1.4.6刀具寿命及其方程式 23
1.4.6.1 刀具寿命方程式 24
1.4.6.2刀具寿命的合理选择 25
1.4.7最佳切削速度 26
1.4.7.1 刀具相对磨损 26
1.4.7.2最佳切削速度 26
1.4.8.2刀具破损寿命的计算方法 27
1.4.8刀具的非正常磨损 破损 27
1.4.8.1 刀具破损的形式 27
1.4.8.3刀具破损寿命的实验方法 28
1.5切屑控制 29
1.5.1切屑的流出和卷曲 29
1.5.2断屑机理 29
1.5.3切屑控制方法 30
1.6磨削原理 30
1.6.1 磨削过程 30
1.6.1.1 磨削特点 30
1.6.1.2磨削过程分析 32
1.6.2磨削力 33
1.6.2.1磨削力理论计算式 33
1.6.2.2磨削力经验计算式 33
1.6.3磨削温度 34
1.6.4砂轮磨损及修整 34
1.6.4.1砂轮磨损形式及磨损原因 34
1.6.4.2砂轮修整 35
1.6.5砂轮磨削性能的评定指标 36
1.6.6高效磨削 37
1.6.6.1 高速磨削 37
1.6.6.2缓进磨削 38
1.6.6.3 砂带磨削 40
1.6.7难加工材料的磨削规律 42
1.6.7.1 高温合金的磨削 42
1.6.7.2钛合金的磨削 43
第2章航空金属材料的分类及其切削加 45
工性 45
2.1 航空金属材料的分类及应用 45
2.1.1高温合金 45
2.1.1.1高温合金的分类 45
2.1.1.2高温合金在航空工业中的应用 46
2.1.2.1工业钛合金的分类 47
2.1.2钛合金 47
2.1.2.2钛合金在航空工业中应用 48
2.1.3不锈钢 49
2.1.3.1不锈钢分类 49
2.1.3.2不锈钢在航空工业中应用 50
2.1.4高强度钢 50
2.1.4.1高强度钢的分类 50
2.1.4.2高强度钢在航空工业中的应用 51
2.1.5.1铝镁合金的分类 52
2.1.5.2铝镁合金在航空工业中的应用 52
2.1.5铝镁合金 52
2.1.6其他材料 55
2.1.6.1喷涂(焊)材料 55
2.1.6.2高熔点金属及其合金 56
2.2金属材料切削加工性的概念 57
2.2.1金属材料切削加工性的评定 57
2.2.2影响切削加工性的因素 57
2.2.3磨削加工性 59
2.2.4航空金属材料的相对切削加工性 59
2.3高温合金的切削加工性 60
2.3.1高温合金的切削加工特点 60
2.4.1钛合金的切削加工特点 62
2.4钛合金的切削加工性 62
2.3.2高温合金切削加工中的注意事项 62
2.4.2钛合金切削加工中的注意事项 64
2.5不锈钢的切削加工性 64
2.5.1不锈钢的切削加工特点 64
2.5.2不锈钢切削加工中的注意事项 65
2.6高强度钢的切削加工性 66
2.6.1高强度钢的切削加工特点 66
2.6.2高强度钢切削加工中的注意事项 66
2.7铝镁合金的切削加工性 66
2.8.2 高熔点金属及其合金的切削加工特点 67
2.8.1 喷涂(焊)材料的切削加工特点 67
2.8其他材料的切削加工性 67
第3章刀具材料及砂轮 69
3.1刀具材料概述 69
3.1.1 刀具材料的分类及其性能 69
3.1.2刀具材料选择的一般原则 69
3.2高速钢 70
3.2.1普通高速钢和高碳高速钢 70
3.2.2超硬高速钢 71
3.2.2.1钴高速钢 71
3.2.2.2高钒高速钢 71
3.2.2.5含SiNbAl高速钢 72
3.2.2.3铝高速钢 72
3.2.2.4含氮高速钢 72
3.2.3高速钢的选用 75
3.2.4粉末冶金高速钢 76
3.2.4.1粉末冶金高速钢特性 76
3.4.4.2粉末冶金高速钢主要牌号及其应用 77
3.2.5涂层高速钢 77
3.2.5.1涂层高速钢特性 78
3.2.5.2涂层高速钢的应用 78
3.3.1硬质合金特点 79
3.3.2硬质合金的ISO分类分组代号 79
3.3硬质合金 79
3.3.3 国产硬质合金分类和通用牌号 81
3.3.4 国产新牌号硬质合金性能及适用范围 83
3.3.5 国外若干厂家研制的硬质合金牌号 86
3.3.6涂层硬质合金 89
3.3.6.1涂层硬质合金特性与适用范围 90
3.3.6.2涂层硬质合金主要牌号及其应用 90
3.4陶瓷刀具材料 93
3.4.1陶瓷刀具材料的特性 94
3.4.2陶瓷刀具材料的种类 94
3.4.3国产陶瓷刀具材料牌号及性能 95
3. 4.4国外陶瓷刀具材料牌号及性能 96
3.5超硬刀具材料 97
3.4.5陶瓷刀具材料的应用 97
3.5.1金刚石刀具材料 98
3.5.2立方氮化硼刀具材料 100
3.6可转位硬质合金刀片 101
3.6.1 公制可转位刀片的标记法 102
3.6.2英制可转位刀片的标记法 104
3.6.3国产可转位刀片型号标记法 104
3.6.4部分特型可转位刀片 107
3.6.5可转位刀片选用示例 107
3.7.1.1普通磨料及其选择 108
3.7砂轮 108
3.7.1普通磨料砂轮 108
3.7.1.2普通磨料的粒度及其选择 110
3.7.1.3普通磨料砂轮的结合剂及其选择 111
3.7.1.4普通磨料砂轮的硬度及其选择 111
3.7.1.5 普通磨料砂轮的组织及其选择 111
3.7.1.6普通磨料砂轮的形状和尺寸 112
3.7.1.7普通磨料砂轮的标志 112
3.7.2超硬磨料砂轮 113
3.7.2.1超硬磨料及其选择 113
3.7.2.2超硬磨料的粒度及其选择 114
3.7.2.3超硬磨料砂轮的浓度及其选择 115
3.7.2.4超硬磨料砂轮的结合剂及其选择 116
3.7.2.5超硬磨料砂轮的形状和尺寸 116
3.7.2.6超硬磨料砂轮的标志 118
第4章刀具切削部分几何参数 119
4.1刀具切削部分几何参数合理选择原则 119
4.1.1刃形的选择 119
4.1.2切削刃区剖面形式的选择 119
4.1.3刀面形式的选择 120
4.1.4刀具几何参数的选择 120
4.2.1.1 车刀、镗刀切削部分的标注角度 121
4.2.1.2车刀、镗刀几何角度选择 121
4.2车刀、镗刀 121
4.2.1车刀、镗刀切削部分几何参数 121
4.2.2断屑槽 122
4.2.2.1断屑槽基本槽型 122
4.2.2.2断屑槽基本截形 123
4.2.2.3断屑板 124
4.2.3刀具角度换算 124
4.3.1.2端面铣刀几何参数选择 125
4.3.1.1 端面铣刀切削部分的主要标注角度 125
4.3.1端面铣刀 125
4.3铣刀 125
4.3.2三面刃铣刀 126
4.3.2.1 三面刃铣刀切削部分的主要标注角度 126
4.3.2.2三面刃铣刀几何角度选择 126
4.3.3立铣刀 126
4.3.3.1 立铣刀(铣周边和槽)切削部分的主要标注角度 126
4.3.3.2立铣刀几何参数选择 126
4.4.1.2高速钢麻花钻几何参数选择 127
4.4.1.1 高速钢麻花钻切削部分结构 127
4.4.1钻头 127
4.4钻头、深孔钻和铰刀 127
4.4.2深孔钻 128
4.4.2.1 深孔钻(枪钻)主要几何参数标注 128
4.4.2.2枪钻的结构及主要几何参数选择指南 128
4.4.3铰刀 129
4.4.3.1 铰刀切削部分主要几何参数标注 129
4.4.3.2铰刀主要几何参数选择 129
4.4.3.3铰刀几何参数选择指南 129
4.5.1.1 拉刀切削部分主要几何参数标注 130
4.5.1.2拉刀主要几何角度选择 130
4.5 拉刀 130
4.5.1拉刀切削部分几何参数 130
4.5.1.3拉刀几何参数选择指南 131
4.5.2容屑槽 131
4.6螺纹刀具 132
4.6.1螺纹车刀 132
4.6.1.1 螺纹车刀切削部分主要几何参数标注 132
4.6.1.2螺纹车刀主要几何角度选择 133
4.6.2螺纹梳刀 133
4.6.2.1径向梳刀、圆梳刀和切向梳刀切削部分主要几何角度标注 133
4.6.2.2 径向梳刀、圆梳刀和切向梳刀几何角度选择 133
4.6.3.1 丝锥切削部分主要几何角度标注 134
4.6.3丝锥 134
4.6.3.2丝锥几何参数选择 135
4.6.3.3丝锥几何参数选择指南 135
4.7数控刀具 136
4.7.1数控刀具特点 136
4.7.1.1数控刀具材料选用 136
4.7.1.2数控刀具结构 136
4.7.1.3数控刀具寿命 136
4.7.2数控加工铣刀的选择 136
4.7.3孔加工用数控刀具的选择 137
5.1车削加工方法 138
第5章车削加工用量 138
5.2单刃和可转位刀具车削加工用量 141
5.2.1高速钢、硬质合金刀具车削加工用量 141
5.2.1.1高温合金车削加工用量 141
5.2.1.2钛合金车削加工用量 144
5.2.1.3不锈钢车削加工用量 148
5.2.1.4高强度钢车削加工用量 153
5.2.1.5铝合金车削加工用量 154
5.2.1.6镁合金车削加工用量 156
5.2.1.7工具钢车削加工用量 157
5.2.2.1 陶瓷刀具车削高温合金加工用量 160
5.2.2陶瓷刀具车削加工用量 160
5.2.2.2陶瓷刀具车削不锈钢加工用量 161
5.2.2.3陶瓷刀具车削高强度钢加工用量 161
5.2.3立方氮化硼(CBN)刀具车削加工用量 162
5.2.3.1 立方氮化硼刀具车削高温合金加工用量 162
5.2.3.2立方氮化硼刀具车削工具钢加工用量 162
5.2.4金刚石刀具车削加工用量 163
5.2.4.1 金刚石刀具车削铝合金加工用量 163
5.2.4.2金刚石刀具车削镁合金加工用量 163
5.3切断和成形刀具车削加工用量 164
5.3.1 高温合金车削加工用量 164
5.3.2钛合金车削加工用量 167
5.3.3不锈钢车削加工用量 169
5.3.4高强度钢车削加工用量 171
5.3.5铝合金车削加工用量 172
5.3.6镁合金车削加工用量 174
5.3.7工具钢车削加工用量 174
5.4数控车削加工用量 176
5.4.1数控车削高温合金加工用量 176
5.4.2数控车削钛合金加工用量 180
5.4.3数控车削不锈钢加工用量 184
5.4.4数控车削高强度钢加工用量 190
5.5车削中常见问题、产生原因及解决方法 195
第6章铣削加工用量 196
6.1铣削加工方法 196
6.1.1铣削加工范围 196
6.1.2铣削用量要素及铣削参数计算 197
6.1.2.1 铣削用量要素的构成与表示方法 197
6.1.2.2铣削参数计算 197
6.2端面铣刀平面铣削用量 200
6.2.1端面铣刀平面铣削高温合金用量 200
6.2.2端面铣刀平面铣削钛合金用量 203
6.2.3端面铣刀平面铣削不锈钢用量 205
6.2.4端面铣刀平面铣削高强度钢用量 208
6.2.5端面铣刀平面铣削铝合金用量 210
6.2.6端面铣刀平面铣削镁合金用量 212
6.2.7端面铣刀平面铣削工具钢用量 213
6.3圆柱铣刀平面铣削用量 215
6.3.1 圆柱铣刀平面铣削高温合金用量 215
6.3.2圆柱铣刀平面铣削钛合金用量 216
6.3.3圆柱铣刀平面铣削不锈钢用量 217
6.3.4圆柱铣刀平面铣削高强度钢用量 218
6.3.6圆柱铣刀平面铣削镁合金用量 219
6.3.5圆柱铣刀平面铣削铝合金用量 219
6.3.7圆柱铣刀平面铣削工具钢用量 220
6.4三面刃铣刀侧面和槽铣削用量 221
6.4.1三面刃铣刀侧面和槽铣削高温合金用量 221
6.4.2三面刃铣刀侧面和槽铣削钛合金用量 224
6.4.3三面刃铣刀侧面和槽铣削不锈钢用量 226
6.4.4三面刃铣刀侧面和槽铣削高强度钢用量 229
6.4.5三面刃铣刀侧面和槽铣削铝合金用量 231
6.4.6三面刃铣刀侧面和槽铣削镁合金用量 233
6.4.7三面刃铣刀侧面和槽铣削工具钢用量 234
6.5.1立铣刀侧面铣削用量 236
6.5.1.1立铣刀侧面铣削高温合金用量 236
6.5立铣刀侧面和槽铣削用量 236
6.5.1.2立铣刀侧面铣削钛合金用量 239
6.5.1.3立铣刀侧面铣削不锈钢用量 241
6.5.1.4立铣刀侧面铣削高强度钢用量 245
6.5.1.5立铣刀侧面铣削铝合金用量 247
6.5.1.6立铣刀侧面铣削镁合金用量 249
6.5.1.7立铣刀侧面铣削工具钢用量 250
6.5.2立铣刀槽铣削用量 253
6.5.2.1立铣刀槽铣削高温合金用量 253
6.5.2.2立铣刀槽铣削钛合金用量 254
6.5.2.3立铣刀槽铣削不锈钢用量 255
6.5.2.4立铣刀槽铣削高强度钢用量 258
6.5.2.5立铣刀槽铣削铝合金用量 259
6.5.2.6立铣刀槽铣削镁合金用量 260
6.5.2.7立铣刀槽铣削工具钢用量 261
6.6数控铣削用量 263
6.6.1端面铣刀数控平面铣削用量 263
6.6.1.1 端面铣刀数控平面铣削高温合金用量 263
6.6.1.2端面铣刀数控平面铣削钛合金用量 266
6.6.1.3端面铣刀数控平面铣削不锈钢用量 268
6.6.1.4端面铣刀数控平面铣削高强度钢用量 271
6.6.1.5端面铣刀数控平面铣削铝合金用量 273
6.6.1.6端面铣刀数控平面铣削镁合金用量 274
6.6.1.7 端面铣刀数控平面铣削工具钢用量 275
6.6.2立铣刀数控侧面铣削用量 277
6.6.2.1 立铣刀数控侧面铣削高温合金用量 277
6.6.2.2 立铣刀数控侧面铣削钛合金用量 280
6.6.2.3立铣刀数控侧面铣削不锈钢用量 283
6.6.2.4立铣刀数控侧面铣削高强度钢用量 287
6.6.2.5立铣刀数控侧面铣削铝合金用量 290
6.6.2.6立铣刀数控侧面铣削镁合金用量 292
6.6.2.7立铣刀数控侧面铣削工具钢用量 293
6.7铣削中常见问题的产生原因及解决方法 296
7.1孔加工的一般方法 298
第7章钻削、扩孔、铰削、镗削及珩磨 298
加工用量 298
7.2钻削加工用量 302
7.2.1普通钻削加工用量 302
7.2.1.1高温合金普通钻削加工用量 302
7.2.1.2钛合金普通钻削加工用量 304
7.2.1.3不锈钢普通钻削加工用量 306
7.2.1.4高强度钢普通钻削加工用量 308
7.2.1.5铝合金普通钻削加工用量 308
7.2.1.6镁合金普通钻削加工用量 309
7.2.1.7工具钢普通钻削加工用量 310
7.2.2.1高温合金外排屑深孔钻削加工用量 311
7.2.2外排属深孔钻削加工用量 311
7.2.2.2钛合金外排屑深孔钻削加工用量 314
7.2.2.3不锈钢外排屑深孔钻削加工用量 315
7.2.2.4高强度钢外排屑深孔钻削加工用量 317
7.2.2.5铝合金外排屑深孔钻削加工用量 318
7.2.2.6镁合金外排屑深孔钻削加工用量 319
7.2.2.7工具钢外排屑深孔钻削加工用量 319
7.2.3 内排屑深孔钻削加工用量 320
7.2.3.1 钛合金内排屑深孔钻削加工用量 320
7.2.3.2不锈钢内排屑深孔钻削加工用量 322
7.2.3.3高强度钢内排屑深孔钻削加工用量 324
7.2.3.4铝合金内排屑深孔钻削加工用量 325
7.2.3.5镁合金内排屑深孔钻削加工用量 326
7.2.3.6工具钢内排屑深孔钻削加工用量 326
7.3扩孔加工用量 327
7.3.1高温合金扩孔加工用量 327
7.3.2钛合金扩孔加工用量 329
7.3.3不锈钢扩孔加工用量 331
7.3.4高强度钢扩孔加工用量 333
7.3.5铝合金扩孔加工用量 335
7.3.7工具钢扩孔加工用量 336
7.3.6镁合金扩孔加工用量 336
7.4.1高温合金铰削加工用量 338
7.4铰削加工用量 338
7.4.2钛合金铰削加工用量 342
7.4.3不锈钢铰削加工用量 346
7.4.4高强度钢铰削加工用量 352
7.4.5铝合金铰削加工用量 354
7.4.6镁合金铰削加工用量 355
7.4.7工具钢铰削加工用量 356
用量 359
7.5.1.1高速钢、硬质合金刀具镗削高温合金加工用量 359
7.5.1高速钢、硬质合金刀具镗削加工 359
7.5镗削加工用量 359
7.5.1.2高速钢、硬质合金刀具镗削钛合金加工用量 362
7.5.1.3高速钢、硬质合金刀具镗削不锈钢加工用量 365
7.5.1.4高速钢、硬质合金刀具镗削高强度钢加工用量 368
7.5.1.5高速钢、硬质合金刀具镗削铝合金加工用量 370
7.5.1.6高速钢、硬质合金刀具镗削镁合金加工用量 371
7.5.1.7高速钢、硬质合金刀具镗削工具钢加工用量 372
7.5.2陶瓷刀具镗削加工用量 375
7.5.2.1 陶瓷刀具镗削不锈钢加工用量 375
7.5.2.3陶瓷刀具镗削工具钢加工用量 377
7.5.2.2陶瓷刀具镗削高强度钢加工用量 377
7.5.3金刚石刀具镗削加工用量 379
7.5.3.1 金刚石刀具镗削铝合金加工用量 379
7.5.3.2金刚石刀具镗削镁合金加工用量 380
7.6珩磨加工用量 380
7.7孔加工中常见问题、产生原因及解决方法 381
7.7.1钻削中常见问题、产生原因及解决方法 381
7.7.1.1普通钻削中常见问题、产生原因及解决方法 381
7.7.1.2深孔钻削中常见问题、产生原因及解决方法 383
7.7.2扩孔中常见问题、产生原因及解决方法 384
7.7.3铰削中常见问题、产生原因及解决方法 384
7.7.4镗削中常见问题、产生原因及解决方法 385
7.7.5珩磨中常见问题、产生原因及解决方法 386
第8章拉削加工用量 388
8.1拉削加工方法 388
8.1.1拉削特点 388
8.1.2拉削方式 388
8.1.3拉削加工范围 390
8.2拉削加工用量 391
8.2.1高温合金拉削用量 391
8.2.2钛合金拉削用量 392
8.2.3不锈钢拉削用量 394
8.2.5铝合金拉削用量 395
8.2.4高强度钢拉削用量 395
8.2.7工具钢拉削用量 396
8.2.6镁合金拉削用量 396
8.3航空典型零件拉削加工用量 397
8.3.1 涡轮叶片典型工序拉削用量 397
8.3.2压气机叶片典型工序拉削用量 398
8.3.3涡轮盘典型工序拉削用量 398
8.3.4花键内套齿典型工序拉削用量 399
8.4拉削加工中常见问题、产生原因及解决方法 400
9.1磨削加工方法 406
9.1.1磨削加工方法分类 406
第9章磨削加工用量 406
9.1.2磨削参数计算公式 407
9.2砂轮修整 408
9.2.1 普通磨料砂轮修整方法及修整用量 408
9.2.1.1砂轮修整方法分类 408
9.2.1.2修整工具及修整用量 410
9.2.2超硬磨料砂轮修整方法及修整用量 412
9.3卧轴矩台平面磨削加工用量 415
9.3.1高温合金卧轴矩台平面磨削加工用量 415
9.3.2钛合金卧轴矩台平面磨削加工用量 418
9.3.3不锈钢卧轴矩台平面磨削加工用量 420
9.3.4高强度钢卧轴矩台平面磨削加工用量 422
9.3.5铝合金卧轴矩台平面磨削加工用量 423
9.3.6镁合金卧轴矩台平面磨削加工用量 423
9.3.7工具钢卧轴矩台平面磨削加工用量 424
9.3.8硬质合金卧轴矩台平面磨削加工用量 427
9.3.9火焰喷涂航空金属材料卧轴矩台平面磨削加工用量 427
9.4立轴圆台平面磨削加工用量 428
9.4.1高温合金立轴圆台平面磨削加工用量 428
9.4.2钛合金立轴圆台平面磨削加工用量 430
9.4.3 不锈钢立轴圆台平面磨削加工用量 431
9.4.5铝合金立轴圆台平面磨削加工用量 432
9.4.4高强度钢立轴圆台平面磨削加工用量 432
9.4.6镁合金立轴圆台平面磨削加工用量 433
9.4.7工具钢立轴圆台平面磨削加工用量 434
9.5外圆磨削加工用量 435
9.5.1 高温合金外圆磨削加工用量 435
9.5.2钛合金外圆磨削加工用量 438
9.5.3 不锈钢外圆磨削加工用量 440
9.5.4高强度钢外圆磨削加工用量 443
9.5.5铝合金外圆磨削加工用量 444
9.5.6镁合金外圆磨削加工用量 444
9.5.7工具钢外圆磨削加工用量 445
9.5.8硬质合金外圆磨削加工用量 447
9.5.9 火焰喷涂航空金属材料外圆磨削加工用量 448
9.6内圆磨削加工用量 449
9.6.1 高温合金内圆磨削加工用量 449
9.6.2钛合金内圆磨削加工用量 452
9.6.3不锈钢内圆磨削加工用量 454
9.6.4高强度钢内圆磨削加工用量 457
9.6.5铝合金内圆磨削加工用量 458
9.6.6镁合金内圆磨削加工用量 458
9.6.7工具钢内圆磨削加工用量 460
9.6.8硬质合金内圆磨削加工用量 462
9.6.9 火焰喷涂航空金属材料内圆磨削加工用量 463
9.7无心磨削加工用量 464
9.7.1高温合金无心磨削加工用量 464
9.7.2钛合金无心磨削加工用量 466
9.7.3不锈钢无心磨削加工用量 467
9.7.4高强度钢无心磨削加工用量 468
9.7.5铝合金无心磨削加工用量 468
9.7.6镁合金无心磨削加工用量 469
9.7.7工具钢无心磨削加工用量 469
9.7.8硬质合金无心磨削加工用量 470
9.7.9 火焰喷涂航空金属材料无心磨削加工用量 471
9.8砂带磨削加工用量 471
9.9缓进给磨削加工用量 472
9.10磨削加工中常见问题、产生原因及解决方法 473
9.10.1 平面磨削中常见问题、产生原因及解决方法 473
9.10.2外圆磨削中常见问题、产生原因及解决方法 474
9.10.3 内圆磨削中常见问题、产生原因及解决方法 476
9.10.4 无心外圆磨削中常见问题、产生原因及解决方法 477
第10章螺纹加工用量 479
10.1螺纹加工方法 479
10.1.1螺纹车削加工方法 479
10.1.2螺纹铣削加工方法 480
10.1.3螺纹磨削加工方法 481
10.1.4螺纹攻丝加工方法 482
10.1.4.1丝锥分类及特点 482
10.1.4.2冷挤压攻丝 484
10.1.5滚丝轮滚压加工方法 487
10.2螺纹车削加工用量 489
10.2.1高温合金螺纹车削用量 489
10.2.2钛合金螺纹车削用量 492
10.2.3不锈钢螺纹车削用量 493
10.2.4高强度钢螺纹车削用量 495
10.2.5铝合金螺纹车削用量 496
10.2.7工具钢螺纹车削用量 497
10.2.6镁合金螺纹车削用量 497
10.3螺纹铣削加工用量 499
10.3.1高温合金螺纹铣削用量 499
10.3.2钛合金螺纹铣削用量 501
10.3.3不锈钢螺纹铣削用量 502
10.3.4高强度钢螺纹铣削用量 503
10.3.5铝合金螺纹铣削用量 503
10.3.6镁合金螺纹铣削用量 504
10.3.7工具钢螺纹铣削用量 504
10.4螺纹磨削加工用量 505
10.4.1高温合金螺纹磨削用量 505
10.4.2不锈钢螺纹磨削用量 507
10.4.3高强度钢螺纹磨削用量 509
10.4.4工具钢螺纹磨削用量 509
10.5螺纹攻丝加工用量 510
10.5.1高温合金螺纹攻丝加工用量 510
10.5.2钛合金螺纹攻丝加工用量 512
10.5.3不锈钢螺纹攻丝加工用量 513
10.5.4高强度钢螺纹攻丝加工用量 514
10.5.5铝合金螺纹攻丝加工用量 514
10.5.6镁合金螺纹攻丝加工用量 515
10.5.7工具钢螺纹攻丝加工用量 516
10.6.3滚丝轮径向进给量 517
10.6.2滚丝轮滚压力 517
10.6螺纹滚压加工用量 517
10.6.1滚丝轮滚压速度 517
10.6.4滚丝轮滚压时间 518
10.7螺纹加工中常见问题、产生原因及解决方法 518
10.7.1螺纹车削中常见问题、产生原因及解决方法 518
10.7.2螺纹铣削中常见问题、产生原因及解决方法 519
10.7.3螺纹磨削中常见问题、产生原因及解决方法 519
10.7.4螺纹攻丝中常见问题、产生原因及解决方法 521
10.7.5冷挤压螺孔中常见问题、产生原因及解决方法 522
10.7.6螺纹滚压中常见问题、产生原因及解决方法 522
11.1齿轮加工方法 524
第11章齿轮加工用量 524
11.2齿轮加工用量 526
11.2.1滚齿加工用量 526
11.2.2插齿加工用量 527
11.2.3剃齿加工用量 528
11.2.4磨齿加工用量 530
11.2.5直齿及弧齿锥齿轮铣(刨)齿加工用量 530
11.3齿轮加工中常见问题、产生原因及解决方法 531
11.3.1滚齿加工中常见问题、产生原因及解决方法 531
11.3.2插齿加工中常见问题、产生原因及解决方法 532
11.3.3剃齿加工中常见问题、产生原因及解决方法 532
11.3.4磨齿加工中常见问题、产生原因及解决方法 533
11.3.5直齿及弧齿锥齿轮铣(刨)齿加工中常见问题、产生原因及解决方法 534
第12章切削力和功率 535
12.1车削切削力和功率 535
12.1.1 车削各类材料时切削力的比较 535
12.1.2车削高温合金的切削力和功率 535
12.1.2.1 车削变形高温合金的切削力和功率 535
12.1.2.2车削铸造高温合金的切削力和功率 536
12.1.3车削钛合金的切削力和功率 537
12.1.4 车削不锈钢的切削力和功率 538
12.1.4.1 车削马氏体不锈钢的切削力和功率 538
12.1.4.2车削奥氏体不锈钢的切削力和功率 539
12.1.5 车削高强度钢的切削力和功率 540
12.2钻削切削力和功率 542
12.2.1钻削高温合金的切削力和功率 542
12.2.1.1钻削变形高温合金的轴向力,扭矩和功率 542
12.2.1.2钻削铸造高温合金的轴向力,扭矩和功率 544
12.2.2钻削钛合金的切削力和功率 545
12.2.3钻削不锈钢的切削力和功率 546
12.2.4钻削高强度钢的切削力和功率 549
12.2.5钻削铝合金的切削力和功率 552
12.2.6钻削镁合金的切削力和功率 553
12.3.1.1 铣削变形高温合金的切削力和功率 555
12.3铣削切削力和功率 555
12.3.1铣削高温合金的切削力和功率 555
12.3.1.2铣削铸造高温合金的切削力和功率 558
12.3.2铣削钛合金的切削力和功率 558
12.3.3铣削不锈钢的切削力和功率 560
12.3.4铣削高强度钢的切削力和功率 563
12.4拉削时切削刃单位长度上的切削力 566
12.5磨削力和功率 567
13.1.1 切削液和磨削液的使用目的 570
13.1.2 切削液和磨削液的作用 570
13.1 切削液和磨削液的使用目的和作用 570
第13章切削液和磨削液 570
13.2切削液和磨削液的种类和配方 571
13.2.1 切削液和磨削液的种类 571
13.2.2常用切削液和磨削液的配方 571
1 3.2.2.1合成化学切削液配方 571
13.2.2.2乳化切削液配方 573
13.2.2.3切削油配方 576
13.2.2.4固体切削剂配方 578
13.3切削液和磨削液的选择 578
13.3.1 切削液和磨削液的标准与选择原则 578
13.3.1.1切削液和磨削液的标准 578
13.3.1.2切削液和磨削液的选择原则 579
13.3.3磨削加工时磨削液的选用 580
13.3.3.1 磨削液的特性对磨削性能的影响 580
13.3.2切削加工时切削液的选用 580
13.3.3.2磨削液的选用 581
13.4切削液和磨削液的使用方法 583
13.5.2.1清洁管理 585
13.5.2.2浓度管理 585
13.5.3切削液和磨削液的净化 585
13.5.2切削液和磨削液的使用液的管理 585
13.5.1 切削液和磨削液的保管 585
13.5切削液和磨削液的管理和废液的处理 585
13.5.4废液的处理 586
第14章切削加工零件的表面完整性 587
14.1表面完整性概念 587
14.2表面特征 587
14.2.1表面特征定义与内容 587
14.2.2表面特征的注写位置 587
14.2.3加工纹理方向符号 587
14.2.4表面粗糙度常用参数的定义与符号 589
14.2.5表面粗糙度参数的标注 590
14.2.8 表面粗糙度与零件使用性能 592
14.2.7 推荐选用的表面粗糙度值 592
14.2.6表面粗糙度与尺寸精度 592
14.2.6.1 常用切削加工方法能达到的表面粗糙度 592
14.2.6.2尺寸精度与相应的表面粗糙度 592
14.3表层特性 593
14.3.1表层定义与内容 593
14.3.2表层特性与加工强度 597
14.4表面完整性评价方法与检测技术 598
14.4.1表面完整性评价方法 598
14.4.1.1基本评价方法 598
14.4.1.2标准评价方法 599
14.4.1.3扩大评价方法 599
14.4.3.1表面粗糙度的测量方法 600
14.4.2表面完整性的综合效应 600
14.4.3表面完整性的检测技术 600
14.4.3.2金相试样制备 601
14.4.3.3表层硬度测定 601
14.4.3.4残余应力测定 603
14.4.3.5疲劳强度试验 605
14.4.3.6应力腐蚀试验 605
14.5表面完整性指导原则 606
14.5.1一般指导原则 606
14.5.2切削加工指导原则与数据 607
14.5.3磨削加工指导原则和数据 616
14.5.4后置处理工艺指导原则与数据 622
第15章切削振动及其抑制 627
15.1振动基础知识 627
15.1.1 振动的力学模型与振动标准方程 627
15.1.2 自由振动与强迫振动 627
15.1.2.1 自由振动 627
15.1.2.2强迫振动 629
15.1.3自激振动与自激条件 630
15.1.3.1 自激振动的本质及其发生机理 630
15.2.1切削加工系统简化框图 631
15.2切削颤振基础 631
15.1.3.2 自激振动中的阻尼与能量条件 631
15.2.2切削环节的动态特性 632
15.2.3机床环节的动态特性 634
15.2.3.1独立结构体的动态特性 634
15.2.3.2组合结构体的动态特性 634
15.2.3.3机床结构系统的动态特性 635
15.2.4切削系统稳定性分析 637
15.2.4.1 切削颤振发生机理 638
15.3.1 再生颤振 639
15.3几种常见的切削颤振 639
15.2.5 二元切削系统切削颤振分析结果的推广应用 639
15.2.4.2 切削颤振的临界切削用量 639
15.3.2 摩擦颤振 640
15.3.3振型耦合颤振 641
13.3.4位移干扰混合放大型颤振 642
15.3.5断续切削时的颤振 643
15.3.6切屑形成周期性引起的颤振 643
15.3.7 常见颤振的鉴别特征与消振对策 643
15.4切削振动的故障诊断方法与常用消振抑振措施 644
15.4.1 切削振动故障诊断的方法与程序 644
15.4.2 生产中常用的消振措施和方法 646
第16章切削加工的经济性 648
16.1加工成本与加工工时的构成 648
16.2影响加工成本与生产率的因素 650
16.2.1 工件材料对加工成本与生产率的影响 650
16.2.2 刀具材料对加工成本与生产率的影响 651
16.2.3 加工精度对加工成本与生产率的影响 651
16.2.4切削用量对加工成本与生产率的影响 652
16.3加工成本与生产率的计算 652
16.3.1车削成本与生产率计算实例 652
16.3.2平面铣削成本与生产率计算实例 654
16.3.3钻削45钢成本与生产率计算实例 656
16.4加工过程优化的理论与方法 658
16.4.1加工过程优化数学模型 658
16.4.1.1优化目标函数 658
16.4.1.2制约条件函数 658
16.4.1.3加工过程优化数学模型 659
16.4.2加工过程优化问题的边界极值求解方法 660
16.4.2.1边界极值的求解方法 660
16.4.2.2 边界极值求解方法的计算机实现 660
16.5 车间内切削用量的优化 662
16.5.1优化步骤 663
16.5.2 优化实例 664
附 录 666
附录1 切削加工方法与表面粗糙度 666
附录2 表面粗糙度R?值与孔、轴尺寸公差等级的相应关系 668
附录3 航空金属材料国内外牌号对照表 668
附录4 金属材料相对切削加工性系数 690
附录5 国内外刀具材料牌号对照表 697
附录6 国内外砂轮标志代号对照表 700
附录7 国外300M等高强度钢切削加工用量 705
参考文献 722
- 《市政工程基础》杨岚编著 2009
- 《工程静力学》王科盛主编 2019
- 《中国制造业绿色供应链发展研究报告》中国电子信息产业发展研究院 2019
- 《中央财政支持提升专业服务产业发展能力项目水利工程专业课程建设成果 设施农业工程技术》赵英编 2018
- 《Maya 2018完全实战技术手册》来阳编著 2019
- 《化学反应工程》许志美主编 2019
- 《绿色过程工程与清洁生产技术 张懿院士论文集精选 上》《绿色过程工程与清洁生产技术》编写组编 2019
- 《软件工程》齐治昌,谭庆平,宁洪编著 2019
- 《高等教育双机械基础课程系列教材 高等学校教材 机械设计课程设计手册 第5版》吴宗泽,罗圣国,高志,李威 2018
- 《化学工程与工艺专业实验指导》郭跃萍主编 2019
- 《莼江曲谱 2 中国昆曲博物馆藏稀见昆剧手抄曲谱汇编之一》郭腊梅主编;孙伊婷副主编;孙文明,孙伊婷编委;中国昆曲博物馆编 2018
- 《指向核心素养 北京十一学校名师教学设计 英语 七年级 上 配人教版》周志英总主编 2019
- 《植物百科彩色图鉴 第2卷》植物百科彩色图鉴编委会主编 2012
- 《远去的老调》经典文库编委会编 2019
- 《北京生态环境保护》《北京环境保护丛书》编委会编著 2018
- 《莼江曲谱 1 中国昆曲博物馆藏稀见昆剧手抄曲谱汇编之一》郭腊梅主编;孙伊婷副主编;孙文明,孙伊婷编委;中国昆曲博物馆编 2018
- 《共和国日记 1964》《共和国日记》编委会编 2019
- 《中国地方艺文荟萃 华北东北卷 第1辑 3》《中国地方艺文荟萃》编委会编 2018
- 《绿色过程工程与清洁生产技术 张懿院士论文集精选 上》《绿色过程工程与清洁生产技术》编写组编 2019
- 《中国地方艺文荟萃 华北东北卷 第1辑 1》《中国地方艺文荟萃》编委会编 2018
- 《指向核心素养 北京十一学校名师教学设计 英语 七年级 上 配人教版》周志英总主编 2019
- 《北京生态环境保护》《北京环境保护丛书》编委会编著 2018
- 《指向核心素养 北京十一学校名师教学设计 英语 九年级 上 配人教版》周志英总主编 2019
- 《高等院校旅游专业系列教材 旅游企业岗位培训系列教材 新编北京导游英语》杨昆,鄢莉,谭明华 2019
- 《中国十大出版家》王震,贺越明著 1991
- 《近代民营出版机构的英语函授教育 以“商务、中华、开明”函授学校为个案 1915年-1946年版》丁伟 2017
- 《新工业时代 世界级工业家张毓强和他的“新石头记”》秦朔 2019
- 《智能制造高技能人才培养规划丛书 ABB工业机器人虚拟仿真教程》(中国)工控帮教研组 2019
- 《陶瓷工业节能减排技术丛书 陶瓷工业节能减排与污染综合治理》罗民华著 2017
- 《全国职业院校工业机器人技术专业规划教材 工业机器人现场编程》(中国)项万明 2019