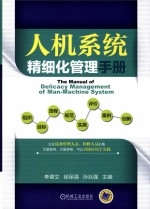
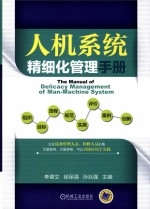
人机系统精细化管理手册PDF电子书下载
- 电子书积分:18 积分如何计算积分?
- 作 者:李葆文,徐保强,孙兆强主编;马迅,王章明,余培峰,柳草,蔡宗照,蒋坛军,车贺威,刘大永,张洪飞,袁斯殷,陆婉莹,甘艳慧,郭智聪参编
- 出 版 社:北京:机械工业出版社
- 出版年份:2014
- ISBN:9787111471929
- 页数:643 页
第1篇 设备引进前期管理篇 4
第1章 设备前期管理总体框架 4
1.1 设备前期管理组织职责 4
1.1.1 组织职责分工 4
1.1.2 系统管理 4
1.2 设备前期管理目标和手段 4
1.3 设备前期管理工作流程 5
1.4 设备前期管理制度规范 6
1.4.1 设备规划管理规定 6
1.4.2 设备选型决策管理规定 6
1.4.3 设备安装调试管理规定 6
1.4.4 设备运行初期管理规定 6
1.4.5 设备合同管理规定 6
1.5 设备前期管理实施细则 6
1.5.1 设备招标管理实施细则 6
1.5.2 设备工程监理实施细则 6
1.5.3 设备监造实施细则 6
1.5.4 设备安装实施细则 6
1.5.5 设备调试实施细则 6
1.5.6 设备验收实施细则 7
1.6 设备前期管理评价激励 7
1.6.1 评价目的 7
1.6.2 评价指标体系 7
1.6.3 评价流程 7
1.6.4 激励 7
1.7 设备前期管理案例分析 7
1.7.1 宝钢大型流程设备引进案例描述 7
1.7.2 宝钢设备引进优势 8
1.7.3 不足 8
1.8 设备前期管理创新方向 8
1.8.1 可行性研究的突破 8
1.8.2 招标选型综合评价决策模型的应用 8
1.8.3 安全、低碳、环保成为新时代设备引进的关键要素 9
第2章 设备规划和可行性研究 11
2.1 规划和可行性研究组织的职责 11
2.1.1 构成 11
2.1.2 职责 11
2.2 规划和可行性研究目标和手段 11
2.2.1 预测市场 11
2.2.2 知己知彼 11
2.2.3 把握方向 11
2.3 规划和可行性研究工作流程 11
2.4 规划和可行性研究制度规范 12
2.4.1 设备规划的主要内容 12
2.4.2 设备规划目的与依据 12
2.4.3 设备规划可行性分析 13
2.4.4 设备投资效益分析 13
2.4.5 设备寿命周期费用分析 13
2.4.6 设备规划决策流程 13
2.5 规划和可行性研究实施细则 13
2 5.1 规划组织机构和职责分工 13
2.5.2 市场预测小组工作任务描述及其工作流程 13
2.5.3 可行性研究小组工作任务描述及其工作流程 13
2.5.4 投资效益分析小组工作任务描述及其工作流程 13
2.5.5 寿命周期效益分析工作任务描述及其工作流程 13
2.5.6 规划报告研讨与汇总 13
2.5.7 规划的申报和审批 14
2.5.8 规划分解和年度实施计划工作细则 14
2.6 规划和可行性研究评价激励 14
2.6.1 评价指标体系 14
2.6.2 激励 14
2.7 规划和可行性研究案例分析 14
2.7.1 案例一 14
2.7.2 案例二 14
2.7.3 案例三 14
2.7.4 案例四 14
2.7.5 案例五 14
2.8 规划和可行性研究创新方向 15
2.8.1 第一层面的战略性思考 15
2.8.2 第二层面的战略性思考 15
第3章 设备选型决策 17
3.1 设备选型决策组织职责 17
3.1.1 构成 17
3.1.2 职责 17
3.2 设备选型决策目标和手段 17
3.3 设备选型决策工作流程 17
3.4 设备选型决策制度规范 19
3.4.1 设备选型决策规定 19
3.4.2 设备招标管理制度 19
3.5 设备选型决策实施细则 20
3.5.1 设备选型实施细则 20
3.5.2 设备采购招标实施方案 20
3.6 设备选型决策评价激励 21
3.6.1 选型过程评价指标 21
3.6.2 选型结果评价指标 21
3.6.3 招标过程评价指标 21
3.6.4 招标结果评价指标 21
3.6.5 激励 21
3.7 设备选型决策案例分析 21
3.8 设备选型决策创新方向 21
第4章 设备安装调试 24
4.1 设备安装调试组织职责 24
4.1.1 构成 24
4.1.2 职责 24
4.2 设备安装调试目标 24
4.2.1 安装目标 24
4.2.2 调试目标 24
4.2.3 验收目标 24
4.3 设备安装调试工作流程 24
4.4 设备安装调试制度 24
4.4.1 设备安装管理制度 24
4.4.2 设备调试管理制度 27
4.4.3 设备验收管理制度 27
4.5 设备安装调试实施细则 27
4.6 设备安装调试评价激励 27
4.7 设备安装调试案例分析 28
4.7.1 案例一 28
4.7.2 案例二 30
4.8 设备安装调试创新方向 30
4.8.1 充分利用社会化安装公司 30
4.8.2 用户检修和使用部门的全程参与 30
4.8.3 安装调试中的知识管理 30
第5章 设备运行初期管理 32
5.1 运行初期管理组织职责 32
5.1.1 构成 32
5.1.2 职责 32
5.2 运行初期管理目标和手段 32
5.2.1 按照时间承诺达标达产 32
5.2.2 掌握设备工艺质量要领 32
5.2.3 摸清设备运行调整及维护保养规律 32
5.3 运行初期管理工作流程 32
5.4 运行初期管理制度规范 33
5.4.1 设备运行初期组织职责分工 33
5.4.2 设备运行初期管理要点 33
5.5 运行初期管理实施细则 34
5.5.1 设备操作工艺流程图 34
5.5.2 设备操作可视化细则 34
5.5.3 设备保养可视化细则 34
5.5.4 设备运行状态跟踪记录表 34
5.5.5 质量控制关键操作指南 35
5.5.6 设备检修流程图 35
5.5.7 设备初期管理总结模板 35
5.6 运行初期管理评价激励 35
5.6.1 过程指标 35
5.6.2 结果指标 36
5.7 运行初期管理案例分析 36
5.8 运行初期管理创新方向 36
第6章 设备合同管理 39
6.1 设备合同管理组织职责 39
6.1.1 构成 39
6.1.2 职责 39
6.2 设备合同管理目标和手段 39
6.2.1 目标 39
6.2.2 手段 39
6.3 设备合同管理工作流程 39
6.4 设备合同管理制度规范 39
6.4.1 合同谈判规范 39
6.4.2 合同签订规范 41
6.4.3 合同执行规范 43
6.5 设备合同管理实施细则 44
6.5.1 合同谈判实施细则 44
6.5.2 合同签订实施细则 45
6.5.3 合同执行实施细则 46
6.6 设备合同管理评价激励 46
6.6.1 评价目的 46
6.6.2 评价内容 46
6.6.3 激励方式 46
6.7 设备合同管理案例分析 47
6.7.1 案例一 47
6.7.2 案例二 47
6.8 设备合同管理创新方向 47
第2篇 资产台账知识管理篇 52
第1章 设备分类与资产编号 52
1.1 设备分类与资产编号组织职责 52
1.1.1 设备管理部门 52
1.1.2 财会部门及设备使用单位 52
1.2 设备分类与资产编号目的 52
1.3 设备分类与资产编号工作流程 52
1.4 设备分类与资产编号原则 52
1.5 设备分类与资产编号实施细则 53
1.5.1 设备分类 53
1.5.2 设备资产编号 56
1.6 设备分类与资产编号的评价激励 56
1.7 设备分类与资产编号的案例分析 57
1.8 设备分类与资产编号的创新方向 57
第2章 设备台账和设备卡片 59
2.1 设备台账和设备卡片组织职责 59
2.1.1 构成 59
2.1.2 职责 59
2.2 设备台账和设备卡片目的 59
2.3 设备台账和设备卡片工作流程 59
2.4 设备台账和设备卡片制度规范 59
2.5 设备台账和设备卡片实施细则 59
2.5.1 建立设备台账 59
2.5.2 设备卡片 61
2.6 设备台账和设备卡片的评价激励 61
2.7 设备台账和设备卡片的案例分析 61
2.8 设备台账和设备卡片的创新方向 62
第3章 设备档案与资料管理 64
3.1 设备档案与资料管理组织职责 64
3.1.1 设备管理部门 64
3.1.2 企业维修部门和生产车间(分厂) 64
3.2 设备档案与资料管理目标 64
3.3 设备档案与资料管理工作流程 64
3.4 设备档案与资料管理要求 64
3.4.1 设备档案与资料管理基本要求 64
3.4.2 设备档案的编制要求 64
3.4.3 收集编制资料注意事项 64
3.5 设备档案与资料管理实施细则 66
3.5.1 设备档案与资料内容 66
3.5.2 设备档案与资料的管理内容 67
3.6 设备档案与资料管理的评价激励 67
3.7 设备档案与资料管理案例分析 67
3.7.1 设备档案管理办法主要内容 67
3.7.2 设备资料室管理制度 68
3.8 设备档案与资料管理创新方向 68
第3篇 赢在基层团队成长篇 72
第1章 团队培训 72
1.1 团队培训推行组织及职责 72
1.2 团队培训的主要内容和目标 72
1.2.1 工作现场培训 72
1.2.2 集中培训 72
1.2.3 好的培训 73
1.3 团队培训的工作流程 73
1.3.1 公司级别培训的主要流程 73
1.3.2 班组培训流程 74
1.4 团队培训的制度规范 75
1.4.1 确定培训需求 75
1.4.2 设计培训内容 75
1.5 团队培训的实施细则 75
1.6 团队培训的评价与激励 75
1.6.1 团队培训的评价 75
1.6.2 团队培训的激励 76
1.7 团队培训的案例分析 76
1.8 团队培训的创新方法 77
1.8.1 培训角色的创新 77
1.8.2 培训方法的创新 77
第2章 团队沟通 80
2.1 团队沟通的组织及职责 80
2.2 团队沟通的主要内容 80
2.2.1 质量管理方面 80
2.2.2 设备管理方面 81
2.2.3 物料管理方面 81
2.2.4 关于人员方面的沟通 81
2.2.5 其他方面涉及的沟通管理 81
2.3 团队沟通的工作流程 81
2.4 团队沟通的实施细则 84
2.4.1 文件(含文书)沟通 84
2.4.2 会议沟通 84
2.4.3 沟通的反馈 85
2.5 团队沟通案例分析 85
2.6 团队沟通的创新方向 86
2.6.1 班组例会 86
2.6.2 橱窗展示 86
2.6.3 绩效面谈 86
2.6.4 班组长谈心 86
2.6.5 非正式的随时沟通 86
第3章 有氧活动 88
3.1 有氧活动的组织职责 88
3.2 有氧活动的主要内容和目标 89
3.2.1 OPL的主要内容 89
3.2.2 OPS的主要内容 89
3.3 有氧活动的工作流程 90
3.3.1 OPL的工作流程 90
3.3.2 OPS的工作流程 90
3.4 有氧活动的制度规范 90
3.5 有氧活动的实施细则 90
3.5.1 OPL的实施细则 90
3.5.2 OPS的实施细则 92
3.6 有氧活动的评价与激励 92
3.6.1 员工编制的OPL 92
3.6.2 员工编制的OPS 96
3.6.3 奖励 100
3.7 有氧活动的案例分析 100
3.8 有氧活动的创新方向 101
3.8.1 OPL展示形式创新 101
3.8.2 OPL概念的延伸 101
3.8.3 OPS应用方式的创新 102
3.8.4 从OPS到小组改善 102
第4章 团队激励 107
4.1 团队激励的组织及职责 107
4.1.1 组织的构成 107
4.1.2 组织的职责 107
4.2 团队激励的主要内容和目标 107
4.2.1 正向激励 107
4.2.2 负向激励 108
4.2.3 定期激励 108
4.2.4 不定期激励 108
4.3 团队激励的工作流程 108
4.3.1 定期激励 108
4.3.2 不定期激励 108
4.4 团队激励种类的定义 108
4.5 团队激励的实施细则 109
4.5.1 员工激励制度具体内容 109
4.5.2 员工激励制度需求的提出 109
4.6 团队激励的效果评价与激励 109
4.6.1 评价指标体系 109
4.6.2 激励 110
4.7 团队激励案例分析 110
4.8 团队激励的创新方向 110
4.8.1 团队激励的活性化 110
4.8.2 团队激励的需求化 111
4.8.3 团队激励的生活化 111
4.8.4 团队激励的菜单化 112
第5章 团队看板 115
5.1 团队看板的组织职责 115
5.2 团队看板的主要内容和目标 116
5.3 团队看板的工作流程 116
5.4 团队看板的制度规范编制 117
5.4.1 目标分解展示板 117
5.4.2 文化士气看板 118
5.4.3 质量控制看板 118
5.4.4 设备计划保全日历 119
5.4.5 区域责任图 119
5.4.6 安全看板 119
5.4.7 疑难点清单 120
5.4.8 班组管理现况板 121
5.4.9 QC工具与改善 121
5.4.10 小组活动板 122
5.4.11 TnPM诊断现况板 122
5.5 团队看板的实施细则和工作要求 123
5.5.1 看板版式及内容要求 123
5.5.2 看板管理的具体要求 123
5.5.3 看板信息的更新 124
5.5.4 看板的监察与维护 124
5.6 团队看板的评价和激励 124
5.7 团队看板的案例分析 124
5.8 团队看板的创新方向 125
第6章 团队领导 127
6.1 团队领导的组织职责 127
6.1.1 按照主管管理的五大职责分类 127
6.1.2 按照生产的管控目标分类 127
6.1.3 按生产要素分类 127
6.1.4 八大修炼 128
6.1.5 结果是以过程为导向 128
6.2 团队领导的目标 128
6.3 团队领导的工作流程 129
6.4 团队领导的制度规范 130
6.5 团队领导的工作细则 130
6.5.1 本部门工作要点分时段制订 131
6.5.2 上班前该做什么? 131
6.5.3 生产前准备要点 131
6.5.4 生产过程中工作要点(人) 131
6.5.5 生产过程中工作要点(机) 131
6.5.6 生产过程中工作要点(料) 131
6.5.7 生产过程中工作要点(法) 132
6.5.8 生产过程中工作要点(环) 132
6.5.9 生产过程中工作要点(品质) 132
6.5.10 生产过程中工作要点(士气) 132
6.5.11 信息管理 132
6.5.12 下班前工作要点 133
6.5.13 其他专题会议与人选 133
6.5.14 其他专业项目的工作 133
6.6 团队领导的评价和激励 134
6.6.1 团队领导的评价 134
6.6.2 团队领导的激励 137
6.7 团队领导的案例分析 138
6.7.1 团队领导职务说明书(车间主任级) 138
6.7.2 团队领导每日工作细分案例 139
6.8 团队领导的创新方向 147
6.8.1 团队领导者的角色变革 147
6.8.2 团队领导者知识结构的转变 147
6.8.3 团队领导考核方式的转变 147
第4篇 精心创造卓越现场篇 152
第1章 创造卓越现场——6S 152
1.1 6S管理的组织职责 152
1.1.1 6S项目推行委员会的主要职责 152
1.1.2 6S项目推行小组的主要职责 152
1.1.3 6S项目检查小组的主要职责 153
1.1.4 各实施小组的主要职责 153
1.1.5 公司各级人员在6S活动中的职责 153
1.2 6S管理的主要内容与目标 154
1.2.1 6S管理的主要内容 154
1.2.2 6S管理的目标 154
1.3 6S管理的工作流程 155
1.3.1 实施6S的阶段 155
1.3.2 实施6S的流程 155
1.4 6S管理的制度规范编制 156
1.4.1 6S责任区域划分 156
1.4.2 6S准则(要求、规范) 157
1.4.3 6S活动程序 157
1.5 6S管理的实施细则和展开步骤 158
1.5.1 6S管理的实施细则 158
1.5.2 6S管理的展开步骤 158
1.6 6S管理的评价与激励 159
1.6.1 6S评价的方式分两类 159
1.6.2 6S评委评审6S的流程 159
1.6.3 自主检查 160
1.6.4 6S评审标准 160
1.6.5 6S检查结果的处置和改善 164
1.7 6S管理的企业案例分析 166
1.8 6S管理的创新方向 168
第2章 创造卓越现场——清除6H 170
2.1 6H的组织和职责 170
2.1.1 6H的组织 170
2.1.2 6H组织的职责 170
2.2 6H管理的主要内容与目标 170
2.2.1 6H管理的主要内容 170
2.2.2 清除6H的管理目标 173
2.3 6H管理的工作流程 173
2.4 6H管理的制度规范编制 176
2.5 6H管理的查找指引和分析工具 177
2.5.1 6H管理的查找指引 177
2.5.2 6H管理的分析工具 182
2.6 6H管理的评价与激励 191
2.6.1 6H改善的评价指标 191
2.6.2 6H改善的激励 191
2.7 6H管理的企业案例分析 191
2.8 6H管理的创新方向 192
第3章 可视化管理 194
3.1 可视化管理的组织职责 194
3.2 可视化管理的主要内容与目标 195
3.2.1 可视化管理的目的 195
3.2.2 可视化管理的目标 195
3.3 可视化管理的工作流程 195
3.4 可视化管理的制度规范编制 196
3.4.1 可视化推进准备 196
3.4.2 可视化的组织职责 196
3.4.3 可视化的展开实施检查、评比和激励 196
3.5 可视化管理的实施细则和工作要求 196
3.5.1 建立推进组织 196
3.5.2 制定活动计划 196
3.5.3 现场诊断,识别可视化对象清单 196
3.5.4 可视化对象实施 197
3.5.5 可视化管理手册编制 197
3.6 可视化管理的评价与激励 197
3.6.1 评价流程 197
3.6.2 激励 198
3.7 可视化管理的企业案例分析 198
3.8 可视化管理的创新方向 199
第4章 定置管理 202
4.1 定置管理的组织职责 202
4.2 定置管理的主要内容与目标 203
4.2.1 定置管理的主要内容 203
4.2.2 定置管理的目标 203
4.3 定置管理的工作流程 204
4.4 定置管理的制度规范编制 205
4.4.1 定置管理推进准备 205
4.4.2 定置管理的组织职责 205
4.4.3 定置管理展开实施 205
4.5 定置管理的实施细则和工作要求 205
4.6 定置管理的评价和激励 206
4.6.1 评价流程 206
4.6.2 激励 206
4.7 定置管理的企业案例分析 206
4.8 定置管理的创新方向 207
第5篇 全员自主维护保障篇 212
第1章 全员自主维护保障总体框架 212
1.1 全员自主维护保障组织职责 212
1.2 自主维护保障基本目标 212
1.2.1 设备功能本质状态改善方面变化 212
1.2.2 员工维护技能素质方面变化 212
1.2.3 设备小停机快速处理方面变化 212
1.3 全员自主维护保障工作流程 212
1.3.1 四大流程阶段 212
1.3.2 自主维护各阶段主要工作内容 213
1.4 全员自主维护规范 214
1.4.1 自主维护推进管理办法 214
1.4.2 自主维护活动技术标准 214
1.5 自主维护实施 214
1.5.1 防止人为劣化意识的教育 214
1.5.2 设备原理与结构培训 215
1.5.3 工具技术准备 215
1.5.4 安全防范强化 215
1.6 全员自主维护保障评价 215
1.6.1 自主维护管理策划能否体现5W2H2C1T原则 215
1.6.2 活动过程组织领导的参与程度与职责落实情况 216
1.6.3 标准的完整性与可操作性 216
1.6.4 自主维护活动要求执行是否到位 216
1.6.5 指标是否完成 216
1.6.6 自主维护效果评价及推广 216
1.7 全员自主维护推进管理案例分析 216
1.8 全员自主维护管理的创新方向 216
1.8.1 巧用杠杆与灵活维护 216
1.8.2 创新方法与综合推进 217
第2章 设备清扫 219
2.1 设备清扫组织职责 219
2.2 设备清扫的目标和主要内容 219
2.2.1 设备清扫的目标 219
2.2.2 设备清扫主要内容 219
2.3 设备清扫工作流程 219
2.4 设备清扫作业制度规范 220
2.4.1 “谁使用谁清扫”原则 220
2.4.2 清扫基准书 220
2.5 设备清扫活动实施 220
2.5.1 选择清扫点 220
2.5.2 安全清扫 220
2.5.3 全面清扫 221
2.5.4 闭环清扫 221
2.6 设备清扫评价 221
2.6.1 定期组织考核 221
2.6.2 清扫评价标准 221
2.7 设备清扫案例 222
2.7.1 灰尘遮掩“光眼”导致提升机运行不稳定 222
2.7.2 用心对待清扫维护工作 222
2.8 设备清扫管理创新 222
2.8.1 不断提升设备清扫必要性的认识 222
2.8.2 不断创新清扫工具开发 223
2.8.3 严格交接班管理考核 224
第3章 设备点检 226
3.1 设备点检组织职责 226
3.1.1 点检定义与分类 226
3.1.2 点检工作主要责任部门与岗位职责 226
3.2 设备点检目标 227
3.3 设备点检工作流程 227
3.4 设备点检规范 228
3.5 设备点检实施 229
3.5.1 编制点检计划 229
3.5.2 做好点检准备 230
3.5.3 组织点检实施 230
3.6 点检评价 232
3.6.1 点检要素完备性 232
3.6.2 点检实绩情况 232
3.6.3 点检激励机制的建立 233
3.7 设备点检案例 233
3.7.1 钟表点检法 233
3.7.2 “五感法”点检 233
3.7.3 点检基准实例 234
3.8 点检创新 236
3.8.1 将可视化管理与防呆手法相结合,广泛运用到点检工作中 236
3.8.2 运用现代检测工具,发挥精密检测功效 236
3.8.3 融合CMMS信息技术,开发简洁实用的点检流程与手段 236
第4章 设备保养 239
4.1 设备保养组织职责 239
4.1.1 保养定义与分类 239
4.1.2 主要部门与岗位职责 239
4.2 设备保养目标与内容 239
4.2.1 保养目标 239
4.2.2 保养内容 239
4.3 设备保养工作流程 240
4.4 设备保养规范 241
4.5 设备保养实施 241
4.5.1 编制保养计划 241
4.5.2 定人 241
4.5.3 定时 241
4.5.4 定点 242
4.5.5 定方法 242
4.5.6 定项目 242
4.5.7 定标准 243
4.5.8 定记录 245
4.6 设备保养管理的评价 245
4.6.1 保养计划达成率 245
4.6.2 设备故障停机率 245
4.6.3 设备完好率 245
4.6.4 综合保养考核 245
4.7 规范化设备保养管理案例分析 245
4.7.1 记录卡定位法 245
4.7.2 设备保养维护完好率考核表 246
4.8 设备保养探索创新 247
第5章 “三闭环”流程实施 250
5.1 “三闭环”组织职责 250
5.1.1 “三闭环”定义与构成 250
5.1.2 “三闭环”维护主要部门职责 250
5.2 “三闭环”的目的 250
5.3 “三闭环”流程 250
5.4 “三闭环”规范 251
5.4.1 AM自主维护基准书 251
5.4.2 “三闭环”维修综合总基准书 251
5.5 “三闭环”实施细则 252
5.5.1 AM自主维护闭环开始与深入 252
5.5.2 PM专业维护闭环的触发和嵌入 252
5.5.3 MP维修预防闭环触发和嵌入 253
5.5.4 及时传递维修工单 253
5.6 “三闭环”案例 255
5.6.1 AM闭环自主设计 255
5.6.2 机械维修“请修单”作业法 255
5.6.3 清扫点检维保总基准书 255
5.7 “三闭环”管理评价 257
5.7.1 自主维护技能培训考评 257
5.7.2 专业维保实施考评 257
5.8 “三闭环”创新 257
第6篇 全优规范润滑管理篇 262
第1章 润滑六定管理 262
1.1 设备润滑六定管理的组织职责 262
1.1.1 组织职责分工 262
1.1.2 系统管理 262
1.2 润滑六定管理的主要内容和目标 262
1.2.1 定点 262
1.2.2 定人 262
1.2.3 定质 263
1.2.4 定量 264
1.2.5 定法 265
1.2.6 定期 265
1.2.7 管理目标 266
1.3 润滑六定管理工作流程 266
1.4 润滑六定管理的制度规范 266
1.5 润滑六定管理的实施细则 266
1.5.1 设备润滑六定的技术规范 266
1.5.2 润滑六定文件的制定流程 267
1.5.3 设备润滑作业责任制 267
1.5.4 润滑记录规范 267
1.5.5 润滑油领用统计规范 267
1.5.6 泄漏预防 267
1.5.7 润滑故障分析 267
1.6 润滑六定管理的评价激励 267
1.6.1 评价目的 267
1.6.2 评价指标体系 267
1.6.3 评价基本流程 268
1.6.4 激励 268
1.7 润滑六定管理的案例分析 268
1.8 润滑六定管理的创新方向 268
1.8.1 润滑六定标准与最新的技术相结合 268
1.8.2 定量加油的进步 268
1.8.3 润滑油定质的优化 268
第2章 润滑二洁管理 271
2.1 “二洁”管理的组织职责 271
2.1.1 组织职责分工 271
2.1.2 系统管理 271
2.2 “二洁”管理的主要内容和目标 271
2.2.1 润滑部位的清洁 271
2.2.2 润滑工具的清洁 272
2.2.3 润滑“二洁”管理的目标 272
2.3 “二洁”管理的工作流程 272
2.4 润滑“二洁”管理的制度规范 273
2.5 “二洁”管理的实施细则 273
2.6 润滑“二洁”管理的评价激励 273
2.6.1 评价指标体系 273
2.6.2 评价流程 274
2.6.3 激励 274
2.7 “二洁”管理的案例分析 274
2.8 “二洁”管理的创新方向 274
第3章 润滑三级过滤管理 277
3.1 三级过滤的组织职责 277
3.1.1 组织职责分工 277
3.1.2 系统管理 277
3.2 三级过滤的主要内容和目标 277
3.2.1 什么是三级过滤? 277
3.2.2 三级过滤的重要意义 277
3.2.3 三级过滤的实现手段 277
3.2.4 在用油的过滤 278
3.3 三级过滤的工作流程 279
3.4 三级过滤的制度规范 279
3.4.1 三级过滤管理规定 279
3.4.2 润滑油的再生使用管理规定 279
3.4.3 三级过滤的培训 279
3.5 三级过滤管理的实施细则 279
3.5.1 润滑油的定期监测规范 279
3.5.2 润滑过滤装置 280
3.5.3 滤芯管理规范 280
3.5.4 润滑培训的流程规范 280
3.6 三级过滤的评价激励 280
3.6.1 三级过滤评价指标 280
3.6.2 评价流程 280
3.6.3 激励 280
3.7 三级过滤的案例分析 280
3.8 三级过滤的创新方向 280
第4章 换油管理 283
4.1 换油管理的组织职责 283
4.1.1 组织职责分工 283
4.1.2 系统管理 283
4.2 换油管理的主要内容和目标 283
4.2.1 换油计划 283
4.2.2 趋势管理 283
4.2.3 换油管理的目标 283
4.3 换油管理的工作流程 283
4.4 换油管理的制度规范 284
4.4.1 润滑油更换管理规定 284
4.4.2 废油处理的若干规定 284
4.5 换油管理的实施细则 284
4.5.1 润滑油更换作业流程 284
4.5.2 润滑油更换判断标准 284
4.5.3 润滑油使用统计分析流程 284
4.6 换油管理的评价激励 284
4.7 换油管理的案例分析 285
4.8 换油管理的创新方向 285
第5章 油液分析与故障诊断 287
5.1 油液分析和故障诊断的组织职责 287
5.1.1 组织职责分工 287
5.1.2 系统管理 287
5.2 油液分析和故障诊断的主要内容和目标 287
5.2.1 油液分析的作用 287
5.2.2 常用的油液分析方法 288
5.2.3 油液分析与故障诊断的作用 291
5.2.4 故障的趋势管理 292
5.2.5 油液取样管理 293
5.3 油液分析和故障诊断的工作流程 294
5.4 油液分析和故障诊断的制度规范 294
5.4.1 油液分析管理 294
5.4.2 润滑油取样管理 294
5.4.3 故障管理 294
5.4.4 油库采样管理 294
5.5 油液分析和故障诊断的实施细则 294
5.5.1 油液分析取样点确定 294
5.5.2 油液化验作业流程 295
5.5.3 油品更换参考标准 295
5.5.4 故障分析流程 295
5.6 油液分析和故障诊断的评价激励 295
5.6.1 评价标准 295
5.6.2 评价流程 295
5.6.3 激励 295
5.7 油液分析和故障诊断的案例分析 295
5.8 油液分析和故障诊断的创新方向 296
第6章 润滑站管理 298
6.1 润滑站管理的组织职责 298
6.1.1 组织职责分工 298
6.1.2 系统管理 298
6.2 润滑站管理的主要内容和目标 298
6.2.1 公司润滑站管理 298
6.2.2 车间润滑站的日常维护 299
6.3 润滑站管理的工作流程 300
6.4 润滑站管理的制度规范 301
6.4.1 润滑站管理制度 301
6.4.2 油料采购领用管理规定 301
6.4.3 润滑站安全管理制度 301
6.5 润滑站管理的实施细则 301
6.5.1 油料采购申请流程 301
6.5.2 油料领用流程 301
6.5.3 润滑站油料化验流程 301
6.5.4 润滑站油料化验判断标准 302
6.6 润滑站管理的评价激励 302
6.6.1 评价标准 302
6.6.2 评价流程 302
6.6.3 激励 302
6.7 润滑站管理的案例分析 302
6.8 润滑站管理的创新方向 303
第7章 润滑管理体系的评价 305
7.1 润滑管理体系评价的组织职责 305
7.1.1 组织职责分工 305
7.1.2 系统管理 305
7.2 润滑管理评价的内容和主要目标 305
7.2.1 评价的内容 305
7.2.2 润滑管理评价的标准 306
7.2.3 评价的目标 306
7.3 润滑管理评价的工作流程 306
7.4 润滑管理评价的制度规范 306
7.4.1 润滑管理体系的评价 306
7.4.2 评价的KPI设计原则 307
7.4.3 润滑管理评价的周期安排 307
7.5 润滑管理评价的实施细则 307
7.5.1 润滑管理体系评价标准 307
7.5.2 管理体系评价项目配分标准 307
7.5.3 评价的项目要素 307
7.6 润滑管理评价的激励 307
7.7 润滑管理评价的案例分析 308
7.8 润滑管理评价的创新方向 308
第7篇 检维修系统设计优化篇 312
第1章 维修策略设计 312
1.1 维修策略设计的组织职责 312
1.1.1 组织职责分工 312
1.1.2 系统管理 312
1.2 维修策略设计的内容和目标 312
1.2.1 维修策略设计的内容 312
1.2.2 维修策略设计的原则 313
1.2.3 常用维修策略 313
1.3 维修策略设计的工作流程 325
1.4 维修策略设计的制度规范 326
1.4.1 设备维修策略设计 326
1.4.2 设备维修策略的管理 326
1.4.3 维修策略的优化 326
1.4.4 维修策略设计的培训 326
1.5 维修策略设计规范的实施细则 326
1.5.1 设备维修策略设计的要素 326
1.5.2 维修策略设计的流程 326
1.5.3 设备运行的信息收集类别 326
1.6 维修策略设计的评价激励 326
1.7 维修策略设计的案例分析 327
1.8 维修策略设计的创新方向 328
第2章 设备信息采集 331
2.1 设备信息采集的组织职责 331
2.1.1 组织职责分工 331
2.1.2 系统管理 331
2.2 设备信息采集的内容和目标 331
2.2.1 设备信息采集的内容 331
2.2.2 设备信息的分析和故障诊断 333
2.2.3 设备信息采集方式的选择 335
2.3 设备信息采集的工作流程 335
2.4 设备信息采集的制度规范 336
2.4.1 点检的管理 336
2.4.2 状态监测的应用 336
2.4.3 点检的培训 336
2.5 设备信息采集的实施细则 336
2.5.1 设备点检文件设计的要素 336
2.5.2 点检的八定一成管理 336
2.5.3 状态监测的设计要素 336
2.5.4 培训管理 336
2.5.5 故障的诊断流程 336
2.6 设备信息采集的评价激励 337
2.7 设备信息采集的案例分析 337
2.7.1 案例一 337
2.7.2 案例二 338
2.8 设备信息采集的创新方向 338
第3章 维修组织设计 341
3.1 维修组织设计的组织职责 341
3.1.1 组织职责分工 341
3.1.2 系统管理 341
3.2 维修组织设计的主要内容和工作目标 341
3.2.1 维修组织设计的原则 341
3.2.2 常见的维修组织结构特点 342
3.2.3 维修组织设计的目标 343
3.3 维修组织设计的工作流程 343
3.4 维修组织设计的制度规范 344
3.4.1 设备维修组织建立的目标 344
3.4.2 维修组织设计的原则 344
3.4.3 组织设计的实施 344
3.4.4 组织设计的效果评价 344
3.5 设备维修组织设计的实施细则 344
3.5.1 维修组织设计的KPI指标 344
3.5.2 维修组织设计的流程 344
3.5.3 维修组织考核流程 344
3.6 维修组织设计的评价激励 344
3.7 维修组织设计的案例分析 344
3.8 维修组织设计的创新方向 345
3.8.1 维修组织的变革 345
3.8.2 维修组织再造过程 346
第4章 维修资源配置 349
4.1 维修资源配置的组织职责 349
4.1.1 组织职责分工 349
4.1.2 系统管理 349
4.2 维修资源配置的主要内容和目标 349
4.2.1 维修资源配置的原则 349
4.2.2 维修资源的整合 350
4.2.3 维修资源配置的目标 351
4.3 维修资源配置的工作流程 351
4.4 维修资源配置的制度规范 351
4.4.1 自主维护的管理 351
4.4.2 专业维修队伍的管理 351
4.4.3 委外维修的管理 352
4.4.4 培训管理 352
4.4.5 维修资源的优化 352
4.5 维修资源配置的实施细则 352
4.5.1 员工自主维护管理细则 352
4.5.2 专业维修人员管理细则 352
4.5.3 外包管理员管理细则 352
4.5.4 外包合同管理实施细则 352
4.5.5 招标管理细则 352
4.6 维修资源配置的评价激励 352
4.6.1 评价的指标体系 352
4.6.2 评价流程 352
4.6.3 激励 352
4.7 维修资源配置的案例分析 353
4.8 维修资源配置的创新方向 354
第5章 维修计划制订 356
5.1 维修计划制订的组织职责 356
5.1.1 组织职责分工 356
5.1.2 系统管理 356
5.2 维修计划制订的主要内容和目标管理 356
5.2.1 维修计划制订的原则 356
5.2.2 维修计划制订的要素 356
5.2.3 维修计划制订的管理 356
5.2.4 计划的目标管理 357
5.3 维修计划制订的工作流程 357
5.4 维修计划制订的制度规范 358
5.4.1 维修计划编制原则 358
5.4.2 维修计划制订 358
5.4.3 维修计划的实施 358
5.4.4 维修计划与信息化 358
5.5 维修计划制订的实施细则 358
5.5.1 维修计划编制的要素 358
5.5.2 维修计划的指标体系 359
5.5.3 维修计划的评价体系 359
5.6 维修计划制订的评价激励 359
5.7 维修计划制订的案例分析 359
5.7.1 案例一 359
5.7.2 案例二 360
5.8 维修计划制订的创新方向 361
第6章 大检修管理 363
6.1 大检修管理的组织职责 363
6.1.1 组织职责分工 363
6.1.2 系统管理 363
6.2 大检修管理的主要内容和目标计划 363
6.2.1 大检修的计划管理 363
6.2.2 大检修的安全管理 363
6.2.3 大检修的成本管理 364
6.2.4 大检修供应商的管理 364
6.2.5 大检修的过程管理 365
6.2.6 大检修的现场管理 366
6.2.7 大检修质量管理的工作重点 366
6.2.8 大检修信息化与知识资产管理 368
6.3 大检修管理的工作流程 368
6.4 大检修管理的制度规范 369
6.4.1 设备大检修管理内容 369
6.4.2 供应商管理 369
6.4.3 大检修的管理评审 369
6.4.4 设备技术鉴定管理 369
6.4.5 开工管理 370
6.4.6 档案管理 370
6.5 大检修管理的实施细则 370
6.5.1 大检修的管理流程要素 370
6.5.2 大检修计划的制订要素 370
6.5.3 供应商管理要素 370
6.5.4 大检修现场管理要素 370
6.5.5 设备技术质量鉴定标准要素 370
6.5.6 开工管理 370
6.5.7 大检修档案管理要素 370
6.6 大检修管理的评价激励 370
6.7 大检修管理的案例分析 371
6.8 大检修管理的创新方向 372
第7章 维修标准规范 375
7.1 维修标准规范的组织职责 375
7.1.1 组织职责分工 375
7.1.2 系统管理 375
7.2 维修标准规范的主要内容和目标 375
7.2.1 维修标准规范的制订 376
7.2.2 维修标准规范的日常管理 376
7.2.3 维修标准规范的实施 376
7.2.4 维修标准规范的效果评价管理 376
7.2.5 维修标准规范的优化 376
7.2.6 维修标准规范管理的目标 377
7.3 维修标准规范的工作流程 377
7.4 维修标准规范管理的制度规范 378
7.4.1 设备维修作业规范 378
7.4.2 维修技术规范管理 378
7.4.3 维修质量验收规范管理 378
7.5 维修标准规范管理制度的实施细则 378
7.5.1 设备维修流程规范的要素 378
7.5.2 设备维修技术标准的要素 378
7.5.3 设备维修质量验收标准的要素 378
7.6 维修标准规范的评价激励 378
7.7 维修标准规范的案例分析 379
7.7.1 案例一 379
7.7.2 案例二 379
7.7.3 案例三 379
7.7.4 案例四 379
7.8 维修标准规范的创新方向 382
第8篇 六项改善持续进步篇 391
引言 391
第1章 六项改善培训 391
1.1 六项改善培训的组织职责 391
1.2 六项改善培训的主要内容和目标 391
1.3 六项改善培训的工作流程 392
1.4 六项改善培训的制度规范编制 392
1.4.1 六项改善培训制度总则 392
1.4.2 六项改善培训的评估管理 394
1.4.3 内部培训责任人和外聘培训讲师管理 394
1.5 六项改善培训的实施流程和工作要求 394
1.6 六项改善培训的评价和激励 397
1.7 六项改善培训的创新方向 399
第2章 改善技巧方法研究 401
2.1 改善技巧方法研究的组织职责 401
2.2 改善技巧方法研究的主要内容和目标 401
2.3 改善技巧方法研究的工作流程 402
2.4 改善技巧方法研究的制度规范编制 403
2.4.1 提案/项目申报 403
2.4.2 立项审批 403
2.4.3 项目实施 403
2.4.4 项目过程监控 404
2.4.5 项目成果申报 404
2.4.6 项目成果评审 404
2.4.7 项目成果发布评审 404
2.4.8 成果奖励 404
2.4.9 成果推广应用 404
2.5 改善技巧方法研究的实施流程和工作要求 404
2.6 改善技巧方法研究的评价和激励 405
2.7 改善技巧方法研究案例分析 405
2.8 改善技巧方法研究的创新方向 406
第3章 六项改善的实施 409
3.1 六项改善实施的组织职责 409
3.2 六项改善实施的主要内容和目标 409
3.3 六项改善实施的工作流程 409
3.4 六项改善实施的制度规范编制 409
3.4.1 目的 409
3.4.2 适用范围 409
3.4.3 小组改善实施 410
3.4.4 审核 410
3.4.5 改善跟踪 410
3.4.6 知识共享 410
3.5 六项改善实施的实施流程和工作要求 410
3.6 六项改善实施的评价和激励 411
3.7 六项改善实施的案例分析 411
3.8 六项改善实施的创新方向 412
第4章 六项改善的评价和激励 414
4.1 改善评价和激励的组织职责 414
4.2 改善评价和激励的主要内容和目标 414
4.2.1 现金奖励标准(例) 414
4.2.2 荣誉与职业奖励 414
4.3 改善评价和激励的工作流程 414
4.4 改善评价和激励的制度规范编制 415
4.4.1 目的 415
4.4.2 适用范围 415
4.4.3 改善评价和激励 415
4.5 改善评价和激励的实施流程和工作要求 415
4.6 改善评价和激励的创新方向 417
第9篇 精细备件管控模式篇 422
第1章 备件管理总体框架 422
1.1 备件管理的组织职责 422
1.1.1 组织职责分工 422
1.1.2 系统管理 422
1.2 备件管理的主要内容和目标 422
1.2.1 备件管理的主要内容 422
1.2.2 备件管理目标 423
1.3 备件管理的工作流程 423
1.3.1 某石化企业备件管理工作流程 423
1.3.2 某汽车企业备件管理工作流程 424
1.3.3 某企业备件管理工作流程 424
1.3.4 备件无库存管理业务流程 424
1.3.5 网络虚拟备件库的业务流程 424
1.4 备件管理的制度规范编制 427
1.4.1 备件的计划控制管理 427
1.4.2 备件的自制和国产化 427
1.4.3 备件的修旧利废 427
1.4.4 备件供应商管理 427
1.4.5 备件采购和合同管理 427
1.4.6 备件的验收和入库 427
1.4.7 备件的库存管理 427
1.4.8 备件的出库与领用 427
1.4.9 备件图样和技术资料管理 427
1.4.10 备件的统计管理 427
1.4.11 备件的外销和报废 427
1.5 备件管理的实施细则和工作要求 427
1.5.1 备件计划控制的实施细则和工作要求 428
1.5.2 备件自制和国产化的实施细则和工作要求 428
1.5.3 备件修旧利废的实施细则和工作要求 428
1.5.4 备件供应商管理的实施细则和工作要求 428
1.5.5 备件采购和合同管理的实施细则和工作要求 429
1.5.6 备件库存管理的实施细则和工作要求 429
1.5.7 备件图样和技术资料管理的实施细则和工作要求 429
1.5.8 备件统计管理的实施细则和工作要求 430
1.5.9 备件外销和报废的实施细则和工作要求 430
1.6 备件管理的评价和激励 430
1.6.1 评价目的 430
1.6.2 评价指标体系 430
1.6.3 评价流程 431
1.6.4 激励 431
1.7 备件管理的案例分析 432
1.7.1 某钢铁集团备件内部虚拟共享机制 432
1.7.2 某钢厂备件国产化探索 432
1.7.3 某电厂设备备件国产化的探索 432
1.8 备件管理的创新方向 433
1.8.1 备件供管模式的创新方向 433
1.8.2 网络虚拟备件库 433
1.8.3 周期备件费用最小化 433
1.8.4 备件管理其他方面的创新方向 434
第2章 备件分类和编码库存模型优化 436
2.1 备件技术管理的组织职责 436
2.1.1 构成 436
2.1.2 职责 436
2.2 备件技术管理的主要内容和目标 436
2.2.1 主要内容 436
2.2.2 管理目标 437
2.3 备件属性分类判断流程 437
2.4 备件技术管理的制度规范编制 438
2.4.1 备件分类的原则和主要方法 438
2.4.2 备件编码原则和良好编码的特点 438
2.4.3 备件的ABC分类原则和标准 439
2.4.4 备件3A管理的分类原则和状态类型 441
2.5 备件技术管理的实施细则和注意事项 442
2.5.1 备件基础技术资料整理的实施细则和注意事项 442
2.5.2 备件分类的实施细则和注意事项 443
2.5.3 备件编码的实施步骤和注意事项 443
2.5.4 备件ABC分类法管理准则和注意事项 443
2.5.5 备件3A管理的实施细则和注意事项 446
2.6 备件技术管理的评价和激励 446
2.6.1 评价指标 446
2.6.2 激励 446
2.7 备件技术管理的案例分析 447
2.7.1 某钢铁企业的备件分类方式 447
2.7.2 某大型电厂的备件分类管理方式 447
2.7.3 某电子企业的备件编码方式 447
2.7.4 某钢铁企业的备件编码方式 448
2.7.5 某钢铁集团的备件编码方式 449
2.7.6 某核电站备件物项编码管理案例 450
2.7.7 某企业备件ABC分类管理案例 451
2.7.8 某烟厂备件3A管理案例 453
2.8 备件技术管理的创新方向 454
第3章 备件计划的平衡与优化 457
3.1 备件计划管理的组织职责 457
3.1.1 构成 457
3.1.2 职责 457
3.2 备件计划管理的主要任务和目标 458
3.2.1 主要任务 458
3.2.2 目标 458
3.3 备件计划管理的工作流程 458
3.4 备件计划管理的制度规范编制 460
3.4.1 备件计划的分类 460
3.4.2 备件计划的组织申报原则 460
3.4.3 备件计划的监控和调整原则 460
3.4.4 备件质量异议的处理原则 460
3.5 备件计划管理的实施细则和工作要求 461
3.5.1 备件计划的拟订 461
3.5.2 备件计划的申报方式 461
3.5.3 备件计划的监控和调整方法 462
3.6 备件计划管理的评价和激励 462
3.6.1 评价指标体系 462
3.6.2 激励 462
3.7 备件计划管理案例分析 462
3.7.1 某钢铁公司强化计划管理, 提高备件计划准确性 462
3.7.2 某钢铁公司加强设备维护管理,减少备件申报计划 463
3.7.3 某化工公司加强备件计划的动态管理 463
3.8 备件计划管理的创新方向 463
第4章 备件采购和供管方式优化 466
4.1 备件采购管理的组织职责 466
4.2 备件采购管理的主要内容和目标 467
4.2.1 主要内容 467
4.2.2 目标 467
4.3 备件采购管理的工作流程 467
4.4 备件采购管理的制度规范编制 468
4.4.1 备件采购作业主要工作的目的和环节 468
4.4.2 外购备件的考虑因素 468
4.4.3 备件采购定价方法 469
4.4.4 备件订货方式的选择原则 469
4.4.5 备件集中与分散采购原则 469
4.4.6 备件采购订单计划的编制要点 469
4.4.7 备件采购合同条款的编制要点 470
4.4.8 备件无库存管理模式的制度规范 470
4.5 备件采购管理的实施细则和工作要求 471
4.5.1 备件采购作业实施细则和工作要求 471
4.5.2 备件采购订单计划实施细则和工作要求 471
4.5.3 备件采购合同管理的实施细则和工作要求 472
4.5.4 备件无库存管理的实施细则和工作要求 472
4.6 备件采购管理的评价和激励 473
4.6.1 评价指标体系 473
4.6.2 激励 473
4.7 备件采购管理案例分析 473
4.7.1 用最佳性价比指导备件采购 473
4.7.2 宝钢对标准备件的采购管理机制 474
4.7.3 宁波钢铁采购进口备件的经验分享 474
4.8 备件采购管理和供管方式的创新方向 474
4.8.1 备件采购与设备前期管理 474
4.8.2 备件采购模式创新 475
4.8.3 联合库存备件管理模式 475
4.8.4 供应商管理备件库存模式 476
第5章 备件库存和领用管理优化 478
5.1 备件库存和领用管理的组织职责 478
5.1.1 构成 478
5.1.2 职责 478
5.2 备件库存和领用管理的主要内容和目标 478
5.2.1 主要内容 478
5.2.2 目标 480
5.3 备件库存和领用管理的工作流程 480
5.4 备件库存和领用的管理原则 481
5.4.1 备件库存管理的基本原则 481
5.4.2 选择备件存放位置的总体策略 481
5.4.3 备件库位编码的作用 482
5.4.4 备件出入库作业设计要点 482
5.5 备件库存和领用管理的实施细则和工作要求 483
5.5.1 备件库位编码的常用方法 483
5.5.2 备件验货收货入库的实施细则和工作要求 484
5.5.3 备件存货保管的实施细则和工作要求 484
5.5.4 备件发货出库的实施细则和工作要求 486
5.6 备件库存和领用管理的评价和激励 487
5.6.1 评价指标体系 487
5.6.2 激励 487
5.7 备件库存和领用管理的案例分析 487
5.8 备件库存和领用管理的创新方向 487
5.8.1 旋转式备件货架应用 487
5.8.2 立体备件库 488
5.8.3 备件仓储可视化定置化管理 489
第6章 备件修复回用和国产化 492
6.1 备件修复回用和国产化的组织职责 492
6.1.1 构成 492
6.1.2 职责 492
6.2 备件修复和国产化的主要内容和目标 492
6.2.1 主要内容 492
6.2.2 目标 492
6.3 备件回收修复的工作流程 492
6.4 备件修复和国产化的制度规范编制 493
6.4.1 备件修复回用的范围 493
6.4.2 备件国产化应有的意识和原则 493
6.5 备件修复和国产化的实施细则和工作要求 493
6.5.1 备件修复实施细则和工作要求 493
6.5.2 备件国产化实施要点和工作要求 494
6.6 备件修复和国产化的评价和激励 496
6.6.1 评价指标体系 496
6.6.2 激励 496
6.7 备件修复和国产化的案例分析 496
6.7.1 宝新公司管理创新让备件修复创效益 496
6.7.2 安彩高科进口设备关键备件的国产化体会 497
6.7.3 某企业备件国产化工作案例 497
6.8 备件修复和国产化的创新方向 499
6.8.1 绿色维修 499
6.8.2 重视表面修复技术的应用 500
第10篇 特种设备安全节能篇 504
第1章 动力设备管理 504
1.1 动力设备管理组织职责 504
1.2 动力设备管理目标 504
1.3 动力设备管理的工作流程 505
1.4 动力设备管理的制度规范 506
1.4.1 建立健全动力设备的各种规程并予以执行 506
1.4.2 层层落实责任制,建立全员参与设备管理的体制 506
1.4.3 以自主维修为核心,建立“三零”的设备管理模式 506
1.4.4 建立可视化定置化管理规范 507
1.5 动力设备管理实施细则 507
1.5.1 动力设备安全运行管理实施细则 507
1.5.2 动力设备日常点巡检管理实施细则 508
1.5.3 动力设备的安全操作管理实施细则 508
1.5.4 动力设备维修管理实施细则 509
1.5.5 动力设备防火保卫实施细则 509
1.5.6 动力设备交接班实施细则 509
1.5.7 动力设备清洁卫生实施细则 510
1.6 动力设备管理评价与激励 510
1.6.1 评价的目的 510
1.6.2 评价指标设计 510
1.6.3 评价流程 511
1.6.4 动力设备规范管理的评价细则 511
1.6.5 激励 513
1.7 动力设备管理的案例分析 513
1.7.1 对原有的设备管理模式进行调研分析 513
1.7.2 在动力车间建立设备管理新模式 514
1.7.3 动力车间运行设备管理新模式后的效果 516
1.8 动力设备管理的创新方向 516
1.8.1 电力变压器状态监测技术的应用 516
1.8.2 其他动力设备状态监测技术的应用 517
第2章 特种设备管理 519
2.1 特种设备管理组织及职责 519
2.2 特种设备管理目标 519
2.3 特种设备管理工作流程 519
2.4 特种设备管理制度规范 520
2.4.1 特种设备的作业人员及其相关管理人员的资质 520
2.4.2 特种设备的制造、安装、改造及维修 521
2.4.3 特种设备的使用 521
2.4.4 检验检测 522
2.4.5 特种设备的事故预防和调查处理 522
2.4.6 特种设备的行政许可变更 522
2.5 特种设备管理实施细则 522
2.6 特种设备管理评价与激励 525
2.6.1 评价目的 525
2.6.2 评价指标体系 525
2.6.3 评价范畴 526
2.6.4 标准项目及评价细则 526
2.6.5 激励 528
2.7 特种设备管理案例分析 528
2.7.1 事故概况 529
2.7.2 事故发生过程 529
2.7.3 事故调查分析 529
2.7.4 事故调查结论 530
2.7.5 事故处理 530
2.8 特种设备管理创新方向 531
2.8.1 特种设备管理信息化 531
2.8.2 特种设备管理新技术的应用 531
第3章 节能减排管理 533
3.1 节能减排管理组织及职责 533
3.1.1 节能减排工作领导小组 533
3.1.2 节能减排办公室 533
3.1.3 设备管理部门 533
3.1.4 安全环保部门 534
3.1.5 基建管理部门 534
3.1.6 生产管理部门 534
3.1.7 财务审计部门 534
3.1.8 技术管理部门 535
3.1.9 行政部门 535
3.1.10 人力资源部门 535
3.2 节能减排管理主要内容和目标 535
3.2.1 节能减排管理主要内容 535
3.2.2 节能减排管理目标 535
3.3 节能减排管理工作流程 535
3.4 节能减排管理制度规范 536
3.4.1 成立节能减排领导小组的文件 537
3.4.2 明确节能减排目标与责任的文件 537
3.4.3 节能减排管理制度(规定) 537
3.4.4 节能减排管理其他方面的制度(规定) 537
3.5 节能减排管理实施细则 537
3.5.1 节能减排的方针与目标指标 537
3.5.2 节能减排基础工作的管理 537
3.5.3 节能减排统计监测与报告 539
3.5.4 节能减排规划 544
3.5.5 节能减排考核 544
3.5.6 节能产品认证与能源效率标识 544
3.6 节能减排管理评价与激励 545
3.6.1 工业企业节能减排主要指标解释 545
3.6.2 节能减排目标责任评价考核 546
3.7 节能减排管理案例分析 548
3.7.1 企业概况 548
3.7.2 清洁生产的宣传 548
3.7.3 审核重点分析 549
3.7.4 清洁生产审核绩效 550
3.8 节能减排管理创新方向 550
3.8.1 合同能源管理 550
3.8.2 再制造 551
第11篇 技术改造更新拓展篇 556
第1章 设备技术经济分析 556
1.1 设备技术经济分析组织职责 556
1.1.1 设备管理部门 556
1.1.2 设备管理部门负责人 556
1.1.3 设备使用单位 556
1.1.4 公司生产主管领导(总经理) 556
1.2 设备技术经济分析原则 556
1.3 设备技术经济分析工作流程 556
1.4 设备技术经济分析方法 557
1.4.1 设备更新的技术经济分析方法 557
1.4.2 设备技术改造的技术经济分析方法 557
1.4.3 设备更新、技术改造综合技术经济分析方法 557
1.5 设备技术经济分析实施细则 557
1.5.1 有形磨损的更新决策 557
1.5.2 无形磨损的更新决策 558
1.5.3 生产能力不足时的更新决策 558
1.5.4 设备总费用现值比较 558
1.5.5 设备技术改造的效益评价 558
1.5.6 总使用成本比较法计算公式 558
1.5.7 指标对比法使用的参数和符号 559
1.6 设备技术经济分析评价激励 560
1.7 设备技术经济分析案例 560
1.7.1 有形磨损的更新决策 560
1.7.2 生产能力不足时的更新决策 560
1.7.3 设备总费用现值比较 560
1.7.4 总使用成本比较法 561
1.8 设备技术经济分析创新方向 562
第2章 技改前期准备 564
2.1 技改前期准备组织职责 564
2.2 技改前期准备目标 564
2.3 技改前期准备工作流程 564
2.4 技改前期准备规范要求 564
2.4.1 安全规范 564
2.4.2 标准规范 564
2.4.3 环保规范 564
2.4.4 产业规范 564
2.5 技改前期准备实施细则 564
2.5.1 改造思路的确定 564
2.5.2 改造前的技术准备工作 565
2.6 技改前期准备评价激励 566
2.7 技改前期准备案例 566
2.8 技改前期准备创新方向 566
第3章 技改实施 568
3.1 技改实施组织职责 568
3.1.1 技改项目负责人 568
3.1.2 技改项目小组 568
3.1.3 技改施工单位 568
3.1.4 公司生产主管领导(总经理) 568
3.2 技改实施目标 568
3.3 技改实施工作流程 568
3.4 技改实施规范要求 569
3.5 技改实施细则 569
3.5.1 原设备的全面保养 569
3.5.2 保留的机械电气部分最佳化调整 569
3.5.3 改造部分拆除 569
3.5.4 合理安排改造部分的位置及相互连接 569
3.5.5 调试 569
3.5.6 验收及后期工作 569
3.6 技改实施评价激励 570
3.7 技改实施案例 570
3.8 技改实施创新方向 570
第4章 技改效果跟踪评估 572
4.1 技改效果跟踪评估组织职责 572
4.1.1 设备使用单位 572
4.1.2 评估小组 572
4.1.3 设备管理部门负责人 572
4.1.4 公司生产主管领导 572
4.2 技改效果跟踪评估 572
4.2.1 设备改造目标 572
4.2.2 技改效果跟踪评估目的 572
4.3 技改效果跟踪评估工作流程 572
4.4 技改效果跟踪评估规范要求 572
4.5 技改效果跟踪评估实施细则 572
4.5.1 技改效果跟踪评估内容 572
4.5.2 技改评价总结 574
4.6 技改效果跟踪评估评价激励 574
4.7 技改效果跟踪评估案例 574
4.8 技改效果跟踪评估创新方向 574
第12篇 精益TnPM体系融合篇 581
第1章 精益TnPM体系融合总体框架 581
1.1 精益TnPM体系融合的组织职责 581
1.1.1 组织职责分工 581
1.1.2 系统管理 581
1.2 精益TnPM体系融合的目标 581
1.2.1 目标 581
1.2.2 手段 581
1.3 精益TnPM体系融合工作流程 581
1.4 精益TnPM体系融合管理制度规范 582
1.4.1 精益TnPM规划管理规定 582
1.4.2 精益TnPM体系融合实施管理规定 582
1.5 精益TnPM体系融合实施细则 582
1.6 精益TnPM体系融合的评价与激励 582
1.6.1 评价范畴 582
1.6.2 评价指标设计 583
1.6.3 评价的流程 583
1.6.4 激励 583
1.7 精益TnPM体系融合案例分析 583
1.7.1 背景介绍 583
1.7.2 规划 583
1.7.3 效果 583
1.7.4 不足 584
1.8 精益TnPM体系融合的创新方向 584
第2章 精益TnPM体系融合生产线改造 586
2.1 生产线改造的组织职责 586
2.1.1 组织职责分工 586
2.1.2 系统管理 586
2.2 生产线改造的目标 586
2.2.1 目标 586
2.2.2 手段 586
2.3 生产线改造工作流程 586
2.4 生产线改造管理制度规范 586
2.4.1 生产线改造规划管理规定 586
2.4.2 生产线改造实施管理规定 586
2.5 生产线改造实施细则 587
2.5.1 单件流(小批量流)实施细则 587
2.5.2 看板生产方式实施细则 587
2.5.3 均衡生产实施细则 587
2.5.4 标准作业实施细则 588
2.5.5 产线平衡实施细则 588
2.5.6 多能工培养实施细则 588
2.5.7 “水蜘蛛”作业实施细则 588
2.5.8 “安灯”实施细则 588
2.5.9 设备布局实施细则 588
2.6 生产线改造的评价与激励 588
2.6.1 评价指标设计 588
2.6.2 评价的流程 588
2.6.3 激励 589
2.7 生产线改造案例分析 589
2.7.1 背景 589
2.7.2 改善前后数据对比 589
2.8 生产线改造创新方向 589
第3章 精益TnPM体系融合快速换模 591
3.1 快速换模的组织职责 591
3.1.1 规划与决策 591
3.1.2 系统管理 591
3.2 快速换模的目标 591
3.2.1 目标 591
3.2.2 实现目标的手段 591
3.3 快速换模管理工作流程 591
3.4 快速换模管理制度规范 592
3.5 快速换模管理实施细则 592
3.6 快速换模评价与激励 592
3.6.1 评价指标 592
3.6.2 评价流程 592
3.6.3 激励 592
3.7 快速换模案例分析 592
3.7.1 背景 592
3.7.2 快速换模的主要实施步骤 592
3.7.3 效果 592
3.7.4 不足 592
3.8 快速换模的创新方向 593
第4章 精益TnPM体系融合自动化 595
4.1 实施自动化的组织职责 595
4.1.1 组织职责分工 595
4.1.2 系统管理 595
4.2 自动化的目标 595
4.2.1 目标 595
4.2.2 达成手段 595
4.3 自动化工作流程 595
4.4 自动化管理制度规范 596
4.5 自动化实施细则 596
4.6 自动化的评价与激励 596
4.6.1 评价指标 596
4.6.2 评价流程 596
4.6.3 激励 597
4.7 自动化案例分析 597
4.7.1 案例分析一 597
4.7.2 案例分析二 597
4.7.3 案例分析三 597
4.8 自动化的创新方向 597
第5章 精益TnPM体系融合动作改善 600
5.1 动作改善的组织职责 600
5.1.1 组织职责分工 600
5.1.2 系统管理 600
5.2 动作改善的目标 600
5.3 动作改善工作流程 600
5.4 动作改善管理制度规范 601
5.5 动作改善实施细则 601
5.6 动作改善评价与激励 602
5.6.1 评价指标设计 602
5.6.2 评价的流程 602
- 《Maya 2018完全实战技术手册》来阳编著 2019
- 《一本书读懂无人机》姜魁著 2019
- 《高等教育双机械基础课程系列教材 高等学校教材 机械设计课程设计手册 第5版》吴宗泽,罗圣国,高志,李威 2018
- 《慢性呼吸系统疾病物理治疗工作手册》(荷)瑞克·考斯林克(RikGosselink) 2020
- 《战略情报 情报人员、管理者和用户手册》(澳)唐·麦克道尔(Don McDowell)著 2019
- 《实用内科手册》黄清,阮浩航主编 2016
- 《基层医疗卫生机构安全用药手册》黎月玲,熊慧瑜 2019
- 《同仁眼科手册系列 同仁儿童眼病手册》付晶编 2018
- 《环境噪声监测实用手册》中国环境监测总站编 2018
- 《高度关注物质(SVHC)毒性手册 上》顾爱华主编 2019
- 《指向核心素养 北京十一学校名师教学设计 英语 七年级 上 配人教版》周志英总主编 2019
- 《北京生态环境保护》《北京环境保护丛书》编委会编著 2018
- 《高等教育双机械基础课程系列教材 高等学校教材 机械设计课程设计手册 第5版》吴宗泽,罗圣国,高志,李威 2018
- 《指向核心素养 北京十一学校名师教学设计 英语 九年级 上 配人教版》周志英总主编 2019
- 《高等院校旅游专业系列教材 旅游企业岗位培训系列教材 新编北京导游英语》杨昆,鄢莉,谭明华 2019
- 《中国十大出版家》王震,贺越明著 1991
- 《近代民营出版机构的英语函授教育 以“商务、中华、开明”函授学校为个案 1915年-1946年版》丁伟 2017
- 《新工业时代 世界级工业家张毓强和他的“新石头记”》秦朔 2019
- 《智能制造高技能人才培养规划丛书 ABB工业机器人虚拟仿真教程》(中国)工控帮教研组 2019
- 《AutoCAD机械设计实例精解 2019中文版》北京兆迪科技有限公司编著 2019