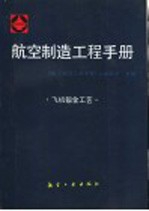
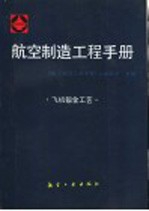
航空制造工程手册 飞机钣金工艺PDF电子书下载
- 电子书积分:20 积分如何计算积分?
- 作 者:《航空制造工程手册》总编委会主编
- 出 版 社:北京:航空工业出版社
- 出版年份:1992
- ISBN:7800464903
- 页数:737 页
第1章 飞机钣金工艺概述 1
1.1 飞机钣金工艺的重要性 1
目录 1
符号说明 1
第1篇 飞机钣金工艺的一般性问题 1
1.2 飞机钣金工艺的特点 2
2.1.2 铝及铝合金 3
2.1.1 飞机机体常用钣金材料的分类 3
第2章 飞机钣金零件用材及热、表处理2.1 飞机钣金零件常用材料 3
2.1.2.1 板材 4
2.1.2.2 型材与管材 14
2.1.3.1 镁合金 17
2.1.3 镁合金与钛及钛合金 17
2.1.3.2 钛及钛合金 18
2.1.4.1 板材 21
2.1.4 优质碳素结构钢 21
2.1.4.2 管材 23
2.1.5.1 板材 24
2.1.5 不锈钢 24
2.1.5.2 管材 25
2.1.6.1 板材 27
2.1.6 合金钢 27
2.2.1 成形性指数的重要性 28
2.2 板材成形性和试验方法 28
2.1.6.2 管材 28
2.2.3 基本成形性试验与指数 29
2.2.2 成形性指数的分类 29
2.2.4 成形性模拟试验与用途 31
2.2.6 成形极限曲线 33
2.2.5 金属学的成形性能指数及其试验 33
2.2.7.2 下陷成形试验及其指数 34
2.2.7.1 凸耳试验及其指数 34
2.2.7 特定成形试验与指数 34
2.3.1.2 淬火(固溶处理) 35
2.3.1.1 退火 35
2.3 飞机钣金零件的热处理 35
2.3.1 铝合金 35
2.3.1.3 时效处理 37
2.3.2.2 钛及钛合金 38
2.3.2.1 镁合金 38
2.3.1.4 回归处理 38
2.3.2 镁合金与钛及钛合金 38
2.3.3 不锈钢 39
2.3.4 碳钢及合金钢热处理规范 41
2.4.1.1 铝合金表面处理的分类 42
2.4.1 铝合金表面处理 42
2.4 表面处理与保护 42
2.4.1.2 铝合金表面处理的应用范围 43
2.4.3 钢的表面处理 44
2.4.2.2 镁合金的化学氧化和阳极化 44
2.4.2 镁合金的表面处理 44
2.4.2.1 镁合金表面处理的要求 44
第3章 飞机钣金零件分类及工艺方案技术经济分析 45
2.4.4 涂漆 45
3.1.3 分类图表 47
3.1.2 分类原则和方法 47
3.1 飞机钣金零件分类 47
3.1.1 分类目的 47
3.1.3.1 板材零件分类 48
3.1.3.2 挤压型材零件分类 54
3.2.2 工艺方案技术经济评价方法 55
3.2.1 工艺方案选择原则 55
3.1.3.3 管材零件分类 55
3.2 典型零件工艺方案及技术经济分析 55
3.2.3 年度工艺成本计算 56
3.2.4 工艺方案技术经济评价 57
4.1.3.1 协调路线 69
4.1.3 协调路线与协调图表 69
第4章 飞机钣金零件的协调 69
4.1 飞机钣金零件协调的一般概念 69
4.1.1 互换与协调 69
4.1.2 准确度与条件准确度 69
4.1.2.1 制造准确度与协调准确度 69
4.1.2.2 条件准确度 69
4.1.3.2 协调图表 70
4.2.1 定义 72
4.2 飞机钣金零件的协调依据 72
4.1.4 飞机钣金零件协调的部位 72
4.1.4.1 歼击机 72
4.1.4.2 大型客机 72
4.1.4.3 直升机 72
4.2.2.2 样板 74
4.2.2.1 数据(尺寸) 74
4.2.2 协调依据内容 74
4.2.2.3 标准工艺装备 75
4.2.2.4 移形工艺装备 77
4.2.2.5 标准实样 78
4.3.2 基本协调方法 79
4.3.1 协调方法分类 79
4.3 飞机钣金零件协调的方法 79
4.3.3 飞机钣金零件协调方法举例 85
4.4.2.1 编制协调路线 101
4.4.2 钣金零件协调误差计算举例 101
4.4 飞机钣金零件协调误差的计算 101
4.4.1 计算公式 101
4.4.2.4 计算超差危率 105
4.4.2.3 计算协调误差 105
4.4.2.2 查组成环公差 105
第5章 飞机钣金零件通用检验技术要求及检验方法 106
4.4.2.5 提高准确度措施 106
5.2.1 外形公差 107
5.2 平板零件和毛料的检验要求 107
5.1 定义与适用范围 107
5.1.1 定义 107
5.1.2 适用范围 107
5.2.4 其他几何形状的公差 108
5.2.3 平板零件角度的公差 108
5.2.2 平板零件的平面度要求 108
5.3.1 外形公差 109
5.3 成形零件检验要求 109
5.3.3.2 常见挤压型材下陷类型和公差要求 112
5.3.3.1 板制零件下陷尺寸公差 112
5.3.2 弯曲半径公差 112
5.3.3 下陷公差 112
5.3.4.3 挤压型材零件斜角公差 113
5.3.4.2 板弯型材零件斜角公差 113
5.3.4 弯边斜角公差 113
5.3.4.1 板弯零件的弯边斜角公差 113
5.3.5 型面畸变公差 114
5.3.6.3 加强槽和加强窝深度的公差 116
5.3.6.2 零件弯边高度公差 116
5.3.6 其他几何要求的公差 116
5.3.6.1 翻边 116
5.3.9 制孔的公差 117
5.3.8 平面度要求 117
5.3.6.4 封闭形和搭边类零件的公差 117
5.3.7 外缘切割公差 117
5.4.2 碳钢、结构钢和不锈钢钣金零件边缘要求 118
5.4.1 钣金零件边缘的一般要求 118
5.3.10 厚度的公差 118
5.4 钣金零件边缘状态要求 118
5.5.1 一般术语 119
5.5 钣金零件表面质量要求 119
5.4.3 噪音区钣金零件边缘要求 119
5.5.3 表面擦、划伤的验收要求 120
5.5.2 对表面质量的一般要求 120
5.7.1.1 硬度检验 121
5.7.1 热处理状态的检验 121
5.6 钣金零件加压检验 121
5.7 钣金零件内在质量检验 121
5.7.1.2 导电率检验 122
5.7.2.1 渗透检验 129
5.7.2 无损检测的要求 129
5.7.2.2 磁力探伤 130
5.7.3 变形量的检查 131
6.3.1.1 无试压要求的工装验收 132
6.3.1 工装的验收 132
第6章 飞机钣金零件质量控制 132
6.1 概述 132
6.2 材料的控制 132
6.2.1 原材料的性能指标 132
6.2.2 材料的入厂复验 132
6.2.3 材料的保管和发放 132
6.3 工装的控制 132
6.3.2.2 保管要求 134
6.3.2.1 使用要求 134
6.3.1.2 有模具试压的工装验收 134
6.3.2 工装的合理使用 134
6.4.2 设备的使用和保养 135
6.4.1 设备的合理选用 135
6.3.3 工装的二次合格及定期检修 135
6.3.3.1 工装二次鉴定合格 135
6.3.3.2 工装的定期检修 135
6.4 设备的控制 135
6.5.3 工艺文件的控制 136
6.5.2 首件三检 136
6.5 制造过程的控制 136
6.5.1 对操作者的要求及开工前的“三对照” 136
6.5.1.1 对操作者的要求 136
6.5.1.2 开工前的“三对照” 136
6.5.5.2 外在质量的控制 137
6.5.5.1 概述 137
6.5.4 关键件、重要件及其工序的控制 137
6.5.5 钣金零件制造质量控制要求 137
6.5.5.3 内在质量的控制 139
6.6.2 周转、运输过程的要求 140
6.6.1 零件存放的要求 140
6.6 零件存放和周转过程的质量控制 140
7.2.1.2 零件的可生产性 141
7.2.1.1 零件的成形性 141
第7章 飞机钣金工艺技术准备工作 141
7.1 概述 141
7.2 工艺性审查 141
7.2.1 工艺性审查重点 141
7.3.1 原始资料的主要内容 142
7.3 原始资料汇集 142
7.2.1.3 零件的协调性 142
7.2.1.4 新工艺新技术的工程化 142
7.2.2 工艺性审查内容 142
7.5.1 文件种类 143
7.5 工艺文件编制 143
7.3.2 整理记录的重点问题 143
7.4 零件工艺分析 143
7.7.1 技术攻关 144
7.7 技术攻关和技术改造 144
7.5.2 文件编制程序 144
7.5.3 文件编制要求 144
7.5.4 文件更改规定 144
7.6 工艺装备选择 144
7.6.1 选择原则 144
7.6.2 注意事项 144
7.6.3 工艺装备系数选择 144
7.6.3.1 不同批次工艺装备系数 144
7.6.3.2 钣金零件工艺装备系数 144
7.8.1 民用飞机工艺鉴定 145
7.8 工艺鉴定 145
7.7.2 技术改造 145
7.8.2 军用飞机工艺鉴定 146
8.1.3 模拟软件系统的基本结构 147
8.1.2 模拟的主要方法 147
第8章 计算机技术在钣金成形中的应用8.1 成形过程的计算机模拟 147
8.1.1 模拟的意义 147
8.1.4 现有的分析模拟软件系统 149
8.1.5 示例 150
8.2.3.1 冲裁模 151
8.2.3 典型模具CAD/CAM 151
8.2 模具的计算机辅助设计与制造 151
8.2.1 模具CAD/CAM系统的配置 151
8.2.2 模具CAD/CAM的功能与效果 151
8.2.3.2 成形模 154
8.3.1.1 数控成形设备的意义 157
8.3.1 数控成形设备概况 157
8.3 成形设备的数控 157
8.3.1.2 成形设备数控的特点 158
8.3.4.1 普通旋压机 159
8.3.4 典型录返式系统 159
8.3.2 数控成形设备的控制方式 159
8.3.3 数控成形设备的品种 159
8.3.4.2 拉形机 160
8.3.6 典型自适应数控系统 161
8.3.5.2 数控弯管机 161
8.3.5 典型模型式系统 161
8.3.5.1 数控闸压机 161
8.4.1 工艺过程计算机辅助设计的作用与意义 163
8.4 工艺过程计算机辅助设计 163
8.4.3.1 编码系统的作用与意义 164
8.4.3 成组技术及其在CAPP中的应用 164
8.4.2 CAPP系统的基本类型 164
8.4.3.3 钣金成形件分类编码系统示例 165
8.4.3.2 编码系统的结构形式 165
8.4.3.4 开发或选用编码系统的注意事项 166
8.4.5 创成式CAPP系统 167
8.4.4 派生式CAPP系统 167
8.4.6 钣金成形CAPP系统示例 169
8.5.1 柔性制造系统的目的与构成 171
8.5 柔性制造系统 171
8.5.2 工作地 172
8.5.4 模具(包括其他工装)系统 173
8.5.3 材料运输系统 173
8.5.5 国外系统示例 175
8.6 软件评估 176
9.1.2 结构工艺性 181
9.1.1.2 典型零件分类 181
第2篇 飞机钣金零件工艺设计 181
第9章 平板零件制造 181
9.1 零件分类及结构工艺性 181
9.1.1 定义和典型零件分类 181
9.1.1.1 定义 181
9.2.1.3 编制依据 182
9.2.1.2 构成 182
9.2 材料消耗定额及排样下料 182
9.2.1 材料消耗定额 182
9.2.1.1 分类 182
9.2.1.4 材料利用率 183
9.2.2.2 排样下料 184
9.2.2.1 节约原材料途径 184
9.2.2 节约原材料途径和排样下料 184
9.3.1 剪切形式及适用范围 186
9.3 剪切 186
9.3.2 剪切力计算 187
9.4.1 铣切形式及适用范围 188
9.4 铣切 188
9.4.3 铣切样板 189
9.4.2 铣刀、靠柱与靠套 189
9.5.2 典型零件冲裁方法 190
9.5.1 定义与适用范围 190
9.5 冲裁 190
9.5.3 冲裁条料排样 191
9.5.5 冲裁力计算 192
9.5.4 搭边数值的确定 192
9.5.7.2 分类 194
9.5.7.1 含义 194
9.5.6 卸料力、推料力和顶件力计算 194
9.5.7 冲裁间隙 194
9.5.8 冲裁模形式及适用范围 195
9.5.7.3 间隙值确定 195
9.6.2 电火花线切割 200
9.6.1 激光切割 200
9.6 其他下料方法 200
9.6.3 高压水切割 201
9.7.2 工艺孔的加工 202
9.7.1 工艺设计内容 202
9.7 平板件工艺设计 202
9.7.5 除油和表面保护 203
9.7.4 校平 203
9.7.3 去毛刺方法 203
9.7.6 典型零件工艺流程 204
9.8 平板零件加工先进方法示例 205
9.7.7 超薄蒙皮零件加工注意事项 205
10.1.2.1 最小弯曲半径 208
10.1.2 零件结构工艺性要求 208
第10章 板弯型材零件工艺设计 208
10.1 典型零件分类及结构工艺性要求 208
10.1.1 典型零件分类 208
10.1.2.3 最小弯边高度 212
10.1.2.2 孔边缘距弯曲处的位置尺寸 212
10.1.2.6 板弯型材在闸压成形时的开敞性 213
10.1.2.5 止裂孔、止裂槽的大小及位置 213
10.1.2.4 板材纤维方向与弯曲线的夹角 213
10.2.2.1 展开尺寸计算 214
10.2.2 板弯型材展开尺寸计算及下料要求 214
10.2 压弯和折弯成型 214
10.2.1 定义及范围 214
10.2.2.2 下料要求 225
10.2.3.1 刚性模弯曲件的回弹 226
10.2.3 弯曲回弹 226
10.2.3.2 弹性凹模弯曲件的回弹 233
10.2.3.3 修正回弹的基本方法 236
10.2.4.1 冲压弯曲模 237
10.2.4 弯曲模设计要求 237
10.2.4.2 聚胺酯橡胶弯曲模 238
10.2.4.3 闸压弯曲模 241
10.2.4.4 弯曲件的工序分步及模具典型结构 242
10.2.5.1 弯曲力 244
10.2.5 弯曲力与弯曲力矩 244
10.2.6 板弯型材质量控制 248
10.2.5.2 弯曲力矩 248
10.2.7 典型零件工艺流程 249
10.3.2.1 成形过程 250
10.3.2 型辊成形过程与成形力 250
10.3 型辊成形 250
10.3.1 定义及应用范围 250
10.3.3.1 型辊成形机的类型 251
10.3.3 型辊成形机 251
10.3.2.2 成形力 251
10.3.3.2 机床的选择 252
10.3.4.1 辊轮组数和花型展开图设计 253
10.3.4 辊轮设计 253
10.3.3.3 辅助设备 253
10.3.4.4 辊轮的节圆直径 255
10.3.4.3 辊压方向 255
10.3.4.2 导向线的确定 255
10.3.4.7 回弹修正 256
10.3.4.8 辊轮 256
10.3.4.5 型辊成形顺序 256
10.3.4.6 辊轮间隙 256
10.3.5.2 热成形辊轮 257
10.3.5.1 加热装置 257
10.3.5 钛合金板料的热辊成形 257
10.3.6 典型零件工艺流程 258
10.3.5.3 Ti-6A1-4V钛合金的热型辊工艺 258
11.1.1 拉深零件的分类 263
11.1 典型零件分类及结构工艺性要求 263
第11章 拉深零件成形 263
11.1.2 拉深零件结构工艺性要求 264
11.2 拉深成形法的分类及特点 267
11.3.1.1 确定形状、尺寸的原则 272
11.3.1 拉深件毛料形状及尺寸的确定 272
11.3 拉深成形的工艺设计 272
11.3.1.2 旋转体拉深件毛料形状与尺寸的确定 273
11.3.1.3 盒形件毛料形状及尺寸的确定 284
11.3.1.4 不规则拉深件展开毛料的确定 289
11.3.2.1 拉深件变形程度——拉深系数的确定 291
11.3.2 拉深成形工艺参数的确定 291
11.3.2.2 拉深件的成形次数与成形高度的估算 300
11.3.3.1 采用压边圈的条件 305
11.3.3 模具的压边方式及压边力的确定 305
11.3.3.2 压边力的计算 306
11.3.3.3 压边圈的结构形式 307
11.3.4.1 拉深力的计算 309
11.3.4 拉深力及拉深功的计算 309
11.3.4.2 拉深功与拉深功率的计算 311
11.3.5.1 无凸缘的旋转体筒形件 312
11.3.5 拉深件的工序设计 312
11.3.5.2 有凸缘的旋转体筒形件 313
11.3.5.3 阶梯筒形件 315
11.3.5.4 锥形件 317
11.3.5.5 球形件 321
11.3.5.6 抛物线形件 322
11.3.5.8 盒形件 323
11.3.5.7 双曲线形件 323
11.3.5.9 方锥台件 329
11.3.6.1 筒形件变薄拉深工艺参数的确定 330
11.3.6 筒形件的变薄拉深 330
11.3.7 大型覆盖件的拉深成形 332
11.3.6.2 变薄拉深模的设计要点 332
11.3.7.2 压边面及拉深埂的设置 333
11.3.7.1 大型覆盖件成形的工艺特点 333
11.3.8.2 润滑、润滑剂及其使用方法 334
11.3.8.1 热处理工序及其安排 334
11.3.8 拉深件成形过程中的热处理及其润滑 334
11.4.2 拉深零件的质量分析 336
11.4.1 拉深成形的准确度 336
11.4 拉深零件的质量分析 336
11.4.3 运用成形极限图(FLD)确保零件的成形质量 341
12.1.1 分类 343
12.1 蒙皮零件分类与结构工艺性 343
第12章 蒙皮零件成形 343
12.2.2.2 最小结构高度 344
12.2.2.1 最小弯曲半径 344
12.1.2 特点 344
12.1.3 结构工艺性 344
12.2 蒙皮闸压成形 344
12.2.1 定义 344
12.2.2 工艺参数 344
12.2.3.2 弹性模闸压 345
12.2.3.1 刚性模闸压 345
12.2.2.3 回弹量 345
12.2.2.4 闸压力 345
12.2.2.5 展开件的确定 345
12.2.3 蒙皮闸压的工艺方法 345
12.2.3.3 拉伸闸压 346
12.2.4.2 闸压模材料 347
12.2.4.1 模具结构 347
12.2.4 专用闸压模设计 347
12.2.6 典型零件工艺流程 348
12.2.5 设备选择 348
12.3.3.1 辊轴压下量 349
12.3.3 工艺参数 349
12.3 蒙皮滚弯成形 349
12.3.1 定义 349
12.3.2 蒙皮滚弯方式 349
12.3.3.4 毛料展开 350
12.3.3.3 成形力计算 350
12.3.3.2 辊轴距离 350
12.3.4.1 圆筒形零件滚弯 351
12.3.4 典型零件的工艺方法 351
12.3.4.3 变厚度蒙皮的滚弯 352
12.3.4.2 圆锥形零件滚弯 352
12.4.3.1 拉形系数 353
12.4.3 工艺参数 353
12.3.5 设备选择 353
12.3.6 典型零件工艺流程 353
12.4 蒙皮拉形 353
12.4.1 定义 353
12.4.2 蒙皮拉形方式 353
12.4.3.2 极限拉形系数 354
12.4.3.4 热处理状态选择 355
12.4.3.3 拉形力与拉形速度 355
12.4.3.5 毛料尺寸的确定 356
12.4.4.1 拉形方法 357
12.4.4 拉形工艺 357
12.4.4.2 拉形的成形过程 358
12.4.4.4 拉形成形的影响因素 359
12.4.4.3 拉形中的皱褶 359
12.4.5.1 外形准确度 360
12.4.5 质量控制 360
12.4.7.1 制造依据 361
12.4.7 拉形模 361
12.4.5.2 表面质量 361
12.4.6 切割和开孔 361
12.4.6.1 切割 361
12.4.6.2 开孔 361
12.4.7.3 模具材料 362
12.4.7.2 结构形式 362
12.4.9 典型零件工艺流程 363
12.4.8 设备选择 363
12.6.2 蒙皮保护 364
12.6.1 镜面蒙皮拉形成形 364
12.5 蒙皮的组合成形 364
12.6 镜面蒙皮成形 364
12.6.3 损伤修复 365
13.2.1 板坯的种类 367
13.2 板坯制备和型面加工 367
第13章 整体壁板成形 367
13.1 概述 367
13.1.1 定义 367
13.1.2 特点 367
13.1.3 结构工艺性 367
13.2.2.2 拉伸处理 368
13.2.2.1 各种方法简介 368
13.2.2 提高板坯平面度的方法 368
13.2.3 板坯制造方案 371
13.2.3.1 轧制—拉伸—机加 372
13.2.3.2 轧制—拉伸—化铣 373
13.2.3.3 轧制特形板坯加工 374
13.2.3.5 模锻板坯加工 376
13.2.3.4 挤压板坯加工 376
13.3.1 成形方法简介 377
13.3 整体壁板成形 377
13.2.3.6 铸造板坯加工 377
13.3.2.2 垫板和垫块 378
13.3.2.1 单曲度壁板成形 378
13.3.2 滚弯成形 378
13.3.4 拉形成形 379
13.3.3 压弯成形 379
13.3.6.2 特点 380
13.3.6.1 定义 380
13.3.5 机、尾翼前缘整体厚蒙皮成形 380
13.3.6 喷丸成形 380
13.3.6.4 工艺参数 381
13.3.6.3 喷丸成形极限成形半径 381
13.3.6.6 喷丸成形方法 386
13.3.6.5 工艺过程的影响因素 386
13.3.6.8 双曲度壁板喷丸成形 387
13.3.6.7 单曲度壁板喷丸成形 387
13.3.6.9 喷丸校形 389
13.3.6.10 典型工艺流程 390
13.3.6.11 喷丸设备 391
13.3.6.12 弹丸 393
13.3.6.13 预应力夹具 394
13.3.7 爆炸成形 395
13.3.8.2 原理 397
13.3.8.1 定义 397
13.3.8 应力松弛成(校)形 397
13.3.8.4 工艺参数 398
13.3.8.3 特点和适用范围 398
13.4.1 零件成形举例 400
13.4 整体壁板成形工艺流程设计 400
13.3.8.5 工艺流程 400
13.3.8.6 注意事项 400
13.4.2 成形质量要求 405
14.1.2.2 注意事项 407
14.1.2.1 应用范围 407
第14章 落压零件成形 407
14.1 落压成形定义及落压零件的结构工艺性 407
14.1.1 落压成形定义与特点 407
14.1.1.1 定义 407
14.1.1.2 特点 407
14.1.2 落压成形的应用范围与注意事项 407
14.1.3.2 结构工艺性要求 408
14.1.3.1 分类 408
14.1.3 落压零件分类及结构工艺性要求 408
14.2.1 毛料的确定 409
14.2 落压零件的毛料 409
14.2.2 落压零件的展开样板 410
14.2.3.1 定位形式与方法 411
14.2.3 展开料在落压模上的定位 411
14.2.2.1 展开件的制造 411
14.2.2.2 展开样板的制造 411
14.2.4.1 确定毛料的经验方法及注意事项 412
14.2.4 确定毛料和展开料的经验方法和注意事项 412
14.2.3.2 安装定位销的要求 412
14.2.4.2 确定展开料的经验方法和注意事项 414
14.3.1.1 按材料变形方式分类 415
14.3.1 落压成形方法的种类 415
14.3 落压成形 415
14.3.2.1 单套模成形法 416
14.3.2 落压成形方法 416
14.3.1.2 按落压模套数分类 416
14.3.2.2 多套模成形法 419
14.3.2.3 组合成形法 422
14.4.4 低熔点合金模校形 424
14.4.3 橡皮容框校形 424
14.4 落压校形 424
14.4.1 落压模校形 424
14.4.2 缩口圈校形 424
14.6.1 工件的检验要求 425
14.6 落压零件的质量控制 425
14.5 辅助加工 425
14.6.3.1 保证零件质量的措施 426
14.6.3 质量保证措施 426
14.6.2 零件的检验要求 426
14.6.3.2 落压零件的废品种类、原因与改进措施 427
14.7.2 特殊零件的典型工艺流程 429
14.7.1 一般零件的典型工艺流程 429
14.7 落压零件典型工艺流程 429
14.8.2.1 下模的结构形式 430
14.8.2 一般结构技术要求 430
14.8 落压模设计技术要求 430
14.8.1 设计技术要求的内容 430
14.8.3.1 下模的特殊要求 431
14.8.3 合用模的特殊要求 431
14.8.2.2 导向形式 431
14.8.2.3 模具与落锤的匹配 431
14.8.4.2 过渡模的制形与打样依据 432
14.8.4.1 过渡模的制造依据 432
14.8.3.2 上模的特殊要求 432
14.8.4 对过渡模的特殊要求 432
14.8.5 落压模材料的选择 433
14.9.3 落压成形中的技术安全 434
14.9.2 落压模的保管 434
14.9 落压模的安装保管及成形中的技术安全 434
14.9.1 落压模的安装 434
14.10.1 气动落锤 435
14.10 落压成形设备 435
14.10.2.5 辗光机 436
14.10.2.4 收边机 436
14.10.2 辅助设备 436
14.10.2.1 剪切设备 436
14.10.2.2 点击锤 436
14.10.2.3 收缩机 436
14.10.2.6 成形机 437
15.1.2.1 零件弯边的工艺性 439
15.1.2 橡皮成形零件结构工艺性 439
第15章 橡皮成形零件工艺设计 439
15.1 零件分类及其结构工艺性 439
15.1.1 定义及零件分类 439
15.1.1.1 定义 439
15.1.1.2 零件分类 439
15.2.1.2 橡皮容框设计要求 440
15.2.1.1 橡皮容框结构 440
15.1.2.2 零件结构形式的工艺性 440
15.1.2.3 零件成形极限的工艺性 440
15.2 橡皮成形方法 440
15.2.1 橡皮容框成形 440
15.3.1.2 成形极限 441
15.3.1.1 典型零件 441
15.2.1.3 容框中橡皮的选择 441
15.2.2 橡皮囊液压成形 441
15.3 成形工艺参数 441
15.3.1 直线弯边 441
15.3.2.1 凸曲线弯边典型零件及成形极限 442
15.3.2 曲线弯边 442
15.3.2.2 凹曲线弯边典型零件及成形极限 444
15.3.3.3 下陷成形工艺要求 446
15.3.3.2 加强窝成形工艺要求 446
15.3.3 其他成形工艺要求 446
15.3.3.1 减轻孔成形工艺要求 446
15.4.2.1 压型模设计要求 447
15.4.2 压型模设计 447
15.3.3.4 加强埂成形工艺要求 447
15.4 橡皮成形工艺设计 447
15.4.1 展开件的确定 447
15.4.2.4 零件在模具上的定位方法 449
15.4.2.3 模具高度的确定 449
15.4.2.2 压型模的材料 449
15.4.3 提高曲线弯边零件成形质量的措施 450
15.4.4.1 保护橡皮胎的方法及措施 453
15.4.4 橡皮囊的保护 453
15.4.5 橡皮囊液压机中辅助橡皮的选择 454
15.4.4.2 安放模具操作上应遵循的规则 454
15.5.4 模具回弹角的确定 455
15.5.3 平面平直度的保证 455
15.5 “一步法”成形 455
15.5.1 定义与应用范围 455
15.5.2 “一步法”成形冷藏参数的确定 455
15.5.2.1 成形前最长存放时间 455
15.5.2.2 LY12材料冷藏温度与机械性能的关系 455
15.5.5.2 多辊板材矫正机 456
15.5.5.1 低温室 456
15.5.5 “一步法”生产线的主要设备 456
15.5.5.3 无齿收缩机 457
15.5.6 典型零件工艺流程 458
15.7 液压橡皮囊成形机的规格 459
15.6 橡皮压制镁合金零件 459
16.2 零件分类及结构工艺性 460
16.1 定义与范围 460
第16章 旋压零件成形 460
16.2.2 结构工艺性 461
16.2.1 零件分类 461
16.3.1.2 毛坯与材料 465
16.3.1.1 普通旋压的主要成形方法 465
16.3 旋压的基本成形方法 465
16.3.1 普通旋压 465
16.3.1.3 工艺参数 466
16.3.1.4 工艺装备 471
16.3.2.1 非筒形件变薄旋压 474
16.3.2 变薄旋压 474
16.3.1.5 零件质量 474
16.3.2.2 筒形件变薄旋压 482
16.3.3.1 锥形小端与筒形组合件的旋压工艺 490
16.3.3 基本旋压工艺方法的联合应用 490
16.3.4.1 分层错距旋压 491
16.3.4 几种特殊的旋压方法 491
16.3.3.2 锥形大端与筒形组合件的旋压工艺 491
16.3.4.2 滚珠旋压 492
16.3.4.6 加热旋压和收口 493
16.3.4.5 无模旋压 493
16.3.4.3 内旋压 493
16.3.4.4 张力旋压 493
16.3.5 典型零件的旋压工艺 495
16.4 旋压过程中的一些特殊问题和解决措施 496
16.5.1 通用自动旋压机 497
16.5 旋压机床选用 497
16.5.2 专用自动旋压机 499
16.5.3 自动旋压机的数控化 501
17.1.2 型材零件结构工艺性 503
17.1.1 典型零件分类 503
第17章 型材零件成形 503
17.1 典型零件分类及结构工艺性 503
17.2.1.2 “T”型材切断模 504
17.2.1.1 常用型材组合冲模 504
17.2 型材下料 504
17.2.1 冲切 504
17.3.2.1 拉弯方式 505
17.3.2 拉弯方式及参数选择 505
17.2.1.3 槽型材切断组合冲模 505
17.2.2 锯切 505
17.2.3 铣切 505
17.3 拉弯成形 505
17.3.1 定义、特点及适用范围 505
17.3.2.2 拉弯工艺参数的选择 506
17.3.2.3 拉弯变形量的控制 507
17.3.5 拉弯夹头 508
17.3.4 拉弯模的安装 508
17.3.3 拉弯机 508
17.3.7.1 正反曲率方向变化零件的拉弯 509
17.3.7 几种特殊形状零件的拉弯 509
17.3.6 拉弯成形中的润滑 509
17.3.7.4 异型截面型材的拉弯 510
17.3.7.3 变截面型材的拉弯 510
17.3.7.2 变角度零件的拉弯 510
17.3.8.2 复杂截面型材零件 511
17.3.8.1 一般零件 511
17.3.8 典型拉弯零件工艺流程 511
17.4.2.2 回转牵引绕弯 512
17.4.3 绕弯力矩计算 512
17.4 绕弯成形 512
17.4.1 定义与适用范围 512
17.4.2 绕弯方法 512
17.4.2.1 侧压绕弯 512
17.4.4.2 回弹量计算 513
17.4.4.1 绕弯工装设计要求 513
17.4.4 绕弯工装设计及回弹量计算 513
17.5.3 型材滚弯质量问题及解决措施 514
17.5.2 等曲率型材零件的滚弯 514
17.5 滚弯成形 514
17.5.1 定义与适用范围 514
17.6.2 压弯成形工艺过程 515
17.6.1 定义与适用范围 515
17.5.4 滚轮设计 515
17.6 压弯成形 515
17.7.2 型材下陷标准 516
17.7.1 型材下陷分类 516
17.7 型材压下陷 516
17.7.4.2 专用下陷模 517
17.7.4.1 通用下陷模 517
17.7.3 下陷压制要求 517
17.7.4 下陷模 517
17.7.5.4 测温方法 518
17.7.5.3 加热方式 518
17.7.5 加热压下陷 518
17.7.5.1 LC4材料加热压下陷 518
17.7.5.2 镁合金的加热压下陷 518
17.8.2.2 校形顺序 519
17.8.2.1 型材校形的一般要求 519
17.8 型材的校形 519
17.8.1 型材的畸变校形 519
17.8.2 型材校形的顺序及范围 519
17.8.2.4 型材校形的设备、装备及方法 520
17.8.2.3 校形的范围 520
17.9.1 制工艺孔 521
17.9 型材的辅助加工 521
17.9.2 制斜角 522
18.1.2 导管零件分类 524
18.1.1 航空导管零件特点 524
第18章 导管零件成形 524
18.1 导管零件特点、分类及结构工艺性 524
18.2.1 除油 526
18.2 管子除油与下料 526
18.1.3 结构工艺性 526
18.2.2 下料 527
18.3.1 导管取样 528
18.3 导管弯曲 528
18.3.2.1 绕弯法 529
18.3.2 冷弯法与所用的工具 529
18.3.2.2 绕弯工具 531
18.3.2.3 其他弯管法 535
18.3.3 热弯法及所用的工装设备 537
18.3.4 弯管填充料及润滑剂 538
18.3.5 弯管故障及排除 539
18.3.6 弯管主要设备 540
18.3.7 工艺参数及计算公式 542
18.3.8.1 国内标准 545
18.3.8 弯管制造标准 545
18.3.8.2 国外标准 546
18.4 管子端头加工 548
18.4.1.1 管端扩口形式及几何尺寸 549
18.4.1 管子扩口 549
18.4.1.2 常用的扩口方法及扩口工艺参数 550
18.4.2.1 导管端头镶装橄榄头的管端加工 552
18.4.2 无扩口连接管端加工 552
18.4.2.3 导管端头挤压锥形定位环 553
18.4.2.2 导管端头镶装柔性环的管端加工 553
18.4.2.5 管套紧箍 554
18.4.2.4 导管端头胀挤 554
18.4.3 波纹成形 555
18.4.4 管子缩口 557
18.4.4.2 旋压缩口 558
18.4.4.1 模压缩口 558
18.4.4.5 缩口工艺参数 560
18.4.4.4 加热缩口 560
18.4.4.3 冲击缩口(旋转模锻缩口) 560
18.4.5.1 管端扩径 562
18.4.5 管端其他成形方法 562
18.4.5.2 小翻边和小卷边 563
18.5.1 模压成形 565
18.5 异型管成形与半管焊接成形 565
18.5.3.1 矩形管弯曲的特点 566
18.5.3 矩形管弯曲 566
18.5.2 滚压成形 566
18.5.3.2 矩形管弯曲方法及故障分析 567
18.5.4.2 焊前准备 568
18.5.4.1 制造依据及协调 568
18.5.4 半管焊接成形 568
18.5.4.5 钛和钛合金半管氩弧焊 569
18.5.4.4 半管氩弧焊 569
18.5.4.3 半管气焊 569
18.5.5.2 焊接夹具 570
18.5.5.1 制孔 570
18.5.5 支管焊接成形 570
18.6.1.2 铝合金导管的阳极化处理 572
18.6.1.1 铝合金导管的化学氧化 572
18.6 导管表面处理与保护 572
18.6.1 铝合金导管的表面处理 572
18.7.1 导管外形与接头检验 573
18.7 导管的检验、试验、清洗与包封 573
18.6.2 碳钢导管的表面处理 573
18.6.3 铜导管的表面处理 573
18.6.4 导管涂漆 573
18.7.2 导管管壁检验 574
18.7.5.1 试验压力 575
18.7.5 导管液压试验 575
18.7.3 导管端头检验 575
18.7.3.1 带球体和内锥体接管嘴的端头检验 575
18.7.3.2 扩口端头检验 575
18.7.4 导管气密试验 575
18.7.6 导管最后清洗 576
18.7.5.2 渗漏试验 576
18.8 导管零件典型工艺流程 577
18.7.7.2 导管的封存 577
18.7.7 导管端头包装和导管封存 577
18.7.7.1 导管端头包装 577
19.1.1 钛板的成形特性 580
19.1 钛合金成形的特性和种类 580
第19章 钛合金钣金零件成形 580
19.2.1 冷成形特点和工艺方法 582
19.2 冷成形 582
19.1.2 钛合金钣金零件成形工艺种类 582
19.2.2.3 闸压成形 583
19.2.2.2 橡皮成形 583
19.2.2 工艺参数 583
19.2.2.1 覆盖成形 583
19.2.2.4 型辊成形 584
19.2.2.7 压下陷 585
19.2.2.6 压窝 585
19.2.2.5 翻边 585
19.2.2.8 拉深 586
19.2.2.9 拉形和拉弯 587
19.2.3 消除应力 588
19.2.2.10 冷校形 588
19.2.6 典型工艺流程和实例 589
19.2.5.2 解决起皱的方法 589
19.2.4 工装设备要求 589
19.2.5 质量问题及解决方法 589
19.2.5.1 解决回弹的方法 589
19.3.1 热成形的特点、类型和应用范围 590
19.3 热成形 590
19.3.2.1 成形温度 591
19.3.2 工艺参数 591
19.3.2.3 成形时间 592
19.3.2.2 成形压力 592
19.3.2.4 其他规范 593
19.3.3 加热方法 594
19.3.2.6 基本金属去除量 594
19.3.2.5 氧化膜厚度 594
19.3.4.2 热膨胀差值修正 595
19.3.4.1 设计要求 595
19.3.4 热成形模具设计要求 595
19.3.4.3 模具材料 596
19.3.7.1 典型工艺流程 597
19.3.7 典型零件工艺流程和实例 597
19.3.5 热成形设备 597
19.3.6 润滑 597
19.4.1 热校形特点、类型和应用范围 598
19.4 热校形 598
19.3.7.2 实例 598
19.4.2 工艺参数 599
19.4.4 典型零件工艺实例 600
19.4.3 设备选择 600
19.4.5.4 注意事项 601
19.4.5.3 验收 601
19.4.5 钛零件的质量控制 601
19.4.5.1 制造过程控制 601
19.4.5.2 形状和尺寸检验 601
19.5.2 模具典型结构与应用实例 602
19.5.1 半模热成形的特点和介质材料 602
19.5 半模热成形和热校形技术 602
20.2.1 爆炸拉深分类,特点及用途 604
20.2 爆炸拉深 604
第20章 爆炸成形零件工艺设计 604
20.1 定义与特点 604
20.1.1 定义 604
20.1.2 爆炸成形的特点 604
20.2.2.1 药形 605
20.2.2 爆炸拉深工艺参数的选择 605
20.2.2.3 药量 606
20.2.2.2 药位 606
20.2.2.4 水头(或水深) 607
20.2.2.10 变薄量 608
20.2.2.9 压边力 608
20.2.2.5 真空度 608
20.2.2.6 传压介质的边界条件 608
20.2.2.7 拉深比 608
20.2.2.8 凹模圆角半径 608
20.2.3 爆炸拉深中出现的质量问题分析 609
20.2.4.1 环形冷气瓶爆炸拉深成形 610
20.2.4 典型爆炸拉深件的工艺参数 610
20.3.2 爆炸胀形工艺参数选择 611
20.3.1 爆炸胀形分类 611
20.2.4.2 油箱零件爆炸拉深工艺参数 611
20.3 爆炸胀形 611
20.3.2.2 药包形状与位置 612
20.3.2.1 胀形毛坯的形状及尺寸 612
20.3.2.3 药量的估算及影响因素 613
20.3.4 爆炸胀形典型零件工艺参数 614
20.3.3 爆炸胀形的质量分析 614
20.3.5.3 工艺参数 615
20.3.5.2 胀形装置结构 615
20.3.5 真空模腔橡皮囊爆炸胀形 615
20.3.5.1 特点 615
20.4.1 导向型材爆炸校形 616
20.4 爆炸校形 616
20.5 爆炸冲孔 617
20.4.2 隔板爆炸校形 617
20.6.1 成组爆炸成形特点 618
20.6 成组爆炸成形 618
20.6.3 橡胶板的选用 619
20.6.2.4 容框的密封 619
20.6.2 容框的设计 619
20.6.2.1 容框的工艺要求 619
20.6.2.2 容框结构尺寸的确定 619
20.6.2.3 容框材料及典型结构 619
20.6.5 成组爆炸的质量分析 620
20.6.4 成组爆炸成形工艺参数 620
20.7.1 炸药 621
20.7 爆炸成形常用的爆炸用品 621
20.7.2.1 起爆用品的性能、规格和用途 622
20.7.2 起爆用品及引爆技术 622
20.8 爆炸成形设施 623
20.7.2.2 引爆技术 623
20.8.2.1 爆炸成形水井的结构形式 624
20.8.2 爆炸成形水井 624
20.8.1 爆炸成形平台 624
20.8.3.1 封闭爆炸成形机床 625
20.8.3 爆炸成形机床 625
20.8.2.2 爆炸成形水井结构尺寸的确定 625
20.8.2.3 井壁强度估算 625
20.8.3.2 火药锤 626
20.8.4.2 爆炸成形场地面积的确定 627
20.8.4.1 爆炸成形厂房的要求 627
20.8.4 爆炸成形厂房 627
20.9 爆炸成形的安全 628
21.1.2 胀形方法 629
21.1.1 胀形的定义及应用 629
第21章 局部成形零件工艺设计 629
21.1 胀形 629
21.1.3 胀形参数 631
21.1.6 液压胀形典型零件举例 633
21.1.5 胀形件质量控制 633
21.1.4 胀形过程中的润滑 633
21.2.3 起伏成形的工艺参数 634
21.2.2 起伏成形的方法 634
21.2 起伏成形 634
21.2.1 起伏成形的定义及应用 634
21.2.3.1 起伏成形的极限高(深)度 635
21.3.1 压印定义及应用 636
21.3 压印 636
21.2.3.2 成形力 636
21.3.2 工艺压印设计要求 638
21.3.3.1 工艺压印的要求 640
21.3.3 压印工艺要求 640
21.3.4 压印力 641
21.3.3.2 艺术压印的要求 641
21.3.6 压印模设计要求 643
21.3.5 压印中的润滑 643
21.4.2.1 圆孔翻边对结构要素的要求 646
21.4.2 圆孔翻边 646
21.3.7 压印设备 646
21.3.8 压印质量 646
21.4 翻边 646
21.4.1 翻边的定义与应用 646
21.4.2.2 圆孔翻边系数 647
21.4.3 非圆孔翻边 648
21.4.2.4 圆孔翻边工艺设计 648
21.4.2.3 影响翻边成形极限的因素 648
21.4.4.2 翻边高度较大的小零件 650
21.4.4.1 变薄翻边工艺计算 650
21.4.4 变薄翻边 650
21.4.6 翻边模设计要求 651
21.4.5 翻边力 651
21.4.7 翻边质量 653
22.1.3.1 超塑性变形的宏观特性 654
22.1.3 超塑性的宏观特性及其工程特点 654
第22章 超塑性成形结构件工艺设计 654
22.1 超塑性成形 654
22.1.1 定义 654
22.1.2 分类 654
22.1.4.1 金属超塑性变形的力学特征 655
22.1.4 影响金属超塑性的变形因素 655
22.1.3.2 超塑性成形的工程特点 655
22.1.5 超塑性机理 658
22.1.4.2 金属超塑性的组织特性 658
22.1.7 辅助材料 659
22.1.6 超塑性金属材料 659
22.1.8.1 零件壁厚的结构工艺性 660
22.1.8 超塑性成形(含超塑成形/扩散连接)零件的结构工艺性 660
22.1.8.3 夹层壁板类构件的结构工艺性 662
22.1.8.2 便于脱模和保证高温密封保护的结构工艺性 662
22.1.9.1 超塑性成形的工艺参数 663
22.1.9 超塑性成形的工艺参数和方法 663
22.1.9.2 超塑性成形方法 665
22.1.9.3 超塑性成形的典型工艺流程(超塑气压法) 666
22.1.9.4 零件壁厚控制方法 667
22.1.9.5 铝合金超塑性成形的空洞抑制方法 668
22.1.10.2 模具设计结构形式 669
22.1.10.1 模具材料 669
22.1.10 超塑性成形模具 669
22.1.11 超塑性成形设备(装置) 671
22.2.1.1 钣金的扩散连接 675
22.2.1 组合工艺的基础和基本内容 675
22.2 超塑成形/扩散连接组合工艺 675
22.2.2 组合工艺的结构基本形式 677
22.2.1.2 组合工艺的条件 677
22.2.3 组合工艺方法和规范 678
22.2.5 构件质量检验的技术要求和检验内容 679
22.2.4 组合工艺的温度、压力、时间(即T-P-t)曲线 679
23.2.1 生产纲领 681
23.2 飞机钣金车间的生产纲领和劳动量 681
第3篇 飞机钣金车间工艺设计环境要求和技术安全第23章 飞机钣金车间工艺设计23.1 飞机钣金车间工艺设计的内容 681
23.2.2.1 用统计法估算劳动量 682
23.2.2 劳动量 682
23.2.2.3 用比例分配法估算劳动量 683
23.2.2.2 用零件分类法估算劳动量 683
23.3.2 工人年时基数 684
23.3.1 飞机钣金车间的人员分类 684
23.3 飞机钣金车间的人员 684
23.3.3 估算生产工人数量的方法 685
23.4.1.3 飞机钣金车间设备数量的计算 686
23.4.1.2 设备分类和设备年时基数 686
23.4 飞机钣金车间的设备 686
23.4.1 飞机钣金车间工艺设备选择 686
23.4.1.1 钣金设备选择的注意事项 686
23.4.2 飞机钣金车间设备的主要技术参数 688
23.4.3.1 上部运输设备的主要参数 700
23.4.3 飞机钣金车间的上部运输设备 700
23.5.1 飞机钣金车间的面积分类 703
23.5 飞机钣金车间的面积 703
23.4.3.2 布置上部运输设备的注意事项 703
23.5.2.2 用计算法估算面积 704
23.5.2.1 用对比法估算面积 704
23.5.2 确定车间面积的方法 704
23.6.1 飞机钣金车间工艺布置的主要内容 707
23.6 飞机钣金车间的工艺布置 707
23.6.2 绘制飞机钣金车间工艺布置图的步骤 709
23.6.3 设备布置 712
23.6.4 设备间距 713
23.7.1.2 进口设备费用的估算 714
23.7.1.1 国内设备费用的估算 714
23.7 飞机钣金车间的技术经济估算和指标 714
23.7.1 工艺设备投资的估算方法 714
23.7.3 飞机钣金车间设计的技术经济指标 715
23.7.2 飞机钣金车间投资估算 715
第24章 飞机钣金车间的环境要求和技术安全24.1 飞机钣金车间的环境要求 717
24.2 控制飞机钣金车间噪声、振动的基本措施 718
24.3 飞机钣金车间应用色彩效应的方法 719
24.4 飞机钣金车间的技术安全 721
A.1.1 变形铝合金 723
A.1 常用材料国内外牌号对照 723
附录 723
附录A 常用材料国内外牌号对照 723
A.1.3 铜及铜合金 725
A.1.2 变形镁合金 725
A.1.5 常用钢材 726
A.1.4 钛及钛合金 726
B.2 美国铝合金热处理状态代号说明 727
B.1 有色金属及合金材料状态代号 727
附录B 有色金属的材料状态 727
附录C 美国板料厚度编级表 730
E.1.2 感光液成分 731
E.1.1 印制网格过程 731
附录D 英制单位与国际单位换算 731
附录E 坐标网格技术 731
E.1 接触照相法印制网格 731
E.2.5 各种形式的网格图案及模版 732
E.2.4 电蚀参数 732
E.1.3 显影液(偶联剂) 732
E.2 电化学腐蚀法印制网格 732
E.2.1 电化学腐蚀法印制网格过程 732
E.2.2 电解液成分 732
E.2.3 中和液成分 732
参考文献 734
- 《市政工程基础》杨岚编著 2009
- 《工程静力学》王科盛主编 2019
- 《中国制造业绿色供应链发展研究报告》中国电子信息产业发展研究院 2019
- 《中央财政支持提升专业服务产业发展能力项目水利工程专业课程建设成果 设施农业工程技术》赵英编 2018
- 《Maya 2018完全实战技术手册》来阳编著 2019
- 《化学反应工程》许志美主编 2019
- 《绿色过程工程与清洁生产技术 张懿院士论文集精选 上》《绿色过程工程与清洁生产技术》编写组编 2019
- 《软件工程》齐治昌,谭庆平,宁洪编著 2019
- 《高等教育双机械基础课程系列教材 高等学校教材 机械设计课程设计手册 第5版》吴宗泽,罗圣国,高志,李威 2018
- 《化学工程与工艺专业实验指导》郭跃萍主编 2019
- 《莼江曲谱 2 中国昆曲博物馆藏稀见昆剧手抄曲谱汇编之一》郭腊梅主编;孙伊婷副主编;孙文明,孙伊婷编委;中国昆曲博物馆编 2018
- 《指向核心素养 北京十一学校名师教学设计 英语 七年级 上 配人教版》周志英总主编 2019
- 《植物百科彩色图鉴 第2卷》植物百科彩色图鉴编委会主编 2012
- 《远去的老调》经典文库编委会编 2019
- 《北京生态环境保护》《北京环境保护丛书》编委会编著 2018
- 《莼江曲谱 1 中国昆曲博物馆藏稀见昆剧手抄曲谱汇编之一》郭腊梅主编;孙伊婷副主编;孙文明,孙伊婷编委;中国昆曲博物馆编 2018
- 《共和国日记 1964》《共和国日记》编委会编 2019
- 《中国地方艺文荟萃 华北东北卷 第1辑 3》《中国地方艺文荟萃》编委会编 2018
- 《绿色过程工程与清洁生产技术 张懿院士论文集精选 上》《绿色过程工程与清洁生产技术》编写组编 2019
- 《中国地方艺文荟萃 华北东北卷 第1辑 1》《中国地方艺文荟萃》编委会编 2018
- 《指向核心素养 北京十一学校名师教学设计 英语 七年级 上 配人教版》周志英总主编 2019
- 《北京生态环境保护》《北京环境保护丛书》编委会编著 2018
- 《指向核心素养 北京十一学校名师教学设计 英语 九年级 上 配人教版》周志英总主编 2019
- 《高等院校旅游专业系列教材 旅游企业岗位培训系列教材 新编北京导游英语》杨昆,鄢莉,谭明华 2019
- 《中国十大出版家》王震,贺越明著 1991
- 《近代民营出版机构的英语函授教育 以“商务、中华、开明”函授学校为个案 1915年-1946年版》丁伟 2017
- 《新工业时代 世界级工业家张毓强和他的“新石头记”》秦朔 2019
- 《智能制造高技能人才培养规划丛书 ABB工业机器人虚拟仿真教程》(中国)工控帮教研组 2019
- 《陶瓷工业节能减排技术丛书 陶瓷工业节能减排与污染综合治理》罗民华著 2017
- 《全国职业院校工业机器人技术专业规划教材 工业机器人现场编程》(中国)项万明 2019