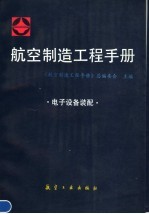
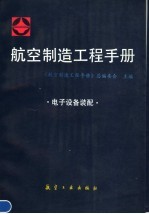
航空制造工程手册:电子设备装配PDF电子书下载
- 电子书积分:17 积分如何计算积分?
- 作 者:《航空制造工程手册》总编委会主编
- 出 版 社:北京:航空工业出版社
- 出版年份:1995
- ISBN:7800468682
- 页数:554 页
第1章 航空电子设备装配 1
1.1 航空电子设备发展和装配工艺 1
1.2 航空电子设备装配特点 2
1.4 航空电子设备装配分类 3
1.3 航空电子设备装配要求 3
1.5.1 电装装配工艺 4
1.5 航空电子设备装配工艺 4
1.6 印制板组装件装配 5
1.5.3 其他装配工艺 5
1.5.2 机械装配工艺 5
1.6.3 印制板组装件手工装配一般操作步骤 6
1.6.2 表面安装元器件在印制板上的安装 6
1.6.1 通孔安装元器件在印制板上的安装 6
1.6.4 印制板组装件装配中应注意的特殊问题 7
1.7.1 电气组(部)件手工装配一般操作步骤 8
1.7 电气组(部)件装配 8
1.7.2 电气组(部)件装配中应注意的问题 9
1.8.2 机械结构组(部)件装配中应注意的问题 10
1.8.1 机械结构组(部)件手工装配一般操作步骤 10
1.8 机械结构组(部)件装配 10
1.9.1 整机(单元体)装配一般操作步骤 11
1.9 整机(单元体)装配 11
1.9.2 整机装配中应注意的问题 12
1.10.2 机械环境对产品的影响及应采取的装配措施 13
1.10.1 气候环境对产品的影响及应采取的装配措施 13
1.10 环境条件与装配的关系 13
1.11.1 装配图分类 14
1.11 装配用技术文件 14
1.11.2 装配图应表达内容 15
1.11.3 工艺文件的组成 16
1.11.4 工艺文件编制要求 17
2.1.1 印制板的分类 19
2.1 印制板 19
第2章 装配用印制板、元器件和材料 19
2.1.4 印制电路用覆铜箔层压板的识别 20
2.1.3 印制板储存和保管要求 20
2.1.2 印制板的外形特征及识别 20
2.1.2.1 刚性印制板的外形 20
2.1.2.2 刚性印制板的识别 20
2.2.1.1 电阻器的类别 21
2.2.1 电阻器 21
2.2 阻容器件 21
2.2.1.3 电阻器实物的识别 23
2.2.1.2 图纸上电阻器的识别 23
2.2.2.1 电位器的类别 25
2.2.2 电位器 25
2.2.1.4 电阻器储存和保管要求 25
2.2.3.1 电容器的类别 27
2.2.3 电容器 27
2.2.2.2 图纸上电位器的识别 27
2.2.2.3 电位器实物的识别 27
2.2.2.4 电位器储存和保管要求 27
2.2.3.4 电容器储存和保管要求 31
2.2.3.3 电容器实物的识别 31
2.2.3.2 图纸上电容器的识别 31
2.3.1.1 半导体二极管类别 32
2.3.1 半导体二极管 32
2.3 半导体分立器件 32
2.3.1.2 图纸上半导体二极管的识别 33
2.3.1.3 半导体二极管实物的识别 34
2.3.2.1 半导体三极管类别 35
2.3.2 半导体三极管 35
2.3.2.3 半导体三极管实物的识别 36
2.3.2.2 图纸上半导体三极管的识别 36
2.3.3 半导体晶体管储存和保管要求 37
2.3.2.4 半导体三极管引脚的识别 37
2.4.1 半导体集成电路类别 38
2.4 半导体集成电路 38
2.4.2 国内外同类产品型号对照 39
2.4.3 集成电路封装形式 62
2.4.5 集成电路实物的识别 65
2.4.4 图纸上集成电路的识别 65
2.4.6 半导体集成电路储存和保管要求 66
2.5.1 SMD的类别 67
2.5 表面安装元器件(SMD) 67
2.5.2.1 SMD外形特征 68
2.5.2 SMD外形特征及引脚类型 68
2.5.2.2 引脚类型 69
2.6.1 电连接器类别 70
2.6 电连接器 70
2.5.3 SMD在图纸上的表示方法 70
2.5.4 表面安装元器件储存和保管要求 70
2.6.2 XKE型压接电连接器 71
2.6.5 ATR机箱后连接器 74
2.6.4 53系列焊接式印制板电连接器 74
2.6.3 DK-621型总线电连接器 74
2.6.6 38999系列耐环境快速分离高密度小圆形电连接器 76
2.6.7 耐环境快速分离圆形电连接器 78
2.7.1 开关的分类与识别 80
2.7 开关 80
2.6.8 电连接器的储存和保管 80
2.8.1 密封电磁继电器的类别 81
2.8 密封继电器 81
2.7.2 开头的储存和保管 81
2.9.1 电线和电缆的分类 84
2.9 电线和电缆 84
2.8.2 继电器储存和保管 84
2.9.2 绝缘电线、电缆的型号与结构特征 85
2.9.3.1 电线、电缆在图纸上的识别 86
2.9.3 电线和电缆的识别 86
2.10.1 紧固件的分类 87
2.10 紧固件 87
2.9.3.2 电线、电缆实物的识别 87
2.9.4 电线、电缆的储存和保管 87
2.10.2.2 紧固件实物的识别 88
2.10.2.1 紧固件在图纸上的标记方法 88
2.10.2 紧固件的识别 88
3.1.2 洁净车间(厂房)使用要求 90
3.1.1 环境洁净度要求 90
第3章 装配前的准备 90
3.1 装配环境控制及工艺布置 90
3.1.4.2 静电防护操作要求 91
3.1.4.1 静电敏感器件 91
3.1.3 污染物和剩余物的控制 91
3.1.4 静电防护要求 91
3.1.4.3 静电敏感器件装配要求 94
3.1.4.4 测试和试验设备 95
3.1.4.5 防静电器材 96
3.1.5 工艺布置要求 97
3.2.2.1 初步设计阶段工艺性审查的内容 98
3.2.2 工艺性审查的内容 98
3.2 产品设计工艺性审查 98
3.2.1 工艺性审查的目的 98
3.2.3 工艺性审查的基本要求 99
3.2.2.3 工作图设计阶段工艺性审查的内容 99
3.2.2.2 技术设计阶段工艺性审查的内容 99
3.2.5 产品设计工艺性主要指标项目 100
3.2.4 工艺性审查的方式和程序 100
3.2.6.2 电子产品可靠性设计的工艺性审查 102
3.2.6.1 总则 102
3.2.6 可靠性设计工艺性审查 102
3.4.1 元器件入库检验 104
3.4 元器件的入库检验与复验 104
3.3 元器件和材料的备料 104
3.3.1 备料原则 104
3.3.2 备料方法 104
3.4.2 库存元器件的复验 106
3.5 元器件的老化筛选 107
3.5.1 半导体分立器件老化筛选 108
3.5.2 钽电容老化筛选 112
3.5.3 继电器老化筛选 113
3.5.4 电阻和电位器老化筛选 115
3.5.5 元器件老化筛选试验报告和结果处理 116
3.6.2.2 自动化清洗 117
3.6.2.1 手工清洗 117
3.6 装配用零件、紧固件的表面处理 117
3.6.1 表面处理要求 117
3.6.2 清洗方法 117
3.7.1 手工装配工具 118
3.7 工具和设备的选用 118
3.6.2.3 印制板组装件焊接面的清洗 118
3.6.2.4 机械零、部件清洗 118
3.7.2 印制板通孔安装设备 120
3.7.3 印制板表面安装设备 121
4.1.1 分立元器件引线成形要求 122
第4章 元器件引线、导线端头的成形和连接4.1 元器件引线成形 122
4.1.3 元器件引线成形方法 124
4.1.2 扁平封装集成电路引线成形要求 124
4.1.4 元器件引线的矫直 125
4.2.3 钩绕连接方法 126
4.2.2 缠绕连接方法 126
4.1.5 元器件引线成形中应注意事项 126
4.2 元器件引线在接线端子上的连接 126
4.2.1 连接形式 126
4.3.1 连接形式 127
4.3 导线端头与接线端子连接 127
4.2.4 插接连接方法 127
4.2.5 连接要求 127
4.3.3 导线端头与各种接线端子连接 128
4.3.2 连接要求 128
4.4 工序检验 131
5.2.1 套管的材料及其特性 133
5.2 套管的合理选用 133
第5章 套管的使用和安装 133
5.1 套管的使用 133
5.2.2.2 套管尺寸的选择 137
5.2.2.1 套管材料的选择 137
5.2.2 套管的选用 137
5.3.1 安装方法 139
5.3 元器件引线套管的安装 139
5.3.2.2 套管颜色的代用色 140
5.3.2.1 套管颜色的表示 140
5.3.2 色标套管 140
5.4 导线套管的安装 141
5.5.2 单根导线套管的固定 143
5.5.1 电连接器套管的固定 143
5.5 电连接器导线端头套管安装特殊要求及捆扎 143
5.6 热缩绝缘套管的安装要求 144
5.7.1 导线、电缆的整体套管 145
5.7 整体套管使用场合的规定 145
5.8 套管在装配操作中的维护 146
5.7.2 元器件的整体套管 146
5.9 套管安装后的检验 147
6.1 一般要求 148
第6章 通孔元器件在印制板上安装 148
6.2 操作元器件时应注意的事项 150
6.3.1.2 安装要求 151
6.3.1.1 安装形式 151
6.3 通孔元器件安装 151
6.3.1 轴向引线元器件水平安装 151
6.3.3.2 安装要求 152
6.3.3.1 安装形式 152
6.3.2 轴向引线元器件垂直安装 152
6.3.2.1 安装条件 152
6.3.2.2 安装要求 152
6.3.3 径向引线元器件的安装 152
6.4.2.2 安装要求 154
6.4.2.1 安装方式 154
6.4 集成电路的安装 154
6.4.1 扁平封装器件的安装 154
6.4.1.1 安装方式 154
6.4.1.2 安装要求 154
6.4.2 双列直插器件的安装 154
6.5.2.2 粘合剂的类型 155
6.5.2.1 粘合剂的性能 155
6.5 元器件的粘接安装 155
6.5.1 粘接安装适用范围 155
6.5.2 粘合剂 155
6.5.3 元器件粘接安装形式 156
6.5.4.1 粘接安装步骤和操作要点 157
6.5.4 元器件粘接安装工艺 157
6.6.2 安装用机械零件 158
6.6.1 钳装安装适用范围 158
6.5.4.2 粘合剂的使用 158
6.5.4.3 粘合剂施加方法 158
6.6 元器件的钳装安装 158
6.6.4.1 紧固件连接要求 159
6.6.4 钳装中紧固件连接 159
6.6.3 元器件钳装安装的形式 159
6.7.2 铆接方法 160
6.7.1 铆接要求 160
6.6.4.2 螺钉的松动和防松措施 160
6.7 铆接件的安装 160
6.7.4 铆接件的拆卸与重铆 161
6.7.3 铆接缺陷 161
6.8.1 插装工序 162
6.8 插装机插装 162
第7章 表面安装元器件在印制板上安装 163
6.8.2 插装设备 163
7.1.3 表面安装技术与传统插装技术的区别 165
7.1.2 SMT的内容 165
7.1 表面安装技术 165
7.1.1 概念 165
7.2.1.1 电阻器 166
7.2.1 常用SMD的特征 166
7.2 SMD概况 166
7.2.1.2 电容器 169
7.2.1.4 片式机电元件 171
7.2.1.3 电感器 171
7.2.1.5 片式二极管与三极管 172
7.2.1.6 集成电路 173
7.2.2 常用SMD的工艺性 175
7.2.1.7 其他元件 175
7.2.3.1 外观质量检查 176
7.2.3 SMD质量检查与试验 176
7.2.3.2 可靠性及物理特性试验 177
7.2.4.1 SMD包装 181
7.2.4 SMD包装、标记及国内生产厂商 181
7.2.4.2 SMD国内生产厂商 182
7.3.1 组装方式 183
7.3 SMT组装工艺及生产线 183
7.3.2.2 混合组装工艺流程 184
7.3.2.1 全部SMD组装工艺流程 184
7.3.2 基本工艺流程 184
7.3.2.3 底面贴装工艺流程 185
7.3.3.1 生产线上的基本设备 186
7.3.3 生产线的组建 186
7.3.2.4 其他工艺流程 186
7.3.3.4 生产线的布局 187
7.3.3.3 生产线组建时应考虑的因素 187
7.3.3.2 实际生产线上的设备配置 187
7.4.1 焊膏 188
7.4 涂布材料 188
7.4.1.1 焊膏的组成 189
7.4.1.2 焊膏参数的选择 191
7.4.2 胶粘剂 193
7.4.1.3 对焊膏的基本要求 193
7.4.3 国内外生产涂布材料的主要厂商 194
7.4.2.2 胶粘剂的基本性能 194
7.4.2.1 胶粘剂的类型 194
7.5.1 基本涂布方法 195
7.5 涂布 195
7.5.2.1 焊膏涂布方法 196
7.5.2 焊膏涂布 196
7.5.2.2 影响焊膏涂布的参数 197
7.5.3.2 胶粘剂涂布中应注意的事项 198
7.5.3.1 胶粘剂涂布方法 198
7.5.2.3 焊膏涂布参数值 198
7.5.3 胶粘剂涂布 198
7.5.4.1 丝网印刷机的基本结构和操作 199
7.5.4 丝网印刷机 199
7.5.4.2 国内外丝网印刷机生产厂商 200
7.6.1 贴装位置精度要求 201
7.6 贴装 201
7.6.2 组装精度 204
7.6.3.1 贴片机分类 205
7.6.3 贴片机 205
7.6.3.2 贴片机主要技术指标 206
7.6.3.3 自动贴片机的结构 207
7.6.3.4 贴片机的编程与操作 210
7.6.3.5 国内外贴片机主要生产厂商 211
7.7.1.2 再流加温曲线 212
7.7.1.1 再流焊机理及特点 212
7.7 再流焊 212
7.7.1 再流焊的特点及工作原理 212
7.7.3 红外再流焊 213
7.7.2 几种再流焊方法比较 213
7.7.3.3 红外再流机国内外产品概况 214
7.7.3.2 红外再流焊时应注意的事项 214
7.7.3.1 红外再流机 214
7.7.4.3 汽相再流焊机 215
7.7.4.2 汽相再流焊中应注意的事项 215
7.7.4 汽相再流焊 215
7.7.4.1 汽相再流焊原理 215
7.7.6.1 热板式再流焊原理 216
7.7.6 热板式再流焊 216
7.7.5 激光再流焊 216
7.7.5.1 激光再流焊原理 216
7.7.5.2 激光再流焊应用场合 216
7.8.1 SMD波峰焊接时的主要缺陷 217
7.8 波峰焊 217
7.7.6.2 工作过程与应用场合 217
7.8.2 三种SMT波峰焊接法 218
7.8.4 SMT波峰焊机国内外生产厂商 219
7.8.3 SMT波峰焊的特点 219
7.10.1.1 矩形无引线焊端的焊点 220
7.10.1 SMD焊点标准 220
7.9 清洗、检测与返修 220
7.9.1 清洗 220
7.9.2 检测及返修 220
7.10 SMT组件的焊点 220
7.10.1.3 L形引线焊端的焊点 221
7.10.1.2 圆柱形无引线焊端的焊点 221
7.10.1.4 J形、V形引线焊端的焊点 222
7.10.1.7 无引线LCC的焊点 223
7.10.1.6 底部焊端的焊点 223
7.10.1.5 I形引线焊端的焊点 223
7.10.2.2 再流焊接缺陷及改进措施 224
7.10.2.1 常见SMD焊接缺陷 224
7.10.2 焊接缺陷、产生原因及改进措施 224
7.10.2.3 波峰焊接缺陷及改进措施 227
8.1.1.1 焊接材料的准备 230
8.1.1 焊接前的准备 230
第8章 手工焊和自动焊 230
8.1 手工烙铁焊接 230
8.1.1.2 电烙铁的选择 233
8.1.1.3 元器件引线和导线端头的搪锡 234
8.1.2.2 电烙铁的操作方法 239
8.1.2.1 电烙铁的握法 239
8.1.2 焊接操作 239
8.1.2.5 焊接基本步骤 240
8.1.2.4 焊接中的热分流 240
8.1.2.3 松香芯焊锡丝的使用方法 240
8.1.2.6 正确操作与不正确操作实例 242
8.1.3.2 插装(通孔)元器件的焊接 243
8.1.3.1 焊接中应注意的事项 243
8.1.3 印制板组装件焊接 243
8.1.4 导体与接线端子焊接 244
8.1.3.3 贴装(表面安装)元器件的焊接 244
8.1.4.1 导体与片状接线端子的焊接 245
8.1.5.1 印制板组装件焊盘上的焊点标准 246
8.1.5 焊点标准 246
8.1.4.2 导线与柱状接线端子的焊接 246
8.1.4.3 导线与管状接线端子的焊接 246
8.1.5.2 接线端子上的焊点标准 247
8.1.6 焊点缺陷 248
8.1.7.2 清除焊点上焊料的方法和步骤 251
8.1.7.1 焊点缺陷的可修复性 251
8.1.7 焊点的修正和重焊 251
8.1.7.3 焊点缺陷修正(重焊)方法和步骤 252
8.1.8 焊接质量工序检验 253
8.2.2.1 元器件引脚可焊性处理 254
8.2.2 焊接前的准备 254
8.2 自动焊接 254
8.2.1 自动焊接工艺流程 254
8.2.1.1 一次焊接工艺流程 254
8.2.1.2 二次焊接工艺流程 254
8.2.1.3 工艺特点比较 254
8.2.2.2 元器件引脚的成形 255
8.2.2.3 元器件插装 256
8.2.3.2 焊接前的预热 257
8.2.3.1 涂覆助焊剂 257
8.2.3 自动焊接 257
8.2.3.3 流动焊焊接 258
8.2.4.1 焊接参数 259
8.2.4 波峰焊焊接参数及注意事项 259
8.2.3.4 冷却 259
8.2.5 波峰焊常见故障及排除方法 260
8.2.4.2 波峰焊中应注意事项 260
8.2.6 波峰焊机的类别及结构 262
9.1.2 污染的危害 263
9.1.1 污染的类别 263
第9章 印制板组装件的清洗 263
9.1 印制板组装件的污染 263
9.3.1.2 清洗剂的选用 264
9.3.1.1 清洗剂的分类 264
9.2 印制板组装件的清洁度要求 264
9.3 清洗工艺方法的选用 264
9.3.1 清洗剂的分类及选用 264
9.3.2 清洗工艺方法的选用 265
9.4.1 溶剂基清洗工艺方法说明 266
9.4 熔剂基的清洗工艺操作方法 266
9.4.2 印制板组装件清洗工艺操作步骤 267
9.5.1 水基清洗工艺方法说明 269
9.5 水基清洗工艺操作方法 269
9.5.2.2 实例二 美国ECD620mp型清洗剂系统 271
9.5.2.1 实例一 水清洗与半水清洗 271
9.5.2 国外印制板组装件清洗工艺操作步骤 271
9.6 清洗后的包装和保管 273
9.5.2.3 F-113的替代产品 273
9.8.2.1 萃取熔液法 274
9.8.2 离子污染度测试 274
9.7 清洗中产生的缺陷类别及预防 274
9.8 印制板组装件清洁度检验 274
9.8.1 目视检查 274
9.8.2.2 “离子污染度测定仪”测试法 275
10.1.2 涂覆材料的类别 276
10.1.1 涂覆材料的性能 276
第10章 印制板组装件的涂覆 276
10.1 涂覆材料 276
10.1.3 涂覆材料的储存 277
10.1.4 涂覆材料分装 278
10.2.1 配比与混合 279
10.2 涂覆材料制备中应注意的事项 279
10.1.5 涂覆材料的环境适应性 279
10.3.1 待涂印制板组装件的准备 280
10.3 涂覆前的准备 280
10.2.2 混合中的气泡排除 280
10.3.2 不涂覆部位的掩蔽 281
10.4.2 刷涂工艺 282
10.4.1 工艺方法比较 282
10.4 印制板组装件敷形涂覆工艺 282
10.4.3 浸涂工艺 283
10.5.3 涂覆层易产生的缺陷及其防止方法 285
10.5.2 涂料厚度控制 285
10.5 涂覆工艺质量控制要点 285
10.5.1 涂覆材料存放时间的控制 285
10.7.2 合格标准 287
10.7.1 检验要求和方法 287
10.6 掩蔽层去除方法 287
10.7 涂覆的检验及合格标准 287
10.8 涂覆修正操作工序 288
11.2 返修时应注意的事项 290
11.1 印制板组装件缺陷及检查 290
第11章 印制板组装件返修 290
11.3.1.2 更换元器件步骤 291
11.3.1.1 拆卸元器件方法 291
11.3 通孔安装元器件印制板组装件返修 291
11.3.1 元器件的更换 291
11.3.2 元器件上固定物的更换 292
11.3.1.3 更换元器件应注意事项 292
11.4.2 拆卸(重装)SMD方法 293
11.4.1 返修步骤 293
11.4 表面安装元器件印制板组装件返修 293
11.4.3 重新涂布焊膏方法 294
11.5.2 修复工艺方法 295
11.5.1 印制板缺陷及修复限制 295
11.5 装配后印制板缺陷的返修 295
11.6 表面涂覆层的清除 296
11.6.2 表面涂覆层的清除方法 297
11.6.1 表面涂覆层的判别 297
11.6.3 清除表面涂覆层应注意事项 298
12.1.1.2 导线剥头 299
12.1.1.1 下料要求 299
第12章 接线装配 299
12.1 导线端头加工 299
12.1.1 一般导线端头加工 299
12.1.1.5 导线拼接 303
12.1.1.4 搪锡 303
12.1.1.3 捻头 303
12.1.2.1 不接地屏蔽导线 304
12.1.2 屏蔽导线及同轴电缆的端头加工 304
12.1.2.2 有接地端屏蔽导线 305
12.1.2.4 同轴电缆的加工 306
12.1.2.3 屏蔽导线端头加工注意事项 306
12.1.3.2 标记的方向和位置 308
12.1.3.1 导线标记的种类 308
12.1.3 导线标记 308
12.1.4 导线端头加工常见缺陷 309
12.1.3.3 标记检验 309
12.2.2 布线的注意事项 310
12.2.1 布线原则 310
12.2 布线 310
12.2.3.2 布线作业顺序 311
12.2.3.1 两种布线方法的比较 311
12.2.3 布线方法 311
12.3 线束的扎制 312
12.2.4 布线检验 312
12.3.1 线束图 313
12.3.2 线束卡 317
12.3.4 钉扎线钉 318
12.3.3 扎线板 318
12.3.5 放线 319
12.3.6 绑扎 320
12.3.7 线束包扎 322
12.3.8 线束检验 323
13.2.1 绕接工具的类别 324
13.2 绕接工具 324
第13章 导线与接线端绕接 324
13.1 绕接工艺特点 324
13.2.2 绕接工具简介 325
13.4.1 绕接导线要求 326
13.4 绕接前的准备 326
13.3 绕接分类 326
13.4.4 缠绕圈数的确定 327
13.4.3 接线端子的检查 327
13.4.2 接线端子要求 327
13.5.2 绕接操作中注意事项 328
13.5.1 绕接步骤 328
13.4.5 绕接导线端头绝缘层剥除 328
13.5 绕接器绕接 328
13.6 绕接工序质量控制要求 329
13.7.2 返修工序操作步骤 330
13.7.1 可返修的缺陷 330
13.7 绕接操作工序返修 330
14.1.2 装配步骤 331
14.1.1 连接电缆装配要求 331
第14章 整、部件装配 331
14.1 连接电缆装配 331
14.1.4.1 压接连接的特点 332
14.1.4 压接连接 332
14.1.3 连接电缆检验 332
14.1.4.2 压接操作 333
14.1.4.3 压接检查 334
14.1.4.5 压接工具 335
14.1.4.4 接触偶的装配 335
14.1.5 双屏蔽层电缆装配 337
14.1.4.6 工具的校正 337
14.2.1 概述 339
14.2 变压器装配 339
14.1.6 电缆打标记 339
14.1.6.1 电连接器打标记 339
14.1.6.2 电缆打标记 339
14.1.6.3 细电缆打标记 339
14.1.6.4 电缆标记检验 339
14.2.2 铁芯和绕组制造 341
14.2.4.3 配装灌封模 347
14.2.4.2 连线 347
14.2.3 变压器装配工艺的特点 347
14.2.4 脉冲变压器装配的操作方法 347
14.2.4.1 准备 347
14.2.5.2 打包 348
14.2.5.1 准备 348
14.2.4.4 清洗检查 348
14.2.5 电源变压器装配的操作方法 348
14.2.6.2 标记方法 349
14.2.6.1 标记的意义 349
14.2.5.3 连线 349
14.2.6 变压器的标记 349
14.3 传动控制机构的装配 350
14.2.7.3 通电检查 350
14.2.7 变压器的检验 350
14.2.7.1 外观 350
14.2.7.2 电气连续性 350
14.3.1.1 航空电子设备齿轮传动的特点 351
14.3.1 齿轮传动 351
14.3.1.3 齿轮传动机构装配的主要步骤 353
14.3.1.2 齿轮传动机构的装配要求 353
14.3.1.4 直齿圆柱齿轮传动机构的装配调整 358
14.3.1.5 圆锥齿轮传动机构的装配 364
14.3.1.6 蜗杆传动机构的装配 365
14.3.2.1 航空电子设备用滚动轴承的特点 366
14.3.2 滚动轴承的装配 366
14.3.2.3 滚动轴承的装配工艺及注意事项 368
14.3.2.2 滚动轴承的选配与修配 368
14.3.3 对其他一些控制机构的装配要求 372
14.4.1.1 微波器件的结构特点 374
14.4.1 微波器件的结构与工艺特点 374
14.4 微波器件的装配 374
14.4.2.2 典型微波器件的装配工艺要求 375
14.4.2.1 装配前的准备 375
14.4.1.2 微波器件的装配工艺特点 375
14.4.2 微波器件装配工艺要求及注意事项 375
14.4.2.3 微波器件装配注意事项 378
14.5.1 开关类器件的安装 379
14.5 电气部件的装配 379
14.5.2 大功率晶体管的安装 380
14.5.3 电连接器的安装 381
14.5.4 其他电子器件的安装 384
14.5.5 其他零组件的安装 385
15.1.1 灌封操作间的配置 386
15.1 电子组部件灌封的一般要求 386
第15章 电子组部件灌封 386
15.1.3 灌封模具 387
15.1.2 操作间污染的控制 387
15.1.4 灌封材料 388
15.1.6 灌封中的特殊问题 395
15.1.5 灌封质量保证条件 395
15.2.1.3 真空浇铸法 396
15.2.1.2 压力注射浇铸法 396
15.2 灌封方法和用料控制 396
15.2.1 灌封方法 396
15.2.1.1 静态浇铸法 396
15.2.1.4 真空压力浇铸法 397
15.2.2 灌封中用料量的缺陷和控制 398
15.3.2 电子组部件灌封操作步骤 399
15.3.1 电子组部件灌封流程 399
15.3 电子组部件灌封 399
15.5.3 工艺流程 405
15.5.2 流化设备简介 405
15.4 灌封产品的修整和返修 405
15.4.1 灌封产品的修整 405
15.4.2 灌封产品的返修 405
15.5 环氧粉末的硫化包封 405
15.5.1 简单的工艺过程 405
15.6.2 灌封质量标准 406
15.6.1 检验方法 406
15.5.4 流化包封工艺说明 406
15.6 灌封工序质量检验 406
16.1.1 外场可更换单元 407
16.1 概述 407
第16章 航空电子设备整机装配 407
16.1.2 航空电子设备安装架 408
16.2.1 LRU和安装架的定位基准体系 410
16.2 LRU与安装架的装配定位基准体系 410
16.3.1 前紧定装置的类型 411
16.3 LRU与安装架的前紧定装置 411
16.2.2 定位基准体系特点与基准顺序 411
16.2.2.1 定位基准体系特点 411
16.2.2.2 基准顺序的确定 411
16.4.2 后紧定装置的几种类型 413
16.4.1 导向件 413
16.3.2 前紧定装置装配注意事项 413
16.4 导向件、后紧定装置与电气接口 413
16.4.3.1 线缆连接接口 415
16.4.3 电气接口 415
16.4.3.2 微波接口 418
16.4.4.1 后紧定装置装配精度及误差因素 419
16.4.4 导向件、后紧定装置及电连接器装配 419
16.4.4.2 导向件和后紧定装置的装配方法 422
16.5.1 LRU底部通风 424
16.5 航空电子设备通风接口装配 424
16.4.4.3 电连接器的装配 424
16.5.2 LRU后部通风接口 425
16.6 LRU内部结构 426
16.5.3 橡胶密封环的安装 426
16.7.3 导轨装配工艺注意事项 428
16.7.2 印制板导轨的形式和锁紧 428
16.7 印制板在LRU内的装配 428
16.7.1 印制板在LRU内的装配方式 428
16.8.2 密封机箱装配工艺要点 429
16.8.1 LRU的密封方式 429
16.8 LRU的密封装配 429
16.9.1 对保险链缠绕的要求 430
16.9 保险链缠绕 430
16.8.3 密封试验 430
16.10.1.1 接地方式与接地点 431
16.10.1 航空电子设备的接地 431
16.9.2 螺栓、螺钉的保险链 431
16.10 航空电子设备接地、搭接和屏蔽结构 431
16.10.2 搭接工艺 433
16.10.1.2 航空电子系统的接地 433
16.10.3 屏蔽结构装配工艺 434
16.11 航空电子设备装配工艺要求 435
17.1.1 印制板的设计图纸 436
17.1 印制板生产的准备 436
第17章 印制板制造 436
17.1.2.2 多层板用的粘结片 437
17.1.2.1 覆箔板 437
17.1.2 印制板用的材料 437
17.1.2.3 阻焊剂 439
17.1.3 印制板制造环境要求 440
17.2.1 印制板制造工艺技术动向 441
17.2 印制板制造工艺 441
17.2.3.1 照相底图 442
17.2.3 照相底图、照相原版、照相底版 442
17.2.2 各类印制板制造工艺 442
17.2.3.2 照相原版和照相底版 444
17.2.4 图形印制 448
17.2.4.1 抗蚀干膜工艺 449
17.2.4.2 电沉积光敏抗蚀剂(ED)工艺 456
17.2.4.3 丝网漏印法 458
17.2.5 钻孔 469
17.2.6.1 孔金属化工艺 473
17.2.6 化学镀和电镀 473
17.2.6.2 电镀铜 477
17.2.6.3 电镀锡铅 480
17.2.6.4 电镀金 483
17.2.7.1 概述 484
17.2.7 蚀刻 484
17.2.6.5 电镀镍 484
17.2.7.2 酸性氯化铜蚀刻液 486
17.2.7.3 碱性氯化铜蚀刻液 488
17.2.7.4 硫酸——双氧水蚀刻液 491
17.3.1 多层板定位 493
17.3 多层板制造 493
17.3.2 内层板 495
17.3.3 层压前的准备 497
17.3.4 层压 499
17.3.5.2 去环氧沾污 505
17.3.5.1 钻孔 505
17.3.5 多层板的金属化孔 505
17.3.5.3 多层板的孔金属化 508
17.4.2.1 退除锡铅法 509
17.4.2 工艺方式说明 509
17.4 裸铜覆阻焊工艺(SMOBC) 509
17.4.1 SMOBC实施方式 509
17.4.3.1 阻焊干膜 510
17.4.3 阻焊涂层 510
17.4.2.2 退除金属抗蚀层法 510
17.4.2.3 掩蔽法 510
17.4.2.4 加成法 510
17.4.3.2 阻焊油墨 511
17.4.3.3 液态光致成像阻焊油墨 513
17.4.4 热风整平 516
17.5 印制板的计算机辅助设计、制造和测试 518
17.5.1 印制板的计算机辅助设计 518
17.5.1.1 设计输入 519
17.5.1.2 库和建库 519
17.5.1.3 自动/交互布局 519
17.5.1.4 自动/交互布线 519
17.5.1.5 设计规则检查 520
17.5.1.6 设计分析 520
17.5.1.7 设计输出 520
17.5.1.8 数据库 521
17.5.2 印制板的计算机辅助制造 521
17.5.3 印制板的计算机辅助测试 522
18.1 印制板检验 523
18.1.1 工序检验 523
第18章 检验与测试 523
18.1.2 质量合格检验 526
18.1.3 印制板成品合格与不合格准则 528
18.2.2 印制板组装件焊接质量检查 531
18.2.1 安装质量的检验 531
18.2.2.1 焊点术语 531
18.2 印制板组装件的检验 531
18.2.2.2 合格焊点准则 532
18.2.2.3 不合格焊点 533
18.2.2.4 焊接质量检验 536
18.3 组件和整机的环境应力筛选试验 537
18.3.1 环境应力筛选概念 537
18.2.2.5 焊接质量的判断 537
18.3.2 环境应力筛选的应用 539
18.3.2.1 受试产品的选择 539
18.3.2.2 应力量值的选择 540
18.3.3 环境应力筛选大纲的制订 540
18.3.4 环境应力筛选试验 541
A3 目前国内外常用的测试方法 542
A2 可焊性测试方法比较 542
A4 温度为235℃的焊槽测试方法 542
A1 焊点可焊性测试方法 542
附录A 可焊性测试 542
A5 温度为350℃的烙铁测试方法 543
A6 温度为235℃的焊球测试方法 544
A7 国内外常用测试设备 544
附录B 焊料纯度的维持 546
附录C 清洗设备简介 547
附录D 印制板用材料 549
参考文献 553
- 《市政工程基础》杨岚编著 2009
- 《工程静力学》王科盛主编 2019
- 《中国制造业绿色供应链发展研究报告》中国电子信息产业发展研究院 2019
- 《中央财政支持提升专业服务产业发展能力项目水利工程专业课程建设成果 设施农业工程技术》赵英编 2018
- 《Maya 2018完全实战技术手册》来阳编著 2019
- 《化学反应工程》许志美主编 2019
- 《绿色过程工程与清洁生产技术 张懿院士论文集精选 上》《绿色过程工程与清洁生产技术》编写组编 2019
- 《软件工程》齐治昌,谭庆平,宁洪编著 2019
- 《高等教育双机械基础课程系列教材 高等学校教材 机械设计课程设计手册 第5版》吴宗泽,罗圣国,高志,李威 2018
- 《化学工程与工艺专业实验指导》郭跃萍主编 2019
- 《莼江曲谱 2 中国昆曲博物馆藏稀见昆剧手抄曲谱汇编之一》郭腊梅主编;孙伊婷副主编;孙文明,孙伊婷编委;中国昆曲博物馆编 2018
- 《指向核心素养 北京十一学校名师教学设计 英语 七年级 上 配人教版》周志英总主编 2019
- 《植物百科彩色图鉴 第2卷》植物百科彩色图鉴编委会主编 2012
- 《远去的老调》经典文库编委会编 2019
- 《北京生态环境保护》《北京环境保护丛书》编委会编著 2018
- 《莼江曲谱 1 中国昆曲博物馆藏稀见昆剧手抄曲谱汇编之一》郭腊梅主编;孙伊婷副主编;孙文明,孙伊婷编委;中国昆曲博物馆编 2018
- 《共和国日记 1964》《共和国日记》编委会编 2019
- 《中国地方艺文荟萃 华北东北卷 第1辑 3》《中国地方艺文荟萃》编委会编 2018
- 《绿色过程工程与清洁生产技术 张懿院士论文集精选 上》《绿色过程工程与清洁生产技术》编写组编 2019
- 《中国地方艺文荟萃 华北东北卷 第1辑 1》《中国地方艺文荟萃》编委会编 2018
- 《指向核心素养 北京十一学校名师教学设计 英语 七年级 上 配人教版》周志英总主编 2019
- 《北京生态环境保护》《北京环境保护丛书》编委会编著 2018
- 《指向核心素养 北京十一学校名师教学设计 英语 九年级 上 配人教版》周志英总主编 2019
- 《高等院校旅游专业系列教材 旅游企业岗位培训系列教材 新编北京导游英语》杨昆,鄢莉,谭明华 2019
- 《中国十大出版家》王震,贺越明著 1991
- 《近代民营出版机构的英语函授教育 以“商务、中华、开明”函授学校为个案 1915年-1946年版》丁伟 2017
- 《新工业时代 世界级工业家张毓强和他的“新石头记”》秦朔 2019
- 《智能制造高技能人才培养规划丛书 ABB工业机器人虚拟仿真教程》(中国)工控帮教研组 2019
- 《陶瓷工业节能减排技术丛书 陶瓷工业节能减排与污染综合治理》罗民华著 2017
- 《全国职业院校工业机器人技术专业规划教材 工业机器人现场编程》(中国)项万明 2019