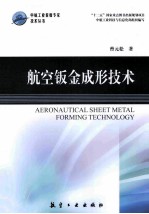
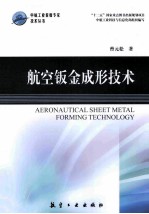
航空钣金成形技术PDF电子书下载
- 电子书积分:17 积分如何计算积分?
- 作 者:曾元松著
- 出 版 社:北京:航空工业出版社
- 出版年份:2014
- ISBN:9787516503706
- 页数:573 页
第1章 概述 1
1.1 航空钣金成形技术的种类 1
1.2 航空钣金成形技术特点 2
1.2.1 板材成形技术特点 3
1.2.2 管材成形技术特点 5
1.2.3 型材成形技术特点 6
1.3 航空钣金成形变形方式 7
1.4 航空钣金成形技术的地位和作用 7
1.4.1 板材在航空领域的地位与作用 11
1.4.2 管材在航空领域的地位与作用 13
1.4.3 型材在航空领域的地位与作用 14
1.5 航空钣金成形技术的现状与发展趋势 15
1.5.1 世界航空钣金成形技术的现状与发展趋势 15
1.5.2 我国在航空钣金成形技术领域与先进水平间的差距 19
第2章 超塑成形/扩散连接技术 22
2.1 超塑成形/扩散连接技术的原理与特点 22
2.1.1 材料的超塑性 22
2.1.2 超塑性分类 22
2.1.3 超塑性变形机理 23
2.1.4 超塑性能的影响因素 24
2.1.5 超塑性材料 26
2.1.6 材料扩散连接 26
2.1.7 扩散连接接头形成机制 28
2.1.8 扩散连接接头质量的主要影响因素 29
2.1.9 超塑成形/扩散连接组合工艺 30
2.1.10 超塑成形/扩散连接组合工艺典型结构形式 31
2.1.11 超塑成形/扩散连接构件的结构特点 32
2.2 超塑成形/扩散连接技术研究应用进展 32
2.2.1 国外研究应用进展 32
2.2.2 国内研究应用进展 35
2.3 钛合金超塑成形/扩散连接技术 37
2.3.1 单层结构超塑成形技术 38
2.3.2 钛合金多层结构超塑成形/扩散连接技术 41
2.4 超塑成形/扩散连接结构主要缺陷形式及质量控制 54
2.5 SPF/DB设备与模具 56
2.5.1 SPF/DB设备组成和分类 56
2.5.2 SPF/DB设备的关键技术要求 58
2.5.3 SPF/DB模具 59
2.6 技术发展展望 62
第3章 喷丸成形技术 64
3.1 喷丸成形原理与特点 64
3.1.1 喷丸成形原理及工艺参数 64
3.1.2 喷丸成形种类 65
3.1.3 喷丸成形特点 67
3.2 壁板零件的种类及其喷丸成形方法 68
3.2.1 壁板零件的种类 68
3.2.2 典型壁板零件的喷丸成形方法 69
3.3 喷丸成形技术研究应用进展 73
3.3.1 国外研究应用进展 73
3.3.2 国内研究应用进展 74
3.4 壁板零件喷丸工艺数字化几何分析技术 75
3.4.1 壁板外形曲面类型区域分析及展向折弯线 75
3.4.2 弦向喷丸路径及其规划方法 76
3.4.3 特征点选取及相关数据提取 79
3.5 喷丸成形过程数值模拟技术 81
3.5.1 喷丸模拟方法 81
3.5.2 弹丸撞击过程模拟及残余应力分析 82
3.5.3 等效热载荷模拟及宏观变形预测 93
3.6 壁板喷丸成形工艺参数的确定 101
3.6.1 喷丸成形工艺参数对喷丸变形的影响规律 101
3.6.2 弦向喷丸成形工艺参数的确定 103
3.6.3 展向喷丸成形工艺参数的确定 107
3.7 壁板零件喷丸强化及变形校正 110
3.7.1 喷丸强化基本概念 110
3.7.2 壁板零件的喷丸强化技术 111
3.7.3 壁板零件喷丸强化变形校正技术 112
3.8 喷丸工艺对材料表面质量和力学性能的影响 114
3.8.1 喷丸工艺对材料表面质量的影响 114
3.8.2 喷丸工艺对材料力学性能的影响 118
3.9 喷丸成形设备及工装 124
3.9.1 喷丸成形设备 124
3.9.2 喷丸成形工装 126
3.10 喷丸成形技术的工程应用 130
3.10.1 ARJ21飞机机翼壁板喷丸成形 130
3.10.2 带筋整体壁板喷丸成形 134
3.11 技术发展展望及新型喷丸加工方法 137
3.11.1 激光喷丸技术 137
3.11.2 不同尺寸弹丸双面喷丸成形技术 139
3.11.3 超声喷丸技术 139
3.11.4 高压水喷丸技术 140
第4章 蠕变时效成形技术 142
4.1 原理与特点 142
4.1.1 蠕变时效成形原理 142
4.1.2 蠕变时效成形宏观力学变形和微观组织演变机制 142
4.1.3 蠕变时效成形工艺特点及工艺参数 144
4.2 蠕变时效成形技术研究应用进展 144
4.2.1 研究应用进展 144
4.2.2 应用现状 150
4.3 蠕变时效成形材料组织和性能控制 151
4.3.1 室温力学性能 151
4.3.2 断裂韧性 152
4.3.3 疲劳裂纹扩展速率 154
4.3.4 高周疲劳性能 156
4.3.5 应力腐蚀性能 158
4.3.6 微观组织 158
4.4 蠕变时效成形材料变形规律 161
4.4.1 时效成形温度对回弹的影响规律 161
4.4.2 时效成形时间对回弹的影响规律 162
4.4.3 预弯曲率半径对回弹的影响规律 164
4.4.4 板材厚度对回弹的影响规律 164
4.4.5 主要工艺参数与回弹量之间的关系 165
4.5 蠕变时效成形有限元数值模拟 167
4.5.1 蠕变时效成形本构方程的建立 167
4.5.2 双凸外形零件时效成形有限元模拟 175
4.5.3 马鞍外形零件时效成形有限元模拟 178
4.5.4 扭转外形零件时效成形有限元模拟 180
4.5.5 微观组织结构的有限元模拟 183
4.6 蠕变时效成形模具型面优化技术 186
4.6.1 基于零件回弹补偿的模具型面修正方法 186
4.6.2 基于实际零件回弹量的模具型面优化方法 194
4.7 蠕变时效成形设备与模具 201
4.7.1 蠕变时效成形设备 201
4.7.2 时效成形工装模具 202
4.8 工程应用 206
4.8.1 典型壁板零件蠕变时效成形工艺流程 206
4.8.2 C919飞机机翼上壁板模拟件 207
4.8.3 机身带筋整体壁板模拟件 216
4.9 技术发展展望 220
第5章 旋压成形技术 221
5.1 原理、分类和特点 221
5.1.1 旋压成形原理 221
5.1.2 旋压成形技术分类 221
5.1.3 旋压成形技术特点 227
5.2 技术研究应用进展 231
5.2.1 旋压技术在国内外的发展现状 231
5.2.2 旋压技术应用研究进展 233
5.3 铝合金强力旋压成形技术 236
5.3.1 尖锥形曲面外形构件旋压成形 236
5.3.2 大长径比小曲率曲面外形构件旋压成形 238
5.3.3 曲面外形带环形内筋构件旋压成形 242
5.3.4 变壁厚曲面外形构件旋压成形 245
5.3.5 筒形与锥形组合型面旋压成形 247
5.4 难变形材料热旋压成形技术 249
5.4.1 钛合金旋压成形技术 249
5.4.2 高温合金旋压成形技术 252
5.4.3 金属间化合物旋压成形技术 256
5.5 铌金属旋压成形技术 257
5.5.1 铌超导腔半腔零件旋压成形 257
5.5.2 铌材料筒形零件旋压成形 263
5.5.3 旋压及热处理对铌材料组织性能的影响 265
5.6 旋压产品主要缺陷形式及质量控制 268
5.6.1 旋压产品主要缺陷形式及消除措施 268
5.6.2 金相组织及性能控制 269
5.6.3 外形尺寸精度控制 269
5.7 旋压设备及工装模具 271
5.7.1 旋压设备技术要求和分类 271
5.7.2 旋压设备的组成 273
5.7.3 典型旋压设备 275
5.7.4 旋压成形芯模 277
5.7.5 旋轮 277
5.8 旋压成形技术发展展望 279
第6章 柔性多点模具蒙皮拉形技术 280
6.1 原理与特点 280
6.1.1 蒙皮类零件及其成形方法 280
6.1.2 柔性多点模具蒙皮拉形原理及特点 281
6.2 技术研究应用进展 283
6.2.1 国外研究应用进展 283
6.2.2 国内研究应用现状 284
6.3 柔性多点模具结构及型面控制 285
6.3.1 柔性多点模具结构及模具型面调整驱动方式 285
6.3.2 一拖多驱动方式柔性多点模具结构 286
6.3.3 一拖多驱动方式柔性多点模具型面控制 288
6.4 柔性多点模具蒙皮拉形型面有限元优化技术 290
6.4.1 柔性多点模具蒙皮拉形模型的选择 290
6.4.2 柔性多点模具包络面简化模型可行性的验证 292
6.4.3 基于回弹补偿的模具型面优化方法 296
6.5 柔性多点模具蒙皮拉形工艺技术 298
6.5.1 单曲率零件柔性多点模具蒙皮拉形 300
6.5.2 双凸零件柔性多点模具蒙皮拉形 300
6.5.3 拉形零件外形检测及数据处理 301
6.6 主要缺陷形式及质量控制 305
6.6.1 主要缺陷形式 305
6.6.2 表面质量影响因素分析及试验方案设计 306
6.6.3 表面质量试验结果分析 308
6.7 工程应用 312
6.7.1 工艺准备 313
6.7.2 柔性多点模具蒙皮拉形 315
6.7.3 蒙皮零件数字化切割和测量 315
6.8 技术发展展望 318
第7章 板材柔性介质压力辅助成形技术 319
7.1 引言 319
7.2 工艺分类及特点 319
7.2.1 柔性介质压力辅助成形工艺分类 319
7.2.2 柔性介质压力辅助成形类工艺特点 319
7.3 技术研究应用进展 320
7.3.1 柔性介质压力辅助成形技术发展历程 320
7.3.2 板材充液成形技术研究现状 321
7.4 板材充液成形技术 325
7.4.1 充液成形基本原理及常用工艺方法 325
7.4.2 充液拉深成形基本力学模型 328
7.4.3 液体压力对充液成形的影响 338
7.4.4 板材液压胀形关键问题 342
7.4.5 液体加载曲线的处理 346
7.4.6 筒形件充液拉深成形主要工艺参数 347
7.4.7 板材充液成形设备与模具 351
7.4.8 典型工程应用实例 357
7.5 技术发展展望 368
7.5.1 脉动液压成形技术 368
7.5.2 热油介质成形技术 368
第8章 钛合金板材热成形技术 370
8.1 原理与特点 370
8.1.1 钛合金板材热成形技术原理 370
8.1.2 钛合金板材加热的方法 370
8.1.3 钛合金板材热成形技术特点 372
8.2 钛合金板材热成形技术研究应用进展 372
8.3 钛合金板材热成形的成形极限图 374
8.3.1 钛合金热态成形极限试验网格印制方法 374
8.3.2 钛合金热态成形极限试验 376
8.3.3 应用实例 378
8.4 钛合金板材热成形工艺过程、方法与主要工艺参数 381
8.4.1 钛合金板材热成形工艺过程 381
8.4.2 钛合金板材热成形主要工艺参数 384
8.4.3 钛合金板材典型热成形工艺方法 385
8.5 主要缺陷形式及质量控制 392
8.5.1 主要成形缺陷 392
8.5.2 显微组织及性能控制 393
8.5.3 外形尺寸精度控制 394
8.6 钛合金板材热成形设备与模具 397
8.6.1 热成形设备 397
8.6.2 热成形模具 399
8.7 钛合金热成形/焊接组合工艺 401
8.7.1 零件主要外形和结构特点 401
8.7.2 工艺方案的制定 402
8.7.3 分瓣压弯成形工艺及质量控制 403
8.7.4 整体组焊工艺及质量控制 404
8.7.5 整体热胀形工艺及质量控制 405
第9章 型材拉弯成形技术 407
9.1 原理与特点 407
9.1.1 拉弯成形基本原理 407
9.1.2 型材拉弯成形工艺特点 407
9.1.3 型材拉弯工艺分类 407
9.1.4 拉弯成形加载方式 409
9.2 技术研究应用进展 410
9.2.1 拉弯成形塑性理论研究 410
9.2.2 拉弯成形试验研究 411
9.2.3 拉弯成形数值模拟技术 412
9.2.4 专用型材拉弯应用系统开发 412
9.3 型材拉弯变形理论解析 413
9.3.1 拉弯过程应力应变分析 413
9.3.2 回弹计算 416
9.4 型材拉弯主要工艺参数 417
9.5 拉弯成形工艺 418
9.5.1 一次拉弯工艺 418
9.5.2 二次拉弯工艺 418
9.5.3 数控拉弯过程及参数设定 418
9.6 热拉弯成形工艺 420
9.6.1 加热规范 421
9.6.2 热拉弯拉伸量 422
9.6.3 热拉弯润滑剂 422
9.7 型材拉弯过程数值模拟 422
9.7.1 拉弯成形数值模拟主要流程 423
9.7.2 型材拉弯数值模拟主要技术内容 423
9.7.3 典型实例分析 426
9.8 拉弯成形主要缺陷及质量控制 428
9.9 拉弯设备及模具 430
9.9.1 拉弯机 430
9.9.2 拉弯模具 433
9.10 工程应用 436
9.10.1 铝合金球面框零件拉弯成形 436
9.10.2 新型铝锂合金型材拉弯成形 441
9.11 技术发展展望 444
第10章 管材成形与连接技术 445
10.1 原理与特点 445
10.1.1 管材弯曲成形技术原理与特点 445
10.1.2 异形截面管材胀形技术原理与特点 448
10.1.3 管端成形与连接技术原理与特点 450
10.2 技术研究应用进展 452
10.2.1 国外研究应用进展 452
10.2.2 国内研究应用现状 454
10.3 大直径薄壁管件弯曲成形技术 456
10.3.1 大直径薄壁管定义及成形难点分析 456
10.3.2 大直径薄壁管绕弯成形过程数值模拟 456
10.3.3 典型大直径薄壁管绕弯成形工艺 462
10.3.4 主要缺陷形式及质量控制 463
10.4 小弯曲半径管件推弯成形技术 463
10.4.1 小弯曲半径管的定义及应用 463
10.4.2 小弯曲半径管推弯过程数值模拟 464
10.4.3 典型小弯曲半径管推弯成形工艺 470
10.4.4 主要缺陷形式及质量控制 472
10.5 复杂截面管件弯/胀成形技术 473
10.5.1 复杂截面管件及其应用 473
10.5.2 管材弯/胀成形过程数值模拟 473
10.5.3 典型复杂截面管弯/胀成形工艺 474
10.5.4 主要缺陷形式及质量控制 475
10.6 钛合金无扩口内径滚压连接技术 476
10.6.1 钛合金无扩口内径滚压连接管件结构及其应用 476
10.6.2 钛合金无扩口内径滚压连接过程数值模拟 477
10.6.3 管材无扩口内径滚压连接密封性能分析与测试方法 480
10.6.4 典型钛合金无扩口内径滚压连接工艺 482
10.6.5 主要缺陷形式及质量控制 488
10.7 典型设备及工装模具 489
10.7.1 推弯成形设备及工装模具 489
10.7.2 无扩口内径滚压连接设备及工装模具 489
第11章 精密化学铣切成形技术 492
11.1 化学铣切成形原理与特点 492
11.1.1 化学铣切成形原理 492
11.1.2 化学铣切加工特点 492
11.1.3 化学铣切加工方法的分类 493
11.2 技术研究应用进展 494
11.3 典型化学铣切零件结构与工艺特点 496
11.3.1 典型化学铣切零件结构特点 496
11.3.2 典型工艺过程 500
11.3.3 典型工艺选择与控制 500
11.4 铝(锂)合金化学铣切成形技术 507
11.4.1 化学铣切前零件验收 507
11.4.2 清洁处理 508
11.4.3 涂覆保护涂料 508
11.4.4 刻形 509
11.4.5 腐蚀加工 510
11.4.6 除胶 519
11.4.7 检验 519
11.5 钛合金化学铣切成形技术 526
11.5.1 前处理 527
11.5.2 涂覆保护涂料 529
11.5.3 腐蚀加工 529
11.5.4 检验 533
11.6 化学铣切对材料组织性能的影响 535
11.6.1 晶间腐蚀 535
11.6.2 表面粗糙度 537
11.6.3 力学性能 541
11.6.4 吸氢 548
11.7 化学铣切设备和仪器 552
11.7.1 清洁处理线 552
11.7.2 化学铣切生产线 553
11.7.3 涂胶设备 554
11.7.4 刻形设备与样板 554
11.7.5 废物处理设备 555
11.7.6 测量仪器 555
11.8 工程应用实例 555
11.9 技术发展展望 556
参考文献 558
- 《钒产业技术及应用》高峰,彭清静,华骏主编 2019
- 《现代水泥技术发展与应用论文集》天津水泥工业设计研究院有限公司编 2019
- 《异质性条件下技术创新最优市场结构研究 以中国高技术产业为例》千慧雄 2019
- 《Prometheus技术秘笈》百里燊 2019
- 《中央财政支持提升专业服务产业发展能力项目水利工程专业课程建设成果 设施农业工程技术》赵英编 2018
- 《药剂学实验操作技术》刘芳,高森主编 2019
- 《林下养蜂技术》罗文华,黄勇,刘佳霖主编 2017
- 《脱硝运行技术1000问》朱国宇编 2019
- 《催化剂制备过程技术》韩勇责任编辑;(中国)张继光 2019
- 《信息系统安全技术管理策略 信息安全经济学视角》赵柳榕著 2020
- 《催眠人生》于松著 2019
- 《暗杀者的后代》陈应松著 2019
- 《逐梦岁月》覃世松著 2019
- 《纸上风景》徐明松著 2015
- 《搜寻梦的精灵》曾元孝 2017
- 《像法学家那样思考=THINKING LIKE A LAWYER》刘昌松著 2020
- 《晚霞涛声》周汝松著 2019
- 《阳光小旅馆》刘松著 2018
- 《叶片结构强度与振动》徐自力,艾松著 2018
- 《助力脱贫攻坚 校园携手田园》陈治松著 2019
- 《指向核心素养 北京十一学校名师教学设计 英语 七年级 上 配人教版》周志英总主编 2019
- 《北京生态环境保护》《北京环境保护丛书》编委会编著 2018
- 《指向核心素养 北京十一学校名师教学设计 英语 九年级 上 配人教版》周志英总主编 2019
- 《高等院校旅游专业系列教材 旅游企业岗位培训系列教材 新编北京导游英语》杨昆,鄢莉,谭明华 2019
- 《中国十大出版家》王震,贺越明著 1991
- 《近代民营出版机构的英语函授教育 以“商务、中华、开明”函授学校为个案 1915年-1946年版》丁伟 2017
- 《新工业时代 世界级工业家张毓强和他的“新石头记”》秦朔 2019
- 《智能制造高技能人才培养规划丛书 ABB工业机器人虚拟仿真教程》(中国)工控帮教研组 2019
- 《陶瓷工业节能减排技术丛书 陶瓷工业节能减排与污染综合治理》罗民华著 2017
- 《全国职业院校工业机器人技术专业规划教材 工业机器人现场编程》(中国)项万明 2019