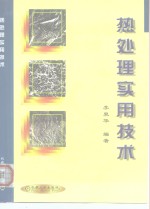
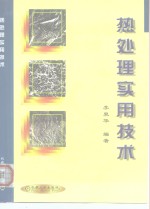
热处理实用技术PDF电子书下载
- 电子书积分:10 积分如何计算积分?
- 作 者:李泉华编著
- 出 版 社:北京:机械工业出版社
- 出版年份:2000
- ISBN:7111076990
- 页数:219 页
第1章 热处理工艺技术 1
1.1 钢的退火工艺 1
1.1.1 完全退火 1
1.1.2 不完全退火 1
前言 1
1.1.3 去应力退火 2
1.1.4 操作注意事项 3
1.2 钢的正火工艺 3
1.2.1 目的及应用 3
1.3 钢的淬火工艺 4
1.3.1 钢的淬火 4
1.2.2 工艺规范 4
1.2.3 操作要点 4
1.3.2 淬火工件的工艺流程 5
1.3.3 淬火前的准备 5
1.3.4 装炉 5
1.3.5 加热 5
1.3.6 冷却方法及冷却剂的选择 8
1.3.10 45钢淬裂及其对策 9
1.3.9 调质件淬火工序 9
1.3.8 淬火状态硬度 9
1.3.7 操作注意事项 9
1.4 钢的回火工艺 11
1.4.1 回火的定义 11
1.4.2 回火的准备工作 11
1.4.3 回火的分类 11
1.4.4 回火温度的确定 11
1.5.2 开炉前的准备 13
1.5.1 气体渗碳的目的 13
1.5 气体渗碳工艺 13
1.4.7 操作注意事项 13
1.4.6 冷却 13
1.4.5 回火保温时间的确定 13
1.5.3渗碳操作 14
1.6 固体渗碳工艺 16
1.6.1 固体渗碳特点 16
1.6.2 开炉前的准备工作 16
1.7.2 设备及开炉前的准备 17
1.7.1 气体碳氮共渗 17
1.7 气体碳氮共渗工艺 17
1.6.5 质量检验 17
1.6.3工艺规范 17
1.6.4 操作程序 17
1.7.3碳氮共渗操作 18
1.7.4 新的工艺配方 18
1.8 气体氮碳共渗工艺 19
1.8.1 气体氮碳共渗 19
1.8.2 设备 19
1.8.3 准备工作 19
1.8.4 工艺过程 19
1.9 气体渗氮工艺 20
1.9.1 气体渗氮 20
1.9.2渗氮工件的工艺流程 20
1.9.3 渗氮前的准备工作 20
1.9.4 渗氮工艺及操作 21
1.10.1 离子渗氮 22
1.10.2 材料的选用 22
1.10.3 准备工作 22
1.10 离子渗氮工艺 22
1.9.5 渗氮过程中遇到下列情况的处理方法 22
1.10.4 装炉 23
1.10.5 开炉 23
1.10.6 质量检验 23
1.11 一般工件盐炉淬火工艺 24
1.11.1 工艺流程 24
1.11.2淬火加热 24
1.11.3 淬火冷却 24
1.12 高速钢刀具淬火工艺 25
1.11.5 回火 25
1.11.4淬火操作 25
1.12.1 材料 26
1.12.2 技术要求 26
1.12.3 工艺流程 26
1.12.4 下艺操作 26
1.12.5 高速钢采用一次回火新工艺 28
1.12.6 若干类型工件淬火变形规定 28
1.12.7 盐浴炉的管理 29
1.12.8 刀具导向及柄部淬火工艺 30
1.12.9 高速钢刀具深冷处理工艺 31
1.13.1 退火工艺 32
1.13 模具预先热处理工艺 32
1.13.2 模具钢的调质热处理 34
1.14 热作模具热处理工艺 34
1.14.1 锻模热处理工艺 34
1.14.2 热作模具的真空热处理 37
1.14.4 压铸模热处理工艺 41
1.14.5 切边模具热处理工艺 41
1.14.6 小型锻模热处理工艺 42
1.14.7 3Cr2W8V钢模具化学热处理工艺 42
1.14.8 双金属电渣熔铸模块热处理工艺 44
1.14.9 45Cr2NiMoVSi、5Cr2NiMoVSi高强韧性大截面热锻模具热处理工艺 45
1.14.10 4Cr3Mo2VNiNb(HD)700℃高温热作模具钢热处理工艺 45
1.14.11 RM2系中碳中合金高热强度热作模具钢热处理工艺 45
1.14.12 HMl钢新型热作模具钢热处理工艺 46
1.14.13 3CrM03VNb(HM3)新型超高强韧性模具钢热处理工艺 46
1.15.1 总则 47
1.15.2 碳素工具钢模具的热处理工艺 47
1.15 冷作模具热处理工艺 47
1.15.3 合金钢模具热处理工艺 49
1.15.4 65Cr4W3M02VNb(65Nb)含铌基体钢热处理工艺 51
1.15.5 6CrMnNiMoVSi(GD)高强韧性低合金冷作模具钢热处理工艺 51
1.15.6 GM新型耐磨冷作模具钢热处理工艺 51
1.16 铜及铜合金退火工艺 53
1.16.1 目的及应用 53
1.16.2 准备工作 53
1.16.3 退火规范 53
1.16.4质量检验 53
1.16.5 电冰箱、空调管、T2管及TUP镜面铜管热处理工艺 53
1.17 铍青铜热处理工艺 54
1.17.1 总则 54
1.17.2 准备工作 54
1.17.3 工艺规范 55
1.17.4 质量检验 55
1.18.2 工艺程序 56
1.18.3 准备工作 56
1.18.4 发蓝操作 56
1.18.1 目的 56
1.18 发蓝工艺 56
1.18.7 碱性发蓝的改进工艺 57
1.18.6 发蓝质量控制 57
1.18.5 操作注意事项 57
1.14.3 5CrMnMo钢热锻模的强韧化处理和复合渗处理工艺 58
1.18.8 BFH钢铁低温高效快速发黑工艺 58
1.18.9 无污染的发蓝工艺 59
1.18.10 JH-160、JH-350型钢铁发黑工艺 59
1.18.11 钢铁常温发黑工艺 59
1.18.12 石墨流态粒子炉发蓝、淬火复合工艺 60
1.18.13 气体氧氮化代替发蓝、磷化工艺 60
1.19 火焰淬火工艺 60
1.19.3 准备工作 61
1.19.4 淬火 61
1.19.1 目的及特点 61
1.19.2 材料 61
1.19.5 回火 62
1.20 清洗、喷砂和喷丸、防锈工艺 62
1.20.1 目的 62
1.20.2清洗、脱脂 62
1.26 缸体激光淬火生产线工艺 62
1.20.3喷砂、喷丸 63
1.21.3 校直操作 64
1.21.2 准备工作 64
1.22 铸铁件热处理工艺 65
1.21.5 操作中的安全注意事项 65
1.22.1 铸铁热处理特点 65
1.22.2 铸铁热处理分类及目的 65
1.22.3 灰铸铁件去应力退火 65
1.20.6 注意事项 65
1.21.4 校直质量要求 65
1.21.1 总则 65
1.21 校直工艺 65
1.20.5 质量要求 65
1.20.4 防锈 65
1.22.4 球墨铸铁高温石墨化退火工艺 66
1.22.5 球墨铸铁低温石墨化退火工艺 66
1.22.6 球墨铸铁去应力退火工艺 68
1.22.7 铸铁件淬火、回火 68
1.22.8 铸铁件正火 69
1.22.9 球墨铸铁曲轴传统的正火工艺 69
1.22.10 稀土镁铜钼合金球墨铸铁曲轴零保温正火工艺 70
1.22.11 稀土镁铜钼合金球墨铸铁曲轴双重正火工艺 70
1.22.12 稀土镁球墨铸铁曲轴破碎状铁素体二段正火工艺 70
1.22.15 稀土镁球墨铸铁曲轴的铸造余热正火工艺 71
1.22.14 金属型铸造稀土镁球墨铸铁曲轴的两段高温正火工艺 71
1.22.13 稀土镁球墨铸铁曲轴中-高温二段快速正火工艺 71
1.23.1 目的 72
1.23.2准备工作 72
1.22.16 稀土镁球墨铸铁曲轴一段快速正火工艺 72
1.22.17 稀土镁球墨铸铁曲轴零保温正火、不回火工艺 72
1.23 变形铝合金热处理工艺 72
1.23.3 工艺规范 73
1.23.4操作要点 74
1.23.5 质量检验 75
1.24 铸造(ZL104)铝合金热处理工艺 75
1.24.1 准备工作 75
1.24.2 淬火规范 75
1.24.3 时效规范 75
1.24.6 ZL104铸造铝合金热处理工艺 76
1.24.4检查制度 76
1.24.5 返修制度 76
1.25 感应加热热处理工艺 77
1.25.1 保证感应加热热处理质量的必要条件 77
1.25.2 感应加热热处理工艺的制订 80
1.26.3 淬火前的准备 82
1.26.1 激光淬火 82
1.26.2 缸体淬火的工艺流程 82
1.25.3 感应加热热处理常见质量问题及产生原因 82
1.25.4 感应加热热处理零件的质量返修 82
1.27 钢铁磷化工艺 83
1.27.1 磷化处理工艺过程 83
1.27.2常温磷化工艺 84
1.27.3 中温磷化工艺 84
1.26.7 注意事项 85
1.26.6 淬火参数 85
1.26.5 淬火方式 85
1.26.4 装夹 85
1.27.4 高温磷化工艺 85
1.27.5 磷化溶液的配制和调整 85
1.27.6 磷化后处理 86
1.27.7 磷化膜质量检验 86
1.27.8 磷化时常见的缺陷、产生原因及排除方法 87
1.28 钢件渗铝工艺 88
1.28.1 钢件热浸渗铝工艺 88
1.28.2 钢件粉末渗铝工艺 89
1.29.2 碱洗脱脂 90
1.29.1 工艺流程 90
1.28.3 膏剂法铝硅共渗工艺 90
1.29 热浸镀锌工艺 90
1.28.4 铝、铬、硅三元共渗工艺 90
1.29.3 酸洗 91
1.29.4 助镀处理 91
1.29.5 热浸镀锌 91
1.29.6 冷却和钝化处理 91
1.29.7 质量检验 91
1.30 化学沉积镍磷合金表面强化工艺 92
1.30.1 工艺过程 92
1.30.2 化学镀液成分 92
1.30.3 化学沉积镍磷合金层的一般性能 93
1.30.4 镍磷合金层结构和热处理后的组织 93
1.30.5 化学沉积镍磷合金层的应用 94
1.31 渗硼及多元硼共渗工艺 94
1.31.1 固体渗硼工艺 94
1.31.2 膏剂渗硼工艺 95
1.31.5 硼氮共渗工艺 96
1.31.3 盐浴渗硼工艺 96
1.31.4 气体渗硼工艺 97
1.31.6 硼铝共渗工艺 98
1.31.7 硼硅共渗工艺 98
1.31.8 硼铬共渗工艺 98
1.31.9 硼钛共渗工艺 98
1.31.10 硼锆共渗工艺 98
1.31.11 硼钒共渗工艺 98
1.31.12 镍硼共渗工艺 99
1.31.13 复合镀铁及镀铁后渗硼处理工艺 99
1.31.17 硼铜共渗工艺 100
1.31.19 渗硼什的质量检验 100
1.31.18 硼磷共渗工艺 100
1.31.14 碳硼复合渗工艺 100
1.31.16 硼钨共渗工艺 100
1.31.15 碳、氮、氧、硫、硼多元共渗工艺 100
1.32.1 固体渗铬工艺 101
1.32.2 膏剂离子渗铬工艺 101
1.32.3 盐浴渗铬工艺 101
1.33 钢件渗钒工艺 102
1.32.5 铬硅共渗工艺 102
1.32.4 铬钒共渗工艺 102
1.34 碳化钛(或TiN)涂覆工艺 103
1.34.1 固体包装法沉积TiC工艺 103
1.34.2 氯基熔盐涂覆TiC工艺 103
1.34.3 电泳法涂覆TiC工艺 103
1.34.4 化学气相沉积(CVD)Ti(C、N)工艺 104
1.34.5 物理气相沉积(PVD)Ti(C、N)工艺 104
1.34.6 等离子化学气相沉积(PECVD)工艺 104
1.35 渗硫及多元硫共渗工艺 105
1.35.1 固体渗硫工艺 105
1.35.2 液体渗硫工艺 105
1.35.3 电解渗硫工艺 106
1.35.4 离子渗硫工艺 106
1.35.8 离子硫氮碳共渗工艺 107
1.35.5 气体硫氮共渗工艺 107
1.35.6 液体硫氮共渗工艺 107
1.35.7 离子硫氮共渗工艺 107
1.35.9 气体氧硫氮共渗工艺 108
2.1 箱式电炉操作技术 109
1.32 钢件渗铬工艺 109
第2章 热处理设备操作技术 109
2.2 井式回火电炉操作技术 111
2.3 盐浴炉操作技术 112
2.4 硅碳棒箱式电炉操作技术 113
2.5 高温井式电炉操作技术 113
2.6 深井式电炉操作技术 114
2.7 井式气体渗碳电炉操作技术 114
2.8 加氧气体氮碳共渗炉操作技术 116
2.9 震底式煤气加热炉操作技术 118
2.10 电加热震底炉操作技术 120
2.11 推杆式煤气炉操作技术 121
2.12 离子渗氮装置操作技术 123
2.13 火焰淬火装置操作技术 124
2.14 LD51型推杆炉操作技术 125
2.15 KEMP公司PSN-1型制氮装置操作技术 127
2.16 AbarZPsen周期炉生产线的操作技术 131
2.17 VSE立式真空淬火炉设备的操作技术 137
2.18 BPS型中频机组操作技术 139
2.19 曲轴旋转淬火机床操作技术 142
2.20 GP型高频感应加热装置操作技术 145
2.21 缸体激光淬火生产线操作技术 147
2.22 磷化生产线操作技术 148
2.23 硝盐炉操作技术 150
2.24 硝盐槽操作技术 150
2.25 回火用盐浴坩埚电炉操作技术 151
2.26 煤气烘干炉操作技术 152
2.27 盐浴含氯钡废渣的处理技术 152
2.28 锻模燕尾回火操作技术 153
2.29 15-HERT-24128-17AS链板式连续热处理生产线操作技术 153
2.30 54m3/h凡制氮系统操作技术 159
2.31 高速钢校直操作技术 161
2.32 镗杆热点校直操作技术 163
2.33 氧—乙炔气热点校直操作技术 163
2.34 电阻炉温度管理技术 163
2.35 UDS碳势控制仪操作技术 165
2.36 链板炉温度控制仪操作技术 166
2.37 326B型氧分析仪操作技术 167
2.38 54m3氮气发生器氧分析仪操作技术 168
2.39 电加热连续式气体渗碳炉生产线操作技术 169
2.40 60m3/h电加热吸热式气体发生炉操作技术 171
2.41 Q3110型抛丸清理滚筒操作技术 174
2.42 喷砂机操作技术 176
第3章 热处理质量检验技术 177
3.1 热处理质量检验总则 177
3.2 退火、正火及调质件质量检验 178
3.3 淬火件质量检验 179
3.4 渗碳件质量检验 181
3.5 碳氮共渗件质量检验 183
3.6 气体渗氮件质量检验 185
3.7 氮碳共渗件质量检验 186
3.8 冷作模具热处理质量检验 187
3.9 热作模具热处理质量检验 188
3.10 高速工具钢金相检验 189
3.11 感应加热热处理件质量检验 202
3.12 火焰淬火件质量检验 208
3.13 铸造铝合金铝锭及铸件针孔度检验 210
3.14 铸造Al-Si系合金变质处理显微组织检验 211
3.15 ZL10系铸造铝合金过烧检验 212
3.16 45钢连杆热加工质量检验 214
参考文献 219
- 《钒产业技术及应用》高峰,彭清静,华骏主编 2019
- 《现代水泥技术发展与应用论文集》天津水泥工业设计研究院有限公司编 2019
- 《异质性条件下技术创新最优市场结构研究 以中国高技术产业为例》千慧雄 2019
- 《Prometheus技术秘笈》百里燊 2019
- 《中央财政支持提升专业服务产业发展能力项目水利工程专业课程建设成果 设施农业工程技术》赵英编 2018
- 《药剂学实验操作技术》刘芳,高森主编 2019
- 《林下养蜂技术》罗文华,黄勇,刘佳霖主编 2017
- 《脱硝运行技术1000问》朱国宇编 2019
- 《催化剂制备过程技术》韩勇责任编辑;(中国)张继光 2019
- 《信息系统安全技术管理策略 信息安全经济学视角》赵柳榕著 2020
- 《市政工程基础》杨岚编著 2009
- 《家畜百宝 猪、牛、羊、鸡的综合利用》山西省商业厅组织技术处编著 1959
- 《《道德经》200句》崇贤书院编著 2018
- 《高级英语阅读与听说教程》刘秀梅编著 2019
- 《计算机网络与通信基础》谢雨飞,田启川编著 2019
- 《看图自学吉他弹唱教程》陈飞编著 2019
- 《法语词汇认知联想记忆法》刘莲编著 2020
- 《培智学校义务教育实验教科书教师教学用书 生活适应 二年级 上》人民教育出版社,课程教材研究所,特殊教育课程教材研究中心编著 2019
- 《国家社科基金项目申报规范 技巧与案例 第3版 2020》文传浩,夏宇编著 2019
- 《流体力学》张扬军,彭杰,诸葛伟林编著 2019
- 《指向核心素养 北京十一学校名师教学设计 英语 七年级 上 配人教版》周志英总主编 2019
- 《北京生态环境保护》《北京环境保护丛书》编委会编著 2018
- 《高等教育双机械基础课程系列教材 高等学校教材 机械设计课程设计手册 第5版》吴宗泽,罗圣国,高志,李威 2018
- 《指向核心素养 北京十一学校名师教学设计 英语 九年级 上 配人教版》周志英总主编 2019
- 《高等院校旅游专业系列教材 旅游企业岗位培训系列教材 新编北京导游英语》杨昆,鄢莉,谭明华 2019
- 《中国十大出版家》王震,贺越明著 1991
- 《近代民营出版机构的英语函授教育 以“商务、中华、开明”函授学校为个案 1915年-1946年版》丁伟 2017
- 《新工业时代 世界级工业家张毓强和他的“新石头记”》秦朔 2019
- 《智能制造高技能人才培养规划丛书 ABB工业机器人虚拟仿真教程》(中国)工控帮教研组 2019
- 《AutoCAD机械设计实例精解 2019中文版》北京兆迪科技有限公司编著 2019