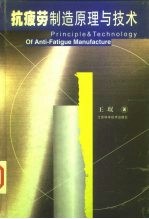
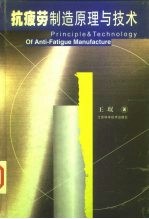
抗疲劳制造原理与技术PDF电子书下载
- 电子书积分:17 积分如何计算积分?
- 作 者:王珉著
- 出 版 社:南京:江苏科学技术出版社
- 出版年份:1999
- ISBN:7534527694
- 页数:585 页
目录 1
前言 1
第一章 绪论 1
第一节 疲劳基本定义 2
第二节 疲劳研究的发展简史 3
第三节 疲劳研究发展现状 9
第四节 抗疲劳制造方法简介 13
第二章 金属表面理论与位错 15
第一节 金属的界面与表面 15
一、金属的界面 15
二、金属的表面 16
三、表面粗糙度 17
四、微凸体的接触 19
五、塑性接触和形变硬化的影响 22
第二节 金属表面组织结构 23
一、金属的表面形貌 23
二、机械加工后的金属表面组织 25
三、金属表面晶体结构 26
第三节 位错的基本性质 30
一、位错的定义与柏氏矢量 30
二、位错的基本形式 32
三、位错强化机制 38
第三章 疲劳相关理论 41
第一节 线弹性断裂力学 41
一、断裂的宏观表现方式 42
二、应力强度因子K 43
三、K控制的条件 46
四、断裂韧性 48
五、线弹性断裂力学在非完全弹性体中应 52
力的推广 58
第二节 金属的疲劳破坏机理 58
一、疲劳裂纹萌生 59
二、疲劳裂纹扩展 62
三、最后断裂 66
四、疲劳断口的特征 66
一、线性累积损伤理论 72
第三节 疲劳的累积损伤理论 72
二、修正线性损伤理论 73
三、其他理论 74
第四节 疲劳裂纹扩展理论及寿命预测 74
一、疲劳裂纹扩展理论 74
二、疲劳裂纹扩展寿命预测 76
第五节 抗疲劳设计方法 79
一、无限寿命设计法 79
二、名义应力有限寿命设计法 79
三、局部应力应变分析法 80
四、损伤容限设计法 82
五、疲劳可靠性设计 84
一、塑性变形体模型及屈服准则 87
第一节 有限元分析理论基础及应用 87
第四章 抗疲劳的研究分析方法 87
二、加载条件与加载曲面 90
三、弹塑性本构关系及其矩阵表达式 93
四、有限元分析过程 97
五、小弹塑性有限元基本解法 102
六、残余应力的计算 104
七、工程应用实例——冷挤压孔的有限元 104
分析 108
第二节 上限元理论及其应用 108
一、上限元法(UBET)的理论基础 110
二、上限元法在分析内螺纹挤压成形中的 110
三、计算实例 118
应用 118
第三节 疲劳试验 121
一、疲劳试验与设备的分类 122
二、疲劳特征试验分类 123
三、疲劳试验数据分析和处理 137
第四节 测试分析方法 140
一、光塑性力学分析 140
二、云纹法 160
三、X射线应力测试方法 166
四、电子显微分析 170
第五章 抗疲劳制造原理 176
第一节 各因素对疲劳性能的影响 176
一、材料静强度的影响 177
二、显微组织的影响 179
三、热处理组织的影响 183
四、表面状况的影响 186
五、应力集中的影响 187
六、尺寸效应的影响 189
七、表层残余应力的影响 190
八、腐蚀环境的影响 197
九、载荷频率的影响 200
第二节 提高零部件疲劳性能的途径 201
一、减少应力集中 201
二、提高零件的表面强度 205
三、配合连接过程中提高疲劳寿命的途径 208
第一节 概述 209
第六章 螺纹滚压和挤压技术 209
第二节 螺纹滚压 210
一、螺纹滚压成形过程及其特点 211
二、螺纹滚压加工方法 215
三、螺纹滚压参数的选择 220
四、螺纹滚压工具 227
五、滚压螺纹质量分析 229
第三节 内螺纹挤压成形概述 230
一、内螺纹挤压成形的优缺点 230
二、内螺纹挤压成形的研究现状 232
三、内螺纹冷挤压成形的理论基础 233
一、内螺纹冷挤压成形机理 234
第四节 内螺纹冷挤压成形与增寿机理 234
二、挤压螺纹表层组织结构的变化与作用 240
三、螺纹表面显微硬度与疲劳性能 241
四、采用不同挤压工艺时螺纹的残余应力 245
五、表面粗糙度的影响 251
第五节 高强度钢内螺纹冷挤压成形的 252
试验研究 252
一、技术关键与技术路线 252
二、挤压丝锥的设计 254
三、工件对内螺纹冷挤压成形的影响 259
四、挤压速度对内螺纹冷挤压的影响 265
五、冷却润滑液对内螺纹冷挤压的影响 267
六、挤压螺纹的质量分析 271
七、大直径内螺纹的冷挤压成形试验 278
八、挤压丝锥的损伤机理 281
第六节 疲劳对比试验 288
一、试验条件 288
二、试验结果与讨论 289
三、疲劳断口分析 291
四、改善螺纹零件疲劳性能的途径 294
第七章 孔的带开缝衬套冷挤压技术 296
第一节 概述 296
一、孔的抗疲劳强化技术 297
二、孔的冷挤压技术的研究现状 303
一、工艺系统的基本硬件组成 308
第二节 孔的带开缝衬套冷挤压工艺 308
二、带开缝衬套冷挤压工艺过程 316
三、带开缝衬套冷挤压工艺参数 317
四、带开缝衬套冷挤压工艺质量控制 322
第三节 孔壁受力分析及疲劳寿命预测 324
一、孔壁受力及残余应力分析 324
二、弹塑性应力场分析 327
三、工程寿命预测模型的建立 335
第四节 带开缝衬套冷挤压孔的微观分 339
析 340
一、试验条件及分析方法 340
二、强化层微观结构分析 343
三、位错强化机理分析 354
第五节 疲劳对比试验及断口宏、微观 356
分析 357
一、试验条件 357
二、试验结果与分析 359
三、疲劳断口分析及裂纹扩展特征 363
第六节 材料对挤压强化效果的影响 369
一、冷挤压强化中常用工件材料 369
二、材料对冷挤压强化的敏感性 370
第八章 喷丸强化技术 375
第一节 概述 375
第二节 喷丸强化机理 378
一、喷丸表层的弹塑性变形和残余压应力 378
二、喷丸后表层的组织结构变化 387
三、喷丸对表面粗糙度的影响 393
第三节 喷丸设备及弹丸 394
一、气动式喷丸机 395
二、机械离心式喷丸机 399
三、内孔喷丸机 401
四、手提式气动喷丸机 401
五、旋片(板)喷丸器 402
六、零件运转机构 404
七、喷丸设备的选择原则 405
八、弹丸 406
一、喷丸强化工艺参数 408
第四节 喷丸强化工艺及质量控制 408
二、喷丸强化工艺质量的控制和检验 411
第五节 喷丸强化工艺对疲劳强度的影 415
响 416
一、钢制零件喷丸强化的效果 416
二、铝合金的喷丸强化效果 420
三、钛合金的喷丸强化效果 421
四、高温合金的喷丸强化效果 424
五、飞机结构材料的喷丸强化效果 425
第九章 高能束抗疲劳制造技术 429
第一节 概述 429
第二节 激光相变硬化 435
一、激光相变硬化的参数控制 435
二、各种材料抗疲劳性能的改善 444
第三节 激光冲击强化 458
一、激光冲击过程分析 458
二、激光冲击区表面质量对疲劳寿命的 467
影响 477
三、激光冲击强化效果的直观检验与控制 477
四、激光冲击抗疲劳断裂优化试验 484
五、激光冲击改善材料抗疲劳性能的机理 495
分析 513
第四节 激光表面合金化 513
一、试验方法 513
二、试验结果分析 514
第五节 爆炸冲击 518
第六节 离子注入表面处理 523
一、离子注入的特点 523
二、离子注入改善材料抗疲劳性能的机理 524
三、离子注入抗疲劳试验结果及分析 528
第十章 工程应用实例 537
第一节 螺纹挤压强化工艺应用实例 537
第二节 带开缝衬套冷挤压工艺应用 538
实例 538
一、飞机制造中的应用实例 538
二、飞机维修中的应用实例 547
第三节 喷丸强化工艺应用实例 550
参考文献 560
- 《钒产业技术及应用》高峰,彭清静,华骏主编 2019
- 《现代水泥技术发展与应用论文集》天津水泥工业设计研究院有限公司编 2019
- 《异质性条件下技术创新最优市场结构研究 以中国高技术产业为例》千慧雄 2019
- 《Prometheus技术秘笈》百里燊 2019
- 《中国制造业绿色供应链发展研究报告》中国电子信息产业发展研究院 2019
- 《中央财政支持提升专业服务产业发展能力项目水利工程专业课程建设成果 设施农业工程技术》赵英编 2018
- 《药剂学实验操作技术》刘芳,高森主编 2019
- 《林下养蜂技术》罗文华,黄勇,刘佳霖主编 2017
- 《脱硝运行技术1000问》朱国宇编 2019
- 《催化剂制备过程技术》韩勇责任编辑;(中国)张继光 2019
- 《浙江特色经济文化研究报告 筱簜之乡 浙江竹文化概说》沈珉著 2012
- 《美国本土音乐印象》王珉著 2013
- 《南湖文化名人 蒲华》马雪腾主编;沈珉著 2012
- 《浙江特色经济文化研究报告 天之美禄 浙江黄酒文化研究》沈珉著 2012
- 《曾国藩成功的秘密》张晓珉著 2013
- 《大家学标准日本语 完全图像日语学习书》(韩)坂野治,(韩)朴世利,(韩)金志珉著;李浩译 2013
- 《浙江特色经济文化研究报告 芸香楮影 浙江书籍文化研究》沈珉著 2012
- 《中小投资者法律保护与权益资本成本 基于中国上市公司的实证研究》肖珉著 2009
- 《形势与政策教程》陈红儿,王珉,何增光主编 2009
- 《素描 造型·创意·表现》王珉主编 2009
- 《钒产业技术及应用》高峰,彭清静,华骏主编 2019
- 《现代水泥技术发展与应用论文集》天津水泥工业设计研究院有限公司编 2019
- 《异质性条件下技术创新最优市场结构研究 以中国高技术产业为例》千慧雄 2019
- 《Prometheus技术秘笈》百里燊 2019
- 《中央财政支持提升专业服务产业发展能力项目水利工程专业课程建设成果 设施农业工程技术》赵英编 2018
- 《药剂学实验操作技术》刘芳,高森主编 2019
- 《林下养蜂技术》罗文华,黄勇,刘佳霖主编 2017
- 《脱硝运行技术1000问》朱国宇编 2019
- 《催化剂制备过程技术》韩勇责任编辑;(中国)张继光 2019
- 《信息系统安全技术管理策略 信息安全经济学视角》赵柳榕著 2020