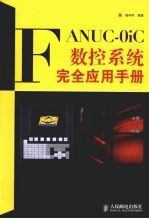
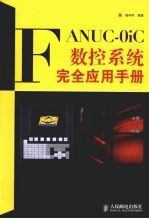
FANUC-0iC数控系统完全应用手册PDF电子书下载
- 电子书积分:23 积分如何计算积分?
- 作 者:龚仲华编著
- 出 版 社:北京:人民邮电出版社
- 出版年份:2009
- ISBN:9787115192868
- 页数:895 页
第1章 绪论 1
1.1 数控系统及其组成 1
1.1.1 数控技术的基本概念 1
1.1.2 数控系统及其组成 3
1.2 CNC的工作原理与特点 5
1.2.1 数控机床的工作过程 5
1.2.2 插补原理 6
1.2.3 CNC控制的特点 6
1.3 伺服驱动系统的分类 7
1.3.1 开环、半闭环、闭环驱动 7
1.3.2 模拟伺服与数字伺服驱动 9
1.4 常用的CNC产品 11
1.4.1 FANUC公司产品简介 11
1.4.2 其他CNC产品简介 13
第1篇 系统选型篇 14
第2章 FS-OiC的组成与硬件 14
2.1 FS-OiC概述 14
2.1.1 产品型号与系列 14
2.1.2 FS-与FS-OiMate 16
2.1.3 FS-OiC的组成与原理 16
2.2 CNC单元及主要附件 19
2.2.1 CNC单元与附件规格 19
2.2.2 CNC与MDI/LCD单元 20
2.2.3 标准机床操作面板 20
2.3 I/O-Link从站设备 24
2.3.1 I/O-Link从站的分类与规格 24
2.3.2 操作面板I/O单元 27
2.3.3 机床I/O连接单元 31
2.3.4 分布式I/O单元 32
2.3.5 βi系列伺服驱动 35
2.4 FSSB从站设备 36
2.4.1 FSSB从站设备 36
2.4.2 FSSB从站的配置原则 37
第3章 FS-OiC的功能与软件 39
3.1 坐标轴控制功能 39
3.1.1 机床坐标系与参考点 39
3.1.2 坐标轴控制与插补功能 41
3.1.3 轴撤销与位置跟随功能 45
3.1.4 位置误差补偿功能 46
3.2 轴安全保护功能 47
3.2.1 运动保护功能 48
3.2.2 禁区保护功能 49
3.3 进给控制功能 51
3.3.1 进给速度控制功能 51
3.3.2 加减速控制功能 52
3.4 主轴控制功能 55
3.4.1 主轴的控制方式与功能 55
3.4.2 主轴转速控制功能 57
3.4.3 主轴位置控制功能 59
3.4.4 多主轴控制功能 60
3.5 辅助功能 61
第4章 伺服与主轴驱动 64
4.1 αi系列伺服驱动器 64
4.1.1 电源模块 65
4.1.2 伺服驱动模块 65
4.1.3 主轴驱动模块 67
4.1.4 驱动器附件 69
4.2 βi系列伺服驱动器 69
4.2.1 结构与型号 69
4.2.2 产品规格 71
4.2.3 驱动器附件 72
4.3 伺服电机 72
4.3.1 αis/αHVis系列伺服电机 73
4.3.2 α/αHVi系列伺服电机 75
3.3.3 βis系列伺服电机 76
4.3.4 伺服电机的安装尺寸 77
4.4 主轴电机 80
4.4.1 αi系列主轴电机的分类 80
4.4.2 标准αi系列主轴电机 81
4.4.3 αiP系列大范围恒功率输出主轴电机 82
4.4.4 αiT主轴直连型电机 84
4.4.5 αiL强制冷却主轴直连型电机 85
4.4.6 βi系列主轴电机 85
4.4.7 主轴89电机的安装尺寸 85
第2篇 编程篇 89
第5章 FS-OiC编程基础 89
5.1 编程的基本概念 89
5.1.1 编程的基本要求与方法 89
5.1.2 程序的组成 90
5.1.3 程序段的组成与结构 92
5.1.4 子程序编程 93
5.2 坐标系的建立与选择指令 95
5.2.1 机床坐标系的建立与选择 96
5.2.2 工件坐标系的建立与选择 97
5.3 位置、速度的单位选择与编程 100
5.3.1 位置单位的选择与指定方式 101
5.3.2 速度单位的选择与指定方式 102
5.4 基本移动指令的编程 103
5.4.1 快速定位、直线插补与暂停 103
5.4.2 圆弧插补与加工平面选择 106
5.5 加工准备指令的编程 110
5.5.1 行程保护与参数的输入 110
5.5.2 刀具补偿与工件坐标系原点的输入 111
5.5.3 刀具长度测量与位置偏置 112
第6章 FS-OiTC的编程 114
6.1 FS-OiTC代码体系与编程特点 114
6.1.1 FS-OiTC代码体系 114
6.1.2 FS-OiTC的编程特点 116
6.2 FS-OiTC的特殊编程 117
6.2.1 FS-OiTC的特殊编程方式 117
6.2.2 FS-OiTC的专用编程指令 118
6.3 普通车削加工固定循环 123
6.3.1 简单固定循环 123
6.3.2 复合型车削固定循环 126
6.3.3 其他车削循环 131
6.4 车削中心固定循环 133
6.4.1 固定循环的基本说明 133
6.4.2 钻孔循环G83.G87 136
6.4.3 攻丝与镗孔循环G84/G88、G85/G89 138
6.5 自动倒角与蓝图编程 139
6.5.1 自动倒角 139
6.5.2 蓝图编程 140
6.6 刀具偏置与刀尖半径补偿 143
6.6.1 刀具偏置 144
6.6.2 刀尖半径补偿 146
6.7 数控车床程序的基本格式 148
6.7.1 程序的基本格式 148
6.7.2 车削加工编程实例 150
第7章 FS-OiMC的编程 153
7.1 FS-OiMC代码体系与编程特点 153
7.1.1 FS-OiMC的编程特点 153
7.1.2 FS-OiMC的G代码体系 154
7.2 FS-OiMC的特殊编程 157
7.2.1 基本移动指令 157
7.2.2 切削速度自动控制指令 158
7.2.3 坐标变换指令 159
7.2.4 自动倒角 166
7.3 FS-OiMC的通用固定循环 167
7.3.1 孔加工固定循环概述 167
7.3.2 循环动作说明 171
7.3.3 固定循环的编程实例 177
7.4 FS-OiMC的特殊固定循环 178
7.4.1 G83小孔排屑钻孔循环 178
7.4.2 G74、G84刚性攻丝 181
7.5 FS-OiMC的刀具补偿 183
7.5.1 刀具长度偏置 183
7.5.2 刀具半径补偿 186
7.6 FS-OiMC的程序格式 189
第8章 用户宏程序编程 191
8.1 宏程序变量 191
8.1.1 变量的基本概念 191
8.1.2 变量的分类 192
8.1.3 系统变量 193
8.2 用户宏程序指令 198
8.2.1 算术与逻辑运算指令 198
8.2.2 转移与循环指令 199
8.2.3 外部数据输出指令 201
8.3 宏程序调用、返回与变量赋值 203
8.3.1 宏程序调用与返回 203
8.3.2 自变量传送赋值 204
8.3.3 宏程序编程实例 206
8.4 宏程序执行与中断 207
8.4.1 宏程序的执行 207
8.4.2 宏程序中断 209
第9章 对话编程与Oi引导编程 213
9.1 FS-OiC的对话编程 213
9.1.1 对话编程与引导编程 213
9.1.2 对话编程的程序输入 214
9.1.3 对话编程的程序编辑 215
9.2 Oi引导编程的基本操作 216
9.2.1 常规指令的引导编程 216
9.2.2 加工循环的引导编程 219
9.3 OiTC引导循环 220
9.3.1 孔加工循环 221
9.3.2 内外圆与端面车削循环. 222
9.3.3 槽加工循环 223
9.3.4 螺纹加工循环 225
9.4 OiMC引导循环 225
9.4.1 孔群加工循环 226
9.4.2 平面铣削加工循环 229
9.4.3 型腔/槽铣削加工循环 230
9.5 OiC的轮廓编程 232
9.5.1 轮廓编程的基本操作 232
9.5.2 轮廓参数的定义 235
9.5.3 相邻两图形的轮廓计算 236
9.5.4 相邻三图形的轮廓计算 238
9.6 OiC的辅助计算功能 240
9.6.1 辅助计算的内容与操作 240
9.6.2 坐标点的辅助计算 242
9.6.3 直线与圆弧的辅助计算. 243
第3篇 硬件设计篇 246
第10章 CNC控制系统总体设计 246
10.1 设计原则与步骤 246
10.1.1 系统设计原则 246
10.1.2 系统的设计步骤与内容 247
10.2 CNC的选择 251
10.2.1 CNC的型号与规格的确定 251
10.2.2 CNC功能的确定 252
10.3 主轴系统的设计 257
10.3.1 电机基本参数的确定 257
10.3.2 电机功率的选择 258
10.3.3 加减时间的计算 261
10.4 伺服进给系统设计 263
10.4.1 伺服电机的基本选择 263
10.4.2 进给系统的稳态设计 264
10.4.3 伺服进给系统的动态设计 269
10.5 采用S形加减速的进给系统设计 272
10.5.1 进给系统加减速特性分析 272
10.5.2 S形加减速的基本设计原则 276
10.5.3 S形加减速的主要参数确定 278
10.6 进给系统驱动器的选择 282
10.6.1 驱动器的基本要求与电流计算 282
10.6.2 不同原则下的加减速电流计算 284
10.6.3 驱动器选择实例 285
第11章 电路图设计的基本准则 288
11.1 主回路与控制回路设计准则 288
11.1.1 电路图设计概述 288
11.1.2 主回路设计准则 289
11.1.3 控制回路设计准则 290
11.2 安全电路设计准则 291
11.2.1 安全电路设计准则 291
11.2.2 安全电路设计 293
11.3 I/O接口电路设计 295
11.3.1 输入连接的一般原则 295
11.3.2 开关量输出连接 302
11.4 CNC控制系统电路设计实例 304
11.4.1 主回路设计 305
11.4.2 电源回路设计 305
11.4.3 安全电路设计 307
第12章 FS-OiC控制电路设计 310
12.1 FS-OiC的综合连接 310
12.2 FS-OiC系统主回路设计 313
12.2.1 主回路的基本要求 313
12.2.2 FS-OiC主回路设计实例 315
12.3 CNC接口电路设计 317
12.3.1 CNC的基本连接 317
12.3.2 RS-232C的连接 320
12.4 I/O-Link从站接口的设计 323
12.4.1 OiC-I/O单元 323
12.4.2 主操作面板I/O单元 326
12.4.3 小型操作面板I/O单元 332
12.4.4 矩阵扫描输入操作面板I/O单元 333
12.4.5 通用I/O连接单元 335
12.4.6 源/汇点输入I/O单元 337
12.4.7 分布式I/O单元的连接 338
第13章 驱动器控制电路设计 342
13.1 αi系列伺服驱动器 342
13.1.1 伺服驱动的综合连接 342
13.1.2 驱动器主回路设计 342
13.1.3 电源模块的控制 345
13.1.4 伺服驱动模块的控制 345
13.2 αi系列主轴驱动器 347
13.2.1 主轴驱动的综合连接 347
13.2.2 主轴电机的连接 350
13.2.3 外置式位置检测元件的连接 351
13.2.4 与外部操作显示装置的连接 353
13.3 βi系列单轴伺服驱动器 354
13.3.1 伺服驱动的综合连接 354
13.3.2 驱动器主回路设计 356
13.3.3 驱动单元的连接 357
13.4 βi系列多轴驱动器 358
13.4.1 伺服驱动的综合连接 358
13.4.2 驱动器主回路设计 360
13.4.3 驱动器的连接 361
13.5 βi系列I/O-Link驱动器 362
13.5.1 伺服驱动的综合连接 362
13.5.2 伺服驱动的设计要点 364
第14章 安装与连接设计 367
14.1 电气安装设计 367
14.1.1 CNC的基本安装要求 367
14.1.2 元器件的布置要求 368
14.2 散热设计 371
14.2.1 发热量的计算 371
14.2.2 散热能力计算 373
14.2.3 热交换器与空调的选择 374
14.3 电气连接设计 376
14.3.1 连接的基本要求 376
14.3.2 干扰及其预防 377
14.3.3 接地系统设计 378
14.4 安装与连接图设计 380
第4篇 PMC设计篇 382
第15章 PMC设计基础 382
15.1 PMC的结构与原理 382
15.1.1 PMC基本结构 382
15.1.2 PMC的工作原理 385
15.1.3 PMC的工作过程 386
15.1.4 PMC的工作特点 388
15.2 PMC编程语言与程序结构 389
15.2.1 PMC的编程语言 389
15.2.2 PMC程序的基本结构 391
15.3 SA1/SB7的性能与特点 393
15.3.1 SA1/SB7的基本性能 393
15.3.2 SA1/SB7的程序特点 395
15.4 确定控制要求与选择I/O单元 396
15.4.1 PMC控制要求的确定 396
15.4.2 FS-OiC的I/O单元选择 399
15.5 PMC-I/O地址的设定与实例 400
15.5.1 PMC-I/O地址的设定 400
15.5.2 PMC的地址设定实例 402
第16章 PMC指令与编程(一) 405
16.1 PMC-SA1/SB7基本指令的编程 405
16.1.1 SA1/SB7的地址格式与范围 405
16.1.2 基本逻辑运算符号与特点 407
16.1.3 逻辑梯形图编程要点 408
16.1.4 典型梯形图程序 412
16.2 PMC-SA1/SB7功能指令概述 414
16.2.1 功能指令的编程格式 414
16.2.2 数据的存储格式 415
16.2.3 功能指令的分类 416
16.3 定时与计数指令 418
16.3.1 定时指令 418
16.3.2 计数指令 420
16.3.3 回转控制指令 421
16.4 数据比较、译码、转换与传送 423
16.4.1 数据比较指令 423
16.4.2 数据译码指令 425
16.4.3 数据转换指令 426
16.4.4 数据传送指令 428
16.5 逻辑运算扩展与算术运算指令 429
16.5.1 边沿检测指令 429
16.5.2 字节、字、双字逻辑操作指令 429
16.5.3 算术运算指令 431
16.6 PMC程序编制实例 433
16.6.1 自动换刀控制程序设计 433
16.6.2 波段开关倍率控制程序设计 435
16.6.3 倍率调节键控制程序设计 439
第17章 PMC指令与编程(二) 442
17.1 程序控制指令 442
17.1.1 程序结束指令 442
17.1.2 公共线控制指令 443
17.1.3 跳转控制指令 445
17.1.4 子程序控制指令 448
17.2 数据表操作指令 450
17.2.1 数据表的基本概念 450
17.2.2 数据检索 451
17.2.3 数据表的变址传送 453
17.3 文本显示与MMC数据读写指令 454
17.3.1 文本显示的指令 454
17.3.2 外部文本输入与显示指令 455
17.3.3 MMC数据读写指令 457
17.4 CNC状态信息的读入 458
17.4.1 CNC与PMC的数据交换 458
17.4.2 CNC状态信息的读入 462
17.4.3 加工程序执行信息的读入 464
17.5 CNC数据的读入与写出 468
17.5.1 CNC偏置值的读写 468
17.5.2 机床参数与设定数据的读写 469
17.5.3 用户宏程序变量的读写 470
17.5.4 I/O-Link输入/输出程序号的写出 471
17.6 驱动参数读写指令 471
17.6.1 伺服驱动参数的读入/写出 471
17.6.2 串行主轴参数的读入 473
17.7 刀具寿命管理数据读写指令 474
17.7.1 刀具寿命管理数据的读入 474
17.7.2 刀具寿命管理数据的写出 476
17.8 PMC轴控制 478
17.8.1 PMC轴控制的基本概念 478
17.8.2 PMC轴控制指令 479
17.8.3 PMC轴控制信号 480
第18章 PMC操作 482
18.1 PMC编辑器功能概述 483
18.1.1 PMC编程器与编辑功能 483
18.1.2 PMC编程器的基本操作 483
18.2 PMC程序参数的显示与设定 485
18.2.1 控制继电器的设定 485
18.2.2 数据表的设定 489
18.2.3 定时器与计数器的设定 491
18.3 梯形图程序的输入 492
18.3.1 程序编辑的选择与标题栏输入 492
18.3.2 独立编程元件的输入 494
18.3.3 功能指令的输入 496
18.4 梯形图程序的编辑 497
18.4.1 编程元件、行的插入 497
18.4.2 编程元件与程序段的删除 499
18.4.3 编程元件的搜索 500
18.4.4 程序块的复制与移动 501
18.4.5 地址的一次性更改 501
18.5 符号地址与文本信息的编辑 502
18.5.1 符号地址与直接输入 502
18.5.2 符号表及其编辑 504
18.5.3 文本信息及其编辑 505
18.6 PMC存储器清除与交叉表显示 506
18.6.1 PMC存储器的清除与压缩 506
18.6.2 交叉表显示 507
18.7 I/O接口、系统参数与在线监控的设定 508
18.7.1 I/O接口设定 508
18.7.2 系统参数的设定 510
18.7.3 在线监控的设定页面 511
18.8 PMC诊断功能 512
18.8.1 PMC的启动/停止与状态显示 512
18.8.2 信号跟踪 514
18.8.3 动态梯形图显示 515
18.8.4 动态梯形图瞬时采样功能 516
18.8.5 动态梯形图分割显示功能 518
第5篇 功能调试篇 519
第19章 功能调试基础 519
19.1 调试前的准备 519
19.1.1 资料与工具 519
19.1.2 基本状况检查 520
19.2 FS-OiC的连接检查 521
19.2.1 CNC连接检查 521
19.2.2 驱动器连接检查 522
19.2.3 伺服电机的连接检查 524
19.3 强电回路调试 525
19.4 CNC功能调试基础 527
19.4.1 功能调试的基本步骤 527
19.4.2 信号与参数的基本说明 528
19.4.3 CNC参数总述 531
19.4.4 参数的MDI输入与I/O接口输入 532
19.5 引导系统操作 534
19.5.1 引导系统的功能 534
19.5.2 系统数据的装载、校验与删除 535
19.5.3 系统数据的保存、备份 537
19.5.4 存储器卡的文件删除与格式化 538
第20章 伺服与主轴系统的配置 540
20.1 FSSB从站配置 540
20.1.1 CNC基本功能参数的设定与检查 540
20.1.2 FSSB从站配置 542
20.1.3 FSSB设定的引导操作 546
20.2 位置控制系统的建立与设定 549
20.2.1 闭环位置控制系统的基本概念 549
20.2.2 CNC指令与机床测量系统的匹配 550
20.2.3 半闭环系统参数计算与设定实例 552
20.3 伺服设定的引导操作 553
20.3.1 伺服设定引导页面 553
20.3.2 伺服设定参数说明与引导操作 554
20.3.3 伺服电机代码表 555
20.4 位置全闭环系统的建立与设定 557
20.4.1 位置全闭环系统的基本结构 557
20.4.2 位置全闭环系统的建立与设定 559
20.4.3 全闭环系统参数计算与设定实例 562
20.4.4 绝对式光栅全闭环系统的设定 564
20.5 主轴驱动系统的配置 566
20.5.1 主轴的功能配置与选择 566
20.5.2 串行主轴的引导操作 569
20.6 串行主轴驱动的结构配置 571
20.6.1 主轴系统的结构形式 571
20.6.2 串行主轴的配置参数 574
20.6.3 串行主轴的配置实例 576
第21章 基本坐标轴调试 578
21.1 坐标轴运行方式与条件 578
21.1.1 坐标轴调试与准备 578
21.1.2 坐标轴的特殊运行方式 579
21.1.3 坐标轴运动的基本条件与状态检查 581
21.2 坐标轴的手动功能调试 583
21.2.1 手动操作的控制信号与参数 583
21.2.2 手动操作的动作与要求 585
21.3 手动回参考点的调试 587
21.3.1 手动回参考点的方式与要求 587
21.3.2 利用编码器零脉冲建立参考点 591
21.3.3 碰撞式回参考点 593
21.3.4 绝对式编码器(或光栅)回参考点 595
21.4 轴安全保护功能的建立与调试 596
21.4.1 运动保护功能及其设定 596
21.4.2 禁区保护功能及其设定 597
21.4.3 与安全保护功能相关的信号与参数 598
21.5 坐标轴特殊选择功能的调试 600
21.5.1 位置开关功能 600
21.5.2 倾斜轴控制功能 602
21.5.3 坐标轴回退功能 603
21.6 坐标轴的误差补偿 604
21.6.1 反向间隙补偿与螺距误差补偿 604
21.6.2 螺距误差补偿实例 606
第22章 自动运行 608
22.1 自动运行的启动与停止 608
22.1.1 自动运行的内容与条件 608
22.1.2 自动运行的启动与停止 610
22.1.3 自动运行的控制信号、参数与状态清除 611
22.2 程序运行控制 613
22.2.1 程序运行控制的方式 613
22.2.2 程序运行控制信号 615
22.2.3 程序运行控制参数 615
22.3 插补功能 616
22.3.1 运动轨迹、位置控制与功能设定 616
22.3.2 运动速度控制参数 619
22.3.3 加减速控制参数 622
22.3.4 插补控制信号 623
22.4 程序与编程功能 624
22.4.1 程序输入/输出与编辑功能 625
22.4.2 程序格式的定义参数 626
22.4.3 坐标系设定参数 630
22.4.4 刀具补偿、测量与寿命管理参数 630
22.4.5 固定循环控制参数 634
22.4.6 用户宏程序控制参数 636
22.4.7 程序输入/输出信号 638
22.5 操作与显示功能 639
22.5.1 操作与显示参数 639
22.5.2 数据输入/输出控制参数 646
22.5.3 操作与显示信号 649
22.6 辅助功能控制 650
22.6.1 辅助功能的特点与处理 650
22.6.2 辅助功能控制参数与信号 652
22.7 外部数据输入与程序号检索 654
22.7.1 外部数据输入 654
22.7.2 程序号检索 656
第23章 主轴调试(一) 659
23.1 主轴功能调试概述 659
23.1.1 模拟主轴与串行主轴的特点 659
23.1.2 速度控制与位置控制功能 660
23.1.3 主轴其他控制功能 661
23.2 主轴转速控制功能 662
23.2.1 转速控制功能说明 662
23.2.2 CNC转速控制参数 663
23.2.3 转速控制信号与旋转条件 665
23.3 主轴传动级交换控制 666
23.3.1 传动级交换的基本形式 666
23.3.2 T型换挡功能说明 667
23.3.3 M型换挡功能说明 668
23.4 主轴转速控制的其他功能 671
23.4.1 主轴转速模拟量的调整 671
23.4.2 线速度恒定控制 672
23.4.3 外部主轴定向准停与换挡转速输出 673
23.4.4 主轴速度波动检测与实际转速输出 675
23.5 串行主轴速度控制 676
23.5.1 功能特点与控制参数 676
23.5.2 串行主轴速度控制信号 677
23.6 FS-OiTC的定向与定位控制 679
23.6.1 功能特点、控制参数与控制信号 679
23.6.2 定向与定位功能的使用条件 682
23.6.3 定向与定位的动作过程 684
23.7 串行主轴的定向与定位 686
23.7.1 功能特点与参数设定 686
23.7.2 控制信号与动作过程 688
第24章 主轴调试(二) 692
24.1 Cs轴控制功能 692
24.1.1 Cs轴控制的基本说明 692
24.1.2 Cs轴的设定与方式转换 696
24.1.3 Cs轴的基本操作 696
24.2 刚性攻丝功能 698
24.2.1 刚性攻丝的基本要求 698
24.2.2 刚性攻丝功能使用要点 704
24.2.3 刚性攻丝的动作调试 705
24.3 多主轴控制 707
24.3.1 多主轴控制功能 707
24.3.2 多主轴控制的配置与参数 709
24.3.3 多主轴控制信号 711
24.4 主轴同步控制 711
24.4.1 主轴同步控制的结构 711
24.4.2 主轴同步控制功能的使用 713
24.4.3 主轴同步的控制 714
24.4.4 主轴同步的动作过程 716
24.5 串行主轴附加控制功能 717
24.5.1 串行主轴附加控制功能概述 717
24.5.2 PMC主轴控制 720
24.5.3 Y/△切换控制 722
24.5.4 电机切换控制 725
第25章 特殊轴控制功能 728
25.1 PMC轴的功能与控制 728
25.1.1 PMC轴的功能特点与控制通道 728
25.1.2 PMC轴控制命令的组成 729
25.1.3 PMC轴的控制 730
25.1.4 PMC轴的运行控制 731
25.2 PMC轴控制信号与参数 732
25.2.1 PMC轴控制信号 732
25.2.2 PMC轴控制参数 735
25.3 I/O-Link轴的功能与基本控制 736
25.3.1 I/O-Link轴的特点与控制方式 736
25.3.2 I/O-Link轴的CNC控制参数与信号 738
25.3.3 I/O-Link轴参数与控制信号 739
25.4 I/O-Link轴的循环操作控制 745
25.4.1 控制命令与响应数据 745
25.4.2 循环操作的动作控制 748
25.4.3 循环操作响应数据的读入 750
25.5 I/O-Link轴的直接命令控制 752
25.5.1 I/O地址分配与信号说明 752
25.5.2 控制标记的功能 754
25.5.3 控制命令与响应数据 755
25.6 PowerMate管理器 758
25.6.1 PowerMate管理器的功能与显示 758
25.6.2 PowerMate管理器的操作 759
25.7 轴其他控制功能 761
25.7.1 双电机驱动功能 761
25.7.2 主-从同步控制功能 762
第6篇 维修篇 766
第26章 CNC状态诊断与检查 766
26.1 系统配置与状态显示 766
26.1.1 CNC配置的检查 766
26.1.2 伺服与主轴配置的检查 769
26.1.3 软件配置的变更 770
26.1.4 CNC基本工作状态的显示 771
26.2 模块工作状态的指示 772
26.2.1 故障诊断的方法与主板状态指示 772
26.2.2 附加功能板工作状态指示 774
26.3 CNC诊断数据的显示 777
26.3.1 CNC诊断信息显示 777
26.3.2 伺服驱动诊断 778
26.3.3 FSSB总线诊断 782
26.3.4 主轴诊断 782
26.4 负载表与波形显示 784
26.4.1 负载表显示 784
26.4.2 波形显示的基本设定 785
26.4.3 波形显示 787
26.5 日常维护页面的显示与设定 789
26.5.1 日常维护状态显示与编辑 789
26.5.2 日常维护页面的设定 791
第27章 CNC报警与处理 793
27.1 CNC报警的分类与显示 793
27.1.1 CNC报警的分类 793
27.1.2 现行报警的显示 794
27.1.3 报警履历的显示 795
27.2 操作履历的显示 797
27.2.1 操作履历的显示格式 797
27.2.2 操作履历显示的设定 800
27.3 常见报警的处理 801
27.3.1 常见报警的处理 801
27.3.2 回参考点报警的处理 802
27.4 伺服、主轴系统报警的处理 805
27.4.1 位置测量系统报警的处理 805
27.4.2 驱动器报警的处理 806
27.4.3 FSSB总线报警的处理 809
27.4.4 串行主轴通信报警的处理 809
27.5 CNC故障的综合分析 810
27.5.1 手动操作不能进行 810
27.5.2 回参考点故障 812
27.5.3 自动工作不能进行 813
第28章 驱动器报警与处理 815
28.1 αi系列电源与伺服模块的检查与维修 815
28.1.1 电源模块的状态指示与风机维修 815
28.1.2 伺服驱动模块的状态指示与维修 818
28.1.3 利用伺服调整页面的故障检查 819
28.2 α系列主轴模块的检查与维修 820
28.2.1 α系列主轴驱动的基本诊断 820
28.2.2 SPM的报警显示 821
28.2.3 SPM的错误显示 825
28.3 βi系列驱动器的故障诊断与维修 826
28.3.1 βi系列驱动器的故障显示 826
28.3.2 熔断器与风机的更换 828
28.4 电机与编码器的检查与维修 829
28.4.1 电机的基本状态检查 829
28.4.2 编码器的检查 830
28.5 伺服驱动器故障的分析与处理 831
28.6 I/O-Link轴的报警处理 834
附录A PMC信号地址分配表 839
附录B PMC信号说明表 846
附录C 串行主轴参数汇总表 861
附录D FS-OiCCNC报警总览 869
附录E 串行主轴CNC报警与PSM模块报警总览 883
附录F PMC报警总览 887
- 《管理信息系统习题集》郭晓军 2016
- 《信息系统安全技术管理策略 信息安全经济学视角》赵柳榕著 2020
- 《Maya 2018完全实战技术手册》来阳编著 2019
- 《高等教育双机械基础课程系列教材 高等学校教材 机械设计课程设计手册 第5版》吴宗泽,罗圣国,高志,李威 2018
- 《系统解剖学速记》阿虎医考研究组编 2019
- 《慢性呼吸系统疾病物理治疗工作手册》(荷)瑞克·考斯林克(RikGosselink) 2020
- 《战略情报 情报人员、管理者和用户手册》(澳)唐·麦克道尔(Don McDowell)著 2019
- 《社会文化系统中的翻译》姜秋霞,杨正军 2019
- 《中国生态系统定位观测与研究数据集 森林生态系统卷 云南西双版纳》邓晓保·唐建维 2010
- 《实用内科手册》黄清,阮浩航主编 2016
- 《市政工程基础》杨岚编著 2009
- 《家畜百宝 猪、牛、羊、鸡的综合利用》山西省商业厅组织技术处编著 1959
- 《《道德经》200句》崇贤书院编著 2018
- 《高级英语阅读与听说教程》刘秀梅编著 2019
- 《计算机网络与通信基础》谢雨飞,田启川编著 2019
- 《看图自学吉他弹唱教程》陈飞编著 2019
- 《法语词汇认知联想记忆法》刘莲编著 2020
- 《培智学校义务教育实验教科书教师教学用书 生活适应 二年级 上》人民教育出版社,课程教材研究所,特殊教育课程教材研究中心编著 2019
- 《国家社科基金项目申报规范 技巧与案例 第3版 2020》文传浩,夏宇编著 2019
- 《流体力学》张扬军,彭杰,诸葛伟林编著 2019
- 《指向核心素养 北京十一学校名师教学设计 英语 七年级 上 配人教版》周志英总主编 2019
- 《办好人民满意的教育 全国教育满意度调查报告》(中国)中国教育科学研究院 2019
- 《北京生态环境保护》《北京环境保护丛书》编委会编著 2018
- 《人民院士》吴娜著 2019
- 《指向核心素养 北京十一学校名师教学设计 英语 九年级 上 配人教版》周志英总主编 2019
- 《中国人民的心》杨朔著;夕琳编 2019
- 《高等院校旅游专业系列教材 旅游企业岗位培训系列教材 新编北京导游英语》杨昆,鄢莉,谭明华 2019
- 《中华人民共和国成立70周年优秀文学作品精选 短篇小说卷 上 全2册》贺邵俊主编 2019
- 《指向核心素养 北京十一学校名师教学设计 数学 九年级 上 配人教版》周志英总主编 2019
- 《中华人民共和国成立70周年优秀文学作品精选 中篇小说卷 下 全3册》洪治纲主编 2019