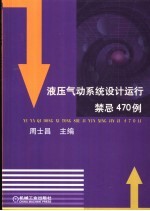
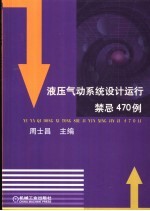
液压气动系统设计运行禁忌470例PDF电子书下载
- 电子书积分:9 积分如何计算积分?
- 作 者:周士昌主编
- 出 版 社:北京:机械工业出版社
- 出版年份:2002
- ISBN:7111107918
- 页数:163 页
第1章 传动系统的选型 1
1.1 功率重量比要求大时宜采用液压传动 1
1.2 轻载高精度位置控制宜尽量采用电气传动 1
1.3 负载大响应要求快时不宜采用气压传动 1
1.4 要求无级变速、调速范围大时宜采用液压传动 1
1.5 要求低速稳定性高时不宜采用气压传动 2
1.6 直线往复运动宜选用液压或气压传动 2
1.7 要求刚度大的系统不宜采用气压传动 2
1.8 要求价格低廉,能用电动机带动简单机械机构实现的简单运动在负载不大控制精度要求不高的场合不宜选用液压传动 2
1.9 要求定位精度高的场合不宜选用气压传动 2
1.10 有冲击载荷的场合宜用液压传动 2
1.16 能用普通液压传动系统完成的动作不用液压比例系统,能用液压比例系数完成的动作不用液压伺服系统 3
1.15 对降低噪声要求高的场合不宜用液压传动和气压传动 3
1.14 易燃易爆、多尘多水等环境恶劣的场合一般不宜用液压传动 3
1.13 温度变化大的场合用液压系统不易获得高的控制精度 3
1.12 要求效率高的场合不宜用液压传动和气压传动 3
1.11 环境防污染要求高的场合不宜用液压传动 3
1.17 除简单功能外,不宜用纯液压或纯气动系统完成控制功能,最好采用机电液(气)一体化系统来完成 4
1.18 超高速旋转或往复运动的场合不宜用电气或液压传动,应选用气压传动 4
1.19 低速大转矩场合不宜用气压传动和电气传动,应选用液压传动 4
1.20 有过载保护要求的场合宜用液压或气压传动 4
1.21 传动比要求严格的场合不宜用液压或气压传动 4
1.22 远距离传输功率时不宜用液压传动 5
1.23 冬季北方严寒地区,野外不宜采用液压传动 5
第2章 液压缸的设计与运行 6
2.1 柱塞缸不能靠液压力回程 6
2.2 应避免活塞杆失稳 6
2.3 间隙密封活塞的液压缸不宜承受重载 6
2.4 快速动作液压缸应设置缓冲装置 6
2.8 长液压缸应避免使用拉杆结构 7
2.7 液压缸的安全系数不能过小 7
2.5 液压缸固定安装时应避免两端都固定 7
2.6 液压缸设计应尽量避免采用非标尺寸 7
2.9 拉杆结构的液压缸不宜用于恶劣的工作环境 8
2.10 大型液压缸活塞的滑动表面宜软不宜硬 8
2.11 工程机械设备上不宜使用普通液压缸 8
2.12 缸筒内表面粗糙度的要求 9
2.13 活塞杆导向套长度不宜过小 9
2.14 高速、长行程液压缸的导向套应采用特殊结构 9
2.15 短行程液压缸不宜用两端缓冲装置 9
2.16 低速液压缸不必采用缓冲装置 10
2.17 大型液压缸不宜由安装螺栓承受负载 10
2.18 液压缸基座必须有足够的刚度 10
2.20 尾部法兰固定式液压缸不能使固定螺栓承受弯矩 11
2.21 耳环式安装的液压缸应注意负载方向 11
2.19 法兰式安装的液压缸不宜由螺栓承受负载 11
2.22 耳轴式安装的液压缸应注意负载方向 12
2.23 耳轴支座应尽量靠近耳轴根部 12
2.24 不能带压拆卸液压缸 12
2.25 拆卸液压缸活塞时不能硬性操作 12
2.26 活塞杆导向套不均匀磨损不能太大 12
2.27 新组装的液压缸应进行耐压试验 13
2.28 液压缸的缓冲结构中单向阀通流能力不能太小 13
2.29 耳轴式液压缸的耳轴必须与液压缸轴线成直角 13
2.30 柱塞缸不宜水平放置 14
2.31 缸筒必须保证必要的形位公差 14
2.32 液压缸耳环的位置公差 14
2.33 销轴式液压缸的位置公差 14
2.37 高压长液压缸的特殊问题 15
2.36 密封沟槽不宜设置在缸筒上 15
2.34 端部焊接焊缝应距液压缸工作表面有一定距离 15
2.35 缸筒内壁的形位公差 15
2.38 端盖采用螺纹连接时应注意的问题 16
2.39 端盖不宜过薄 16
2.40 活塞与缸筒的配合必须符合标准 17
2.41 活塞长度不宜过短 17
2.42 活塞应要求足够精度的形位公差 17
2.43 液压缸端面的形位公差 17
2.44 活塞杆的形位公差 18
2.45 应注意防止液压缸动作时产生别劲现象 18
2.46 活塞杆端部螺纹损坏的原因 18
2.47 活塞杆轴径过渡必须圆滑 19
2.48 钢球式排气阀座的接触表面角度不能任意 19
2.51 不宜用固定安装的液压缸驱动摆动式负载 20
2.49 锥阀式排气阀产生泄漏的主要原因 20
2.50 液压缸轴线应与负载运动方向严格一致 20
2.52 耳轴式液压缸不宜采用球面轴承 21
2.53 液压缸中的摩擦副应避免采用相同材料 21
2.54 液压缸位置布置应考虑拆装方便 21
2.55 避免液压缸活塞杆承受较大径向力 21
2.56 检修主机上的液压缸应使活塞杆缩回并泄压后进行 22
2.57 液压缸正式运行前需排净缸内的气体,卧式液压缸进出油口最好向上 22
2.58 采用耳环或铰轴的液压缸,油口需采用软管联接 22
第3章 液压马达的选择设计与运行 23
3.1 液压马达的转速不能太低 23
3.2 液压马达与变速箱不宜配套使用 23
3.3 液压马达的泄油口应单独回油箱 23
3.6 液压马达输出轴与负载必须保证同轴度 24
3.7 液压马达在驱动大惯性负载时不宜突然停车 24
3.5 液压马达轴端不能承受径向力 24
3.4 柱塞式马达首次使用时应将壳体内充满油液 24
3.8 液压马达内不宜进入空气 25
3.9 闭式马达回路中的流量匹配必须合理 25
3.10 启动液压马达时液压介质的粘度不宜过低或过高 25
3.11 中大功率液压马达不宜采用节流调速 25
3.12 将多个液压马达的输出轴用机械方法连接在一起实现同步时应有补油回路 26
3.13 曲柄连杆式液压马达的回油不宜直接回油箱 26
3.14 行走或起重驱动用液压马达必须加限速阀 26
3.15 长时间保持制动状态的液压马达必须使用制动器 26
3.16 带载启动的液压马达应注意不要超载 27
3.17 摆动液压马达应考虑液压冲击的吸收问题 27
3.18 摆动液压马达不能承受轴向和径向载荷 27
3.19 安装马达的机架应该有足够的刚度 27
3.21 内曲线马达出油口应具有0.5~Mpa左右的背压 28
3.20 马达泄油管的安装方位应向上 28
第4章 液压泵的选择及其系统设计与运行 29
4.1 自吸性差的液压泵,避免在其吸油管上装设过滤器 29
4.2 配管时,避免造成液压泵吸油阻力过大 29
4.3 液压泵吸油管漏气时,避免继续使用 29
4.6 避免将溢流阀的排油管与液压泵的吸油管相连 30
4.7 避免将液压泵的外泄漏油管与该泵的吸油管相连 30
4.5 液压泵轴与原动机轴装配后同轴度超差应禁止液压泵运转 30
4.4 避免液压泵的安装基础不牢 30
4.8 避免液压泵带负载启动 31
4.9 在带负载启动不可避免的情况下,应采取相应措施 31
4.10 液压泵内装溢流阀不宜做系统调压用,只宜用作安全阀 31
4.11 避免在油温偏低或偏高的情况下,启动运转液压泵 32
4.12 避免液压泵传动轴承受较大径向力 32
4.13 避免液压泵较长时间在最大压力下运转 32
4.14 避免液压泵较长时间在最高转速下运转 32
4.17 使用手动伺服变量泵控制执行机构换向的闭式液压系统应避免自吸补油 33
4.15 避免液压泵较长时间在转速偏低的情况下运转 33
4.16 避免主泵与其辅助泵之间的启动或停止的时间间隔过短 33
4.18 用变量泵与单杆缸组成闭式液压系统应采取相应措施 34
4.19 壳体内未注满油的液压泵应禁止启动 34
4.20 向泵和马达壳体内通油进行冷却,避免使壳体内压力偏高 34
4.21 避免壳体涂有油漆的液压泵安装在油箱内的油面以下 34
4.22 在变量泵和马达组成的闭式系统中,在马达作泵运行的工况,避免主泵承受工作压差 35
4.23 恒功率调速回路避免单独使用 35
4.24 避免几台泵的泄油管并联成一根等直径管后再通往油箱 35
4.25 避免将液压泵的泄油管与系统的总回油管相连 36
4.26 避免用较软的胶管或塑料管作泵的吸油管 36
4.27 液压泵初次启动避免泵内空气无排出通路 36
4.29 从原理上来说,液压马达可以作泵运行,但泵作马达运行是有条件的 37
4.30 管路压力损失过大导致恒功率变量泵输出流量达不到预计要求 37
4.28 变量泵为主泵的闭式系统避免以该泵在系统中的实际流量为依据确定所需的补油量 37
4.31 液压泵吸油口或排油口的过滤器应该清洗时,避免继续使用 38
4.32 多执行机构采用节流调速时避免只采用一个泵供油 38
4.33 避免用普通电动机的前端盖悬臂支撑液压泵 38
4.34 避免液压泵泵体上泄油口所接的油管的最高部分低于泵的轴线 38
4.35 设计泵 马达组成的重物起升闭式系统时,注意考虑开车瞬间重物下滑情况 39
4.36 补油回路的油不宜采用未经冷却的回油 39
4.37 泵与电动机的联轴器的螺栓不宜凸出在联轴器之外 40
4.38 尾部张力液压控制回路应采用优先供油方式 40
4.39 泵吸油口不宜采用铰接管接头 40
4.40 避免液压泵配管别劲 41
4.41 避免液压泵支承架(弯板)刚度不够 41
4.42 避免安装泵轴端联轴节时采用铁锤 41
4.43 变量泵采用自吸式向系统提供较小流量时,避免在较小偏角时启动 41
5.1 使用遥控卸荷溢流阀时,避免其遥控口所接液压元件的泄漏量偏大 42
5.2 两个规格和调定参数相同的溢流阀易产生共振 42
第5章 液压控制阀的选择及其系统设计及运行 42
5.3 配管不当引起溢流阀产生噪声 43
5.4 溢流阀的遥控口所串接的小型溢流阀和换向阀,应注意它们的先后顺序 43
5.5避免将压力表接在溢流阀的遥控口上 43
5.6 溢流节流阀只能接在执行机构的进油路上 44
5.7 节流调速回路中的调速元件在回路中位置不当,使油温偏高 44
5.8 避免通过同步阀的实际流量较之其额定流量小太多 44
5.9 高压下,避免突然使溢流阀卸荷 45
5.10 选型不当导致溢流阀动作缓慢 45
5.11 避免设计液压回路选择液压阀时只从原理出发而不考虑结构 45
5.12 避免执行机构负载交变导致冲击 46
5.13 同时进行速度和顺序控制的回路,顺序阀的控制方式应慎重考虑 47
5.14 避免回路设计不当导致垂直下落的平衡回路产生干涉故障 48
5.15 长时间卸荷的液压系统宜采用先导式卸荷溢流阀 49
5.16 卸压回路设计不当导致“炮鸣现象” 50
5.17 避免回路设计不合理导致液压卡紧系统出现工作松动 53
5.18 调速阀流量瞬间跳跃导致压力冲击 54
5.19 流量阀结构不合理导致调节手轮费力 54
5.20 所选顺序阀的结构不当导致压力失控和噪声 55
5.21 避免累计误差不能消除导致分流阀同步回路不同步 55
5.22 避免换向阀突然回到中位,导致激烈压力冲击 55
5.23 溢流阀的设定压力不当导致液压缸运动速度达不到要求 56
5.24 节流调速回路未考虑负载变化,导致液压缸速度不稳定 56
5.25 减压阀阀芯的阻尼孔部分堵塞造成二次压力不稳定 57
5.26 未考虑局部调整对全局的影响导致插装阀节流调速系统调速适得其反 57
5.27 液动换向阀的控制油的回油避免与背压偏高的回油管路相接 58
5.28 使用没有单独泄油口的手动换向阀应避免回油背压较高或泄油管路过长过细 58
5.29 避免将多个换向阀的泄油管直接并联成一个回油管而回油 59
5.30 液动换向阀阀芯动作过快导致换向时产生冲击 59
5.31 使用中位具有卸荷功能的电液换向阀不能换向的原因分析 59
5.33 避免单纯用换向阀的中位机能来锁定要求定位精度高的执行机构 60
5.32 避免通过换向阀的实际流量远大于该阀的额定流量 60
5.35 在锁紧回路内不允许有泄漏 61
5.34 用液控单向阀锁紧执行机构时其控制油口一定要接油箱 61
5.36 液控单向阀选型不当时可能导致工作不正常 62
5.37 重力负载向下运动时可能导致液压缸驱动一侧油路压力过低 62
5.38 换向阀内泄可能导致液压缸缓慢滑动 63
5.39 电液换向阀的换向平稳性要好于电磁换向阀 63
5.40 液压泵的出口在任何瞬间都不允许封闭 64
5.41 溢流阀遥控口必须封闭严密 64
5.42 阀的泄漏油一定要直接回油箱 65
5.43 液压力驱动换向的双向变量泵应注意变换方向时在零排量处失去驱动力 65
5.44 大惯量且频繁启动系统,应兼顾功能与节能 66
5.45 高精度同步系统宜采用比例控制或伺服控制 66
5.47 多缸同时动作的系统,应注意负载不同而引起的互相干扰 67
5.48 不可忽略液压元件的内泄漏对系统的影响 67
5.46 负载差异大的多缸系统,应注意节能 67
5.49 油箱散热面积应足够大,以免系统温升过大 68
5.50 大功率液压系统中忌用节流调速 68
5.51 液压系统中切忌残留空气 68
5.52 两套闭式液压系统并联,由于设计不当导致两执行机构功率相差过大 69
5.53 溢流阀和顺序阀调节参数不当导致顺序动作达不到要求 69
5.54 压力调定参数不当导致恒压泵供油系统油温过高 70
5.55 多路阀等阀体内的溢流阀只宜用作安全阀 70
5.56 有同步要求的液压缸不宜简单并联 71
5.57 电磁换向阀应注意控制电源参数应与电磁阀一致 71
5.58 电液换向阀应注意先导阀控制形式与阀功能一致 72
5.59 检修换向阀时应注意阀芯的装配方向 72
5.60 管式液压元件之间配管时忌讳采用的螺纹形式及尺寸参数不对 73
5.61 管式阀避免在进出油口未判明时进行配管 73
5.64 液压阀失灵后,忌讳采用锤打阀体的做法 74
5.63 液压阀调节手柄忌讳在调节后不锁紧 74
5.62 电液换向阀先导控制压力应符合产品样本中的使用范围 74
5.65 液压系统在运行中忌讳带压进行维修 75
5.66 完成配管的液压系统忌讳在未进行循环清洗的状态下投入运行 75
5.67 电液换向阀采用内控形式所不能采用的几种滑阀机能 76
5.68 防止或减少换向冲击宜采取的几种措施 77
第6章 液压辅件的选择设计及运行 78
6.1 加热器不宜设置于管路中 78
6.2 加热器安装位置不宜过高 78
6.3 冷却器不宜放置于回油过滤器前 78
6.4 冷却器散热面积应足够 79
6.5 冷却器通流能力不能过低 79
6.6 辅助供油或作应急能源用蓄能器容量不能过小 79
6.10 液位计不宜过长或过短 80
6.9 蓄能器安装方向应合理 80
6.8 蓄能器安装位置应便于检修 80
6.7 蓄能器与液压泵间应设置单向阀 80
6.11 液位计选型应考虑使用环境 81
6.12 安装压力表的支撑强度应足够 81
6.13 压力表量程选择应适当 81
6.14 过滤器通流能力不能过低 81
6.15 应合理选择过滤器滤芯 82
6.16 过滤器安装法兰孔不宜过小 82
6.17 切忌过滤器中液流方向不固定 82
6.18 吸油过滤器精度不宜过高 83
6.19 液压泵吸油口设过滤器应注意液压泵的具体要求 83
6.20 高压过滤器应注意拆装空间 83
6.21 管路中设置过滤器应有堵塞报警装置 83
6.25 回油过滤器的通流能力不能简单地按液压泵的流量来选择 84
6.24 高压过滤器应放在溢流阀之前 84
6.23 防止冷却水管表面结露 84
6.22 油箱底部设过滤器时应考虑更换元件时的防漏 84
6.26 过滤器应尽量安排在油箱外部,以便更换滤芯 85
6.27 直接装于油箱上的回油过滤器应置于回油液面以下 85
6.28 温度传感器温包位置不宜过高 85
6.29 空气过滤器型号不宜过小 85
6.30 密封沟槽设计应合理 86
6.31 软密封安装不宜过紧 86
6.32 密封法兰安装螺钉应对称放置 86
6.33 拆装密封圈时应尽量用专用工具 86
6.34 O型密封圈用于高压时应有挡圈 86
6.38 密封圈沟槽边缘应倒角但倒角半径R不能太大 87
6.40 唇形密封圈安装时应有导向套 87
6.39 密封圈安装时应防止拧扭 87
6.36 不宜用螺纹端压盖来压紧V型圈等密封填料 87
6.35 正确安装防尘密封圈 87
6.37 注意密封带缠绕方向应使密封带愈拧愈紧 87
6.41 旋转密封处速度不宜过高 88
6.42 动密封用O型圈压缩量应小于静密封O型圈压缩量 88
6.43 密封轴表面粗糙度不宜过低 88
6.44 密封轴表面硬度应合理选择 88
6.45 密封圈安装结构应合理,以免损伤密封圈 88
6.48 集成块体积不宜过大 89
6.49 联轴器选型应合理 89
6.46 连接螺栓应有足够刚度 89
6.47 进出油箱管路应密封良好 89
6.50 联轴器应设轴向定位装置 90
6.51 截止阀应有足够耐压能力 90
6.52 油箱连接法兰结构应合理,以防漏油 90
6.53 放油塞位置应合理,以便维修 90
6.57 蓄能器专用截止阀通径大小应根据系统使用情况适当选择 91
6.56 选择冷却器的冷却面积时应考虑现场提供冷却介质的条件 91
6.54 液压泵吸油口截止阀通径不宜过小 91
6.55 加热器安装面不宜采用橡胶材料密封 91
6.58 蓄能器安装时忌讯用管路作为支撑 92
6.59 不允许在蓄能器上进行加工和焊接 92
6.60 蓄能器充气应注意的问题 92
6.61 选择充氮工具要注意的问题 92
6.62 辅件中发讯器的使用电压应与系统控制电压相一致 93
6.63 电磁水阀的使用电压应与系统控制电压一致 93
6.64 过滤器不能用管路作为固定支撑 93
6.65 使用水乙二醇介质时,选择过滤器要特殊标明 93
6.66 在油箱内测温元件的温包应远离加热器和回油、冷却油管 94
6.67 棒式磁滤器安装时应远离液位发讯器 94
6.68 过滤器的过滤精度应满足元件对介质精度的要求 94
6.71 提高冷却器冷却效果的方法 95
6.72 普通冷却器不宜采用海水作为冷却介质 95
6.70 冷却器进水管路应根据实际情况设置水过滤器 95
6.69 防止冷却器管路结垢的方法 95
6.73 无缝钢管忌讳的几种煨管形状 96
6.75 集成块加工后宜采用化学防锈处理 96
6.76 集成块内孔道加工后需去除毛刺飞边 97
第7章 液压站、油箱、管路及管接头的设计和运行 98
7.1 柱塞泵安装位置低于油箱液面 98
7.2 大功率液压站泵与油箱应采用软管连接 98
7.3 液压泵置于油箱盖上时,油箱盖应有足够的强度 99
7.4 液压泵的转速不宜过高 99
7.5 液压系统必须设置压力调节和显示装置 100
7.6 液压集成块钻相交孔最大偏心距不大于规定值 100
7.9 液压集成块孔间距壁厚不宜小于5mm 101
7.8 液压集成块通道应尽量避免斜孔 101
7.7 液压集成块油口间的间距应注意管接头旋转空间 101
7.10 液压集成块深孔应考虑加工可能性 102
7.11 油箱底面应设计成斜坡状 102
7.12 油箱底不可做成双层底面 103
7.13 油箱底同不应与地面接触 103
7.14 泵吸油管不可离油箱底面太近 104
7.15 液压系统回油管出口应浸在液面以下 104
7.16 较在大油箱应设置隔板将吸油、回油管隔开 104
7.17 油箱隔板应有适宜高度以免液压泵吸空 105
7.18 油箱应封闭防尘 105
7.19 油箱装置空气过滤器大小应按泵流量考虑 105
7.20 吸油管密封要严,不得漏气 105
7.23 尽量减少接头、转弯的数量及管子的长度 106
7.24 弯曲管路的曲率应尽可能小 106
7.22 管路较长时应使用管夹 106
7.21 具有外泄漏的元件的泄漏油管与回油管连通时,不得有背压 106
7.25 使用焊接式管接头的管路应保证拆卸方便 107
7.26 管子用法兰连接时,法兰必须在管路平直部分接合 107
7.27 在管路适当地方设置测压孔,以便检查 107
7.28 油管配置后应进行酸洗 107
7.29 执行机构的液压胶管应避免与其它构件摩擦 107
7.30 胶管的弯曲同胶管接头的安装应在同一运动平面上,以防扭转 108
7.31 胶管连接管路应有一定的余量 109
7.32 胶管曲率半径应大于管径10倍以上 109
7.33 平行或交叉布置的管路之间应有10mm以上的空隙 109
7.34 系统不允许在执行元件运动状态下调节系统工作压力 109
7.35 无压力表的液压系统不可盲目调压 109
7.37 液压站注油宜采用过滤器精度相适合的滤油小车加油 110
7.38 油箱内的吸油及回油管端部加工成45°斜断面 110
7.36 装有蓄能器的液压系统,拆卸管路前,必须先将蓄能器中油压卸掉 110
7.39 油箱内壁宜采用喷塑工艺 111
7.40 油箱应根据需要设置相应的清洗口 111
7.41 管路焊接前管子端面需打破口 111
7.42 管路切割忌讳采用火焰切割 112
7.43 压力管路应在管路高点位置设置排气接头 112
7.44 不允许在管路表面采用焊接形式固定管道 113
8.5 乙烯橡胶、丁基橡胶密封件不能用于油包水型乳化液 114
8.9 乳化液介质不能用于0℃以下及65℃以上的系统 114
8.8 水乙二醇不能用于温度高于65℃的系统 114
8.6 硅橡胶、聚氯烷橡胶密封件不能用于水乙二醇液压介质 114
8.7 丁腈橡胶不能用于磷酸脂液压介质 114
8.3 油液粘度不宜过高或过低 114
8.2 新油液使用前必须过滤 114
8.1 不同型号液压油不可混合使用 114
第8章 液压介质的选择及使用 114
8.4 乙烯橡胶、丁基橡胶密封件不能用于矿物油系液压介质中 114
第9章 机液伺服阀及系统设计运行 115
9.1 注意机液伺服阀与普通换向阀的图形符号是有区别的 115
9.2 注意机液伺服阀与普通换向阀相比,在尺寸精度上有较高的要求 115
9.4 注意机液伺服阀与普通换向阀开口型式上的区别 116
9.3 注意用机液伺服阀控制液压缸与用普通换向阀控制液压缸有本质的区别 116
9.5 注意与普通换向阀不同,机液伺服阀需要考虑其阀位移一流量曲线(xv-QL)及流量增益(KN)问题 117
9.6 机液伺服阀对执行器的控制,可以用液阻桥路图表示(未表示反馈方式)。这种表示法有利于进一步的分析 117
9.7 注意普通三位四通换向阀也可用液阻桥路图来表示它对液压缸的控制 118
9.8 注意直线输入/直线输出(1∶1)机液伺服系统的原理及液阻桥路的特点 118
9.9 注意直线输入/直线输出(非1∶1)机液伺服系统的原理及液阻桥路的特点 119
9.10 注意旋转输入/旋转输出机液伺服系统的原理及液阻桥路的特点 120
9.11 注意旋转输入/直线输出机液伺服系统的原理及液阻桥路的特点 121
9.13 注意机液伺服系统还存在精度问题 122
9.14 注意机液伺服系统的响应问题 122
9.12 机液伺服系统要能正常工作,必须考虑其稳定性问题 122
第10章 电液伺服阀及系统设计运行 123
10.1 电液伺服阀基本功能 123
10.2 电液伺服阀与电液换向阀在图形符号上的区别 123
10.3 电液伺服阀与机液伺服阀在图形符号上的区别 124
10.4 电液伺服系统与机液伺服系统在控制系统和框图上的区别 124
10.5 电液伺服阀的三大组件 125
10.6 电液伺服阀有3种前置放大器 125
10.7 力矩马达与力马达的工作原理不同 125
10.8 力反馈两级电液伺服阀的控制原理框图特点 126
10.9 流量反馈两级电液伺服阀的控制原理框图特点 126
10.10 压力反馈两级电液伺服阀的控制原理框图特点 127
10.11 两级电液伺服阀无输入电流时,也要消耗流量(静耗流量) 127
10.13 电液伺服阀线圈的接法 128
10.12 电液伺服阀的几个动态指标 128
10.14 电液伺服阀的安装位置应尽可能靠近液压执行器(液压缸或液压马达) 129
10.15 电液伺服阀与执行机构之间尽量避免使用软管,管内应排尽气体 129
10.16 电液伺服系统要使用过滤精度高于5μm的过滤器,以除去介质中的固体颗粒 129
10.17 电液伺服系统在使用前应进行预先清洗 129
10.18 电液伺服系统应定期维修 129
第11章 插装阀系统设计及运行 130
11.1 插装阀基本单元的组成 130
11.2 插装阀有各种功能单元 130
11.3 插装阀有减压功能单元 130
11.4 插装阀的单向功能单元 131
11.5 插装阀的液控(通导型)单向功能单元 131
11.6 插装阀的液控(截止型)单向功能单元 131
11.7 插装阀的两位三通换向功能单元 131
11.10 插装阀通道块设计应注意的事项 132
11.9 插装阀的诸多特点 132
11.8 插装阀的两位四通换向功能单元 132
11.11 如何正确选择插装阀的阀芯 133
11.12 插装阀液压系统的运行及维护 133
第12章 气源装置及气动辅件的选择设计和运行 134
12.1 必须正确选择空压机的种类 134
12.2 有些特殊场合必须选用无油润滑空压机 135
12.3 自由空气流量和压缩空气流量不能混淆 135
12.4 空压机铭牌流量值的确定必须考虑三种因素 135
12.5 后冷却器在空压站中不可缺少 136
12.6 后冷却器的类型及规格应正确选择 136
12.7 油水分离器类型选择应正确 137
12.8 油水分离器的结构必须合理 138
12.9 贮气罐应配置必要的辅件 138
12.11 贮气罐结构设计应符合规范 139
12.10 贮气罐容积不宜过小 139
12.12 干燥器的选型应合理 140
12.13 空压站内设备排序不能颠倒 141
12.14 气源装置均应进行水压试验 141
12.15 分水滤气器规格不宜过小 141
12.16 分水滤气器安装方向不能颠倒 142
12.17 分水滤气器必须自动排水或不定期手动排水 143
12.18 分水滤气器滤芯必须定期清洗或更换 144
12.19 油雾器的规格不宜过小,也不宜过大 144
12.20 油雾器安装距离不能过远 144
12.21 油雾器油杯中的润滑油位应适中 145
12.22 油雾器注油时不应停气 145
12.23 油雾器润滑油的流量必须适中 146
12.24 选择消声器的种类应考虑降噪的频率 146
12.25 消气器规格不宜过小 146
12.27 气液转换器的规格应适中 147
12.26 气液转换器侧壁应配置视窗 147
12.28 气动软管只适于无热源的气动系统中 148
12.29 气动硬管应选用不易生锈的管材 148
12.30 气动管接头应考虑拆卸的便利 148
12.31 厂区及车间干线管道应有一定角度的倾斜 149
12.32 干线管道及支线管道终点应设置集水罐 149
12.33 支管必须在干管的上部采用大角度拐弯后再向下引出 150
12.34 各干管和支管的空气流速不能太高 151
12.35 必须严格控制整个供气系统的压力损失 151
12.36 空压站输出的压缩空气相对湿度必须小于90% 151
第13章 气动执行机构的选择设计和运行 152
13.1 气卸输出力(动载荷)计算时,必须考虑其“负载率” 152
13.2 弹簧复位单动气缸行程不能过大 152
13.3 薄膜式气缸只能适用于短行程 152
13.4 气缸运动速度较高时,必须选用可调缓冲型气缸 152
13.8 为获得多个精度位控制,宜选用数字气缸 153
13.7 径向尺寸受限而须增大输出力时宜选用串联气缸 153
13.5 安装空间受限时宜选用薄型气缸 153
13.6 为实现反向同步宜选用双活塞气缸 153
13.9 为获得局部超高压压缩空气,宜选用增压气缸 154
13.10 为获得稳速运动,宜选用气——液阻尼缸 154
13.11 为获得高精度位置控制时,宜选用气可调行程气缸 154
13.12 超长行程气缸应设置加强环 154
13.13 为获得较长的冲击动能,宜选用普通型冲击气缸 155
13.14 为延长气缸寿命,应保证良好的润滑 155
13.15 气缸运动速度不宜过低 155
13.16 气缸不能承受径向力 155
13.17 输出力在40kN以上时,不宜选用气缸驱动 155
13.24 在变载荷工况下,选择气马达应考虑速度范围及力矩 156
13.23 工作环境恶劣时宜选用气马达 156
13.22 低速大转矩宜选用活塞式气马达 156
13.20 往复回转运动宜选用摆动气马达驱动 156
13.19 连续回转宜选用气马达驱动 156
13.18 气缸尽量不使用满行程 156
13.21 高速小转矩宜选用叶片式气马达 156
13.25 在均衡载荷下,选择气马达应着重考虑工作速度 157
13.26 气马达运转中必须保证良好的润滑 157
13.27 供给气马达的压缩空气必须达到规定的清洁度 157
13.28 气马达应定期检修 157
13.29 叶片式马达工作转速低于空载最大转速的25%时,应改用活塞式气马达 157
第14章 气动控制元件的选择设计及系统设计运行 158
14.1 通过某些特殊气体时(有毒、有害),应选择非溢流式减压阀 158
14.2 有远程调压需要时,应选用外先导式减压阀 158
14.3 气动减压阀的规格不宜过小 158
14.4 气动减压阀应安装在过滤器与油雾器之间 158
14.7 为获得高精度的稳定气压,应选择定值器 159
14.8 空压机及贮气罐上必须设置安全阀(溢流阀) 159
14.6 减压阀的进、出口不能颠倒 159
14.5 减压阀不使用时,应放松其调压旋钮 159
14.9 气动节流阀不能保证气动执行机构稳速运动 160
14.10 气动气流阀应尽量安装在执行机构附近 160
14.11 通过气体流量较大时,应选用截止式换向阀 160
14.12 要保证较好的密封性能,应选用截止式换向阀 160
14.13 压缩空气的质量较差时,应选用截止工换向阀 160
14.14 要实现“记忆”功能时,应选用滑 阀式换向阀 161
14.15 工作环境恶劣时,宜选用气控换向阀 161
14.16 为提高气缸往复运动速度,应采用快速排气阀 161
14.17 进入大型用气设备的气源管路上应设置主路过滤器 161
14.18 多个控制元件串联的系统,应复核其合成“S”值是否满足要求 161
14.19 为提高气缸运动的平稳性,应尽量采用排气节流调速方式 162
参考文献 163
- 《指向核心素养 北京十一学校名师教学设计 英语 七年级 上 配人教版》周志英总主编 2019
- 《北京生态环境保护》《北京环境保护丛书》编委会编著 2018
- 《高等教育双机械基础课程系列教材 高等学校教材 机械设计课程设计手册 第5版》吴宗泽,罗圣国,高志,李威 2018
- 《指向核心素养 北京十一学校名师教学设计 英语 九年级 上 配人教版》周志英总主编 2019
- 《高等院校旅游专业系列教材 旅游企业岗位培训系列教材 新编北京导游英语》杨昆,鄢莉,谭明华 2019
- 《中国十大出版家》王震,贺越明著 1991
- 《近代民营出版机构的英语函授教育 以“商务、中华、开明”函授学校为个案 1915年-1946年版》丁伟 2017
- 《新工业时代 世界级工业家张毓强和他的“新石头记”》秦朔 2019
- 《智能制造高技能人才培养规划丛书 ABB工业机器人虚拟仿真教程》(中国)工控帮教研组 2019
- 《AutoCAD机械设计实例精解 2019中文版》北京兆迪科技有限公司编著 2019