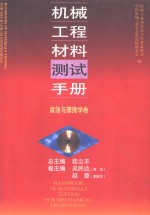
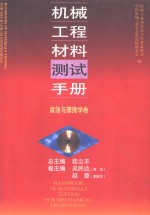
机械工程材料测试手册 腐蚀与摩擦学卷PDF电子书下载
- 电子书积分:23 积分如何计算积分?
- 作 者:桂立丰总主编;吴民达,赵源卷主编;机械工业部科技与质量监督司,中国机械工程学会理化检验分会编
- 出 版 社:沈阳:辽宁科学技术出版社
- 出版年份:2002
- ISBN:7538132198
- 页数:885 页
1.1 金属腐蚀的定义及其重要意义 3
目 录 3
1 概述 (71 3
1.2 金属腐蚀的分类 3
5.3 离子氮化 (84 3
第1章金属腐蚀原理 3
第一部分腐 蚀 3
第1篇 金属腐蚀及其试验方法概述 3
1 金属腐蚀的定义和分类 3
1.2.1 非电化学腐蚀和电化学腐蚀 4
1.2.2 均匀腐蚀(也称全面腐蚀)和局部腐蚀 4
1.2.3 按金属发生腐蚀时所处环境介质分类 5
2 金属氧化 5
2.1 金属氧化的定义 5
2.2 氧化热力学 5
2.3 氧化的起始阶段 6
2.5.2 恒温动力学曲线 7
7 硫氮碳共渗 (84 7
2.5.1 氧化速度 7
2.4 保护性的和非保护性的膜——庇林-贝德沃斯比 7
2.5 氧化过程动力学 7
2.6 瓦格纳(Wagner)的氧化理论 10
2.7 金属氧化物的性质和氧化作用 11
2.8 氧化膜的内应力及膜的破坏 12
2.9 热腐蚀及热灰腐蚀 12
2.10 内氧化 13
2.11 与氢的作用 13
2.13 抗氧化合金 14
2.12 铁和铁基合金的氧化 14
3 电化学腐蚀 15
3.1 电极电位与腐蚀倾向 15
3.1.1 自由能变化和腐蚀倾向的电化学判据 15
3.1.2 腐蚀原电池 15
3.1.3 双电层结构和电极电位 16
3.1.4 平衡电极电位与能斯特(Nernst)方程 17
3.1.5 可逆电极与不可逆电极 19
3.1.6 电位-pH图 22
3.1.7 标准电极电位表和电偶序 24
3.1.8 腐蚀电池的类型 26
3.2 极化与腐蚀速度 28
3.2.1 腐蚀的阳极过程和阴极过程 28
3.2.3 极化作用 29
3.2.2 法拉第(Faraday)定律与腐蚀速度 29
3.2.4 浓差极化与活化极化 30
3.2.5 阳极极化与阴极极化 32
3.2.6 腐蚀电位与腐蚀电流 33
3.2.7 腐蚀极化图 33
3.3.1 实验极化曲线 35
3.3 腐蚀金属电极的极化 35
3.3.2 实验极化曲线与真实极化曲线的关系 36
3.3.3 腐蚀金属电极的极化方程式 36
3.3.4 电偶腐蚀效应与差异效应 37
3.3.5 阴极保护效应 38
3.4 混合电位理论及其应用 38
3.4.2 混合电位理论的应用 38
3.4.1 混合电位理论 38
3.5 放氢腐蚀与耗氧腐蚀 40
3.5.1 放氢腐蚀 40
3.5.2 耗氧腐蚀 44
3.6 金属的钝化 47
3.6.1 钝化现象与阳极钝化 47
3.6.2 金属的自钝化 50
7.3.4 热对流法回路试验 (1 52
3.6.3 钝化理论 53
4.1.2 溶液pH值的影响 54
4 影响腐蚀过程的因素 54
4.1.1 氧化剂和溶解氧的影响 54
4.1 环境因素 54
4.1.3 溶解盐与阴、阳离子的影响 55
4.1.4 温度的影响 56
4.1.6 其他 57
4.1.5 流速的影响 57
4.2 材料因素 58
4.2.1 金属种类的因素 58
4.2.2 合金元素和微量杂质的影响 58
4.2.3 晶体结构、结晶取向与晶体缺陷的影响 59
4.2.4 表面状态的影响 59
4.2.5 热处理的影响 59
4.3 应力作用 60
4.3.1 应力腐蚀破裂和腐蚀疲劳 60
1 腐蚀试验的目的和分类 61
1.1 腐蚀试验的目的 61
第2章 金属腐蚀试验方法概论 61
4.3.2 氢脆 61
1.2 腐蚀试验的分类 62
1.2.1 实验室试验 62
1.2.2 现场试验 63
1.2.3 实物试验 63
2 试验条件与影响因素 63
2.1 材料和试样 63
2.2 试样表面的制备 63
2.3 试样的暴露技术 63
2.4 通气 65
2.5 温度 65
2.6 流速 65
2.7 试验持续时间 66
2.9 腐蚀产物的清除方法 66
2.8 分段试验法 66
3 耐蚀性能的评定及表示方法 67
4.1 腐蚀试验设计原则 69
4 腐蚀试验设计与数据处理 69
4.1.1 明确试验目的 69
4.1.2 科学地安排试验 70
4.2 腐蚀试验数据初步整理 71
4.2.1 列表表示法 71
4.1.4 对比性试验 71
4.1.3 平行试验 71
4.2.2 图示法 72
4.3 腐蚀试验数据的统计分析 73
4.3.1 腐蚀试验数据的误差分析及消除方法 73
4.3.2 试验数据重现性和精确度评定 74
5 腐蚀失效分析及验证试验 74
5.1 腐蚀失效现场考察 74
5.1.1 腐蚀失效现场记录 74
5.1.2 腐蚀失效构件的处理及断口的保存 74
5.2.3 腐蚀失效构件的性能测定 75
5.2 腐蚀失效构件性能的测定和无损检测 75
5.2.1 腐蚀失效构件性能测定及无损检测的必要性 75
5.2.2 腐蚀失效构件的无损检测 75
5.3.1 断口的宏观分析(断裂源的寻找与判断) 76
5.3 腐蚀断裂构件主断面的断口分析 76
5.3.2 断口的微观观察 77
5.3.3 断裂途径与显微组织的关系 79
5.3.4 断口产物的分析 79
5.3.5 断口分析 79
5.4 腐蚀失效原因的判定及重现性实验 79
5.4.1 检验数据的处理 79
5.4.2 图片处理 80
5.4.3 重演性实验 80
5.5 总结及分析报告 81
参考文献 81
1.2 参比电极 85
第2篇金属腐蚀主要形态及其实验室测试技术第1章金属腐蚀电化学测试技术 85
1 电极电位测定 85
1.1 绝对电极电位与相对电极电位 85
1.4 电极电位测量 87
1.5 电极电位测量应用实例 87
1.3 自然腐蚀电位(开路电位) 87
2 极化曲线测量 88
2.1 极化曲线原理 88
2.2 极化曲线测量方法 88
2.3 稳态和准稳态测量系统 89
2.5.1 真实极化曲线(也称理想极化曲线)与实验极化曲线(也称表观极化曲线) 90
2.4 动态扫描测量系统 90
2.5 极化曲线分析 90
2.6.1 极化曲线外延法测定金属腐蚀速度 91
2.6 极化曲线应用举例 91
2.5.2 活化极化控制、浓差极化控制和钝化极化控制的极化曲线 91
2.6.2 阳极极化曲线评定耐蚀合金 92
2.6.3 极化曲线在缓蚀剂保护中的应用 93
3 极化电阻技术测量腐蚀速度 93
3.1 极化电阻方程式 93
3.2 线性极化方程式 94
3.4 确定常数的方法 94
3.3 线性极化电阻的测量 94
3.4.3 从电化学特性计算ba和bc值 95
3.4.2 挂片失重校正法 95
3.4.5 查文献数据或估计 95
3.5 误差分析 95
3.4.1 极化曲线法 95
3.4.4 弱极化区测量法 95
3.6 弱极化区测量方法 97
3.6.1 Engell两点法 97
3.6.2 Barnartt三点法 97
3.6.3 Mansfeld曲线重合法 97
3.6.4 杨璋四点法和截距法 98
3.6.5 曹楚南近似法 99
4.1.2 腐蚀金属电极的等效电路 99
4 电化学阻抗谱 99
4.1 电化学阻抗的基本概念 99
4.1.1 电化学阻抗的定义和特点 99
4.1.3 阻抗的图示 100
4.1.4 Warburg扩散阻抗 101
4.2.1 电解池的阻抗 101
4.2 电化学阻抗谱的实验测量 101
4.2.2 阻抗测量的基本原理 102
4.2.3 阻抗测量线路 102
4.2.4 阻抗测量的各种方法 103
4.2.6 阻抗谐波分析 103
4.2.5 阻抗的时域测量 103
4.3.1 图解分析阻抗数据 104
4.3 电化学阻抗的数据处理 104
4.3.2 用等效电路处理阻抗数据 105
4.3.3 用阻抗数学模型处理数据 105
4.4 电化学阻抗在金属腐蚀研究中的应用 106
4.4.1 均匀腐蚀速度的监测 106
4.3.4 K-K转换与阻抗数据分析 106
4.4.3 研究缓蚀剂 107
4.4.2 评定有机涂层 107
4.4.4 研究钝化和点腐蚀 108
5 实验电位-pH图绘制技术 108
5.1 电位-pH图简介 108
5.2 实验电位-pH图的制作 109
6 高温电化学测试技术 111
6.1 高温高压容器 112
6.2 参比电极 112
6.3 IR降引起的测量误差 113
第2章金属的全面腐蚀测试 114
1.1.1 试验装置 114
1.1 全浸法浸泡试验 114
1 浸泡试验 114
1.1.2 试验条件 115
1.1.3 结果评定 116
1.2 半浸法浸泡试验 118
1.3 间浸法浸泡试验 119
2 盐雾试验 119
2.1 中性盐雾试验(NSS试验) 120
2.1.1 试验设备 120
2.1.2 试验溶液 120
2.2.2 试验溶液 122
2.2.4 结果评定 122
2.2.3 试验条件 122
2.1.4 结果评定 122
2.2 醋酸盐雾试验(ASS试验) 122
2.2.1 试验设备 122
2.1.3 试验条件 122
2.3 铜加速醋酸盐雾试验(CASS试验) 123
2.3.2 试验溶液 124
3 加速腐蚀试验 124
3.1 电解加速腐蚀试验(EC试验) 124
2.3.3 试验条件 124
2.3.1 试验设备 124
2.3.4 结果评定 124
3.2 腐蚀膏试验(Corrodokote试验或 125
CORR试验) 125
3.2.1 腐蚀膏的配制 126
3.2.2 试验条件 126
3.2.3 结果评定 126
3.3 湿热试验 126
3.3.1 试验设备 126
3.3.2 试验方法 126
3.4 模拟工业大气的SO2试验 127
3.3.3 结果评定 127
3.4.4 结果评定 128
3.5 硫酸露点腐蚀试验 128
3.4.3 二氧化硫制备方法 128
3.4.1 试验设备 128
3.4.2 试验条件 128
3.5.1 机理 129
3.5.2 影响因素 129
3.5.3 防止措施 131
3.5.4 硫酸露点温度测定方法 132
3.5.5 硫酸露点腐蚀试验方法 133
4 磨耗腐蚀试验 134
4.1 冲刷腐蚀试验 135
4.2 空泡腐蚀试验 135
4.3.1 试验方法 137
4.3 微动腐蚀试验 137
4.4 稳态和暂态型的腐蚀磨损试验 138
4.3.2 性能评定 138
4.3.3 电化学测试 138
4.3.4 展望 138
4.4.1 稳态型腐蚀磨损试验 138
5.1.1 标准试验法 139
5.1 几种常用高温氧化试验方法 139
4.4.2 暂态型腐蚀磨损试验 139
5 高温氧化试验 139
5.1.2 连续称重法 139
5.1.4 慢应变速率法 140
5.2.1 试验设备 140
5.1.5 热震法 140
5.2 试验条件 140
5.1.3 振动法 140
5.2.2 试样 141
5.2.3 安放试样的器皿 141
5.2.4 试验温度及时同 141
5.2.5 试样装炉和出炉 141
5.3 结果评定 141
5.3.1 失重法 141
5.3.2 增重法 142
5.3.3 测厚法 142
6 热腐蚀试验 142
6.1 试验方法 143
6.1.2 涂盐法 143
6.1.5 盐膜热振法 143
6.1.4 连续供盐凝聚法(又称迪安装置试验法) 143
6.1.3 淋盐法 143
6.1.1 坩埚法 143
6.1.6 电化学法 144
6.1.7 喷烧法 144
6.2 各种方法的比较 144
7 液态金属和熔盐腐蚀试验 144
7.1 液态金属腐蚀特征 145
7.1.1 液态金属腐蚀类型 145
7.1.2 液态金属腐蚀特征 145
7.2.1 熔盐腐蚀类型和特征 146
7.1.3 各种钢在常用液态金属中的耐蚀性 146
7.2 熔盐腐蚀特征 146
7.2.2 金属在熔盐中的腐蚀 147
7.3 液态金属和熔盐腐蚀试验方法 150
7.3.1 静态坩埚密封法试验 151
7.3.2 静态炉密封法试验 151
8 高温抗渗碳试验 152
7.3.3 摇摆法试验 152
7.3.5 强制循环法回路试验 152
8.1 高温抗渗碳试验方法 153
8.1.1 固体渗碳法 153
8.1.2 气体渗碳法 153
8.2 渗碳程度的评定方法 153
8.2.1 增重法 153
8.2.2 金相法 154
8.2.3 剥层化学分析法 155
8.2.4 力学性能法 155
1.1 定义 156
1.2 特征 156
1 概述 156
第3章晶间腐蚀测试评定 156
1.3 影响因素 158
1.3.1 成分的影响 158
1.3.2 组织的影响 161
1.3.3 热处理工艺的影响 162
1.3.4 冷加工的影响 163
1.3.5 环境的影响 163
1.4 控制措施 164
1.4.1 基于合金成分方面的控制措施 164
1.4.2 基于析出部位方面的控制措施 165
1.4.3 基于热力学方面的控制措施 165
2 示例 165
2.1 不锈钢 165
2.1.1 奥氏体不锈钢 165
2.1.2 铁素体不锈钢 166
2.2 铁基高镍耐蚀合金 167
2.1.3 奥氏体-铁素体双相不锈钢 167
2.3 镍基耐蚀合金 168
2.4 铝及其合金 169
2.4.1 铝 169
2.5 其他金属材料 170
2.4.2 铝合金 170
3 测试方法 171
3.1 说明 171
3.2.1 化学浸蚀法 174
3.2 方法简介 174
3.2.2 电化学法 175
3.3 原理 176
3.4 特点 178
3.5 应用范围 181
3.6 应用实例 185
3.7 要点 188
3.7.1 方法选择要点 188
3.7.2 试验装置要点 188
3.7.3 取样及试样制备要点 188
3.7.4 操作要点 189
3.8 评定方法 192
3.8.1 试验标准中推荐的评定方法 192
1.2 特征 194
1.1 定义 194
3.8.2 其他评定方法 194
1 点腐蚀概述 194
第4章点腐蚀测试评定 194
1.3.1 环境因素 196
1.4 点蚀危害性及某些实例 196
1.3.2 材料因素 196
1.3 主要影响因素 196
1.5 防护与控制措施 197
2 点蚀敏感性的试验评定和研究方法 197
2.1 化学浸泡法 198
2.1.1 三氯化铁试验 198
2.1.2 临界点蚀温度试验 200
2.2 电化学测试法 201
2.2.1 动电位法测点蚀电位 202
2.2.2 恒电位法测点蚀电位 205
2.2.3 恒电流法测点蚀电位 205
2.2.4 再钝化时间法(即划伤法)测点蚀电位 205
2.2.5 点蚀发展速率(PPR)试验 206
2.2.6 扫描微参比电极技术 207
2.2.7 恒电位区段法 207
2.2.8 电化学噪声法 208
2.2.9 电位-pH图在点蚀研究中的应用 208
2.2.11缓蚀电位(Ei) 212
2.2.10点蚀前兆电位(Ez) 212
2.3 点蚀数据的统计分析 213
2.2.12小结 213
1 缝隙腐蚀概述 214
1.1 定义 214
1.2 特征 214
第5章缝隙腐蚀测试评定 214
1.3 主要影响因素 215
1.3.1 缝隙的几何因素 216
1.3.2 环境因素 216
1.4 控制措施 216
2 缝隙腐蚀敏感性的试验评定和研究方 216
法 216
2.1 浸泡试验法 216
1.3.3 材料因素 216
2.1.1 三氯化铁试验 217
2.1.2 多缝隙试样试验 219
2.1.4 活性炭加速试验 220
2.1.3 临界缝隙腐蚀温度试验 220
2.2.1 临界(再钝化)电位测试法 221
2.2 电化学测试法 221
2.2.2 以(Eb-Ep)差值为判据的方法 223
2.2.3 去钝化pH值比较法 225
2.2.4 稳态pH与去钝化pH值比较法 227
2.3 预测不锈钢缝隙腐蚀性能的数学模型及实验研究 229
第6章应力腐蚀开裂测试评定 232
1 定义和特征 232
1.1 定义 232
1.2 SCC的特征 233
1.2.1 力学特性 233
1.2.2 环境的特性 233
1.2.3 冶金学特性 237
1.2.4 形态特征 238
2.3.2 恒变形法 240
2.1 试验目的 240
2.3 试验方法 240
2.3.1 恒载荷法 240
2 应力腐蚀开裂的试验方法 240
2.2 加速试验的途径 240
2.3.3 恒应变速率法(或称慢应变速率加载法) 242
2.3.4 断裂力学试验方法 244
2.4 应力腐蚀开裂试验方法标准 246
2.3.5 环境体系——腐蚀介质的加入方法 246
2.5 应力腐蚀开裂试验数据的处理和评定 247
2.6 标准应力腐蚀开裂试验方法实例 248
2.6.1 NACE TM01-77金属在常温下抗硫 248
化物应力腐蚀开裂标准试验方法 248
2.6.2 ASTM G35-1973不锈钢和有关镍- 252
铬-铁合金在连多硫酸中应力腐蚀开 252
裂敏感性的测定方法 252
第7章腐蚀疲劳测试评定 253
1 定义、特征及实例 253
1.1 定义 253
1.2 腐蚀疲劳断裂的特征 254
1.2.1 力学特征 254
1.2.3 形态特征 256
1.2.2 介质特征 256
1.3 实例 261
2.1 腐蚀疲劳试验目的 263
2 腐蚀疲劳试验方法 263
2.2 腐蚀疲劳试验中的加载方法 264
2.3 腐蚀介质的加入方法 265
1 定义、特征及实例 266
1.1 氢损伤的定义及其发展 266
1.2 氢损伤的分类 266
2 氢腐蚀和氢脆的特征及其影响因素 266
第8章 氢损伤测试评定 266
2.1 氢腐蚀的特征 266
2.2 影响氢腐蚀的因素 268
2.2.1 温度和压力 268
2.2.2 含碳量的影响 269
2.2.3 合金元素的影响 269
2.2.4 热处理的影响 269
3 氢脆的特征 270
3.2 延迟破坏 270
3.1 拉伸性能的表观规律 270
2.2.5 冷加工影响 270
3.3 氢脆断裂的形态特征 271
4 实例——高强度螺栓的氢脆开裂 273
5.5 慢应变速率法 275
5.6 氢渗透法 275
5.4 σ-tF法 275
5.3 爆破压力法 275
5.2 断面收缩率比较法 275
5.1 弯曲次数法 275
5 评定氢脆的试验方法 275
5.7 氢的放射性同位素照像法 276
第9章 电偶腐蚀测试评定 277
1 定义、影响因素及实例 277
1.1 电偶腐蚀定义与电偶序 277
1.3.1 电偶腐蚀破坏举例 278
1.2.3 面积影响 278
1.3 电偶腐蚀实例 278
1.2.2 距离影响 278
1.2.1 环境影响 278
1.2 电偶腐蚀影响因素 278
1.3.2 电偶腐蚀原理的应用 279
2 电偶腐蚀测试方法 280
2.1 试样制备 280
2.1.1 试样材料要求 280
2.1.2 试样形状与尺寸 280
2.1.3 试样制备方法 280
2.1.4 试样数量 280
2.2 实验室试验 280
2.2.1 试验仪器 280
2.2.2 试验条件 280
2.2.3 试验步骤 280
1 定义 281
第10章选择性腐蚀测试评定 281
2.3.1 试验环境 281
2.2.4 试验结果的评定 281
2.3 现场试验 281
2.3.2 试验方法 281
2.2.2 溶解-沉积机理 282
2 黄铜脱锌腐蚀 282
2.2.1 选择性溶解机理 282
2.1 特征 282
2.2 机理 282
2.4.1 控制合金成分 283
2.2.3 综合机理 283
2.3 影响因素 283
2.4 防止措施 283
2.3.2 介质的影响 283
2.3.1 合金成分的影响 283
3.1 青铜的脱铝、脱锡和脱硅 284
3.1.1 现象 284
3.1.2 影响因素 284
3.1.3 防止措施 284
3 种常用材料的成分选择性腐蚀 284
2.4.3 其他方法 284
2.4.2 控制介质侵蚀性 284
3.2.1 特点 285
3.2.2 影响因素 285
3.2.3 防止措施 285
3.3 贵金属合金的成分选择性腐蚀 285
3.4 灰口铸铁石墨化腐蚀 285
3.2 铜镍合金的脱铜和脱镍 285
4 几种常用材料的组织选择性腐蚀 286
4.2 铝及铝合金 286
4.1 不锈钢 286
4.4 钛及钛合金 287
5 高温条件下的选择性腐蚀 287
5.1 高温氧化性气氛下的选择性氧化和内氧化 287
4.3 镍及镍合金 287
5.2 高温还原性气氛下的脱碳腐蚀 288
5.3 高温熔盐中的选择性腐蚀 288
5.4 高温液态金属中的选择性腐蚀 288
6 选择性腐蚀测试评定方法 288
6.1 黄铜脱锌腐蚀性能的测定 288
6.2 成分选择性腐蚀的电化学试验方法 289
6.2.1 恒电位极化试验法 289
6.1.4 结果评定 289
6.1.1 试验设备 289
6.1.2 试样制备 289
6.1.3 试验条件 289
6.3 组织选择性腐蚀试验方法 290
6.2.2 恒电流极化试验法 290
6.2.3 旋转圆盘电极试验法 290
6.4.1 外观检验 291
6.4.2 质量变化 291
6.4 选择性腐蚀倾向的评定指标 291
6.4.3 学性能 292
6.4.4 显微组织 292
6.4.5 脱合金系数 292
参考文献 292
第3篇现场腐蚀试验 301
第1章大气腐蚀试验 301
1 大气腐蚀及其腐蚀特点 301
1.1 大气腐蚀的分类 301
1.2 大气腐蚀的特点 301
1.2.1 表面清洁金属的腐蚀 301
2 大气腐蚀试验方法 302
1.2.2 表面带锈层金属的腐蚀 302
2.1 大气暴露腐蚀试验 302
2.1.1 试验站场所的选择 303
2.1.2 暴晒装置 303
2.1.4 环境因素的测定 303
2.1.3 试样 303
2.2 实验室加速试验 305
2.1.5 记录和评定 305
2.2.1 盐水喷雾试验法 306
2.2.2 人工气候试验法 306
2.2.3 潮湿箱试验法 306
3.1 降雨和结露的影响 306
3.2 气温的影响 306
3 大气腐蚀的影响因素 306
3.3 SO2的影响 307
3.4 海盐颗粒的影响 307
3.5 固体尘粒的影响 307
4.1 使用耐候钢 310
4 防止大气腐蚀的方法 310
4.2 覆盖层保护 311
4.3 其他 314
第2章海水及淡水中的腐蚀试验 317
1.2 海洋环境的分类及腐蚀特点 317
1.1 海水的特点 317
1 海洋环境及其腐蚀特点 317
1.3 海水中异种金属接触的电偶腐蚀 318
2 淡水的分类及其腐蚀特点 319
2.1 淡水的分类 319
2.2.1 氧的阴极还原反应决定腐蚀的程度 320
2.2 金属材料在淡水中的腐蚀特点 320
2.2.2 金属阳极反应不均匀引起的局部腐蚀 321
3 试验方法 321
3.1 海水腐蚀试验 321
3.1.1 海水腐蚀试验的目的和内容 321
3.1.2 试验地点的选择 322
3.1.3 试验装置与试样 322
3.1.4 试验记录和评定 323
3.2 淡水腐蚀试验 323
3.3 实验室加速试验 323
3.3.1 电连接模拟试验 323
3.3.3 盐雾试验 324
3.3.4 流动水腐蚀试验 324
3.3.2 干湿交替试验 324
4.1 盐度的影响 325
4.2 pH值的影响 325
4.3 溶解氧量的影响 325
4 海水和淡水腐蚀的影响因素 325
4.4 温度的影响 326
4.5 流速的影响 327
4.6 溶解物质的影响 327
4.7 生物的影响 327
5 防护措施 328
5.1 合理选用金属材料 328
5.1.1 淡水环境中通常使用的金属材料 328
5.1.2 海水环境中使用的金属材料 329
5.2 涂层保护 331
5.3.2 外加电流法 333
5.3 阴极保护 333
5.3.1 牺牲阳极法 333
5.3.3 阴极保护的保护电位值 334
5.3.4 联合保护 334
5.4 其他 334
5.4.1 添加缓蚀剂 334
5.4.2 防蚀绷带-保护套 334
第3章土壤腐蚀试验 335
1 金属的土壤腐蚀及其腐蚀特点 335
2 影响土壤腐蚀的因素 336
2.1 土壤透气性 336
2.2 土壤电阻率 336
2.3 土壤pH值 336
2.4 土壤含水量 337
2.5 土壤氧化还原电位和细菌腐蚀 337
2.6 土壤含盐量 337
3 壤中各种金属的耐蚀特性 338
3.1 铸铁、低合金钢 338
4.2 浓差电池腐蚀 339
4.4 高温引起的异常腐蚀 339
4.3 pH差腐蚀电池 339
4 土壤中的异常腐蚀 339
4.1 异种金属接触腐蚀(电偶腐蚀) 339
3.2 不锈钢、非铁金属材料 339
5.1 埋藏试验 340
5 土壤腐蚀试验 340
4.5 杂散电流腐蚀(电蚀) 340
5.2 土壤腐蚀性评定 341
5.2.1 简单土壤腐蚀性评价 341
5.2.2 复杂土壤腐蚀性评价 342
5.3 土壤腐蚀性的定量估算 347
6 土壤物理、化学性质的测试方法 347
6.1 壤理化性质分类 347
6.2 现场测试点的选择 347
5.4 土壤腐蚀试验方法的比较 347
6.3 土壤样品的野外采集和实验室处理 348
6.3.1 土壤样品的野外采集 348
6.4 土壤物理、化学性质的测试方法 349
6.3.2 土壤样品分析前的实验室处理 349
6.4.2 土壤电阻率测定 349
6.4.1 土壤类型 349
6.4.4 土壤pH值测定 352
6.4.3 土壤含水量测定 352
6.4.5 土壤氧化还原电位测定 353
6.4.6 土壤化学性质的分析方法 354
7 防止土壤腐蚀的方法 354
7.1 防腐蚀方法及其比较 354
7.2 选择防腐蚀方法的依据 354
7.4 阴极保护 356
7.3 防腐蚀绝缘层的性能要求 356
参考文献 361
第4篇非金属材料耐腐蚀性能测试 365
第1章概述 365
1 化学腐蚀与物理腐蚀 365
2 偶联剂的作用机理 366
3 试验方法与评定 367
3.1 以K值来评定 367
2.1 低分子化合物的溶解过程 368
2.2 非晶态聚合物的溶胀和溶解 368
2 溶剂对聚合物的作用 368
1 塑料在化工防腐蚀上的应用 368
3.2 以腐蚀后试样质量和强度变化来评定 368
第2章塑料、纤维增强塑料耐腐蚀性能测试 368
3.3 以腐蚀后试样质量、体积、硬度以及试样介质等的变化来评定 368
2.4 聚合物在溶剂中的稳定性 369
2.3 结晶聚合物的溶解 369
3.1 聚烯烃的耐化学性能 370
3 聚合物的分子结构与耐化学性 370
3.2 聚芳烃的耐化学性能 371
3.3 聚二烯烃的耐化学性能 371
3.4 含氯、氟聚合物的耐化学性能 372
3.5 含羟基聚合物的耐化学性能 372
3.7 聚酰胺、聚氨酯的耐化学性能 372
3.6 聚酯的耐化学性能 372
3.8 聚缩醛的耐化学性能 373
4 塑料吸水性能测试 373
4.1 塑料吸水性试验标准方法 373
4.2 方法要点 373
4.2.1 试样及预处理 373
4.2.2 试验条件 373
4.2.3 试验步骤 373
5.1 标准方法 374
5 硬质微孔塑料吸水率的测定 374
4.2.4 试验结果计算 374
4.3 各种塑料吸水性试验方法比较 374
5.2 方法要点 375
5.2.4 步骤 375
5.2.2 仪器及材料 375
5.2.3 试样 375
5.2.1 原理 375
5.2.5 计算 376
6 玻璃钢吸水性试验方法 376
6.1 标准方法 376
6.2 方法要点 376
6.2.1 试样尺寸及数量 376
6.2.2 试验条件 376
6.2.3 试验步骤 377
6.2.4 计算 377
7.2 方法要点 377
7.1 标准方法 377
7 玻璃纤维增强塑料耐水性能测试 377
8 玻璃纤维增强塑料耐水性加速试验 378
方法 378
8.1 标准方法 378
8.2 方法要点 378
9 塑料耐液体化学介质性能测试 379
9.1 标准方法 379
9.2 方法要点 379
10 塑料耐油性能的测试 382
10.2 方法要点 382
11 玻璃纤维增强塑料用不饱和聚酯树 382
脂耐碱性能测试 382
11.1 标准方法 382
11.2 方法要点 382
10.1 标准方法 382
12.1 标准方法 383
12.2 方法要点 383
测定 383
12 玻璃纤维增强塑料耐化学药品性能 383
13 玻璃纤维增强塑料耐湿热性能测试 384
13.1 标准方法 384
13.2 方法要点 384
1.3.1 紫外光的影响 385
第3章耐老化性能的测试评定 385
1.3 原因和影响因素 385
1.2 特征 385
1 高分子材料老化原理 385
1.1 定义 385
1.3.2 氧的作用 386
1.3.3 热和温度的影响 386
1.3.4 水分的影响 387
2 高分子材料自然老化试验方法 387
2.1 自然气候暴露试验方法 387
2.1.1 标准方法 387
2.1.2 方法要点 387
3.1.1 试验设备 392
2.2.1 标准试验方法 392
3.1 人工气候试验方法 392
3 高分子材料人工加速老化试验方法 392
2.2.2 方法要点 392
2.2 耐光性试验方法 392
3.1.2 标准方法 393
3.1.3 方法要点 393
3.2.2 方法要点 394
3.2 热老化试验方法 394
3.2.1 标准试验方法 394
3.1.5 试验结果 394
3.1.4 试验步骤 394
3.3 湿热老化试验方法 396
3.3.2 方法简介 396
第4章橡胶、涂料、防锈油脂耐腐蚀性能试验方法 397
1 橡胶 397
1.1 扯断法 397
1.2 体积法和称重法 397
1.3 橡胶薄膜的浸油增厚试验 398
1.4 橡胶薄膜浸油减重试验 398
2 涂料 398
2.1 常温耐盐水性的测定 398
2.2 耐加温盐水性能的测定 398
2.3 耐酸碱性的测定 398
3.3 结果判断 399
3.2 试验方法 399
3.1 准备工作 399
3 防锈油脂 399
参考文献 400
一、 中国国家标准项目 401
附 录 401
附录 有关金属腐蚀试验标准方法 401
二、 国际标准项目 402
三、 其他国家标准项目 403
第二部分摩擦学 411
第1篇 总 论 411
第1章概论 411
第2章磨损问题的系统分析 412
1 磨损特性不是材料固有特性 412
2 磨损系统概念 412
3 磨损的系统表征 413
4 配副性 414
第3章摩擦过程系统结构元素的相互作用 416
1 摩擦副两元素的相互作用 416
2 润滑剂与摩擦副材料相互作用 417
3 环境气氛与其他结构元素相互作用 421
3.1 环境气氛与摩擦副材料相互作用 421
3.2 环境气氛与润滑剂相互作用 425
第4章摩擦过程结构元素性能变化 427
1 表面形貌变化 427
2 表面层成分变化 428
3 表面层结构 429
第5章磨损试验 430
1 磨损试验的特殊性和复杂性 430
2 实验室磨损试验 430
3 应应用性试样试验方法 431
3.1 应用性试样试验的模拟原则 431
3.2 应用性试样试验方法设计 432
3.3 应用性试样试验的注意事项 433
2 分析 434
4.1 往复磨损试验机试验方法 434
4 实验室模拟试验方法的制定 434
3 改善措施 434
1 问题的提出 434
第6章应用实例 434
3.4 应用性试样试验机的选择 434
4.2 环块磨损试验机试验方法 435
5 实验室快速试样试验结果 435
6 柴油发动机全速全载荷1000h台架强 436
参考文献 436
化试验和结果 436
第2篇摩擦测试 441
第1章概论 441
2 摩擦 443
1 固体表面及其接触 443
第2章名词术语 443
第3章 固体表面及其接触 444
1 表面形貌 444
1.1 表面形貌图形表示法 445
1.2 表面形貌参数表示法 445
2 表面形貌的测量 445
2.1 表面形貌测量方法简介 445
2.2 触针测量法 445
3 表面性质 450
5.1.1 赫兹理论——弹性接触解法 451
5.1.2 塑性接触 451
5.1 接触力学 451
5 表面接触过程 451
4 表面能 451
5.2 接触物理和接触化学 454
6 真实接触面积的测量 454
第4章摩擦及其测试 455
1 滑动摩擦 455
1.1 滑动摩擦及其测试的一般概念 455
7 摩擦测试用表面的制备 455
1.2 Stribeck曲线——有润滑表面滑动摩擦的特征 456
1.3 滑动摩擦副边界摩擦测试方法准则 457
1.4 试样模拟试验测试滑动摩擦 458
1.4.1 用于滑动摩擦测试的两分 458
力传感器 458
1.4.2 MMN-005型双功能粘滑摩擦系数 458
试验机 458
1.4.3 带计算机的往复摩擦试验仪 460
1.4.4 橡胶材料摩擦双轴测试仪 460
1.5.2 惯性测试法 462
1.5.1 热平衡法 462
1.5 零件模拟试验中的间接法测试滑动摩擦 462
1.6 零件模拟试验中的直接法测试滑动摩擦 465
1.6.1 径向滑动轴承的摩擦测试 465
1.6.2 推力滑动轴承的摩擦测试 467
2 滚动摩擦 468
2.1 滚动摩擦及其测试的一般概念 468
2.1.1 对滚动摩擦起主要作用的效应 468
2.1.2 滚动摩擦测试的控制条件 469
2.1.3 滚动摩擦系数 469
2.2 试样模拟试验测试滚动摩擦 469
2.2.1 双轮式滚动摩擦试验机 471
2.2.2 四轮式滚动摩擦试验机 472
3 滑动和滚动复合的摩擦 472
3.1 滑动和滚动复合的摩擦及其测试的一般概念 472
3.2 试样模拟试验测试滑动和滚动复合的摩擦 472
3.3 零件模拟试验测试滑动和滚动复合的摩擦 473
3.3.1 齿轮副的摩擦测试 473
3.3.2 凸轮-挺杆副的摩擦测试 473
1 真空中的摩擦 474
1.1 表面污染与真空 474
第5章特殊环境中的摩擦及其测试 474
1.2 温度对金属摩擦的影响 475
1.3 真空下的放气 475
2.1 石墨 476
2 几种润滑材料的真空摩擦特性 476
2.2 二硫化钼 477
2.3 氟化石墨 478
2.4 氮化硼 478
第6章摩擦温度及其测量 479
2 摩擦表面温度的测量 479
2.1 热电偶 479
2.1.1 由摩擦副双方构成的自然热电偶 479
1 摩擦表面的温升 479
2.1.2 由摩擦副中一方参与构成的自然热 480
电偶 480
2.1.3 拖曳式热电偶 480
2.1.4 插入式热电偶 481
2.2.1 红外线辐射温度计 481
2.2 红外线测量技术 481
2.2.2 红外线热像仪 482
2.3 微型薄膜温度传感器 482
参考文献 484
第3篇 磨损测试及磨损减缓 489
第1章概论 489
1 概述 489
2 磨损试验问题 490
3 研究摩擦学的分析工具 490
4 磨损类型与影响因素的关系 491
第2章名词术语 492
第3章磨损类型及减缓磨损的措施 495
1 粘着磨损 495
1.1 影响粘着磨损的因素 495
1.2 提高抗粘着磨损能力的措施 500
2 磨料磨损 503
2.1 影响磨料磨损的因素 503
2.2 提高抗磨料磨损能力的措施 510
3 表面疲劳磨损 514
3.1 影响表面疲劳磨损的因素 514
4.1 影响腐蚀磨损的因素 515
4 腐蚀磨损 515
3.2 提高抗表面疲劳磨损性能的措施 515
4.2 减缓腐蚀磨损的措施 517
5 气蚀 518
7 微动损伤 519
6 液滴冲蚀 519
7.1 微动磨损 520
7.2 微动腐蚀 525
7.3 微动疲劳 527
7.4 减缓微动损伤的措施 529
1 磨损的表征方法 531
第4章磨损的测量 531
2 磨损表征方法的选择 532
3 一般磨损量测量 533
4 称重法 533
5 测表法(测长法) 534
6 人工基准法 537
1 磨损试验方法分类 538
1.1 使用试验 538
第5章磨损试验方法及试验机 538
1.2 实验室试验 539
2 试样模拟试验原则 539
3 试样试验方法设计 539
4 M-2000型磨损试验机 540
5 ML-100磨料磨损试验机 543
6 MLS-225湿砂橡胶轮磨损试验机 544
7 MPX-2000盘销式磨损试验机 546
8 MK-200快速磨损试验机 547
9 JPM-1型接触疲劳磨损试验机 549
10 MH-1型漆膜磨损试验机 552
11 定速式摩擦试验机 553
12 MM-1000摩擦试验机 555
13 微动损伤试验装置 556
13.1 微动磨损试验装置 557
13.2 微动腐蚀试验装置 559
13.3 微动疲劳试验装置 560
14 气蚀试验 561
14.1 Venturi型气蚀试验装置 561
14.2 转盘型气蚀试验装置 562
14.3 振荡型气蚀试验装置 563
15 液滴冲蚀试验装置 565
15.1 旋转轮装置 565
15.2 旋转臂装置 565
14.4 喷射型气蚀试验装置 565
16 橡胶磨损试验机 566
16.1 NBS橡胶磨损试验机 566
16.2 PICO橡胶磨损试验机 567
16.3 格拉西里磨损试验机 567
17 零件模拟试验 568
17.1 轴承pv值试验 568
17.2 密封圈磨损试验装置 571
17.3 MCL-1000齿轮磨损试验机 572
17.4 超高真空摩擦试验机 574
17.5 超高真空原位表面分析摩擦实验装置 575
参考文献 576
第1章概论 583
1.1 润滑剂对摩擦的影响 583
第4篇润滑测试 583
1 概述 583
1.2 润滑剂对磨损的影响 584
1.3 润滑剂的冷却降温作用 585
1.4 润滑剂的防蚀和减震降噪作用 585
2 润滑剂的分类及其性能特点 585
2.1 液体润滑剂 585
2.2 半固体润滑剂 586
2.3 固体润滑剂 587
2.4 气体润滑剂 587
第2章名词术语 587
3.3.1 标准试验方法 596
1 概述 597
2 液体润滑剂与添加剂 597
第3章润滑剂与添加剂 597
2.1 润滑油的物理化学性能检验 600
2.1.1 粘度的测定 600
2.1.2 密度的测定 605
2.1.3 颜色 607
2.1.4 闪点和燃点的测定 608
2.1.5 凝点和倾点的测定 609
2.1.6 水分的测定 609
2.1.7 机械杂质的测定 609
2.1.8 残炭的测定 609
2.1.9 灰分的测定 610
2.1.10酸值、碱值及中和值的测定 610
2.1.11水溶性酸及碱的测定 611
2.1.12防锈性试验 611
2.1.1 3腐蚀试验 612
2.1.14 抗泡性和空气释放性测定 612
2.1.15 抗乳化性测定 613
2.1.17 氧化安定性测定 614
2.1.16 密封适应性指数测定 614
2.1.18 水解安定性 615
2.1.19 长霉试验 615
2.2 润滑油及添加剂的仪器分析 616
2.2.1 系统分析的基本程序 616
2.2.2 润滑油及添加剂的仪器分析类型 617
2.2.3 常用仪器分析方法简介 617
2.3.1 内燃机油的模拟台架测试方法 623
2.3 润滑油及添加剂的模拟台架测试 623
2.3.2 齿轮油的模拟台架测试方法 634
3 润滑脂及其添加剂 636
2.3.3 液压油的模拟台架试验方法 636
3.1 润滑脂的分类 637
3.1.1 矿物油润滑脂的分组、命名和代号 638
3.1.3 稠化剂的分类和代号 639
3.1.2 合成润滑脂的命名和代号 639
3.2.1 抗氧化剂 641
3.2 润滑脂的添加剂 641
3.2.2 抗腐蚀剂 642
3.2.3 防锈添加剂 642
3.2.4 极压抗磨添加剂 642
3.2.5 结构改善剂 643
3.3 润滑脂的流变性能及低温性能 644
3.3.1 润滑脂锥入度测定方法 644
3.3.2 润滑脂的强度极限及其测定方法 646
3.3.3 润滑脂的相似粘度及其测定法 647
3.3.4 润滑脂的触变性 650
3.3.5 润滑脂的机械安定性及其测定方法 651
3.3.6 润滑脂的低温转矩测定方法 651
3.3.7 润滑脂的低温泵送性测定方法 653
3.3.8 润滑脂的滴点测定法 653
3.3.9 高温流动性及其测定方法 655
3.3.10润滑脂的蒸发性测定方法 656
3.3.11 润滑脂的氧化安定性及其测定方法 657
3.3.12润滑脂胶体安定性测定方法 659
3.3.13润滑脂轴承寿命测定方法 660
3.3.14 润滑脂在轴承中的抗漏失性及其测定方法 662
3.3.15 润滑脂的降低噪音特性及其测试方法 667
3.4 润滑脂的润滑性能 667
3.4.1 润滑脂的润滑作用机理 667
3.4.2 润滑脂的极压抗磨性测试方法 668
3.4.3 润滑脂的抗微动磨损性测试方法 670
3.4.4 提高润滑脂润滑性能的途径 673
3.5 润滑脂的防护性等性能及其测试方法 674
3.5.1 润滑脂的防护性测试方法 674
3.5.2 润滑脂的抗水性测定方法 675
3.6 润滑脂的有害组分测定方法 676
3.6.1 润滑脂机械杂质测定法 676
3.6.2 润滑脂水分测定法 677
3.6.3 润滑脂皂分测定法 677
3.6.4 润滑脂灰分测定法(SH/T 0327) 677
3.7 润滑脂与合成橡胶的相容性测试方法 677
4 固体润滑剂 678
4.1 固体润滑剂的定义与分类 678
4.2 一些固体润滑剂的性质 679
4.2.1 固体润滑剂的优缺点和主要用途 679
4.2.3 固体润滑膜的一般性质 680
4.2.2 粉末固体润滑剂的一般性质 680
4.3 粉末固体润滑剂的性能测试 685
4.3.1 纯度 685
4.3.2 水分 686
4.3.3 挥发分 688
4.3.4 灰分 688
4.3.5 水溶物含量 689
4.3.6 pH值和酸碱度 690
4.3.7 含油量 690
4.3.8 粒度及筛余物 690
4.3.9 密度 694
4.3.10润滑性 696
4.4.1 膜厚度 698
4.3.11 固体润滑剂粉末的其他评定方法 698
4.4 固体润滑膜的性能测试 698
4.4.2 附着力 699
4.4.3 抗液性 704
4.4.4 耐腐蚀性 705
4.4.5 耐热性 706
4.4.7 硬度 707
4.4.8 弯曲和耐冲击性 709
4.4.9 耐磨寿命和承载能力 710
第4章 润滑剂摩擦学性能的测试方法与 713
试验机 713
2 试验机 713
2.1 四球试验机 713
2.2 环-块试验机 714
2.3 法兰克斯(Falex)系列试验机 716
2.4 LFW系列试验机 717
2 拉伸性能 719
2.1 塑料拉伸试验方法 719
(GB/T 1040—1992) 719
第5章 固体润滑材料测试技术 719
1 概述 719
2.2 玻璃纤维增强塑料拉伸性能试验方法(GB 1447—1983) 720
2.3 玻璃纤维增强塑料层合板层间拉伸强度试验方法(GB 4944—1996) 722
2.4 金属基自润滑复合材料拉伸强度的测定 723
3 压缩性能和压溃强度 723
3.1 塑料压缩试验方法 723
(GB/T1041—1992) 723
3.2 玻璃纤维增强塑料压缩性能试验方法(GB 1448—1983) 724
3.3 玻璃纤维增强塑料薄层板压缩性能 725
试验方法(GB 5258—1985) 725
3.4 金属基和无机非金属基自润滑复合材料压缩强度或压溃强度的测定 726
(GB 1043—1993) 727
4.2 玻璃纤维增强塑料简支梁式冲击试验方法(GB 1451—1983) 727
4 冲击韧度 727
4.1 塑料简支梁冲击试验方法 727
4.3 金属基和无机非金属基自润滑复合材料冲击韧度的测定 728
5 弯曲强度 729
5.2 玻璃纤维增强塑料弯曲性能试验方法(GB 1449—1983) 730
6.1 塑料球压痕硬度试验方法 732
(GB 3398—1982) 732
6.2 纤维增强塑料巴氏(巴柯尔)硬度试验方法(GB 3854—1983) 732
6 硬度 732
6.3 金属基和无机非金属基自润滑复合材料硬度的测定 733
6.3.1 布氏硬度(GB 231—1984) 734
6.3.2 洛氏硬度(GB/T 230—1991) 734
6.3.3 维氏硬度(GB/T 4340.1—1999) 735
6.3.4 显微硬度(GB/T 4340.1—1999) 736
6.3.5 肖氏硬度(GB 4341—1984) 736
7 密度 736
7.1 塑料密度和相对密度试验方法 736
(GB 1033—1986) 736
(GB 6343—1 995) 738
7.2 泡沫塑料和橡胶表观密度的测定 738
7.3 渗透性烧结金属材料的密度和开孔率的测定法(ISO 2738) 739
7.4 贵金属及其合金密度测量法 739
(GB/T 1423—1996) 739
8 膨胀系数 740
8.1 塑料线膨胀系数试验方法 740
(GB/T 1036—1989) 740
8.2 膨胀合金平均线膨胀系数测定法 741
(YB 940—1978) 741
9 摩擦磨损性能 741
9.1 塑料滑动摩擦磨损试验方法 741
(GB 3960—1983) 741
9.2 塑料-磨轮滚动磨损试验方法 742
(GB 5478—1985) 742
试验(GB 12444.1—1990) 743
9.3 金属磨损试验方法——MM型磨损 743
9.4 环-块试验机测定固体润滑材料摩擦磨损性能的试验方法 744
10.1 塑料轴承极限Pv值试验方法 745
10 极限pv值 745
(GB 7948—1987) 745
9.5 销-盘式试验机测定固体润滑材料摩擦磨损性能的试验方法 745
10.2 各种自润滑复合材料极限pv值试验方法 747
1 润滑油的粘温特性 748
1.1 粘度指数 748
第6章润滑油的粘温特性和粘压特性 748
1.2 粘度比 749
1.1.2 粘度指数算表 749
1.3 常用粘温关系式 749
2.2 Cameron幂函数关系式 750
2.1 Barus指数关系式 750
2.3 Roeland粘压关系式 750
2 润滑油的粘压特性 750
3 润滑油粘压特性的测定 751
2.4 粘度同时随温度和压力变化的关系式 751
3.1 落体测定法 751
3.3 旋转粘度计测定法 752
3.2 毛细管粘度测定法 752
3.4 石英振子测定法 753
参考文献 754
1 概述 759
第1章概论 759
2 摩擦系数资料 759
2.1 材料静摩擦系数 759
第5篇摩擦学应用资料 759
2.2 常用材料的摩擦系数 760
2.3 离合器中摩擦材料的摩擦系数 761
2.4 轴承的摩擦系数 761
1.1 塑料摩擦磨损的基础 763
1 塑料及其填充改性物 763
1.1.1 摩擦机理 763
1.1.2 磨损机理 763
第2章非金属材料 763
1.1.3 各种因素对塑料摩擦磨损的影响 764
1.2 塑料及其填充改性复合材料的磨擦 766
磨损特性 766
1.2.1 聚四氟乙烯 766
1.2.2 聚甲醛 772
1.2.4 聚乙烯 774
1.2.3 聚酰胺(尼龙) 774
1.2.5 聚氯乙烯(PVC) 775
1.2.7 酚醛树脂 776
1.2. 6 聚酰亚胺 776
1.2.8 聚邻苯二甲酸二丙烯酯 778
1.2.9 环氧树脂与不饱和聚酯 782
2 碳素材料及其他非金属材料 783
2.1 碳素材料 783
2.4 金刚石 787
2.3 玻璃 787
3 结构陶瓷 787
2.2 铁梨木 787
3.1.2 氧化锆(ZrO2)陶瓷 788
3.1.1 氧化铝(A12O3)陶瓷 788
3.1.3 氮化硅(Si3N4)陶瓷 788
3.1 结构陶瓷的结构和性能 788
3.1.5 碳化硅(SiC)陶瓷 789
3.1.4 赛隆(Sialon)陶瓷 789
3.1.6 陶瓷复合材料 789
3.2.1 微断裂 790
3.2 结构陶瓷的磨损机理 790
3 2.2 摩擦化学磨损 790
3.2.4 塑性流动 791
3.2.3 热机械磨损及熔化 791
3.3 结构陶瓷的摩擦学应用 791
3.3.1 陶瓷的用途 791
3.3.2 某些陶瓷制品性能 792
概述 795
第3章金属材料 795
2 耐磨钢 795
3 耐磨铸铁 813
4 轴承的磨损性能 820
4.1 轴承合金 820
4.2 粉末冶金材料 825
第4章减摩耐磨处理 827
1 概述 827
2 渗碳 827
3 渗硼 830
4 碳化物被覆处理 832
4.1 渗铬 833
4.2 渗钒 833
4.4 化学气相沉积(CVD) 835
4.3 盐浴热浸碳化物覆层的比较 835
4 5 物理气相沉积(PVD) 837
5.1 体氮化(渗氮) 841
5 氮化 841
5.2 液体渗氮 842
6 渗硫 844
5.4 几种氮化层的比较 844
8 磷化 851
9 离子注入 852
10 激光处理 853
11 电镀 858
第5章润滑材料的选用 858
1 概述 858
2 润滑油的选用 858
2.1 粘度 858
2.2 润滑状态 859
2.3 抗摩擦耐磨损与极压性能 861
2.4 润滑油的安定性 862
2.5 润滑油添加剂 862
2.6 合成油 862
2.7 其他选择因素 862
3 润滑脂的选用 862
3.1 润滑脂的组成 865
3.2 润滑脂的选择 865
4 固体润滑剂 867
4.2 固体润滑剂的分类 868
4.3 石墨 868
4.3.1 石墨的一般性质 868
4 1 固体润滑剂的基本性能 868
4.3.2 石墨的润滑性能与润滑机理 869
4.4 二硫化钼 870
4.4.1 二硫化钼的一般性能 870
4.3.3 石墨的应用实例 870
4.4.2 二硫化钼的润滑性能 871
4.4.3 二硫化钼的应用实例 872
4.5.1 氟化石墨的结构及一般性质 873
4.5.2 氟化石墨的润滑性能 873
4.5 氟化石墨 873
4.6 氮化硼 874
4.6.1 氮化硼的结构及一般性质 874
4.6.2 氮化硼的润滑性能及应用 874
4.7 稀土化合物 875
4.7.1 稀土化合物的一般性质 875
4.7.2 稀土化合物的润滑性能 875
5 自润滑材料 876
5.1 自润滑材料的组成 877
5.2 高分子自润滑复合材料 877
5.2.1 高分子自润滑材料的成型工艺 877
5.2.2 高分子自润滑材料的摩擦磨损特性及其应用 878
5.3 金属基自润滑复合材料 880
5.3.1 金属基自润滑材料的成型工艺 882
5.3.2 金属基自润滑材料的摩擦磨损特性 882
及其应用 882
参考文献 883
4.4.6 涂料固体含量测定法(GB/T 1725
5.1 塑料弯曲试验方法(GB 9341— 1988
1.1.1 粘度指数计算法(GB/T 1995— 1998
5.3 金属弯曲试验方法(GB 232— 1999
- 《市政工程基础》杨岚编著 2009
- 《工程静力学》王科盛主编 2019
- 《中央财政支持提升专业服务产业发展能力项目水利工程专业课程建设成果 设施农业工程技术》赵英编 2018
- 《化学反应工程》许志美主编 2019
- 《绿色过程工程与清洁生产技术 张懿院士论文集精选 上》《绿色过程工程与清洁生产技术》编写组编 2019
- 《软件工程》齐治昌,谭庆平,宁洪编著 2019
- 《全球贸易摩擦与大国兴衰》任泽平,罗志恒著 2019
- 《高等教育双机械基础课程系列教材 高等学校教材 机械设计课程设计手册 第5版》吴宗泽,罗圣国,高志,李威 2018
- 《化学工程与工艺专业实验指导》郭跃萍主编 2019
- 《天水师范学院60周年校庆文库 新工科视域下的工程基础与应用研究》《天水师范学院60周年校庆文库》编委会编 2019
- 《钒产业技术及应用》高峰,彭清静,华骏主编 2019
- 《现代水泥技术发展与应用论文集》天津水泥工业设计研究院有限公司编 2019
- 《异质性条件下技术创新最优市场结构研究 以中国高技术产业为例》千慧雄 2019
- 《Prometheus技术秘笈》百里燊 2019
- 《中央财政支持提升专业服务产业发展能力项目水利工程专业课程建设成果 设施农业工程技术》赵英编 2018
- 《药剂学实验操作技术》刘芳,高森主编 2019
- 《林下养蜂技术》罗文华,黄勇,刘佳霖主编 2017
- 《脱硝运行技术1000问》朱国宇编 2019
- 《催化剂制备过程技术》韩勇责任编辑;(中国)张继光 2019
- 《信息系统安全技术管理策略 信息安全经济学视角》赵柳榕著 2020