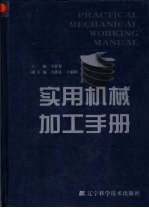
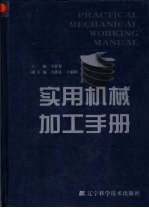
实用机械加工手册PDF电子书下载
- 电子书积分:54 积分如何计算积分?
- 作 者:马贤智主编
- 出 版 社:沈阳:辽宁科学技术出版社
- 出版年份:2002
- ISBN:7538129537
- 页数:2444 页
第1章 常用金属材料及热处理 1
1 金属热处理工艺常用术语 1
2 金属材料牌号的表示方法 1
2.1 黑色金属材料牌号的表示方法 1
2.2 有色金属材料牌号的表示方法 2
2.3 粉末冶金材料牌号的表示方法 5
3 金属材料化学成分和力学性能 6
3.1 黑色金属材料的化学成分和力学性能 6
3.2 有色金属材料的化学成分和力学性能 58
3.3 粉末冶金的化学成分和力学性能 113
4 常用材料的选用 116
4.1 选材的一般原则 116
4.2 常用材料的选用 117
1 光滑圆柱体公差 135
1.1 公差与配合的示意图 135
1.2 基本偏差系列图示 135
第2章 公差与配合 135
1.3 基本尺寸分段 136
1.4 标准公差 137
1.5 基本偏差 139
1.6 优先、常用的孔轴公差带与配合 145
1.7 孔、轴的极限偏差 148
2 角度公差 177
2.1 圆锥角公差 177
1.8 线性尺寸的未注公差 177
3 形状和位置公差 180
3.1 形状和位置公差的符号 180
2.2 未注公差角度的极限偏差 180
3.2 形状和位置公差的定义 181
3.3 形状和位置公差值 198
4 螺纹的公差与配合 204
4.1 普通螺纹的公差与配合 204
4.2 梯形螺纹的公差 238
4.3 锯齿形螺纹的公差 249
4.4 管螺纹的公差 259
5 键、花键联结的公差与配合 264
5.1 平键与键槽尺寸与公差 264
5.2 半圆键和键槽尺寸与公差 267
5.3 楔键和键槽尺寸与公差 268
5.4 矩形花键的公差与配合 269
5.5 圆柱直齿渐开线花键的公差与配合 270
6 齿轮公差 303
6.1 渐开线圆柱齿轮及其传动公差 303
6.2 锥齿轮及其传动公差 325
6.3 蜗轮、蜗杆及其传动公差 351
6.4 齿轮、齿条及其传动公差 364
1.1 机械加工余量的概念 370
1.2 确定加工余量应考虑的因素 370
1.3 加工余量的计算 370
1 概述 370
第3章 机械加工余量 370
2 毛坯机械加工余量和公差 371
2.1 铸件的机械加工余量和公差 371
2.2 锤上钢质自由锻件机械加工余量与公差 376
2.3 水压机上自由锻件机械加工余量与公差 388
2.4 锤上钢质胎模锻件机械加工余量与公差 397
2.5 钢质模锻件机械加工余量与公差 399
2.6 径向锻机上钢质轴类锻件机械加工余量与公差 411
2.7 直齿锥齿轮精锻件的机械加工余量与公差 413
2.8 金属冷冲压件机械加工余量与公差 417
2.9 轧制毛坯机械加工余量与公差 423
3 工序间机械加工余量 435
3.1 轴的加工余量 435
3.2 孔的加工余量 444
3.3 平面加工余量 454
3.4 齿轮加工余量 456
3.5 花键(轴、孔)和平键、键槽加工余量 458
3.6 攻螺纹前的钻孔直径和滚螺纹前螺杆直径 459
1.2 切削用量选用原则 469
1.1 切削用量的基本概念 469
2 车削用量 469
2.1 高速钢车刀常用切削用量 469
1 切削用量的基本概念及选用原则 469
第4章 切削用量及切削液 469
2.2 硬质合金车刀常用切削用量 474
2.3 金刚石车刀和陶瓷车刀常用切削用量 477
2.4 粗车外圆与孔常用进给量 478
2.5 切断、车槽及成形车削切削用量 479
2.6 高速车削细长轴的切削用量 481
2.7 使用条件变换时车削速度修正系数 481
2.8 车削速度计算公式 486
3 铣削用量 489
3.1 套式面铣刀常用切削用量 489
3.2 圆柱铣刀常用切削用量 493
3.3 三面刃圆盘铣刀常用切削用量 496
3.4 立铣刀常用切削用量 500
3.5 槽(花键)铣刀常用切削用量 506
3.6 切断铣刀常用切削用量 509
3.7 其他铣刀切削用量 511
3.8 使用条件变换时铣削速度修正系数 512
3.9 铣削速度和切削功率计算公式 517
4 刨、插削切削用量 521
4.1 龙门刨床常用切削用量 521
4.2 牛头刨床常用切削用量 523
4.3 龙门刨床和牛头刨床刨槽的切削速度 525
4.4 插床切削用量 525
4.5 使用条件变换时刨插削速度修正系数 527
4.6 刨、插削速度和切削力计算公式 528
5 钻、扩、铰、镗削用量 529
5.1 钻孔常用切削用量 529
5.2 扩孔常用切削用量 536
5.3 钻孔与扩孔切削速度修正系数 538
5.4 钻中心孔的切削用量及热处理后修中心孔的时间 540
5.5 铰孔常用切削用量 541
5.6 用锪钻锪端面的切削用量 544
5.7 镗孔常用切削用量 545
6 拉削的切削用量 547
7 磨削用量 550
7.1 磨外圆的切削用量 550
7.2 磨内圆的切削用量 552
7.3 磨平面的切削用量 555
7.4 无心磨床切削用量 562
7.8 研磨工艺参数 565
7.7 超精加工工艺参数 565
7.9 滚轮珩磨工艺参数 565
7.6 珩磨切削用量 565
7.5 砂带磨床切削用量 565
7.10 磨削时砂轮耐用度 566
8 螺纹加工切削用量 567
8.1 车螺纹切削用量 567
8.2 攻螺纹和套螺纹切削用量 569
8.3 铣螺纹切削用量 570
8.4 磨螺纹切削用量 572
8.5 在组合机床上加工螺纹的切削速度 572
8.6 螺纹加工切削速度计算公式 573
9 齿轮与花键加工切削用量 575
9.1 滚齿切削用量 575
9.2 插齿切削用量 579
9.3 铣齿和刨齿切削用量 581
9.4 剃齿和珩齿切削用量 582
9.5 磨齿切削用量 583
9.6 花键加工切削用量 585
9.7 滚齿、插齿及滚花键的切削速度与功率计算公式 588
10 切削液 589
10.1 切削液的分类及其组成 589
10.3 油基切削液与水基切削液使用性能对比及其应用情况 590
10.4 部分国产切削液性能及其适用范围 590
10.2 切削液的选择依据与程序 590
10.5 切削液的选用 598
10.6 切削液流量的一般要求 599
10.7 切削液使用和管理上常出现的故障及其解决方法 599
1 金属切削机床的型号 604
1.1 通用机床型号 604
第5章 金属切削机床 604
1.2 专用机床编号 626
2 常用金属切削机床的主要技术参数 627
2.1 车床 627
1.3 机床自动线编号 627
2.2 铣床 652
2.3 刨、插床 657
2.4 钻床 663
2.5 镗床 666
2.6 加工中心 671
2.7 拉床 675
2.8 磨床 676
2.9 齿轮与螺纹加工机床 684
2.10 特种加工机床 694
3 金属切削机床工作精度检验 699
3.1 车床工作精度检验 699
2.11 柔性加工单元 699
3.2 铣床工作精度检验 723
3.3 刨、插、拉、锯床工作精度检验 739
3.4 钻、镗床工作精度检验 747
3.5 磨床工作精度检验 765
3.6 齿轮加工机床工作精度检验 787
3.7 特种加工机床工作精度检验 797
3.8 组合机床工作精度检验 803
第6章 金属切削刀具 805
1 刀具结构要素及一般资料 805
1.1 直柄回转工具柄部和传动方头尺寸 805
1.2 直柄工具用传动扁尾及套筒 806
1.3 机床和工具柄用自夹圆锥 807
1.4 7:24圆锥联接工具锥柄 811
1.5 铣刀直柄 812
1.6 铣刀和铣刀杆互换尺寸 815
1.7 套式铰刀和套式扩孔钻用芯轴 818
1.8 拉刀柄部形式和尺寸 819
1.9 切削加工刀具用硬质合金分类、分组代号 826
1.10 刀具用高速钢分类代号 828
1.11 硬质合金焊接刀片 829
1.12 可转位硬质合金刀片 836
2.1 车刀的种类 887
2.2 高速钢车刀条 887
2 车刀 887
2.3 焊接式硬质合金车刀 888
2.4 硬质合金机械夹固式车刀 905
2.5 可转位车刀 909
3 钻头 951
3.1 麻花钻 951
3.2 中心钻 979
3.3 扩孔钻 981
3.4 锪钻 984
3.5 其他钻头 991
4 铰刀 996
4.1 铰刀的结构 996
4.2 铰刀专用公差 997
4.3 标准铰刀 997
5.1 铣刀的种类 1010
5.2 普通标准铣刀 1010
5 铣刀 1010
5.3 可转位铣刀 1036
6 拉刀 1047
6.1 拉刀的种类和结构 1047
6.2 拉刀的形式和尺寸 1049
7 螺纹加工刀具 1063
7.1 螺纹加工刀具的种类及特点 1063
7.2 丝锥 1063
7.3 圆板牙 1093
7.4 滚丝轮 1099
7.5 搓丝板 1102
8 切齿刀具 1104
8.1 切齿刀具的种类和应用 1104
8.2 齿轮铣刀 1105
8.3 齿轮滚刀 1107
8.4 插齿刀 1112
8.5 直齿锥齿轮精刨刀 1117
8.6 盘形剃齿刀 1121
8.7 花键加工刀具 1122
9 磨料、磨具 1126
9.1 磨具的分类和代号 1126
9.2 磨具的形状代号和尺寸标记 1127
9.3 常用砂轮的主要尺寸 1138
9.4 磨料、磨具的选择 1147
2 普通车床辅具 1157
1 概述 1157
2.1 刀杆 1157
第7章 机床辅具 1157
2.2 刀杆夹 1163
2.3 夹套 1165
3 自动车床辅具 1167
3.1 刀杆 1167
2.4 切制螺纹夹头 1167
3.2 刀架 1173
3.3 刀座 1180
3.4 刀夹 1181
3.5 接套 1190
4 铣床辅具 1191
4.1 铣刀杆 1191
4.2 中间套 1201
4.3 铣夹头 1208
4.4 接杆 1213
4.5 其他 1215
5 刨床、拉床辅具 1221
5.1 刀杆 1221
5.2 夹头 1223
5.3 接头 1226
5.4 导套和导套用支座 1228
5.5 其他 1231
6 钻床辅具 1235
6.1 接长套和过渡套 1235
6.2 夹紧套 1239
6.3 快换套 1241
6.4 接杆 1244
6.5 刀杆 1248
6.6 夹头 1250
6.7 扁尾锥柄工具用楔 1251
7 镗床辅具 1252
7.1 刀杆 1252
7.2 刀架 1271
7.3 接杆 1275
7.4 径向刀架用刀座 1277
7.5 镗刀杆用定心圆锥螺钉 1277
8 磨床辅具 1278
9 齿轮加工机床辅具 1283
9.1 滚齿刀杆 1283
9.2 插齿刀垫 1284
9.3 插齿刀接套 1285
9.4 锥柄插齿刀接套 1286
第8章 机床夹具 1288
1 概述 1288
1.1 夹具的定义和作用 1288
1.2 机床夹具的分类 1288
1.3 夹具设计中需注意的问题 1289
1.4 各种机床夹具种类和设计要点 1290
2 机床夹具零、部件标准及应用 1292
2.1 定位件 1292
2.2 导向件 1321
2.3 对刀件及其应用 1332
2.4 夹紧件 1335
2.5 塑料夹具用零件 1379
2.6 操作件 1382
2.7 其他件 1387
2.8 夹具零、部件综合应用示例及典型结构 1413
3 通用夹具 1429
3.1 顶尖 1429
3.2 卡头及快换卡头 1435
3.3 拨盘和花盘 1440
3.4 卡盘及过渡盘 1444
3.5 滑柱钻模 1458
3.6 气动滑柱钻模 1459
3.7 气动回转台 1460
4 气动夹具用气动元件 1461
4.1 汽缸 1461
4.2 气动控制元件 1471
4.3 气源处理元件 1478
4.4 气动辅助元件 1484
5.1 组合夹具的特点和使用范围 1498
5.2 组合夹具的加工精度 1498
5 组合夹具 1498
5.4 组合夹具元件的编号 1499
5.5 组合夹具元件 1499
5.3 组合夹具的标准化概况 1499
5.6 组合夹具的组装过程 1504
5.7 组合夹具组装守则 1505
1.1 工艺规程的类型、文件形式及其使用范围 1507
1 概述 1507
1.2 工艺规程设计的基本原则与要求 1507
第9章 工艺规程设计 1507
1.3 工艺规程的设计与审批程序 1508
2 工艺规程设计中常用工艺符号与代号 1511
2.1 机械加工定位与夹紧符号 1511
2.2 工艺流程图表用图形符号及应用示例 1514
2.3 工艺装备编号 1518
2.4 工艺文件编号 1526
3 常用工艺术语 1528
3.1 一般术语 1528
3.2 典型表面加工术语 1535
3.3 冷作、钳工及装配常用术语 1537
3.4 自动化制造系统术语 1539
4 常用工艺文件格式 1540
4.1 常用工艺规程格式 1540
4.2 管理用工艺文件格式 1577
5 机械加工工艺规程设计 1601
5.1 零件结构工艺性分析 1601
5.2 确定毛坯类型及其制造方法 1602
5.3 选择工艺基准 1604
5.4 选择加工方法 1612
5.5 设计零件加工路线 1614
5.6 确定加工余量和毛坯尺寸 1615
5.7 选择加工设备 1615
5.9 选择切削用量 1618
5.10 制定材料消耗工艺定额 1618
5.8 选择工艺装备 1618
6 自动车床加工工艺规程设计 1620
6.1 自动车床的加工工艺范围 1620
5.11 制定工时定额 1620
6.2 自动车床加工工艺方案的确定 1623
6.3 棒料毛坯和加工余量的选择 1623
6.4 自动车床调整卡片的设计 1624
6.5 凸轮的设计 1628
7 组合机床加工工艺规程设计 1632
7.1 组合机床的类型与适用范围 1632
7.2 组合机床加工工艺方案的确定 1634
7.3 组合机床加工切削用量的确定 1635
7.4 切削力、扭矩、切削功率及刀具耐用度的计算 1635
8.1 数控机床加工工艺准备工作内容和工艺规程特点 1644
8.2 数控机床加工路线及工序结构的设计 1644
8 数控机床加工工艺规程设计 1644
8.3 数控机床加工工序图的绘制及坐标计算 1646
8.5 数控机床加工切削用量的确定 1648
8.6 数控机床加工时间定额的确定 1648
8.4 数控机床调整卡片的设计 1648
8.7 数控机床加工程序编制 1649
第10章 切削加工通用工艺守则及典型工艺 1649
1 切削加工通用工艺守则 1650
1.1 切削加工通用工艺守则总则 1650
1.2 切削加工通用工艺守则车削 1651
1.3 切削加工通用工艺守则铣削 1652
1.4 切削加工通用工艺守则刨插削 1654
1.5 切削加工通用工艺守则钻削 1654
1.6 切削加工通用工艺守则镗削 1655
1.7 切削加工通用工艺守则拉削 1655
1.8 切削加工通用工艺守则磨削 1656
1.9 切削加工通用工艺守则齿轮加工 1657
1.10 切削加工通用工艺守则数控加工 1666
1.11 切削加工通用工艺守则下料 1666
1.12 切削加工通用工艺守则划线 1667
1.13 切削加工通用工艺守则钳工 1669
2 工艺典型化导则及典型工艺应用示例 1672
2.1 工艺典型化导则主要内容 1672
2.2 典型工艺示例 1674
3 典型零件加工工艺 1682
3.1 主轴加工 1682
3.2 细长轴加工 1694
3.3 曲轴加工 1696
3.4 丝杠的加工 1708
3.5 薄壁套筒的加工 1713
3.6 渐开线圆柱齿轮加工 1718
3.7 箱体的加工 1725
3.8 连杆的加工 1735
3.9 薄壁轴瓦加工 1751
1.1 现代制造技术的发展 1754
1 概述 1754
1.2 成组技术的发展与应用 1754
第11章 成组技术 1754
2 成组技术的分类编码系统 1757
2.1 分类方法 1757
2.2 零件编码系统 1758
2.3 零件编码系统的选择与应用 1849
2.4 零件编码系统的设计 1863
3 成组技术在工艺设计中的应用 1864
3.1 概述 1864
3.2 成组技术在工艺规程设计中的应用 1864
3.3 成组技术在工装设计中的应用 1881
4 成组生产系统的设计 1886
4.1 成组生产类型的分析 1886
4.2 成组生产的总体规划 1889
4.3 成组生产车间的布局设计 1891
5 成组生产的组织管理 1893
5.1 成组生产技术准备 1893
5.2 成组生产管理 1896
5.3 成组生产计划的编制 1900
1 概述 1904
1.1 材料的可加工性 1904
1.2 机械制造中常用难加工材料的类型 1904
第12章 难加工材料的切削加工 1904
2.1 常用冷硬铸铁的化学成分、力学性能及用途 1905
2 冷硬铸铁的加工 1905
2.2 冷硬铸铁的加工难点及解决措施 1905
1.4 解决难加工材料加工问题的主要途径 1905
1.3 难加工材料的切削加工特点 1905
2.3 加工冷硬铸铁应选用的刀具材料、几何参数和切削用量 1906
2.4 车削加工冷硬铸铁件的实例 1906
3 淬硬钢的加工 1907
3.1 车削 1907
3.2 刨削 1908
3.3 钻削 1909
3.4 硬齿面滚齿 1909
4 不锈钢的加工 1912
4.1 不锈钢的切削加工特点 1912
4.2 不锈钢的车削 1913
4.3 钻孔与铰孔 1915
4.4 铣削 1918
4.5 螺纹加工 1919
4.6 磨削 1921
5 高强度钢的加工 1922
5.1 切削加工高强度钢的主要难点及解决的途径 1922
5.2 高强度钢的车削 1925
5.3 高强度钢的铣削 1926
5.4 钻孔与铰孔 1927
5.5 高强度钢的螺纹加工 1929
6 钛合金的加工 1930
6.1 钛合金的车削 1930
6.2 钛合金的铣削 1932
6.3 钛合金的钻削 1933
6.4 钛合金的铰削 1935
6.5 钛合金螺纹加工 1936
6.6 钛合金拉削 1937
6.7 钛合金磨削 1937
7 热喷涂(焊)合金材料层的加工 1938
7.1 概述 1938
7.2 热喷涂(焊)合金层的车削 1939
8 高温合金的加工 1941
8.1 高温合金切削加工的主要难点 1941
7.3 热喷涂(焊)层的磨削 1941
8.2 高温合金的车削 1942
8.3 高温合金的铣削 1945
8.4 高温合金的钻削 1946
8.5 高温合金的铰削 1947
8.6 攻螺纹 1948
8.7 高温合金的磨削 1949
1.1 特种加工的定义 1951
1 特种加工概述 1951
1.2 特种加工的分类与代码 1951
第13章 特种加工与超精密加工 1951
1.3 几种常用特种加工方法的综合对比 1952
2 电物理加工 1954
2.1 电火花加工 1954
2.2 电子束加工 1964
2.3 离子束加工 1966
2.4 等离子加工 1967
2.5 激光加工 1968
2.6 超声波加工 1972
3 电化学加工 1976
3.1 电解加工 1976
3.2 电铸 1983
3.3 电化学抛光 1985
3.4 阳极机械切割 1988
4.1 化学加工的基本原理和应用 1989
4.2 化学铣切 1989
4 化学加工 1989
4.3 照相制版 1990
4.4 光刻 1991
5 复合加工 1992
5.1 电解磨削 1992
5.2 等离子体加热切削 1996
5.3 超声波振动切削 1998
6 水喷射加工与磨料流加工 2000
6.1 高压水切割 2000
6.2 磨料流加工 2002
7 超精密加工 2007
7.1 超精密加工的一般概念 2007
7.2 超精密切削 2008
7.3 超精密磨削 2012
7.4 超精密研磨 2013
7.5 超精密特种加工 2014
7.6 超精密加工应遵循的基本准则 2014
1.1 测量与检验的定义 2016
1 概述 2016
1.2 测量方法与计量器具的分类 2016
第14章 技术检验与测量 2016
2 光滑工件的检验与测量 2017
2.1 车间条件下的尺寸检验 2017
2.2 计量室内测量 2044
3 角度和锥度测量 2052
3.1 用角度量块测量 2052
3.2 用90°角尺测量 2054
3.3 用圆锥量规测量 2056
3.4 用正弦规测量 2057
3.5 用万能角度尺测量 2062
3.6 用圆球或圆柱测量 2063
3.7 用光学仪器测量 2066
4 形状与位置误差测量 2068
4.1 形状误差测量 2068
4.2 位置误差测量 2081
5 表面粗糙度的检测 2087
5.1 概述 2087
5.2 用比较法检查 2088
5.3 用轮廓法测量 2090
5.4 用干涉法测量 2091
5.5 用光切法测量 2092
5.6 用印模法测量 2094
6 螺纹与丝杠测量 2095
6.1 圆柱螺纹测量 2095
6.2 圆锥螺纹的测量 2104
6.3 丝杠测量 2107
7 齿轮测量 2108
7.1 渐开线圆柱齿轮检验组的选择 2108
7.2 渐开线圆柱齿轮的测量方法 2109
8 蜗杆、蜗轮测量 2138
8.1 蜗杆、蜗轮检验组及其选用 2138
8.2 蜗轮测量 2144
9 键与花键测量 2148
9.1 键与键槽的测量 2148
9.2 花键的测量 2150
10 特殊零件和尺寸的测量 2154
10.1 大尺寸测量 2154
10.2 微小尺寸测量 2158
10.4 高精度齿轮测量 2165
10.5 交点尺寸测量 2165
10.3 少齿数齿轮测量 2165
10.6 轮廓形状样板尺寸的测量 2168
10.7 凸轮的测量 2168
10.8 渐开线的测量 2169
10.9 非整形圆弧样板半径的测量 2170
10.10 滚柱法 2172
11 计量检测设备的质量保证要求 2173
11.1 计量检测设备的确认体系 2173
11.2 测量过程控制 2174
1 自动制造系统的基础技术 2176
1.1 数控加工与数控编程 2176
第15章 自动制造系统 2176
1.2 计算机控制在数控(NC)中的应用 2194
1.3 自适应控制机械加工系统 2200
2 计算机辅助工艺规程设计(CAPP) 2203
2.1 计算机辅助工艺规程设计的几种类型 2203
2.2 计算机辅助工艺规程设计的系统分析和系统设计 2204
3 柔性制造技术 2216
3.1 多品种生产对柔性制造技术的要求 2217
3.2 柔性制造技术的几种类型 2220
3.3 柔性制造系统 2223
4 计算机集成制造(CIM) 2226
4.1 计算机集成制造的基本概念 2226
4.2 计算机集成制造发展概况 2228
4.3 计算机集成制造系统(CIMS)的关键技术 2230
4.4 计算机集成制造系统(CIMS)的系统分析与设计 2235
5 自动制造系统的管理与控制 2257
5.1 概述 2257
5.2 自动制造系统中管理与控制的优化技术 2258
5.3 计算机辅助制造系统的管理 2259
5.4 计算机辅助质量控制(CAQC) 2262
1.1 装配方法的选用 2268
1 概述 2268
1.2 装配组织形式的确定 2268
第16章 装配 2268
2 零件的清洗与防锈 2269
1.4 我国机械产品装配中常出现的质量问题及解决措施 2269
2.1 清洗剂的选择 2269
1.3 装配的基本要求 2269
2.2 清洗方法的选用 2272
2.3 零件清洗后的防锈 2273
3 装配中常用连接方法及要求 2274
3.1 螺钉、螺栓连接 2274
3.2 销连接 2277
3.3 键连接 2282
3.4 过盈连接 2282
3.5 铆接 2288
3.6 粘接 2289
4 典型部件装配 2299
4.1 滚动轴承装配 2299
3.7 焊接 2299
4.2 滑动轴承装配 2305
4.3 齿轮及齿轮箱的装配 2311
4.4 链轮链条的装配 2317
4.5 制动器的装配 2317
4.6 联轴器的装配 2318
4.7 液压系统的装配 2319
4.8 密封件的装配 2322
4.9 电气系统装配 2327
5 平衡 2329
5.1 平衡的类型与范围 2329
5.2 校正不平衡质量的方法 2329
5.3 对组合旋转体的平衡 2329
5.4 静平衡 2329
5.5 动平衡 2331
6.1 总装的基本要求 2333
6.2 总装后的试验和检验 2333
6.3 总装后的清洗与防锈 2333
6 总装 2333
7.1 设计装配工艺规程的主要技术依据 2336
7.2 设计装配工艺规程的程序 2336
7 装配工艺规程设计 2336
7.3 手工装配工时定额和自动流水装配时间节拍的计算 2337
1 常用数学资料 2340
1.1 常用数学符号 2340
第17章 常用有关资料 2340
1.3 圆锥体各要素的计算 2341
1.4 外接圆直径与内切圆直径的关系 2341
1.2 1~20的阶乘值及其倒数、对数 2341
1.5 圆周等分长度计算 2342
1.6 圆的内接、外切多边形几何尺寸 2342
1.7 圆的弓形尺寸系数 2343
1.8 常用各种表面的面积计算 2345
1.9 常用几何体的表面面积及体积的计算 2346
1.10 展开长度的计算 2347
1.11 正多角形求圆计算 2348
1.12 基本运算公式 2349
1.13 连分数及其应用 2350
1.15 一般三角形的边角关系 2352
1.16 反三角函数的定义记号及主值区 2352
1.14 特殊角的三角函数 2352
1.18 用同角某三角函数表示其他三角函数 2353
1.19 三角函数的解法 2353
1.17 用α的三角函数表示(nπ/2±α)的三角函数 2353
1.20 三角恒等式 2354
2 常用希腊字母、物理系数和化学符号 2355
2.1 常用希腊字母 2355
2.3 常用金属材料弹性模量和泊松系数 2356
2.4 常用材料和物体的摩擦系数 2356
2.2 常用材料线膨胀系数 2356
2.5 常用固体材料的密度 2358
2.6 主要元素的化学符号、原子量和密度 2358
3.1 国际单位制(SI)的基本单位和辅助单位 2359
3.2 用SI基本单位和辅助单位表示的SI导出单位示例 2359
3 常用法定计量单位和相关单位间的换算 2359
3.4 由于人类健康与安全防护上的需要而确定的具有专门名称的SI导出单位 2360
3.5 用专门名称表示的SI导出单位示例 2360
3.3 具有专门名称的SI导出单位 2360
3.6 SI用的十进词头 2361
3.7 可与SI单位并用的我国法定计量单位 2361
3.8 具有专门名称的厘米克秒制(CGS)单位 2362
3.9 应淘汰的常用计量单位与符号 2362
3.10 不同单位制的基本单位和力学单位 2364
3.11 各种单位换算 2365
3.12 各种有关单位对照 2370
4 技术制图与机械制图 2371
4.1 图纸幅面尺寸 2371
4.2 图框格式及尺寸 2372
4.3 图纸的对中符号和方向符号 2373
4.4 图纸的剪切符号 2374
4.5 图纸分区 2374
4.6 米制参考分度 2375
4.7 图线 2375
4.8 字体 2376
4.9 比例 2377
4.10 尺寸标注 2377
4.11 尺寸简化画法 2379
4.12 螺纹及螺纹紧固件的画法 2381
4.13 滚动轴承的简化画法和示意画法的尺寸比例 2383
4.14 各种孔的标准注法 2384
4.15 尺寸公差注法 2385
4.16 螺纹的标注方法 2386
5.1 表面粗糙度符号和加工纹理方向符号 2387
5.2 表面粗糙度参数及其数值 2387
5 表面粗糙度 2387
5.3 表面光洁度参数值(1968年旧国标)与表面粗糙度参数值(1983年新国标)之间的过渡关系 2391
5.4 表面粗糙度的标注 2391
5.5 表面粗糙度与公差等级的关系 2395
5.6 常用工作表面的表面粗糙度数值的选择 2398
5.7 各种加工方法所能达到的工件表面粗糙度 2401
6 常用零件结构要素 2407
6.1 零件倒圆与导角 2407
6.2 滚花 2408
6.3 润滑槽 2408
6.4 球面半径 2410
6.5 砂轮越程槽 2411
6.6 中心孔 2412
6.7 锥斜度与锥(斜)角 2415
6.8 T形槽 2417
6.9 螺纹紧固件的末端及螺纹收尾 2421
6.10 粗牙螺栓、螺钉的拧入深度 2430
6.11 紧固件沉孔尺寸 2431
6.12 螺钉和螺栓通孔直径 2433
7.2 挂轮计算中用的近似分式 2435
7.1 车螺纹、蜗杆时的挂轮计算 2435
7.3 复式分度表 2435
7 挂轮计算 2435
7.4 用分度头分度铣齿计举例 2437
8 渐开线圆柱齿轮模数 2438
9 常用金属材料重量 2439
10.2 国际和国际组织标准代号 2441
10.1 国内标准代号 2441
10.3 各主要国家标准代号 2441
10 常用国内外标准代号 2441
10.4 国外主要协(学)会和其他组织标准代号 2442
10.5 国际区域标准代号 2442
参考文献 2443
- 《激光加工实训技能指导理实一体化教程 下》王秀军,徐永红主编;刘波,刘克生副主编 2017
- 《Maya 2018完全实战技术手册》来阳编著 2019
- 《先进激光加工技能实训》肖海兵主编 2019
- 《高等教育双机械基础课程系列教材 高等学校教材 机械设计课程设计手册 第5版》吴宗泽,罗圣国,高志,李威 2018
- 《慢性呼吸系统疾病物理治疗工作手册》(荷)瑞克·考斯林克(RikGosselink) 2020
- 《战略情报 情报人员、管理者和用户手册》(澳)唐·麦克道尔(Don McDowell)著 2019
- 《实用内科手册》黄清,阮浩航主编 2016
- 《基层医疗卫生机构安全用药手册》黎月玲,熊慧瑜 2019
- 《同仁眼科手册系列 同仁儿童眼病手册》付晶编 2018
- 《AutoCAD机械设计实例精解 2019中文版》北京兆迪科技有限公司编著 2019
- 《钒产业技术及应用》高峰,彭清静,华骏主编 2019
- 《现代水泥技术发展与应用论文集》天津水泥工业设计研究院有限公司编 2019
- 《异质性条件下技术创新最优市场结构研究 以中国高技术产业为例》千慧雄 2019
- 《Prometheus技术秘笈》百里燊 2019
- 《中央财政支持提升专业服务产业发展能力项目水利工程专业课程建设成果 设施农业工程技术》赵英编 2018
- 《药剂学实验操作技术》刘芳,高森主编 2019
- 《林下养蜂技术》罗文华,黄勇,刘佳霖主编 2017
- 《脱硝运行技术1000问》朱国宇编 2019
- 《催化剂制备过程技术》韩勇责任编辑;(中国)张继光 2019
- 《信息系统安全技术管理策略 信息安全经济学视角》赵柳榕著 2020