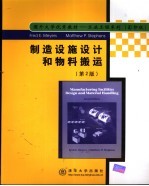
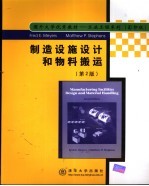
制造设施设计和物料搬运 第2版PDF电子书下载
- 电子书积分:14 积分如何计算积分?
- 作 者:FredE.Meyers,MatthewP.Stephens著
- 出 版 社:北京:清华大学出版社
- 出版年份:2002
- ISBN:7302056668
- 页数:415 页
THE IMPORTANCE OF MANUFACTURING FACILITIES DESIGN AND MATERIAL HANDLING 1
CHAPTER 1 Introduction to Manufacturing Facilities Design and Material Handling 1
LEAN THINKING AND LEAN MANUFACTURING 4
THE GOALS OF MANUFACTURING FACILITIES DESIGN AND MATERIAL HANDLING 4
THE MANUFACTURING FACILITIES DESIGN PROCEDURE 9
TYPES AND SOURCES OF MANUFACTURING FACILITIES DESIGN PROJECTS 11
COMPUTERS AND SIMULATION IN MANUFACTURING FACILITIES DESIGN 12
ISO 9000 and Facilities Planning 13
GLOSSARY OF MAJOR TERMS 14
QUESTIONS 16
CHAPTER 2 Sources of lnformation for Manufacturing Facilities Design 18
THE MARKETING DEPARTMENT 19
THE PRODUCT DESIGN DEPARTMENT 21
Inventory Policy 28
Lean Thinking and Muda as a Part of Management Policy 28
MANAGEMENT POLICY INFORMATION 28
Investment Policy 29
Starmp Schedule 29
Make or Buy Decisions 30
Organizational Relationships 30
Feasibility Studies 31
CONCLUSION 32
QUESTIONS 33
WHAT IS A TIME STANDARD? 34
CHAPTER 3 Time Study 34
IMPORTANCE AND USES OF TIME STUDY 37
1. How Many Machines Do We Need? 38
2. How Many People Should We Hire? 39
3. How Much Will Our Product Cost? 41
4. When Should We Start a Job, and How Much Work Can We Handle with the Equipment and People We Have? Or, How Do We Schedule and Load Machines, Work Centers, Departments, and Plants? 43
5. Determine the Assembly Line Balance, Determine the Conveyor Belt Speed, Load the Work Cells with the Correct Amount of Work,and Balance the Work Cells? 44
6. How Do We Measure Productivity? 44
8. How Can We Select the Best Method or Evaluate Cost Reduction Ideas? 46
7. How Can We Pay Our People for Outstanding Performance? 46
9. How Do You Evaluate New Equipment Purchases to Justify Their Expense? 48
TECHNIQUES OF TIME STUDY 48
10. How Do We Develop a Personnel Budget? 49
Predetermined Time Standards Systems 49
Stopwatch Time Study 52
Time Study Procedure and the Step-by-Step Form 52
Principles of Elemental Breakdown 57
Rating, Leveling, and Normalizing 61
ALLOWANCES 65
Types of Allowances 65
Methods of Applying Allowances 68
Work Sampling 71
Standard Data 72
Expert Opinion Time Standards and Historical Data 72
TIME STANDARDS FOR MANUFACTURING FACILITIES DESIGN 74
QUESTIONS 75
CHAPTER 4 Process Design 76
Route Sheets 77
FABRICATION: MAKING THE INDIVIDUAL PARTS 77
The Number of Machines Needed 80
WORK CELL LOAD CHART 82
Step-by-Step Procedure for Preparing a Work Cell Load Chart 86
ASSEMBLY AND PACKOUT PROCESS ANALYSIS 86
The Assembly Chart 87
Time Standards Are Required for Every Task 87
Paint Conveyor Speed 88
Plant Rate and Conveyor Speed 88
Assembly Line Balancing 90
STEP-BY-STEP PROCEDURE FOR COMPLETING THE ASSEMBLY LINE BALANCING FORM 94
CALCULATING THE EFFICIENCY OF THE ASSEMBLY LINE 100
Use of Computer Simulation 101
LAYOUT ORIENTATION 104
QUESTIONS 104
CHAPTER 5 Flow Analysis Techniques 106
FABRICATION OF INDIVIDUAL PARTS 109
String Diagram 110
Multi-Column Process Chart 112
From-To Chart 113
Process Chart 117
Step-by-Step Description for the Process Chart 117
TOTAL PLANT FLOW 121
Flow Diagrams 121
The Operations Chart 124
Step-by-Step Procedure for Developing a Flow Diagram 124
Step-by-Step Procedures for Preparing an Operations Chart 126
Flow Process Chart 130
Step-by-Step Procedure for Preparing a Flow Process Chart 130
COMPUTER-AIDED FLOW DESIGN AND ANALYSIS 130
CONCLUSION 133
QUESTIONS 133
CHAPTER 6 Activity Relationship Analysis 137
THE ACTIVITY RELATIONSHIP DIAGRAM 138
Determining the Relationship Code 140
WORKSHEET 141
DIMENSIONLESS BLOCK DIAGRAM 142
FLOW ANALYSIS 144
COMPUTER-GENERATED ACTIVITY RELATIONSHIP CHART 146
QUESTIONS 150
CHAPTER 7 Ergonomics and Workstation Design Space Requirement 152
WORKSTATION DESIGN 152
ERGONOMICS AND THE PRINCIPLES OF MOTION ECONOMY 158
Principle 1: Hand Motions 159
Principle 2: Basic Motion Types 160
Principle 3: Location of Parts and Tools 160
Principle 4: Free the Hands from as Much Work as Possible 160
Principle 5: Use Gravity 163
Principle 6: Operator Safety and Health Considerations 165
SPACE DETERMINATION 165
QUESTIONS 169
The Advantages and Disadvantages of Centralized Receiving and Shipping 170
CHAPTER 8 Auxiliary Services Requirement Space 170
RECEIVING AND SHIPPING 170
The Trucking Industry s Effect on Shipping and Receiving 171
The Functions of a Receiving Department 171
Facilities Required for Receiving Departments 173
Space Requirements for the Receiving Department 175
The Functions of a Shipping Department 176
Space Requirements for Shipping Departments 179
STORAGE 180
Just-in-Time Inventories 182
Maximizing the Use of the Cubic Space 182
Provide Immediate Access to Everything 184
Provide Safekeeping 191
WAREHOUSING 192
Warehouse Design Criteria 193
The Functions of a Warehouse 194
Procedure for Sales Analysis of ABC Inventory 196
ABC Inventory Layout of a Hand Tool Manufacturing Company s Warehouse 198
Warehouse Space Determination 200
Warehouse Equipment 201
Conclusion 203
MAINTENANCE AND TOOL ROOM 203
UTILITIES 204
QUESTIONS 205
CHAPTER 9 Employee Services—Space Requirements 207
PARKING LOTS 208
EMPLOYEE ENTRANCES 209
LOCKER ROOMS 211
TOILETS AND RESTROOMS 212
LUNCH ROOMS 215
RECREATION 217
DRINKING FOUNTAINS 218
AISLES 218
MEDICAL FACILITIES 219
MISCELLANEOUS EMPLOYEE SERVICES 220
BREAK AREAS AND LOUNGES 220
QUESTIONS 222
CHAPTER 10 Material Handling 223
COST JUSTIFICATION 224
Sample Material Handling Cost Problem 224
GOALS OF MATERIAL HANDLING 225
THE 20 PRINCIPLES OF MATERIAL HANDLING 226
1. The Planning Principle 226
2. The Systems Principle 227
3. The Material Flow Principle 228
4. The Work Simplification Principle 228
5. Use Gravity 229
6. Maximize the Building Code 229
7. Unit Size Principle 230
8. Mechanization Principle 231
9. Automation Principle 231
10. Equipment Selection Principle 231
11. The Standardization Principle 233
12. The Adaptability Principle 234
13. The Dead Weight Principle 234
14. The Utilization Principle 234
15. The Maintenance Principle 234
16. The Obsolescence Principle 235
17. The Control Principle 235
18. The Capacity Principle 235
20. The Safety Principle 236
19. The Performance Principle 236
THE MATERIAL HANDLING PROBLEM-SOLVING PROCEDURE 237
MATERIAL HANDLING CHECKLIST 238
QUESTIONS 241
CHAPTER 11 Material Handling Equipment 243
RECEIVING AND SHIPPING 244
Receiving and Shipping Docks 244
Dock Equipment 246
Fork Trucks 250
Moving Equipment 250
Telescopic Conveyor 256
Bridge Cranes 256
Weight Scale 257
Systems Required on Shipping and Receiving Docks 257
STORES 260
Storage Units 260
Stores Mobile Equipment 262
Systems Required for Stores Department 267
Tubs and Baskets 269
FABRICATION 269
Shop Containers 269
Workstation Material Handling Devices 273
Manipulators and Lifting Devices 273
Mobile Fabrication Equipment 284
ASSEMBLY AND PAINT 289
Belt Conveyors 291
Slat Conveyor 292
Powered Roller Conveyor 292
Car-Type Conveyor 292
Tow Conveyor 294
Overhead Trolley Conveyor 294
Power and Free Conveyor 295
PACKOUT 298
Box Formers 298
Automatic Taping, Gluing, and Stapling 298
Palletizers 298
Pick and Place Robots 300
Banding 300
Stretch Wrap 300
WAREHOUSING 302
Picking Carts 302
Gravity Flow Bins 303
Tractor-Trailer Picking Cart 303
Rotary Conveyor Bins 305
Clamp Trucks 305
Vertical Warehouse and Picking Cars 307
Packing Station 307
Shipping Containers 308
BULK MATERIAL HANDLING 309
Bulk Material Conveyors 310
COMPUTER-INTEGRATED MATERIAL HANDLING SYSTEMS 313
Cross-Docking and Flow-Through 314
QUESTIONS 316
CHAPTER 12 Office Layout Techniques and Space Requirements 317
GOALS OF OFFICE LAYOUT DESIGN 317
TYPES OF OFFICE SPACE 318
Supervisors Offices 319
Open Office Space 320
Conventional Offices 322
The Modem Office 323
SPECIAL REQUIREMENTS AND CONSIDERATIONS OF SOME OFFICES 325
THE TECHNIQUES OF OFFICE LAYOUT 329
The Organizational Chart 330
Flowchart 331
Communications Force Diagram 332
Activity Relationship Diagram 335
Activity Worksheet 335
Dimensionless Block Diagram 336
Office Space Determination 338
Detailed Master Layout 339
QUESTIONS 341
CHAPTER 13 Area Allocation 342
SPACE REQUIREMENTS PLANNING: STEP ONE 342
BUILDING SIZE DETERMINATION 345
DIMENSIONLESS BLOCK DIAGRAM 345
AREA ALLOCATION PROCEDURE 345
OFFICE AREA ALLOCATION 347
QUESTIONS 351
PLOT PLAN 352
CHAPTER 14 Facilities Design—The Layout 352
Plant Layout Methods 355
MASTER PLAN 355
Advanced Computer Systems 361
PLANT LAYOUT PROCEDURE—TOOLBOX PLANT 366
Office Layout for Toolbox Plant 368
EVALUATION 368
QUESTIONS 373
INTRODUCTION 374
CHAPTER 15 Application of Computer Simulation and Modeling 374
DEFINING COMPUTER SIMULATION 375
ADVANTAGES AND DISADVANTAGES OF SIMULATION 376
SIMULATION IN FACILITIES PLANNING 376
HOW SIMULATION WORKS 377
AN OVERVIEW OF LAYOUT AND SIMULATION SOFTWARE 379
COMPUTER-AIDED LAYOUT DESIGN 379
Computer-Assisted Layout Performance Analysis 381
Simulation in Manufacturing 386
CASE STUDIES 386
Waste Handling and Simulation 387
Simulation and Health Care 387
QUESTIONS 388
CHAPTER 16 Selling the Layout 389
THE PROJECT REPORT 389
THE PRESENTATION 392
ADJUSTMENTS 392
APPROVAL 392
Sourcing 393
THE REST OF THE PROJECT 393
Installation 394
Engineering Plot 394
Production Start 394
Debugging and Follow-Up 395
Conclusion 395
Answers 397
Index 411
- 《中国制造业绿色供应链发展研究报告》中国电子信息产业发展研究院 2019
- 《中央财政支持提升专业服务产业发展能力项目水利工程专业课程建设成果 设施农业工程技术》赵英编 2018
- 《指向核心素养 北京十一学校名师教学设计 英语 七年级 上 配人教版》周志英总主编 2019
- 《设计十六日 国内外美术院校报考攻略》沈海泯著 2018
- 《计算机辅助平面设计》吴轶博主编 2019
- 《高校转型发展系列教材 素描基础与设计》施猛责任编辑;(中国)魏伏一,徐红 2019
- 《景观艺术设计》林春水,马俊 2019
- 《高等教育双机械基础课程系列教材 高等学校教材 机械设计课程设计手册 第5版》吴宗泽,罗圣国,高志,李威 2018
- 《指向核心素养 北京十一学校名师教学设计 英语 九年级 上 配人教版》周志英总主编 2019
- 《Cinema 4D电商美工与视觉设计案例教程》樊斌 2019
- 《大学计算机实验指导及习题解答》曹成志,宋长龙 2019
- 《指向核心素养 北京十一学校名师教学设计 英语 七年级 上 配人教版》周志英总主编 2019
- 《大学生心理健康与人生发展》王琳责任编辑;(中国)肖宇 2019
- 《大学英语四级考试全真试题 标准模拟 四级》汪开虎主编 2012
- 《大学英语教学的跨文化交际视角研究与创新发展》许丽云,刘枫,尚利明著 2020
- 《北京生态环境保护》《北京环境保护丛书》编委会编著 2018
- 《复旦大学新闻学院教授学术丛书 新闻实务随想录》刘海贵 2019
- 《大学英语综合教程 1》王佃春,骆敏主编 2015
- 《大学物理简明教程 下 第2版》施卫主编 2020
- 《指向核心素养 北京十一学校名师教学设计 英语 九年级 上 配人教版》周志英总主编 2019