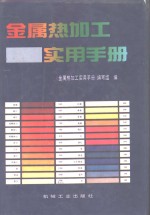
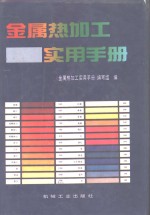
金属热加工实用手册PDF电子书下载
- 电子书积分:28 积分如何计算积分?
- 作 者:《金属热加工实用手册》编写组编
- 出 版 社:北京:机械工业出版社
- 出版年份:1996
- ISBN:7111050096
- 页数:1139 页
第1章 基础知识及通用资料 3
1.1 常用金属材料分类及其牌号 3
1.1.1 铸铁和钢 3
1.分类 3
2.牌号 3
第1篇 热加工工艺 3
3.化学成分 5
1.1.2 非铁金属 15
1.概述 15
2.铝及铝合金 16
3.铜及铜合金 20
5.镁合金 23
4.钛及钛合金 23
6.锌、铅、锡合金 25
1.2 合金相图 25
1.2.1 常用铁基二元合金相图 27
1.2.2 常用铝基二元合金相图 27
1.2.3 常用铜基二元合金相图 27
1.3 常用金属的显微组织 30
1.3.1 钢和铸铁的显微组织 30
1.碳钢和白口铸铁的平衡组织 30
2.非白口铸铁的显微组织 30
3.钢的不平衡相变和不平衡组织 32
4.TTT曲线与CCT曲线 32
3.5 模锻后续工序 33
1.3.2 铝合金及铜合金的显微组织 34
5.合金元素在钢铁材料中的作用 34
1.铝合金的显微组织 34
2.常用铜、铝及其合金的物理性能 46
1.铸造性能 46
1.4.3 金属材料热加工工艺性能的涵义 46
2.铜合金的显微组织 46
1.常用钢材的物理性能 46
1.4.2 常用金属材料的物理性能 46
1.4.1 元素的物理性能 46
1.4 常用材料数据及热加工工程术语 46
2.可锻性 63
3.可焊性 63
4.热处理工艺性能 67
1.5 金属热加工常用标准索引 67
1.5.1 常用铸造标准索引 67
1.5.2 常用锻压标准索引 69
1.5.3 常用焊接标准索引 75
1.5.4 常用热处理标准索引 77
参考文献 78
第2章 铸造工艺 80
2.1 造型(芯)用型(芯)砂的配制 80
2.1.1 粘土砂 80
1.铸铁件用粘土砂 80
2.铸钢件用粘土砂 80
3.非铁合金用粘土砂 82
2.1.2 水玻璃系砂 82
1.水玻璃砂 82
2.1.4 石灰石砂 83
2.1.5 油砂及合脂砂 83
2.1.3 双快水泥自硬砂 83
2.硅酸二钙-水玻璃自硬砂 83
2.1.7 涂料及型芯修补材料 85
1.涂料的分类及分级 85
1.壳芯用砂 85
2.1.6 树脂砂 85
2.热芯盒砂 85
3.冷硬呋喃树脂砂 85
2.涂料的配比 86
3.型(芯)修补膏和胶合材料 86
2.1.8 型(芯)砂及涂料的混制方法 87
1.一般型(芯)砂的混制方法 87
1.对冲天炉操作的总要求 88
2.2.1 冲天炉的基本操作 88
2.2 铸铁的熔炼 88
2.1.9 型(芯)砂的烘干规范 88
2.涂料的混制 88
2.冲天炉熔炼的基本操作 89
2.2.2 炉况判断 90
1.风口观察 90
2.加料口观察 90
3.出渣口观察 90
4.炉渣颜色观察 90
5.铁液温度观察 90
6.铁液氧化程度观察 90
7.铁液成分观察 90
2.2.3 铁液温度的控制 91
1.焦炭 91
3.供风 92
2.2.4 常见元素在冲天炉内的变化 92
2.金属炉料和熔剂 92
3.计算实例 93
2.2.5 配料计算 93
1.配料原则 93
2.配料计算步骤 93
2.2.6 炉前合金加入量计算 94
2.2.7 灰铸铁的熔制 94
1.化学成分的控制 94
2.孕育处理 95
2.2.8 可锻铸铁的熔制 96
1.化学成分的控制 96
2.孕育处理 96
3.国内铁素体可锻铸铁生产实例 97
2.2.9 球墨铸铁的熔制 97
1.球墨铸铁对原铁液的要求 97
2.球化处理与孕育处理 97
3.蠕化处理与孕育处理 100
2.2.10 蠕墨铸铁件的生产 100
2.蠕化剂 100
1.蠕铁的化学成分 100
4.我国蠕墨铸铁的牌号和力学性能 102
2.2.11 耐热铸铁 102
2.2.12 耐腐蚀铸铁 103
2.2.13 抗磨白口铸铁 103
2.3 铸钢的熔炼 104
2.3.1 电弧炉炼钢工艺 104
3.感应电炉炼钢时合金元素的加入 106
1.炉料的组成及准备 106
2.4 非铁合金的熔炼 106
2.4.1 炉料 106
2.碱性感应电炉炼钢工艺 106
2.3.2 感应电炉炼钢工艺 106
1.酸性电炉炼钢工艺 106
2.中间合金的熔制 107
2.4.2 铸造铝合金的熔炼 108
1.铝合金的熔炼工艺过程 108
2.铝合金常用熔剂 108
3.铝合金常用的除气精炼方法 108
4.铝硅合金常用的变质剂及处理工艺 109
5.铝合金熔炼工艺举例 110
2.4.3 铜合金熔炼 110
1.铜合金的精炼 110
2.铜合金熔炼工艺举例 111
2.5.1 铸造工艺方案的确定 112
1.造型、造芯方法的选择 112
2.5 铸造工艺设计 112
2.浇注位置的选择 114
3.分型面的确定 115
4.砂箱中铸件数目的确定 115
2.5.2 铸造工艺图及工艺卡 123
1.铸造工艺图 123
2.工艺卡举例 123
2.5.3 主要工艺参数的选择 124
1.铸件精度等级、尺寸与重量允许误差的确定 124
2.铸造收缩率 124
3.机械加工余量和铸孔与非铸孔的确定 126
4.起模斜度的确定 129
5.工艺补正量的确定 129
6.分型负数的确定 130
7.铸件畸变补偿量 130
8.砂芯负数 131
9.非加工面壁厚的负余量 132
2.5.4 砂芯设计 132
1.砂芯数量的确定 132
2.芯头设计 133
2.5.5 浇注系统的设计 135
1.浇注系统的选择 135
2.金属液引注位置的确定 139
3.浇注系统各部分尺寸的确定 139
3.冒口的位置 144
4.铸钢件冒口尺寸的确定 144
1.冒口的种类 144
2.5.6 冒口冷铁的设计 144
2.冒口的形状 144
5.铸铁件冒口尺寸的确定 148
6.冷铁 148
7.铸肋 148
2.6 特种铸造工艺 154
2.6.1 熔模铸造 154
1.压型制造 154
2.熔模(易熔模样)制造 156
3.模壳的制造 156
1.准备模样 157
3.陶瓷浆的制备 157
2.砂型制备 157
4.失蜡工艺 157
6.浇注 157
5.熔烧工艺 157
2.6.2 陶瓷型铸造 157
4.陶瓷浆的浇灌 158
5.脱模与焙烧 158
2.6.3 金属型铸造 158
1.金属型的设计 158
2.金属型铸造工艺 160
2.6.4 压力铸造 161
1.压铸机 161
2.压铸型 162
3.压铸工艺 162
2.6.5 低压铸造 165
1.低压铸造设备 165
2.低压铸造工艺 165
2.挤压铸型设计 166
2.6.6 挤压铸造 166
1.挤压铸造分类 166
3.挤压铸造工艺实例 168
4.复合材料的挤压铸造 171
5.半固态挤压铸造 171
2.6.7 离心铸造 171
1.离心机的种类 171
2.转速的稳定 173
3.离心铸造用金属型 173
4.离心铸造用涂料 173
5.双金属离心铸造 173
6.离心铸管 175
2.6.8 连续铸造 176
1.半连续铸管 176
3.连续铸钢 178
2.连铸铝杆 178
2.7 铸造工艺材料 180
2.7.1 造型材料 180
1.铸造用原砂 180
2.粘结剂 183
3.型(芯)砂辅助材料 184
2.7.2 冲天炉熔炼用原辅材料 185
1.焦炭 185
2.牛铁 185
3.铁合金 185
4.非铁合金金属材料 187
1.铝合金用熔剂 188
2.7.4 非铁合金添加剂 188
2.蠕化剂 188
1.球化剂 188
2.7.3 铸铁添加剂 188
3.孕育剂 188
2.铜合金用熔剂 189
参考文献 189
1.常见下料方法及特点 191
2.材料工艺消耗定额(Gc) 191
第3章 锻压工艺 191
3.1.1 坯料的准备 191
3.1 锻前准备 191
3.剪切坯料的相关因素 194
3.1.2 坯料的加热 195
1.术语及说明 195
2.常见金属材料的锻造温度范围 195
3.加热时间 195
4.加热规范 202
3.2 自由锻 202
3.2.1 自由锻的分类及作用 202
3.2.2 中小型自由锻件常用锻造成形工序 202
3.2.3 自由锻工艺规程的制定 211
1.锻件图设计 211
2.确定毛坯的重量与尺寸 221
3.制订变形工艺与锻比 222
4.选择锻造设备规格 223
5.锻件图格式 224
6.锻件的质量 224
7.高合金钢的常见锻造方法 227
8.中小型水压机所需的基本工具 233
3.3 模锻 234
3.3.1 术语 234
3.3.2 常见模锻件的设计 234
1.钢质热模锻件的工艺结构要素 235
2.工艺结构要素的确定原则 235
3.锻件尺寸标准及测量 240
4.模锻件的公差及机械加工余量 240
5.锻件图(冷锻件图)的制订 250
6.锻件图实例 250
3.3.3 模锻工艺过程设计与计算 261
3.制坯模膛设计 269
1.终锻模膛设计 269
2.预锻模膛设计 269
3.3.4 锤模锻锻模的设计 269
4.模膛布置 276
5.锁扣的设计 276
6.模块尺寸与重量的确定 282
7.模块规格及验收 282
8.锻模的其他结构及加工 282
9.模锻锤用镶块模结构特点 285
10.其他要求 289
3.3.5 常见胎模锻锻件的设计 289
1.胎模锻锻件设计特点 289
2.钢质胎模锻锻件的加工余量及公差 289
4.变形方式的选择 295
6.自由锻锤上固定模模锻 295
5.常见胎模锻造成形工艺过程 295
3.胎模锻设备规格(吨位)的选择 295
3.3.6 胎模设计 300
1.摔模设计 300
2.扣模设计 300
3.套模设计 300
4.合模设计 304
5.漏模设计 308
6.实例 310
7.固定模模具设计 312
3.4 螺旋压力机上模锻工艺及模具设计特点 317
3.4.1 锻件的分类及特点 317
3.4.2 螺旋压力机模锻锻件成形工艺特点 319
1.螺旋压力机规格的选择原则 319
2.顶镦件成形工艺特点 319
1.点焊机及凸焊机 320
3.无飞边模锻锻件成形工艺特点 320
4.开式模锻件成形工艺特点 321
5.组合凹模锻造成形工艺特点 321
6.精锻件成形工艺特点 321
1.螺旋压力机常见开式锻模及模座设计特点 322
2.模座—模块的紧固方式及零件 331
3.无飞边闭式模锻锻模设计特点 332
4.模具设计实例 333
3.5.1 切边与冲孔 337
1.切边、冲孔工艺及模具类型选择原则 337
2.切边与冲孔模具设计 337
3.4.3 螺旋压力机模锻模具设计特点 342
1.校正的分类与用途 354
2.校正模结构特点 354
3.5.2 校正 354
3.凸、凹模材料及热处理硬度 354
1.精压件图与精压毛坯图的设计 356
3.5.3 精压 356
2.精压变形工艺特点 357
3.精压模具设计特点 358
4.精压模结构示例 360
3.6 挤压工艺与模具设计 362
3.6.1 挤压用材料及备料特点 362
3.6.2 挤压件设计要点 364
1.常见挤压件的工艺结构要素 364
2.挤压件精度 364
3.6.3 冷挤压工艺特点 368
1.冷挤压的变形程度与许用变形程度 368
2.冷挤压压力的估算 368
3.冷挤压成形工艺实例 369
3.6.4 挤压模具设计特点 371
2.挤压模的卸料装置 371
1.挤压模工作部分结构及尺寸设计 371
3.挤压模的导向装置 376
3.6.5 冷挤压模具结构示例 376
3.7 冲裁 382
3.7.1 概述 382
3.7.2 冲裁件的工艺件 383
1.冲裁件的精度和表面粗糙度 383
2.冲裁件的结构工艺性 383
3.7.3 冲裁件排样与搭边 385
1.材料利用率 385
2.排样方法 386
3.搭边 386
3.7.4 冲裁间隙 388
1.凸、凹模刃口尺寸计算原则 390
2.凸、凹模刃口尺寸计算 390
3.7.5 冲裁模凸、凹模刃口尺寸计算 390
5.红外线分析仪 390
3.7.6 冲裁力、卸料力、推(顶)料力计算 392
1.冲裁力的计算 392
2.推料力、顶料力、卸料力的计算 393
3.压力机吨位的选择 394
3.7.7 冲裁模的基本形式与结构 394
1.单工序冲裁模 394
2.复合模 396
3.连续模 398
3.7.8 冲裁模主要部件与零件的结构 401
1.凸模设计 401
2.凹模设计 405
3.定位装置 409
5.出件装置 414
4.卸料装置 414
6.导向装置 417
7.冲模零件用材料 418
3.7.9 压力中心的确定 420
3.7.10 硬质合金模具 421
1.工艺设计的要求 421
2.模具结构特点 421
3.7.11 提高冲裁件质量和精度的工艺方法 424
1.提高冲裁件质量的冲压工艺方法 424
2.整修 425
2.最小弯曲半径 427
3.弯曲件形状及尺寸要求 427
1.弯曲线的方向 427
3.8.1 弯曲件的工艺性 427
3.8 弯曲 427
3.7.12 冲模的闭合高度 427
4.弯曲件的精度 429
5.弯曲件尺寸标注 429
1.中性层位置 430
3.8.2 弯曲件坯料尺寸的计算 430
2.弯曲件坯料尺寸计算 431
3.8.3 弯曲力的计算 435
1.自由弯曲力 435
2.校正弯曲力 435
3.顶件力或压料力 436
4.压力机压力的确定 436
3.8.4 弯曲件的回弹 436
1.相对弯曲半径r/t较大的工件 436
2.相对弯曲半径r/t较小的工作 436
3.8.5 弯曲模工作部分尺寸计算 438
1.弯曲凸、凹模的间隙计算 438
2.凸、凹模结构尺寸确定 439
1.弯曲工序安排 441
2.弯曲模的结构设计 441
3.8.6 弯曲模结构设计 441
3.8.7 聚氨酯弯曲模 445
1.聚氨酯橡胶弯曲模的设计 447
3.8.8 斜楔计算 448
1.楔块的尺寸、程度计算 448
2.聚氨酯弯曲模结构 448
3.拉深件的尺寸标注 450
1.拉深件的结构工艺性 450
1.坯料尺寸的计算 450
3.9.2 圆筒形(无凸缘)拉深件的工艺计算 450
2.拉深件的尺寸精度 450
3.9.1 拉深件的工艺性 450
3.9 拉深 450
3.斜楔的结构 450
2.楔块的受力状态 450
2.拉深系数及拉深次数的决定 452
3.9.3 带凸缘圆筒形拉深件的工艺计算 454
1.坯料尺寸的计算 454
2.拉深系数及拉深次数的确定 455
1.矩(方)形件的坯料尺寸计算 457
3.9.4 矩形(或正方形)件拉深工艺计算 457
2.矩(方)形件的拉深系数、拉深次数及工序间尺寸的计算 459
3.9.5 复杂旋转体曲面工件的拉深 462
1.复杂旋转体拉深件坯料尺寸的计算 462
2.阶梯形件的拉深工艺 463
3.锥形件的拉深工艺 463
4.半球形件的拉深工艺 465
5.抛物线形件的拉深工艺 465
3.9.6 拉深模的凸、凹模设计 465
1.拉深模的凸、凹模圆角半径 465
2.拉深模的凸、凹模结构 467
3.拉深模的凸、凹模间隙 467
4.凸、凹模工作部分尺寸计算 468
3.压边圈的类型 470
3.9.7 压边圈的应用及其类型 470
1.采用压边圈的条件 470
2.压边装置的类型 470
3.9.8 拉深模结构 471
1.首次拉深模 471
4.压边力的计算 471
2.后续各次拉深模 472
3.9.9 其他拉深方法 476
1.反拉深 476
2.变薄拉深 476
3.带料连续拉深 478
4.软模拉深 478
2.退火 481
2.压机吨位的选择 482
1.拉深力 482
3.9.10 拉深力、拉深功及压机的选择 482
3.拉深功 483
3.9.11 切边及切边模 485
1.切边方法 485
2. 切边模 485
1.润滑 487
3.9.12 拉深的辅助工序 487
3.酸洗 489
3.10 成形工艺 490
3.10.1 翻孔和翻边 490
1.翻孔 490
2.翻边 491
3.变薄翻孔 492
3.10.2 胀形 493
1.胀形系数 494
2.胀形坯料计算 496
3.胀形力计算 497
4.胀形模 497
3.10.3 缩口 498
参考文献 501
3.T型(十字)接头 502
2.搭接接头 502
第4篇 焊接工艺 502
4.1.1 焊接接头形式 502
4.1 接头型式及接头强度 502
1.对接接头 502
4.角接接头 503
5.端接接头 503
4.1.2 焊接接头在图纸上的表示方法 503
1.焊缝符号与焊接方法代号 503
2.焊接接头在图纸上的表示方法 508
2.接头强度 509
1.焊接接头设计原则 509
4.1.3 接头设计 509
4.2 装配焊接工艺 512
4.2.1 工艺试验 512
1.材质复验 512
2.焊接工艺评定 512
3.焊接方法选择 514
3.定位焊 516
4.2.2 焊接结构装配-焊接工艺 516
2.工艺文件 516
1.产品结构工艺性审查 516
4.常用的焊接装配胎夹具 518
5.装配-焊接工艺 518
4.2.3 焊缝施焊方式 520
1.焊缝截面上的施焊方式 520
2.焊缝长度上的施焊方式 520
4.2.4 焊接材料消耗 520
4.3 焊接结构的备料工艺 522
4.3.1 钢板及型材的矫正 522
2.切割 523
1.剪切 523
4.3.3 钢材的剪切及切割 523
1.机械法 523
4.3.2 钢材的表面处理 523
2.化学法 523
4.3.5 封头、弯曲件、弯边、滚圆加工 524
1.封头加工 524
4.3.4 坡口制备 524
2.弯曲件加工 525
4.4 焊接畸变控制及矫正 525
4.4.1 焊接畸变控制 525
1.焊接畸变类型 525
2.焊接畸变的估算 527
3.控制焊接畸变的措施 529
4.4.2 焊接畸变的矫正 533
1.机械矫正法 533
4.4.3 焊接残余内应力的调节 534
1.设计措施 534
3.电磁锤法 534
2.火焰矫正法 534
2.工艺措施 535
3.焊后消除残余内应力的方法 535
4.5 焊接工艺制度 535
4.5.1 焊接材料的选用 535
1.焊条 535
2.焊丝 541
3.焊剂 543
4.焊接用气体 544
5.钎料和钎剂 544
6.焊粉 546
4.5.2 焊接工艺参数和工艺要点 548
1.手弧焊 548
2.埋弧焊 549
3.二氧化碳气体保护焊 550
4.氩弧焊 550
6.电阻焊 553
5.气焊 553
7.钎焊 554
4.5.3 焊前预热温度和加热方法的选择 555
4.5.4 层间温度的控制 555
4.5.5 后热和焊后热处理 555
4.5.6 焊接裂纹及气孔控制 555
4.6 常用金属材料的焊接工艺 555
4.6.1 低碳钢的焊接 555
1.低碳钢的焊接性 555
2.低碳钢焊接工艺要点 555
4.6.2 中碳钢和高碳钢的焊接 556
1.中碳钢焊接工艺要点 556
2.普通低合金结构钢的焊接工艺要点 557
1.普通低合金结构钢的焊接性 557
4.6.3 普通低合金结构钢的焊接 557
2.高碳钢的焊接 557
4.6.4 低碳合金结构钢的焊接 560
1.低碳合金结构钢的焊接性 560
2.低碳合金结构钢焊接工艺要点 560
4.6.5 中碳合金结构钢的焊接 561
1.中碳合金结构钢的焊接性 561
2.中碳合金结构钢的焊接工艺要点 561
4.6.6 铬钼耐热钢的焊接 562
1.低合金珠光体耐热钢的焊接 562
2.中合金耐热钢的焊接 563
4.6.7 马氏体不锈钢的焊接 564
1.马氏体不锈钢的焊接性 564
2.马氏体不锈钢焊接工艺要点 564
2.奥氏体不锈钢焊接工艺要点 565
1.奥氏体不锈钢的焊接性 565
4.6.9 奥氏体不锈钢的焊接 565
2.铁素体不锈钢的焊接工艺要点 565
4.6.8 铁素体不锈钢的焊接 565
1.铁素体不锈钢的焊接性 565
4.6.10 异种钢的焊接 566
1.珠光体钢与奥氏体钢的焊接 566
2.不锈钢复合板的焊接 567
4.6.11 铸铁的焊接 569
1.灰铸铁的焊接 569
2.球墨铸铁的焊接 571
4.6.12 铝及其合金的焊接 571
1.铝及铝合金的焊接性 571
2.铝及铝合金焊接工艺要点 571
4.6.13 铜及铜合金的焊接 574
1.铜及铜合金的焊接性 574
2.铜及铜合金焊接工艺要点 574
3.堆焊工艺要点 577
1.堆焊材料的选择 577
4.6.14 堆焊 577
2.堆焊方法的选择 577
参考文献 578
第5章 热处理工艺 579
5.1 钢和铸铁的退火与正火 579
5.1.1 钢制工件退火与正火的目的与应用 579
1.退火 579
2.正火 579
1.加热温度 581
2.加热速度及透烧保温时间 581
5.1.2 钢的退火和正火工艺 581
5.1.3 铸铁的退火与正火 582
1.可锻铸铁件的退火 582
2.球墨铸铁的退火 582
3.灰铸铁及球墨铸铁的正火 582
3.临界直径测定法 586
2.端淬法及端淬曲线 586
1.淬透性的含义 586
4.铸铁件的去应力退火 586
5.2.1 钢的淬透性 586
5.2 钢的淬火 586
5.2.2 淬火介质 587
5.2.3 淬火加热 590
1.加热前的准备 590
2.加热温度 590
3.保温时间 590
5.2.4 淬火方法 598
1.单介质淬火 598
2.双介质淬火 598
3.马氏体分级淬火 598
4.贝氏体等温淬火 599
5.深冷处理 599
5.2.6 球墨铸铁的等温淬火 600
5.锻造余热淬火 600
1.完全奥氏体化等温淬火 600
2.亚共析钢高温加热淬火 600
5.2.5 其他淬火方法 600
1.亚共析钢亚温淬火 600
4.循环快速加热淬火 600
3.高碳钢低温、快速、短时加热淬火 600
3.注意事项 601
5.3 钢的回火 601
5.3.1 回火温度与钢回火后的力学性能 601
5.3.2 回火工艺 601
1.加热温度 601
2.部分奥氏体化等温淬火的工艺参数 601
3.注意事项 601
2.回火时间 601
5.4 化学热处理 608
5.4.1 渗碳 608
1.固体渗碳 608
2.液体渗碳 610
3.气体渗碳 611
4.真空渗碳 615
5.离子渗碳 615
7.渗碳后的淬火与回火 616
6.非渗碳面的防护 616
5.4.2 渗氮 617
1.特点 617
2.气体渗氮 617
3.离子渗氮 621
4.抗蚀渗氮 622
5.4.3 碳氮共渗 623
1.气体碳氮共渗 623
2.液体碳氮共渗 623
4.渗层厚度 624
3.液体(熔盐)渗硼渗剂及工艺 624
2.固体(粉末)渗硼(装箱渗)渗剂与工艺 624
1.特点 624
2.工艺 624
5.4.4 氮碳共渗 624
5.4.5 渗硼 624
1.渗剂 624
5.渗后热处理 625
5.4.7 TiC沉积 626
1.特点 626
5.4.6 渗硫及硫氮碳共渗 626
2.硫氮碳共渗 626
1.渗硫 626
2.渗剂与工艺 627
3.沉积层的硬度 627
5.4.8 化学沉积Ni-P合金 627
1.特点 627
2.沉积技术 627
3.晶化处理 627
5.5 表面热处理 628
5.5.1 感应加热表面淬火 628
1.基础知识 628
2.高中频感应器 628
3.感应加热表面淬火工艺 631
3.加热装置 632
4.烧嘴 632
2.火焰加热表面淬火工艺 632
1.热源 632
5.5.2 火焰加热表面淬火 632
5.5.3 激光热处理 633
5.5.4 电接触加热表面淬火 634
5.5.5 电火花表面强化 634
5.6 非铁金属的热处理 636
1.加工铝合金的热处理 636
5.6.1 铝合金的热处理 636
2.铸造铝合金的热处理 639
5.铜合金的固溶热处理及时效 640
4.中间退火与最终再结晶退火 640
3.去应力退火 640
2.均匀化退火 640
1.铜合金热处理类型 640
5.6.2 铜合金的热处理 640
6.铜合金热处理注意事项 643
1.钛合金 644
2.钛合金的热处理工艺 644
5.6.3 钛合金的热处理 644
5.6.4 镁合金的热处理 647
1.镁合金的化学成分及力学性能 647
2.镁合金热处理类型 647
3.镁合金热处理工艺 647
4.镁合金热处理注意事项 647
5.7.1 淬火回火实例 649
5.7 工件热处理实例 649
5.7.2 表面热处理实例 653
5.7.3 化学热处理实例 657
参考文献 663
7.钢包精炼炉 667
5.红外熔炼炉 667
6.1.2 冲天炉 667
11.真空感应电炉 667
10.真空电弧炉 667
9.电渣熔炼炉 667
8.氩氧脱碳精炼炉(AOD) 667
第6章 铸造设备与工装 667
6.电弧炉 667
第2篇 热加工设备 667
4.电阻炉 667
3.坩埚炉 667
2.感应电炉 667
1.冲天炉 667
6.1.1 常用熔炼设备 667
6.1 熔炼浇注设备 667
1.国内常用冲天炉结构及主要参数 668
3.电磁配铁秤 672
2.冲天炉用鼓风机 672
6.1.3 电弧炉 677
1.熔炼铸铁用工频感应电炉 677
6.1.4 工频感应电炉 677
2.熔铜及熔锌用无芯工频感应电炉 678
3.熔铝用无芯工频感应电炉 678
6.1.5 无芯中频感应电炉 680
6.1.6 电阻熔炼炉 680
6.1.7 浇注设备 681
6.2 砂处理设备 682
6.2.2 松砂机 683
6.2.1 辗轮式混砂机 683
6.2.3 破碎设备 684
6.2.4 筛分设备 685
6.2.5 磁分离设备 686
6.3 造型制芯设备 687
6.3.1 震压造型机 687
6.3.2 震实造型机 688
6.3.5 抛砂机 689
6.3.4 射压造型机 689
1.多触头高压造型机 689
2.水平分型脱箱压实造型机 689
6.3.3 压实造型机 689
2.热芯盒射芯机 690
3.冷芯盒射芯机 690
6.3.6 射芯机 690
1.普通射芯机主要特点及技术规格 690
6.3.7 壳芯机 691
6.4 落砂与清理设备 691
6.5 特种铸造设备 694
6.5.1 压力铸造设备 694
1.蜡料制备装置 696
2.单工位压蜡机 696
6.5.2 熔模铸造设备 696
6.5.3 低压铸造设备 697
6.5.4 离心铸造设备 698
6.6 铸造工装设计 699
6.6.1 模样 699
1.木模用材 699
2.塑料模材料 699
3.泡沫塑料模材料 700
4.金属模样 700
6.6.2 模板 705
2.模板本体结构 705
1.底板材料 705
1.芯盒材料 712
2.金属芯盒分盒面的分类 712
3.盒体结构 712
6.6.3 芯盒 712
4.芯盒的定位 714
5.芯盒夹紧装置 714
6.金属芯盒的尺寸偏差和表面粗糙度 717
7.热芯盒 717
6.6.4 砂箱设计 728
1.砂箱的类别、结构、材料及尺寸 728
2.砂箱机械加工技术要求 730
3.砂箱排气孔布置及出气孔尺寸 731
4.箱带 731
5.砂箱的定位结构 731
参考文献 736
7.1.2 锻压设备型号 737
1.通用锻压设备型号的表示方法 737
7.1 锻压设备分类及型号 737
7.1.1 锻压设备分类 737
第7章 锻压车间设备 737
2.专用锻压设备型号的表示方法 738
7.2 机械压力机 738
7.2.1 概述 738
1.结构 738
1.开式压力机 739
2.主要参数 739
7.2.2 通用压力机 739
2.闭式压力机 741
7.2.3 拉深压力机 746
1.闭式单点、双点双动拉深压力机 746
2.闭式底传动双动拉深压力机 746
7.2.4 精压机 749
7.2.5 金属挤压机 750
1.曲轴式冷挤压机 750
2.肘杆式冷挤压机 750
7.2.6 开式自动压力机 751
7.3 液压机 752
7.3.1 概述 752
1.类型 752
2.主要参数 752
7.3.2 锻造液压机 755
2.下拉式锻造液压机 755
1.单臂式锻造液压机 755
3.正装式锻造液压机 755
7.3.3 冲压液压机 758
7.3.4 通用液压机 760
7.4 锻锤 763
7.4.1 空气锤 763
7.4.2 蒸汽-空气锻锤 763
1.蒸汽-空气自由锻锤 763
2.蒸汽-空气模锻锤 763
7.4.3 液气锤 763
7.3.5 金属挤压液压机 763
2.CJ83系列液压模锻锤 763
7.4.4 螺旋压力机 763
1.摩擦压力机 763
2.电动螺旋压力机 763
1.CDC83系列液气锤 763
3.液压螺旋压力机 769
7.4.5 锻锤基础 771
1.不隔振锻锤基础 771
2.隔振基础 772
7.5 剪切机 773
7.5.1 剪板机 773
7.5.2 捧料剪断机 775
7.5.3 联合冲剪机 776
7.6 弯曲校正机 776
7.6.1 板料折弯压力机 776
7.6.2 折边机 776
7.6.3 卷板机 776
1.对称式三辊卷板机 776
2.非对称式三辊卷板机 776
3.下调式三辊卷板机 776
1.型材卷弯机 779
7.6.4 弯管机 779
7.6.5 其他 779
4.四辊卷板机 779
2.板料校平机 786
3.圆材校直切断机 786
7.7 锻造机械化装置 787
7.7.1 锻造操作机 787
7.7.2 装出料机 789
7.7.3 调头转台 789
7.8.3 钩式自动送料装置 791
7.8 冲压自动送料装置和自动冲模 791
7.8.2 夹持式自动送料装置 791
7.8.1 滚轴式自动送料装置 791
7.8.4 工序件自动送料装置 794
参考文献 798
第8章 焊接设备 799
8.1 弧焊电源 799
8.1.1 弧焊电源种类 799
1.交流弧焊电源 799
2.直流弧焊发电机 799
3.硅整流弧焊机 799
4.晶闸管弧焊电源 801
5.晶体管弧焊电源 801
7.矩形波交流弧焊电源 803
6.逆变式弧焊电源 803
8.脉冲弧焊电源 804
8.2.3 面罩、护目镜片 805
8.2.2 焊接电缆 805
8.2.1 焊钳 805
1.根据焊接方法选择 805
8.1.2 弧焊电源选择 805
8.2 手弧焊辅助设备 805
2.弧焊电源电流类型选择 805
3.焊缝背面强迫成型装置 806
8.3 埋弧焊设备 806
8.3.1 自动埋弧焊机 806
1.焊接夹具 806
8.3.2 埋弧焊辅助设备 806
2.工件变位和焊机变位装置 806
4.焊剂回收输送设备 807
8.4 钨极氩弧焊设备 807
8.4.1 钨极氩弧焊机 807
8.4.2 焊枪 807
3.供气和冷却水系统 808
8.5 熔化极气体保护焊设备 808
4.控制系统 808
8.5.2 辅助设备 808
2.送丝系统 808
1.焊枪 808
8.5.1 熔化极气体保护焊机 808
8.4.3 供气系统和水冷系统 808
8.6 等离子弧焊及切割设备 811
8.6.1 等离子弧焊机 811
1.焊枪 812
8.6.2 辅助设备 812
2.控制电路 812
3.供气系统 813
8.6.3 等离子弧切割设备 813
1.等离子弧切割机 813
2.控制系统 813
3.割枪 813
5.焊矩与割矩 814
4.回火防止器 814
3.乙炔发生器及乙炔瓶、液化石油气瓶 814
2.减压器 814
1.氧气瓶 814
8.7.1 一般气焊气割设备 814
8.7 气焊及气割设备 814
8.7.2 自动和半自动切割机 816
8.7.3 火焰喷涂设备 816
8.8 电阻焊及摩擦焊设备 816
8.8.1 电阻焊设备分类及主要技术要求 816
4.电极材料选择 820
2.缝焊机 820
3.对焊机 820
8.8.2 电阻焊设备 820
8.8.3 摩擦焊机 822
8.9 其他焊接设备 823
8.9.1 电渣焊设备 823
8.9.2 电子束焊设备 823
8.9.3 扩散焊设备 824
参考文献 824
9.1.1 热处理炉的分类 825
9.1 热处理设备分类 825
第9章 热处理设备 825
9.1.2 热处理加热装置的分类 827
9.1.3 热处理冷却设备的分类 829
9.1.4 热处理辅助设备的分类 830
9.2 热处理炉 830
9.2.1 热处理炉的结构类型 830
9.2.2 热处理电阻炉 833
1.箱式电阻炉 833
2.井式电阻炉 837
5.输送带式电阻炉 838
4.台车式电阻炉 838
3.罩式电阻炉 838
6.热处理电阻炉功率计算与分配 840
7.电阻炉的电热元件 844
8.电阻炉的安装、维护与安全操作 848
9.2.3 热处理浴炉 849
1.内热式浴炉 849
2.外热式电热浴炉 857
3.盐浴炉使用、维修与安全操作 858
2.电子管变频装置 859
1.分类 859
9.3.1 电磁感应加热装置 859
9.3 热处理表面加热装置 859
3.机式变频装置 860
4.可控硅变频装置 860
5.工频感应加热装置 860
9.3.2 感应加热淬火机床 862
1.轴类通用淬火机床 862
2.铀及齿轮类通用淬火机床 863
9.3.3 火焰表面加热装置 865
4.曲轴淬火机床 865
3.齿轮淬火机床 865
9.4 冷却装置 867
1.淬火槽结构与计算 867
2.冷处理设备 870
1.清洗设备 871
9.5 热处理车间辅助设备 871
2.清理设备 873
3.矫正与矫直设备 874
4.热处理用夹具 874
9.6 测温仪表 878
1.玻璃液体温度计 878
2.热电偶 880
3.光学高温计 882
4.光电高温计 882
5.测温仪表 883
6.特种结构的热电偶 885
9.7 可控气氛的分析、测量与控制 889
1.钢箔法 889
2.奥氏体分析法 889
6.氧位(氧势)测定法 890
4.露点仪法 890
3.气相色谱法 890
参考文献 891
第10章 起重运输设备 892
10.1 千斤顶 892
10.2 液压升降台 893
10.3 钢丝绳电动葫芦 894
10.4 电动单梁起重机 895
10.5 电动葫芦双梁桥式起重机 895
10.6 通用桥式起重机 896
10.7 抓斗、电磁桥式起重机 897
参考文献 899
第3篇 热加工缺陷及质量分析 903
第11章 金属材料的试验与检验 903
11.1 化学成分检验 903
11.1.1 化学分析方法 903
1.化学分析方法简介 903
2.钢铁材料中常有元素的化学分析方法要点 903
3.化学分析的检测标准和误差 904
11.1.2 原子光谱分析 905
1.原子发射光谱 905
1.电子探针 906
11.1.3 微区化学成分分析 906
2.原子吸收光谱 906
3.原子荧光光谱分析 906
2.俄歇电子能谱仪 907
3.离子探针仪 908
4.激光显微光谱分析 908
11.1.4 钢的火花鉴别 908
1.火花的基本特征 908
2.碳素钢的火花 909
3.合金元素对火花特征的影响 910
1.试样制备 911
2.酸蚀方法及酸蚀剂 911
11.2 宏观试验 911
11.2.1 酸蚀法 911
4.火花检验设备及方法 911
3.酸蚀法的应用 913
11.2.2 印痕法 915
1.硫印法 915
2.铅印法及铅“汗”法 916
11.2.3 断裂试验 916
1.钢材冶金质量检验 916
3.失效分析 917
2.热加工工艺评价 917
11.3.1 光学显微镜 920
1.主要光学零件的性能 920
2.显微镜工作方式 920
11.3 微观试验 920
11.3.2 金相试样的制备 921
1.镶嵌 921
2.机械磨光与抛光 921
3.显微组织的显示 924
1.晶粒大小的测定 927
11.3.3 显微组织的定量测定 927
2.次生相相对量及相间距的测量 931
11.3.4 钢中非金属夹杂物的检验 932
1.夹杂物的评级 932
2.夹杂物类型及组成的确定 932
11.3.5 电子显微分析方法 932
1.扫描电子显微镜的工作原理及特点 932
2.扫描电镜的应用 933
11.4.1 硬度试验 934
1.布氏硬度试验 934
11.4 力学性能试验 934
3.透射电子显微分析简介 934
2.洛氏硬度试验 936
3.维氏硬度试验 938
4.努氏硬度试验 939
5.显微硬度试验 940
6.肖氏硬度试验 940
7.理氏硬度试验 940
2.工程应力-应变曲线及性能指标 941
1.试样及试验机 941
11.4.2 拉伸试验 941
8.硬度与强度换算及硬度之间的换算 941
3.拉伸试样的断口 948
11.4.3 压缩、弯曲、扭转试验 948
1.压缩试验 948
2.弯曲试验 948
3.扭转试验 949
11.4.4 冲击试验 950
1.冲击试验方法及试样 950
2.系列冲击试验 951
2.疲劳曲线及疲劳极限 952
11.4.5 疲劳试验 952
1.疲劳现象分类 952
3.疲劳试验方法及试验机 953
11.4.6 磨损试验 953
1.磨损的分类 953
2.磨损试验机类型 953
3.磨损的评定方法 955
11.5 无损检测 955
11.5.1 超声检测 957
1.超声检测的基本原则 957
2.超声检测设备 958
3.超声检测技术 959
4.超声检测的标准 962
5.超声检测的应用 963
6.常用超声检测方法的比较 964
11.5.2 射线检测 964
1.射线检测的基本原理 964
2.射线检测的设备及器材 964
3.射线检测技术 967
4.射线检测标准 968
6.常用射线检测方法的比较 969
5.射线检测应用 969
1.磁粉检测的基本原理 970
2.磁粉检测设备及附件 970
11.5.3磁粉检测 970
3.磁粉检测技术 971
4.磁粉检测的标准 972
5.磁粉检测应用 972
2.渗透检测技术 974
3.渗透检测的标准 974
1.渗透检测的基本原理 974
11.5.4 渗透检测 974
4.渗透检测应用 977
11.5.5 涡流检测 978
1.涡流检测的基本原理 978
2.涡流检测设备及检测线圈 979
3.涡流检测技术 980
4.涡流检测应用 981
11.5.6 材料硬度无损检测 981
参考文献 982
12.1 铸铁件的冶金质量 983
1.灰铸铁冶金质量指标 983
第12章 铸造缺陷及质量控制 983
2.提高灰铸铁质量与性能途径 984
12.2 铸铁件砂型铸造时产生的缺陷及防止方法 987
12.2.1 灰铸铁件的缺陷及防止方法 987
1.气孔,针孔 987
2.缩孔、缩松、疏松 988
3.裂纹 989
4.冷隔 990
5.夹砂 990
7.化学粘砂 991
6.机械粘砂 991
8.型砂紧实度的影响 992
9.组织不合格 992
12.2.2 球墨铸铁件的缺陷及防止方法 993
1.缩孔、缩松、缩陷 993
2.夹渣 993
3.皮下气孔 994
4.石墨漂浮 994
5.球化不良 994
2.缩松及枝状缩松 995
12.2.3 可锻铸铁件的缺陷及防止方法 995
1.灰点 995
6.球化衰退 995
7.关于基体组织 995
1.蠕墨铸铁的特征 996
12.2.5 耐磨铸铁件的缺陷及防止方法 996
2.在质量控制方面应注意的问题 996
1.减磨铸铁 996
12.2.4 蠕墨铸铁件的缺陷及防止措施 996
5.回火脆性 996
4.铸件表面氧化皮 996
3.裂纹 996
2.抗磨铸铁 997
12.3 铸钢件砂型铸造的缺陷及质量控制 999
12.3.1 碳钢及低合金钢铸造缺陷及防止方法 999
1.气孔 999
2.缩孔及缩松 1003
3.夹渣与夹砂 1006
4.热裂纹 1007
5.冷裂纹 1009
7.皱纹 1010
8.冷隔和浇注不足 1010
6.粘砂 1010
9.偏析 1011
10.晶粒粗大 1011
11.其他缺陷 1012
12.3.2 高合金钢铸件的缺陷及防止方法 1012
1.概述 1012
2.铸造不锈钢 1012
12.4 非铁合金的铸造缺陷及防止措施 1013
12.4.1 铝合金的铸造缺陷及防止方法 1013
4.铸造高锰钢 1013
3.铸造耐热钢 1013
1.气孔 1014
2.针孔 1014
3.疏松 1014
4.夹杂 1014
5.夹渣 1015
6.裂纹 1015
7.偏析 1015
12.4.2 铜合金的铸造缺陷及防止方法 1015
6.偏析 1016
5.夹渣 1016
4.锡汗和铅汗 1016
3.铸件表面出现虫蛀状或局部发黑 1016
2.针孔 1016
1.气孔 1016
7.缩孔、缩松 1017
8.说明 1017
12.5 特种铸造方法产生的缺陷及防止方法 1017
12.5.1 熔模铸造 1017
1.熔模的缺陷 1017
2.型壳的缺陷 1018
3.熔模铸件的缺陷 1019
12.5.2 陶瓷型铸造 1021
1.型裂 1021
2.气孔 1022
12.5.3 金属型铸造 1022
1.气孔 1022
2.夹渣 1022
3.裂纹 1022
3.表面凸起 1023
2.冷隔 1023
12.5.4 压力铸造 1023
1.孔洞 1023
6.龟裂 1023
5.披缝 1023
4.浇注不足 1023
参考文献 1024
第18章 锻压缺陷及质量控制 1025
13.1 锻造生产过程中的主要缺陷及质量控制 1025
13.1.1 锻造过程中的常见缺陷 1025
13.1.2 下料过程中的缺陷分析 1032
1.剪切下料的缺陷分析 1032
2.提高剪切质量的措施 1034
1.晶粒粗大 1042
13.1.4 锻造工艺过程中的缺陷分析 1042
13.1.3 加热过程中的缺陷分析 1042
2.纤维组织 1043
3.折迭 1045
4.裂纹 1048
13.1.5 锻模寿命 1052
1.锻模的损伤形式和模具寿命 1052
2.影响锻模寿命的因素 1053
3.提高锻模寿命的措施 1053
4.锻模修理 1053
4.齿轮锻件表层的增碳缺陷 1057
3.过热对碳氮共渗后马氏体的影响 1057
2.气割下料引起的裂纹 1057
13.2 锻件缺陷分析实例 1057
1.原材料折迭 1057
5.锻件端面裂纹 1058
6.铜脆 1058
7.锻件的对称性折迭 1058
8.柴油机连杆断裂 1058
9.打标记引起的裂纹 1059
10.W18Cr4V锻件中心轴向裂纹 1059
14.滚齿刀崩刃 1060
15.冷冲模工作时压裂 1060
12.W18Cr4V车刀锻后冷却裂纹 1060
13.齿轮铣刀热处理时内孔淬裂 1060
11.键槽拉刀表面纵向裂纹 1060
16.冷冲凹模断裂 1061
17.切边模刃口崩裂 1061
18.1Cr18Ni9Ti管接头裂纹 1061
19.进气阀锻件粗晶 1062
20.流线切断 1062
13.3 板料成形过程中的常见缺陷分析 1062
13.3.1 冲裁过程中的工件缺陷分析 1062
13.3.2 弯曲过程中的工件缺陷分析 1064
13.3.3 拉深过程中的工件缺陷分析 1066
13.4 挤压成形过程中的常见缺陷分析 1067
13.4.1 挤压件的常见缺陷及其产生原因 1067
13.4.2 冷挤压模具寿命分析 1067
参考文献 1071
14.1.1 熔焊的焊接缺陷特征及分类 1073
1.焊接结构及焊接接头的外形缺陷 1073
2.焊接结构及焊接接头的性能缺陷 1073
14.1 焊接过程中的常见缺陷 1073
第14章 焊接缺陷及质量控制 1073
3.焊接接头组织结构缺陷 1075
4.气体保护焊焊接接头的缺陷 1079
14.1.2 电阻焊的焊接缺陷及其产生原因 1079
14.1.3 钎焊接头的缺陷及其产生原因 1081
14.2 焊接缺陷分析及质量控制 1081
14.2.1 焊接裂纹 1081
1.结晶裂纹 1081
2.液化裂纹 1082
3.再热裂纹 1083
4.冷裂纹 1084
5.层状撕裂 1087
6.应力腐蚀开裂 1088
14.2.2 气孔 1092
1.气孔的类型及分布特征 1092
2.气孔的控制 1092
14.2.4 未熔合或未焊透 1093
1.未熔合或未焊透的特征 1093
2.未熔合或未焊透的控制 1093
2.夹杂的控制 1093
1.夹杂物的类型 1093
14.2.3 夹杂 1093
14.2.5 电弧擦伤和过量飞溅 1094
1.电弧擦伤 1094
2.过量飞溅 1094
14.3 焊接缺陷的危害与容限 1094
14.3.1 焊接结构的断裂事故 1094
14.3.2 焊接缺陷的危害 1097
1.焊接缺陷对静载强度的影响 1097
2.焊接缺陷对动载强度的影响 1097
3.焊接缺陷对疲劳强度的影响 1097
2.CVDA-1984规范内容简介 1100
1.质量评定标准 1100
14.3.3 焊接缺陷的容限 1100
4.改进措施 1102
2.焊接工艺 1102
1.结构形式 1102
14.4.2 钢桥工字梁的焊接 1102
3.失效分析 1102
3.失效分析 1102
2.焊接工艺 1102
1.结构形式 1102
14.4.1 汽车大梁焊接 1102
14.4 焊接结构失效分析举例 1102
4.改进措施 1103
14.4.3 公路钢桥工字梁失效分析 1103
1.结构形式 1103
2.失效分析 1103
3.改进措施 1103
14.4.4 大型厚壁筒焊接 1103
1.结构形式 1103
2.焊接工艺 1103
3.失效分析 1103
1.结构形式 1104
14.4.6 锅炉汽包焊接的再热裂纹 1104
2.焊接工艺 1104
3.失效分析 1104
1.结构形式 1104
2.失效分析 1104
14.4.5 立式油罐的低温脆性断裂 1104
4.改进措施 1104
3.改进措施 1104
4.改进措施 1105
14.4.7 铝厂低碳钢设备的应力腐蚀开裂 1105
1.结构形式 1105
2.失效分析 1105
3.改进措施 1105
参考文献 1106
1.一般过热 1107
3.粗大组织的遗传性 1107
2.断口遗传 1107
第15章 热处理缺陷及质量控制 1107
15.1.1 过热 1107
15.1 加热缺陷 1107
15.1.2 过烧 1109
15.1.3 脱碳 1109
1.脱碳层的组织特征 1109
2.氧化脱碳的控制 1110
1.氧化层的结构 1110
15.1.4 氧化 1110
2.脱碳层的测定方法 1110
15.2 退火,正火缺陷 1112
15.2.1 硬度偏高 1112
15.2.2 球化不完全 1112
15.2.3 脱碳 1113
15.2.4 球化不均 1113
15.2.5 过共析钢正火时出现网状碳化物 1113
3.影响畸变的因素 1113
15.3 淬火缺陷 1114
15.3.1 热处理应力 1114
15.2.8 带状组织 1114
15.2.7 退火石墨 1114
15.2.6 粗大魏氏组织 1114
15.3.2 畸变 1115
1.淬火畸变类型及形成原因 1115
2.淬火畸变的一般趋势 1116
4.减少热处理畸变的途径和方法 1123
4.防止淬火开裂的措施 1123
5.热处理畸变工件的校正 1125
3.产生淬火开裂的场合及原因 1126
1.淬火裂纹的形成 1126
15.3.3 淬火开裂 1126
2.常见裂纹类型及其与内应力的关系 1126
15.3.4 硬度不足 1128
15.3.5 软点 1129
15.3.6 表面腐蚀——麻点 1130
15.4 回火缺陷 1130
15.5 感应加热淬火缺陷 1131
15.5.1 硬度不足 1131
15.5.2 软点 1131
15.5.3 软带 1131
15.5.4 淬火裂纹 1131
15.5.5 畸变 1131
15.5.6 淬硬区分布不合理 1132
1.渗层不均 1133
3.网状或堆状碳化物 1133
2.渗层过浅 1133
4.心部铁素体量过多 1133
15.6.1 渗碳和碳氮共渗 1133
15.6 钢的化学热处理缺陷 1133
15.5.7 表面灼伤 1133
5.渗层残佘奥氏体量过多 1134
6.黑色组织 1134
7.黑色孔洞 1135
8.表面脱碳 1135
9.畸变 1135
10.渗碳开裂 1136
15.6.2 渗氮 1136
2.裂纹 1137
1.疏松或孔洞 1137
15.6.3 渗硼 1137
3.硼化物层与基体之间出现铁素体软带 1138
4.渗硼层剥落 1138
5.渗硼层太浅 1138
6.渗硼层过烧 1138
15.7 非铁金属热处理缺陷及控制 1138
15.7.1 铝合金热处理 1138
15.7.2 镁合金热处理 1139
15.7.3 铜合金热处理 1139
15.7.4 钛合金热处理 1139
参考文献 1139
- 《激光加工实训技能指导理实一体化教程 下》王秀军,徐永红主编;刘波,刘克生副主编 2017
- 《Maya 2018完全实战技术手册》来阳编著 2019
- 《先进激光加工技能实训》肖海兵主编 2019
- 《高等教育双机械基础课程系列教材 高等学校教材 机械设计课程设计手册 第5版》吴宗泽,罗圣国,高志,李威 2018
- 《慢性呼吸系统疾病物理治疗工作手册》(荷)瑞克·考斯林克(RikGosselink) 2020
- 《战略情报 情报人员、管理者和用户手册》(澳)唐·麦克道尔(Don McDowell)著 2019
- 《实用内科手册》黄清,阮浩航主编 2016
- 《基层医疗卫生机构安全用药手册》黎月玲,熊慧瑜 2019
- 《同仁眼科手册系列 同仁儿童眼病手册》付晶编 2018
- 《环境噪声监测实用手册》中国环境监测总站编 2018
- 《电子测量与仪器》人力资源和社会保障部教材办公室组织编写 2009
- 《学前儿童发展心理学 第2版》刘万伦主编;王文秀,甘卫群,刘万伦编写人员 2019
- 《习近平总书记教育重要论述讲义》本书编写组 2020
- 《液固旋流分离新技术》中国化工学会组织编写;汪华林等著 2019
- 《新编高中物理竞赛教程习题全解》钟小平主编;钟小平,倪国富,曹海奇编写 2019
- 《声动中国 七十年歌声里的中国故事》王一诺责任编辑;(中国)《声动中国》编写组 2019
- 《对话中国》《对话中国》编写组著 2019
- 《绿色过程工程与清洁生产技术 张懿院士论文集精选 上》《绿色过程工程与清洁生产技术》编写组编 2019
- 《近代中国分省人文地理影像采集与研究 甘肃》《近代中国分省人文地理影像采集与研究》编写组 2019
- 《创新的脚步 全国社区治理和服务创新实验区成果集萃》民政部编写组编著 2018
- 《指向核心素养 北京十一学校名师教学设计 英语 七年级 上 配人教版》周志英总主编 2019
- 《北京生态环境保护》《北京环境保护丛书》编委会编著 2018
- 《高等教育双机械基础课程系列教材 高等学校教材 机械设计课程设计手册 第5版》吴宗泽,罗圣国,高志,李威 2018
- 《指向核心素养 北京十一学校名师教学设计 英语 九年级 上 配人教版》周志英总主编 2019
- 《高等院校旅游专业系列教材 旅游企业岗位培训系列教材 新编北京导游英语》杨昆,鄢莉,谭明华 2019
- 《中国十大出版家》王震,贺越明著 1991
- 《近代民营出版机构的英语函授教育 以“商务、中华、开明”函授学校为个案 1915年-1946年版》丁伟 2017
- 《新工业时代 世界级工业家张毓强和他的“新石头记”》秦朔 2019
- 《智能制造高技能人才培养规划丛书 ABB工业机器人虚拟仿真教程》(中国)工控帮教研组 2019
- 《AutoCAD机械设计实例精解 2019中文版》北京兆迪科技有限公司编著 2019