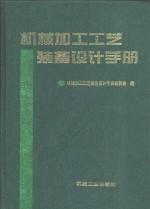
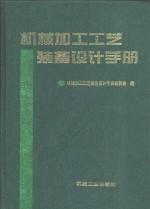
机械加工工艺装备设计手册PDF电子书下载
- 电子书积分:32 积分如何计算积分?
- 作 者:机械加工工艺装备设计手册编委会编
- 出 版 社:北京:机械工业出版社
- 出版年份:1998
- ISBN:7111058577
- 页数:1314 页
1 概述 1
1.1 机器生产与市场需要 1
1.2 产品在市场上的兴衰过程和市场竞争力 1
1.2.1 产品在市场上的兴衰过程 1
1.2.2 产品的市场竞争力 1
第一章 总论 1
2 机器的生产过程和工艺装备设计 3
2.1 机器的生产过程 3
1.2.3 企业的市场竞争力 3
2.2 工艺装备设计方法的演变 4
2.2.1 传统设计方法 4
2.2.2 现代设计方法 5
3 机械制造系统的建立及其优化 8
3.1 系统和系统工程的基本概念 8
3.2 机械加工工艺系统 9
3.3 机械制造系统 11
3.4.3 影响机械加工过程优化的因素 12
3.4.2 机械加工过程优化的评价标准 12
3.4.1 机械加工过程优化的概念 12
3.4 机械加工过程的优化 12
3.4.4 机械加工过程优化方法 13
3.5 机械制造系统的优化 14
3.5.1 生产计划的最优决策 14
3.5.2 生产调度的最优决策 14
3.5.3 项目投资优化决策 14
4 成组技术与工艺装备设计 14
4.1 成组技术在机械制造中的应用 14
4.1.2 制造工艺方面 15
4.1.1 产品设计方面 15
4.1.3 生产管理方面 16
4.2 成组技术与产品设计和工艺设计 16
4.2.1 成组技术与产品设计 16
4.2.2 成组技术与工艺设计 18
4.3 成组技术的工艺装备设计 21
4.3.1 工艺装备设计在成组技术中的作用 21
4.3.2 成组生产条件下的机床 22
4.3.3 成组夹具设计 23
4.3.4 成组加工中的刀具和辅助工具 24
参考文献 26
第2章 刀具 27
1 刀具材料 27
1.1 刀具材料的种类和应用 27
1.2 碳素工具钢及合金工具钢 27
1.3 高速钢 28
1.3.1 高速钢的牌号和性能 28
1.3.2 高速钢刀具牌号的选择 30
1.3.3 粉末冶金高速钢 31
1.4 硬质合金 34
1.4.1 切削加工用硬质合金分类、分组代号 34
1.4.2 硬质合金牌号、成分、性能及用途 35
1.4.3 涂层硬质合金 35
1.5 陶瓷刀具材料 44
1.6 超硬刀具材料 45
1.7 高速钢刀条和硬质合金刀片 46
1.7.1 高速钢车刀条 46
1.7.2 硬质合金焊接刀片 48
1.7.3 硬质合金可转位刀片 54
2 切刀 68
2.1 切刀各部分名称及几何参数 68
2.2 硬质合金车刀 72
2.2.1 硬质合金车刀型号 72
2.2.2 硬质合金外表面车刀 74
2.2.3 硬质合金内表面车刀 74
2.3.1 可转位车刀型号表示规则 82
2.3 可转位车刀 82
2.3.2 可转位车刀通用车刀 84
2.3.3 可转位外表面车刀 86
2.3.4 可转位内表面车刀 114
2.3.5 可转位车刀的结构形式 125
2.3.6 可转位车刀的角度形成及计算 127
2.4 机夹车刀 129
2.4.1 机夹切断车刀 129
2.4.2 机夹螺纹车刀 130
2.5.1 刨刀的形式和尺寸 132
2.5.2 插刀的形式和尺寸 132
2.5 刨刀和插刀 132
3 孔加工刀具 133
3.1 孔加工刀具的种类和应用 133
3.2 麻花钻 134
3.2.1 高速钢麻花钻的尺寸系列 134
3.2.2 标准麻花钻的柄部形式 140
3.2.3 硬质合金麻花钻的形式和尺寸 140
3.2.4 阶梯麻花钻的形式和尺寸 140
3.3 扩孔钻 146
3.4 中心钻的形式和尺寸 149
3.5 锪钻的形式和尺寸 151
3.6 喷吸钻的形式和尺寸 156
3.7 铰刀 158
3.7.1 铰刀的结构 158
3.7.2 铰刀的形式和尺寸 158
3.7.3 铰刀的精度等级及公差 180
4 铣刀 180
4.2.1 立铣刀的形式和尺寸 181
4.2 立铣刀 181
4.1 铣刀的种类和应用 181
4.2.2 粗加工立铣刀的形式和尺寸 184
4.2.3 套式立铣刀的形式和尺寸 187
4.2.4 硬质合金斜齿立铣刀的形式和尺寸 187
4.3 镶齿套式面铣刀和圆柱形铣刀 190
4.4 槽铣刀 191
4.4.1 尖齿槽铣刀和螺钉槽铣刀的形式和尺寸 191
4.4.2 T形槽铣刀的形式的尺寸 192
4.5.1 键槽铣刀的形式和尺寸 195
4.5 键槽铣刀 195
4.5.2 半圆键槽铣刀的形式和尺寸 197
4.6 燕尾槽铣刀和反燕尾槽铣刀 198
4.7 锯片铣刀 200
4.7.1 锯片铣刀的形式和尺寸 200
4.7.2 整体硬质合金锯片铣刀的形式和尺寸 200
4.8 三面刃铣刀 203
4.8.1 三面刃铣刀的形式和尺寸 203
4.8.2 硬质合金错齿和机夹三面刃铣刀的形式和尺寸 203
4.9 模具铣刀 207
4.10 角度铣刀 215
4.11 凸凹半圆铣刀和圆角铣刀 217
4.12 可转位铣刀 218
5 拉刀 223
5.1 拉刀的种类和应用 223
5.2 拉刀设计 227
5.2.1 拉削方式 227
5.2.2 拉削余量 229
5.2.5 拉刀的几何参数 230
5.2.3 拉刀齿升量 230
5.2.4 拉刀容屑槽 230
5.2.6 拉刀的分屑槽 234
5.2.7 拉刀校准部 235
5.2.8 拉刀其他部分设计 235
5.2.9 拉削力计算及拉刀强度校核 239
5.2.10 拉刀主要技术条件 240
5.3.1 圆拉刀 242
5.3.2 圆推刀 242
5.3 圆拉(推)刀 242
5.4 键槽拉刀 246
5.5 花键拉刀 258
6 螺纹刀具 269
6.1 螺纹刀具的种类和应用 269
6.2 丝锥 270
6.2.1 机用和手用丝锥 270
6.2.2 螺母丝锥 284
6.2.3 螺旋槽丝锥 292
6.2.4 螺尖丝锥 295
6.2.5 梯形螺纹丝锥 300
6.2.6 55℃管螺纹丝锥 300
6.2.7 内容屑丝锥 306
6.2.8 米制锥螺纹丝锥 313
6.3 板牙 314
6.3.1 机用和手用圆板牙 314
6.3.2 55℃管螺纹圆板牙 314
6.3.3 六方板牙 320
6.4 滚丝轮 322
6.4.1 普通螺纹用滚丝轮 322
6.4.2 55℃圆锥管螺纹滚丝轮 327
6.4.3 米制锥螺纹滚丝轮 328
6.5 搓丝板 329
6.5.1 普通螺纹用搓丝板 329
6.5.2 55℃圆锥管螺纹搓丝板 332
6.5.3 米制锥螺纹搓丝板 333
7 切齿刀具 334
7.1 切齿刀具的种类和应用 334
7.2 盘形齿轮铣刀 338
7.3 齿轮滚刀 338
7.3.1 渐开线齿轮滚刀 338
7.3.2 磨前齿轮滚刀 342
7.3.3 剃前齿轮滚刀 346
7.3.4 双圆弧齿轮滚刀 349
7.3.5 渐开线花键滚刀 350
7.3.6 短形花键滚刀 352
7.4.1 蜗轮滚刀结构形式 354
7.4.2 蜗轮滚刀参数及其计算 354
7.4 蜗轮滚刀设计 354
7.5 插齿刀 364
7.5.1 直齿插齿刀 364
7.5.2 小模数直齿插齿刀 369
7.5.3 渐开线内花键插齿刀 371
7.6 盘形剃齿刀 374
7.7 直齿锥齿轮精刨刀 376
8.1.1 普通磨料 381
8.1 磨料 381
8 磨料与磨具 381
7.8 弧齿圆锥齿轮铣刀盘 381
8.1.2 超硬磨料 382
8.2 普通磨具 385
8.2.1 普通磨具代号 385
8.2.2 磨具最高工作速度 393
8.2.3 砂轮 393
8.2.4 磨头形状和尺寸 410
8.2.5 油石的形状和尺寸 412
8.2.6 砂瓦形状和尺寸 415
8.3 超硬磨具 416
参考文献 431
1 概述 432
1.1 夹具的组成 432
1.2 夹具的功用 432
1.3 夹具的类型及其举例 432
1.3.1 机床夹具的分类 432
1.3.2 举例 433
1.4 定位和夹紧符号及标注举例 435
1.4.1 定位、夹紧符号 435
1.4.2 定位及夹紧(装置)符号举例 440
1.5 夹具设计的经济评价方法 440
2 工件的定位原理和定位元件 440
2.1 工件定位和基准的概念 440
2.1.1 工件的定位 440
2.1.2 工件的基准 440
2.2.1 工件的定位原理 441
2.2.2 工件定位原理的应用 441
2.2 工件的定位原理及其应用 441
第3章 夹具 444
2.3 工件的定位方法和定位元件 444
2.3.1 工件以平面为定位基面 444
2.3.2 工件以外圆柱面为定位基面 452
2.3.3 工件以圆孔为定位基面 455
2.3.4 工件以特殊表面为定位基面 467
2.3.5 工件以组合表面为定位基面 473
2.3.6 常用定位元件所能限制的工件自由度 473
2.4.2 误差的合成及与工序公差的关系 478
2.4 工件在夹具中加工的误差分析 478
2.4.1 加工误差的组成 478
2.5 定位误差的分析与计算 479
2.5.1 产生定位误差的原因 479
2.5.2 定位误差的计算 479
2.6 辅助支承及其应用 487
2.6.1 辅助支承的作用 487
2.6.2 辅助支承的典型结构 487
2.6.3 辅助支承的使用方法 490
3.1 确定夹紧力的基本原则 491
3.1.1 夹紧力方向的选择 491
3 夹紧力的计算及夹紧机构 491
3.1.2 着力点的选择 492
3.1.3 夹紧力的大小 492
3.2 各种夹紧机构的设计计算 497
3.2.1 斜楔夹紧机构的设计计算 497
3.2.2 螺旋夹紧机构的设计计算 502
3.2.3 偏心夹紧机构的设计计算 503
3.2.4 铰链夹紧机构的设计计算 518
3.2.5 联动夹紧机构的设计计算 525
3.2.6 定心夹紧机构的设计计算 531
3.3 典型夹紧机构及其应用 550
3.4 夹紧元件及部件 551
4 对刀元件、导向元件的选择 614
4.1 对刀、导向元件的作用 614
4.1.1 对刀装置 614
4.1.2 导向元件 614
4.2.1 对刀装置的选择及分析计算 626
4.2 对刀、导向元件的选择及分析计算 626
4.2.2 导向元件的选择及分析计算 628
4.3 夹具与机床的连接方式及其元件 636
5 分度装置及分度误差 643
5.1 分度装置 643
5.1.1 分度装置的类型 643
5.1.2 分度装置的基本结构 643
5.1.3 分度销的操纵机构 646
5.1.5 精密分度装置 648
5.1.4 分度装置的锁紧机构 648
5.2 分度误差计算 658
5.2.1 直线分度误差 658
5.2.2 回转分度误差 659
5.2.3 分度销分度的概率精度 659
6 夹具体、垫块相基础件、随动托板 660
6.1 设计要求 660
6.2 设计方法 661
6.2.1 夹具体的设计 661
6.2.2 垫块和基础件的设计 664
6.3.1 自动线随动托板 668
6.3 随动托板的设计 668
6.3.2 加工中心随动托板 670
6.3.3 柔性制造系统和柔性加工单元随动托板 671
7 夹具的动力装置 671
7.1 气压传动装置 672
7.1.1 气压系统的组成 672
7.1.2 气压传动的特点 672
7.1.3 气压传动设计的主要问题 672
7.2.2 液压基本回路 675
7.2 液压传动装置 675
7.2.1 液压传动的特点 675
7.2.3 液压缸 680
7.2.4 液压传动系统的设计计算 684
7.2.5 液压站 685
7.3 气—液增力传动装置 685
7.3.1 装置特点 685
7.3.2 装置的工作原理及基本计算 685
7.4.1 工作原理及夹紧力计算 687
7.4.2 设计真空夹紧装置应注意事项 687
7.4 真空夹紧装置 687
7.5 电动传动装置 688
7.6 磁力夹紧装置 690
8 各类机床夹具设计原则和方法 692
8.1 机床夹具设计原则和方法 692
8.1.1 夹具设计程序 692
8.1.2 夹具设计的一般要求 694
8.1.3 夹具装配图的绘制 697
8.1.4 制订夹具总图技术要求 699
8.2.1 车、磨床夹具特点和设计要求 701
8.2 车、磨床夹具特点和设计方法 701
8.2.2 车、磨夹具与机床主轴的连接 703
8.2.3 心轴设计 704
8.2.4 专用卡爪的设计 715
8.3 铣床夹具特点和设计方法 719
8.3.1 铣床夹具特点 719
8.3.2 铣床夹具的主要类型 720
8.3.3 夹具方案的设计 720
8.3.4 定位元件的设计 722
8.3.5 夹紧机构的设计 722
8.3.7 对刀元件的设计 723
8.3.6 夹具体的设计 723
8.4 钻床夹具特点和设计方法 724
8.4.1 钻床夹具特点 725
8.4.2 钻模结构和操纵要领 731
8.5 镗床夹具特点和设计方法 733
8.5.1 镗床夹具特点 733
8.5.2 镗套导向的布置形式及选用 733
8.5.3 导向部件结构参数 738
8.5.5 镗套的选用 739
8.5.4 镗杆和镗刀的选用 739
8.5.6 镗床夹具基础件的设计 740
8.6 其他机床夹具特点和设计方法 742
8.6.1 拉床夹具特点和设计方法 742
8.6.2 齿轮加工机床夹具特点和设计方法 745
8.6.3 组合机床夹具特点和设计方法 749
9 柔性制造系统的夹具特点和设计原则 757
9.1 柔性制造系统中工件运储系统的特点 757
9.2.2 柔性制造系统的夹具设计原则 758
9.2.1 数控机床夹具的特点 758
9.2 柔性制造系统夹具设计的原则和要求 758
9.2.3 柔性制造系统的夹具设计要求 759
9.3 柔性制造系统夹具方案的选定和设计 762
9.3.1 夹具方案的选定 762
9.3.2 模块式组合夹具的分类 762
10.1.3 工件装卸及防误结构工艺性 765
10.1.2 排屑、防屑的结构工艺性 765
10.1.1 保证工件正确定位的结构工艺性 765
l0.1 夹具的结构工艺性 765
10 夹具的制造和使用 765
9.3.4 模块式组合夹具的设计 765
9.3.3 模块式组合夹具结构特点 765
10.1.4 提高夹具零件强度、寿命的结构工艺性 771
10.2 工艺孔的应用 772
10.3 合理的加工、装配工艺性 776
10.3.1 合理的加工工艺性 776
10.3.2 合理的装配工艺性 776
10.4 夹具的维修工艺性 778
参考文献 779
第4章 量具量仪 781
1 概述 781
2 测量方法和量具量仪分类 782
2.1 测量方法分类 782
2.2 量具量仪分类 786
3 通用量具量仪的选择 786
3.1 测量误差的基本概念 786
3.2.2 量具量仪的选择方法 787
3.2.1 量具量仪的选择原则 787
3.2 适用量具量仪的选择 787
3.2.3 常用量具量仪 791
4 量规设计 799
4.1 光滑极限量规 799
4.1.1 光滑极限量规的名称、代号及用途 799
4.1.2 光滑极限量规的公差及公差带 799
4.1.3 光滑极限量规尺寸偏差的计算 802
4.1.4 光滑极限量规的结构形式及尺寸 802
4.1.6 光滑极限量规设计举例 817
4.1.5 光滑极限量规的技术要求 817
4.2 直线尺寸量规 818
4.2.1 高度量规和深度量规 822
4.2.2 长度和宽度量规 825
4.2.3 直线尺寸量规的技术要求 825
4.3 莫氏与米制圆锥量规 826
4.3.1 莫氏与米制圆锥量规的形式和尺寸 826
4.3.2 莫氏与米制圆锥量规的精度等级和公差 826
4.3.3 莫氏与米制圆锥量规的技术要求 830
4.4.2 位置量规一般规定 832
4.4 位置量规 832
4.4.1 位置量规术语、定义及代号 832
4.4.3 位置量规公差 833
4.4.4 位置量规计算 837
4.4.5 位置量规技术要求 837
4.4.6 位置量规计算示例 837
4.4.7 位置量规结构原理与计算 859
4.5 普通螺纹量规 859
4.5.1 普通螺纹量规的名称和代号 860
4.5.2 普通螺纹量规的公差和公差带 861
4.5.3 普通螺纹量规的螺纹牙型 863
4.5.4 普通螺纹量规的计算 865
4.5.5 普通螺纹量规的形式和尺寸 867
4.5.6 普通螺纹量规的技术要求 876
4.5.7 检验工件螺纹用的光滑极限量规 876
4.5.8 普通爆纹量规设计示例 877
4.6 矩形花键量规 878
4.6.1 矩形花键量规的种类与代号 878
4.6.2 矩形花键量规的公差与公差带 878
4.6.3 矩形花键量规的技术要求 883
4.6.4 矩形花键量规的测量长度 883
5 表面粗糙度测量 883
5.1 表面粗糙度的测量要求 883
5.2 表面粗糙度的测量方法 884
6.2 定位装置的设计 890
6.2.1 平面定位 890
6.2.2 外圆面定位 890
6 测量装置 890
6.1 概述 890
6.2.3 内圆面定位 892
6.3 传递装置 895
6.3.1 直线传递装置 895
6.3.2 杠杆传递装量 897
6.4 运动导向机构 900
6.4.1 转动导向机构 900
6.4.2 直线导向机构 900
6.5.1 夹紧装置 904
6.5 辅助元件 904
6.5.2 测量仪表夹持装置 905
6.6 测量装置举例 906
6.6.1 长度测量装置 906
6.6.2 形位误差测量装置 907
7 自动化测量系统 909
7.1 自动化测量系统的组成和分类 909
7.1.1 主动测量 910
7.1.2 被动测量 911
7.2 自动化测量系统的设计原则 911
7.3 自动化测量系统的设计方法 912
7.4 自动化测量系统举例 914
参考文献 918
1.2 机床辅具的主要类型及特点 920
2.1 车床辅具 920
2 机床辅具 920
2.1.1 刀杆与刀杆夹 920
1.1 机床辅具的功用 920
1 机床辅具的功用及类型 920
第5章 机床辅具 920
2.1.2 立式车床辅具 928
2.2 钻床辅具 932
2.3 铣床辅具 947
2.4 镗床辅具 959
2.5 拉床辅具 976
2.6 刨床及齿轮加工机床辅具 983
2.6.1 刨床辅具 983
2.6.2 齿轮机床辅具 983
3.1 TSG82数控工具系统的结构形式及型号 988
3 数控机床辅具 988
3.2 数控机床主轴孔用刀杆柄部形式 992
3.3 一类数控机床辅具 995
3.4 二类数控机床辅具 1010
3.4.1 ZB直柄二类辅具 1010
3.4.2 7:24锥柄快换刀柄型二类辅具 1014
3.4.3 莫氏锥柄型二类辅具 1018
3.4.4 攻螺纹夹套 1020
参考文献 1021
2 清洗及其装置 1022
2.1 清洗方法的分类 1022
第6章 装配工具及装置 1022
1 概述 1022
2.2 清洗液 1023
2.2.1 清洗液的分类 1023
2.2.2 几种典型清洗工艺 1026
2.3 清洗装置 1030
2.4 清洗质量检测 1034
3 螺纹联接工具 1036
3.1 一般螺纹联接工具 1036
3.2 螺纹联接工具的扳手空间 1047
3.3 规定预紧力的螺纹联接工具 1049
4 过盈联接工具 1053
4.1 过盈联接装配方法的选择 1053
4.2 过盈联接工具的选择 1054
5 刮配和研配工具 1058
5.1 刮配工具 1059
5.2 研配工具 1068
6 装配、检测辅具的选择和设计 1077
6.1 装拆辅具的功用和设计 1077
6.2 检测辅具的功用和设计 1088
7 平衡装置及使用 1093
7.1 转子的分类与平衡方法 1093
7.2 静平衡装置及其应用 1095
7.3 动平衡装置及其应用 1097
8 装配生产线和自动化装配系统 1103
8.1 装配生产线和自动化装配系统的条件和工艺原则 1103
8.2 装配生产线和自动化装配系统的组成 1103
参考文献 1110
1.1.2 自动生产线 1111
1.1.1 单机自动化 1111
1.1.3 综合自动化系统 1111
第7章 机械加工自动化系统的辅助装置 1111
1.1 大批量生产机械加工系统的自动化 1111
1 概述 1111
1.2 中小批量机械加工系统的自动化 1112
1.2.I 数控机床 1112
1.2.2 加工中心 1112
1.2.3 柔性制造单元(FMC) 1112
1.2.4 柔性制造系统(FMS) 1113
1.2.5 计算机集成制造系统(CIMS) 1113
2 机械加工自动线的辅助装置 1114
2.1 工件的装、运、储系统 1114
2.2 自动装卸料装置 1115
2.2.1 自动装卸料装置的类型 1115
2.2.2 自动装卸料装置设计的主要依据 1117
2.2.3 料仓式装料装置设计 1117
2.2.4 料斗式装料装置设计 1124
2.2.5 振动式装料装置设计 1133
2.3 工件输送系统 1146
2.3.1 料道式工件输送系统 1147
2.3.2 步伐式工件输送系统 1171
2.4 机械加工自动线的储料仓库系统 1181
2.4.1 储料器 1182
2.4.2 中间储料库 1184
2.5 典型机械加工自动线装运储系统 1187
2.5.1 载重汽车气缸体的加工自动线实例 1187
2.5.2 喷油器壳体加工自动线的装运储系统 1191
2.5.3 汽车轴承套圈加工自动线 1196
3 柔性制造系统(FMS)的辅助装置 1198
3.1 FMS中工件装、运、储系统的组成和分类 1199
3.2 机械手与机器人 1199
3.2.1 机械手的组成和分类 1199
3.2.2 典型的机械手结构 1206
3.2.3 工业机器人 1226
3.3 FMS中工件的运输系统 1229
3.3.1 FMS中工件运输系统的组成和分类 1229
3.3.2 传送机 1231
3.3.3 搬运小车 1232
3.3.4 堆垛起重机 1234
3.4 FMS的储料仓库系统 1234
3.5 典型的FMS装运储系统 1237
3.5.1 机加工柔性制造系统 1237
3.5.2 钣金柔性制造系统 1240
3.5.3 FMS的设计方法 1243
参考文献 1245
1.1.2 工艺装备CAD的类型 1246
1.2.1 工艺装备CAD硬件 1246
1.2 计算机辅助工艺装备设计系统的构成 1246
第8章 工艺装备的计算机辅助设计 1246
1.1.1 工艺装备CAD概念 1246
1.1 计算机辅助工艺装备设计的概念 1246
1 计算机辅助工艺装备设计系统 1246
1.2.2 工艺装备CAD软件 1249
1.3 硬件和软件配置 1250
2.1.2 数据的组织形式 1252
2.1.1 数据的描述 1252
2.1 数据描述、组织和管理 1252
2 数据库技术 1252
2.2 数据库体系结构 1253
2.2.1 体系结构 1253
2.2.2 数据模型 1254
2.3 数据库管理系统及分布式数据库 1254
2.3.1 数据库管理系统 1254
2.3.2 分布式数据库 1255
2.4.1 ORACLE数据库特点 1256
2.4 ORACLE关系型数据库 1256
2.4.2 ORACLE内核程序 1257
2.4.3 ORACLE软件产品和配置 1258
2.4.4 0RACLE分布式处理环境 1259
2.5 数据库结构式查询语言SQL 1260
2.6 高级语言预编译程序接口 1260
2.6.1 预编译PR0*C及其特点 1260
2.6.2 PRO*C编程 1261
2.6.3 程序首部 1261
2.6.4 应用程序体 1263
2.6.5 动态SQL语句 1266
3 图形处理软件 1270
3.1 图形变换 1270
3.1.1 图形中点的向量表示 1270
3.1.2 变换矩阵 1270
3.1.3 三维图形的几何变换 1270
3.1.4 三维图形的变换 1272
3.2 图形支撑软件 1274
3.2.1 概述 1274
3.2.2 AutoCAD软件 1274
3.2.3 AutoCAD的二次开发技术 1277
3.2.4 Microstation图形软件 1283
3.3 绘图程序的编制 1286
3.3.1 参数法 1286
3.3.2 图形元素组合法 1288
3.3.3 用算法绘制图形 1291
3.4 图形库 1291
3.4.1 图形库技术 1291
3.4.2 图形库的结构 1292
4.1 刀具计算机辅助设计概述 1293
3.4.3 参数化图库的实现 1293
4 刀具计算机辅助设计 1293
4.2 齿轮滚刀CAD 1294
4.2.1 齿轮滚刀CAD工作方式 1294
4.2.2 数据文件或数据库的建立 1294
4.2.3 齿轮滚刀的设计计算 1296
4.2.4 齿轮滚刀的绘制程序 1296
4.2.5 齿轮滚刀CAD系统运行方式 1297
4.3 可转位面铣刀CAD 1298
4.3.1 可转位面铣刀CAD作业方式 1298
4.3.2 WF系列可转位面铣刀 1298
4.3.3 结构参数数据库的建立和输入管理 1298
4.3.4 零件图的绘制 1299
4.3.5 装配图的交互拼装 1299
5 夹具计算机辅助设计 1300
5.1 夹具CAD的特点 1300
5.3.1 系统接口 1301
5.3.2 夹具信息编码系统 1301
5.2 夹具CAD应用软件开发 1301
5.3 CIMS中的组合夹具CAD系统 1301
5.3.3 夹紧力校验 1302
5.3.4 夹具二维图形 1302
5.4 CAD-MFS系统 1303
5.4.1 CAD-MPS组成 1303
5.4.2 夹具设计与拼装 1304
6 人工智能在工艺装备CAD中的应用 1307
6.1 专家系统的基本结构 1307
6.2.3 定位件选择规则 1309
6.2.4 压紧件选择规则 1309
6.2 组合夹具元件选择知识库 1309
6.2.2 基础板选择规则 1309
6.2.1 知识表示 1309
6.2.5 紧固件选择规则 1310
6.3 圆孔拉刀智能CAD系统 1310
6.3.1 系统构成和功能 1310
6.3.2 知识库、数据库和公式库的建立 1310
6.3.3 圆孔拉刀设计 1313
参考文献 1314
- 《激光加工实训技能指导理实一体化教程 下》王秀军,徐永红主编;刘波,刘克生副主编 2017
- 《Maya 2018完全实战技术手册》来阳编著 2019
- 《先进激光加工技能实训》肖海兵主编 2019
- 《高等教育双机械基础课程系列教材 高等学校教材 机械设计课程设计手册 第5版》吴宗泽,罗圣国,高志,李威 2018
- 《慢性呼吸系统疾病物理治疗工作手册》(荷)瑞克·考斯林克(RikGosselink) 2020
- 《战略情报 情报人员、管理者和用户手册》(澳)唐·麦克道尔(Don McDowell)著 2019
- 《实用内科手册》黄清,阮浩航主编 2016
- 《基层医疗卫生机构安全用药手册》黎月玲,熊慧瑜 2019
- 《同仁眼科手册系列 同仁儿童眼病手册》付晶编 2018
- 《AutoCAD机械设计实例精解 2019中文版》北京兆迪科技有限公司编著 2019
- 《东方杂志 第110册 第25卷 第一至四号 1928年1月-1928年2月》上海书店出版社编 2012
- 《清明 我们的节日》冯骥才编 2017
- 《现代水泥技术发展与应用论文集》天津水泥工业设计研究院有限公司编 2019
- 《甘肃省档案馆指南》甘肃省档案馆编 2018
- 《莼江曲谱 2 中国昆曲博物馆藏稀见昆剧手抄曲谱汇编之一》郭腊梅主编;孙伊婷副主编;孙文明,孙伊婷编委;中国昆曲博物馆编 2018
- 《花时间 我的第一堂花艺课 插花基础技法篇》(日)花时间编辑部编;陈洁责编;冯莹莹译 2020
- 《中央财政支持提升专业服务产业发展能力项目水利工程专业课程建设成果 设施农业工程技术》赵英编 2018
- 《东方杂志 第94册 第22卷 第四至七号 1925年2月-1925年4月》上海书店出版社编 2012
- 《远去的老调》经典文库编委会编 2019
- 《东方杂志 第13册 第四年 第一至三期 1907年3月-1907年5月》上海书店出版社编 2012
- 《指向核心素养 北京十一学校名师教学设计 英语 七年级 上 配人教版》周志英总主编 2019
- 《北京生态环境保护》《北京环境保护丛书》编委会编著 2018
- 《高等教育双机械基础课程系列教材 高等学校教材 机械设计课程设计手册 第5版》吴宗泽,罗圣国,高志,李威 2018
- 《指向核心素养 北京十一学校名师教学设计 英语 九年级 上 配人教版》周志英总主编 2019
- 《高等院校旅游专业系列教材 旅游企业岗位培训系列教材 新编北京导游英语》杨昆,鄢莉,谭明华 2019
- 《中国十大出版家》王震,贺越明著 1991
- 《近代民营出版机构的英语函授教育 以“商务、中华、开明”函授学校为个案 1915年-1946年版》丁伟 2017
- 《新工业时代 世界级工业家张毓强和他的“新石头记”》秦朔 2019
- 《智能制造高技能人才培养规划丛书 ABB工业机器人虚拟仿真教程》(中国)工控帮教研组 2019
- 《AutoCAD机械设计实例精解 2019中文版》北京兆迪科技有限公司编著 2019