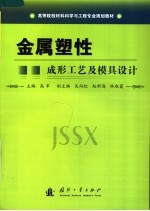
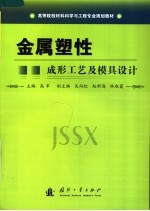
金属塑性成形工艺及模具设计PDF电子书下载
- 电子书积分:12 积分如何计算积分?
- 作 者:高军主编;吴向红,赵新海,林淑霞副主编
- 出 版 社:北京:国防工业出版社
- 出版年份:2007
- ISBN:7118051624
- 页数:335 页
第1篇 金属板料成形工艺及模具设计第1章 板料成形基本概念及基本知识 1
1.1 板料成形概述 1
1.2 冲压工艺设计概述 3
1.2.1 工艺设计的原始资料 3
1.2.2 工艺设计的基本内容 4
1.3 冲压模具设计概述 4
1.3.1 模具总装图及零件图绘制 5
1.3.2 模具典型结构 6
1.4 常用冲模材料 7
1.4.1 冲压对模具材料的要求 7
1.4.2 冲模材料的选用原则 8
1.4.3 冲模材料及热处理要求 8
1.5 毛坯材料及其冲压成形性能 11
1.5.1 冲压工艺对毛坯材料的要求 11
1.5.2 常用毛坯材料 11
1.5.3 材料的冲压成形性能 13
1.6 常用冲压设备及其选用 13
1.6.1 常用冲压设备 13
1.6.2 冲压设备的选用 14
1.7 模具的安装 15
第2章 冲裁及冲压模具设计 16
2.1 概述 16
2.1.1 冲裁设计的基本内容 17
2.1.2 冲裁设计的基本要求及一般工作程序 18
2.1.3 冲裁设计中必须考虑的若干问题 19
2.2 冲裁工艺设计 19
2.2.1 工艺设计的基本内容与一般步骤 20
2.2.2 凸、凹模刃口尺寸的计算 24
2.3 冲裁力 28
2.3.1 冲裁力的计算 28
2.3.2 卸料力及推件力计算 29
2.3.3 降低冲裁力的方法 29
2.4 排样与搭边 31
2.4.1 排样 31
2.4.2 搭边 32
2.4.3 条料宽度 33
2.5 冲压模具设计 34
2.5.1 冲模设计的原则及步骤 34
2.5.2 冲模分类 35
2.5.3 冲模的零部件构成 36
2.5.4 冲模非工作零部件设计 37
2.5.5 冲裁模工作零件设计 44
2.5.6 复合模设计 54
2.5.7 级进模设计 56
第3章 弯曲 68
3.1 概述 68
3.2 弯曲变形分析 69
3.2.1 弯曲变形过程 69
3.2.2 变形区应力应变状态 69
3.2.3 弯曲变形程度及其表示 71
3.2.4 板料弯曲变形的特点 72
3.2.5 最小相对弯曲半径 73
3.3 弯曲回弹 74
3.3.1 弯曲回弹现象 74
3.3.2 影响弯曲回弹的因素 75
3.3.3 弯曲回弹值的确定 76
3.3.4 减少弯曲回弹的措施 78
3.4 弯曲毛坯尺寸 80
3.4.1 弯曲中性层位置的确定 80
3.4.2 弯曲毛坯尺寸的计算 80
3.5 弯曲力的计算 82
3.5.1 自由弯曲时的弯曲力 82
3.5.2 校正弯曲时的弯曲力 82
3.5.3 顶件力或压料力 82
3.5.4 压力机公称压力的确定 82
3.6 弯曲件的工艺性 83
3.6.1 弯曲件的精度 83
3.6.2 弯曲毛坯材料 83
3.6.3 弯曲件的结构形状 83
3.7 弯曲工序安排 85
3.7.1 弯曲工序安排原则 85
3.7.2 典型弯曲工序安排 86
3.8 弯曲模典型结构 86
3.8.1 单工序弯曲模 86
3.8.2 级进模 91
3.8.3 复合模 91
3.8.4 通用弯曲模 92
3.9 弯曲模结构设计 93
3.9.1 弯曲模结构设计应注意的问题 93
3.9.2 弯曲模工作部分设计 94
第4章 拉深 97
4.1 概述 97
4.2 圆筒形件拉深的变形分析 98
4.2.1 拉深变形过程 98
4.2.2 拉深过程中毛坯各处的应力应变状态 99
4.2.3 拉深缺陷及防止措施 101
4.3 旋转体拉深毛坯尺寸的确定 102
4.3.1 毛坯形状和尺寸确定的依据 102
4.3.2 简单旋转体拉深件毛坯尺寸的确定 103
4.3.3 复杂旋转体拉深件毛坯尺寸的确定 105
4.4 无凸缘圆筒形件的拉深工艺计算 106
4.4.1 拉深系数与极限拉深系数 106
4.4.2 拉深次数 108
4.4.3 压边力与拉深力 112
4.5 其它形状零件的拉深 113
4.5.1 有凸缘圆筒形件的拉深 113
4.5.2 阶梯形零件的拉深 117
4.5.3 曲面形状零件的拉深 119
4.5.4 盒形件的拉深 121
4.6 拉深件的工艺性 123
4.6.1 拉深件的公差等级 123
4.6.2 拉深件的结构工艺性 123
4.6.3 拉深件的材料 123
4.7 拉深模的典型结构 123
4.7.1 首次拉深模 124
4.7.2 以后各次拉深模 126
4.7.3 落料、拉深复合模 127
4.8 拉深模工作零件的设计 128
4.8.1 凸、凹模圆角半径 128
4.8.2 拉深模间隙 129
4.8.3 凸、凹模结构 130
4.8.4 凸、凹模工作部分尺寸及公差 132
4.9 辅助工序 133
4.9.1 润滑 133
4.9.2 热处理 134
4.9.3 酸洗 134
第5章 其它冲压成形工艺 135
5.1 概述 135
5.2 胀形 135
5.2.1 变形特点 135
5.2.2 平板毛坯的局部成形 136
5.2.3 空心毛坯的胀形 137
5.3 翻边 139
5.3.1 内孔翻边 139
5.3.2 外缘翻边 142
5.3.3 变薄翻边 144
5.3.4 翻边模结构 145
5.4 缩口 146
5.4.1 缩口变形程度的计算 146
5.4.2 缩口后材料厚度的变化 147
5.4.3 缩口的毛坯计算 147
第6章 典型冲压工艺及模具设计实例 148
6.1 复合冲裁模 148
6.2 落料、冲孔、弯曲复合模 152
第7章 覆盖件成形 156
7.1 覆盖件概述 156
7.2 覆盖件冲压工艺及模具设计原则 156
7.2.1 冲压工艺设计原则 156
7.2.2 冲压模具设计原则 159
7.3 覆盖件拉深工艺及模具设计 160
7.3.1 拉深工艺设计 160
7.3.2 拉深模设计 172
7.4 覆盖件修边、冲孔工艺及模具设计 178
7.4.1 修边、冲孔工艺设计 178
7.4.2 修边、冲孔模设计 181
7.4.3 斜楔机构 186
7.5 覆盖件翻边工艺及模具设计 192
7.5.1 翻边工艺设计 192
7.5.2 翻边模设计 193
7.6 压力机的选择 195
第2篇 金属体积成形工艺及模具设计第1章 锻造基本概念和基本知识 197
1.1 绪论 197
1.1.1 锻造生产的特点及其作用 197
1.1.2 锻造工艺分类 198
1.1.3 锻造生产现状及发展趋势 199
1.2 锻造用原材料及下料方法 200
1.2.1 锻造用原材料 200
1.2.2 下料方法 203
1.3 锻造的热规范 207
1.3.1 金属的锻造加热 207
1.3.2 金属加热时产生的缺陷及防止措施 209
1.3.3 锻造温度范围的确定 213
1.3.4 加热规范 214
1.3.5 少、无氧化加热 217
1.3.6 锻后冷却 218
1.3.7 锻件热处理 222
第2章 自由锻 224
2.1 概述 224
2.2 自由锻工序特点及锻件分类 224
2.2.1 自由锻工序 224
2.2.2 自由锻件的分类 226
2.3 自由锻基本工序分析 227
2.3.1 镦粗 227
2.3.2 拔长 229
2.3.3 冲孔 232
2.3.4 扩孔 233
2.3.5 弯曲 234
2.3.6 错移 234
2.3.7 扭转 234
2.4 自由锻件变形方案的确定 235
2.5 自由锻工艺规程的制定 236
2.5.1 锻件图的制定 237
2.5.2 毛坯重量和尺寸的确定 238
2.5.3 变形工艺过程的制定 239
2.5.4 锻造比的选择及计算 239
2.5.5 选定锻造设备吨位 240
2.6 大型自由锻件锻造工艺特点 240
2.6.1 锻造对钢锭组织和性能的影响 240
2.6.2 提高大型锻件质量的工艺措施 242
第3章 锤上模锻 244
3.1 锤上模锻特点及应用范围 244
3.2 锤上模锻方式与变形特征 244
3.2.1 开式模锻 244
3.2.2 闭式模锻 245
3.3 模锻件分类 246
3.4 模锻件图设计 249
3.4.1 锤上模锻锻件图设计 249
3.4.2 机械加工余量和锻件公差 250
3.4.3 模锻斜度 251
3.4.4 圆角半径 251
3.4.5 冲孔连皮 252
3.5 模锻变形工步的确定 253
3.6 坯料尺寸的确定 254
3.7 模锻锤吨位计算 255
第4章 热模锻压力机上模锻 258
4.1 热模锻压力机上模锻的特点及应用 258
4.2 锻件图设计特点 260
4.2.1 选择分模面位置的特点 260
4.2.2 余量和公差 261
4.2.3 模锻斜度、圆角半径和冲孔连皮 261
4.3 变形工步、工步图设计及毛坯尺寸计算 263
4.3.1 变形工步的选择 263
4.3.2 工步设计 265
4.3.3 确定毛坯尺寸 268
4.4 变形力的计算与设备吨位选择 269
4.4.1 经验公式 269
4.4.2 理论-经验公式 269
4.5 锻模结构 270
4.5.1 锻模模架 270
4.5.2 型槽及镶块设计特点 271
4.5.3 顶件装置 273
4.5.4 导向装置 275
4.6 热模锻压力机上模锻实例 276
4.6.1 连接叉锻件在热模锻锻压机上模锻 276
4.6.2 圆锥齿轮的精密模锻 276
第5章 平锻机上模锻 278
5.1 工艺特点及应用范围 278
5.2 平锻机模锻工步及锻件分类 279
5.2.1 模锻基本工步 279
5.2.2 模锻件分类 280
5.3 锻件图设计 280
5.3.1 分模位置 280
5.3.2 机械加工余量和公差 281
5.3.3 模锻斜度 281
5.3.4 圆角半径 281
5.4 顶镦规则及聚集工步计算 282
5.4.1 顶镦规则 282
5.4.2 聚集工步计算 283
5.5 通孔锻件和盲孔锻件的工步计算 285
5.5.1 通孔锻件热锻件图设计 285
5.5.2 冲孔次数的确定和冲孔工步设计 285
5.5.3 聚集工步与原毛坯尺寸 286
5.6 管类平锻件的工艺特点 287
5.7 平锻设备吨位的确定 288
5.7.1 经验-理论公式 288
5.7.2 经验公式 288
5.8 平锻机上模锻的锻模结构 289
5.8.1 平锻模的固定及固定空间 289
5.8.2 平锻模结构设计特点 290
5.8.3 型槽设计 291
第6章 螺旋压力机上模锻 295
6.1 螺旋压力机工作特点及应用范围 295
6.2 锻件图设计 296
6.2.1 螺旋压力机模锻件的分类及模锻特点 296
6.2.2 锻件图的制定 296
6.3 型槽设计 298
6.4 设备吨位的确定 299
6.4.1 对照锤上模锻和曲柄压力机模锻时的压力进行换算 299
6.4.2 按锻件投影面积和变形难易程度计算 299
6.5 锻模结构特点 299
6.5.1 锻模结构形式和紧固方法 299
6.5.2 模座设计 301
6.5.3 锻模导向部分 302
6.6 综合举例 303
6.6.1 长杆螺栓的模锻 303
6.6.2 法兰盘的开式模锻 303
6.6.3 微型车发动机曲轴的模锻 304
第7章 液压机上模锻 307
7.1 液压机上模锻成形的特点 307
7.2 锻件图设计及工艺特点 308
7.2.1 分模面的选择 308
7.2.2 加工余量的确定 309
7.2.3 结构要素的设计 309
7.2.4 设计锻件图的其它问题 314
7.3 设备吨位的计算 315
7.3.1 根据模锻材料及投影面积确定 315
7.3.2 经验公式计算 316
7.4 液压机上锻模设计 317
7.4.1 工步设计 317
7.4.2 模膛设计 317
7.4.3 模具结构设计 320
7.5 液压机锻模材料的选择 322
第8章 模锻后续工序 324
8.1 切边与冲孔 324
8.1.1 切边力、冲孔力的计算 324
8.1.2 切边、冲孔方式及模具类型 325
8.1.3 切边模 326
8.2 精压与校正 331
8.2.1 精压 331
8.2.2 校正 332
8.3 锻件表面清理 332
8.4 锻件质量检验 334
8.4.1 生产过程检验 334
8.4.2 成品检验 334
参考文献 335
- 《指向核心素养 北京十一学校名师教学设计 英语 七年级 上 配人教版》周志英总主编 2019
- 《设计十六日 国内外美术院校报考攻略》沈海泯著 2018
- 《计算机辅助平面设计》吴轶博主编 2019
- 《高校转型发展系列教材 素描基础与设计》施猛责任编辑;(中国)魏伏一,徐红 2019
- 《景观艺术设计》林春水,马俊 2019
- 《高等教育双机械基础课程系列教材 高等学校教材 机械设计课程设计手册 第5版》吴宗泽,罗圣国,高志,李威 2018
- 《指向核心素养 北京十一学校名师教学设计 英语 九年级 上 配人教版》周志英总主编 2019
- 《Cinema 4D电商美工与视觉设计案例教程》樊斌 2019
- 《通信电子电路原理及仿真设计》叶建芳 2019
- 《高等学校“十三五”规划教材 C语言程序设计》翟玉峰责任编辑;(中国)李聪,曾志华,江伟 2019
- 《断陷湖盆比较沉积学与油气储层》赵永胜等著 1996
- 《高考快速作文指导》张吉武,鲍志伸主编 2002
- 《建筑施工企业统计》杨淑芝主编 2008
- 《钒产业技术及应用》高峰,彭清静,华骏主编 2019
- 《近代旅游指南汇刊二编 16》王强主编 2017
- 《汉语词汇知识与习得研究》邢红兵主编 2019
- 《生物质甘油共气化制氢基础研究》赵丽霞 2019
- 《黄遵宪集 4》陈铮主编 2019
- 《孙诒让集 1》丁进主编 2016
- 《近代世界史文献丛编 19》王强主编 2017
- 《指向核心素养 北京十一学校名师教学设计 英语 七年级 上 配人教版》周志英总主编 2019
- 《北京生态环境保护》《北京环境保护丛书》编委会编著 2018
- 《指向核心素养 北京十一学校名师教学设计 英语 九年级 上 配人教版》周志英总主编 2019
- 《抗战三部曲 国防诗歌集》蒲风著 1937
- 《高等院校旅游专业系列教材 旅游企业岗位培训系列教材 新编北京导游英语》杨昆,鄢莉,谭明华 2019
- 《中国十大出版家》王震,贺越明著 1991
- 《近代民营出版机构的英语函授教育 以“商务、中华、开明”函授学校为个案 1915年-1946年版》丁伟 2017
- 《新工业时代 世界级工业家张毓强和他的“新石头记”》秦朔 2019
- 《智能制造高技能人才培养规划丛书 ABB工业机器人虚拟仿真教程》(中国)工控帮教研组 2019
- 《陶瓷工业节能减排技术丛书 陶瓷工业节能减排与污染综合治理》罗民华著 2017