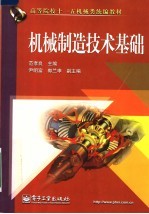
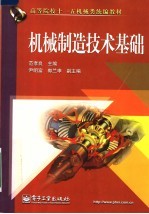
机械制造技术基础PDF电子书下载
- 电子书积分:13 积分如何计算积分?
- 作 者:范孝良主编;尹明富,郭兰申副主编
- 出 版 社:北京:电子工业出版社
- 出版年份:2008
- ISBN:7121053365
- 页数:382 页
第1章 绪论 1
1.1 机械制造工业 1
1.1.1 机械制造工业在国民经济建设和社会发展中的地位与作用 1
1.1.2 国民经济发展对机械制造工业的需求 3
1.1.3 我国机械制造工业发展现状与差距 4
1.1.4 国外机械制造工业发展态势 5
1.2 机械制造技术 7
1.2.1 机械制造技术概述 7
1.2.2 先进制造技术 7
1.3 机械制造(冷加工)学科的范畴、研究内容及特点 12
1.4 课程的特点、研究的主要内容、学习目的与要求 13
第2章 机械制造中的加工方法 15
2.1 概述 15
2.1.1 去除材料的制造过程(△m<0) 15
2.1.2 材料成形制造过程(△m=0) 16
2.1.3 材料累积制造过程(△m>0) 16
2.2 零件的成形方法 16
2.2.1 零件表面的形状 16
2.2.2 表面成形原理 16
2.2.3 零件表面的形成方法 17
2.2.4 零件表面的成形运动 19
2.3 外圆表面加工 19
2.3.1 外圆表面的车削 19
2.3.2 外圆表面的磨削 21
2.3.3 外圆表面的光整加工 23
2.4 孔加工 26
2.4.1 钻孔、扩孔和铰孔 27
2.4.2 镗孔 28
2.4.3 拉孔 30
2.4.4 磨孔 32
2.4.5 研磨孔 32
2.4.6 珩磨孔 33
2.5 平面加工 34
2.5.1 铣平面 34
2.5.2 刨平面 37
2.5.3 磨平面 37
2.5.4 刮研平面 38
2.6 成形表面加工 38
2.6.1 用成形刀具加工 39
2.6.2 仿形加工 39
2.7 数控加工 41
2.7.1 数控加工的产生和发展 41
2.7.2 数控加工的特点 42
2.8 特种加工 42
2.8.1 特种加工概述 42
2.8.2 电火花加工 43
2.8.3 电解加工 44
2.8.4 激光加工 46
2.8.5 电子束加工 47
2.8.6 离子束加工 47
2.8.7 超声波加工 48
思考与练习题 49
第3章 金属切削过程及其控制 50
3.1 概述 50
3.2 金属切削加工的基本概念 50
3.2.1 切削加工 50
3.2.2 切削运动 50
3.2.3 加工表面 51
3.2.4 切削用量 51
3.2.5 切削层参数 52
3.3 金属切削加工用的刀具 53
3.3.1 刀具的结构及参考系 53
3.3.2 常用刀具 57
3.3.3 常用刀具材料 69
3.3.4 磨料与磨具 73
3.4 金属切削过程中的变形 76
3.4.1 切屑的形成过程及变形区的划分 76
3.4.2 前刀面的挤压与摩擦及其对切削变形的影响 78
3.4.3 积屑瘤的形成及其对切削过程的影响 81
3.5 金属切削过程中切屑的类型及控制 82
3.5.1 切屑的类型与分类 82
3.5.2 切屑的控制措施 83
3.6 金属切削过程中的切削力和切削功率 85
3.6.1 切削力 85
3.6.2 切削功率 86
3.6.3 切削力的测量 86
3.6.4 切削力的经验公式和切削力的估算 87
3.6.5 影响切削力的因素 90
3.7 金属切削过程中的切削热和切削温度 93
3.7.1 切削热的产生与传导 93
3.7.2 切削温度的测量与分布 94
3.7.3 影响切削温度的主要因素 96
3.8 刀具磨损和刀具寿命 97
3.8.1 刀具磨损形态和磨损机理 97
3.8.2 刀具磨损过程及磨钝标准 98
3.8.3 刀具耐用度和刀具寿命 99
3.8.4 刀具的破损 100
3.8.5 刀具状态监控 101
3.9 工件材料的切削加工性 103
3.9.1 衡量材料切削加工性的指标 103
3.9.2 改善材料切削加工性的措施 103
3.10 切削条件的合理选择 104
3.10.1 刀具几何参数的选择 104
3.10.2 切削用量的选择 106
3.10.3 切削液的合理使用 109
3.11 磨削过程与磨削机理 111
3.11.1 磨削概述 111
3.11.2 磨料的形状特征 111
3.11.3 磨屑的形成过程 111
3.11.4 磨削力 112
3.11.5 磨削温度 112
3.11.6 砂轮的磨损与耐用度 114
思考与练习题 114
第4章 金属切削机床 116
4.1 概述 116
4.1.1 机床的基本组成 116
4.1.2 机床的技术性能 117
4.2 金属切削机床的分类和型号的编制 118
4.2.1 机床的分类 118
4.2.2 通用机床型号的编制 119
4.2.3 其他类型机床型号的编制 121
4.3 卧式车床CA6140介绍 122
4.3.1 CA6140的工艺范围 122
4.3.2 CA6140的主要技术参数 122
4.3.3 CA6140的传动分析 123
4.3.4 CA6140的主要结构及部件 129
4.4 数控机床介绍 139
思考与练习题 145
第5章 机床夹具设计 147
5.1 机床夹具概述 147
5.1.1 机床夹具的功能 147
5.1.2 机床夹具应满足的要求 147
5.1.3 机床夹具的类型 148
5.1.4 机床夹具的基本组成 149
5.2 机床夹具定位机构的设计 151
5.2.1 工件的定位方法 151
5.2.2 工件定位的基本原理 151
5.2.3 典型的定位方式及定位元件的选择 157
5.2.4 定位误差的分析与计算 165
5.3 机床夹具夹紧机构的设计 169
5.3.1 夹紧机构设计应满足的要求 169
5.3.2 夹紧力的确定 169
5.3.3 常用夹紧机构 173
5.3.4 其他夹紧机构 177
5.3.5 夹紧机构的动力装置 181
5.4 主要机床夹具 183
5.4.1 钻床夹具 183
5.4.2 镗床夹具 189
5.4.3 铣床夹具 192
5.4.4 车床夹具 197
5.5 其他类型夹具 199
5.5.1 成组夹具 199
5.5.2 组合夹具 203
5.5.3 随行夹具 210
思考与练习题 212
第6章 机械加工工艺规程设计 218
6.1 概述 218
6.1.1 生产过程与工艺过程 218
6.1.2 生产纲领与生产类型 218
6.1.3 机械加工工艺规程的作用 220
6.1.4 机械加工工艺规程的制订步骤 221
6.1.5 机械加工工艺规程设计所要研究的主要问题 221
6.2 机械加工工艺规程的设计 222
6.2.1 机械加工工艺规程的组成 222
6.2.2 机械加工工艺规程的格式 224
6.2.3 机械加工工艺规程设计所需原始资料 226
6.2.4 机械加工工艺规程的设计原则 226
6.2.5 机械加工工艺规程设计的步骤与内容 227
6.2.6 工艺路线的拟订 230
6.3 机械加工工序的设计 246
6.3.1 机床设备与工艺装备的选择 246
6.3.2 加工余量 247
6.3.3 工序尺寸及公差的确定 251
6.3.4 时间定额的估算 265
6.3.5 工艺方案的比较与技术经济分析 266
6.3.6 编制工艺文件 269
6.4 机械产品设计的机械加工工艺性评价 269
6.5 成组机械加工工艺规程设计 273
6.5.1 成组技术的基本概念 274
6.5.2 零件的分类编码 274
6.5.3 机械产品零件设计的成组技术 279
6.5.4 成组工艺 279
6.5.5 机床的选择与布置 281
6.5.6 应用成组技术的效益 283
6.6 计算机辅助工艺规程设计 284
6.6.1 CAPP概述 284
6.6.2 基于GT的派生式CAPP系统 285
思考与练习题 288
第7章 机械制造质量分析与控制 291
7.1 概述 291
7.2 机械加工精度 292
7.2.1 机械加工精度概述 292
7.2.2 工艺系统的几何误差 293
7.2.3 定位误差 298
7.2.4 工艺系统受力变形引起的误差 300
7.2.5 工艺系统受热变形引起的误差 305
7.2.6 内应力重新分布引起的误差 309
7.2.7 保证和提高机械加工精度的主要途径 311
7.3 加工误差的统计分析 314
7.3.1 加工误差统计分析概述 314
7.3.2 工艺过程的分布图分析法 316
7.3.3 工艺过程的点图分析法 323
7.4 机械加工表面质量 327
7.4.1 机械加工表面质量概述 327
7.4.2 机械加工表面质量对机械产品使用性能的影响 327
7.4.3 影响表面粗糙度的因素 329
7.4.4 影响加工表面层物理机械性能的因素 331
7.5 机械加工过程中的振动 334
7.5.1 机械加工过程中振动概述 334
7.5.2 机械加工过程中的强迫振动 335
7.5.3 机械加工过程中的自激振动 337
7.5.4 控制机械加工过程中振动的途径 338
思考与练习题 339
第8章 机械产品装配工艺规程设计 341
8.1 概述 341
8.1.1 装配的概念 341
8.1.2 装配的组织形式 342
8.1.3 装配工艺系统图 342
8.1.4 装配精度的概念 343
8.1.5 装配精度与零件精度的关系 343
8.1.6 装配尺寸链 343
8.2 保证装配精度的工艺方法 345
8.2.1 互换法 345
8.2.2 选配法 346
8.2.3 修配法 348
8.2.4 调整法 349
8.3 装配工艺规程设计 351
8.4 机械产品设计的装配工艺性评价 355
思考与练习题 359
第9章 制造技术的新发展 362
9.1 超精密加工与纳米加工技术 362
9.1.1 超精密加工的特点 363
9.1.2 超精密加工的主要方法 363
9.1.3 纳米加工技术 367
9.2 快速成形制造技术 368
9.2.1 光敏树脂液相固化成形 368
9.2.2 叠层实体制造 369
9.2.3 选择性激光粉末烧结成形 370
9.2.4 熔融沉积制造 370
9.2.5 三维打印制造 371
9.2.6 RP技术的发展趋势 372
9.3 网络制造 372
9.3.1 网络制造的特性 373
9.3.2 网络制造的核心问题 374
9.3.3 网络制造的研究与应用 375
9.4 虚拟制造 376
9.4.1 虚拟制造的概念 376
9.4.2 虚拟制造的特点及其种类 377
9.4.3 虚拟制造系统 378
9.4.4 虚拟制造的国内外研究现状 378
9.5 先进生产模式 379
9.5.1 智能制造 379
9.5.2 绿色制造 380
9.5.3 并行工程 381
9.5.4 精益生产 381
思考与练习题 382
- 《市政工程基础》杨岚编著 2009
- 《零基础学会素描》王金著 2019
- 《计算机网络与通信基础》谢雨飞,田启川编著 2019
- 《生物质甘油共气化制氢基础研究》赵丽霞 2019
- 《花时间 我的第一堂花艺课 插花基础技法篇》(日)花时间编辑部编;陈洁责编;冯莹莹译 2020
- 《中国制造业绿色供应链发展研究报告》中国电子信息产业发展研究院 2019
- 《Photoshop CC 2018基础教程》温培利,付华编著 2019
- 《看视频零基础学英语口语》宋德伟 2019
- 《胃癌基础病理》(日)塚本彻哉编者;宫健,刘石译者 2019
- 《高校转型发展系列教材 素描基础与设计》施猛责任编辑;(中国)魏伏一,徐红 2019
- 《电子测量与仪器》人力资源和社会保障部教材办公室组织编写 2009
- 《少儿电子琴入门教程 双色图解版》灌木文化 2019
- 《指向核心素养 北京十一学校名师教学设计 英语 七年级 上 配人教版》周志英总主编 2019
- 《北京生态环境保护》《北京环境保护丛书》编委会编著 2018
- 《指向核心素养 北京十一学校名师教学设计 英语 九年级 上 配人教版》周志英总主编 2019
- 《通信电子电路原理及仿真设计》叶建芳 2019
- 《高等院校旅游专业系列教材 旅游企业岗位培训系列教材 新编北京导游英语》杨昆,鄢莉,谭明华 2019
- 《电子应用技术项目教程 第3版》王彰云 2019
- 《中国十大出版家》王震,贺越明著 1991
- 《近代民营出版机构的英语函授教育 以“商务、中华、开明”函授学校为个案 1915年-1946年版》丁伟 2017