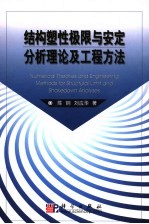
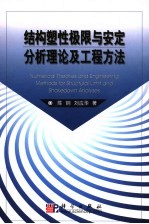
结构塑性极限与安定分析理论及工程方法PDF电子书下载
- 电子书积分:17 积分如何计算积分?
- 作 者:陈钢,刘应华著
- 出 版 社:北京:科学出版社
- 出版年份:2006
- ISBN:9787030152466
- 页数:570 页
第一篇 基础理论与解析方法第一章 绪论 3
1.1 引言 3
1.2 基础理论 5
1.2.1 极限分析理论 5
1.2.2 安定分析理论 6
1.3 分析方法及应用 7
1.3.1 极限分析的基本方法 8
1.3.2 安定分析的基本方法 12
1.3.3 极限与安定分析方法的应用 18
1.4 发展趋势 20
1.4.1 极限分析 20
1.4.2 安定分析 21
1.5 工程应用的迫切需求 23
1.6 本书主要内容 24
参考文献 30
第二章 极限与安定分析的基本理论 52
2.1 极限分析的基本理论 52
2.1.1 塑性极限分析的任务和假设 52
2.1.2 塑性材料的应力-应变曲线及其简化模型 54
2.1.3 极限状态下应力和应变率的特点 56
2.1.4 塑性极限分析的基本原理和方法 58
2.1.5 上、下限定理的推论 62
2.1.6 多组独立外载的情况 63
2.1.7 存在间断场情况下载荷因子的计算 65
2.2 安定分析的基本理论 68
2.2.1 安定问题的提法与任务 68
2.2.2 假设及简化处理 69
2.2.3 残余应力-应变状态的基本性质 70
2.2.4 安定定理 74
参考文献 77
第三章 典型结构极限与安定分析的解析方法 79
3.1 梁和刚架 79
3.1.1 梁和刚架极限分析中的上、下限定理 79
3.1.2 上限法和下限法 80
3.1.3 应用实例 81
3.2 板 85
3.2.1 圆板的基本方程 85
3.2.2 实例分析 88
3.3 薄壳 91
3.3.1 基本假设 91
3.3.2 旋转轴对称夹层壳的极限条件 92
3.3.3 夹层球壳的极限分析 98
3.4 压力管道管件极限载荷的解析解 102
3.4.1 复杂载荷下无缺陷弯管的塑性极限载荷 103
3.4.2 焊制三通塑性极限荷载的工程分析 110
3.5 其他典型结构极限与安定分析解析解 124
参考文献 124
第二篇 数值理论与实验方法第四章 确定极限载荷的弹塑性增量分析原理 129
4.1 确定极限载荷的方法 129
4.2 增量弹塑性有限元 130
4.2.1 增量理论弹塑性有限元 130
4.2.2 求解极限载荷的要点 131
4.3 有限元分析中确定极限载荷的方法 133
4.3.1 确定极限载荷的工程方法 133
4.3.2 有限元分析中确定极限载荷的方法 133
4.4 通用有限元分析软件简介 136
4.5 主要结论 136
参考文献 137
第五章 极限与安定下限分析的数值计算方法 139
5.1 引言 139
5.2 极限与安定载荷下限的降维迭代法 140
5.2.1 下限分析的数学规划格式 140
5.2.2 自平衡应力场空间 145
5.2.3 降维迭代法 147
5.2.4 搜索子空间Br,k的形成 151
5.2.5 优化方法探讨 154
5.2.6 算法的程序实现 164
5.3 极限下限分析的P范数方法 166
5.3.1 极限分析问题的提出 166
5.3.2 极限下限问题的格式 167
5.3.3 下限有限元方法 171
5.4 算例 177
5.4.1 降维迭代法 177
5.4.2 P范数法 181
5.5 主要结论 184
参考文献 185
第六章 极限与安定上限分析的数值计算方法 188
6.1 引言 188
6.2 极限上限分析的无搜索迭代算法 189
6.2.1 加载路径的径向辐射求解方案 189
6.2.2 结构极限上限分析的数学规划格式 190
6.2.3 直接迭代优化算法 191
6.2.4 算法的收敛性证明 194
6.3 理想弹塑性结构安定上限分析的数值方法 197
6.3.1 数学规划格式 197
6.3.2 优化迭代算法 200
6.4 考虑应变强化结构安定上限分析的数值方法 204
6.4.1 数学规划格式 204
6.4.2 优化迭代算法 207
6.5 极限与安定载荷计算的有限元简化算法 211
6.5.1 基于形变理论的弹塑性有限元分析方法 211
6.5.2 结构极限载荷的确定 215
6.6 算例 218
6.6.1 无搜索迭代算法 218
6.6.2 有限元简化算法 225
6.7 主要结论 227
参考文献 228
第七章 多种数值计算方法的主要特点与应用范围 231
7.1 主要特点 231
7.2 应用范围 232
7.3 典型算例计算结果的比较 233
7.4 主要结论 239
参考文献 240
第八章 极限载荷的实验测试方法 241
8.1 实验测试方法简介 241
8.1.1 实验极限载荷定义方法 241
8.1.2 极限载荷实验测试主要步骤 244
8.1.3 材料机械性能测试 244
8.1.4 实验装置与测试方案 244
8.1.5 实验结果分析 245
8.2 含凹坑压力容器应用案例 245
8.2.1 试件的设计与制备 245
8.2.2 材料机械性能测试 248
8.2.3 实验装置和测试方案 250
8.2.4 实验结果和分析 255
8.3 含局部减薄压力管道应用案例 261
8.3.1 试件的设计与制备 261
8.3.2 材料机械性能测试 263
8.3.3 实验装置与测试方案 263
8.3.4 实验结果与分析 264
8.4 主要结论 267
参考文献 268
第三篇 一般工程方法与典型应用案例第九章 工程应用的一般方法 271
9.1 工程背景分析 271
9.2 模型建立与数据准备 271
9.2.1 力学计算模型建立 271
9.2.2 单元选取与网格划分 272
9.2.3 有限元数据前后处理 273
9.3 计算结果验证 274
9.4 影响因素化简 275
9.5 塑性变形过程与失效模式分析 277
9.6 塑性极限与安定载荷数据库建立与分析 278
9.7 计算公式拟合与分析 279
9.8 工程设计与安全评定方法制定 281
9.9 主要结论 283
参考文献 284
第十章 含凹坑缺陷压力容器塑性极限与安定分析 285
10.1 工程背景 285
10.2 模型建立与数据准备 286
10.2.1 力学计算模型建立 286
10.2.2 单元选取与网格划分 289
10.2.3 数据前后处理 292
10.3 计算结果的验证 293
10.4 影响因素化简 299
10.5 塑性变形过程与失效模式的分析和探讨 301
10.5.1 平板表面凹坑 301
10.5.2 球壳表面凹坑 301
10.5.3 圆筒壳表面凹坑 306
10.6 塑性极限荷载数据库的建立和分析 307
10.6.1 平板表面凹坑 307
10.6.2 球壳表面凹坑 308
10.6.3 筒壳表面凹坑 312
10.7 塑性极限载荷的数据拟合与分析 317
10.7.1 平板表面凹坑 317
10.7.2 球壳表面凹坑 317
10.7.3 圆筒壳表面凹坑 319
10.8 安定性分析 321
10.9 含凹坑缺陷压力容器安全评定方法的制定 325
10.9.1 凹坑缺陷控制条件的探讨 325
10.9.2 凹坑缺陷的安全评定 326
10.9.3 凹坑缺陷评定方法与国内外现有规程的比较 331
10.10 主要结论 336
参考文献 338
第十一章 含局部减薄压力管道塑性极限分析 340
11.1 工程背景 340
11.2 模型建立与数据准备 342
11.2.1 力学计算模型建立 342
11.2.2 单元选取与网格划分 343
11.2.3 数据前后处理 343
11.3 计算结果的验证 345
11.4 影响因素化简 348
11.5 塑性变形过程与失效模式的分析 350
11.5.1 单一内压载荷工况 350
11.5.2 单一弯矩工况 352
11.5.3 内压与弯矩组合工况 353
11.6 塑性极限载荷数据库的建立与拟合分析 353
11.6.1 计算方案 353
11.6.2 单一内压载荷工况 354
11.6.3 单一弯矩载荷工况 358
11.6.4 内压与弯矩组合工况 362
11.6.5 其他载荷组合工况 369
11.7 含局部减薄缺陷压力管道直管段评定方法的制定 373
11.7.1 局部减薄缺陷控制条件 373
11.7.2 压力管道直管段体积缺陷安全评定方法 378
11.7.3 本章方法与国内外规范的比较 384
11.8 含局部减薄管道弯头、三通塑性极限分析 386
11.8.1 含局部减薄弯头 387
11.8.2 含局部减薄三通 390
11.9 管系结构内力计算与极限分析软件 394
11.9.1 管系结构内力计算与极限分析软件的基本流程 395
11.9.2 软件的基本组成及其主要功能 395
11.10 主要结论 397
参考文献 398
第十二章 压力管道弯头塑性极限分析 402
12.1 工程背景 402
12.2 弯头塑性极限载荷解析解 402
12.3 模型建立与数据准备 404
12.3.1 力学计算模型建立 404
12.3.2 单元选取与网格划分 406
12.3.3 数据前处理 406
12.4 计算结果的验证 407
12.5 影响因素化简 407
12.5.1 参数的无量纲化 407
12.5.2 弯矩方向的影响 408
12.5.3 约束条件对塑性极限载荷的影响 409
12.5.4 参数取值范围的选择 414
12.6 塑性变形过程与失效模式的分析 414
12.6.1 单一内压载荷工况 414
12.6.2 单一闭合弯矩载荷工况 414
12.6.3 内压与弯矩组合工况 414
12.7 塑性极限载荷及其工程计算方法 415
12.7.1 单一内压和单一弯矩下弯头极限载荷计算公式 415
12.7.2 内压、弯矩组合载荷作用下弯头的塑性极限载荷估算式 418
12.8 主要结论 419
参考文献 420
第十三章 压力容器大开孔接管和压力管道三通塑性极限分析 422
13.1 工程背景 422
13.2 三通塑性极限载荷解析解 423
13.3 模型建立与数据准备 425
13.3.1 力学计算模型建立 425
13.3.2 单元选取与网格划分 428
13.3.3 数据前处理 429
13.4 计算结果的验证 429
13.5 影响因素化简 430
13.5.1 参数的无量纲化 430
13.5.2 强度比参量Ptd的引入 431
13.6 塑性变形过程与失效模式 431
13.6.1 单一内压载荷工况 431
13.6.2 单一面内弯矩载荷工况 432
13.6.3 单一面外弯矩载荷工况 432
13.7 塑性极限载荷及其工程计算方法 433
13.7.1 单一内压工况 433
13.7.2 单一面内弯矩工况 435
13.7.3 单一面外弯矩工况 439
13.8 三通塑性极限载荷数值解与解析解的比较 442
13.8.1 两种方法计算结果偏差的原因分析 442
13.8.2 两种方法主要特点的比较分析 443
13.9 主要结论 444
参考文献 445
第十四章 薄壁圆筒壳双轴热棘轮效应 450
14.1 工程背景 450
14.2 模型建立与基本计算条件 451
14.3 轴向应力作用下双轴热棘轮变形机理 452
14.3.1 轴向压应力情况 452
14.3.2 轴向拉应力情况 464
14.4 双轴力薄壁筒壳热棘轮变形临界限 466
14.4.1 以单轴梁模型为基础的Bree图 466
14.4.2 双轴热棘轮变形临界限的确定 467
14.4.3 无轴力薄壁筒壳 469
14.4.4 轴向拉应力薄壁筒壳 470
14.4.5 轴向压力应力薄壁筒壳 472
14.5 相关规范与Bree图的适用范围及局限性 475
14.6 主要结论 476
参考文献 478
第十五章 典型结构塑性极限与安定载荷及弹塑性应力图谱 479
15.1 本篇各章附图 480
15.2 常见典型结构 491
15.3 工程实际案例 518
附录 典型结构极限与安定分析的解析解 547
一、典型结构的极限分析 547
二、典型结构的安定分析 568
- 《联吡啶基钌光敏染料的结构与性能的理论研究》李明霞 2019
- 《异质性条件下技术创新最优市场结构研究 以中国高技术产业为例》千慧雄 2019
- 《柏里曼人体结构绘画教学描摹本 第2册 头手足结构》杨建飞主编 2019
- 《强度理论与数值极限分析》郑颖人,孔亮,阿比尔的著 2020
- 《认知语言学视野的抽象方位结构研究》曹爽著 2019
- 《无机材料晶体结构学概论》毛卫民编著 2019
- 《数据结构教程》付婷婷,王志海,张磊编著 2019
- 《数据结构 C语言版 第5版》邓文华 2019
- 《RNA折叠结构预测算法与计算复杂性》刘振栋著 2019
- 《中国好字帖 硬笔楷书教程 结构》张鹏涛主编 2016
- 《刘泽华全集 先秦政治思想史 下》刘泽华著;南开大学历史学院编 2019
- 《口译理论研究》王斌华著 2019
- 《陶瓷工业节能减排技术丛书 陶瓷工业节能减排与污染综合治理》罗民华著 2017
- 《郎才女貌》李之华著 1942
- 《最美的时光》桐华著 2020
- 《禅宗精神与后现代精神的“家族相似”》邱紫华著 2019
- 《钢琴演奏与钢琴教学研究》张鲜华著 2018
- 《澳门人家》梁振华著 2019
- 《春日之书》陆烨华著 2019
- 《刘泽华全集 先秦政治思想史 上》刘泽华著;南开大学历史学院编 2019
- 《指向核心素养 北京十一学校名师教学设计 英语 七年级 上 配人教版》周志英总主编 2019
- 《《走近科学》精选丛书 中国UFO悬案调查》郭之文 2019
- 《北京生态环境保护》《北京环境保护丛书》编委会编著 2018
- 《中医骨伤科学》赵文海,张俐,温建民著 2017
- 《美国小学分级阅读 二级D 地球科学&物质科学》本书编委会 2016
- 《指向核心素养 北京十一学校名师教学设计 英语 九年级 上 配人教版》周志英总主编 2019
- 《强磁场下的基础科学问题》中国科学院编 2020
- 《小牛顿科学故事馆 进化论的故事》小牛顿科学教育公司编辑团队 2018
- 《小牛顿科学故事馆 医学的故事》小牛顿科学教育公司编辑团队 2018
- 《高等院校旅游专业系列教材 旅游企业岗位培训系列教材 新编北京导游英语》杨昆,鄢莉,谭明华 2019