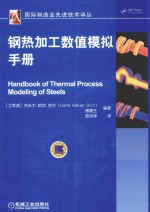
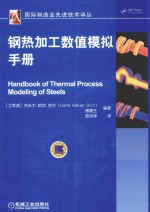
钢热加工数值模拟手册PDF电子书下载
- 电子书积分:16 积分如何计算积分?
- 作 者:(土)杰米尔·哈坎·吉尔(Cemil Hakan Gur),潘健生著
- 出 版 社:北京:机械工业出版社
- 出版年份:2016
- ISBN:9787111531777
- 页数:505 页
第1章 钢热加工过程建模的数学基础 1
1.1 热加工过程的偏微分方程及其求解 1
1.1.1 导热和扩散偏微分方程 1
1.1.2 求解偏微分方程的方法 2
1.2 有限差分法 3
1.2.1 有限差分法原理简介 3
1.2.2 一维传热和扩散偏微分方程的有限差分求解 3
1.2.3 小结 7
1.3 有限单元法 7
1.3.1 简介 8
1.3.2 伽辽金法二维瞬态温度场有限元分析 9
1.3.3 三维瞬态导热的有限元分析 14
1.4 相变量的计算 15
1.4.1 相变与温度的耦合作用 15
1.4.2 扩散型相变 15
1.4.3 马氏体相变 22
1.4.4 应力状态对相变动力学的影响 23
1.5 固体材料的本构方程 24
1.5.1 弹性本构方程 24
1.5.2 弹塑性本构方程 27
1.5.3 黏塑性本构方程 36
1.6 热加工中的计算流体动力学基础 40
1.6.1 简介 40
1.6.2 流体微分控制方程 40
1.6.3 控制方程的通用形式 43
1.6.4 简化后的热加工过程特定流体力学方程 43
1.6.5 控制方程的求解 44
参考文献 46
第2章 建模方法和基本原则 49
2.1 数学建模 49
2.2 控制方程 50
2.3 边界条件和初始条件 52
2.4 控制方程的数值解 53
2.5 有限单元法 54
2.6 有限体积法 63
2.7 蒙特卡罗法 74
2.8 相场法 78
2.9 结束语 80
第3章 钢的热/温加工模型 81
3.1 微观组织概述 81
3.2 流动曲线建模——单道次 81
3.2.1 热加工行为 81
3.2.2 热加工本构模型 84
3.2.3 动态再结晶的开始 85
3.2.4 包含动态再结晶的高级本构模型 86
3.3 静态再结晶 88
3.3.1 Tnr方法 89
3.3.2 静态再结晶建模 91
3.3.3 应变诱发析出模型 96
3.3.4 结合动态再结晶的先进本构模型 100
3.4 晶粒长大 102
3.5 相变和最终的力学性能 103
3.6 温加工 103
3.7 多道次条件的应力-应变和组织建模 104
3.8 先进模拟和建模技术 106
3.8.1 CA元胞自动机模拟 107
3.8.2 MCP模拟 111
3.8.3 相场模拟 114
3.8.4 耦合模拟 115
3.8.5 常见问题 115
参考文献 116
第4章 铸造模拟 118
4.1 引言 118
4.1.1 冶金过程的数值模拟总则 118
4.1.2 铸造工艺模拟的原因及潜力 120
4.1.3 解析模型和数值方法 121
4.2 凝固机制 124
4.2.1 均匀形核 125
4.2.2 非均匀形核 126
4.2.3 晶体长大 126
4.2.4 枝晶长大 128
4.2.5 铸锭的组织和缺陷 131
4.2.6 连铸件的组织和缺陷 134
4.2.7 充型与冒口 136
4.3 工业铸造钢锭和钢坯 144
4.3.1 连铸 144
4.3.2 模铸 146
4.4 铸造模拟的展望 148
4.4.1 充型计算 148
4.4.2 边界条件 150
4.4.3 无量纲分析 151
4.4.4 应力分布预测 152
4.4.5 组织模拟 153
参考文献 155
第5章 工业热处理作业模拟 158
5.1 引言 158
5.1.1 热处理作业数学模型的必要性 158
5.1.2 工业过程模拟和优化:挑战和方法 159
5.1.3 本章结构 160
5.2 工业案例研究:棒材连续退火的工艺模型 160
5.2.1 连续退火作业的背景 160
5.2.2 棒束退火的工艺模型 161
5.2.3 工艺设计:棒束与棒的考虑 162
5.2.4 基于模型调度提高生产率 163
5.3 工业案例研究:冷轧钢卷箱式炉退火的集成模型 164
5.3.1 箱式炉退火的背景 164
5.3.2 箱式炉退火控制的传热模型 165
5.3.3 传热模型的限制:集成模型的必要性 167
5.3.4 箱式退火集成模型:公式和优势 168
5.4 工业案例研究:渗碳作业的成本模型 170
5.4.1 成本模型背景 170
5.4.2 模型公式 171
5.4.3 渗碳作业的最优化 173
5.5 过程模型的在线运用 173
5.5.1 过程模型作为软传感器 173
5.5.2 以模型为基础的过程控制解 174
5.5.3 基于数据的过程模型 175
5.5.4 显微组织介观模型 176
5.6 总结 178
参考文献 178
第6章 淬火模拟 181
6.1 引言 181
6.2 淬火过程中的相变 182
6.3 淬火模拟技术现状 184
6.4 传热建模 187
6.4.1 简介 187
6.4.2 淬火过程中的传热控制方程 191
6.4.3 传热问题的有限单元公式 192
6.5 相变建模 196
6.5.1 简介 196
6.5.2 临界温度的确定 197
6.5.3 扩散型转变动力学模型 199
6.5.4 等温转变模型 199
6.5.5 非等温转变模型 199
6.5.6 马氏体相变模型 203
6.5.7 动力学参数的测定 203
6.5.8 等温转变图中等温动力学参数的提取 203
6.5.9 连续冷却转变图中等温动力学参数的提取 204
6.5.10 应力和塑性对相变的影响 204
6.6 力学相互作用建模 208
6.6.1 简介 208
6.6.2 本构模型 209
6.6.3 混合相整体力学性能预测 211
6.6.4 相变引起的塑性记忆损失 212
6.6.5 力学行为控制方程 212
6.6.6 淬火的热-弹-塑性公式 216
6.6.7 热弹塑性问题的有限元求解 220
6.6.8 相变诱导塑性(TRIP)的模拟 223
6.7 FEA软件实现指南 227
6.7.1 ABAQUS中的实现 227
6.7.2 MSC.MARC中的实现 231
6.8 总结与建议 236
术语 237
参考文献 240
第7章 感应硬化过程模拟 255
7.1 引言 255
7.2 感应热处理概述 257
7.2.1 感应热处理的发展 257
7.2.2 涡旋电流的产生 258
7.2.3 感应加热装置 259
7.2.4 工件的能量吸收 260
7.2.5 感应系统中的电磁效应 262
7.2.6 温度分布 265
7.2.7 感应线圈参数变化 267
7.2.8 感应加热中的电动力 268
7.2.9 淬火和冷却 269
7.3 热处理线圈的建模 270
7.3.1 感应线圈的要求 270
7.3.2 圆柱形线圈 271
7.3.3 其他“标准”热处理线圈 274
7.3.4 特殊热处理线圈 276
7.4 感应硬化系统模拟 277
7.4.1 感应系统的物理过程 277
7.4.2 电磁场 278
7.4.3 材料的电磁性质 280
7.4.4 感应硬化系统中的热力学过程 282
7.4.5 淬火过程的换热 284
7.4.6 物理建模 284
7.5 数值方法 285
7.5.1 概述 285
7.5.2 微分模型 287
7.5.3 有限差分法 289
7.5.4 有限单元法 290
7.5.5 积分方法 294
7.5.6 数值方法比较 298
7.6 关于数值优化 299
7.6.1 感应加热的优化问题 299
7.6.2 数值优化 300
7.6.3 热处理工艺设计 303
7.6.4 车轴硬化优化设计 306
7.7 结论 310
参考文献 310
第8章 激光表面硬化模拟 313
8.1 激光材料加工进展 313
8.2 激光光学和光束特性 319
8.2.1 单透镜聚焦 319
8.2.2 焦距 319
8.2.3 焦数 319
8.2.4 焦点处的光束直径 319
8.2.5 焦深 320
8.2.6 激光束表征 320
8.3 激光吸收率 321
8.3.1 温度的影响 321
8.3.2 吸收测量技术 326
8.4 激光表面硬化 335
8.4.1 激光加热和冷却 335
8.4.2 激光硬化过程中的冶金学 337
8.4.3 钢的奥氏体化 342
8.4.4 硬化深度的数学预测 355
8.4.5 计算温度循环的方法 362
8.4.6 热流模型 365
8.4.7 材料激光硬化和熔化的热分析 371
8.5 激光表面硬化后的残余应力 376
8.5.1 背景 376
8.5.2 热应力和相变应力的测定 377
8.5.3 计算残余应力的简单数学模型 382
8.5.4 用数值模拟方法确定应力 386
8.5.5 评估残余应力分布的简单方法 393
8.5.6 预测硬化轨迹和优化工艺 397
8.5.7 模型应用 400
8.5.8 经激光表面重熔处理的微观组织分析 405
参考文献 413
第9章 表面硬化数值模拟 419
9.1 引言 419
9.2 渗碳表面硬化技术 420
9.3 渗氮和碳氮共渗表面硬化技术 422
9.4 表面硬化模拟的多场耦合 426
9.4.1 模块1)碳和氮同时扩散和析出 427
9.4.2 模块2)传热 433
9.4.3 模块3)相变 434
9.4.4 模块4)应力应变分布 437
9.5 残余应力和工件性能的关系 438
9.6 文献典型实例 439
9.6.1 不同角度楔形板的渗碳工艺 439
9.6.2 纯铁脉冲离子渗氮过程中氮化层的生长及氮在ε-Fe2-3N、γ′-Fe4N和α-Fe中的分布 443
9.6.3 铁素体马氏体双相不锈钢高温气体渗氮过程中马氏体层的生长动力学 444
9.6.4 渗碳钢中多相相变的有限元研究 449
参考文献 454
第10章 热处理和化学热处理计算机模拟的工业应用 460
10.1 阶梯轴的加热CAE 460
10.1.1 三维温度场计算机模拟的实验验证 460
10.1.2 优化加热工艺的CAD技术 461
10.2 复杂形状零件淬火工艺CAE/CAPP 463
10.3 曲轴渗氮畸变控制CAE 465
10.4 气体渗碳CAE/CAPP/CAM 466
10.4.1 齿轮渗碳工艺CAE 466
10.4.2 智能型密封箱式炉生产线CAM 468
10.5 基于计算机模拟的动态可控渗氮技术 473
10.6 热处理设备的智能CAD 474
10.7 大型钢模块淬火冷却虚拟生产 476
10.7.1 P20塑料模具钢淬火工艺模拟与设计 476
10.7.2 静止水淬火 480
10.7.3 小结 481
参考文献 483
第11章 钢热加工过程建模的展望 485
11.1 热加工过程建模与计算机模拟存在的问题 485
11.1.1 工程技术方面的问题 485
11.1.2 基础理论方面的问题 486
11.2 热加工过程建模与计算机模拟的发展趋势 493
11.2.1 材料加工成形的建模与模拟的发展趋势 493
11.2.2 热处理与表面改性的建模与模拟的发展趋势 499
11.2.3 高集成度的产品CAE技术 502
参考文献 503
- 《激光加工实训技能指导理实一体化教程 下》王秀军,徐永红主编;刘波,刘克生副主编 2017
- 《Maya 2018完全实战技术手册》来阳编著 2019
- 《FDS火灾数值模拟》李胜利,李孝斌编著 2019
- 《先进激光加工技能实训》肖海兵主编 2019
- 《高等教育双机械基础课程系列教材 高等学校教材 机械设计课程设计手册 第5版》吴宗泽,罗圣国,高志,李威 2018
- 《慢性呼吸系统疾病物理治疗工作手册》(荷)瑞克·考斯林克(RikGosselink) 2020
- 《战略情报 情报人员、管理者和用户手册》(澳)唐·麦克道尔(Don McDowell)著 2019
- 《实用内科手册》黄清,阮浩航主编 2016
- 《基层医疗卫生机构安全用药手册》黎月玲,熊慧瑜 2019
- 《同仁眼科手册系列 同仁儿童眼病手册》付晶编 2018
- 《剑桥国际英语写作教程 段落写作》(美)吉尔·辛格尔顿(Jill Shingleton)编著 2019
- 《希利尔讲雕塑》(美)维吉尔·莫里斯·希利尔(Virgil Mores Hillyer)著 2019
- 《专属孩子的好习惯赢星书 我会用钱》(英)吉尔斯著 2015
- 《铁型覆砂铸造及其应用》黄列群,潘东杰,沈永华 2019
- 《中国名记者系列丛书 中国名记者 第9卷》柳斌杰,李东东 2019
- 《发育生物学》(芬)S.F.吉尔伯特,(美)M.J.F.巴雷西编者;罗静,岳漫宇,刘晶责编石德利译者 2020
- 《我的同时代人的故事 第1卷》(俄)符拉季米尔·加拉克齐昂诺维奇·柯罗连科著;丰子恺,丰一吟译 2020
- 《为什么迈克尔要穿白袜子》张彦翔,周连杰责编;李力丰译者;(日)野吕英四郎 2020
- 《蓝经幡》诺布朗杰 2018
- 《绘本的力量》(瑞士)玛丽亚·尼古拉杰娃,(美)卡罗尔·斯科特著 2018
- 《指向核心素养 北京十一学校名师教学设计 英语 七年级 上 配人教版》周志英总主编 2019
- 《北京生态环境保护》《北京环境保护丛书》编委会编著 2018
- 《高等教育双机械基础课程系列教材 高等学校教材 机械设计课程设计手册 第5版》吴宗泽,罗圣国,高志,李威 2018
- 《指向核心素养 北京十一学校名师教学设计 英语 九年级 上 配人教版》周志英总主编 2019
- 《高等院校旅游专业系列教材 旅游企业岗位培训系列教材 新编北京导游英语》杨昆,鄢莉,谭明华 2019
- 《中国十大出版家》王震,贺越明著 1991
- 《近代民营出版机构的英语函授教育 以“商务、中华、开明”函授学校为个案 1915年-1946年版》丁伟 2017
- 《新工业时代 世界级工业家张毓强和他的“新石头记”》秦朔 2019
- 《智能制造高技能人才培养规划丛书 ABB工业机器人虚拟仿真教程》(中国)工控帮教研组 2019
- 《AutoCAD机械设计实例精解 2019中文版》北京兆迪科技有限公司编著 2019