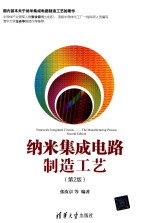
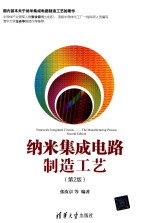
纳米集成电路制造工艺PDF电子书下载
- 电子书积分:15 积分如何计算积分?
- 作 者:张汝京编著
- 出 版 社:北京:清华大学出版社
- 出版年份:2017
- ISBN:9787302452331
- 页数:471 页
第1章 半导体器件 1
1.1 N型半导体和P型半导体 1
1.2 PN结二极管 2
1.2.1 PN结自建电压 3
1.2.2 理想PN结二极管方程 3
1.3 双极型晶体管 4
1.4 金属-氧化物-半导体场效应晶体管 5
1.4.1 线性模型 6
1.4.2 非线性模型 6
1.4.3 阈值电压 8
1.4.4 衬底偏置效应 9
1.4.5 亚阈值电流 9
1.4.6 亚阈值理想因子的推导 9
1.5 CMOS器件面临的挑战 10
1.6 结型场效应晶体管 13
1.7 肖特基势垒栅场效应晶体管 14
1.8 高电子迁移率晶体管 14
1.9 无结场效应晶体管 15
1.9.1 圆柱体全包围栅无结场效应晶体管突变耗尽层近似器件模型 17
1.9.2 圆柱体全包围栅无结场效应晶体管完整器件模型 18
1.9.3 无结场效应晶体管器件制作 20
1.10 量子阱场效应晶体管 22
1.11 小结 26
参考文献 26
第2章 集成电路制造工艺发展趋势 30
2.1 引言 30
2.2 横向微缩所推动的工艺发展趋势 31
2.2.1 光刻技术 31
2.2.2 沟槽填充技术 32
2.2.3 互连层RC延迟的降低 33
2.3 纵向微缩所推动的工艺发展趋势 35
2.3.1 等效栅氧厚度的微缩 35
2.3.2 源漏工程 36
2.3.3 自对准硅化物工艺 37
2.4 弥补几何微缩的等效扩充 37
2.4.1 高k金属栅 38
2.4.2 载流子迁移率提高技术 39
2.5 展望 40
参考文献 40
第3章 CMOS逻辑电路及存储器制造流程 42
3.1 逻辑技术及工艺流程 42
3.1.1 引言 42
3.1.2 CMOS工艺流程 44
3.1.3 适用于高k栅介质和金属栅的栅最后形成或置换金属栅CMOS工艺流程 51
3.1.4 CMOS与鳍式MOSFET(FinFET) 51
3.2 存储器技术和制造工艺 53
3.2.1 概述 53
3.2.2 DRAM和eDRAM 53
3.2.3 闪存 54
3.2.4 FeRAM 56
3.2.5 PCRAM 56
3.2.6 RRAM 57
3.2.7 MRAM 59
3.2.8 3D NAND 59
3.2.9 CMOS图像传感器 62
3.3 无结场效应晶体管器件结构与工艺 64
参考文献 67
第4章 电介质薄膜沉积工艺 71
4.1 前言 71
4.2 氧化膜/氮化膜工艺 71
4.3 栅极电介质薄膜 76
4.3.1 栅极氧化介电层-氮氧化硅(SiOx Ny) 76
4.3.2 高k栅极介质 79
4.4 半导体绝缘介质的填充 83
4.4.1 高密度等离子体化学气相沉积工艺 83
4.4.2 O3-TEOS的亚常压化学气相沉积工艺 87
4.5 超低介电常数薄膜 90
4.5.1 前言 90
4.5.2 RC delay对器件运算速度的影响 91
4.5.3 k为2.7 ~3.0的低介电常数材料 92
4.5.4 k为2.5 的超低介电常数材料 94
4.5.5 刻蚀停止层与铜阻挡层介电常数材料 95
参考文献 96
第5章 应力工程 98
5.1 简介 98
5.2 源漏区嵌入技术 99
5.2.1 嵌入式锗硅工艺 99
5.2.2 嵌入式碳硅工艺 101
5.3 应力记忆技术 103
5.3.1 SMT技术的分类 103
5.3.2 SMT的工艺流程 104
5.3.3 SMT氮化硅工艺介绍及其发展 105
5.4 双极应力刻蚀阻挡层 106
5.5 应力效应提升技术 108
参考文献 110
第6章 金属薄膜沉积工艺及金属化 112
6.1 金属栅 112
6.1.1 金属栅极的使用 112
6.1.2 金属栅材料性能的要求 112
6.2 自对准硅化物 117
6.2.1 预清洁处理 117
6.2.2 镍铂合金沉积 119
6.2.3 盖帽层TiN沉积 120
6.3 接触窗薄膜工艺 121
6.3.1 前言 121
6.3.2 主要的问题 121
6.3.3 前处理工艺 122
6.3.4 PVD Ti 123
6.3.5 TiN制程 124
6.3.6 W plug制程 125
6.4 金属互连 126
6.4.1 前言 126
6.4.2 预清洁工艺 127
6.4.3 阻挡层 128
6.4.4 种子层 131
6.4.5 铜化学电镀 132
6.4.6 洗边和退火 138
6.5 小结 141
参考文献 141
第7章 光刻技术 144
7.1 光刻技术简介 144
7.1.1 光刻技术发展历史 144
7.1.2 光刻的基本方法 144
7.1.3 其他图像传递方法 146
7.2 光刻的系统参数 147
7.2.1 波长、数值孔径、像空间介质折射率 147
7.2.2 光刻分辨率的表示 149
7.3 光刻工艺流程 151
7.4 光刻工艺窗口以及图形完整性评价方法 156
7.4.1 曝光能量宽裕度,归一化图像对数斜率(NILS) 156
7.4.2 对焦深度(找平方法) 158
7.4.3 掩膜版误差因子 161
7.4.4 线宽均匀性 165
7.4.5 光刻胶形貌 172
7.4.6 对准、套刻精度 174
7.4.7 缺陷的检测、分类、原理以及排除方法 180
7.5 相干和部分相干成像 183
7.5.1 光刻成像模型,调制传递函数 183
7.5.2 点扩散函数 193
7.5.3 偏振效应 195
7.5.4 掩膜版三维尺寸效应 198
7.6 光刻设备和材料 198
7.6.1 光刻机原理介绍 198
7.6.2 光学像差及其对光刻工艺窗口的影响 201
7.6.3 光刻胶配制原理 205
7.6.4 掩膜版制作介绍 208
7.7 与分辨率相关工艺窗口增强方法 210
7.7.1 离轴照明 210
7.7.2 相移掩膜版 212
7.7.3 亚衍射散射条 215
7.7.4 光学邻近效应修正 219
7.7.5 二重图形技术 221
7.7.6 浸没式光刻 223
7.7.7 极紫外光刻 224
参考文献 225
第8章 干法刻蚀 229
8.1 引言 229
8.1.1 等离子刻蚀 229
8.1.2 干法刻蚀机的发展 229
8.1.3 干法刻蚀的度量 232
8.2 干法刻蚀建模 234
8.2.1 基本原理模拟 234
8.2.2 经验模型 236
8.3 先进的干法刻蚀反应器 240
8.3.1 泛林半导体 240
8.3.2 东京电子 241
8.3.3 应用材料 241
8.4 干法刻蚀应用 242
8.4.1 浅槽隔离(STI)刻蚀 243
8.4.2 多晶硅栅刻蚀 243
8.4.3 栅侧墙刻蚀 247
8.4.4 钨接触孔刻蚀 249
8.4.5 铜通孔刻蚀 252
8.4.6 电介质沟槽刻蚀 256
8.4.7 铝垫刻蚀 259
8.4.8 灰化 261
8.4.9 新近出现的刻蚀 262
8.5 先进的刻蚀工艺控制 266
参考文献 267
第9章 集成电路制造中的污染和清洗技术 270
9.1 IC制造过程中的污染源 270
9.2 IC污染对器件的影响 270
9.3 晶片的湿法处理概述 272
9.3.1 晶片湿法处理的要求 272
9.3.2 晶片湿法处理的机理 272
9.3.3 晶片湿法处理的范围 273
9.4 晶片表面颗粒去除方法 273
9.4.1 颗粒化学去除 273
9.4.2 颗粒物理去除 274
9.5 制程沉积膜前/后清洗 276
9.6 制程光阻清洗 277
9.7 晶片湿法刻蚀技术 279
9.7.1 晶片湿法刻蚀过程原理 280
9.7.2 硅湿法刻蚀 280
9.7.3 氧化硅湿法刻蚀 280
9.7.4 氮化硅湿法刻蚀 282
9.7.5 金属湿法刻蚀 283
9.8 晶背/边缘清洗和膜层去除 284
9.9 65nm和45nm以下湿法处理难点以及HKMG湿法应用 286
9.9.1 栅极表面预处理 286
9.9.2 叠层栅极:选择性刻蚀和清洗 287
9.9.3 临时poly-Si去除 290
9.10 湿法清洗机台及其冲洗和干燥技术 291
9.10.1 单片旋转喷淋清洗机 291
9.10.2 批旋转喷淋清洗机 292
9.10.3 批浸泡式清洗机 293
9.11 污染清洗中的测量与表征 294
9.11.1 颗粒量测 294
9.11.2 金属离子检测 295
9.11.3 四探针厚度测量 295
9.11.4 椭圆偏光厚度测量 295
9.11.5 其他度量 296
参考文献 296
第10章 超浅结技术 298
10.1 简介 298
10.2 离子注入 298
10.3 快速热处理工艺 303
参考文献 307
第11章 化学机械平坦化 311
11.1 引言 311
11.2 浅槽隔离抛光 312
11.2.1 STI CMP的要求和演化 312
11.2.2 氧化铈研磨液的特点 313
11.2.3 固定研磨粒抛光工艺 314
11.3 铜抛光 317
11.3.1 Cu CMP的过程和机理 317
11.3.2 先进工艺对Cu CMP的挑战 319
11.3.3 Cu CMP产生的缺陷 320
11.4 高k金属栅抛光的挑战 324
11.4.1 CMP在高k金属栅形成中的应用 324
11.4.2 ILD? CMP的方法及使用的研磨液 325
11.4.3 Al CMP的方法及使用的研磨液 326
11.5 GST抛光(GST CMP) 326
11.5.1 GST CMP的应用 326
11.5.2 GST CMP的挑战 327
11.6 小结 327
参考文献 327
第12章 器件参数和工艺相关性 329
12.1 MOS电性参数 329
12.2 栅极氧化层制程对MOS电性参数的影响 330
12.3 栅极制程对MOS电性参数的影响 331
12.4 超浅结对MOS电性参数的影响 331
12.5 金属硅化物对MOS电性参数的影响 332
12.6 多重连导线 333
第13章 可制造性设计 334
13.1 介绍 334
13.2 DFM技术和工作流程 337
13.2.1 光刻DFM 337
13.2.2 Metal-1图形的例子 339
13.3 CMP DFM 341
13.4 DFM展望 343
参考文献 344
第14章 半导体器件失效分析 346
14.1 失效分析概论 346
14.1.1 失效分析基本原则 346
14.1.2 失效分析流程 347
14.2 失效分析技术 350
14.2.1 封装器件的分析技术 350
14.2.2 开封技术 352
14.2.3 失效定位技术 353
14.2.4 样品制备技术 365
14.2.5 微分析技术 366
14.2.6 表面分析技术 376
14.3 案例分析 378
参考文献 383
第15章 集成电路可靠性介绍 384
15.1 热载流子效应(HCI) 385
15.1.1 HCI的机理 385
15.1.2 HCI寿命模型 385
15.2 负偏压温度不稳定性(NBTI) 388
15.2.1 NBTI机理 388
15.2.2 NBTI模型 388
15.3 经时介电层击穿(TDDB) 391
15.4 电压斜坡(V-ramp)和电流斜坡(J-ramp)测量技术 391
15.5 氧化层击穿寿命预测 393
15.6 电迁移 393
15.7 应力迁移 394
15.8 集成电路可靠性面临的挑战 395
15.9 结论 396
第16章 集成电路测量 397
16.1 测量系统分析 397
16.1.1 准确性和精确性 397
16.1.2 测量系统的分辨力 397
16.1.3 稳定分析 398
16.1.4 位置分析 398
16.1.5 变异分析 399
16.1.6 量值的溯源、校准和检定 402
16.2 原子力显微镜 402
16.2.1 仪器结构 402
16.2.2 工作模式 403
16.3 扫描电子显微镜 404
16.4 椭圆偏振光谱仪 406
16.5 统计过程控制 410
16.5.1 统计控制图 411
16.5.2 过程能力指数 415
16.5.3 统计过程控制在集成电路生产中的应用 416
参考文献 417
第17章 良率改善 418
17.1 良率改善介绍 418
17.1.1 关于良率的基础知识 418
17.1.2 失效机制 422
17.1.3 良率学习体系 425
17.2 用于良率提高的分析方法 431
17.2.1 基本图表在良率分析中的应用 431
17.2.2 常用的分析方法 435
17.2.3 系统化的良率分析方法 437
第18章 测试工程 440
18.1 测试硬件和程序 440
18.1.1 测试硬件 440
18.1.2 测试程序 440
18.1.3 缺陷、失效和故障 441
18.2 储存器测试 442
18.2.1 储存器测试流程 442
18.2.2 测试图形 442
18.2.3 故障模型 443
18.2.4 冗余设计与激光修复 443
18.2.5 储存器可测性设计 444
18.2.6 老化与测试 445
18.3 IDDQ测试 445
18.3.1 IDDQ测试和失效分析 446
18.3.2 IDDQ测试与可靠性 446
18.4 数字逻辑测试 446
18.5 可测性设计 448
18.5.1 扫描测试 448
18.5.2 内建自测试 449
参考文献 450
第19章 芯片封装 451
19.1 传统的芯片封装制造工艺 451
19.1.1 减薄(Back Grind) 451
19.1.2 贴膜(Wafer Mount) 451
19.1.3 划片(Wafer Saw) 451
19.1.4 贴片(Die Attach) 453
19.1.5 银胶烘焙(Epoxy Curing) 454
19.1.6 打线键合(Wire Bond) 455
19.1.7 塑封成型(压模成型,Mold) 457
19.1.8 塑封后烘焙(Post Mold Curing) 459
19.1.9 除渣及电镀(Deflash and Plating) 459
19.1.10 电镀后烘焙(Post Plating Baking) 460
19.1.11 切筋整脚成型(Trim/From) 460
19.2 大电流的功率器件需用铝线键合工艺取代金线键合工艺 462
19.3 QFN的封装与传统封装的不同点 463
19.4 铜线键合工艺取代金线工艺 464
19.5 立体封装(3D Package)形式简介 464
19.5.1 覆晶式封装(Flip-Chip BGA) 464
19.5.2 堆叠式封装(Stack Multi-chip package) 465
19.5.3 芯片覆晶式级封装(WLCSP) 465
19.5.4 芯片级堆叠式封装(TSV package) 466
参考文献 467
- 《莎士比亚悲剧集》威廉·莎士比亚 2019
- 《莎士比亚戏剧精选集》(英)威廉·莎士比亚(William Shakespeare)著 2020
- 《乐队伴奏长笛世界名曲集 4》芭芭拉·哈斯勒-哈瑟 2017
- 《柏拉图文艺对话集》(古希腊)柏拉图著 2018
- 《民国时期医药卫生文献集成 37》路丽明编 2019
- 《乐队伴奏长笛世界名曲集 1》芭芭拉·吉斯勒-哈瑟 2017
- 《中国生态系统定位观测与研究数据集 森林生态系统卷 云南西双版纳》邓晓保·唐建维 2010
- 《民国时期医药卫生文献集成 19》路丽明编 2019
- 《抗战三部曲 国防诗歌集》蒲风著 1937
- 《莎士比亚喜剧悲剧集》冯一兵责任编辑;(英国)威廉·莎士比亚 2019
- 《市政工程基础》杨岚编著 2009
- 《家畜百宝 猪、牛、羊、鸡的综合利用》山西省商业厅组织技术处编著 1959
- 《《道德经》200句》崇贤书院编著 2018
- 《高级英语阅读与听说教程》刘秀梅编著 2019
- 《计算机网络与通信基础》谢雨飞,田启川编著 2019
- 《看图自学吉他弹唱教程》陈飞编著 2019
- 《法语词汇认知联想记忆法》刘莲编著 2020
- 《培智学校义务教育实验教科书教师教学用书 生活适应 二年级 上》人民教育出版社,课程教材研究所,特殊教育课程教材研究中心编著 2019
- 《国家社科基金项目申报规范 技巧与案例 第3版 2020》文传浩,夏宇编著 2019
- 《流体力学》张扬军,彭杰,诸葛伟林编著 2019
- 《大学计算机实验指导及习题解答》曹成志,宋长龙 2019
- 《指向核心素养 北京十一学校名师教学设计 英语 七年级 上 配人教版》周志英总主编 2019
- 《大学生心理健康与人生发展》王琳责任编辑;(中国)肖宇 2019
- 《大学英语四级考试全真试题 标准模拟 四级》汪开虎主编 2012
- 《大学英语教学的跨文化交际视角研究与创新发展》许丽云,刘枫,尚利明著 2020
- 《北京生态环境保护》《北京环境保护丛书》编委会编著 2018
- 《复旦大学新闻学院教授学术丛书 新闻实务随想录》刘海贵 2019
- 《大学英语综合教程 1》王佃春,骆敏主编 2015
- 《大学物理简明教程 下 第2版》施卫主编 2020
- 《指向核心素养 北京十一学校名师教学设计 英语 九年级 上 配人教版》周志英总主编 2019