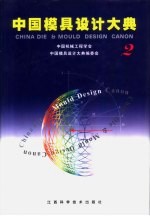
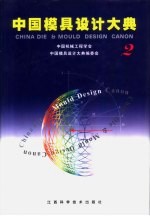
中国模具设计大典 第2卷 轻工模具设计PDF电子书下载
- 电子书积分:38 积分如何计算积分?
- 作 者:李德群,唐志玉主编;中国机械工程学会,中国模具设计大典编委会编
- 出 版 社:南昌:江西科学技术出版社
- 出版年份:2003
- ISBN:7539019492
- 页数:1607 页
第8篇 塑料模设计基础 3
第1章 概论 3
1 塑料模功能 3
2 塑料模现状 3
3 塑料模发展趋势 4
3.1 注塑模CAD实用化 4
3.2 挤塑模CAD的开发 4
3.3 压模CAD的探索 4
3.5 塑料模CAD/CAE/CAM集成化 5
3.4 塑料模专用钢材系列化 5
3.6 塑料模标准化 6
4 塑料模分类 6
4.1 注塑模 6
4.2 压模 6
4.3 传递模 6
4.4 挤塑模 6
4.5 中空吹塑模 6
4.6 热成形模具 6
3 连续性方程 7
2.2 不稳定流动 7
2.1 稳定流动 7
2 流体流动状态 7
1 概述 7
第2章 流体流动与基本方程 7
4 动量方程 8
4.1 欧拉运动方程 8
4.2 奈维-斯托克斯方程 9
5 能量方程 10
6 本构方程 11
1.2 塑料组成 13
1.1 塑料应用 13
1 概述 13
第3章 塑料性能 13
1.3 塑料分类 14
1.4 塑料命名 15
1.5 塑料特性 21
2 塑料力学性能 60
2.1 强度和刚度 60
2.2 应力应变特性 60
2.3 蠕变和应力松弛 60
2.4 塑料韧性 60
3.2 导热系数 61
3 塑料热性能 61
3.1 密度与质量体积 61
2.6 表面性能 61
2.5 疲劳性能 61
3.3 比热容 62
3.4 热扩散率 62
3.5 比焓 63
3.6 不流动温度 63
3.7 线膨胀系数 63
4 黏性流动行为 65
4.1 牛顿黏性定律 65
4.2 非牛顿流体 65
4.3 影响黏性流动因素 67
4.4 熔体流动幂律模型 71
4.5 状态方程 73
5 熔体弹性表现 73
5.1 入口效应 73
5.2 出模膨胀 74
5.3 熔体破裂 74
6 塑料可加工性能 74
6.1 流动性 74
6.2 收缩性 75
6.3 结晶性 76
6.4 取向性 77
6.6 硬化特性 78
6.5 吸湿性 78
第4章 塑料熔体流动行为 80
1 概述 80
2 圆形流道 80
2.1 等截面圆形流道 80
2.2 圆锥形流道 81
2.3 非等温流动 82
2.4 几点结论 84
3 矩形流道 89
3.1 等截面矩形流道 89
3.2 变截面矩形流道 91
3.3 矩形流道通解 92
3.4 非等温流动 93
4 异形流道 94
4.1 多边形流道 94
4.2 三角形流道 96
4.3 椭圆形流道 97
4.4 圆环隙流道 97
4.5 非规则截面流道 100
5 管隙中的拖曳流动 103
5.1 平行板拖曳流动 103
5.2 周向拖曳流动 105
5.3 轴向拖曳流动 105
6 有限元法(F.E.M.)分析 106
第5章 塑件结构设计工艺性 111
1 概述 111
2 塑件常用成形方法 111
3 压塑、传递与注塑成形塑件设计 111
3.1 侧面避免凸凹 111
3.2 脱模斜度 113
3.3 塑件壁厚 115
3.4 加强肋 117
3.7 孔的设计 118
3.6 支承面 118
3.5 圆角 118
3.8 凸台与角撑 122
3.9 边缘、平面与拱底 122
3.10 螺纹设计 123
3.11 花纹设计 125
3.12 文字、标记与符号 128
3.13 嵌件设计 128
3.14 其他注塑件设计 133
4 挤塑型材设计 139
4.1 管材设计 141
4.2 异型材设计 145
4.3 共挤复合型材设计 150
5 旋转成形塑件设计 151
5.1 塑件壁厚 152
5.2 形状设计 152
5.3 圆角半径 153
5.4 脱模斜度 153
5.5 外观设计 153
5.6 合模线 153
6 浇铸成形塑件设计 153
9 塑件尺寸精度 154
9.1 影响因素 154
8 搪塑成形塑件设计 154
7 浸渍成形塑件没计 154
9.2 塑件公差 156
9.3 塑件精度 160
10 塑件设计CAD 163
10.1 概述 163
10.2 塑件设计目录编制 167
10.3 塑件设计诸要素 169
10.4 塑件CAD举例 169
2 塑料干燥 172
2.1 塑料干燥特性 172
1 概述 172
第6章 塑料配制与着色 172
2.2 塑料干燥方法 174
3 塑料输送 175
3.1 气力输送类型 175
3.2 气力输送装置 176
4 塑料混合 177
4.1 混合机理 177
4.2 混合程度 178
5 塑料配方设计 180
5.1 配方表示方法 180
5.2 塑料配方(质量分数)举例 181
6 塑料着色 188
6.1 塑料着色剂 188
6.2 着色剂选择 189
6.3 塑料着色技术 189
7 色彩管理与配色 195
7.1 色彩表示方法 195
7.2 色彩管理硬件 196
7.3 色彩管理软件 197
7.4 计算机调色 198
7.5 塑料制品配色 198
2 压塑成形 200
1 概述 200
第7章 塑料成形加工基本方法 200
2.1 预压 201
2.2 预热 202
2.3 工艺控制 205
3 传递成形 208
3.1 原料 208
3.2 传递成形特点 209
3.3 传递成形设备 209
3.4 传递成形应用 210
3.5 成形工艺过程 210
3.6 主要工艺参数 210
3.8 传递成形类型 211
3.7 制品缺陷分析 211
4 注塑成形 213
4.1 成形工艺过程 213
4.2 常用塑料注塑成形 219
4.3 热固性塑料注塑成形 222
4.4 气体辅助注塑成形 226
4.5 反应注塑成形 228
5 挤出成形 229
5.1 管材成形 230
5.2 吹塑薄膜 234
5.3 棒材成形 237
5.4 异型材成形 241
5.5 板片材和平膜成形 246
6 吹塑成形 254
6.1 吹塑原理 254
6.2 吹塑方法 254
6.3 吹塑材料 255
6.4 吹塑工艺控制 259
7 热成形 263
7.1 热成形概念 263
7.2 热成形应用 263
7.3 热成形装备 265
7.4 热成形方法 266
8 铸塑成形 268
8.1 静态铸塑 268
8.2 嵌铸成形 279
8.3 离心铸塑 281
8.4 流延铸塑 281
8.5 搪铸成形 282
第8章 模腔饰纹加工技术 285
1 概述 285
2 画稿与制版 285
2.1 画稿设计 285
2.2 照相制版 285
2.3 电脑制版 296
3.1 直接照相 297
3 模腔饰纹制作 297
3.2 转移照相 300
3.3 转换照相 302
4 模腔饰纹蚀刻 305
4.1 蚀刻方法及材料 305
4.2 饰纹蚀刻 305
4.3 去膜与油封 306
4.4 饰纹图案修复 306
参考文献 306
1 注射模组成、分类与结构 309
1.1 注射模组成 309
第9篇 注射模设计 309
第1章 注射模设计与成形过程概述 309
1.2 注射模分类 310
1.3 注射模结构 310
2 注射成形过程及其影响因素 313
2.1 注射成形过程 313
2.2 注射成形工艺的影响因素 315
3 注射模的设计步骤 316
3.1 模具设计的前期工作 316
3.2 模具设计的一般步骤 317
3.3 注射模CAD/CAM系统的工作流程 318
1 浇注系统的组成及设计原则 322
1.1 浇注系统的流变学概念 322
第2章 浇注系统设计 322
1.2 浇注系统的组成与作用 323
1.3 浇注系统的设计原则 323
2 流道及浇口设计 324
2.1 流道设计 324
2.2 浇口设计 329
2.3 型腔压力估算 340
3 浇注系统的平衡进料 348
3.2 非平衡式浇注系统 349
3.1 平衡式浇注系统 349
第3章 分型面、排气槽及型腔布置 355
1 分型面设计 355
1.1 分型面的类型 355
1.2 选择分型面的原则 358
2 排气槽设计 358
2.1 排气槽的作用 358
2.2 排气槽设计方法 361
2.3 排气槽截面尺寸计算 361
3 型腔布置 362
3.1 型腔数目的确定 362
3.2 多型腔的排列 363
第4章 成形零件设计 364
1 成形零件结构设计 364
1.1 凹模结构设计 364
1.2 型芯和成形杆的结构设计 365
1.3 螺纹型芯和型环的结构设计 367
2 成形零件钢材选用 368
2.1 成形零件对钢材的要求 368
2.2 注射模常用钢种 368
3 成形零件工作尺寸计算 370
3.1 工作尺寸分类和规定 370
3.2 影响制品尺寸误差的因素及其控制 371
3.3 成形零件工作尺寸计算方法 374
4 成形零件的力学计算 383
4.1 规则凹模及垫板的强度和刚度计算 383
4.2 刚度和强度条件计算公式 385
4.3大型模具刚度计算公式及示例 386
4.4 型芯偏移量计算 390
第5章 导向与定位机构设计 395
1 导向机构的功用 395
2 导向机构设计 395
2.1 导柱设计 395
2.3 导柱和导套的应用实例 397
2.2 导套设计 397
3 定位机构设计 398
3.1 定位圈设计 398
3.2 定位机构设计 400
第6章 脱模机构设计 402
1 设计原则及分类 402
1.1 脱模机构的组成 402
1.2 设计原则 402
1.3 脱模机构分类 402
2.1 简单估算法 403
2 脱模力计算 403
2.2 薄壁制品脱模力的分析计算 405
2.3 厚壁制品脱模力的分析计算 409
2.4 环形侧凹制品的脱模力计算 410
3 简单脱模机构 410
3.1 推杆脱模机构 410
3.2 推管脱模机构 415
3.3 推件板脱模机构 417
3.4 其他脱模机构 419
3.5 推出零件尺寸的确定 420
4.1 气(液)压二级脱模机构 422
4.2 单推板二级脱模机构 422
4 二级脱模机构 422
4.3 双推板二级脱模机构 424
5 定模脱模和双脱模机构 425
5.1 定模脱模机构 425
5.2 双脱模机构 426
6 顺序脱模机构 426
7 浇注系统凝料脱出机构 429
7.1 单分型面模县浇注系统凝料脱出 429
7.2 双分型商模具浇注系统凝料脱出 430
8 螺纹制品脱模机构 431
8.1 非旋转脱模 432
8.2 模内旋转脱模 433
8.3 螺纹脱模力矩和功率计算 435
第7章 侧向分型与抽芯机构设计 437
1 侧抽机构的分类 437
2 抽拔距与抽拔力 437
2.1 抽拔距 437
2.2 抽拔力 437
3 机动侧抽机构 438
3.1 弹簧驱动 438
3.2 斜销驱动 438
3.3 弯销驱动 447
3.4 斜滑槽驱动 448
3.5 斜滑块驱动 449
3.6 齿条驱动 451
4 液压或气动侧抽机构 453
5 手动侧抽机构 453
5.1 模内进行 453
5.2 模外进行 454
第8章 注射模温度调节系统 455
1 模具温度调节的必要求 455
1.1 模具温度调节对制品质量的影响 455
1.2 模具温度调节对生产效率的影响 455
2.1 一维导热微分方程的求解 456
2 冷却时间的计算 456
2.2 无定型塑料厚壁制品冷却时间计算公式 457
2.3 无定型塑料薄壁制品冷却时间计算公式 458
2.4 结晶型塑料的冷却时间计算公式 458
3 冷却系统的计算 459
3.1 冷却系统的简略计算 459
3.2 冷却系统的详细计算 461
4 冷却系统的设计原则 468
5 冷却回路布置 470
5.1 凹模冷却回路 470
5.2 型芯冷却回路 472
6.2 加热功率计算 474
6.1 加热装置设计 474
6 模具的加热 474
第9章 注射模与注射机的关系 476
1 注射机的组成与分类 476
1.1 注射机的组成 476
1.2 注射机的分类 476
2 注射机的技术参数 478
2.1 国产sZ系列注射机主要技术参数 478
2.2 技术参数的说明 480
3 工艺与安装参数校核 481
3.1 工艺参数校核 481
3.2 安装参数校核 482
3.3 开模行程和推出机构的校核 483
第10章 无流道凝料注射模设计 485
1 无流道凝料注射成形的特点 485
1.1 无流道凝料注射成形的优缺点 485
1.2 无流道凝料注射成形的适用范围 485
2 绝热流道注射模设计 486
2.1 井坑式喷嘴注射模 486
2.2 多型腔绝热流道注射模 487
3 热流道注射模设计 488
3.1 延伸式喷嘴注射模 488
3.2 外加热式多型腔热流道注射模 488
3.4 阀式浇口热流道注射模 493
3.3 内加热式多型腔热流道注射模 493
4 温流道注射模设计 494
4.1 成形原理 494
4.2 模具设计 495
第11章 其他注射模设计 496
1 热固性塑料注射模设计 496
1.1 热固性塑料注射成形概述 496
1.2 热固性塑料注射成形工艺过程 496
1.3 热固性塑料注射成形工艺特点 497
1.4 热固性塑料注射模具设计要点 498
2.1 低发泡注射成形方法 503
2 低发泡塑料注射成形 503
2.2 低发泡注射模设计要点 505
2.3 低发泡塑料注射模结构示例 506
3 反应注射成形 507
3.1 反应注射成形过程及其特点 507
3.2 反应注射成形设备 508
3.3 模具设计的工艺要求与设计要点 508
4 共注射成形 510
4.1 双色注射法 510
5.1 气体辅助注射成形过程 511
5 气体辅助注射成形 511
4.2 双层注射法 511
5.2 气体辅助注射成形工艺分类 512
5.3 气体辅助注射成形设备 514
5.4 气体辅助注射成形技术的特点 515
第12章 塑料注射模典型结构 517
2.2 供货周期 545
2.5 模具寿命 545
2.4 技术含量 545
2.3 市场状况 545
2.1 生产成本 545
2 影响价格的因素 545
1 概述 545
第13章 价格估算 545
3 简易估算法 546
3.1 经验估算法 546
3.2 材料价格系数法 546
3.3 类比法 546
4 详细计算法 546
4.1 模具价格构成 547
4.2 模具价格计算方法 547
4.3 模具价格计算公式 547
2.2 容量校核 554
2.1 类型选择 554
2.3 合模力校核 554
1 概述 554
第14章 试模与验收 554
2 注塑机选用 554
2.4 模具厚度校核 557
2.5 推出机构校核 557
2.6 开模行程校核 557
2.7 模具安装尺寸校核 558
2.8 注塑机工作状态检查 561
3 模具安装 561
3.1 模具预检 561
3.3 模具吊装 562
3.2 锁模机构调整 562
3.4 模具紧固 563
3.5 空循环试验 564
3.6 配套部分安装 564
3.7 模具预热 564
4 试模条件确定 565
4.1 塑料选用 565
4.2 工艺条件选择 567
4.3 试模工艺条件倾向性 572
5 成形缺陷与对策 573
6.1 试模记录 576
6 试模结论 576
6.2 模具修整 579
6.3 总体评价 581
7 模具验收 582
7.1 质量控制检查点 582
7.2 工序质量检查 582
7.3 制品检验 583
7.4 模具检验 585
2.2 选择成形设备 590
2.4 合理确定工艺条件 590
2.3 正确安装模具 590
2 使用与维护 590
2.1 模具检查 590
1 概述 590
第15章 模具使用、管理与维修 590
2.5 精心操作 591
2.6 保养和维护 592
3 模具管理 592
3.1 常规管理 592
3.2 计算机管理 595
4 模具维修 597
4.1 常用修理方法 597
4.2 磨损及修复 598
4.3 意外损坏及修复 599
4.4 除锈 600
4.5 除垢 600
第16章 注射模CAD 601
1 注射模CAD概述 601
1.1 CAD的概念 601
1.2 注射模结构CAD的内容 602
1.3 注射模CAD技术的国内外发展状况 602
1.4 注射模CAD技术的应用趋势 603
2 注射模CAD软件开发的技术基础 604
3.1 注射模结构CAD中数据类型 606
3 注射模结构CAD中的数据处理 606
3.2 数据流图 607
3.3 数据管理技术 609
4 注射模CAD中的几何造型 610
4.1 几何造型方法 610
4.2 形体模式与数据结构 612
5 流道系统交互设计 615
5.1 流道分类及平衡分析准则 615
5.2 流道系统平衡设计 616
6.1 校核准则 620
6.2 计算方法 620
6 结构零件强度与刚度校核 620
7 专家系统在注射模中的应用 623
7.1 专家系统结构简介 623
7.2 在注射模中的应用 623
8 注射模CAD的开发与应用 624
8.1 二维CAD系统 624
8.2 三维CAD系统 625
第17章 注射模CAE 629
1 概述 629
1.1 CAE的概念 629
1.2 CAE的发展概况 629
2 充模过程的数学描述 630
1.3 CAE的发展趋势 630
2.1 充模过程的基本方程 631
2.2 基本方程的简化 632
2.3 数学模型及边界条件 632
2.4 塑料熔体的黏度模型 634
3 一维流动分析 634
4 二维流动分析 635
5 三维流动分析 636
5.1 压力场有限元方程 637
5.2 熔体流动前沿位置的确定 638
5.3 温度场计算 638
5.4 数值计算过程 639
6 保压过程分析 640
7 基于实体/表面模型的三维真实感流动保压分析 643
7.1 传统CAE软件的局限性 643
7.2 理论与实现 643
7.3 软件开发 644
8 塑料材料流变参数的拟合 647
8.1 塑料材料流变参数的重要性 647
8.2 流变数据的测定 648
8.3 流变参数的拟合 648
9 冷却过程分析 651
8.4 应用实例 651
9.1 一维冷却分析 652
9.2 二维冷却分析 654
9.3 三维冷却分析 656
10 注射模CAE的开发与应用 658
10.1 充模流动模拟软件 658
10.2 冷却模拟软件 660
参考文献 662
2 压模结构与类型 665
1 概述 665
2.1 压模结构 665
第1章 压模设计 665
第10篇 压模与传递模设计 665
2.2 压模分类 666
3 压模与压机的关系 669
3.1 压机技术规范 669
3.2 工艺参数校核 673
4 压模结构设计 677
4.1 模腔总体设计 677
4.2 加料室设计 683
5 模腔设计 685
5.1 凹模结构设计 685
5.2 凸模结构设计 687
5.3 型芯结构设计 689
5.4 螺纹型芯与型环设计 690
5.5 导向零件设计 694
6 脱模机构设计 695
6.1 移动式压模脱模机构 695
6.2 固定式压模脱模机构 697
6.3 半移动式压模脱模机构 699
6.4 尾轴结构与尺寸 699
7 侧向抽芯机构设计 701
7.1 手动侧抽芯机构 701
7.2 机动侧抽芯机构 703
8 通用模架 704
9.1 压模加热 705
9 压模加热与冷却 705
9.2 压模冷却 707
10 压模结构实例 708
第2章 泡沫塑料压模设计 713
1 概述 713
2 坯料预压模 713
3 聚苯乙烯泡沫塑件压模 714
3.1 塑件设计 714
3.2 模塑工艺过程 715
3.4 典型结构 716
3.3 模具分类 716
3.5 结构设计 717
4 泡沫塑料压模结构实例 722
第3章 压锭模设计 726
1 概述 726
2 压锭模设计要点 727
3 压锭模典型结构 727
4 等压成形压锭模 729
1.2 塑件质量特点 730
1.1 成形工艺特点 730
1.3 模具结构特点 730
1 概述 730
第4章 传递模设计 730
1.4 熔体觅模流动特点 731
2 传递模结构 731
2.1 传递成形实施方法 731
2.2 传递模结构 731
3 传递模分类 732
3.1 罐式传递模 732
3.2 柱塞式传递模 733
3.3 螺杆预塑式传递模 734
4 传递模设计 734
4.1 加料室设计 734
4.2 压料柱塞设计 738
4.3 浇注系统设计 740
4.4 排气隙设计 744
5 传递模结构实例 745
参考文献 752
第11篇 挤塑模设计 755
第1章 概论 755
1 概述 755
1.1 挤塑成形工艺过程 755
1.2 挤塑模功能与作用 755
3 工艺装置 756
2.5 在工艺特性方面 756
2.4 在生产操作方面 756
2.2 在热力学方面 756
2.1 在流变学方面 756
2 挤塑模设计涉及的问题 756
2.3 在模具制造方面 756
3.1 挤塑机性能 757
3.2 联接器设计 760
3.3 栅板与滤网设计 762
4 挤塑模设计程序 764
2 棒材成形模设计 767
2.2 棒材模参数的确定 767
2.1 棒材模结构类型 767
1 概述 767
第2章 棒材模设计 767
3 棒材定型模设计 770
3.1 定型模结构设计 770
3.2 定型模设计要点 771
4 焊条模设计 771
第3章 管材模设计 773
1 概述 773
2 管材模类型 774
2.1 中心供料管材模 775
2.2 侧向供料管材模 775
2.3 螺旋供料管材模 775
2.4 筛孔供料管材模 776
3.1 薄壁管材 777
3.2 厚壁管材 777
3 成形段长度 777
4.2 分流锥尺寸 778
5 管材定型模设计 778
4.3 拉伸比 778
5.1 定径方法 778
4.1 压缩区尺寸 778
4 管材模结构参数 778
3.4 经验确定法 778
3.3 芯模半径 778
5.2 定径套尺寸及材料 779
第4章 平缝模设计 781
1 概述 781
2 平缝模结构设计 781
3 T形流道平缝模 782
3.1 T形流道结构形式 782
3.2 T形流道模拟分析 782
3.3 熔体流动均匀性的考虑 783
3.4 流道尺寸设计 783
3.5 熔体停留时间分析 787
4.2 流道尺寸设计 788
4 鱼尾形流道平缝模 788
4.1 熔体流动模拟分析 788
5 衣架式流道平缝模 792
5.1 流道结构特点 792
5.2 流道尺寸设计 793
5.3 熔体停留时间 795
5.4 剪切速率 795
6 螺杆分配式流道平缝模 796
6.1 结构特点与类型 796
7 自动调节式平缝模 797
7.1 热螺栓自动调节平缝模 797
6.2 流道尺寸设计 797
7.2 微机控制平缝模 798
第5章 线缆包覆模设计 800
1 概述 800
2 线缆包覆模类型 800
2.1 挤压式包覆模 800
2.2 套管式包覆模 801
3 包覆模结构设计 801
3.1 芯模几何设计 801
3.2 流道锥角设计 801
4.1 圆柱形芯模分配流道尺寸 802
4 芯模分配系统设计 802
3.4 口模对中设计 802
3.5 口模形状设计 802
3.3 导向锥间隙设计 802
4.2 截锥形芯模分配流道尺寸 803
5 交联聚乙烯包覆模设计 805
第6章 吹塑模设计 808
1 概述 808
2 吹塑模类型 808
3 吹塑模工艺参数 808
3.5 缓冲槽尺寸 809
3.4 吹胀化 809
3.3 口模环隙 809
3.2 口模成形段长度 809
3.1 挤塑机的匹配 809
3.6 流道扩张角 810
4 吹塑模结构设计 810
4.1 心棒式吹塑模 810
4.2 十字形吹塑模 810
4.3 螺旋式吹塑模 810
4.4 莲花瓣流道吹塑模 810
4.5 旋转吹塑模 811
5.1 设计要求 812
5.2 冷却风环 812
5 冷却装置设计 812
5.3 水冷装置 814
5.4 内冷装置 814
第7章 型坯模设计 816
1 概述 816
2 型坯模工艺参数 816
2.1 成形段长度 816
2.2 环隙尺寸 816
2.3 压降估算 816
3 型坯模结构类型 816
4.1 分离式储料缸 817
4 储料缸设计 817
4.2 一体式储料缸 818
第8章 异型材挤塑模设计 820
1 概述 820
2 异型材挤塑模类型 821
2.1 孔板式挤塑模 821
2.2 多级式挤塑模 821
2.3 流线形挤塑模 821
3 异型材成形模设计 821
3.1 口模尺寸 821
4.1 异型材定型方法 824
4 异型材定型模设计 824
3.2 模具结构参数 824
4.2 定型模结构设计 827
4.3 定型模型腔尺寸 830
5 设计实例 830
2.2 烘箱发泡法 833
3.2 分流锥孔板式挤塑模 833
3 模具结构类型 833
2.3 生产工艺特点 833
3.1 纵向高阻力挤塑模 833
2.1 离模发泡法 833
2 结构泡沫型材的工艺方法 833
1 概述 833
第9章 结构泡沫型材挤塑模设计 833
3.3 中空发泡型材挤塑模 834
3.4 栅格分流梭挤塑模 834
4 模腔流道设计 834
第10章 网材、单丝及造粒挤塑模设计 836
1 塑料网材挤塑模 836
1.1 塑料网材的构成 836
1.2 网材模结构 836
2 塑料喷丝挤塑模 837
2.1 喷丝模结构 837
2.2 喷丝板参数 837
3.1 造粒工艺与操作条件 838
3 塑料造粒挤塑模 838
3.2 口模板设计 839
第11章 共挤复合模设计 840
1 概述 840
2 共挤复合模结构类型 840
2.1 模外复合共挤模 840
2.4 可控型坯共挤模 841
3 多层共挤流动模拟分析 841
2.3 多层复合共挤模 841
2.2 模内复合共挤模 841
3.1 共挤多层流动压降计算 842
3.2 共挤多层流动数值解 843
第12章 挤塑模加热与压力测量 846
1 概述 846
2 加热功率计算 846
2.1 按挤塑模质量确定加热功率 846
2.2 按挤塑模散热面积确定加热功率 846
2.3 按热散失所需补充的热量计算 846
2.4 挤塑模升温所需时间 846
3.2 铸铝加热器 847
3.1 电阻加热器 847
3 加热方式选择 847
4 温度控制与调节 848
5 压力测量 848
第13章 挤塑模力学设计 849
1 概述 849
2 力学设计基本原则 849
2.1 结构设计十原则 849
2.2 构型设计八原则 849
3.1 口模径向允许变形量 850
3.2 支架支撑强度校核 850
3 圆形挤塑模力学设计 850
3.3 联接螺钉计算 851
4 平缝模力学设计 852
4.1 口模板厚度计算 853
4.2 联接螺钉计算 855
4.3 衣架式流道平缝模结构尺寸 855
5 挤塑模用材料 856
5.1 材料须满足的条件 856
5.2 选材须考虑的问题 856
5.3 符合挤塑模用钢材类型 856
3 自增强复合管材模 858
2 可调压力管材模 858
4 波纹管材模 858
第14章 挤塑模结构设计实例 858
1 RPVC管材模及真空定型模 858
5 双型坯挤塑模 859
6 衣架式流道平缝模 859
7 钢管覆层挤塑模 859
8 双色板材挤塑模 859
9 中空异型材定型模 860
10 心层发泡棒材模 861
11 菱形网材模 862
12 3层内复合吹塑模 862
1.1 软件工程构思 864
第15章 挤塑模CAD 864
1 概述 864
1.2 关键技术 865
1.3 CAD/CAM总体框架 865
1.4 系统主要功能 866
2 挤塑模CAD数据管理系统 866
2.1 系统应用环境及功能要求 866
2.2 系统开发一般途径 867
2.3 管理系统构思 867
2.4 版本管理算法 867
3 挤塑模CAD系统并行工程 868
3.1 并行工程 868
2.5 算法与网络并发处理 868
3.2 CAD/CAM设计思路 869
4 挤塑模口模设计 870
4.1 口模图形设计 870
4.2 口模流道优化设计 872
5 挤塑模型芯设计 873
5.1 型芯选型 873
5.2 型芯吊挂 875
5.3 螺钉布置 876
6 挤塑模挤出过程仿真 876
6.1 挤出过程图形仿真 876
6.2 挤塑模智能仿真 878
2 操作人员素质 881
3 拆卸与清理 881
第16章 挤塑模使用与维护 881
1 概述 881
4 装配与维护 882
参考文献 882
第12篇 中空吹塑与热成形模具设计 885
第1章 中空吹塑成形 885
1 概述 885
2 中空吹塑成形的应用 885
3 中空吹塑成形的方法 885
3.1 挤出吹塑法 885
3.3 注塑拉伸吹塑法 886
3.2 注塑吹塑法 886
3.5 多层吹塑法 887
3.6 浸蘸吹塑法 887
3.4 片材吹塑法 887
4 中空吹塑成形的特性 888
4.1 吹塑工艺过程 888
4.2 吹塑工艺参数 889
5 中空吹塑成形的塑料 889
5.1 中空制品用塑料应具备的特性 889
5.2 中空制品常用塑料 890
6.1 圆形容器设计 894
6 中空吹塑制品设计 894
6.2 方形容器设计 895
6.3 椭圆形容器设计 895
6.4 异形容器设计 895
6.5 垂直载荷强度的考虑 895
6.6 圆角与瓶底内凹设计 897
6.7 容器刚性设计 897
6.8 瓶口螺纹设计 898
6.9 嵌件设计 899
6.10 按加工特性设计 899
6.12 多层复合与表面装饰设计 900
6.11 按使用要求设计 900
第2章 中空吹塑模设计 901
1 概述 901
1.1 中空吹塑模结构 901
1.2 中空吹塑模类型 902
2 挤塑吹塑模设计 902
2.1 模口设计 902
2.2 模底设计 903
2.3 分型面选择 904
2.4 排气隙设计 904
2.6 冷却系统设计 905
2.5 模腔表面设计 905
2.7 吹塑模装配 907
3 注塑吹塑模设计 907
3.1 型坯模设计 908
3.2 吹塑模设计 910
3.3 注塑吹塑模组装 911
3.4 脱模板设计 912
4 注-拉-吹成形技术 912
4.1 注-拉-吹制品特性 912
4.2 注-拉-吹工艺过程 912
4.3 注-拉-吹型坯设计 913
2.1 压差热成形 915
2 热成形方法 915
1 热成形特点 915
第3章 热成形及其应用 915
2.2 覆盖热成形 916
2.3 助压热成形 916
2.4 回吸热成形 917
2.5 对模热成形 918
2.6 双片热成形 919
2.7 热成形自动化 919
3.3 零售业 920
3.2 快餐业 920
3.1 包装业 920
3 热成形应用 920
3.4 运输业 921
3.5 家电业 921
3.6 医药业 921
3.7 建筑业 921
3.8 箱包业 921
3.9 园林业 921
3.10 殡葬业 921
4 热成形制品工艺设计 921
4.1 几何形状设计 921
4.3 凹槽设计 922
4.2 脱模斜度 922
4.4 外观设计 923
4.5 转角设计 923
4.6 大平面设计 923
4.7 引伸比与径深比 923
4.8 材料选择 924
4.9 尺寸精度 925
4.10 修边 926
2 吸塑成形模具设计 927
2.1 工艺参数 927
1 概述 927
第4章 热成形模具设计 927
2.2 抽气孔设计 928
2.3 型面设计 929
2.4 型向粗糙度 929
2.5 边缘密封 930
2.6 加热与冷却 930
3 压空成形模具设计 930
3.1 排气孔设计 931
3.2 吹气孔设计 932
3.3 型刃设计 932
3.4 设置缓冲垫 933
3.5 锁模力计算 933
2.3 锑锡等低熔点合金 934
2.2 锌合金 934
2.4 铍铜合金 934
第5章 低压模具材料 934
2.1 铝合金 934
2 金属材料 934
1 概述 934
2.5 碳钢 935
3 非金属材料 935
3.1 木材 935
3.2 石膏 935
3.3 塑料 936
4 材料性能比较 936
参考文献 937
第13篇 塑料模标准件 941
第1章 塑料模标准化及其术语 941
1 模具标准化的重要性 941
1.1 模具标准化的意义 941
1.2 模具标准体系 941
1.3 模具标准化的制订原则 942
1.4 我国塑料模标准化的实施 944
2 塑料成形模具术语 944
第2章 塑料注射模具标准零件 960
1 标准零件的种类及功能 960
2 模具的标准零件 964
3 模具零件的技术条件 976
4 塑料注射模具技术条件 978
第3章 塑料注射模中小型标准模架 982
1 中小型模架的结构型式 982
1.1 结构型式 982
1.2 标记方法 982
2 中小型模架的尺寸组合系列 984
2.1 品种、系列与规格 984
2.2 中小型模架 985
3.2 验收规则 1015
3.3 标记、包装、运输、贮存 1015
3.1 技术要求 1015
3 中小型模架的技术条件 1015
第4章 塑料注射模大型标准模架 1017
1 大型模架的结构型式 1017
1.1 结构型式 1017
1.2 标记方法 1017
2 大型模架的尺寸组合系列 1017
2.1 品种、系列与规格 1017
2.2 大型模架 1018
3.2 验收规则 1030
3.3 包装、运输、贮存 1030
3 大型模架的技术条件 1030
3.1 技术要求 1030
第5章 塑料注射模模架的质量分等及选用 1031
1 模架的质量等级及其应具备的条件 1031
2 模架的选用过程 1034
参考文献 1035
1 橡胶基本性能 1039
1.1 橡胶特性与分类 1039
1.2 橡胶主要性能及用途 1039
第1章 橡胶模设计基础 1039
第14篇 橡胶模设计 1039
1.3 橡胶耐热耐寒极限温度 1041
1.4 橡胶代号及表示方法 1042
2 橡胶制品质量指标 1042
2.1 抗拉强度 1042
2.2 邵氏硬度 1042
2.3 伸长率 1042
2.4 永久变形 1042
2.5 脆性温度 1042
2.6 老化系数 1042
3 常用橡胶制品标准 1043
3.1 工业用橡胶板 1043
3.2 汽车用橡胶配件 1044
3.3 环状密封橡胶制品 1046
3.4 O形橡胶密封圈 1047
3.5 混炼型聚氨酯橡胶 1050
3.6 油封类橡胶制品 1051
3.7 环状橡胶密封圈制品 1054
4 橡胶制品及嵌件设计 1063
4.1 制品设计工艺性 1063
4.2 嵌件设计 1065
5 橡胶制品硫化控制 1068
5.1 硫化反应历程 1068
5.2 硫化压力 1069
5.3 硫化温度 1070
5.4 硫化时间 1071
5.5 等效硫化 1072
5.6 硫化仿真 1074
5.7 群控系统 1076
6 橡胶模分类 1077
6.1 橡胶压模 1077
6.2 橡胶传递模 1078
6.3 橡胶注压模 1078
6.4 橡胶挤出模 1078
第2章 橡胶压模设计 1079
1 结构设计 1079
1.2 分型面选择 1080
1.1 型腔数确定 1080
1.3 凸模与型芯设计 1081
1.4 余料槽设计 1083
1.5 排气孔设计 1084
1.6 启模口设计 1084
1.7 手柄设计 1084
2 模腔设计 1085
2.1 胶料收缩率的确定 1085
2.2 模腔尺寸的计算 1088
2.3 模板强度和刚度校核 1090
2.4 压模外形尺寸确定 1091
3 导向与定位设计 1092
3.1 导向零件 1092
3.2 定位零件 1093
4 模具精度设计 1094
4.1 模具公差 1094
4.2 模具零件精度 1094
4.3 表面粗糙度 1095
5 压模结构设计实例 1095
5.1 管套类橡胶制品压模 1095
5.2 嵌条类橡胶制品压模 1103
5.3 减振类橡胶制品压模 1106
5.4 轮带类橡胶制品压模 1109
5.5 板片类橡胶制品压模 1111
5.6 日用类橡胶制品压模 1114
5.7 大型橡胶制品压模 1119
5.8 橡胶海绵制品压模 1123
6 压模设计标准化 1123
6.1 O形密封圈压模 1123
6.2 V形密封圈压模 1140
6.3 J形密封圈(油封)压模 1142
6.4 橡胶套圈压模 1145
6.5 压模通用标准零件 1147
2 传递模分类 1150
2.1 分类方法 1150
第3章 橡胶传递模设计 1150
1 概述 1150
2.2 罐式传递模 1151
2.3 柱塞式传递模 1151
3 传递模设计 1152
3.1 加料室设计 1152
3.2 压料柱塞设计 1154
3.3 浇注系统设计 1154
3.4 排气隙设计 1156
4.1 薄壁制品传递模 1157
4 传递模典型结构 1157
3.5 信号孔考虑 1157
4.2 厚壁制品传递模 1158
4.3 多孔细长制品传递模 1159
4.4 正压反注传递模 1160
4.5 橡胶制品特殊结构形式传递模 1161
5 传递模结构设计实例 1164
5.1 管套帽类橡胶制品传递模 1164
5.2 减振类橡胶制品传递模 1165
5.3 轮胎类橡胶制品传递模 1168
5.4 杂件类像胶制品传递模 1169
1.2 注压机分类 1171
1.3 注压成形工艺特性 1171
第4章 橡胶注压模设计 1171
1.1 注压成形工艺过程 1171
1 概述 1171
1.4 注压制品缺陷与对策 1173
2 注压模结构 1174
2.1 注压模构成 1174
2.2 注压模分类 1174
3 注压模设计 1176
3.1 浇注系统设计 1176
3.2 模腔设计 1184
3.3 导向与定位机构设计 1190
3.4 脱模机构设计 1192
3.5 侧抽芯机构设计 1197
4 注压模结构设计实例 1200
4.1 O形橡胶密封圈注压模 1200
4.2 油封橡胶制品注压模 1200
4.3 帽套橡胶制品注压模 1201
4.4 绝缘橡胶制品注压模 1201
2.1 棒材模结构 1203
2 橡胶棒材模设计 1203
1.3 口模设计特点 1203
1.2 挤出成形应用 1203
1.1 挤出成形过程 1203
1 概述 1203
第5章 橡胶挤出模设计 1203
2.2 结构与工艺参数 1204
2.3 定型模设计 1205
3 橡胶管材模设计 1205
3.1 结构类型 1206
3.2 成形段长度 1209
3.3 结构参数 1210
3.4 定型模设计 1210
4.1 平缝模结构 1211
4 橡胶板材模设计 1211
4.2 平缝模流道设计 1212
4.3 设计实例 1214
5 线缆覆胶模设计 1215
5.1 覆胶模类型 1215
5.2 覆胶模结构 1216
5.3 芯模分配系统设计 1217
6 橡胶异型材挤出模设计 1218
6.1 设计工艺原则 1218
6.2 结构类型 1218
6.3 结构参数与尺寸 1220
6.4 口模设计实例 1223
7 挤出模力学设计 1223
7.1 结构设计基本原则 1224
7.2 圆形模力学设计 1225
7.3 平缝模力学设计 1226
8 挤出(压)机选用 1229
9 挤出模用材料 1230
3.1 模具验收 1231
3 验收与入库 1231
2.3 制订硫化工艺 1231
2.2 校样 1231
2.1 试模 1231
2 试模与校样 1231
1 概述 1231
第6章 橡胶模管理 1231
3.2 模具入库 1232
3.3 填写报告单 1232
4 清洗与保养 1232
4.1 模具清洗 1232
4.2 模具保养 1233
5.2 档案内容 1234
5.1 建档方法 1234
5 模具档案 1234
4.4 入库保存 1234
4.3 模具涂封 1234
参考文献 1236
第15篇 铝型材挤压模设计 1239
第1章 挤压模设计基础 1239
1 铝型材应用 1239
2 铝型材加工 1239
3 铝型材截面设计 1239
4 铝型材挤压成形工艺方法 1242
4.1 挤压工艺流程 1242
4.2 挤压用铝合金材料 1242
4.3 挤压成形工艺参数 1249
4.4 挤压型材主要缺陷与处理方法 1263
5 挤压工模具类型与组装形式 1266
5.1 挤压工模具类型 1266
5.2 挤压工模具组装形式 1267
第2章 挤压工具设计 1270
1 挤压筒设计 1270
1.1 挤压筒的结构型式 1270
1.2 挤压筒尺寸的确定 1272
1.3 挤压筒衬套厚度的确定 1274
1.4 挤压筒各衬套间配合过盈的确定 1275
1.5 挤压筒的强度计算 1276
1.6 挤压筒的装配 1284
1.7 挤压筒衬套的更换 1285
1.8 挤压筒的使用及维修 1285
1.9 挤压筒的加热方式 1286
2 挤压轴设计 1287
2.1 挤压轴的结构形式 1287
2.2 挤压轴的尺寸确定 1287
2.3 挤压轴的强度校核 1288
3 穿孔系统设计 1290
3.1 挤压针功能与类型 1290
3.2 挤压针结构形式与尺寸 1291
3.3 挤压针强度校核 1293
4 挤压垫设计 1296
4.1 挤压垫的结构 1296
4.2 挤压垫的尺寸 1296
4.3 挤压垫的强度校核 1297
4.4 固定挤压垫的设计及主要结构形式 1297
5 其他挤压工具设计 1299
5.1 模支承 1299
5.2 垫环 1300
5.3 压型嘴和模架 1301
1.1 挤压模结构要素 1303
1 概述 1303
第3章 挤压模具设计 1303
1.2 外形尺寸及其标准化 1304
1.3 设计时应考虑的因素 1305
1.4 设计原则与步骤 1306
1.5 技术条件及基本要求 1307
1.6 工作带标注方法 1307
2 挤压模具类型及组装形式 1309
2.1 挤压模具类型 1309
2.2 挤压模具组装方式 1311
3 实心铝型材挤压模具设计 1312
3.1 实心模结构设计 1312
3.2 棒材模设计 1314
3.3 实心型材模设计 1315
3.4 导流模设计 1319
3.5 保护模设计 1320
3.6 水冷模与氮冷模设计 1322
4 空心铝型材挤压模具设计 1323
4.1 无缝圆管挤压模 1323
4.2 平面分流组合模 1325
5 建筑用铝型材挤压模设计 1331
5.1 建筑用铝型材的特点 1331
5.2 建筑用铝型材模具设计 1331
6.1 变截面型材模设计 1337
6 工业用铝型材挤压模设计 1337
6.2 带肋壁板型材模设计 1340
6.3 宽展模设计 1342
第4章 挤压模设计实例 1345
1 异形空心型材挤压模 1345
1.1 挤压工艺及模具组装方案 1345
1.2 平面分流组合模设计 1345
2 典型铝型材挤压模 1347
2.1 方管模设计 1347
2.2 平开门下方模设计 1348
2.3 90窗下方模设计 1349
3 半空心型材挤压模设计 1350
3.1 舌比概念 1350
2.4 大壁厚差型材模设计 1350
3.2 设计方法 1351
4 双孔平面分流模设计 1352
4.1 挤压工艺的确定 1352
4.2 设计参数的确定 1353
4.3 分流模强度的校核 1355
4.4 模具材料 1355
4.5 M217-105模具挤压试验 1355
5.1 导料板保护悬臂模 1356
5 悬臂模设计 1356
5.2 前室保护悬臂模 1359
5.3 稳定销保护悬臂模 1360
5.4 危险悬臂截面增强方法 1360
5.5 悬臂损坏的修复 1361
5.6 遮盖模 1361
5.7 连体模 1362
5.8 替代模 1363
5.9 悬臂模强度计算 1364
6 臂板模设计 1364
6.1 壁板模设计原则 1364
6.2 壁板模设计举例 1366
第5章 挤压模材料及热处理 1369
1 挤压技术与模具 1369
2 挤压模的工作条件与材料选用 1369
2.1 挤压模的工作条件 1369
2.2 选材须考虑的问题 1369
2.3 常用模具材料牌号 1370
2.4 材料选择原则 1370
3 挤压模具钢热处理 1371
3.1 5CrMnMo、5CrNiMo和5CrNiMoV钢热处理 1371
3.3 H13(4Cr5MoSiV1)钢热处理 1372
3.2 3Cr2W8V钢热处理 1372
3.4 常用模具钢热处理工艺优化 1373
3.5 4Cr3Mo2V钢热处理 1374
3.6 国外常用模具钢组成、热处理及与国产钢牌号对照 1375
3.7 模具钢真空热处理 1381
第6章 挤压模修正技术 1383
1 概述 1383
1.1 修模原则 1383
1.2 修模方法 1384
1.3 修模依据 1385
2 挤压模修正基本方法 1385
2.1 阻碍法 1385
2.2 加快法 1386
2.3 修理法 1387
3 实心型材挤压模的修正 1388
3.1 扭拧 1388
3.2 波浪 1388
3.3 刀形弯曲 1388
3.4 扩口和并口 1389
3.5 平面间隙 1389
3.6 金属填充不足 1389
4 空心型材挤压模的修正 1390
4.1 空心型材模修正的特点 1390
4.2 缺陷产生的原因及修正方法 1391
5 模具修正相关问题 1392
5.1 结构条纹 1392
5.2 挤压珩磨抛光 1393
5.3 模子渗氮 1394
5.4 导向装置 1396
5.5 受料工作台和牵引设备 1397
5.6 模子焊接 1397
参考文献 1398
1.4 玻璃的化学组成 1401
1.3 玻璃的结构 1401
1.1 玻璃的定义 1401
1.2 玻璃的共性 1401
1 概述 1401
第1章 玻璃模设计基础 1401
第16篇 玻璃模设计 1401
1.5 玻璃的性能 1402
1.6 玻璃制品的类型 1407
2 玻璃的可加工性 1408
2.1 黏度与成形 1408
2.2 表面张力与成形 1409
2.3 传热性能 1409
3.1 瓶罐与容器成形 1410
3 玻璃制品加工方法 1410
2.4 热流动性能 1410
3.2 平板类制品成形 1412
3.3 玻璃制品热成形 1413
4 玻璃制品设计 1413
4.1 设计程序 1413
4.2 化学组成设计 1414
4.3 结构工艺性设计 1416
4.4 制品公差选择 1420
4.5 制品变形考虑 1423
4.6 瓶型与强度设计 1423
5.1 按成形方法分 1424
5 玻璃模分类 1424
5.3 按润滑方式分 1425
5.4 按结构类型分 1425
5.2 按成形过程分 1425
5.5 按成形机械分 1426
第2章 玻璃模设计 1427
1 概述 1427
1.1 玻璃制品生产工艺流程 1427
1.2 玻璃模设计须考虑的问题 1427
1.3 玻璃模设计程序 1427
1.5 模腔技术要求 1428
1.4 模腔尺寸公差计算 1428
2 玻璃模类型与结构 1429
2.1 吹制模 1429
2.2 压制模 1429
2.3 机制模 1430
3 模具与成形机 1432
3.1 成形机性能 1432
3.2 成形机类型 1433
3.3 模具与成形机的关系 1442
4.1 设计内容 1444
4.2 瓶罐制品计算 1444
4 玻璃模设计 1444
4.3 夹钳选择 1445
4.4 夹钳与模具的配合 1445
5 初型模设计 1447
5.1 过容量率确定 1447
5.2 延伸量 1448
5.3 雏型确定 1448
5.4 反转值X或Y 1455
5.5 口模选择 1457
5.6 闷头和漏斗选择 1460
5.7 初型模工作图 1463
5.8 有关配件选择 1464
6 成形模设计 1470
6.1 吹气头选择 1470
6.2 冷却吹气头 1470
6.3 模底选择 1470
6.4 模腔设计原则 1470
6.5 成形模工作图 1474
6.6 瓶钳 1475
7 吹制模与压制模设计 1479
7.1 吹制模设计要点 1479
7.2 压制模设计要点 1480
7.3 压制模结构设计 1481
8 玻璃模温度与冷却设计 1483
8.1 模温对成形质量的影响 1483
8.2 模具冷却方式 1484
第3章 玻璃模设计实例 1487
1 初型模设计 1487
1.1 参数确定 1487
1.2 设计校验 1489
1.3 设计示例 1490
2 成形模设计 1492
2.1 瓶塞多工位压制模 1492
2.3 显像管玻壳压制模 1493
2.2 圆柱形器皿压制模 1493
第4章 玻璃模材料与热处理 1495
1 符合模具材料的条件 1495
2 玻璃模材料类型 1496
2.1 常用材料 1496
2.2 研究成果 1499
3 材料热处理 1504
3.1 铸铁热处理 1504
3.2 4Cr13Ni热处理 1504
3.3 激光合金化处理 1504
3.4 表面强化处理 1505
1 模具的安装 1506
2 模具的润滑 1506
第5章 玻璃模使用与维护 1506
3 模具的清洗和修理 1507
3.1 模具清洗 1507
3.2 模具修理 1508
4 提高模具使用寿命 1509
参考文献 1509
1 陶瓷材料性能 1513
1.1 陶瓷分类 1513
1.2 陶瓷原料 1513
第1章 陶瓷模设计基础 1513
第17篇 陶瓷模设计 1513
1.3 日用陶瓷化学组成 1514
1.4 陶瓷材料组织结构 1518
1.5 陶瓷材料性能 1521
2 陶瓷可加工性 1525
2.1 流动性 1525
2.2 可塑性 1528
2.3 收缩性 1530
2.4 烧结硬化性 1531
3 陶瓷制品成形方法 1531
3.1 成形方法选择 1532
3.2 成形方法分类 1532
3.3 成形方法比较 1544
4.1 陶瓷制品的合理构型 1545
4.2 压制成形制品结构工艺性 1545
4 陶瓷制品设计 1545
4.3 日用陶瓷制品形体处理 1547
4.4 日用陶瓷造型设计与变形 1548
4.5 日用陶瓷外观造型设计 1551
4.6 陶瓷制品尺寸精度 1552
5.2 按结构类型分 1553
5.4 按材质类型分 1553
5.3 按陶瓷类型分 1553
5.1 按成形方法分 1553
5 陶瓷模分类 1553
第2章 陶瓷模设计 1554
1 概述 1554
1.1 陶瓷坯料与成形 1554
1.2 陶瓷模制作与设计原则 1554
2 陶瓷模结构与类型 1555
2.1 可塑成形模 1555
2.2 注浆成形模 1558
2.3 压制成形模 1559
2.4 等静压成形模 1563
2.5 热压铸成形模 1565
3.1 成形机械技术规范 1568
3 陶瓷模与成形机械 1568
3.2 真空练泥机工装 1576
3.3 滚压模的固定 1579
3.4 滚压头的联结 1579
3.5 压机的选择 1580
4 压制模主要零件设计 1580
4.1 侧压力和顶出力 1580
4.2 凹模强度计算 1580
4.3 凹模刚性条件 1581
4.4 主要零件结构设计 1581
5.1 放尺 1583
5 模腔尺寸计算 1583
5.2 装料比与模腔高度尺寸 1584
5.3 压制模型腔尺寸 1585
5.4 热压铸模型腔尺寸 1587
第3章 陶瓷模设计实例 1588
1 日用陶瓷制品滚压模 1588
2 1200 ml桶形壶注浆模 1588
3 偏转磁芯压制模 1589
3.1 压坯松装高度 1589
3.2 装粉 1590
3.4 脱模 1591
4 滑石瓷品热压铸模 1591
3.3 压制 1591
5 工形磁芯热压铸模 1592
6 电极支架热压铸模 1592
7 线圈瓷管热压铸模 1593
8 电瓷半干压成形模 1593
9 密封板压制模 1594
10 磁体湿法压制模 1595
10.1 磁体成形方法 1595
10.2 模具结构 1595
第4章 陶瓷模材料与热处理 1597
1 石膏模 1597
2 改性石膏模 1598
3 新型多孔模 1601
3.1 无机填料模 1601
3.2 无机材料模 1602
3.3 有机塑料和其他材料模 1602
4 橡胶模 1604
5 金属模 1604
第5章 陶瓷模使用与维护 1605
1 提高产品合格率的对策 1605
2 模具清理与装配 1606
3 模具使用与保管 1606
4 模具维护与保养 1606
参考文献 1607
- 《指向核心素养 北京十一学校名师教学设计 英语 七年级 上 配人教版》周志英总主编 2019
- 《设计十六日 国内外美术院校报考攻略》沈海泯著 2018
- 《计算机辅助平面设计》吴轶博主编 2019
- 《高校转型发展系列教材 素描基础与设计》施猛责任编辑;(中国)魏伏一,徐红 2019
- 《景观艺术设计》林春水,马俊 2019
- 《高等教育双机械基础课程系列教材 高等学校教材 机械设计课程设计手册 第5版》吴宗泽,罗圣国,高志,李威 2018
- 《指向核心素养 北京十一学校名师教学设计 英语 九年级 上 配人教版》周志英总主编 2019
- 《华乐大典 琵琶卷 乐曲篇 下》中国民族管弦乐学会 2016
- 《Cinema 4D电商美工与视觉设计案例教程》樊斌 2019
- 《通信电子电路原理及仿真设计》叶建芳 2019
- 《高考快速作文指导》张吉武,鲍志伸主编 2002
- 《建筑施工企业统计》杨淑芝主编 2008
- 《国学经典诵读》(中国)严琼燕 2019
- 《钒产业技术及应用》高峰,彭清静,华骏主编 2019
- 《近代旅游指南汇刊二编 16》王强主编 2017
- 《汉语词汇知识与习得研究》邢红兵主编 2019
- 《思维导图 超好用英语单词书》(中国)王若琳 2019
- 《东北民歌文化研究及艺术探析》(中国)杨清波 2019
- 《黄遵宪集 4》陈铮主编 2019
- 《孙诒让集 1》丁进主编 2016
- 《钒产业技术及应用》高峰,彭清静,华骏主编 2019
- 《现代水泥技术发展与应用论文集》天津水泥工业设计研究院有限公司编 2019
- 《异质性条件下技术创新最优市场结构研究 以中国高技术产业为例》千慧雄 2019
- 《Prometheus技术秘笈》百里燊 2019
- 《中央财政支持提升专业服务产业发展能力项目水利工程专业课程建设成果 设施农业工程技术》赵英编 2018
- 《药剂学实验操作技术》刘芳,高森主编 2019
- 《林下养蜂技术》罗文华,黄勇,刘佳霖主编 2017
- 《脱硝运行技术1000问》朱国宇编 2019
- 《催化剂制备过程技术》韩勇责任编辑;(中国)张继光 2019
- 《信息系统安全技术管理策略 信息安全经济学视角》赵柳榕著 2020