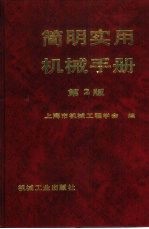
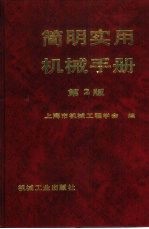
简明实用机械手册 第2版PDF电子书下载
- 电子书积分:35 积分如何计算积分?
- 作 者:上海市机械工程学会编
- 出 版 社:北京:机械工业出版社
- 出版年份:1987
- ISBN:711103273X
- 页数:1462 页
第一节 常用字母及符号 1
表1-1 汉语拼音字母 1
表1-2 拉丁字母 1
第一章 常用资料及计算 1
表1-3 希腊字母 2
表1-4 国内部分标准代号 2
表1-5 国外部分标准代号 2
表1-6 常用数码对照表 3
表1-7 主要化学元素符号、原子量和密度 3
表1-9 国际单位制的辅助单位 4
表1-10 国际单位制中具有专门名称的导出单位 4
第二节 法定计量单位 4
表1-8 国际单位制的基本单位 4
表1-11 国家选定的非国际单位制单位 5
表1-12 用于构成十进倍数和分数单位的词头 6
表1-13 常用法定计量单位及其换算 7
第三节 常用单位换算及系数 15
表1-14 市制计量单位 15
表1-15 米(公)制计量单位 16
表1-17 长度单位换算 17
表1-16 英制计量单位 17
表1-19 体积单位换算 18
表1-20 容积单位换算 18
表1-21 重量单位换算 18
表1-18 面积单位换算 18
表1-22 in分数、in小数与mm换算 19
表1-23 nlm与in小数换算 19
表1-24 角速度单位换算 20
表1-25 材料线膨胀系数α 20
表1-27 常用材料密度 21
表1-26 金属材料的熔点、热导率及比热容 21
表1-28 常用静摩擦与滑动摩擦系数 22
表1-29 部分钢铁硬度及强度换算 23
表1-30 常用材料弹性模量 24
第四节 常用数学资料 25
一、常用数学符号 25
二、乘法及因式分解 26
三、分数 27
五、比例 28
四、根式 28
六、指数与倒数 29
匕、对数 29
八、常用几何图形的计算 30
表1-33 平面积计算 31
表1-34 立体图形计算 35
九、三角函数及公式 39
(一)三角函数的定义 39
(三)任意角三角函数诱导公式 40
(二)三角函数在各象限的正负号 40
(四)函数计算公式 41
(五)直角三角形的解法 42
(六)斜三角形的解法 43
(七)三角函数 43
第五节 常用计算工具 52
一、综述 52
三、电子计算器 53
第六节 机械制图 55
表1-39 图线 56
表1-38 比例 56
表1-37 图纸幅面 56
表1-40 剖面符号 57
表1-41 视图 58
表1-42 剖视 60
表1-43 剖面 62
表1-44 局部放大图 62
表1-45 简化画法 63
表1-46 装配图中零、部件序号及其编排方法 65
表1-47 尺寸注法 66
表1-48 简化注法 68
表1-49 尺寸公差与配合的注法示例 71
表1-50 表面粗糙度代号的注法 72
表1-51 螺纹及螺纹紧固件画法 73
表1-52 齿轮画法 74
表1-53 蜗轮画法 76
表1-54 花键画法 77
表1-55 弹簧画法 78
表1-56 标准尺寸(直径、长度、高度等) 79
应注意的基本原则和改善零件切削加工举例 79
第七节 常用结构要素及标准 79
表1-57 锥度与锥角系列 80
表1-58 特殊用途圆锥的锥度与锥角 81
表1-59 公制锥度 81
表1-60 常用标准角度 82
表1-61 未注公差角度的极限偏差 82
表1-62 零件倒角、倒圆型式与尺寸 82
表1-63 轴与套的倒角 83
表1-64 轴与套的倒圆半径 83
表1-65 球面半径 84
表1-66 中心孔 84
表1-67 平面上用润滑槽型式与尺寸 86
表1-68 机床导轨的润滑槽型式与尺寸 86
表1-69 燕尾槽 86
表1-70 T型槽 87
表1-71 砂轮越程槽 89
表1-72 滚花 90
二、金属材料力学性能 91
一、钢号表示法 91
第一节 常用钢铁及热处理 91
第二章 材料与金属热处理 91
三、钢材的特性 94
四、热处理一般常识 97
五、钢的热处理 99
六、铸铁和铸钢 115
(一)铸造用生铁 115
(二)铸铁牌号 115
(二)标准公差与基本偏差 120
(三)铸钢 121
第二节 常用钢材的品种、尺寸规格和理论重量 123
表2-25 热轧圆钢、方钢、六角钢及八角钢 123
一、型钢 123
表2-26 热轧圆钢,方钢、六角钢及八角钢的供应长度 125
表2-27 冷拉圆、钢方钢及六角钢 125
表2-28 热轧扁钢 128
表2-29 热轧等边角钢 130
表2-30 热轧不等边角钢 133
表2-31 热轧工字钢 135
表2-32 热轧槽钢 137
表2-33 钢筋混凝土用钢筋 138
表2-34 热轧钢板和钢带 140
二、钢板及钢带 140
表2-35 钢带公称厚度和宽度 142
表2-36 冷轧钢板和钢带的尺寸、重量 142
表2-37 单张热镀锌薄钢板 144
表2-39 普通碳素钢冷轧钢带 145
表2-38 花纹钢板 145
三、钢管和其它材料 146
(一)钢管 146
(二)弹簧钢丝 151
第三节 有色金属 154
一、有色金属及合金产品牌号表示方法 154
表2-47 产品代号采用的汉语拼音字母 154
表2-48 有色金属产品类别、代号表示方法 155
表2-49 铸造铝合金化学成分 158
表2-50 国标及IS01338—77合金牌号对照表 160
二、常用有色金属及合金的主要特性和用途 161
表2-51 工业纯铜及合金牌号、代号的主要特性和用途 161
表2-52 铸造铜合金的主要特性和应用举例 164
表2-53 常用工业纯铝及铝合金产品类别、主要特性和应用范围 169
表2-54 常用铸造铝合金类别、主要特性和用途举例 171
表2-55 常用铸造轴承合金的类别、主要特性和用途举例 173
表2-56 常用硬质合金牌号、主要特性和用途举例 174
三、铜材的尺寸规格 175
表2-57 紫铜板及黄铜板 175
表2-58 铜带品种 179
表2-59 铜线的品种 179
表2-60 铜管品种 180
表2-61 铜棒(圆形、方形、六角形)品种 180
四、铝材常用的尺寸规格 181
表2-62 铝及铝合金板 181
表2-63 铝及铝合金棒 182
第四节 非金属材料 183
一、橡胶 183
表2-64 天然橡胶与合成橡胶性能比较 183
表2-65 工业用橡胶板 184
表2-67 织物增强吸水软管 185
表2-66 工业用硫化橡胶板的规格 185
二、塑料 186
表2-68 工程塑料的分类及其品种 186
表2-69 常用工程塑料的特性及用途 186
表2-70 硬聚氯乙烯板材 189
表2-71 化工用硬聚氯乙烯管材 190
表2-72 软聚氯乙烯压延薄膜 191
表2-73 聚四氟乙烯制品规格 192
表2-74 浇铸型工业有机玻璃板材、棒材和管材 194
三、其它非金属材料 195
(一)石墨 195
(二)工业用毛毡 197
第三章 公差配合与表面粗糙度 199
第一节 公差配合的基本概念 199
一、公差配合与极限尺寸 199
(一)基本术语 199
二、互换性与配合 203
(一)零件的互换性 203
(二)配合 203
(三)配合举例 214
一、公差配合的选择 216
(一)公差选择原则 216
(二)公差等级的应用 216
第二节 公差配合的选用及其标准 216
(三)配合选择原则 218
二、配合标准 219
(一)一般用途公差带(包括优先和常用) 219
(二)优先配合和常用配合 219
(三)优先配合公差带图和极限偏差 224
(四)公差与配合新旧国标对照 243
一、名词解释及标注方法 246
(一)名词解释 246
第三节 形状公差和位置公差 246
(二)形状和位置公差的标注方法 248
二、形状与位置公差 255
表3-18 形状公差 255
表3-19 位置公差 263
(二)表面粗糙度的参数和数值 285
一、基本术语及评定方法 285
第四节 表面粗糙度 285
(一)常用基本术语 285
二、表面粗糙度符号及标注方法 288
(一)表面粗糙度符号 288
(二)表面粗糙度在图纸上的标注方法 288
三、表面粗糙度的应用及与旧国标的对照 290
表3-25 新国标表面粗糙度(Rα)的应用举例 290
表3-25 各种加工方法能达到的表面粗糙度值(Rα) 292
表3-27 新国标参数Rα、Rz数值与旧国标光洁度的对照 294
(一)普通螺纹常用基本术语 295
第四章 机械零件 295
一、螺纹 295
第一节 联接与紧固 295
(二)螺纹的种类、特点和用途 298
(三)普通螺纹基本牙型和系列尺寸 301
(四)普通螺纹公差与配合的选用 309
(五)普通螺纹的标记 349
(六)普通螺纹的收尾、肩距、退刀槽和倒角 350
二、螺纹联接的一般常识 355
(一)螺纹联接的基本类型及用途 355
(二)螺纹联接件的相关参考尺寸 356
(三)螺纹紧固件受力情况及常用材料 361
三、螺纹紧固件与垫圈 362
(一)螺钉 362
(二)螺栓与螺母 369
(三)垫圈与挡圈 377
四、销与键 391
(一)销 391
(二)键 400
(三)花键 409
五、联轴器 417
(一)套筒联轴器 417
(二)凸缘联轴器 430
(三)弹性套柱销联轴器 430
(四)尼龙NZ挠性爪型联轴器 430
(五)小型万向联轴器 430
六、常用离合器 448
(一)牙嵌式离合器 448
(二)摩擦片电磁离合器 450
(三)其他常用离合器 450
一、滑动轴承 452
(一)一般滑动轴承的种类和用途 452
第二节 轴承 452
(二)常用滑动轴承 460
(三)轴套与联接方法 466
(四)粉末冶金轴承(含油轴承)与尼龙轴承 473
二、滚动轴承 478
(一)常用滚动轴承的结构型式 478
(二)滚动轴承精度与其配合的公差带 485
(三)滚动轴承常用的紧固方法 491
(四)滚动轴承的润滑油及润滑脂 493
(五)常用滚动轴承的型式及尺寸 493
第三节 机械传动 520
一、带传动 520
(一)普通V带传动 520
(二)窄V带传动 535
(三)平型带传动 537
(四)带传动的张紧方法 540
(五)同步带传动 542
二、链传动 558
(一)套筒滚子链 558
(二)齿形链(又名无声链) 565
三、齿轮传动 565
(一)渐开线圆柱齿轮 565
(二)圆弧圆柱齿轮 580
(三)直齿圆锥齿轮 582
四、蜗杆传动 589
(一)圆柱蜗杆的基本参数与计算 589
(二)常用蜗轮结构与材料 595
五、螺旋传动(丝杆副传动) 598
(一)螺旋传动的种类与用途 598
(二)滑动螺旋传动(滑动丝杆传动) 599
(三)滚动螺旋传动(滚珠丝杆副传动) 607
第四节 润滑、密封、弹簧及其他 612
一、润滑与密封 612
(一)润滑方式 612
(二)一般润滑件 615
(三)润滑剂 631
(四)填料密封 636
(五)O形橡胶密封圈 643
(六)防尘密封 659
(七)油封 663
(八)法兰连接与管道密封 674
二、弹簧 675
(一)基本常识 675
(二)圆柱压缩螺旋弹簧 680
(三)圆柱拉伸螺旋弹簧 684
(四)圆柱扭转螺旋弹簧 687
三、一般管路连接 689
(一)基本资料 689
(二)可锻铸铁管路附件 695
四、常用操作件及起重器具 700
(一)常用操作件 700
(二)常用起重器具 721
(一)铸件结构与铸件缺陷 725
第五节 机械零件工艺结构的合理选择 725
一、铸锻工艺对零件结构的要求 725
(二)力求铸造工艺简化和方便 726
(三)铸件结构要素 728
(四)锻件 734
二、热处理对零件结构的要求 735
(一)基本原则 735
(二)常见材料淬火硬度和改善热处理性能举例 736
三、切削加工对零件结构的要求 739
四、冲压零件的结构 745
(一)冲压零件材料的选择 745
(二)冲压件的结构要素和示例 746
一、常用基本术语 753
第一节 基本概念 753
第五章 测量技术和量具量仪 753
二、测量误差 754
(一)偶然误差 754
(二)系统误差 755
第二节 长度测量 756
一、一般通用量具量仪的性能和用途 756
(一)普通量具 756
(二)游标量具 758
(三)千分尺 764
(四)百分表和千分表 769
(五)测微计和比较仪 771
二、量规和量块 774
(一)光滑量规 775
(二)量块 778
(三)塞尺 779
三、常用光学仪器的种类和用途 779
(一)投影仪 779
(二)光学计 782
(三)测长仪 783
(四)工具显微镜 784
(五)自准直仪 786
(六)水平仪 786
四、气动和电动量仪 787
(一)气动量仪 787
(二)电动量仪 787
(三)万能角度尺(原名角度规) 788
(二)角度块 788
(一)直角尺 788
一、通用角度量具的性能、规范和用途 788
第三节 角度与锥度测量 788
(四)万能角尺 792
(五)锥体量规(又名圆锥量规) 792
(一)平板 793
(六)正弦规(又名正弦尺) 794
二、角度和锥度测量方法 795
(一)一般角度和锥度的测量 795
(二)精密角度的测量 797
第四节 平面和直线度的测量 798
一、测量平面或直线度的常用工具 798
(二)平晶 798
(三)平尺和刀口形直尺 799
(一)一般直线度误差的检验 800
二、直线度与平面度的测量 800
(二)较长直线度误差的检验 803
(三)用标准平板(基准平板)着色检查平直度 805
(四)用标准平板(基准平板)与测微计测量平面度 805
(五)光学平面法 806
第五节 螺纹测量 807
一、常用螺纹量规 807
(一)普通螺纹量规 807
(二)梯形螺纹量规 807
(二)螺距的测量 811
三、精密丝杆的测量 811
(三)螺纹中径的测量 811
(一)牙形半角的测量 811
二、外螺纹参数的测量 811
第六节 齿轮测量 814
一、渐开线圆柱齿轮精度等级和测量 814
(一)渐开线圆柱齿轮精度等级 814
(二)渐开线圆柱齿轮的测量原则和方法 832
(三)齿距测量(周节测量) 832
(四)齿圈径向跳动测量 837
(五)齿厚测量 837
(六)基节测量 837
(七)齿形测量 839
(八)公法线测量 840
(九)齿向误差的测量 841
(一)渐开线齿条的测量 844
(二)圆锥齿轮的测量 844
二、渐开线齿条和锥齿轮的测量 844
三、蜗轮副的测量 845
(一)蜗杆的测量 845
(二)蜗轮的测量 845
第七节 工厂中常用的其他测量方法 846
一、孔中心距离的测量 846
(一)利用通用量具检验孔中心距误差 846
(二)利用专用量规检验孔中心距误差 847
二、圆跳动(径向与端面跳动)的测量 848
(一)径向跳动测量 848
(二)端面跳动测量 849
三、同轴度(旧名同心度)和圆度测量 849
(一)用综合测量法检验同轴度 849
(二)用圆度仪检查圆度和同轴度 850
(一)平行度的测量 854
(三)用V形块检查圆度和圆柱度误差 854
四、平行度和垂直度的测量 854
(二)垂直度的测量 856
第八节 表面粗糙度的测量 859
一、比较法 859
(一)用表面粗糙度比较样块对比 860
(二)用“标准件”对比 860
二、光学法 861
(一)光切法 861
(二)干涉法 861
三、针描法 861
四、印模法 861
第九节 机械工厂其它常用仪表 862
一、玻璃液体温度计 862
三、记数器 863
二、转速表 863
四、压力表 864
五、真空表 865
第六章 金属切削刀具 866
第一节 车刀 866
一、车刀的类型和用途 866
二、常用车刀的规格和尺寸 868
(一)焊接硬质合金车刀 868
(二)机械夹固硬质合金车刀 868
(三)可转位车刀 868
三、车刀材料的选择 902
(三)车刀切削部分的几何角度 903
四、车刀切削部分的几何形状和几何角度的选择 903
(一)车刀切削部分的组成 903
(二)确定车刀几何角度的辅助平面 905
(四)车刀的前面形状 906
(五)车刀几何角度的选择 906
第二节 钻头 914
一、钻头的类型和用途 914
(二)铰刀刃磨方式 916
二、高速钢麻花钻的修磨 917
(一)麻花钻的结构要素和几何参数 917
(二)麻花钻的修磨 918
(三)群钻 920
三、中心钻的类型和用途 920
第三节 铰刀 925
一、铰刀的类型和用途 925
(一)铰刀各部分名称 936
三、铰刀的刃磨 936
二、铰刀的精度等级和公差 936
(三)研磨铰刀 938
第四节 铣刀 939
一、铣刀的类型和用途 939
二、常用铣刀的规格和尺寸 943
表6-51 直柄立铣刀 943
表6-52 莫氏锥柄立铣刀 944
表6-53 套式立铣刀 945
表6-54 直齿三面刃铣刀 946
表6-55 镶齿三面刃铣刀 947
表6-56 圆柱形铣刀 948
表6-57 镶齿套式面铣刀 949
表6-58 锯片铣刀 950
表6-59 链轮铣刀 953
表6-60 齿轮铣刀刀号选用表 954
表6-61 直齿锥齿轮铣刀刀号选用表 954
三、铣刀的刃磨 954
(一)铣刀各部分名称 954
(二)铣刀刃磨方式 954
第五节 丝锥 957
一、丝锥的类型和用途 957
二、丝锥的选择 957
(一)丝锥各部分名称 957
(二)等径和不等径成组丝锥 957
(一)刃磨前面 961
(三)丝锥切削锥部长度的选择 962
(四)丝锥螺纹公差选择 962
三、丝锥的刃磨 963
一、滚刀的类型和用途 964
第六节 滚刀 964
(--)刃磨切削锥部 964
二、常用滚刀的规格和尺寸 965
表6-67 AA、A、B、C级齿轮滚刀 965
表6-68 杆式蜗轮滚刀 967
表6-69 孔式蜗轮滚刀 967
表6-70 链轮滚刀 967
三、滚刀的刃磨 968
(一)螺旋槽滚刀刃磨 968
(二)直槽滚刀刃磨 968
第七节 冷却润滑液 972
表7-1 普通车床 974
第七章 车削加工 974
第一节 车床的主要技术性能 975
表7-2 六角车床 978
表7-3 立式车床 981
表7-6 按表面粗糙度选择进给量(车床及立车) 981
表7-4 数控车床 982
第二节 车床的切削用量 985
表7-5 粗车外圆走刀量 985
表7-7 硬质合金车刀的切削速度 989
表7-8 高速钢车刀切削用量 989
表7-10 切断及车槽的走刀量 990
表7-9 陶瓷车刀切削用量 990
表7-11 在车床上镗孔进给量 991
表7-12 难加工材料车削用量 992
第三节 车外圆 994
一、车刀装夹 994
二、丁件安装 994
(一)用顶尖安装 994
(二)用卡盘安装 995
(三)用芯轴安装 1000
(四)用中心架和跟刀架加工长轴 1001
(一)用宽刀车圆锥表面 1011
(三)偏移尾座车圆锥表面 1011
(二)转动刀架车圆锥表面 1011
一、圆锥常用计算公式 1011
二、圆锥表面的加工方法 1011
第四节 圆锥表面加工 1011
(四)用仿形尺车圆锥表面 1013
(五)成形面加工 1013
第五节 切断 1017
第六节 车内孔 1020
一、孔加工刀具 1020
二、用花盘和角铁车内孔 1021
第七节 薄壁件加工 1023
一、一般常识 1025
第八节 车螺纹 1025
二、多线螺纹车削 1027
第九节 一级保养和文明生产 1029
一、一级保养 1029
二、文明生产 1030
第一节 刨、插削特点及机床 1031
第八章 刨、插削加工 1033
一、刨、插削特点 1033
二、刨、插削机床的主要技术性能 1033
表8-1 牛头刨床 1034
表8-2 龙门刨床 1036
表8-3 插床 1037
第二节 刨、插削常识 1038
一、刨、插削用量 1038
表8-4 切削用量的名词解释和计算公式 1038
表8-5 常用刨削用量 1039
表8-6 插刀切削角度参数和切削用量选择 1040
二、刨刀、插刀的结构特点 1040
(一)刨刀的结构 1040
(二)插刀的结构 1041
(一)机床的维护保养 1042
(二)安全技术 1042
三、刨削类机床的合理使用 1042
四、维护保养和安全技术 1042
第三节 刨、插削加工常用工具、夹具及工件的装夹 1043
一、常用工具 1043
表8-8 撑板与顶具 1046
表8-9 矩形垫板 1046
表8-10 龙门刨支承 1047
表8-11 挡铁 1048
表8-12 平面千斤顶 1048
表8-13 插刀杆及尺寸 1049
(一)精刨斜镶条两宽面的专用夹具 1050
(二)刨薄板用夹具 1050
二、夹具 1050
三、工件的装夹 1051
表8-14 工件的找正 1051
表8-15 常见各种工件的装夹 1052
第四节 刨、插加工方法 1055
一、刨平面、平行面及垂直面 1055
二、刨斜面及薄形工件 1055
三、刨各种槽及切断 1055
四、曲面的刨、插加工 1063
五、键及花键加工 1064
六、孔内槽、多边形、成型面的刨、插加工 1066
七、齿条及直齿锥齿轮加工 1068
(一)齿条加工 1068
(二)直齿锥齿轮加工 1070
八、典型零件的刨削加工 1072
表8-22 轴承盖机械加工工艺过程 1074
表8-23 轴承座机械加工工艺过程 1075
九、刨、插削加工缺陷及措施 1076
表8-24 平面加工缺陷及措施 1076
表8-25 垂直面加工缺陷及措施 1077
表8-26 斜面及槽加工缺陷及措施 1079
表8-27 插键槽加工缺陷及措施 1079
第五节 提高劳动生产率的途径 1081
一、刨床附件的结构形式 1081
二、提高劳动生产率的途径 1082
二、铣削装置 1082
第六节 现代加工技术——拉削 1084
一、拉削过程的特点 1084
二、拉削机床的主要技术性能 1085
表8-30 卧式拉床 1086
表8-31 立式数控液压拉床 1087
三、拉削方式及刀具 1088
(一)拉削方式 1088
(二)拉削刀具 1088
表9-1 立铣可达到的精度 1093
(一)铣削特点及铣削内容 1093
(二)铣削可达到的精度 1093
一、铣削特点 1093
第一节 铣削特点及铣床性能 1093
第九章 铣削加工 1093
表9-2 卧铣可达到的精度 1095
表9-3 龙门铣削可达到的精度表 1095
二、铣床及滚齿机的主要技术性能 1096
表9-4 卧式升降台式铣床 1096
表9-5 立式铣床 1099
表9-6 龙门铣床 1102
表9-7 滚齿机 1104
(三)进给量 1107
(二)铣削宽度 1107
(一)铣削深度 1107
一、铣削用量选择 1107
第二节 铣削常识 1107
(四)铣削速度 1110
二、铣削用量计算 1110
第三节 分度头 1111
表9-15 分度头 1112
表9-16 单式分度表 1115
表9-17 近似分度表 1118
第四节 铣削加工方法 1119
一、逆铣和顺铣 1119
(一)逆铣 1119
三、铣平行平面 1120
二、铣垂直平面 1120
(二)顺铣 1120
四、铣斜面 1124
(一)图上斜面表示法 1124
(二)铣斜面的方法 1124
(三)斜面的检验方法 1124
五、铣台阶面 1129
六、铣削花键 1129
表9-24 铣削花键 1130
表9-25 铣花键时常见的弊病及防止办法 1133
七、铣削钩槽 1134
表9-26 键槽的铣削 1134
表9-27 铣T形槽 1138
八、铣直齿离合器 1139
九、铣螺旋槽 1141
十、铣等速圆盘凸轮 1144
十一、刀具的开齿 1146
(一)圆柱面直齿槽的开齿 1146
(二)端面槽的开齿 1150
十二、铣削齿轮 1151
(一)齿轮的加工方法 1151
(二)铣刀的号数 1152
(三)直齿圆柱齿轮的铣削 1153
表9-37 直齿圆柱齿轮的铣削过程 1153
表9-38 铣齿时产生废品的类型及注意事项 1155
(四)铣直齿条 1156
(五)铣削斜齿圆柱齿轮 1158
表9-40 铣斜齿轮时铣刀号数的选择 1159
表9-41 选择铣刀号数系数K值 1160
表9-42 铣斜齿轮时挂轮的计算 1161
(六)铣直齿圆锥齿轮 1161
第五节 滚削加工 1164
一、飞刀展成铣蜗轮 1164
(二)调整计算与举例 1170
表9-45 滚切直齿圆柱齿轮调整计算 1170
(一)Y 38—1型滚齿机传动系统 1170
二、滚直齿圆柱齿轮 1170
表9-46 单头高速钢滚刀切削速度表 1173
表9-47 速度挂轮表 1174
表9-48 Y38—1型滚齿机分齿挂轮表 1175
表9-49 滚切直齿圆柱齿轮时滚刀架转动方向和角度以及配换齿轮情况 1177
表9-50 刀杆找正精度 1178
表9-51 齿轮齿坯端面的允许偏差 1178
表9-52 齿坯的安装方法及安装精度 1179
三、滚斜齿圆柱齿轮 1180
表9-53 滚斜齿圆柱齿轮的调整计算 1180
表9-54 滚切螺旋齿轮时滚刀架转动方向和角度以及交换齿轮情况 1182
(一)大质数齿轮的滚切原理 1184
(二)滚大质数直齿圆柱齿轮 1184
六、常用的滚齿夹具 1186
(三)滚大质数斜齿圆柱齿轮 1187
五、常用滚齿机挂轮传动比计算 1187
表9-58 滚齿夹具 1188
表9-59 滚齿夹具 1189
表9-60 直形支架 1190
表9-61 滚齿夹具 1191
二、钻削能达到的精度和粗糙度 1192
一、钻削加工的基本概念 1192
三、钻头 1192
第一节 钻削常识 1192
第十章 钻、铰、镗加工 1192
四、钻削时的切削用量及进给量 1193
表10-2 钻削用量计算 1193
表10-3 手动进给钻孔的进给量 1194
表10-4 钻孔径0.25~1mm的切削用量 1194
表10-5 碳结构钢工件上钻孔径2~60mm的切削用量 1195
表10-6 灰铸铁工件上钻孔径2~60mm的切削用量 1196
表10-7 钻奥氏体不锈耐酸钢切削用量表 1198
表10-8 扩孔钻的进给量 1198
表10-9 扩孔钻的切削用量 1199
一、一般钻孔方法 1201
(一)怎样使钻孔轻快 1201
第二节 钻孔方法 1201
(二)怎样提高钻孔的尺寸精度和降低粗糙度 1202
(一)薄板上钻孔 1204
(二)斜面、圆弧面上钻孔 1204
二、特殊工件的钻孔方法 1204
(四)钻十字交叉孔 1205
(五)毛坯上的椭圆孔、偏心孔再扩圆 1205
(三)钻平底孔 1205
(六)钻圆弧、角度等成形孔 1206
(七)钻半壁孔 1206
(八)钻孔径3mm以下的小孔 1207
(九)钻孔径0.5mm以下的微小孔 1208
一、台式钻床 1210
二、立式钻床 1210
第三节 钻孔设备及附件 1210
三、摇臂钻床 1211
四、手电钻 1212
表10-14 JIZ系列单相串激式手电钻技术规格 1212
表10-15 J3Z系列三相工频式手电钻技术规格 1213
五、钻头套 1213
第四节 铰孔一般常识 1213
一、铰孔能达到的精度和粗糙度 1213
二、铰孔方法 1214
(一)铰削余量的选择 1214
(二)铰孔用的冷却润滑液 1214
三、铰刀 1214
四、铰孔的进给量及切削用量 1215
表10-17 铰圆柱孔的进给量 1215
表10-18 钢制件铰孔的切削用量 1216
表10-19 铸铁件铰孔的切削用量 1217
表10-20 铰锥孔的进给量及切削速度 1218
一、影响铰孔精度的因素 1219
二、降低铰孔粗糙度的措施 1219
第五节 提高铰孔精度和降低铰孔粗糙度 1219
三、铰孔常见缺陷 1220
第六节 镗孔常识 1220
(一)镗孔进给量及切削速度的选择 1221
三、镗孔的进给量及切削用量 1221
(二)镗刀进给量的调节 1221
二、镗刀 1221
一、镗孔加工方式 1221
四、温度变化影响镗孔加工精度 1227
(一)机床温度场 1227
一、镗床 1228
第七节 镗孔设备及工具 1228
二、镗孔常用工具 1228
(三)切削热引起工件尺寸变化和形状变化 1228
(二)环境温度 1228
三、镗刀杆 1236
第八节 镗削方法 1240
一、工件装夹 1240
(一)划线法 1242
(二)坐标法 1242
二、镗床主轴定位 1242
(三)利用百分表和块规使主轴定位 1243
(四)利用定位轴和块规使主轴定位 1243
(五)采用通镗杆镗削时的定位法 1245
(六)两孔中心线成直角时的主轴定位法 1246
(一)工件单向镗削 1248
(二)工件调头镗削 1248
三、悬伸镗削 1248
四、通杆镗削 1250
五、镗削螺纹 1252
六、镗削加工的缺陷及原因分析 1255
二、磨床的主要技术性能 1257
一、磨削特点 1257
表11-1 常用外圆磨床及万能外圆磨床 1257
第一节 磨削特点及磨床 1257
第十一章 磨削加工 1257
表11-2 四种型号内圆磨床 1259
表11-3 四种型号平面磨床 1259
表11-4 四种型号工具磨床 1260
第二节 磨削常识 1261
一、磨削的运动方式 1261
表11-5 常用的磨削方式 1262
三、磨削余量与用量的选择 1263
(二)磨削热和磨削温度 1263
(一)磨削余量及其选择 1263
(二)磨削用量的选择 1263
(一)磨削力和磨削功率 1263
二、磨削力、磨削热及磨削温度 1263
(一)切削液的作用 1270
(二)切削液的选择 1270
四、切削液及其净化 1270
一、砂轮的结构特点及标记 1271
第三节 砂轮的选择及修整 1271
(一)砂轮的结构 1271
(四)切削液的净化 1271
(三)切削液使用要点 1271
(二)磨具分类及用途 1272
(三)磨具性能规格的书写顺序 1272
二、砂轮的选择 1278
(一)磨料的选择 1278
(二)粒度的选择 1280
(三)硬度的选择 1280
(四)结合剂的分类及选择 1283
(五)组织及其选择 1284
二、砂轮的平衡及保管 1285
(七)磨具强度及其选择 1285
(一)砂轮的平衡 1285
(六)形状尺寸及其选择 1285
(一)砂轮的修整及修整工具 1286
四、砂轮的修整及其修整用量选择 1286
(二)砂轮的修整用量 1286
(二)砂轮的保管 1286
一、外圆磨床加工 1288
第四节 磨削加工方法 1288
(一)外圆磨床的工作方法 1288
(三)修整砂轮时的注意事项 1288
(二)外圆磨床的工作要点 1289
(三)外圆磨削常见的工件缺陷及其消除 1290
二、内圆磨床加工 1293
(一内圆磨削的工作要点 1293
(二)内圆磨削常见的工件缺陷及其消除 1294
四、曲轴磨床加工 1295
(二)平面磨削常见的工件缺陷及其消除 1295
(一)曲轴磨床的类型 1295
(一)平面磨削的工作要点 1295
三、平面磨床加工 1295
(二)曲轴磨床的工作要点 1296
五、工具磨床加工 1297
(一)工具磨床类型的选择 1297
(一)磨削特点 1298
一、硬脆材料的磨削 1298
(二)超硬磨料砂轮 1298
第五节 特种材料及特种工件的磨削 1298
(二)刃磨刀具时注意事项 1298
(三)金刚石砂轮的选择 1299
(四)金刚石砂轮的磨削用量选择 1301
(二)砂轮选择 1302
(一)磨削特点 1302
(三)磨削用量选择 1302
二、不锈钢及耐热合金的磨削 1302
(三)磨削用量选择 1303
(四)切削液的选择 1303
(二)砂轮选择 1303
四、细长轴的磨削 1303
(一)磨削特点 1303
(一)磨削特点 1303
三、钛合金的磨削 1303
(四)切削液的选择 1303
(一)磨削特点 1304
五、薄壁零件及薄片的磨削 1304
(二)磨削要点 1304
(二)磨削要点 1304
(一)磨削特点 1305
(二)偏心工件的装夹和找正 1305
六、偏心零件的磨削 1305
七、球面的磨削 1306
(一)高精度磨削的特点及应用 1308
一、高精度磨削 1308
(二)工件光滑表面的形成 1308
第六节 高精度和高效率磨削 1308
(三)高精度、低粗糙度磨削砂轮的选择 1309
(四)高精度磨削工艺参数的选择 1309
(一)高速磨削的特点 1312
(二)外圆磨床高速磨削改装(50~60m/s) 1312
二、高速磨削 1312
(三)高速磨削砂轮的选择 1314
(四)高速磨削工艺参数的选择 1314
三、其它高效率磨削 1315
(一)成形磨削 1315
(二)宽砂轮磨削 1316
(三)双端面磨削 1317
(四)主要国家磨具等代号对照表 1318
一、划线 1322
第一节 钳工 1322
(一)划线常识 1322
第十二章 钳工 钣金工 焊接与气割 1322
(二)用平面几何图形作图和等分圆周弦长的方法 1328
(一)凿削常识 1332
二、凿削 1332
(二)凿子的热处理 1332
(三)立体划线实例 1332
三、锯割 1336
(一)锯割常识 1336
(二)锯割方法 1337
(一)锉削常识 1339
(二)锉刀的正确使用和保管 1339
四、锉削 1339
五、攻丝与套丝 1341
(一)攻丝与套丝的常识 1341
(二)丝锥与板牙的修磨 1345
(三)攻丝与套丝的废品分析 1346
(四)丝锥损坏原因及取断丝锥方法 1348
六、刮削 1349
(一)刮削常识 1349
(二)刮削工具 1351
七、研磨 1353
(三)刮削方法 1354
(四)刮削面缺陷分析 1357
(一)研磨常识 1358
(二)研磨剂 1360
(三)研磨工具 1362
八、钳工工具 1363
(二)作展开图的基本方法 1369
(一)线段实长的求法 1369
(三)常用钣金件展开图作法 1369
一、放样 1369
第二节 钣金工 1369
二、剪冲落料 1390
(一)剪切 1390
(二)冲裁 1394
(三)剪冲设备的类型及特点 1394
(四)剪冲机床的型号及主要技术性能 1397
(五)剪冲间隙 1399
(六)剪冲常见缺陷及防止措施 1401
三、弯曲与校正 1402
(一)常用弯曲方法及特点 1402
(二)最小弯曲半径 1406
(三)弯曲件发展开长度计算法 1406
(四)常用校正(校平)方法及特点 1411
(五)弯曲校正机床的型号及主要技术性能 1415
(六)弯曲校正常见缺陷及防止措施 1417
一、焊接常识 1419
(一)焊接的主要方法分类 1419
第三节 焊接与气割 1419
(二)常用的焊接名词术语 1421
表12-67 氧—乙炔气焊的特点及应用范围 1421
二、常用的焊接方法及特点 1423
表12-68 手工电弧焊的特点及应用范围 1424
表12-69 自动埋弧焊的特点及应用范围 1424
表12-70 手工钨极氩弧焊的特点及应用范围 1425
表12-71 二氧化碳气体保护焊的特点及应用范围 1426
表12-72 堆焊的特点及应用范围 1426
三、各种材料的焊接方法 1427
表12-74 碳钢的焊接方法 1427
表12-73 钎焊的特点及应用范围 1427
表12-75 不锈钢的焊接方法 1428
表12-76 低合金钢的焊接特点和焊接方法 1429
表12-77 铜及铜合金的焊接方法 1430
表12-78 铝及铝合金的焊接方法 1431
表12-79 铸铁的焊补方法 1431
四、常见焊接缺陷的产生原因及预防措施 1432
五、气割常识 1434
(一)常用气割的种类 1434
(二)快速气割 1435
(三)等离子弧切割 1437
七、常用焊接、气割设备及工具和材料 1439
(一)常用焊接设备的型号及主要技术性能 1439
六、常见气割缺陷及产生原因 1439
(二)气割设备及工具 1446
(三)焊接材料 1455
(四)气割材料 1459
八、焊接质晕的检验方法 1460
参考文献 1461
四、滚大质数圆柱齿轮 11184
- 《市政工程基础》杨岚编著 2009
- 《零基础学会素描》王金著 2019
- 《工程静力学》王科盛主编 2019
- 《中央财政支持提升专业服务产业发展能力项目水利工程专业课程建设成果 设施农业工程技术》赵英编 2018
- 《Maya 2018完全实战技术手册》来阳编著 2019
- 《化学反应工程》许志美主编 2019
- 《绿色过程工程与清洁生产技术 张懿院士论文集精选 上》《绿色过程工程与清洁生产技术》编写组编 2019
- 《软件工程》齐治昌,谭庆平,宁洪编著 2019
- 《高等教育双机械基础课程系列教材 高等学校教材 机械设计课程设计手册 第5版》吴宗泽,罗圣国,高志,李威 2018
- 《化学工程与工艺专业实验指导》郭跃萍主编 2019
- 《东方杂志 第110册 第25卷 第一至四号 1928年1月-1928年2月》上海书店出版社编 2012
- 《清明 我们的节日》冯骥才编 2017
- 《现代水泥技术发展与应用论文集》天津水泥工业设计研究院有限公司编 2019
- 《甘肃省档案馆指南》甘肃省档案馆编 2018
- 《莼江曲谱 2 中国昆曲博物馆藏稀见昆剧手抄曲谱汇编之一》郭腊梅主编;孙伊婷副主编;孙文明,孙伊婷编委;中国昆曲博物馆编 2018
- 《花时间 我的第一堂花艺课 插花基础技法篇》(日)花时间编辑部编;陈洁责编;冯莹莹译 2020
- 《中央财政支持提升专业服务产业发展能力项目水利工程专业课程建设成果 设施农业工程技术》赵英编 2018
- 《东方杂志 第94册 第22卷 第四至七号 1925年2月-1925年4月》上海书店出版社编 2012
- 《东方杂志 第13册 第四年 第一至三期 1907年3月-1907年5月》上海书店出版社编 2012
- 《远去的老调》经典文库编委会编 2019
- 《指向核心素养 北京十一学校名师教学设计 英语 七年级 上 配人教版》周志英总主编 2019
- 《北京生态环境保护》《北京环境保护丛书》编委会编著 2018
- 《高等教育双机械基础课程系列教材 高等学校教材 机械设计课程设计手册 第5版》吴宗泽,罗圣国,高志,李威 2018
- 《指向核心素养 北京十一学校名师教学设计 英语 九年级 上 配人教版》周志英总主编 2019
- 《高等院校旅游专业系列教材 旅游企业岗位培训系列教材 新编北京导游英语》杨昆,鄢莉,谭明华 2019
- 《中国十大出版家》王震,贺越明著 1991
- 《近代民营出版机构的英语函授教育 以“商务、中华、开明”函授学校为个案 1915年-1946年版》丁伟 2017
- 《新工业时代 世界级工业家张毓强和他的“新石头记”》秦朔 2019
- 《智能制造高技能人才培养规划丛书 ABB工业机器人虚拟仿真教程》(中国)工控帮教研组 2019
- 《AutoCAD机械设计实例精解 2019中文版》北京兆迪科技有限公司编著 2019