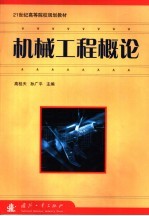
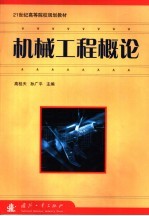
机械工程概论PDF电子书下载
- 电子书积分:12 积分如何计算积分?
- 作 者:高桂天,孙广平主编
- 出 版 社:北京:国防工业出版社
- 出版年份:2006
- ISBN:7118045985
- 页数:344 页
第1章 绪论 1
1.1 材料及其机械制造工艺的历史发展 1
1.2 工程材料的现状及发展趋势 1
1.3 机械制造工艺的现状及发展趋势 3
1.3.1 机械制造工艺概况 3
1.3.2 机械制造工艺的技术进展 4
1.3.3 机械制造技术系统 5
第2章 工程材料的性能 6
2.1 材料的力学性能 6
2.1.1 强度和塑性 6
2.1.2 硬度 8
2.1.3 冲击韧性 10
2.1.4 疲劳极限 10
2.1.5 断裂韧性 11
2.1.6 蠕变极限和持久强度 11
2.2 材料的物理化学及其他性能 12
2.2.1 材料的物理性能 12
2.2.2 材料的化学性能 13
2.2.3 材料的工艺性能 13
2.2.4 材料的经济性 13
3.1.1 结合键 14
第3章 材料的结构与结晶 14
3.1 材料的结合方式 14
3.1.2 晶体和非晶体 15
3.2 金属材料的晶体结构 15
3.2.1 晶体结构的基本概念 15
3.2.2 三种常见的金属晶体结构 16
3.2.3 实际金属的晶体结构 17
3.2.4 合金的相结构 18
3.3.1 陶瓷材料的结构特点 20
3.3.2 高分子材料的结构特点 20
3.3 非金属材料的结构特点 20
3.4 金属材料的结晶 22
3.4.1 纯铁的一次结晶 23
3.4.2 纯铁的同素异构转变 26
3.5 铁碳合金相图 27
3.5.1 铁碳合金的基本组织 27
3.5.2 Fe-Fe3C合金相图分析 28
3.5.3 铁碳合金的分类 30
3.5.4 典型合金的平衡结晶过程及组织 30
3.5.5 含碳量对铁碳合金平衡组织和性能的影响 33
4.1 钢铁材料的热处理 36
第4章 材料的强化和处理 36
4.1.1 钢在加热时的转变 37
4.1.2 钢在冷却时的转变 39
4.1.3 钢的普通热处理 45
4.1.4 钢的表面热处理 50
4.1.5 常见热处理缺陷及其预防 53
4.1.6 热处理工艺的应用 53
4.1.7 热处理新技术简介 54
4.2 工程材料的表面处理 55
4.2.1 气相沉积 56
4.2.2 化学转化膜技术 57
4.2.3 电镀和化学镀 58
4.2.4 涂料和涂装工艺 59
4.3 高聚物的改性强化简介 60
第5章 常用金属材料 62
5.1 非合金钢(碳钢) 62
5.1.1 常存杂质对钢性能的影响 62
5.1.2 非合金钢(碳钢)的分类 62
5.1.3 普通碳素结构钢 63
5.1.4 优质碳素结构钢 63
5.2 合金钢 64
5.1.7 铸造碳钢 64
5.1.6 易切削结构钢 64
5.1.5 碳素工具钢 64
5.2.1 合金元素在钢中的作用 65
5.2.2 低合金高强度结构钢 68
5.2.3 合金结构钢 68
5.2.4 合金工具钢 71
5.2.5 特殊性能钢 75
5.3 铸铁 77
5.3.1 铸铁的分类 77
5.3.2 灰口铸铁 78
5.3.3 球墨铸铁 81
5.3.4 可锻铸铁 84
5.3.5 蠕墨铸铁 85
5.4 非铁金属材料(有色金属) 86
5.4.1 铝及其合金 87
5.4.2 铜及其合金 90
5.4.3 滑动轴承合金 93
5.4.4 粉末冶金材料 94
6.1.2 塑料的分类和应用 96
6.1.1 塑料的特性 96
6.1 工程塑料 96
第6章 非金属材料简介 96
6.2 橡胶 98
6.2.1 橡胶的特性 98
6.2.2 橡胶的种类和应用 98
6.3 陶瓷材料 99
6.3.1 陶瓷的特性 99
6.3.2 陶瓷的种类和应用 99
6.4 复合材料 100
6.4.1 纤维增强复合材料 100
6.4.3 细粒增强复合材料 101
6.4.2 层叠复合材料 101
6.4.4 骨架复合材料 102
第7章 铸造 103
7.1 砂型铸造 103
7.1.1 型(芯)砂 104
7.1.2 造型 105
7.2 合金的铸造性能 107
7.2.1 合金的流动性 107
7.2.2 影响合金流动性的因素 107
7.2.3 合金的凝固与收缩 108
7.2.4 影响合金收缩的因素 109
7.2.5 缩孔缩松的形成及防止措施 109
7.2.6 铸造内应力、变形和裂纹 111
7.2.7 合金的偏析 113
7.2.8 铸件中的气孔 114
7.3 常用合金铸件的生产工艺特点 114
7.3.1 灰铸铁的生产工艺特点 114
7.3.5 铸钢的生产工艺特点 115
7.3.4 蠕墨铸铁的生产工艺特点 115
7.3.3 可锻铸铁的生产工艺特点 115
7.3.2 球墨铸铁的生产工艺特点 115
7.3.6 非铁合金(有色合金)的生产工艺特点 116
7.4 铸造工艺图的制定 117
7.4.1 浇注位置与分型面的选择 117
7.4.2 工艺参数的选择 118
7.4.3 铸造工艺图举例 120
7.4.4 浇注系统 120
7.5 特种铸造 122
7.5.1 熔模铸造 122
7.5.2 金属型铸造 123
7.5.3 压力铸造 124
7.5.4 离心铸造 125
7.5.5 真空实型铸造 126
7.6 零件的铸造结构设计 127
7.6.1 砂型铸造工艺对结构设计的要求 127
7.6.2 合金铸造性能对结构设计的要求 129
第8章 金属压力加工 134
8.1 金属的塑性变形 136
8.1.1 金属塑性变形的实质 136
8.1.2 塑性变形后金属的组织和性能 137
8.1.3 冷变形、热变形和温变形 138
8.1.4 金属锻件的特点 139
8.1.5 金属的锻造性能 140
8.2 自由锻 142
8.2.1 自由锻设备 142
8.2.2 自由锻的基本工序 142
8.2.3 自由锻工艺规程的制订 143
8.2.4 零件的自由锻结构工艺性 147
8.3 模锻 147
8.3.1 胎模锻 148
8.3.2 锤上模锻 149
8.3.3 模锻工艺规程的制定 151
8.3.4 零件的模锻结构工艺性 154
8.3.5 曲柄压力机上模锻 154
8.3.6 平锻机上模锻 156
8.3.7 摩擦压力机上模锻 157
8.4 板料冲压 158
8.4.1 板料冲压的基本工序 158
8.4.2 冲模的分类和结构 162
8.5 其他压力加工方法 164
8.5.3 特种轧制 165
8.5.2 液态模锻 165
8.5.1 精密模锻 165
第9章 焊接 167
9.1 金属熔化焊工艺基础 167
9.1.1 焊接电弧 167
9.1.2 熔化焊的冶金特点 168
9.1.3 熔化焊中需采取的措施 168
9.1.4 焊接接头的金属组织及性能 169
9.1.5 焊接应力、变形及裂纹 171
9.2 焊接方法 174
9.2.1 手工电弧焊 174
9.2.2 埋弧自动焊 177
9.2.3 气体保护焊 178
9.2.4 压力焊 180
9.2.5 钎焊 183
9.2.6 其他焊接方法 184
9.3 常用金属材料的焊接 187
9.3.1 金属材料的焊接性 187
9.3.2 钢的焊接 188
9.3.3 铸铁的焊补 190
9.3.4 非铁金属的焊接 190
9.4.2 焊接方法的选择 192
9.4 焊接结构设计 192
9.4.1 焊接结构材料的选择 192
9.4.3 焊接接头型式的选择 193
9.4.4 焊接结构工艺性 194
第10章 金属切削加工的基础知识 198
10.1 切削运动和切削要素 198
10.1.1 切削运动 198
10.1.2 切削要素 199
10.2 刀具材料和刀具几何形状 201
10.2.1 刀具材料 201
10.2.2 刀具的几何形状 203
10.3 金属切削过程 208
10.3.1 切屑的形成过程及种类 208
10.3.2 积屑瘤 209
10.3.3 切削力 210
10.3.4 切削热 213
10.3.5 刀具磨损和耐用度 214
10.3.6 切削用量的选择 216
10.3.7 工件材料的切削加工性 217
10.4.1 尺寸精度 218
10.4 零件的加工质量 218
10.4.2 形状和位置精度 223
10.4.3 表面粗糙度 227
第11章 金属切削机床的基础知识 230
11.1 机床的分类及型号 230
11.1.1 机床的分类 230
11.1.2 机床的型号 230
11.2 机床的机械传动 233
11.2.1 机床的机械传动机构 233
11.2.2 机床传动链及其传动比 239
11.2.3 卧式车床的传动系统 240
11.3 机床的液压传动 242
第12章 车床及其工作 244
12.1 车床 244
12.2 工件的安装及所用附件 245
12.3 车床工作 248
12.3.1 车外圆 248
12.3.2 车端面 249
12.3.3 切槽和切断 249
12.3.4 孔的加工 249
12.3.5 车锥面 250
12.3.6 车成形面 252
12.3.7 车螺纹 253
12.4 车削加工的特点 256
第13章 钻床、镗床及其工作 258
13.1 钻床 258
13.2 钻头及钻削过程 259
13.2.1 麻花钻 259
13.2.2 钻削过程 259
13.2.3 钻削加工的特点 260
13.3 钻床工作 261
13.5.1 镗床工作 263
13.5 镗床工作及镗削加工的特点 263
13.4 镗床 263
13.5.2 镗削加工的特点 266
第14章 刨床、拉床、铣床及其工作 267
14.1 刨床 267
14.2 刨床工作及刨削加工的特点 268
14.2.1 刨床工作 268
14.2.2 刨削加工的特点 268
14.3 拉床及其工作 269
14.3.1 拉刀 269
14.3.2 拉床 270
14.4 铣床 271
14.3.3 拉床工作 271
14.3.4 拉削加工的特点 271
14.5 铣削过程及铣削方式 273
14.5.1 铣削用量 273
14.5.2 铣削力 273
14.5.3 铣削方式 274
14.6 铣床附件及工件安装 276
14.6.1 铣床附件 276
14.6.2 工件安装 277
14.7.1 铣床工作 278
14.7 铣床工作及铣削加工的特点 278
14.7.2 铣削加工的特点 281
第15章 磨床及其工作 283
15.1 砂轮 283
15.1.1 砂轮特性 283
15.1.2 砂轮的安装和修整 286
15.2 磨削过程及磨削加工的特点 286
15.2.1 砂轮的磨削过程 286
15.2.2 磨削运动和磨削用量 287
15.2.3 磨削加工的特点 287
15.3.1 外圆磨床及其工作 288
15.3 磨床及其工作 288
15.3.2 内圆磨床及其工作 291
15.3.3 平面磨床及其工作 291
15.4 光整加工 292
15.4.1 研磨 292
15.4.2 珩磨 293
15.4.3 超级光磨 293
15.4.4 抛光 294
16.1 外圆面加工 295
16.2 孔加工 295
第16章 各种表面加工方法综述 295
16.3 平面加工 296
16.4 螺纹加工 297
16.4.1 攻丝和套扣 297
16.4.2 车螺纹 298
16.4.3 铣螺纹 298
16.4.4 滚压螺纹 299
16.4.5 磨螺纹 299
16.5 圆柱齿轮的齿形加工 300
16.5.1 齿轮齿形加工 300
16.5.2 齿轮齿形的精加工 303
16.5.3 圆柱齿轮齿形加工方法的选择 306
第17章 机械加工工艺过程 307
17.1 基本概念 307
17.1.1 生产过程和工艺过程 307
17.1.2 生产类型 308
17.2 工件的安装及获得尺寸的方法 309
17.2.1 工件的安装方法 309
17.2.2 工件获得尺寸的方法 310
17.2.3 工件定位的六点定则 310
17.2.4 定位基准的选择 311
17.2.5 夹具简介 314
17.3.1 掌握原始资料 318
17.3.2 工艺分析 318
17.3.3 定位基准的选择和工艺路线的拟订 318
17.3 零件工艺过程的拟订 318
17.3.4 编写工艺文件 319
17.4 典型零件的工艺过程 320
17.4.1 轴类零件 320
17.4.2 盘套类零件 322
17.4.3 箱体件 324
18.1.1 自动和半自动机床 327
第18章 机械加工工艺过程的自动化 327
18.1 大批大量生产的自动化机床 327
18.1.2 专门化机床和专用机床 328
18.1.3 组合机床 328
18.2 数控机床 329
18.2.1 数控机床的工作原理 329
18.2.2 数控机床的分类 329
18.2.3 数控机床的特点及应用 331
18.2.4 数控机床的发展 331
18.3.2 自动线的联结方式 332
18.3.1 自动线的基本机构 332
18.3 自动线 332
18.3.3 自动线的类型 333
第19章 特种加工 335
19.1 电火花加工 335
19.1.1 电火花加工的原理 335
19.1.2 电火花加工的设备 336
19.1.3 电火花加工的特点及应用 337
19.2 电解加工 337
19.2.1 电解加工的原理 337
19.2.3 电解加工的特点及应用 338
19.2.2 电解加工的设备 338
19.2.4 电解磨削简介 339
19.3 超声波加工 339
19.3.1 超声波加工的原理 339
19.3.2 超声波加工设备 340
19.3.3 超声波加工的特点及应用 340
19.4 激光加工 342
19.4.1 激光加工的原理 342
19.4.2 激光加工的特点及应用 342
参考文献 343
- 《市政工程基础》杨岚编著 2009
- 《全国高等中医药行业“十三五”创新教材 中医药学概论》翟华强 2019
- 《工程静力学》王科盛主编 2019
- 《中央财政支持提升专业服务产业发展能力项目水利工程专业课程建设成果 设施农业工程技术》赵英编 2018
- 《化学反应工程》许志美主编 2019
- 《绿色过程工程与清洁生产技术 张懿院士论文集精选 上》《绿色过程工程与清洁生产技术》编写组编 2019
- 《软件工程》齐治昌,谭庆平,宁洪编著 2019
- 《海绵城市概论》刘娜娜,张婧,王雪琴 2017
- 《高等教育双机械基础课程系列教材 高等学校教材 机械设计课程设计手册 第5版》吴宗泽,罗圣国,高志,李威 2018
- 《化学工程与工艺专业实验指导》郭跃萍主编 2019
- 《指向核心素养 北京十一学校名师教学设计 英语 七年级 上 配人教版》周志英总主编 2019
- 《北京生态环境保护》《北京环境保护丛书》编委会编著 2018
- 《指向核心素养 北京十一学校名师教学设计 英语 九年级 上 配人教版》周志英总主编 2019
- 《抗战三部曲 国防诗歌集》蒲风著 1937
- 《高等院校旅游专业系列教材 旅游企业岗位培训系列教材 新编北京导游英语》杨昆,鄢莉,谭明华 2019
- 《中国十大出版家》王震,贺越明著 1991
- 《近代民营出版机构的英语函授教育 以“商务、中华、开明”函授学校为个案 1915年-1946年版》丁伟 2017
- 《新工业时代 世界级工业家张毓强和他的“新石头记”》秦朔 2019
- 《智能制造高技能人才培养规划丛书 ABB工业机器人虚拟仿真教程》(中国)工控帮教研组 2019
- 《陶瓷工业节能减排技术丛书 陶瓷工业节能减排与污染综合治理》罗民华著 2017