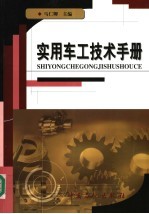
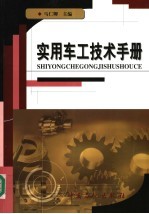
实用车工技术手册PDF电子书下载
- 电子书积分:16 积分如何计算积分?
- 作 者:马仁卿主编
- 出 版 社:北京:中国石化出版社
- 出版年份:2004
- ISBN:7801646258
- 页数:526 页
第1章 车削加工常用资料 1
1.1 常用字母、罗马数字与国家部分标准代号 1
1.1.1 常用字母表与罗马数字表 1
目录 1
1.1.2 常用有关的符号 3
1.1.3 国家部分标准代号 12
1.2 法定计量单位与常见非法定计量单位 12
1.2.1 中华人民共和国法定计量单位 12
1.2.2 法定计量单位与常见非法定计量单位换算 14
1.2.3 法定计量单位常用符号的错误写法 18
1.2.4 平面角的角、分、秒与弧度换算 20
1.3 车削加工常用零件结构要素标准 21
1.3.1 锥度与锥角系列 21
1.3.2 中心孔类型与结构尺寸 22
1.3.4 滚花 24
1.3.3 球面半径 24
1.3.5 零件倒圆与倒角 25
1.3.6 回转面与端面砂轮越程槽 26
1.4 常用材料的有关数据 27
1.4.1 常用金属材料的熔点、热导率与比热容 27
1.4.2 常用材料的线胀系数 28
1.4.3 常用材料的密度 28
1.4.4 常用金属材料的弹性模量和弹性剪切模量 29
1.4.5 常用材料滑动和滚动摩擦系数的概值 29
1.5 热处理及表面处理常识 30
1.5.1 热处理常识 30
1.5.2 化学热处理常识 32
1.5.3 表面处理常识 32
1.6.1 直齿圆柱齿轮渐开线齿形的近似画法 34
1.6 直齿圆柱齿轮渐开线齿形的近似画法及冷缠弹簧心轴直径的计算 34
1.6.2 冷缠拉力弹簧心轴直径的计算与压力弹簧数据表 35
1.7 基本机械传动计算及平带、V带与直齿圆柱齿轮传动计算 37
1.7.1 普通平带传动计算 37
1.7.2 普通V带传动计算 39
1.7.3 直齿圆柱齿轮传动计算 42
1.8 圆柱蜗杆传动精度与公差 53
1.8.1 圆柱蜗杆传动精度等级与其公差 53
1.8.2 蜗杆传动的侧隙规定 57
1.8.3 蜗杆蜗轮图样标注与其齿坯的尺寸形状公差 58
第2章 技术测量及公差与配合 62
2.1 技术测量的基本概念及量具与测量方法的分类 62
2.1.1 技术测量的基本概念 62
2.1.2 计量器具与测量方法的分类 62
2.2.1 计量器具的度量指标 63
2.2 计量器具的度量指标及常用量具量仪 63
2.2.2 常用量具与量仪简介 64
2.2.3 量块与其附件应用简介 70
2.2.4 常用量具与量仪正确操作姿势的示范 71
2.3 测量误差的分析及随机误差的特性与处理 74
2.3.1 测量误差的来源 74
2.3.2 测量误差的分类 74
2.3.3 随机误差的特性与处理 75
2.4 计量器具的选择方法及其主要根据 76
2.4.1 测量不确定度和验收极限 76
2.4.2 计量器具的选择方法 77
2.5 量具、量仪测量的极限误差及其允许误差 79
2.5.1 常用量具、量仪测量的极限误差 79
2.5.2 常用测微量具、量仪测量的允许误差 80
2.6 《公差与配合》新国标的基本结构及公差与配合的基准制 81
2.6.1 标准公差系列 81
2.5.3 量块测量的允许误差 81
2.6.2 基本偏差系列 82
2.6.3 公差与配合的基准制 82
2.6.4 公差带代号、配合代号与其表示方法 82
2.7 标准公差及公差带极限偏差 84
2.7.1 标准公差数值表 84
2.7.2 新国标公差等级与旧国标精度等级对照 84
2.7.3 孔、轴的公差带极限偏差表 85
2.7.4 未注公差的线性和角度尺寸的极限偏差 91
2.8 圆锥角公差及未注公差角度的极限偏差 92
2.8.1 圆锥角的公差数值表 92
2.8.2 圆锥直径公差所能限制的最大圆锥角误差 93
2.9.1 形状和位置公差的定义、符号与图样标注法 94
2.8.3 未注公差角度的极限偏差 94
2.9 形状及位置公差 94
2.9.2 形位公差带的定义、标注和解释 97
2.9.3 图样上注出的形位公差值和未注形位公差值 104
2.9.4 形位公差原则 106
2.9.5 形位误差检测规定 107
2.9.6 形位误差常用检测方案 109
2.10 表面粗糙度评定参数与图样标注及其检测方法 118
2.10.1 表面粗糙度评定参数与其数值 118
2.10.2 表面粗糙度符号、代号与其标注方法 119
2.10.3 表面粗糙度的检测方法 123
2.10.4 新国标的粗糙度与旧国标的光洁度对照表 123
2.10.5 表面粗糙度评定参数值Ra与加工方法的选择 124
3.1.1 产品名称、用途、特性和工艺方法表示符号 127
第3章 金属材料切削加工性能的分析及金属切削的基本规律 127
3.1 产品名称、用途、特性和工艺方法表示符号及牌号表示方法 127
3.1.2 钢号表示方法 128
3.1.3 金属材料力学性能指标的名词解释 129
3.1.4 黑色金属硬度与强度换算值 130
3.2 铸铁及碳素铸钢件牌号表示方法 135
3.2.1 铸铁牌号、化学成分、力学性能与用途 135
3.2.2 铸钢牌号表示方法 137
3.2.3 钢的分类 138
3.3 钢材的涂色标记及常用钢的火花鉴别法 140
3.3.1 钢材的涂色标记 140
3.3.2 常用钢的火花鉴别法 140
3.4 常用钢的牌号、化学成分及其力学性能 142
3.4.1 碳素结构钢牌号、化学成分和力学性能 142
3.4.2 优质碳素钢的牌号、化学成分和力学性能 144
3.4.3 合金结构钢的统一数字代号、牌号、化学成分和力学性能 145
3.4.4 常用弹簧钢与不锈钢的牌号、化学成分和力学性能 146
3.4.5 常用碳素工具钢与合金工具钢的牌号、化学成分和试样淬火硬度 147
3.5 非铁金属及合金产品牌号表示方法与分类 148
3.5.1 常用非铁金属与其合金产品牌号表示方法 148
3.5.2 常用非铁金属与其合金的分类 151
3.5.3 铸造铝合金的牌号、代号、主要元素、杂质限量、铸造方法、合金状态、力学性能与热处理规范 152
3.5.4 铸造铝合金牌号表示方法、主要化学元素和含量与牌号示例 157
3.5.5 铜与铜合金拉制棒和挤制棒的牌号、状态和力学性能 159
3.5.6 铸造铜合金的牌号、名称、主要化学成分、杂质限量、铸造方法、力学性能和主要特性 163
3.6 金属材料切削加工性能及相对切削加工性能的分析 169
3.6.1 金属材料切削加工性能的概述 169
3.6.2 金属材料切削加工性能的主要影响因素 169
3.6.4 金属材料切削加工性能的评定指标与方法 173
3.6.3 改善金属材料切削加工性能的主要方法 173
3.6.5 金属材料相对切削加工性能的简介 174
3.7 金属切削过程的变形规律及切屑种类与其形态变化 175
3.7.1 车削加工的运动与工件上所出现的表面 175
3.7.2 车削过程变形区的划分 175
3.7.3 金属切削过程的变形规律 176
3.7.4 切屑的种类与其形态的变化 177
3.7.5 积屑瘤的形成、作用与其主要影响因素 178
3.7.6 金属工件已加工表面的冷作硬化 179
3.8 切削力及切削功率 179
3.8.1 车削加工的切削力 179
3.8.2 影响切削力的主要因素 180
3.8.3 切削力的试验测量值与经验公式的建立 182
3.8.4 切削力与切削功率计算的举例 187
3.8.5 切削力的修正系数与其数值 189
3.9 切削热及切削温度 192
3.9.1 切削热的来源与传散 192
3.9.2 切削温度 193
3.9.3 切削温度的主要影响因素 193
3.10 刀具的磨损及刀具的耐用度 196
3.10.1 刀具磨损的形式 196
3.10.2 刀具磨损的原因 197
3.10.3 刀具磨损的过程与磨钝标准 198
3.10.4 刀具耐用度的定义和切削用量与刀具耐用度之间的关系式 200
3.10.5 刀具合理耐用度的制定原则 201
4.1.3 我国现用车刀材料的简介 204
4.1.1 常用刀具材料基本特性 204
4.1.2 常用刀具材料基本特性的优劣顺序 204
4.1 刀具材料必须具备的基本特性 204
第4章 刀具材料、几何参数及手工刃磨 204
4.2 刀具材料合理选择的主要依据及其基本原则 209
4.2.1 影响刀具材料合理选择的主要因素 209
4.2.2 刀具材料合理选择的主要依据 210
4.2.3 刀具材料合理选择的基本原则 210
4.3 车刀切削部分的构造要素及静止基准系的切削角度 211
4.3.1 车刀切削部分构造要素的名称和定义 211
4.3.2 车刀静止基准系与切削角度的定义 211
4.4 车刀工作角度的主要影响因素 213
4.4.1 进给运动对车刀工作角度的影响 214
4.4.2 车刀装夹得高和低对车刀工作角度的影响 215
4.4.3 车刀装夹得左右歪斜对车刀工作角度的影响 216
4.5 车刀合理几何参数的选择原则 216
4.5.1 车刀过渡刃的形式与参数 217
4.5.2 车刀的刃口形式与刃口参数 218
4.5.3 车刀前刀面的形状与基本类型 219
4.5.4 车刀基本切削角度的作用与其选择原则 219
4.5.5 车刀合理切削角度的参考值 223
4.6 车刀的基本类型及其结构形式 224
4.6.1 焊接式和机夹式高速钢车刀的基本类型 224
4.6.2 焊接式硬质合金车刀的基本类型 227
4.6.3 机夹不重磨式硬质合金车刀的基本类型 228
4.6.4 机夹不重磨式硬质合金车刀的简介 228
4.7 在车削加工中影响断屑的主要因素及常用断屑的方法 233
4.7.1 影响断屑的主要因素 233
4.7.2 断屑槽断屑台与断屑块进行断屑的简介 235
4.7.3 调节切削用量与改变切削角度进行断屑 236
4.8 刀具的手工刃磨及其步骤 236
4.8.2 根据刀具材料选用砂轮与手工刃磨刀具的步骤 237
4.8.1 手工刃磨刀具的安全守则与注意事项 237
4.8.3 砂轮刃磨后的刀具以油石进行手工研磨 238
4.8.4 刀具刃磨切削角度的检验 239
4.9 先进车刀的介绍 240
4.9.1 45°强力切削车刀 240
4.9.2 75°机械夹固式高速切削车刀 241
4.9.3 90°银白屑车刀 241
4.9.4 93°细长轴精车刀 242
4.9.5 淬硬钢外圆车刀 243
4.9.6 45°机械夹固式奥氏体不锈钢外圆车刀 244
4.9.7 球状切屑的螺纹车刀 245
4.9.8 山形刃屋脊式下料切断刀 245
4.9.9 90°机夹式集屑车刀 246
4.9.10 90°脆铜卷屑车刀 247
4.10 先进群钻的简介 248
4.10.1 基本群钻的几何参数 248
4.10.2 钻铸铁群钻的几何参数 249
4.10.3 钻不锈钢断屑群钻的几何参数 250
4.10.4 钻紫铜群钻的几何参数 251
4.10.5 钻黄铜群钻的几何参数 252
第5章 卧式车床型号构造、传动系统、精度检验与数控机床简介 253
5.1 金属切削机床的型号编制方法 253
5.1.1 通用机床型号的表示方法 253
5.1.2 最早建厂和生产车床的企业名称与代号 256
5.1.3 金属切削机床车床类统一名称与组、系的划分 257
5.1.4 已生产在用卧式车床型号的简介 259
5.2 卧式车床的构造、性能、基本类型及其技术规格和加工范围 260
5.2.1 卧式车床的基本构造 260
5.2.3 卧式车床的基本类型 261
5.2.2 卧式车床的性能 261
5.2.4 常用卧式车床的技术规格 262
5.2.5 卧式车床的加工范围 264
5.3 卧式车床的传动系统分析及C620-1型车床传动系统的特点 264
5.3.1 卧式车床床头变速箱的传动系统分析 266
5.3.2 卧式车床进给箱的传动系统分析 269
5.3.3 卧式车床溜板箱的传动系统分析 270
5.4 卧式车床的维护保养和润滑及其有关的安全技术和安全操作规则 272
5.4.1 卧式车床的维护与保养 272
5.4.2 卧式车床的润滑 273
5.4.3 车工应掌握的安全技术 275
5.4.4 卧式车床的安全操作规则 277
5.5 卧式车床的精度标准及其精度检验 277
5.5.1 卧式车床精度标准的简介 277
5.5.2 普通精度级卧式车床几何精度主要检验项目的检验 278
5.5.3 精密精度级卧式车床工作精度的检验 287
5.5.4 卧式车床的精度对车削加工零件质量的影响 288
5.6 影响加工精度的基本因素及其改善措施 288
5.6.1 影响加工尺寸精度的基本因素及其改善措施 288
5.6.2 影响加工形状精度的基本因素及其改善措施 289
5.6.3 影响加工位置精度的基本因素及其改善措施 291
5.7 工件加工缺陷的原因及其消除、车床主要部位配合间隙的调整 292
5.7.1 工件出现加工缺陷的主要原因及其消除的方法 292
5.7.2 卧式车床主要部位配合间隙的调整 293
5.8 车削振动的原因及消除措施 297
5.8.1 车削振动的主要类型及其特征 297
5.8.2 产生自激振动的主要原因及其主要影响因素 297
5.8.3 消除自激振动的主要措施 299
5.9 提高卧式车床生产率的基本途径 301
5.9.1 单件工时的组成 301
5.9.2 缩短机动时间提高生产率 302
5.9.3 缩短辅助时间提高生产率 304
5.9.4 采用先进刀具、创新工艺技术与数控机床提高生产率 309
5.10 数控机床的简介及简易数控车床的改装 310
5.10.1 数控机床的概述 310
5.10.2 数控机床的分类 312
5.10.3 数控机床的优点 313
5.10.4 数控机床的工作原理 313
5.10.5 简易数控车床技术改装的主要环节与具体问题 320
第6章 车削加工的经济精度和车削步骤 322
6.1 机械加工的精度及其基本概念 322
6.1.1 加工的尺寸精度 322
6.1.2 加工的形状精度 322
6.2.2 加工误差对加工精度的影响 323
6.2.1 产生加工误差的主要根源 323
6.2 产生加工误差的根源及其对加工精度的影响 323
6.1.3 加工的位置精度 323
6.2.3 机床调整误差或试切对刀误差对加工尺寸精度的影响 327
6.3 提高车削加工尺寸精度的方法及限制加工精度的主要因素 327
6.3.1 车削加工提高尺寸精度的方法 327
6.3.2 机床调整误差或试切对刀误差对加工尺寸精度的影响 328
6.3.3 机床、夹具、刀具的制造误差与磨损对加工形状精度的影响 328
6.3.4 工件的安装误差对加工位置精度的影响 329
6.3.5 工艺系统的弹性变形对零件加工形状精度的影响 329
6.4 影响车削加工表面粗糙度的因素 330
6.4.1 影响表面粗糙度的主要因素 330
6.4.2 降低表面粗糙度的主要原因 331
6.4.3 提高表面粗糙度的有效方法 331
6.5 提高车削加工精度的基本途径 333
6.5.5 环境方面的基本途径 334
6.5.4 工艺方面的基本途径 334
6.6 在车床上加工的经济精度 334
6.5.2 刀具方面的基本途径 334
6.5.3 毛坯方面的基本途径 334
6.5.1 机床方面的基本途径 334
6.6.1 在车床上加工的尺寸经济精度 335
6.6.2 在车床上加工的形状经济精度 336
6.6.3 在车床上加工的位置经济精度 337
6.6.4 在车床上加工普通与梯形螺纹达到的加工精度 338
6.6.5 在车床上加工达到的表面粗糙度范围 339
6.7 生产过程及工艺过程 341
6.7.1 生产过程与工厂的生产过程 341
6.7.2 机械加工工艺过程 341
6.7.3 工艺过程对生产的指导、促进、推动作用 341
6.7.4 工艺过程的组成与工艺规程的编制 342
6.8.1 生产类型的划分 343
6.8 生产类型的划分及工序集中与分散的简介 343
6.8.2 工序集中与工序分散原则 345
6.9 车削步骤正确选择的重要性及其一般原则 346
6.9.1 车削步骤正确选择的重要性 346
6.9.2 车削步骤正确选择的一般原则 346
6.10 车削步骤的选择及其实例 348
6.10.1 定位心轴的车削步骤选择 348
6.10.2 丝杠的车削步骤选择 348
6.10.3 齿轮轴的车削步骤选择 349
6.10.4 法兰盘的车削步骤选择 350
6.10.5 尾座套筒的车削步骤选择 350
6.10.6 车床主轴衬套的车削步骤选择 351
7.1.3 基准的定义与其分类 353
7.1.2 工件安装的概念 353
7.1.1 机械工程图样第1角和第3角画法的简介 353
7.1 工件的定位与夹紧及其基准的定义和分类 353
第7章 工件装夹的定位原理及车床夹具与其设计程序 353
7.2 工件定位基准的选择 354
7.2.1 定位粗基准的选择 354
7.2.2 定位精基准的选择 355
7.3 工件的定位原理及工件的不完全定位、完全定位与过定位 356
7.3.1 工件的六点定则 356
7.3.2 工件的不完全定位、完全定位与过定位 357
7.3.3 车床上常用安装方式的支承点与消除自由度数目的分析 357
7.4 工件在夹具上加工误差的分析及尺寸链的换算 358
7.4.1 工件在夹具上的定位误差 358
7.4.2 工艺尺寸链的换算 359
7.5.1 工件以平面定位与其定位元件 361
7.5 工件定位基准面的形状及其定位元件 361
7.4.3 在夹具上达到工件加工精度的条件 361
7.5.2 工件以外圆柱面定位与其定位元件 362
7.5.3 工件以圆柱孔定位与其定位元件 363
7.5.4 工件以其他形状表面定位与其定位元件 364
7.6 夹紧工件的注意事项及防止以摩擦力夹紧方式产生的变形 365
7.6.1 夹紧工件的注意事项 365
7.6.2 防止以摩擦力方式夹紧工件产生变形的主要方法 366
7.7 夹具的用途、分类及其组成 367
7.7.1 夹具的用途 367
7.7.2 夹具的分类 368
7.7.3 夹具的组成 369
7.8 车床上常用的特殊顶尖及弹簧拉力心轴与弹簧夹头 369
7.8.1 常用特殊顶尖 369
7.8.3 弹簧夹头 370
7.8.2 弹簧拉力心轴 370
7.9 组合夹具的简介及车床用组合夹具的组装 371
7.9.1 组合夹具的简介 371
7.9.2 组合夹具元件的种类 371
7.9.3 车床用组合夹具的组装 372
7.9.4 在组合夹具上达到的加工位置精度 373
7.10 车床夹具的设计原则及设计程序 373
7.10.1 车床夹具的设计原则 373
7.10.2 车床夹具的设计程序 374
第8章 切削用量、切削液及有屑与无屑加工的余量 376
8.1 合理的切削用量选择目的及提高切削用量的途径 376
8.1.1 合理切削用量选择目的与其应满足的基本要求 376
8.1.2 提高切削用量的主要途径 376
8.2.2 切削层横截面要素(物理切削要素) 377
8.2.1 切削用量要素(工艺切削要素) 377
8.2 车削加工的工艺切削要素及物理切削要素 377
8.3 限制切削用量的主要因素及其所限制的程度 378
8.3.1 刀具耐用度对切削用量的限制程度 378
8.3.2 表面粗糙度对切削用量的限制 378
8.3.3 工艺系统刚度对切削用量的限制 378
8.3.4 机床切削功率和走刀机构强度对切削用量的限制 378
8.4 选择合理切削用量的依据及其原则 379
8.4.1 选择合理切削用量的主要依据 379
8.4.2 选择合理切削用量的一般原则 379
8.5 选择合理切削用量的次序、步骤及其方法 380
8.5.1 选择合理切削用量的次序 380
8.5.2 选择合理切削用量的步骤 381
8.5.3 选择合理切削用量的方法 385
8.6 切削液的作用、分类及其添加剂 387
8.6.1 切削液的作用 387
8.6.2 切削液的分类 388
8.6.3 切削液中的添加剂 389
8.7 切削液的组成成分及其配方 391
8.7.1 切削液的组成成分 391
8.7.2 切削液的主要配方 392
8.7.3 切削液对切削过程的主要影响 393
8.8 切削液的具体选用及其加注方式 394
8.8.1 切削液的具体选用 394
8.8.2 切削液的加注方式 395
8.9 在车床上有屑切削加工的加工余量 395
8.9.1 半精车和精车外圆柱面的加工余量 395
8.9.2 半精车外圆柱面的磨削加工余量 396
8.9.3 钻、扩、半精镗、半精铰为精镗、精铰的加工余量 396
8.9.4 半精镗圆柱孔的磨削加工余量 397
8.10 在车床上精加工圆柱面及其无屑加工的加工余量 398
8.10.1 精镗圆柱孔用钢球或心轴挤扩无屑加工的加工余量 398
8.9.6 精车后的研磨与抛光用加工余量 398
8.9.5 精车端面的加工余量与半精车端面的磨削加工余量 398
8.10.2 精加工圆柱面用滚压工具滚压无屑加工的加工余量 399
8.10.3 精车外圆柱面用离心力钢珠冲击无屑加工的加工余量 400
第9章 螺纹的切削 401
9.1 螺纹的种类、特点与应用及其代号的标记示例 401
9.1.1 螺纹的种类、特点与应用 401
9.1.2 螺纹的代号标记示例 402
9.2 普通螺纹 403
9.2.1 普通螺纹的基本牙型 403
9.2.2 普通螺纹的公称直径与螺距系列 403
9.2.3 普通螺纹的偏差表 405
9.2.4 普通螺纹收尾、肩距、退刀槽和倒角 424
9.3.2 梯形螺纹的公称直径与螺距系列 426
9.3 梯形螺纹 426
9.3.1 梯形螺纹的基本牙型与基本牙型尺寸 426
9.3.3 梯形螺纹的基本尺寸 427
9.3.4 梯形螺纹的公差 428
9.3.5 梯形螺纹的极限尺寸 432
9.4 管螺纹(圆柱与圆锥管螺纹)米制锥螺纹与60°圆锥螺纹 448
9.4.1 用螺纹密封的管螺纹的基本牙型与基本尺寸 448
9.4.2 非螺纹密封的管螺纹 449
9.4.3 米制锥螺纹基本牙型与基本尺寸 452
9.4.4 60°圆锥螺纹的基本牙型与基本尺寸 455
9.5 吋制螺纹及非标准方形螺纹 455
9.5.1 55°吋制螺纹的基本牙型与基本尺寸 455
9.5.2 29°吋制梯形或蜗杆螺纹的基本牙型与基本尺寸 456
9.6.1 梯形螺纹刀头的刀尖宽度计算 457
9.6 螺纹车刀的刀头尺寸及切削角度的计算 457
9.5.3 米制和吋制方形螺纹的牙型与尺寸 457
9.6.2 蜗杆螺纹刀头的刀尖宽度计算 459
9.6.3 螺纹升角γ对螺纹刀头左、右刃横向工作后角的计算 461
9.6.4 螺纹车刀的前角γ0≠0时对螺纹牙型角的影响 462
9.6.5 车削阿基米德蜗杆螺纹对螺纹车刀装夹的要求 464
9.7 车削螺纹挂轮的计算及挂轮搭配规则 465
9.7.1 挂轮计算公式的推导与挂轮搭配规则在单式和复式挂轮系的应用 465
9.7.2 无进给箱车床的挂轮计算 468
9.7.3 有进给箱车床的新挂轮计算 469
9.8 车削螺纹出现乱扣的原因及车削多线螺纹分线的方法 471
9.8.1 车削螺纹出现乱扣的原因 471
9.8.2 乱扣数的计算 471
9.8.3 防止乱扣的方法 472
9.8.4 车削多线螺纹分线的方法 472
9.8.5 攻螺纹前钻底孔所用钻头直径☆的选择 474
9.9 旋风切削螺纹及其工作原理 476
9.9.1 旋风切削装置的简介 476
9.9.2 旋风切削螺纹的原理、特点与切削方式 477
9.9.3 旋风切削螺纹所用刀具材料、刀头切削角度与切削用量 478
9.10 螺纹的测量及其主要方法 480
9.10.1 用螺纹千分尺测量普通螺纹的中径 480
9.10.2 用齿厚游标卡尺测量梯形与蜗杆螺纹的齿厚 480
9.10.3 用三针测量法测量螺纹的中径 481
第10章 工件加工之中的计算、找正装夹及特殊加工 486
10.1 直齿圆柱齿轮坯及斜齿圆柱齿轮坯车削加工的有关计算 486
10.1.1 直齿圆柱齿轮坯车削加工的有关计算 486
10.1.2 斜齿圆柱齿轮坯车削加工的有关计算 486
10.2.1 模数直齿圆锥齿轮坯车削加工的有关计算 487
10.2 模数直齿圆锥齿轮坯及径节直齿圆锥齿轮坯车削加工的有关计算 487
10.2.2 径节直齿圆锥齿轮坯的车削加工的有关计算 488
10.3 普通圆柱蜗杆及蜗轮坏车削加工的有关计算 489
10.3.1 模数普通圆柱蜗杆与蜗轮坏车削加工的有关计算 489
10.3.2 径节普通圆柱蜗杆与蜗轮坯车削加工的有关计算 491
10.4 圆锥面的车削加工及其计算 492
10.4.1 圆锥基本参数的名称与符号 492
10.4.2 圆锥基本参数的计算公式与斜角近似计算公式的推导 493
10.4.3 车削加工圆锥面的方法 493
10.4.4 圆锥角度的检测方法 499
10.4.5 车削加工圆锥面对背吃刀量和留磨量的控制 500
10.4.6 车削加工圆锥面出现双曲线误差的分析 502
10.5 奇型工件的划线及其找正装夹 503
10.5.1 奇型工件安装常用的附件 503
10.5.2 在花盘上安装奇型工件 504
10.5.3 在花盘与角铁上用划线找正安装奇型工件 505
10.6 偏心工件及曲轴的车削加工 506
10.6.1 偏心轴的划线 506
10.5.4 减小花盘与角铁定位误差的有效方法 506
10.6.2 用床头与尾座上两顶尖支承车削加工偏心轴 507
10.6.3 用四爪单动卡盘装夹车削加工偏心件 507
10.6.4 用三爪自定心卡盘装夹车削加工偏心件 507
10.6.5 用四爪单动卡盘和三爪自定心双重卡盘装夹车削加工偏心件 509
10.6.6 双拐与多拐曲轴的车削加工 509
10.7 细长轴的车削加工及其装夹方式 510
10.7.1 用创新尾座拉力卡头加工细长轴 510
10.7.2 用创新尾座拉力卡头与合理切削角度车刀车削加工细长轴 511
10.7.3 用创新尾座拉力卡头与三支承块跟刀架车削加工细长轴 511
10.8 深孔的加工及套料加工 512
10.8.1 深孔钻的结构形式与几何形状 512
10.7.4 用创新尾座拉力卡头、三支承块跟刀架与改变走刀方向车削加工细长轴 512
10.8.2 枪孔钻的结构形式与几何形状 514
10.8.3 双刃错齿内排屑深孔钻主要参数的确定 515
10.8.4 深孔钻削加工的切削用量与其注意事项 517
10.8.5 深孔的套料加工 517
10.9 精密球面及特种形面的车削加工 519
10.9.1 用球面装置车削加工精密球面 519
10.9.2 用靠模法车削加工凸轮 520
10.9.3 用样件作靠模车削加工特种形面的环状槽 521
10.10 用专用装置车削加工多边形体及其平面度误差分析 522
10.10.1 多边形体的车削加工原理 522
10.10.2 外切法车削加工多边形体专用装置的简介 523
10.10.3 车削加工多边形体的具体操作要求 523
10.10.4 车削加工多边形体平面度误差的分析 524
参考文献 526
- 《钒产业技术及应用》高峰,彭清静,华骏主编 2019
- 《现代水泥技术发展与应用论文集》天津水泥工业设计研究院有限公司编 2019
- 《异质性条件下技术创新最优市场结构研究 以中国高技术产业为例》千慧雄 2019
- 《Prometheus技术秘笈》百里燊 2019
- 《中央财政支持提升专业服务产业发展能力项目水利工程专业课程建设成果 设施农业工程技术》赵英编 2018
- 《药剂学实验操作技术》刘芳,高森主编 2019
- 《林下养蜂技术》罗文华,黄勇,刘佳霖主编 2017
- 《脱硝运行技术1000问》朱国宇编 2019
- 《催化剂制备过程技术》韩勇责任编辑;(中国)张继光 2019
- 《信息系统安全技术管理策略 信息安全经济学视角》赵柳榕著 2020
- 《中国当代乡土小说文库 本乡本土》(中国)刘玉堂 2019
- 《异质性条件下技术创新最优市场结构研究 以中国高技术产业为例》千慧雄 2019
- 《中国铁路人 第三届现实主义网络文学征文大赛一等奖》恒传录著 2019
- 《莼江曲谱 2 中国昆曲博物馆藏稀见昆剧手抄曲谱汇编之一》郭腊梅主编;孙伊婷副主编;孙文明,孙伊婷编委;中国昆曲博物馆编 2018
- 《中国制造业绿色供应链发展研究报告》中国电子信息产业发展研究院 2019
- 《中国陈设艺术史》赵囡囡著 2019
- 《指向核心素养 北京十一学校名师教学设计 英语 七年级 上 配人教版》周志英总主编 2019
- 《《走近科学》精选丛书 中国UFO悬案调查》郭之文 2019
- 《清至民国中国西北戏剧经典唱段汇辑 第8卷》孔令纪 2018
- 《北京生态环境保护》《北京环境保护丛书》编委会编著 2018