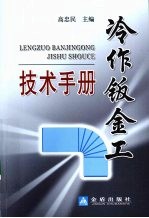
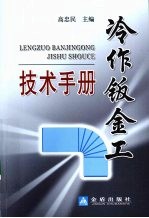
冷作钣金工技术手册PDF电子书下载
- 电子书积分:18 积分如何计算积分?
- 作 者:高忠民编著
- 出 版 社:北京:金盾出版社
- 出版年份:2009
- ISBN:9787508258249
- 页数:628 页
第1部分 冷作钣金工基本知识篇 1
1 钣金工识图与绘图基本知识 1
1.1 正投影法和三视图 1
1.1.1 正投影的概念 1
1.1.2 直线段和平面图形正投影的特性 1
1.1.2.1 真实性 1
1.1.2.2 积聚性 2
1.1.2.3 收缩性 2
1.1.3 三视图的形成和名称 2
1.1.4 三视图的投影规律 3
1.1.4.1 位置关系 3
1.1.4.2 尺寸关系 3
1.1.4.3 方位关系 5
1.2 点、直线、平面的投影 5
1.2.1 点的三面投影 5
1.2.2 各种位置直线的投影 6
1.2.2.1 直线的三面投影 6
1.2.2.2 各种空间位置直线的投影 7
1.2.3 求一般位置直线段的实长和与投影面的夹角 8
1.2.3.1 用旋转法求一般位置直线段的实长 8
1.2.3.2 用更换投影面法求一般位置直线段的实长 12
1.2.3.3 用直角三角形法求一般位置直线段的实长 13
1.2.4 各种位置平面的投影 14
1.2.4.1 投影面的平行面 14
1.2.4.2 投影面的垂直面 14
1.2.4.3 一般位置平面 19
1.3 基本体的投影 19
1.3.1 棱柱体的投影 19
1.3.2 棱柱体表面上点的投影 20
1.3.3 棱锥体的投影 20
1.3.4 棱锥体表面上点的投影 21
1.3.5 圆柱体的投影 22
1.3.6 圆柱体表面上点的投影 23
1.3.7 圆锥体和圆锥台的投影 23
1.3.7.1 圆锥体的投影 23
1.3.7.2 圆锥台的投影 24
1.3.8 圆锥体和圆锥台表面上点的投影 24
1.3.8.1 辅助素线法 25
1.3.8.2 辅助圆法 26
1.3.9 圆球的投影 26
1.3.10 圆球面上点的投影 27
1.3.11 圆环的投影 27
1.3.12 圆环面上点的投影 28
1.3.13 基本体的尺寸标注 28
1.3.13.1 平面体尺寸标注 28
1.3.13.2 回转体尺寸标注 29
1.4 常用几何图形的画法 30
1.4.1 等分直线段 30
1.4.1.1 二等分直线 30
1.4.1.2 分直线为任意等份 31
1.4.2 等分圆周及作正多边形 32
1.4.2.1 用圆规作圆周的三、六、十二等份及作正多边形 32
1.4.2.2 圆周的五等份及作正五边形 33
1.4.2.3 任意等分圆周 33
1.4.3 圆弧连接 34
1.4.3.1 两直线间的圆弧连接 34
1.4.3.2 直线与圆弧间的圆弧连接 34
1.4.3.3 两圆弧间的圆弧连接 34
1.4.4 椭圆的画法 34
1.4.4.1 四心近似画法 34
1.4.4.2 同心圆法 34
1.4.5 斜度与锥度 39
1.4.5.1 斜度 39
1.4.5.2 锥度 40
2 公差与配合基本知识 41
2.1 公差与配合 41
2.1.1 公差与配合的基本概念 41
2.1.1.1 公差与配合的基本术语及定义 41
2.1.1.2 配合 43
2.1.2 标准公差与基本偏差 45
2.1.2.1 标准公差(IT) 45
2.1.2.2 基本偏差 46
2.1.3 基孔制与基轴制配合 48
2.1.3.1 基孔制配合 48
2.1.3.2 基轴制配合 49
2.1.3.3 配合制度的选择 51
2.1.4 极限与配合的标注与读识 51
2.1.4.1 在装配图上的标注 51
2.1.4.2 在零件图上的标注 56
2.2 形状和位置公差 57
2.2.1 形状和位置公差的特征项目及符号 57
2.2.1.1 形状和位置公差的基本术语及定义 57
2.2.1.2 形状和位置公差特征项目的规定符号 57
2.2.2 形状和位置公差的标注与识读 58
2.2.2.1 公差框格及其内容 58
2.2.2.2 被测要素的标注 59
2.2.2.3 基准要素的标注 61
2.2.2.4 形位公差标注示例 62
2.3 表面粗糙度 63
2.3.1 表面粗糙度的概念 63
2.3.2 表面粗糙度的标注与识读 64
2.3.2.1 表面粗糙度的图形符号 64
2.3.2.2 表面粗糙度完整图形符号的组成 64
2.3.2.3 表面粗糙度在图样上的标注 67
3 常用钣金金属材料及热处理基本知识 73
3.1 常用钣金金属材料 73
3.1.1 钢的分类和牌号 73
3.1.1.1 按化学成分分类 73
3.1.1.2 按用途分类 73
3.1.1.3 按质量优劣分类 74
3.1.1.4 钢的牌号 74
3.1.2 钢的技术性能 77
3.1.2.1 钢的物理性能指标 77
3.1.2.2 钢的化学性能指标 78
3.1.2.3 钢的力学性能指标 78
3.1.2.4 钢的工艺性能 82
3.1.3 常用钣金钢材 82
3.1.3.1 低碳钢薄板 82
3.1.3.2 低合金高强度结构钢 84
3.1.3.3 不锈钢和耐热钢 84
3.1.4 常用有色金属材料 86
3.1.4.1 铝及铝合金 87
3.1.4.2 铜及铜合金 87
3.2 钢的热处理基本知识 91
3.2.1 钢的常见组织 91
3.2.1.1 钢的晶体结构 91
3.2.1.2 钢的常见组织 92
3.2.2 钢的铁碳平衡状态图和钢的热处理 94
3.2.2.1 铁-碳平衡状态图 94
3.2.2.2 钢的热处理 95
4 简单构件的展开图 97
4.1 展开图的基本作法 97
4.1.1 放样图和断面图 97
4.1.1.1 放样图 97
4.1.1.2 断面图 98
4.1.2 平行线展开法 102
4.1.2.1 棱柱体表面的展开图 102
4.1.2.2 圆柱体表面的展开图 104
4.1.3 放射线展开法 108
4.1.3.1 棱锥体表面的展开图 108
4.1.3.2 圆锥体表面的展开图 111
4.1.3.3 斜圆锥体表面的展开图 114
4.1.4 三角形展开法 116
4.1.5 其他展开法 121
4.1.5.1 用辅助圆法展开斜截圆管构件 121
4.1.5.2 用系数法展开斜截圆管构件 122
4.1.6 各种展开法的比较和选择 124
4.2 不可展曲面的近似展开方法 126
4.2.1 经线分割法 126
4.2.2 纬线分割法 128
4.2.3 用三角形展开法近似展开不可展曲面 131
5 相交构件的结合线和求结合线的方法 134
5.1 结合线的概念和分类 134
5.1.1 结合线的概念 134
5.1.2 结合线的分类 135
5.1.2.1 必然结合线 135
5.1.2.2 人为结合线 136
5.2 直线型结合线的确定 137
5.2.1 相交旋转体轴线重合时的结合线 138
5.2.2 相交旋转体轴线相交时的结合线 139
5.2.3 相交旋转体有公切面且轴线相交时的结合线 146
5.2.4 锥形、柱形体相交其底面同时重合于同一圆周时的结合线 148
5.2.5 相交旋转体对称于某一平面且在该对称平面上相交的结合线 151
5.3 求作结合线的方法 153
5.3.1 用素线法求结合线 154
5.3.1.1 用素线法求结合线的原理 154
5.3.1.2 用素线法求结合线的实例 155
5.3.2 用纬线法求结合线 160
5.3.2.1 用纬线法求结合线的原理 160
5.3.2.2 用纬线法求结合线的实例 161
5.3.3 用辅助平面法求结合线 165
5.3.3.1 用辅助平面法求结合线的原理 165
5.3.3.2 用辅助平面法求结合线的实例 168
5.3.4 用辅助球面法求结合线 175
5.3.4.1 用辅助球面法求结合线的原理 175
5.3.4.2 用辅助球面法求结合线的实例 177
5.4 人为结合线 181
5.4.1 人为结合线的概念 181
5.4.2 人为结合线的实例 181
第2部分 冷作钣金工技能篇 184
6 钣金下料实例 184
6.1 板厚处理和加工余量 184
6.1.1 板厚处理 184
6.1.1.1 根据构件形状的不同进行板厚处理 184
6.1.1.2 根据构件接口处的情况不同进行板厚处理 186
6.1.1.3 板厚处理的基本原则 190
6.1.2 加工余量 190
6.1.2.1 焊接时的加工余量 191
6.1.2.2 铆接时的加工余量 192
6.1.2.3 咬口时的加工余量 193
6.1.2.4 对加工余量两点补充说明 195
6.2 直圆管和直圆管相交构件 195
6.2.1 任意角度的两节等径圆管弯头 195
6.2.1.1 不铲坡口的一定板厚、任意角度的二节等径圆管弯头 195
6.2.1.2 板厚处理采用双面X形坡口、任意角度的二节等径圆管弯头 196
6.2.2 等径四节90°圆管弯头 197
6.2.3 等径圆管斜T形三通 198
6.2.4 不等径圆管斜T形三通 201
6.2.5 支管中心轴线与主管中心轴线不相交时不等径圆管斜T形三通 203
6.2.6 等径两节圆管弯头外侧斜接一小圆管的三通构件 204
6.3 圆管和正圆锥管或斜圆锥管相交构件 206
6.3.1 正圆锥管连接大小直径圆管的裤形三通构件 206
6.3.2 圆管和正圆锥管组成的两节弯头构件 208
6.3.3 主管为直圆管、支管为正圆锥管的构件 210
6.3.4 直圆管斜插正圆锥管的构件 212
6.3.5 主管为直圆管、支管为斜圆锥管的构件 213
6.4 圆锥管相交构件 215
6.4.1 圆锥管任意角度两节弯头 215
6.4.2 支管和主管均为正圆锥管的三通构件 217
6.4.3 中心线不相交的正圆锥管相交构件 219
6.4.4 斜圆锥管和斜圆锥管相交的三通构件 221
6.4.5 斜圆锥管裤形三通构件 224
6.5 多面体相交构件 225
6.5.1 矩形管三节90°弯头 225
6.5.2 支管斜接主管的矩形管三通构件 226
6.5.3 端口扭转90°的方管两节弯头 227
6.5.4 对称的斜四棱锥构成的三通构件 229
6.5.5 由两个正四棱锥台构成的三通构件 230
6.5.6 正四棱锥接方管的三通构件 233
6.6 直圆管或圆锥管与多面体相交构件 235
6.6.1 由直圆管和棱锥构成的扩散两节任意角度弯头 235
6.6.2 方管与圆管相交的任意角度两节弯头 236
6.6.3 圆管平行直插正四棱锥构件 238
6.6.4 正圆锥斜接方管的三通构件 239
6.6.5 斜圆锥斜接方管的三通构件 240
6.7 球面与其他形体相交的构件 242
6.7.1 矩形管平接球面的构件 242
6.7.2 圆管斜插球面的构件 242
7 裁料 245
7.1 剪裁 245
7.1.1 手工剪裁 245
7.1.1.1 手工剪裁工具 245
7.1.1.2 手工剪切方法 247
7.1.2 剪裁设备 250
7.1.2.1 剪板机 251
7.1.2.2 滚剪机 256
7.1.2.3 振动剪板机 259
7.1.3 剪裁过程及其受力分析 261
7.1.3.1 剪切过程 261
7.1.3.2 剪裁的受力分析 262
7.1.3.3 剪切力的计算 262
7.1.4 剪刃间隙及角度的确定 263
7.1.5 剪裁质量分析 264
7.1.5.1 拱曲和扭曲变形 264
7.1.5.2 过剪和超差 264
7.2 冲裁 265
7.2.1 冲裁设备 266
7.2.1.1 典型冲床的结构和工作原理 266
7.2.1.2 冲床的主要技术参数 267
7.2.1.3 冲床的使用和维护保养 268
7.2.2 冲裁模 269
7.2.2.1 单工序冲裁模的基本结构 269
7.2.2.2 冲裁模的安装和调整 270
7.2.3 冲裁过程 273
7.2.4 冲裁模刃口间隙的确定 275
7.2.5 冲裁模刃口尺寸的计算 279
7.2.5.1 确定冲裁模刃口尺寸的原则 279
7.2.5.2 冲裁模刃口尺寸的计算方法 280
7.2.6 冲床吨位的选择 283
7.2.6.1 冲裁力、卸料力、推件力和顶件力的计算 284
7.2.6.2 冲床吨位的选择 287
7.2.7 影响冲裁质量的主要因素 288
7.2.7.1 冲裁件尺寸精度的影响因素 288
7.2.7.2 冲裁件断面质量的影响因素 288
7.2.7.3 材质与板厚对冲裁件的影响 289
7.3 割裁 290
7.3.1 气割的基本原理和特点 290
7.3.1.1 被切割金属的燃点低于其熔点 290
7.3.1.2 金属的熔点应高于其氧化物的熔点 291
7.3.1.3 金属氧化物黏度、燃烧时放出的热量、导热性等应符合要求 291
7.3.2 割炬和割嘴 292
7.3.2.1 割炬 292
7.3.2.2 割嘴 294
7.3.3 气割薄钢板的工艺参数 295
7.3.3.1 割炬型号和切割氧压力 295
7.3.3.2 气割速度 296
7.3.3.3 预热火焰能率 296
7.3.3.4 割嘴与工件间的倾角 297
7.3.3.5 割嘴离工件表面的距离 297
7.3.4 手工气割操作技术 298
7.3.4.1 射吸式割炬的使用 298
7.3.4.2 乙炔气瓶和乙炔减压器的使用 299
7.3.4.3 氧气瓶和氧气减压器的使用 301
7.3.4.4 气割前的准备 303
7.3.4.5 手工气割操作技术 304
7.4 其他裁料方法 307
7.4.1 锯削 307
7.4.1.1 手工锯削 307
7.4.1.2 机械锯削 311
7.4.2 錾切 311
7.4.2.1 錾切工具及用途 311
7.4.2.2 錾刃的几何角度和刃磨 313
7.4.2.3 常用錾削方法 314
7.4.2.4 錾子的热处理 315
7.4.3 砂轮切割 316
7.4.4 等离子弧切割 317
7.4.5 激光切割 318
7.4.6 电火花线切割 319
7.4.7 铣切 320
7.4.8 碳弧气刨 320
7.5 裁料方法的选择 322
7.5.1 根据零件的尺寸和几何形状选择裁料方法 322
7.5.2 根据零件的厚度选择裁料方法 325
7.5.3 根据零件的材质选择裁料方法 325
8 钣金成形工艺 327
8.1 手工成形 327
8.1.1 手工成形的工具、夹具和量具 327
8.1.1.1 手工成形的常用工具 327
8.1.1.2 常用机具 332
8.1.1.3 常用夹具 334
8.1.1.4 常用量具 335
8.1.2 手工弯曲板料 335
8.1.2.1 折边 335
8.1.2.2 弯卷 338
8.1.2.3 凹凸形工件的手工弯压 341
8.1.3 手工弯曲型钢 341
8.1.4 钢管的弯曲工艺 343
8.1.4.1 手工装砂弯管 343
8.1.4.2 使用弯管器具弯管 344
8.1.5 卷边 346
8.1.6 放边与收边 348
8.1.6.1 放边的操作 348
8.1.6.2 收边的操作 349
8.1.7 拔缘 350
8.1.7.1 自由拔缘 350
8.1.7.2 型胎拔缘 352
8.1.8 拱曲 353
8.1.8.1 冷拱曲 353
8.1.8.2 热拱曲 355
8.1.8.3 拱曲零件的下料 355
8.2 大型弯曲件的机械成形 357
8.2.1 滚弯 357
8.2.1.1 滚弯机的主要技术规格、构造原理及使用维护 358
8.2.1.2 滚弯计算 360
8.2.1.3 滚卷过程和滚弯工艺 363
8.2.1.4 滚弯质量分析 369
8.2.2 折边机弯曲 371
8.2.2.1 折边机的作用和主要技术参数 371
8.2.2.2 折边机的构造和工作原理 371
8.2.2.3 折边机的使用规则及维护保养 373
8.2.3 闸压机弯曲 373
8.2.4 水压机弯曲 375
8.3 冲压弯曲 375
8.3.1 冲压弯曲模 375
8.3.1.1 弯曲模的结构 375
8.3.1.2 冲压弯曲模具工作部分尺寸 377
8.3.1.3 冲压弯曲模凸模、凹模材料及热处理硬度 381
8.3.2 对冲压弯曲件的工艺性要求 381
8.3.2.1 表面质量 381
8.3.2.2 弯曲线方向 381
8.3.2.3 最小弯曲半径Rmin 382
8.3.2.4 最小直边高度H 383
8.3.2.5 孔边距离 383
8.3.2.6 止裂孔和止裂槽 383
8.3.2.7 避让斜边 384
8.3.2.8 限制滑移 384
8.3.2.9 连接带和定位工艺孔 384
8.3.2.10 退火 385
8.3.3 冲压弯曲时压力机的选用 385
8.3.3.1 公称压力 385
8.3.3.2 行程长度 386
8.3.3.3 封闭高度和工作台尺寸 386
8.4 其他成形方法 387
8.4.1 拉深成形 387
8.4.1.1 拉深成形的特点 387
8.4.1.2 拉深系数 388
8.4.1.3 拉深件的工艺计算 390
8.4.1.4 拉深模 393
8.4.1.5 拉深力和压边力的计算 395
8.4.1.6 锅炉和压力容器封头的热拉深加工 397
8.4.2 旋压成形 400
8.4.2.1 旋压工艺 401
8.4.2.2 胎模(旋压芯模)与旋压头 402
8.4.2.3 强力旋压 403
8.4.3 翻边切口 403
8.4.3.1 圆孔翻边 404
8.4.3.2 非圆孔翻边 406
8.4.4 胀形 409
8.4.4.1 胀形系数 409
8.4.4.2 胀形的方法 410
8.4.4.3 胀形力的计算 412
8.4.5 落压成形 412
8.4.6 橡胶成形 413
8.4.7 拉形成形 413
8.4.8 爆炸成形 414
8.4.9 水火成形 415
9 钣金装配与连接 417
9.1 钣金装配 417
9.1.1 钣金装配的特点 417
9.1.1.1 对手工操作技术要求高 417
9.1.1.2 确定合适的装配调整余量的位置和大小 418
9.1.1.3 必须确定合理的装配连接顺序 418
9.1.1.4 总体装配路线较长、刚性较差,容易产生变形 419
9.1.2 钣金装配的基本条件 419
9.1.3 钣金构件的装配顺序 419
9.1.3.1 确定装配顺序的基本方法 419
9.1.3.2 典型钣金构件的连接装配顺序 419
9.2 钣金构件的焊接 436
9.2.1 焊接的方法及其适用范围 436
9.2.2 焊条电弧焊 438
9.2.2.1 焊条电弧焊设备的使用 438
9.2.2.2 焊条 446
9.2.2.3 焊接接头和焊接坡口 452
9.2.2.4 焊条电弧焊工艺 459
9.2.2.5 焊条电弧焊的基本操作技术 463
9.2.2.6 定位焊缝的焊接 469
9.2.2.7 薄板焊接操作技术 470
9.2.2.8 焊条电弧焊安全操作技术 471
9.2.3 CO2气体保护焊 473
9.2.3.1 CO2气体保护焊工艺 473
9.2.3.2 CO2气体保护焊的基本操作技术 479
9.2.4 氩弧焊焊接薄壁不锈钢板和铝板 483
9.2.4.1 手工钨极氩弧焊 484
9.2.4.2 熔化极氩弧焊 496
9.2.5 各种金属薄板的气焊 507
9.2.5.1 气焊的基本原理和特点 507
9.2.5.2 焊炬 511
9.2.5.3 气焊工艺 511
9.2.5.4 低碳钢薄板的气焊 517
9.2.5.5 铝和铝合金薄板的气焊 520
9.2.5.6 紫铜板的气焊 523
9.2.6 锡焊 523
9.2.6.1 锡焊的特点 523
9.2.6.2 锡焊常用的工具 524
9.2.6.3 焊料和焊剂 524
9.2.6.4 锡焊的操作方法 525
9.2.6.5 挂锡的基本知识及操作方法 528
9.2.6.6 锡焊铝制件 528
9.3 钣金构件的铆接 529
9.3.1 铆钉的种类、规格和铆接工具 529
9.3.1.1 铆钉的种类和规格 529
9.3.1.2 铆接工具 531
9.3.2 铆接的类型和铆接接头的形式 533
9.3.2.1 铆接的类型 533
9.3.2.2 铆接的形式 535
9.3.3 铆接工艺 536
9.3.3.1 铆接的方法 536
9.3.3.2 铆钉直径和铆钉长度的确定 536
9.3.3.3 铆钉的布置 537
9.3.3.4 铆接的方法 538
9.3.3.5 有色金属薄板的铆接方法 542
9.3.3.6 液压铆接 543
9.3.3.7 铆接缺陷及其质量分析 543
9.4 薄板钣金构件的咬接 546
9.4.1 咬接的形式 546
9.4.2 手工咬接 547
9.4.2.1 手工咬接工具 547
9.4.2.2 咬口宽度和咬接加工余量 547
9.4.2.3 手工咬接的操作方法 548
9.5 钣金构件的其他连接方法 553
9.5.1 法兰连接 553
9.5.2 胀接 555
9.5.2.1 胀接的结构形式及其特点 556
9.5.2.2 胀接工艺 557
9.5.3 套接 559
9.5.4 卡箍连接 560
9.6 钣金构件的矫正 561
9.6.1 机械矫正 561
9.6.1.1 钢板变形的机械矫正 561
9.6.1.2 型钢变形的机械矫正 564
9.6.2 手工矫正 566
9.6.2.1 手工矫正的工具 566
9.6.2.2 手工矫正的方法 567
9.6.3 火焰矫正 570
9.6.3.1 点状加热 570
9.6.3.2 线状加热 572
9.6.3.3 三角形加热 574
9.6.3.4 加热操作中的注意事项 576
9.6.4 控制焊接变形的方法 577
9.6.4.1 利用装焊顺序和焊接顺序控制焊接变形 577
9.6.4.2 反变形法 578
9.6.4.3 刚性固定法 578
9.6.4.4 散热法 580
9.6.4.5 锤击焊缝法 580
10 钣金构件的质量检验 581
10.1 钣金构件尺寸、形状和位置的质量检验 581
10.1.1 放样、样板和号料的质量检查 581
10.1.2 切割和剪切的质量检查 583
10.1.2.1 火焰切割的质量指标 583
10.1.2.2 机械剪切的质量指标 586
10.1.3 钣金构件的形位检测 587
10.1.3.1 钢材矫正后的允许偏差 587
10.1.3.2 板材冷弯的允许偏差 588
10.1.3.3 钢板卷圆弯曲时的允许偏差值 589
10.1.3.4 管子弯曲的允许偏差 591
10.1.3.5 焊接件的形位检测 593
10.1.3.6 构件预拼装的允许偏差和螺栓联接多层叠板的检验 596
10.2 钣金构件焊缝的质量检验 597
10.2.1 焊接过程的检验 597
10.2.1.1 原材料的检验 598
10.2.1.2 焊接设备的检查 598
10.2.1.3 装配质量的检查 598
10.2.1.4 焊接工艺和焊接规范的检查 598
10.2.1.5 焊接过程中的质量控制 599
10.2.2 常见的焊接缺陷 599
10.2.2.1 焊接缺陷的分类 599
10.2.2.2 焊接缺陷的产生原因、危害和防止措施 600
10.2.3 焊接质量检验 613
10.2.3.1 非破坏性检验 614
10.2.3.2 破坏性检验 626
- 《钒产业技术及应用》高峰,彭清静,华骏主编 2019
- 《现代水泥技术发展与应用论文集》天津水泥工业设计研究院有限公司编 2019
- 《异质性条件下技术创新最优市场结构研究 以中国高技术产业为例》千慧雄 2019
- 《Prometheus技术秘笈》百里燊 2019
- 《中央财政支持提升专业服务产业发展能力项目水利工程专业课程建设成果 设施农业工程技术》赵英编 2018
- 《药剂学实验操作技术》刘芳,高森主编 2019
- 《林下养蜂技术》罗文华,黄勇,刘佳霖主编 2017
- 《脱硝运行技术1000问》朱国宇编 2019
- 《催化剂制备过程技术》韩勇责任编辑;(中国)张继光 2019
- 《信息系统安全技术管理策略 信息安全经济学视角》赵柳榕著 2020
- 《市政工程基础》杨岚编著 2009
- 《家畜百宝 猪、牛、羊、鸡的综合利用》山西省商业厅组织技术处编著 1959
- 《《道德经》200句》崇贤书院编著 2018
- 《高级英语阅读与听说教程》刘秀梅编著 2019
- 《计算机网络与通信基础》谢雨飞,田启川编著 2019
- 《看图自学吉他弹唱教程》陈飞编著 2019
- 《法语词汇认知联想记忆法》刘莲编著 2020
- 《培智学校义务教育实验教科书教师教学用书 生活适应 二年级 上》人民教育出版社,课程教材研究所,特殊教育课程教材研究中心编著 2019
- 《国家社科基金项目申报规范 技巧与案例 第3版 2020》文传浩,夏宇编著 2019
- 《流体力学》张扬军,彭杰,诸葛伟林编著 2019
- 《指向核心素养 北京十一学校名师教学设计 英语 七年级 上 配人教版》周志英总主编 2019
- 《北京生态环境保护》《北京环境保护丛书》编委会编著 2018
- 《指向核心素养 北京十一学校名师教学设计 英语 九年级 上 配人教版》周志英总主编 2019
- 《高等院校旅游专业系列教材 旅游企业岗位培训系列教材 新编北京导游英语》杨昆,鄢莉,谭明华 2019
- 《中国十大出版家》王震,贺越明著 1991
- 《近代民营出版机构的英语函授教育 以“商务、中华、开明”函授学校为个案 1915年-1946年版》丁伟 2017
- 《指向核心素养 北京十一学校名师教学设计 数学 九年级 上 配人教版》周志英总主编 2019
- 《西单大杂院-北京老舍文学院首届中青年作家高研班学员小说作品集》北京老舍文学院编 2019
- 《指向核心素养 北京十一学校名师教学设计 数学 七年级 上 配人教版》周志英总主编 2019
- 《国之重器出版工程 云化虚拟现实技术与应用》熊华平 2019