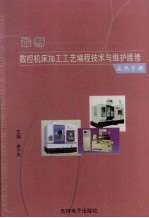
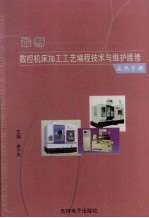
最新数控机床加工工艺编程技术与维护维修实用手册 1PDF电子书下载
- 电子书积分:15 积分如何计算积分?
- 作 者:席文杰主编
- 出 版 社:吉林省电子出版社
- 出版年份:2004
- ISBN:7798902768
- 页数:478 页
第一编 现代数控机床概述 3
第一章 数控机床的基本概念 3
第一节 数控机床的基本情况 3
一、数控机床的定义 3
二、数控机床的加工原理 3
第二节 数控机床的组成及加工特点 5
一、机床数控技术及组成 5
二、数控机床的加工特点 10
第三节 数控机床的分类 11
第四节 数控机床的坐标规定 14
第五节 数控机床的最新发展趋势 16
一、数字控制技术与数控机床的产生与发展 16
二、我国数控机床发展情况 18
三、数控机床的技术发展趋势 21
第二章 加工中心(MC) 32
第一节 概述 32
一、加工中心的定义 32
二、加工中心的发展历程 32
三、加工中心的工作原理 33
四、加工中心的组成及系列型谱 34
五、加工中心的分类 36
第二节 JCS18型立式加工中心 38
一、机床用途 38
二、主要技术性能 39
三、传动系统 41
四、典型部件 42
第三节 加工中心的结构特点 53
一、主传动系统 54
二、加工中心进给系统的机械传动机构 69
三、自动换刀装置 98
第四节 SWORD750立式加工中心主轴系统简介 124
第三章 数控车床 132
第一节 CK7815型数控车床 132
一、CK7815型数控车床的布局及主要部件 132
二、主要技术参数 133
三、机床传动系统 139
四、机床的结构及调整 140
第二节 数控车床的结构特点 149
一、正艺范围与分类 149
二、数控车床的特点与发展 149
三、数控车床的布局形式 150
四、主传动方式 154
五、进给传动系统 157
六、刀架系统 158
第三节 车削中心 163
一、车削中心的工艺范围 164
二、车削中心的C轴 164
三、车削中心的主传动系统 165
四、车削中心自驱动力刀具典型结构 167
第四章 数控机床的主传动系统设计 170
第一节 主传动变速系统的参数 170
一、主传动功率 170
二、主运动的调速范围 171
第二节 主传动系统的设计要求 171
第三节 主传动变速系统的设计 172
一、交、直流无级调速电机的功率扭矩特性 172
二、数控机床分级变速箱的设计 173
第四节 主轴组件设计 183
一、对主轴组件的性能要求 183
二、主轴组件的类型 185
三、主轴 185
四、主轴轴承 187
五、主轴组件的前悬伸和跨距 197
六、主轴组件的技术要求 198
七、主轴组件的动态特性 200
八、主轴组件的平衡 202
九、主轴轴承的润滑与密封 203
十、主轴组件的刚度计算 205
十一、主轴组件径向刚度和转速的参考值 209
十二、超高速主轴组件的设计要点 211
第五节 齿形带传动设计 216
一、多齿形带的强度计算 216
二、齿形带传动的设计计算 217
第五章 进给伺服系统设计 220
第一节 进给伺服系统的设计要求 220
一、对进给伺服系统的基本要求 220
二、进给伺服系统的设计要求 221
第二节 进给伺服系统的组成及其数学模型 222
一、进给伺服系统的组成 222
二、进给伺服系统的数学模型 223
第三节 进给伺服系统的动态响应特性及伺服性能分析 227
一、时间响应特性 227
二、频率响应特性 232
三、稳定性分析 235
四、快速性分析 240
五、伺服精度 246
第四节 系统增益的设计 248
一、三阶系统的增益设计 248
二、五阶系统的系统增益设计 250
三、多坐标系统的系统增益设计 250
第五节 电气驱动部件的设计 252
第六节 机械传动部件的设计 261
一、概述 261
二、谐振频率 272
三、转动惯量 273
四、刚度 275
五、阻尼比 278
六、非线性因素 280
七、工作台导轨 282
八、滚珠丝杠螺母传动装置 283
九、滚珠丝杠支承专用轴承的选用 289
十、同步齿形带传动装置 291
十一、回零减速撞块尺寸的计算 292
第七节 机械传动部件设计举例 293
第六章 床身与导轨 302
第一节 床身结构 302
一、对床身结构的基本要求 302
二、床身的结构 303
三、床身的刚度 305
四、床身的结构设计 306
第二节 贴塑滑动导轨设计 307
一、塑料导轨 307
二、导轨结构 310
三、贴塑导轨设计 312
四、导轨的材料 317
第三节 液体静压导轨设计 318
一、静压导轨的结构 318
二、油腔结构 319
三、导轨间隙和节流形式 321
四、导轨承载能力 323
第四节 滚动导轨设计 328
一、直线滚动导轨副 328
二、滚动导轨块 330
三、滚动导轨设计计算 331
第五节 导轨的润滑与防护 334
一、导轨的油润滑 334
二、导轨的固体润滑 334
三、导轨的防护 334
第六节 导轨的超声频加热淬火 336
一、加热原理 336
二、导轨原始状态的要求 337
三、淬火设备 337
四、工艺参数 338
五、床身导轨超声频加热淬火的优点 338
第七章 数控机床的总体设计 339
第一节 数控机床的结构设计要求 339
一、提高机床的结构刚度 339
二、提高机床的抗振性 345
三、提高低速进给运动的平稳性和运动精度 347
第二节 数控机床的总体布局 350
一、总体布局与工件形状、尺寸和质量的关系 351
二、运动分配与部件的布局 351
三、总体布局与机床结构性能 353
四、自动换刀数控卧式镗铣床(加工中心)的总布局 355
五、机床的使用要求与总布局 357
六、数控机床总布局的其他趋向 357
第八章 数控机床的计算机辅助设计 359
第一节 概述 359
一、数控机床采用计算机辅助设计的意义 359
二、CAD系统的总体描述 359
三、数控机床CAD系统的主要功能 362
四、工程数据管理技术 365
五、CAD系统的工程数据库 369
第二节 数控机床总体方案设计 372
一、机床总体布局的CAD 372
二、机床整机建模与性能分析 377
第三节 主传动系统CAD 385
一、部件装配图CAD 385
二、加工中心和数控机床主轴及主传动系统CAD 389
第四节 服进给系统CAD 395
一、伺服进给系统计算机辅助计算与分析(CASS软件) 395
二、伺服进给系统CAD数据库子系统 399
三、伺服进给系统OD图形子系统 400
四、伺服进给系统设计流程 400
第五节 刀库和机械手CAD 401
一、刀库和机械手CAD的工作模式 401
二、刀库和机械手CAD软件的功能组成 402
三、刀库和机械手CAD的工作流程 404
第六节 机床大件及导轨CAD 404
一、建立大件CAD的工作模式 405
二、建立大件子结构图库 407
三、视图的自动生成 408
四、剖面的自动生成 408
五、提高尺寸标注的效率 408
六、计算分析 409
七、导轨方案设计和性能分析软件 409
第七节 叉架类零件CAD 412
一、叉架类零件以①总框图 412
二、三维几何造型 413
三、二维工作图生成模块 417
第八节 回转体零件CAD 418
一、回转体零件微机智能化CAD 418
二、HZTCAD软件系统总框图 420
三、智能尺寸标注的基本原理 421
四、工作图的编辑和完善 421
五、软件包的辅助功能 422
第九节 数控机床主要零件优化设计分析计算及校核计算 422
一、数控机床主要零件优化分析和校核计算软件(MCECAD) 422
二、多目标优化程序库和主轴静、动态特性计算及优化模块 425
第二编 数控机床加工工艺及设备 431
第一章 数控加工工艺及设备基础 431
第一节 机床数控与数控加工设备概述 431
一、机床中有关数控的概念 431
二、数控机床的组成 432
三、数控机床的分类 434
四、数控机床的基本结构特征和主要辅助装置 436
五、数控机床的规格、性能和可靠性指标 437
六、数控机床的精度项目及检验 439
七、数控机床的主要功能 445
第二节 数控加工原理与数控加工艺概述 448
一、数控加工原理 448
二、数控加工工艺和数控加工工艺过程的概念、主要内容及特点 450
三、数控加工工艺与数控编程的关系 452
第三节 数控机床的坐标系统 452
一、数控机床的坐标系 452
二、机床坐标系与工件坐标系 454
第四节 插补原理及与加工精度和加工效率的关系 457
一、数控加工轨迹控制原理——插补原理 457
二、插补原理、进给速度与加工精度和加工效率的关系 459
第五节 当今国际数控加工技术的发展趋势 460
第二章 数控刀具 463
第一节 数控刀具的种类及特点 463
一、数控刀具的种类 463
二、数控刀具的特点 464
第二节 数控刀具材料 466
一、切削用刀具材料应具备的性能 466
二、各种刀具材料 466
第三节 数控刀具的失效形式及可靠性 471
一、数控刀具的失效形式及对策 471
二、刀具失效在线监测方法 473
三、数控刀具可靠性 473
第四节 数控可转位刀片 474
一、可转位刀片代码 474
二、可转位刀片的断屑槽槽型 475
三、可转位刀片的夹紧方式 475
四、可转位刀片的选择 476
第五节 数控刀具的选择 478
一、选择数控刀具通常应考虑的因素 479
二、数控铣削刀具的选择 479
三、加工中心九具的选择 481
四、数控机床刀柄的选择 487
第六节 工具系统 490
一、工具系统的发展 490
二、车削类工具系统 490
三、镗铣类工具系统 491
四、刀具管理系统 492
第三章 数控车削加工工艺 496
第一节 概述 496
一、数控车床的组成及布局 496
二、数控车床的分类 498
三、数控车削的主要加工对象 498
第二节 数控车削加工工件的装夹及对刀 500
一、数控车削加工工件的装夹 500
二、数控车削加工的对刀 503
第三节 制定数控车削加工工艺要解决的主要问题 512
一、选择并确定进行数控加工的内容 513
二、对零件图进行数控加工工艺分析 515
三、零件图形的数学处理及编程尺寸设定值的确定 518
四、数控车削加工工艺过程的拟定 524
五、数控加工余量、工序尺寸及公差的确定 532
六、切削用量的选择 536
七、首件试加工与现场问题处理 540
第四节 数控车削加工工艺文件 540
第五节 典型数控车削零件的加工工艺分析 542
一、轴类零件数控车削加工工艺 542
二、轴套类零件数控车削加工工艺 543
第六节 难加工材料的数控车削加工 552
一、难加工材料的种类和特点 552
二、难加工材料的数控车削 554
第七节 数控车拉工艺介绍 556
一、车拉工艺原理 556
二、数控车拉工艺在一汽众公司的应用 558
第四章 数控铣削加工工艺 560
第一节 概述 560
一、数控铣床的分类 560
二、数控铣削的主要加工对象 561
三、数控铣削加工工件的安装和对刀、换刀 562
第二节 制定数控铣削加工工艺要解决的主要问题 562
一、选择并确定进行数控铣削加工的内容 562
二、数控铣削加工工艺性分析 563
三、零件图形的数学处理 567
四、与起刀、进刀和退刀有关的工艺问题的处理 569
五、逆铣、顺铣及切削方向、切削方式的确定 572
六、数控铣削加工工艺参数的确定 575
第三节 复杂曲线曲面数控铣削加工的刀具轨迹 583
一、二坐标数控铣削加工刀具轨迹生成 583
二、多坐标数控铣削加工刀具轨迹生成 588
三、数控铣削加工刀具运动轨迹的编辑 602
四、数控铣削加工刀具运动轨迹的干涉检查与修正 605
第四节 复杂表面自动编程工艺处理 607
一、自动编程加工的基本工作原理 607
二、自动编程中机床、刀具、毛坯和工件坐标系的设置 609
三、自动编程中工艺参数设置 611
第五节 汽车覆盖件模具的数控铣削加工 613
一、汽车覆盖件模具数控铣削加工工艺主要内容 613
二、汽车覆盖件模具数控铣削加工需特殊注意的问题 618
第六节 典型数控铣削零件的加工工艺分析 621
一、支架零件的数控铣削加工工艺 621
二、汽车覆盖件模具数控铣削加工工艺介绍 627
第五章 加工中心加工工艺 634
第一节 概述 634
一、加工中心的分类 634
二、加工中心的主要加工对象 635
第二节 加工中心加工工件的安装及对刀、换刀 637
一、加工中心加工工件的安装 637
二、加工中心加工的对刀、换刀 645
第三节 制定加工中心加工工艺要解决的主要问题 657
一、零件的工艺分析 657
二、加工中心的选用 658
三、加工中心加工零件的工艺方案设计 661
四、加工中心加工的工步设计 664
五、加工中心加工进给路线的确定 665
六、加工余量的确定 667
七、工序尺寸及公差的确定 669
八、加工中心加工切削用量的选择 669
第四节 典型加工中心加工零件的工艺分析 673
一、盖板零件加工中心的加工工艺 673
二、支承套零件加工中心的加工工艺 677
三、异形支架零件加工中心的加工工艺 682
第六章 大量生产典型零件数控加工工艺 687
第一节 典型轴类零件数控加工工艺 687
一、典型轴类零件介绍 687
二、工艺分析 687
三、变速器—轴工艺过程卡和工序卡 689
第二节 典型箱体类零件数控加工工艺 704
一、典型箱体类零件介绍 704
二、工艺分析 704
三、变速器后壳体工艺过程卡和工序卡 707
第三编 数控机床操作技术 731
第一章 数控车床的操作 731
第一节 概述 731
第二节 操作面板功能介绍 731
第三节 软菜单键操作 738
一、手动操作 739
二、手脉操作 740
三、程序编辑操作(见图12) 742
四、模拟加工 746
五、设置参数方式 748
六、文件服务 749
七、自动操作 750
八、单段操作 753
九、补偿功能 753
第四节 编程 761
一、数控编程基础 763
二、编程举例(见图15) 773
第二章 数控铣床的操作 774
第一节 KND200—M系统 774
一、KND200数控铣床的结构(见图2) 774
二、KND数控铣床的加工范围 775
三、数控机床的坐标系和运动方向的确定。 775
四、数控铣床控制面板的操作 776
五、数控铣床加工实例 788
第二节 FANUC系统 792
一、代码功能说明 792
二、键盘的说明 794
三、键入缓冲区 796
四、键入缓冲区的内容变更方法 797
五、报警信息 798
六、软键 798
七、软键不足时 798
八、软键的切换方法 799
九、其他操作 800
十、功能选择键 800
十一、子菜单 801
十二、操作选择键 806
十三、CRT画面的消除方法 808
十四、机械操作面板(见图22) 808
第三章 VMC800加工中心的操作 811
第一节 VMC800加工中心的面板 811
第二节 加工指令 816
一、G代码(见表3) 816
二、T代码 816
三、F代码 817
四、辅助功能 817
第三节 加工中心控制器面板 818
一、屏幕部分(见图3) 819
二、主功能画面 820
三、F1机台设定画面 820
四、F2:程序编辑画面(见图3) 822
五、F4:执行加工画面 831
六、F5:警报显示画面(见图32) 833
第四节 新代MVC800系统的加工实例 833
一、原点回归 834
二、功能(JOG,INC—JOG,MPG) 834
三、开启程序(编辑/软驱/RS232) 836
四、刀具设定(G40/G41/G42。G43/G44/G49) 836
五、刀具长度测量(G43/G44/G49)步骤 837
六、设定工作坐标(G54...G59)(见图35) 838
七、手动程序输入(MDl)方法 839
八、自动执行NC程序的操作方法 839
九、图形模拟的操作方法 840
十、新代控制器下检查NC程序的操作方法 840
第四章 SINUMERIK 840D加工中心 841
第一节 操作控制 842
一、操作面板OP031上的键功能 842
二、操作键盘的键功能 842
三、外部机床控制面板上的键功能(见图4) 845
四、图形用户界面(见图4) 848
五、操作区域 848
六、操作方法 850
第二节 加工准备 852
一、开机和回参考点 852
二、输入刀具补偿值 853
三、计算刀具补偿值 856
四、输入/变更零点偏置值 857
五、确定/计算零点偏置值 858
六、编制设定数据 860
第三节 手动操作 861
一、手动/点动—增量方式 861
二、MDA方式 862
三、手动主轴控制 863
四、手动刀库控制 864
第四节 程序管理 865
一、程序菜单页面 865
二、打开/关闭程序 866
三、建立新的工件/零件程序 867
四、编辑/修改程序操作步骤 868
五、复制/粘贴、改名、删除 870
六、运行工件/零件程序 871
七、程序的装载/卸载 872
八、传送数据和程序 872
第五节 自动方式 875
一、选择工件程序 875
二、起动/停止/取消程序 876
三、中断后的重定位 877
四、覆盖存储 878
五、显示程序级 879
六、程序的纠错 879
七、从硬盘中装/卸载程序 880
八、从硬盘执行程序 880
第六节 报警和信息 881
第五章 线切割加工 883
第一节 线切割机床的结构、功能及应用 883
一、DK7725E线切割机床的结构及各部分的功能 883
二、线切割加工的应用范围 884
第二节 线切割加工的程序编制 884
第三节 BKDC控制机的屏幕及菜单 888
一、控制机的屏幕划分 888
二、BKDC控制机的菜单结构 889
三、各项菜单的应用 889
四、线切割编程步骤 894
五、生成加工工件的切割轨迹 894
第四节 线切割加工参数、装夹、调整 897
一、加工参数的选择 897
二、线切割加工的工件装夹 899
三、机床的调整 899
第五节 一个典型的操作实例 900
一、开机到加工结束的具体操作步骤 900
二、加工要求 900
三、加工过程中一些特殊情况的处理 901
第六章 电火花加工操作 902
第一节 概述 902
一、机床结构 902
二、机床的坐标系和运动方向的确定 902
三、系统功能介绍 902
四、加工功能 903
五、加工指标 904
第二节 控制面板的操作 904
一、控制面板的操作(见图6) 905
二、基本操作 905
三、手控盒的操作(见图6) 906
第三节 主功能区的操作 907
一、主功能画面的介绍(见图6) 907
二、功能操作说明 908
第四节 编程 915
一、编程指令表(见表6) 915
二、编程的格式 916
三、编程的输入 916
第四编 数控机床编程技术 921
第一章 数控加工的编程基础 921
第一节 数控编程概述 921
一、数控加工的过程 921
二、数控编程的内容与方法 922
三、数控编程的种类 922
第二节 数控机床与刀具运动 923
一、刀具沿工件的加工轮廓插补 923
二、数控机床的坐标系和运动方向 926
第三节 数控系统与加工功能 928
一、典型数控系统 928
二、数控系统的主要功能 930
第四节 数控加工程序的结构与格式 932
一、程序的结构 932
二、程序段格式 933
第五节 数控系统的常用代码 937
第二章 数控编程中的工艺分析 944
第一节 概述 944
一、数控加工工艺的基本特征 944
二、数控加工工艺分析 944
第二节 数控加工的工艺分析与工艺设计 945
一、数控机床的合理选用 945
二、数控加工零件的工艺性分析 947
三、加工方法的选择与加工方案的确定 949
四、工序与工步的划分 952
五、零件的装卡方法与夹具的选择 954
六、加工路线的确定 954
七、刀具的选择 959
八、切削用量的确定 963
九、对刀点与换刀点的确定 965
第三节 数控加工工艺文件 966
第三章 数控编程中的数学处理 974
第一节 数值计算 974
第二节 基点坐标的计算 975
一、联立方程组法求解基点坐标 976
二、三角函数法求解基点坐标 979
三、三角函数法求解刀位点轨迹的基点坐标 980
第三节 非圆曲线节点坐标的计算 987
一、非圆曲线节点坐标的计算步骤 987
二、常用的计算方法 987
第四节 列表曲线型值点坐标的计算 994
第五节 数控车床使用假想刀尖点时偏置计算 995
第六节 简单立体型面零件的数值计算 996
第四章 数控车削加工编程 999
第一节 数控车削编程概述 999
一、数控车削的编程特点 999
二、车床数控系统的功能与指令代码 1000
三、数控车削编程中的有关问题 1004
第二节 基本功能及其指令的编程 1007
一、尺寸系统 1008
二、刀具功能T、主轴转速功能S和进给功能F 1010
三、常用的辅助功能 1011
第三节 插补指令的编程 1012
一、快速线性移动指令G00 1012
二、带进给率的线性插补指令C01 1014
三、螺纹车削加工指令 1018
四、暂停指令G04 1021
第四节 刀具补偿指令及其编程 1021
一、不具备刀具半径补偿功能时的编程 1022
二、具备刀具半径补偿功能时的刀具半径补偿 1024
第五节 固定循环 1026
一、FANUCOiA系统的固定循环 1026
二、华中数控HNC 21/22T的固定循环 1038
第六节 综合实例 1039
第五章 数控铣削加工编程 1043
第一节 数控铣削编程概述 1043
一、数控铣床的编程特点 1043
二、和控铣削编程中的坐标系 1044
三、典型数控系统的指令代码 1045
第二节 常用指令的编程方法 1053
一、坐标系统与尺寸的编程 1053
二、刀具功能T、主轴转速功能S和进给功能F 1055
三、常用的辅助功能 1055
第三节 运动路径控制指令的编程 1056
一、快速线性移动指令G00 1056
二、带进给率的线性插补指令G01 1056
三、圆弧插补指令G02/G03 1056
四、暂停指令G04 1060
第四节 刀具补偿指令及其编程 1061
一、铣削加工时的刀具路径 1061
二、刀具半径补偿 1062
三、刀具长度补偿 1064
第五节 FANUC固定循环 1066
一、固定循环的动作 1067
二、常用的固定循环 1068
第六节 SIEMENS固定循环功能 1077
一、钻削锪孔加工LCYC82 1078
二、深孔钻削加工LCYC83 1079
三、镗削循环LCYC85 1080
四、槽型铣削循环LCYC75 1081
第七节 子程序及其调用 1086
第八节 铣削编程综合实例 1089
第六章 加工中心编程 1096
第一节 加工中心编程概述 1096
一、加工中心的特点 1096
二、加工中心的主要加工对象 1096
三、加工中心的指令与代码 1098
四、加工中心的主要参数 1099
第二节 加工中心基本指令的编程 1100
一、换刀指令 1100
二、参考点操作指令的编程 1101
三、常用指令的编程 1102
第三节 FANUC数控系统宏指令编程 1103
一、宏变量及常量 1103
二、宏程序调用 1105
三、算术与逻辑运算指令 1105
四、控制类指令 1108
五、用户宏程序应用实例 1111
第四节 SIEMENS系统宏程序应用 1114
第五节 FAGOR高级语言编程简介 1116
一、词汇描述 1116
二、流控制语句 1116
三、子程序语句 1118
第六节 加工中心编程综合实例 1122
第七章 电火花线切割加工编程&(1 140
第一节 电火花线切割加工概述 1140
一、电火花线切割的基本原理 1140
二、电火花线切割的特点电火花线切割具有电火花加工的共性,金属材料 1140
第二节 电火花线切割机床的基本结构 1141
第三节 电火花线切割的工艺与工装 1144
第四节 电火花线切割编程方法 1148
一、3B代码编程 1148
二、4B代码编程 1152
三、ISO代码数控程序编制 1154
第五节 电火花线切割编程综合举例 1162
第八章 自动编程技术 1167
第一节 数控编程软件概述 1167
一、CAD/CAM集成数控编程系统的基本原理 1167
二、CAD/CAM集成数控编程系统的应用 1168
三、常用的CAD/CAM集成数控编程系统简介 1170
第二节 CAD/CAM集成数控编程系统的加工造型 1172
一、CAXA制造工程师XP造型功能 1172
二、CAXA制造工程师XP界面介绍 1173
三、零件的加工造型 1174
一、刀具路径的生成 1176
二、知识库加工 1181
三、刀具路径编辑 1182
四、后置处理与加工代码 1182
第五编 数控机床编程实便 1187
第一章 数控线切割编程实例 1187
例1 五角星的数控线切割加工 1187
例2 凹模的数控线切割加工 1188
例3 样板的数控线切割加工 1190
例4 对称凹模的数控线切割加工 1191
例5 蝶形工件的数控线切割加工 1193
例6 冲压模凹模的慢走丝线切割加工 1198
例7 心形凹模的数控线切割加工 1201
例8 内齿轮的数控线切割加工 1203
例9 “星”字的数控线切割加工 1208
例10 标志图形的数控线切割加工 1211
例11 四棱锥的斜度线切割加工 1214
例12 上圆下方的异形线切割加工 1217
第二章 数控车床编程实例 1220
例13 轴的数控车加工 1220
例14 端盖的数控车加工 1222
例15 手柄的数控车加工 1223
例16 螺纹的数控车加工 1226
例17 异形轴的数控车加工 1227
例18 车床试件的端面加工 1230
例19 车床试件的外圆粗车加工 1235
例20 车床试件的外圆精车加工 1238
例21 车床试件的车螺纹加工 1240
例22 车床试件的数控车加工 1244
第三章 数控铣手工编程实例 1248
例23 凸模的数控铣加工 1248
例24 平板凹槽的数控铣加工 1250
第三节 CAXA制造工程师的数控加工 1176
一、刀具路径的生成 1176
二、知识库加工 1181
三、刀具路径编辑 1182
四、后置处理与加工代码 1182
第五编 数控机床编程实例 921
第一章 数控线切割编程实例 921
例1 五角星的数控线切割加工 921
例2 凹模的数控线切割加工 921
例3 样板的数控线切割加工 922
例4 对称凹模的数控线切割加工 922
例5 蝶形工件的数控线切割加工 923
例6 冲压模凹模的慢走丝线切割加工 923
例7 心形凹模的数控线切割加工 926
例8 内齿轮的数控线切割加工 928
例9 “星”字的数控线切割加工 928
例10 标志图形的数控线切割加工 930
例11 四棱锥的斜度线切割加工 932
例12 上圆下方的异形线切割加工 932
第二章 数控车床编程实例 933
例13 轴的数控车加工 937
例14 端盖的数控车加工 944
例15 手柄的数控车加工 944
例16 螺纹的数控车加工 944
例17 异形轴的数控车加工 944
例18 车床试件的端面加工 945
例19 车床试件的外圆粗车加工 945
例20 车床试件的外圆精车加工 947
例21 车床试件的车螺纹加工 949
例22 车床试件的数控车加工 952
第三章 数控铣手工编程实例 954
例23 凸模的数控铣加工 954
例24 平板凹槽的数控铣加工 959
例25 模板的平面数控铣加工 963
例26 台阶形工件的数控铣加工 965
例27 连杆的数控铣加工 966
例28 8字形密封槽的数控铣加工 974
例29 凸轮外形的数控铣加工 974
例30 钻导柱孔的数控铣加工 975
例31 镗导套孔的数控铣加工 976
例32 钻顶针孔的数控铣加工 979
例33 顶针定位槽的数控铣加工 980
例34 铣台阶孔的数控铣加工 987
例35 螺纹的数控铣加工 987
例36 眼镜形凹模的数控铣加工 987
例37 链轮的数控铣加工 994
第四章 数控铣自动编程实例 995
第一节 MasterCAM编程实例 996
例38 化妆品盒盖型芯粗加工 999
例39 化妆品盒盖型芯侧面精加工 999
例40 化妆品盒盖型芯分型面精加工 999
例41 化妆品盒盖型芯顶面精加工 1000
例42 花形凸模的外形粗加工 1004
例43 花形凸模的外形精加工 1007
例44 花形凸模的花形槽加工 1008
例45 花形凸模的中心通孔加工 1010
例46 花形凸模的孔加工 1011
例47 上壳型芯粗加工 1012
例48 上壳型芯半精加工 1012
例49 上壳型芯浅面半精加工 1014
例50 上壳型芯的曲面交角加工 1018
例51 上壳型芯的精加工 1021
例52 标牌的加工 1021
第二节 Ciamtron编程实例 1022
例53 型芯固定板的粗加工 1024
例54 型芯固定板的精加工 1026
例55 塑料杯凸模的粗加工 1026
例56 塑料杯凸模的精加工 1038
例57 塑料杯凸模的清角加工 1039
例58 盒体凹模的平面加工 1043
例59 盒体凹模的粗加工 1043
例60 盒体凹模的口沿精加工 1043
例61 盒体模的侧壁精加工 1044
例62 盒体凹模的底面精加工 1045
例63 一出四盒体注塑模型腔粗加工 1053
例64 一出四盒体注塑模型腔口沿精加工 1053
例65 一出四盒体注塑模型腔侧壁及底面精加工 1055
例66 鼠标凸模的粗加工 1055
例67 鼠标凸模的半精加工 1056
例68 鼠标凸模的侧面精加工 1056
例69 鼠标凸模的分型面精加工 1056
例70 鼠标凸模的顶面精加工 1056
例71 鼠标凸模的圆角精加工 1060
例72 鼠标凸模的清角加工 1061
例73 鼠标凸模的标记加工 1061
例74 鼠标凸模的顶针孔的引导孔加工 1062
例75 电动工具外壳注塑模电极的粗加工 1064
例76 电动工具外壳注塑模电极的精加工 1066
例77 电动工具外壳注塑模电极的顶面精加工 1067
例78 手机型腔的粗加工 1068
例79 手机凹模的半精加工 1077
例80 手机凹模的分型面精加工 1078
例81 手机凹模的精加工 1079
例82 手机凹模的清角加工 1080
例83 鼠标上盖凹模的粗加工 1081
例84 鼠标上盖凹模的侧面精加工 1086
例85 鼠标上盖凹模的底面精加工 1089
例86 凹轮的平面加工 1096
例87 凸轮的外形精加工 1096
例88 凸轮的连接孔加工 1096
例89 头盔型芯的粗加工 1096
例90 头盔型芯的精加工 1098
例91 头盔型芯的外分型面精加工 1099
例92 头盔型芯的顶部精加工 1100
例93 头盔型芯的分型面精加工 1100
例94 头盔型芯的分型面清角加工 1101
例95 头盔型芯的标记加工 1102
第五章 数控加工中心编程实例 1103
例96 凸轮槽的数控加工中心加工 1103
例97 箱体螺纹孔的数控加工中心加工 1105
例98 支架的数控加工中心加工 1105
例99 花形凸模的数控加工中心加工 1108
例100 凸轮的数控加工中心加工 1111
第六编 数控机床故障诊断及维护维修第一章 数控机床维护及数控系统故障诊断 1114
第一节 数控机床维护 1116
一、点检 1116
二、数控系统日常维护 1116
三、诊断用仪器仪表 1118
四、技术资料 1122
第二节 故障处理 1140
一、检查机床的运行状态 1140
二、检查加工程序及操作情况 1140
三、检查故障的出现率和重要性 1140
四、检查系统的输入电压 1141
五、检查环境状况 1144
六、外部因素 1148
七、检查运行情况 1148
八、检查机床状况 1152
九、检查接口情况 1154
第三节 数控系统故障诊断的方法 1162
一、直观法 1167
二、CNC系统的自诊断功能 1167
三、数控和状态检查 1167
四、报警指示灯显示故障 1168
五、备板置换法 1170
六、交换法 1172
七、敲击法 1172
八、测量比较法 1173
第四节 电源维护及故障诊断 1174
一、电源配置 1176
二、通过电气原理图诊断故障 1176
三、负载对地短路的故障诊断 1181
第五节 数控机床的抗干扰 1182
一、电磁波干扰 1182
二、供电线路干扰 1545
三、信号传输干扰 1545
四、抗干扰的措施 1545
第二章 数控机床精度及性能检验 1548
第一节 精度检验 1549
一、几何精度检验 1550
二、定位精度的检验 1550
三、切削精度检验 1551
第二节 机床性能及数控功能检验 1551
一、机床性能 1551
二、数控功能 1551
三、连续空载运行 1552
第三节 数控系统的验收 1552
一、数控系统外观检查 1552
二、控制柜内元器件的紧固检查 1552
三、输入电源电压、相序的确认 1553
四、检查直流电流输出 1553
五、确认数控系统与机床侧的接口 1553
六、确认数控系统各参数的设定 1553
七、接通电源检查机床状态 1554
八、用手轮进给检查各轴运转情况 1554
九、用准停功能来检查主轴的定位情况 1554
第三章 数控机床机械结构故障诊断及维护 1555
第一节 数控机床机械故障诊断的方法 1555
一、实用诊断技术的应用 1555
二、机床异响的诊断 1556
三、现代诊断技术的应用 1556
第二节 主轴部件 1557
一、维护特点 1558
二、主传动链的维护 1559
三、主传动链的故障诊断 1559
第三节 滚珠丝杠螺母副 1559
一、滚珠丝杠螺母副的维护 1560
二、滚珠丝杠副的故障诊断 1561
第四节 导轨副 1565
一、导轨副的维护 1565
二、导轨的故障诊断 1565
第五节 刀库及换刀装置 1571
一、刀库与换刀机械手的维护要点 1574
二、刀库与换刀机械手的故障诊断 1579
第六节 液压与气压传动系统 1579
一、液压传动系统 1580
二、气动系统 1581
第四章 数控系统操作功能 1581
第一节 SIEMENS数控系统操作面板 1581
一、系统操作面板 1581
第二节 FANUC0数控系统操作面板 1582
一、系统面板 1582
二、机床操作面板 1582
第三节 三菱MELDAS50数控系统诊断页面 1583
一、诊断功能 1583
二、其他功能 1583
第四节 数控机床回参考点的故障诊断 1583
一、回参考点的方式 1584
二、回参考点的故障诊断 1584
三、数控车床参考点的设定 1584
第五章 伺服系统故障诊断 1587
第一节 主轴驱动系统 1590
一、常用主轴驱动系统介绍 1593
二、主轴伺服系统的故障形式及诊断方法 1593
三、直流主轴驱动的故障诊断 1595
四、主轴交流驱动的故障诊断 1596
第二节 进给伺服系统 1597
一、常见进给驱动系统介绍 1597
二、伺服系统结构形式 1598
三、进给伺服系统的故障形式及诊断方法 1599
四、伺服电动机的维护 1599
五、进给驱动的故障诊断 1602
第三节 位置检测装置 1603
一、故障形式 1603
二、位置检测元件的维护 1604
三、位置检测的故障诊断 1604
第四节 伺服系统参数 1604
一、速度环调整 1606
二、位置环调整 1609
三、调试和诊断显示 1609
第六章 数控机床输入/输出(I/O)控制的故障诊断 1609
第一节 数控机床PLC的功能 1615
一、PLC与外部信息的交换 1615
二、数控机床PLC的功能 1616
第二节 PLC输入/输出元件 1619
一、输入元件、1.控制开关 1619
二、输出元件 1621
第三节 数控机床PLC控制的故障诊断 1622
一、PLC故障的表现形式 1622
二、数控机床PLC故障诊断的方法 1624
第七章 维修的基本要求和故障常规处理方法 1625
第一节 维修的基本要求 1629
一、对维修人员的素质要求 1629
二、必要的维修用器具 1630
三、必要的技术资料和技术准备 1630
四、必要的备件 1632
第二节 常见故障分类 1636
一、按数控机床发生故障的部件分类 1647
二、按数控机床发生的故障性质分类 1647
三、按故障发生后有无报警显示分类 1648
四、按故障发生的原因分类 1650
第三节 故障的常规处理方法 1655
一、调查故障现场,充分掌握故障信息 1657
二、分析故障原因,确定检查的方法和步骤 1666
三、故障的检测和排除 1666
第八章 预防性维护方法 1667
第一节 预防性维护的重要性 1669
第二节 预防性维护工作的主要内容 1672
第九章 常用的片级维修方法 1672
第一节 外观法 1672
第二节 电源检查法 1679
第三节 静态测量法 1683
第四节 动态测量法 1683
第五节 在线测试法 1683
第六节 汇编语言测试法 1684
第七节 模拟台测试法 1685
第十章 数控机床开机调试 1686
第一节 通电前的外观检查 1693
第二节 机床总电源接通后的检查 1696
第三节 CNC电器箱通电检查 1696
第四节 手动数据输入(MDI)试验 1698
第五节 编辑(EDIT)功能试验 1707
第六节 自动状态(AUTO)试验 1707
第七节 外围设备试验 1707
第七编 数控机床维修实例 1708
第一章 数控车床维修实例 1708
第一节 概述 1712
第二节 CNC系统故障实例与诊断 1713
第三节 伺服系统故障实例与诊断 1713
第四节 刀架系统的故障实例与诊断 1713
第五节 其它部位故障实例与诊断 1714
第二章 数控铣床维修实例 1715
第一节 概述 1716
第二节 CNC系统故障实例与诊断 1716
第三节 伺服系统故障实例与诊断 1716
第四节 主轴系统故障实例与诊断 1717
第五节 工作台系统故障实例与诊断 1717
第六节 液压、气动系统故障实例与诊断 1719
第七节 其它类型故障实例与诊断 1719
第三章 加工中心维修实例 1719
第一节 CNC系统故障实例与诊断 1722
第二节 伺服系统故障实例与诊断 1722
第三节 刀库、机械手部分故障实例与诊断 1723
第四节 工作台部分故障实例与诊断 1725
第五节 主轴系统故障实例与诊断 1727
第四章 数控镗铣床维修实例 1728
第一节 伺服系统故障实例与诊断 1734
第二节 主轴系统故障实例与诊断 1739
第三节 其它部分故障实例与诊断 1740
第五章 数控电加工机床维修实例 1740
第一节 概述 1741
第二节 CNC系统故障实例与诊断 1741
第三节 脉冲电源系统故障实例与诊断 1742
第四节 其它机电故障实例与诊断 1743
第六章 其它数控加工设备维修实例 1743
第一节 数控磨床故障实例与诊断 1744
第二节 其它数控加工设备的故障实例与诊断 1747
- 《徐振维语文教学思想研究》陈文高编 1992
- 《理想国 维米尔的帽子 17世纪和全球化世界的黎明》(加)卜正民著;黄中宪译 2017
- 《水电厂运维一体化技能培训教材 初级》国网新源控股有限公司组编 2015
- 《光栅尺支架夹具设计及数控加工》张方阳 2019
- 《数控机床主轴系统在线动平衡技术》王展 2020
- 《低维材料及其界面的热输运机制与模型研究》王艳磊著 2019
- 《航空复杂零件数控加工工艺设计与优化》任军学 2018
- 《VERICUT数控仿真实例教程》黄雪梅编著 2019
- 《数控铣削编程与加工 第2版》赵刚主编 2019
- 《UG NX 8.5数控加工自动编程经典实例 第3版》(中国)钟平福 2019
- 《电子测量与仪器》人力资源和社会保障部教材办公室组织编写 2009
- 《吉林省志 卷2 大事记》吉林省地方志编纂委员会编纂 2002
- 《少儿电子琴入门教程 双色图解版》灌木文化 2019
- 《通信电子电路原理及仿真设计》叶建芳 2019
- 《电子应用技术项目教程 第3版》王彰云 2019
- 《中国十大出版家》王震,贺越明著 1991
- 《近代民营出版机构的英语函授教育 以“商务、中华、开明”函授学校为个案 1915年-1946年版》丁伟 2017
- 《中国电子政务发展报告 2018-2019 数字中国战略下的政府管理创新》何毅亭主编 2019
- 《电子管风琴伴奏中外经典合唱曲集》主编;王永刚副主编;宋尧尧陈宏赵雪陈海涛 2019
- 《电工电子技术实验》彭小峰,王玉菡,杨奕主编 2018