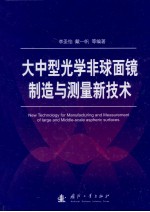
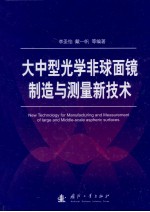
大中型光学非球面镜制造与测量新技术PDF电子书下载
- 电子书积分:18 积分如何计算积分?
- 作 者:李圣怡等编著
- 出 版 社:北京:国防工业出版社
- 出版年份:2011
- ISBN:9787118072372
- 页数:628 页
上篇 制造技术 2
第一章 现代非球面光学研抛技术基础 2
1.1 光学非球面的优点及应用 2
1.1.1 光学非球面的优点 2
1.1.2 非球面光学零件在军用装备的应用 3
1.1.3 非球面光学零件在民用装备的应用 4
1.2 光学非球镜制造的特点 5
1.2.1 现代光学系统对非球面光学零件的要求 5
1.2.2 非球面光学零件的加工分析 9
1.3 超光滑表面制造技术 12
1.3.1 超光滑表面及应用 12
1.3.2 超光滑表面制造技术概述 15
1.3.3 基于机械微切削原理的超光滑表面制造技术 16
1.3.4 传统游离磨料抛光的超光滑表面制造技术 17
1.3.5 非接触超光滑抛光原理和方法 20
1.3.6 非接触化学机械抛光方法(CMP) 22
1.3.7 磁场效应辅助加工技术 23
1.3.8 粒子流加工技术 23
1.4 先进非球面光学研抛技术 25
1.4.1 非球面光学零件的经典研抛方法 25
1.4.2 非球面光学零件的现代数控研抛方法 26
1.4.3 非球面光学零件的可控柔体研抛技术 27
参考文献 34
第二章 非球面光学研抛技术的基础理论 37
2.1 光学机械研抛技术的Preston方程及其应用 37
2.2 非球面加工的确定性成形原理 40
2.3 非球面加工的成形过程理论分析 42
2.3.1 非球面加工的成形过程双级数模型 42
2.3.2 去除函数尺寸大小对加工的影响 43
2.3.3 去除函数扰动影响 45
2.3.4 定位误差影响 48
2.3.5 离散间隔影响 49
2.4 全口径线性扫描方式面形修正理论 51
2.4.1 基于Bayesian的迭代算法 52
2.4.2 脉冲迭代方法 59
2.4.3 截断奇异值分解法 60
2.5 极轴扫描方式面形修正技术 62
2.5.1 去除函数具有(近似)回转对称特性 62
2.5.2 去除函数不具有回转对称特性 65
2.6 成形的频域分析 68
2.6.1 一般成形条件下的频谱特征 69
2.6.2 回转对称型去除函数的修形能力 70
2.7 熵最大研抛原理 71
2.7.1 研抛熵原理表述 72
2.7.2 最大熵原理在定偏心平面研抛中应用的实例 74
2.7.3 基于最大熵原理的双转子小工具加工工艺参数的选择的实例 77
2.7.4 基于熵增原理抑制磁流变修形中、高频误差的实例 78
参考文献 83
附录A 两维Hermite级数 85
附录B 两维Fouier级数 87
附录C 驻留时间双级数模型求解 88
附录D 驻留时间双级数模型求解误差分析 90
第三章 基于小研抛盘工具的CCOS技术 92
3.1 基于小研抛盘工具的CCOS技术综述 92
3.1.1 小工具CCOS技术进展 92
3.1.2 研抛盘小工具CCOS技术的关键问题 94
3.2 AOCMT光学非球面加工机床 96
3.3 去除函数的建模与分析 98
3.3.1 理想去除函数的特性 98
3.3.2 理论模型 99
3.3.3 实验模型 100
3.3.4 去除函数的修形能力分析 102
3.3.5 复杂形状研抛盘去除函数的建模和特性分析 105
3.4 CCOS技术中驻留时间算法及分析 110
3.4.1 基于加工时间的脉冲迭代法 110
3.4.2 卷积效应对残留误差的影响 112
3.5 边缘效应下的去除函数建模 118
3.5.1 抛光模露边时的压力分布 119
3.5.2 边缘效应下的去除函数建模 121
3.6 光学表面小尺度制造误差的产生原因与修正方法 126
3.6.1 光学表面小尺度制造误差的产生原因与评价方法 126
3.6.2 小尺度制造误差的全口径均匀抛光修正法 128
3.6.3 小尺度制造误差的确定区域修正法 137
3.7 大中型非球面研抛加工控制策略及实验 140
3.7.1 大中型非球面的制造工艺路线和研抛加工控制策略 140
3.7.2 φ500mm抛物面镜加工实验 142
参考文献 145
第四章 离子束抛光技术 148
4.1 离子束抛光技术概述 148
4.1.1 离子束加工技术应用 148
4.1.2 光学镜面离子束抛光的基本原理与特点 150
4.1.3 光学镜面离子束抛光技术的发展 153
4.2 光学镜面离子束抛光的基本理论 156
4.2.1 离子溅射过程描述 156
4.2.2 离子束抛光材料去除率 159
4.3 离子束抛光去除函数建模分析 167
4.3.1 离子束抛光去除函数理论建模 167
4.3.2 离子束抛光去除函模型特性分析 172
4.3.3 离子束抛光去除函模型试验建模 177
4.4 离子束加工系统设计与分析 180
4.4.1 系统构建 180
4.4.2 系统分析 181
4.5 离子束抛光面形误差收敛与精度预测预报 188
4.6 离子束抛光的小尺度误差演变 192
4.6.1 表面粗糙度演变 192
4.6.2 微观形貌演变 194
4.7 离子束抛光试验 199
4.7.1 平面光学镜面抛光试验 199
4.7.2 曲面修形试验 203
参考文献 205
第五章 磁流变抛光技术 208
5.1 磁流变抛光技术概述 208
5.1.1 磁流体的应用 208
5.1.2 光学零件磁场效应辅助抛光技术的发展状况 210
5.1.3 确定性磁流变抛光技术发展状况 211
5.2 磁流变抛光材料去除机理与数学模型 216
5.2.1 磁流变抛光的材料去除机理 216
5.2.2 单颗磨粒所受载荷与压入深度理论计算 219
5.2.3 磁流变抛光区域流体动力学分析与计算 221
5.3 磁流变抛光机床 229
5.3.1 磁流变抛光机床结构的基本要求 229
5.3.2 磁流变抛光实验样机的机床结构 232
5.3.3 倒置式磁流变抛光装置的设计 233
5.3.4 磁流变液的循环控制系统 236
5.4 磁流变抛光液及其性能测试研究 240
5.4.1 磁流变抛光液研制的发展现状 240
5.4.2 磁流液的组成成分及性能评价 241
5.4.3 磁流变液的组成选择原则 246
5.4.4 磁流变抛光液配制实例 249
5.4.5 磁流变抛光液的性能测试研究 250
5.5 磁流变抛光工艺参数优化 256
5.5.1 磁流变抛光工艺参数正交实验 256
5.5.2 灰色关联分析 258
5.5.3 多项工艺指标的参数优化 261
5.5.4 加工过程综合优化 262
5.6 磁流变抛光的光学表面成形技术及加工实例 263
5.6.1 MRF的计算机控制光学表面成形(CCOS)技术 263
5.6.2 光学零件磁流变成形抛光驻留时间求解基本算法 264
5.6.3 光学零件磁流变成形抛光实例 267
5.7 磁射流抛光技术研究 277
5.7.1 磨料射流抛光技术概述 277
5.7.2 磁射流聚束稳定性分析 280
5.7.3 磁射流抛光去除机理的CFD分析 284
5.7.4 光学零件磁射流修形抛光实验 287
参考文献 290
第六章 确定性光学加工误差的评价方法 293
6.1 概述 293
6.2 常用的光学加工误差评价方法 294
6.2.1 光学加工误差的几何精度评价参数 295
6.2.2 基于功率谱密度特征曲线的光学加工误差评价 296
6.2.3 基于散射理论的光学加工误差评价 297
6.2.4 基于统计光学理论的光学加工误差评价 298
6.3 光学加工误差分布特征的分析方法 299
6.3.1 光学表面任意方向加工误差的评价与分析 299
6.3.2 光学表面局部误差的评价与分析 305
6.3.3 工艺方法对光学加工误差的影响分析 307
6.4 光学加工误差的散射性能评价方法 321
6.4.1 光学加工误差的二进频带划分方法 321
6.4.2 基于Harvey-Shack散射理论的误差评价方法 325
6.4.3 光学加工误差对散射性能的影响分析 326
6.5 基于光学性能分析的频带误差评价方法 330
6.5.1 不同频带误差对光学性能的影响特点 330
6.5.2 光学系统应用场合对频带误差的要求 333
6.5.3 φ200mm抛物面镜离子束加工误差的评价 339
参考文献 343
下篇 测量技术 346
第一章 大中型光学镜面制造中的测量技术 346
1.1 绪论 346
1.1.1 大中型光学镜面的需求概述 346
1.1.2 大中型光学镜面制造中的测量概况 350
1.2 大中型光学镜面制造中的坐标测量技术原理 351
1.3 大中型光学镜面制造中的干涉零位测量技术 352
1.3.1 干涉零位测量技术基本原理 352
1.3.2 大中型平面和球面的零位测试技术 354
1.3.3 二次非球面曲面的无像差点法零位测试技术 356
1.3.4 非球面镜的补偿检验技术 359
1.3.5 计算机生成全息图测试技术 361
1.4 大中型光学镜面制造中的非零位测量技术 368
1.4.1 剪切干涉测量 369
1.4.2 高分辨率CCD方法 370
1.4.3 欠采样干涉测量方法 370
1.4.4 长波干涉测量方法 371
1.4.5 双波长干涉测量方法 372
1.4.6 子孔径拼接干涉测量方法 372
1.5 相位恢复技术 373
1.6 亚表面质量检测技术 373
1.7 大中型光学镜面制造中的测量实例 374
1.7.1 中国2.16m天文望远镜测量实例 374
1.7.2 GMT望远镜测量实例 375
1.7.3 JWST望远镜测量实例 379
1.7.4 GTC望远镜测量实例 381
1.7.5 MMT望远镜次镜测量实例 384
1.7.6 SPICA望远镜测量实例 385
1.7.7 QED Technologies公司子孔径拼接干涉测量 386
1.7.8 大型平面镜制造中的在位检测 388
参考文献 390
第二章 光学非球面坐标测量技术 393
2.1 光学非球面坐标测量技术的研究现状与发展趋势 393
2.1.1 光学非球面坐标测量技术的地位和特点 393
2.1.2 光学非球面坐标检测国内外研究现状与发展趋势 394
2.2 大口径非球面直角坐标测量技术研究 403
2.2.1 直角坐标测量系统的设计 403
2.2.2 大型非球面镜直角坐标测量原理 410
2.2.3 基于多截线测量的光学非球面面形误差分析与评定 412
2.2.4 加工检测实例——φ500mm非球面镜的加工与检测 423
2.3 大型非球面摆臂式测量技术研究 426
2.3.1 测量原理分析 426
2.3.2 测量系统结构设计 430
2.3.3 测量系统精度分析与建模 432
2.3.4 摆臂式轮廓法测量非球面顶点曲率半径优化算法 438
2.3.5 测量算法仿真与测量试验 441
2.4 基于多段拼接的高陡度非球面坐标检测理论与算法 444
2.4.1 测量原理与数学模型 444
2.4.2 基于最小二乘的迭代算法 447
2.4.3 分段轮廓的自动划分与算法仿真 449
2.4.4 测量试验 451
参考文献 453
第三章 子孔径拼接测量方法 457
3.1 概述 457
3.1.1 子孔径拼接测量的基本原理 457
3.1.2 子孔径拼接测量的发展概况 457
3.2 子孔径拼接基本算法 461
3.2.1 两个子孔径拼接的数学模型 461
3.2.2 子孔径同步拼接模型与算法 462
3.3 子孔径拼接迭代算法 463
3.3.1 数学模型 464
3.3.2 迭代算法 468
3.3.3 大中型光学镜面的粗-精拼接策略 471
3.4 子孔径划分方法 471
3.4.1 子孔径的粗略划分 472
3.4.2 计算子孔径的最佳拟合球 474
3.4.3 子孔径划分的仿真验证 477
3.5 子孔径拼接测量工作站 482
3.5.1 子孔径拼接工作站的机械构型设计 482
3.5.2 子孔径拼接工作站的运动学模型 485
3.6 子孔径拼接测量的实验验证 487
3.6.1 平面镜拼接测量实例 487
3.6.2 球面镜拼接测量实例 492
3.6.3 非球面镜拼接测量实例 496
3.7 子孔径拼接测量方法的发展趋势 499
附录A 线性化位形优化子问题的推导 501
附录B 线性最小二乘问题的分块顺序QR分解程序 504
参考文献 505
第四章 大中型光学镜面相位恢复在位检测技术 508
4.1 相位恢复检测技术综述 508
4.1.1 相位恢复在位检测技术的意义 508
4.1.2 相位恢复方法应用综述 509
4.1.3 相位恢复算法理论综述 511
4.2 相位恢复测量的基本原理和算法 513
4.2.1 相位恢复测量原理 513
4.2.2 光场衍射传播计算 516
4.2.3 镜面检测相位恢复算法 517
4.3 球面波的相位恢复检测 522
4.3.1 测量装置 522
4.3.2 口径200mm球面镜的测量 522
4.3.3 大口径球面镜的测量 527
4.4 亚像素分辨率相位恢复测量研究 531
4.4.1 亚像素分辨率相位恢复测量原理 531
4.4.2 亚像素光强约束函数设计 534
4.4.3 亚像素分辨率镜面测量实验 536
4.5 非球面镜的相位恢复检测技术 539
4.5.1 非球面面形方程和非球面度 539
4.5.2 非球面镜离焦光场特性 540
4.5.3 非球面相位恢复测量规划 542
4.5.4 APR算法设计 544
4.6 非球面镜相位恢复测量实验 548
4.6.1 光源和图像定位 548
4.6.2 定位误差对测量的影响 549
4.6.3 镜面遮光误差对测量的影响和控制方法 551
4.6.4 口径170mm抛物面镜的检测 551
参考文献 554
第五章 光学零件制造中的亚表面质量检测与保障 558
5.1 亚表面质量概述 558
5.1.1 亚表面质量的概念 558
5.1.2 亚表面质量对光学零件使用性能的影响 559
5.2 亚表面损伤的产生机理 563
5.2.1 磨削和研磨损伤产生机理 563
5.2.2 抛光损伤产生机理 565
5.3 磨削和研磨亚表面损伤检测技术 568
5.3.1 损伤性检测技术 568
5.3.2 无损检测技术 572
5.3.3 亚表面损伤检测实验研究 576
5.3.4 基于表面质量关联的亚表面检测技术研究 581
5.4 亚表面损伤表征方法 590
5.4.1 磨削过程 590
5.4.2 研磨过程 591
5.5 亚表面损伤深度预测方法 596
5.5.1 磨削过程亚表面损伤深度预测 596
5.5.2 研磨过程亚表面损伤深度预测 598
5.6 加工参数对亚表面损伤深度的影响规律研究 602
5.6.1 磨削过程参数对亚表面裂纹深度的影响 602
5.6.2 研磨过程参数对亚表面裂纹深度的影响 604
5.7 亚表面质量保障技术 607
5.7.1 抛光亚表面损伤的表现形式 607
5.7.2 抛光亚表面损伤检测 610
5.7.3 抛光亚表面损伤模型 616
5.7.4 传统抛光亚表面损伤的抑制策略 617
5.7.5 复合加工及后处理技术提高激光损伤阈值 620
参考文献 624
- 《电子测量与仪器》人力资源和社会保障部教材办公室组织编写 2009
- 《互换性与测量技术》王宏宇主编 2019
- 《中学物理奥赛辅导:热学 光学 近代物理学》崔宏滨 2012
- 《灰姑娘的难题 测量》(韩)李孝真文 2016
- 《公差配合与测量技术》荀占超 2018
- 《测绘地理信息行业职业技能培训教材 测量基础》自然资源部职业技能鉴定指导中心 2019
- 《电工仪表与测量》殷兴光,王月爱主编 2017
- 《电化学测量》胡会利,李宁编著 2019
- 《光学调频连续波干涉技术》(加)郑刚著;廖寅宵,刘柯,宋金城等译 2019
- 《心理测量》黎光明编著 2019
- 《市政工程基础》杨岚编著 2009
- 《家畜百宝 猪、牛、羊、鸡的综合利用》山西省商业厅组织技术处编著 1959
- 《《道德经》200句》崇贤书院编著 2018
- 《高级英语阅读与听说教程》刘秀梅编著 2019
- 《计算机网络与通信基础》谢雨飞,田启川编著 2019
- 《看图自学吉他弹唱教程》陈飞编著 2019
- 《法语词汇认知联想记忆法》刘莲编著 2020
- 《培智学校义务教育实验教科书教师教学用书 生活适应 二年级 上》人民教育出版社,课程教材研究所,特殊教育课程教材研究中心编著 2019
- 《国家社科基金项目申报规范 技巧与案例 第3版 2020》文传浩,夏宇编著 2019
- 《流体力学》张扬军,彭杰,诸葛伟林编著 2019
- 《指向核心素养 北京十一学校名师教学设计 英语 七年级 上 配人教版》周志英总主编 2019
- 《北京生态环境保护》《北京环境保护丛书》编委会编著 2018
- 《指向核心素养 北京十一学校名师教学设计 英语 九年级 上 配人教版》周志英总主编 2019
- 《抗战三部曲 国防诗歌集》蒲风著 1937
- 《高等院校旅游专业系列教材 旅游企业岗位培训系列教材 新编北京导游英语》杨昆,鄢莉,谭明华 2019
- 《中国十大出版家》王震,贺越明著 1991
- 《近代民营出版机构的英语函授教育 以“商务、中华、开明”函授学校为个案 1915年-1946年版》丁伟 2017
- 《新工业时代 世界级工业家张毓强和他的“新石头记”》秦朔 2019
- 《智能制造高技能人才培养规划丛书 ABB工业机器人虚拟仿真教程》(中国)工控帮教研组 2019
- 《陶瓷工业节能减排技术丛书 陶瓷工业节能减排与污染综合治理》罗民华著 2017