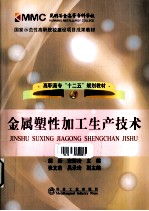
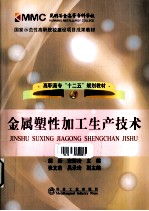
金属塑性加工生产技术PDF电子书下载
- 电子书积分:10 积分如何计算积分?
- 作 者:胡新,宋群玲主编;张文莉,吴承玲副主编
- 出 版 社:北京:冶金工业出版社
- 出版年份:2011
- ISBN:7502454517
- 页数:224 页
Ⅰ 挤压 1
1 挤压概述 1
1.1 挤压基本知识 1
1.1.1 挤压的定义 1
1.1.2 挤压的特点 1
1.1.3 挤压的分类 2
1.2 常见挤压方法 2
1.2.1 正向不脱皮挤压棒材法 2
1.2.2 正向脱皮挤压棒材法 3
1.2.3 正向水封挤压法 3
1.2.4 正向挤压管材法 3
1.2.5 联合挤压管材法 3
1.2.6 反向挤压法 3
1.3 挤压新方法 4
1.3.1 静液挤压法 4
1.3.2 全润滑无压余挤压法 4
1.3.3 随动挤压法 4
1.3.4 有效摩擦挤压法 5
1.3.5 锭接锭挤压法 5
1.3.6 Conform连续挤压法 5
1.4 挤压技术的发展历史和发展趋势 6
1.4.1 发展历史 6
1.4.2 发展趋势 7
复习思考题 7
2 挤压理论 8
2.1 挤压过程中金属的变形特点 8
2.1.1 挤压过程中金属的应力状态和变形状态 8
2.1.2 挤压过程中金属的变形 8
2.1.3 挤压时影响金属流动的因素 10
2.2 挤压变形参数和挤压力 12
2.2.1 挤压变形参数 12
2.2.2 挤压力 13
复习思考题 15
3 挤压工具 16
3.1 概述 16
3.1.1 挤压工具的种类 16
3.1.2 挤压工具的工作条件 16
3.2 易损挤压工具 17
3.2.1 挤压模 17
3.2.2 穿孔针(芯棒) 21
3.2.3 挤压垫 22
3.3 大型挤压工具 23
3.3.1 挤压杆 23
3.3.2 挤压筒 23
3.4 挤压工具材料和提高工具使用寿命的途径 25
3.4.1 对挤压工具材料的要求 25
3.4.2 挤压工具材料的种类及性能 25
3.4.3 合理选择工具材料 27
3.4.4 提高挤压工具使用寿命的途径 27
复习思考题 28
4 挤压设备 29
4.1 锭坯加热设备 29
4.1.1 重油加热炉 29
4.1.2 环行煤气加热炉 29
4.1.3 感应加热炉 29
4.2 挤压机 30
4.2.1 挤压机的分类 30
4.2.2 卧式挤压机 30
4.2.3 立式挤压机 32
4.3 挤压机的主要部件及其结构 33
4.3.1 模座 33
4.3.2 机架 35
4.3.3 缸体与柱塞 35
4.4 挤压机的辅助设备 35
4.4.1 锭坯剪切和剥皮装置 35
4.4.2 供锭机构 36
4.4.3 制品的牵引机构 36
4.4.4 制品接受及运输机构 38
4.4.5 挤压垫与残料分离装置 38
4.5 挤压机的液压传动 38
4.5.1 高压泵直接传动 39
4.5.2 高压泵-蓄能器传动 39
复习思考题 39
5 挤压工艺 40
5.1 锭坯尺寸的选择 40
5.1.1 锭坯尺寸选择的原则 40
5.1.2 锭坯直径的确定 40
5.1.3 锭坯长度的确定 41
5.2 锭坯加热 41
5.2.1 加热目的 41
5.2.2 加热方法 41
5.2.3 加热制度 42
5.3 挤压温度和挤压速度的选择 42
5.3.1 挤压温度的选择 42
5.3.2 挤压速度的选择 46
5.3.3 挤压中的温度-速度控制 47
5.4 挤压润滑 49
5.4.1 挤压润滑的目的 49
5.4.2 润滑应注意的问题 49
5.4.3 选择润滑剂的原则 50
5.4.4 润滑剂的选择 50
复习思考题 51
6 挤压制品的组织、性能和质量 52
6.1 挤压制品的组织 52
6.1.1 正向挤压棒材的组织不均匀性 52
6.1.2 挤压制品的粗晶环 53
6.1.3 挤压制品的层状组织 55
6.2 挤压制品的力学性能 56
6.2.1 挤压制品力学性能的不均匀 56
6.2.2 变形程度对力学性能不均匀的影响 56
6.2.3 挤压制品纵向和横向方向力学性能的差异 56
6.2.4 挤压效应 56
6.3 挤压缩尾 58
6.3.1 中心缩尾 58
6.3.2 环形缩尾 58
6.3.3 皮下缩尾 59
6.3.4 减少挤压缩尾的措施 59
6.4 制品的表面质量 59
6.4.1 挤压裂纹和头部撕裂 59
6.4.2 表面夹灰和压入缺陷 60
6.4.3 皮下气泡、起皮和重皮缺陷 60
6.4.4 擦伤和划伤缺陷 61
6.4.5 制品的尺寸公差 61
复习思考题 61
Ⅱ 拉拔 63
7 拉拔概述 63
7.1 拉拔的基本概念 63
7.1.1 拉拔的定义 63
7.1.2 拉拔的种类 63
7.2 拉拔生产的特点 65
7.3 拉拔生产的历史与发展 66
7.3.1 拉拔生产的历史 66
7.3.2 拉拔生产的发展趋势 67
复习思考题 67
8 拉拔理论 68
8.1 拉拔的变形指数 68
8.1.1 延伸系数λ 68
8.1.2 断面减缩系数μ 68
8.1.3 加工率ε 68
8.1.4 伸长率A 69
8.2 实现拉拔的基本条件 69
8.3 拉拔的应力与应变 70
8.3.1 应力状态与变形状态 70
8.3.2 金属在变形区中的流动特点 70
8.4 拉拔力 71
复习思考题 73
9 拉拔工具 74
9.1 拉拔模 74
9.1.1 普通拉模 74
9.1.2 特殊拉模 77
9.2 芯头 78
9.2.1 固定短芯头 78
9.2.2 游动芯头 79
9.3 模具材料及提高模具使用寿命的途径 81
9.3.1 模具材料 81
9.3.2 拉拔前模具的安装 82
9.3.3 提高模具使用寿命的途径 84
复习思考题 85
10 拉拔设备 86
10.1 管、棒、型材拉拔机 86
10.1.1 链式拉拔机 86
10.1.2 圆盘拉拔机 90
10.1.3 联合拉拔机列 92
10.2 拉线机 94
10.2.1 单次拉线机 95
10.2.2 连续拉线机 95
复习思考题 100
11 拉拔工艺 101
11.1 拉拔配模 101
11.1.1 拉拔配模的要求和分类 101
11.1.2 拉拔配模的内容 101
11.1.3 单模拉拔配模计算 106
11.1.4 多模连续拉拔配模计算 114
11.2 热处理和酸洗 117
11.2.1 热处理 117
11.2.2 酸洗 118
11.3 拉拔润滑 119
11.3.1 拉拔时润滑剂的作用及要求 119
11.3.2 拉拔润滑剂的种类 120
11.4 拉拔时制品的缺陷和消除 124
11.4.1 折叠 124
11.4.2 裂缝(包括裂纹、发纹) 124
11.4.3 凹坑 124
11.4.4 尺寸超差 124
11.4.5 拉裂 125
11.4.6 管材壁厚不均 125
11.4.7 划伤和擦伤 125
11.4.8 拔断 125
11.4.9 空拔头过长 125
11.4.10 抖纹 126
11.4.11 纵向开裂 126
11.4.12 管壁的纵向凹折 126
11.4.13 翘皮 126
11.4.14 表面夹灰和夹杂 126
11.4.15 麻面 127
11.4.16 碰(压)凹 127
11.4.17 矫凹 127
11.5 特殊拉拔方法 127
11.5.1 无模拉拔 127
11.5.2 集束拉拔 128
11.5.3 玻璃膜金属液抽丝 128
11.5.4 静液挤压拉线 129
复习思考题 130
Ⅲ 轧制 131
12 轧制概述 131
12.1 轧制的基本概念 131
12.1.1 轧制的实质 131
12.1.2 轧制分类 131
12.2 有色金属轧材的种类及用途 132
12.2.1 按有色金属种类分类 132
12.2.2 按轧材的断面形状特征进行分类 133
12.3 有色金属及其合金的轧材生产系统 134
12.4 轧制技术的现状与发展 134
12.4.1 轧制理论和实践紧密结合 134
12.4.2 生产过程连续化 134
12.4.3 生产过程自动化 134
12.4.4 节约能源和金属消耗 135
12.4.5 不断扩大产品品种和规格 135
复习思考题 135
13 轧制设备 136
13.1 轧机的分类 136
13.1.1 按用途分类 136
13.1.2 按构造分类 136
13.1.3 按工作方式分类 138
13.1.4 按布置分类 138
13.2 轧机的组成 138
13.2.1 主电动机 139
13.2.2 传动装置 139
13.2.3 工作机座 139
13.3 轧机的工作机座 139
13.3.1 轧辊 139
13.3.2 轧辊轴承 140
13.3.3 轧辊调整装置 140
13.3.4 机架 141
13.4 辅助设备 142
13.4.1 剪切设备 142
13.4.2 矫直设备 144
13.4.3 卷取设备 145
13.4.4 运输设备 146
13.4.5 加热设备 147
复习思考题 147
14 板带材生产 148
14.1 概述 148
14.1.1 板带材的特点、分类和技术要求 148
14.1.2 有色金属板带材的主要生产方法 149
14.1.3 生产流程 151
14.2 热轧板带材的生产 151
14.2.1 热轧的特点 151
14.2.2 热轧对锭坯的要求 152
14.2.3 热轧前的坯料加热 152
14.2.4 热轧的压下制度 155
14.2.5 热轧的工艺润滑和轧辊冷却 158
14.2.6 热轧机和热轧辊 159
14.2.7 热轧后的坯料处理 160
14.3 冷轧板带材的生产 161
14.3.1 冷轧的特点 161
14.3.2 冷轧的压下制度 161
14.3.3 冷轧的工艺冷却和工艺润滑 163
14.3.4 冷轧中的张力轧制 164
14.3.5 冷轧机和冷轧辊 165
14.4 板带材的质量和缺陷消除 166
14.4.1 尺寸精度 166
14.4.2 横向厚差和板形控制 169
14.4.3 脆裂 172
14.4.4 表面质量 174
14.4.5 力学性能 174
14.5 铝、铜板带箔材的生产工艺 175
14.5.1 铝及铝合金板带材的生产工艺 175
14.5.2 铜及铜合金板带材的生产工艺 179
14.5.3 铝箔的生产工艺 181
复习思考题 184
15 型材线材生产 185
15.1 概述 185
15.2 轧辊孔型设计 185
15.2.1 孔型 186
15.2.2 孔型设计内容及要求 187
15.2.3 常用的孔型系统 188
15.2.4 孔型在轧辊上的配置 190
15.3 型线材轧制工艺 191
15.3.1 坯料准备 191
15.3.2 轧制时的工艺参数 192
15.4 型线材轧制设备组成 193
15.4.1 型线材轧机的种类 194
15.4.2 型线材轧机的布置形式 194
15.4.3 Y形三辊小型轧机 195
15.5 型线材轧制产品质量控制 195
15.5.1 型线材轧制时的表面缺陷 195
15.5.2 产品形状及尺寸精度要求 196
15.5.3 化学成分及力学性能 196
15.5.4 包装及标志 196
复习思考题 196
16 管材生产 197
16.1 概述 197
16.2 冷轧管材生产 197
16.2.1 二辊式周期冷轧管法 198
16.2.2 多辊式冷轧法 202
16.2.3 冷轧管生产时管坯变形理论 204
16.3 热轧管材生产 206
16.3.1 斜轧穿孔方法 206
16.4 管材生产的质量控制 209
16.4.1 冷轧管废品 210
16.4.2 斜轧穿孔废品 210
复习思考题 211
Ⅳ 锻造与冲压 211
17 锻造与冲压 213
17.1 锻造 213
17.1.1 概述 213
17.1.2 自由锻 214
17.1.3 模锻 215
17.1.4 锻造设备 215
17.1.5 铝合金锻造 216
17.2 板料冲压 218
17.2.1 概述 218
17.2.2 冲压工艺 219
17.2.3 冲压设备 220
复习思考题 222
参考文献 223
- 《钒产业技术及应用》高峰,彭清静,华骏主编 2019
- 《现代水泥技术发展与应用论文集》天津水泥工业设计研究院有限公司编 2019
- 《激光加工实训技能指导理实一体化教程 下》王秀军,徐永红主编;刘波,刘克生副主编 2017
- 《异质性条件下技术创新最优市场结构研究 以中国高技术产业为例》千慧雄 2019
- 《Prometheus技术秘笈》百里燊 2019
- 《中央财政支持提升专业服务产业发展能力项目水利工程专业课程建设成果 设施农业工程技术》赵英编 2018
- 《药剂学实验操作技术》刘芳,高森主编 2019
- 《林下养蜂技术》罗文华,黄勇,刘佳霖主编 2017
- 《脱硝运行技术1000问》朱国宇编 2019
- 《催化剂制备过程技术》韩勇责任编辑;(中国)张继光 2019
- 《指向核心素养 北京十一学校名师教学设计 英语 七年级 上 配人教版》周志英总主编 2019
- 《北京生态环境保护》《北京环境保护丛书》编委会编著 2018
- 《指向核心素养 北京十一学校名师教学设计 英语 九年级 上 配人教版》周志英总主编 2019
- 《高等院校旅游专业系列教材 旅游企业岗位培训系列教材 新编北京导游英语》杨昆,鄢莉,谭明华 2019
- 《中国十大出版家》王震,贺越明著 1991
- 《近代民营出版机构的英语函授教育 以“商务、中华、开明”函授学校为个案 1915年-1946年版》丁伟 2017
- 《新工业时代 世界级工业家张毓强和他的“新石头记”》秦朔 2019
- 《智能制造高技能人才培养规划丛书 ABB工业机器人虚拟仿真教程》(中国)工控帮教研组 2019
- 《陶瓷工业节能减排技术丛书 陶瓷工业节能减排与污染综合治理》罗民华著 2017
- 《全国职业院校工业机器人技术专业规划教材 工业机器人现场编程》(中国)项万明 2019