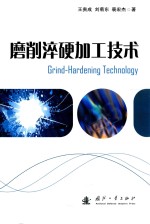
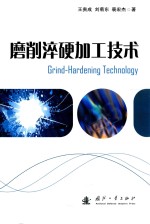
磨削淬硬加工技术PDF电子书下载
- 电子书积分:12 积分如何计算积分?
- 作 者:王贵成,刘菊东,斐宏杰著
- 出 版 社:北京:国防工业出版社
- 出版年份:2015
- ISBN:9787118103953
- 页数:307 页
第一章 绪论 1
1.1 概述 2
1.1.1 磨削淬硬加工及特点 2
1.1.2 磨削淬硬加工技术的形成 3
1.1.3 磨削淬硬研究及进展 9
1.2 磨削淬硬加工技术体系 9
1.2.1 磨削淬硬加工技术优势 9
1.2.2 磨削淬硬加工质量控制体系 11
1.3 磨削淬硬加工研究的主要问题及意义 12
参考文献 13
第二章 磨削淬硬加工的基础 15
2.1 金属材料的表面淬火 15
2.1.1 表面淬火方法分类及特点 15
2.1.2 表面淬火中金属材料奥氏体相变 16
2.2 磨削加工 21
2.2.1 磨削运动 21
2.2.2 磨削加工特征 22
2.2.3 砂轮特性参数 25
2.2.4 磨削要素 26
2.2.5 磨屑及表面形成 29
2.2.6 砂轮选择与修整 32
2.3 磨削淬硬加工的力—热耦合 36
2.3.1 磨削力 36
2.3.2 磨削热 38
2.4 磨削淬硬的主要影响因素及控制途径 41
2.4.1 影响磨削淬硬的主要因素 42
2.4.2 改善与提高磨削淬硬加工效果的基本途径 42
参考文献 45
第三章 磨削淬硬加工区的温度 48
3.1 磨削热量传散机制 48
3.1.1 磨削区的热量 48
3.1.2 磨削热能 49
3.1.3 热量传输载体 50
3.1.4 磨削区温度表示方法 51
3.2 磨削加工热源模型 52
3.2.1 矩形热源模型 52
3.2.2 三角形分布热源模型 53
3.2.3 倾斜三角形热源模型 54
3.2.4 抛物线热源模型 55
3.2.5 各热源模型适用场合比较 56
3.3 磨削区热流量分配 56
3.3.1 磨削区的热流密度 57
3.3.2 流入磨屑的热流密度 57
3.3.3 流入磨削液的热流密度 58
3.3.4 工件和砂轮的热流密度 58
3.4 能量分配系数 59
3.4.1 微观磨粒接触模型 59
3.4.2 宏观的砂轮与工件接触区模型 60
3.4.3 能量分配系数确定 61
3.5 磨削淬硬加工温度场有限元模型 62
3.5.1 有限单元法 62
3.5.2 温度场的基本方程 63
3.5.3 稳态温度场有限单元法 64
3.5.4 瞬态温度场有限元法 67
3.5.5 磨削淬硬温度场的有关参数 68
3.5.6 磨削淬硬温度场的边界条件 69
3.6 温度场数值模拟结果与讨论 69
3.6.1 ANSYS软件 70
3.6.2 磨削淬硬有限元仿真过程 70
3.6.3 温度场模拟结果与分析 76
3.7 磨削淬硬加工区域温度的主动控制 86
3.7.1 磨削淬硬加工层厚度 87
3.7.2 磨削区温度自动控制系统设计 87
3.7.3 磨削区温度自动控制系统 94
参考文献 97
第四章 磨削淬硬层的组织 99
4.1 磨削淬硬层宏观组织形貌 99
4.2 65Mn钢磨削淬硬层显微组织 100
4.2.1 试验方案设计与测试方法 100
4.2.2 试验结果与讨论 101
4.3 45钢和60钢磨削淬硬层组织 104
4.3.1 试验方案设计与测试方法 104
4.3.2 试验结果与讨论 106
4.4 40Cr钢磨削淬硬层组织 109
4.4.1 试验方案设计与测试方法 109
4.4.2 磨削淬硬层组织结构的X射线衍射分析 111
4.4.3 磨削淬硬层组织的扫描电镜分析 114
4.4.4 磨削淬硬层组织的透射电镜分析 122
4.5 磨削淬硬加工组织转变动力学 124
4.5.1 热源模型与热流密度 124
4.5.2 组织相变动力学模型 128
4.5.3 DEFORM有限元软件的二次开发 134
4.6 磨削淬硬层组织的形成及变化 136
4.6.1 磨削温度场与应力场的耦合作用 136
4.6.2 磨削淬硬层组织的形成 137
4.6.3 磨削淬硬层马氏体组织的变化 138
参考文献 139
第五章 磨削淬硬层的性能 142
5.1 磨削淬硬层显微硬度 142
5.1.1 试验方案与测试方法 142
5.1.2 65Mn钢磨削淬硬层显微硬度 142
5.1.3 45钢和60钢磨削淬硬层显微硬度 143
5.1.4 40Cr钢磨削淬硬层显微硬度 144
5.1.5 磨削淬硬层高硬度区的形成及特征 146
5.2 磨削淬硬层及淬硬深度 147
5.2.1 试验方案与测试方法 147
5.2.2 65Mn钢磨削淬硬层深度 148
5.2.3 45钢和60钢磨削淬硬层深度 149
5.2.4 40Cr钢磨削淬硬层深度 149
5.2.5 磨削淬硬层的完全淬硬区深度 152
5.3 磨削淬硬组织与硬化层的数值模拟 153
5.3.1 DEFORM-2D前处理 153
5.3.2 DEFORM-2D求解器 157
5.3.3 DEFORM-2D后处理器 158
5.3.4 工件磨削稳定区的温度场、组织场和硬度场 158
5.3.5 非稳定区的温度场、组织场和硬度场 167
5.4 磨削淬硬深度均匀性 174
5.4.1 试验材料与试验方案 174
5.4.2 磨削淬硬深度与变化 175
5.4.3 磨削条件对淬硬深度均匀性的影响 178
5.5 磨削淬硬层深度预测预报 180
5.5.1 基于神经网络磨削淬硬预测模型 180
5.5.2 系统总体结构与功能模块 181
5.5.3 系统软件的实现与运行 183
5.5.4 系统应用及预测结果分析 185
5.6 磨削淬硬层残余应力 190
5.6.1 磨削淬硬层残余应力的形成 190
5.6.2 试验方案与测试方法 192
5.6.3 试验结果与分析 193
参考文献 194
第六章 磨削淬硬加工的棱边(毛刺)质量 197
6.1 金属切削毛刺形态及其分类 197
6.1.1 切削加工毛刺概念及形态 198
6.1.2 毛刺影响及危害 200
6.1.3 金属切削毛刺分类体系 200
6.2 磨削淬硬加工两侧方向毛刺形成及主要影响因素 203
6.2.1 磨削淬硬加工的两侧毛刺 203
6.2.2 磨削淬硬加工毛刺形成模型 203
6.2.3 影响两侧方向毛刺的主要因素 204
6.3 试验条件与测试方法 205
6.3.1 试验条件 205
6.3.2 测试方法 205
6.4 试验结果与分析 206
6.4.1 毛刺主要形式 206
6.4.2 毛刺形成机理 207
6.4.3 磨削条件对两侧方向毛刺的影响 208
6.4.4 毛刺形成的几种特殊现象 210
6.5 两侧方向毛刺形态转换 213
6.5.1 毛刺形态转变条件 213
6.5.2 排屑状态的影响 213
6.6 控制两侧方向毛刺的主要技术和方法 214
参考文献 214
第七章 磨削淬硬加工的冷却 216
7.1 磨削淬硬加工的射流作用 216
7.1.1 工件的射流冷却区域 216
7.1.2 磨削淬硬加工的射流传热机理 216
7.1.3 射流强化传热的主要影响因素 218
7.2 磨削淬硬加工的冷却作用 220
7.2.1 理想的冷却作用 220
7.2.2 磨削淬硬加工的冷却过程 221
7.2.3 影响淬硬介质冷却能力的主要因素 222
7.3 磨削淬硬加工的冷却介质 224
7.3.1 水基淬硬介质 224
7.3.2 油基淬火介质 226
7.3.3 气体淬火介质 227
7.4 射流冷却在磨削淬硬加工中的应用 229
7.4.1 磨削淬硬加工射流冷却系统 229
7.4.2 液氮射流冷却 230
参考文献 236
第八章 外圆磨削淬硬加工 238
8.1 外圆磨削淬硬加工温度场有限元模型 238
8.1.1 外圆磨削加工几何模型 238
8.1.2 外圆磨削移动热源 240
8.1.3 热量分配比 242
8.1.4 外圆磨削温度场有限元模型 243
8.2 试验条件与检测方法 247
8.3 试验结果与讨论 249
8.3.1 外圆磨削淬硬试样的宏观形貌 249
8.3.2 磨削淬硬层显微组织及形成机理 251
8.3.3 磨削淬硬层显微硬度与变化 254
8.4 提高外圆磨削淬硬加工质量的基本途径 255
参考文献 256
第九章 横向进给磨削淬硬加工 258
9.1 横向进给磨削淬硬温度模拟 258
9.1.1 横向进给磨削淬硬加工 258
9.1.2 横向磨削加工试验参数 259
9.1.3 有限元仿真分析 260
9.1.4 模拟结果与预测 262
9.2 试验条件与测试方法 270
9.3 横向进给磨削淬硬层的宏观形貌 271
9.4 淬硬层显微组织及形成机理 273
9.4.1 单道磨削表面淬硬层组织 273
9.4.2 回火区组织 275
9.4.3 二次淬火区组织 275
9.5 淬硬层显微硬度及其变化 276
9.5.1 深度方向显微硬度分布 276
9.5.2 宽度方向显微硬度分布 277
9.5.3 二次淬火区显微硬度分布 278
9.6 提高横向进给磨削淬硬加工质量的基本途径 278
参考文献 279
第十章 往复磨削淬硬加工 281
10.1 往复磨削淬硬加工的数值模拟 281
10.1.1 数值模拟基础 281
10.1.2 模拟结果与讨论 285
10.1.3 双程磨削淬硬的磨入与磨出端 291
10.1.4 双程磨削淬硬层沿深度方向的分布 297
10.1.5 磨削淬硬层的形成 298
10.2 试验条件与测试方法 299
10.3 往复磨削对淬硬层组织的影响 300
10.4 往复磨削对磨削淬硬层性能的影响 303
10.4.1 淬硬层显微硬度 303
10.4.2 淬硬层深度 303
10.4.3 淬硬层残余应力 304
10.4.4 淬硬层耐磨性 304
10.5 提高往复磨削表面淬硬加工质量的基本途径 305
参考文献 305
- 《钒产业技术及应用》高峰,彭清静,华骏主编 2019
- 《现代水泥技术发展与应用论文集》天津水泥工业设计研究院有限公司编 2019
- 《激光加工实训技能指导理实一体化教程 下》王秀军,徐永红主编;刘波,刘克生副主编 2017
- 《异质性条件下技术创新最优市场结构研究 以中国高技术产业为例》千慧雄 2019
- 《Prometheus技术秘笈》百里燊 2019
- 《中央财政支持提升专业服务产业发展能力项目水利工程专业课程建设成果 设施农业工程技术》赵英编 2018
- 《药剂学实验操作技术》刘芳,高森主编 2019
- 《林下养蜂技术》罗文华,黄勇,刘佳霖主编 2017
- 《脱硝运行技术1000问》朱国宇编 2019
- 《催化剂制备过程技术》韩勇责任编辑;(中国)张继光 2019
- 《中风偏瘫 脑萎缩 痴呆 最新治疗原则与方法》孙作东著 2004
- 《水面舰艇编队作战运筹分析》谭安胜著 2009
- 《王蒙文集 新版 35 评点《红楼梦》 上》王蒙著 2020
- 《TED说话的力量 世界优秀演讲者的口才秘诀》(坦桑)阿卡什·P.卡里亚著 2019
- 《燕堂夜话》蒋忠和著 2019
- 《经久》静水边著 2019
- 《魔法销售台词》(美)埃尔默·惠勒著 2019
- 《微表情密码》(波)卡西亚·韦佐夫斯基,(波)帕特里克·韦佐夫斯基著 2019
- 《看书琐记与作文秘诀》鲁迅著 2019
- 《酒国》莫言著 2019
- 《指向核心素养 北京十一学校名师教学设计 英语 七年级 上 配人教版》周志英总主编 2019
- 《北京生态环境保护》《北京环境保护丛书》编委会编著 2018
- 《指向核心素养 北京十一学校名师教学设计 英语 九年级 上 配人教版》周志英总主编 2019
- 《抗战三部曲 国防诗歌集》蒲风著 1937
- 《高等院校旅游专业系列教材 旅游企业岗位培训系列教材 新编北京导游英语》杨昆,鄢莉,谭明华 2019
- 《中国十大出版家》王震,贺越明著 1991
- 《近代民营出版机构的英语函授教育 以“商务、中华、开明”函授学校为个案 1915年-1946年版》丁伟 2017
- 《新工业时代 世界级工业家张毓强和他的“新石头记”》秦朔 2019
- 《智能制造高技能人才培养规划丛书 ABB工业机器人虚拟仿真教程》(中国)工控帮教研组 2019
- 《陶瓷工业节能减排技术丛书 陶瓷工业节能减排与污染综合治理》罗民华著 2017