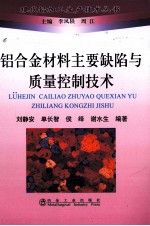
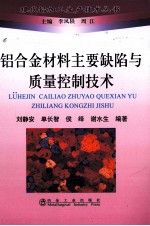
铝合金材料主要缺陷与质量控制技术PDF电子书下载
- 电子书积分:13 积分如何计算积分?
- 作 者:李凤轶,周江主编;谢水生,刘静安常务副主编;吕新宇,尹晓辉,李建荣等副主编;刘静安,单长智,侯绎等编著
- 出 版 社:北京:冶金工业出版社
- 出版年份:2012
- ISBN:9787502458461
- 页数:389 页
1概论 1
1.1铝合金加工材料的分类、品种规格、性能与用途 1
1.1.1铝及铝合金材料的分类 1
1.1.2铝及铝合金加工材料的分类及主要品种与规格 1
1.1.3铝及铝合金加工材料的性能与主要用途 6
1.2铝合金加工材料的加工成形方法与生产工艺流程 33
1.2.1铝及铝合金塑性加工成形方法的分类与特点 33
1.2.2铝及铝合金加工材料的生产工艺流程 40
1.3铝合金加工材料在塑性加工成形时的组织与性能变化 40
1.3.1热变形对铝合金加工材料组织性能的影响 40
1.3.2冷变形对铝合金加工材料组织性能的影响 47
1.4铝及铝合金加工材料生产技术现状与发展趋势 49
1.4.1铝及铝合金材料加工业进入了一个崭新的发展时代 49
1.4.2现代铝合金加工业及技术的发展特点 51
1.4.3铝加工技术的发展趋势 52
1.4.4铝合金加工材料的发展现状与研发方向 54
2铝合金加工材料的质量控制及主要缺陷检测技术 65
2.1铝合金加工材料的质量指标、废品分布及成品率 65
2.1.1铝合金加工材料的质量指标 65
2.1.2铝合金加工材料的废品(缺陷)及成品率控制 66
2.2铝合金加工材料的质量控制 74
2.2.1概述 74
2.2.2质量控制方法 74
2.3变形铝合金加工材料的主要缺陷检测技术 76
2.3.1变形铝及铝合金加工材料的显微组织检测方法 76
2.3.2变形铝及铝合金加工材料的低倍和断口组织检测方法 88
2.3.3变形铝及铝合金加工材料的超声波探伤检测方法 94
2.3.4变形铝及铝合金管材涡流探伤检测方法 98
3变形铝合金铸锭缺陷分析与质量控制 103
3.1偏析 103
3.1.1晶内偏析 103
3.1.2逆偏析 104
3.2偏析瘤 105
3.2.1偏析瘤的宏观组织特征 105
3.2.2偏析瘤显微组织特征 105
3.2.3形成机理 106
3.2.4偏析瘤防止措施 107
3.2.5偏析瘤对制品性能的影响 107
3.3缩孔 107
3.4疏松 107
3.4.1疏松的宏观组织特征 107
3.4.2疏松的显微组织特征 108
3.4.3疏松的形成机理 109
3.4.4疏松的防止措施 109
3.4.5疏松对制品性能的影响 109
3.5气孔 110
3.5.1气孔的组织特征 110
3.5.2气孔形成机理及防止措施 111
3.6夹杂 112
3.6.1非金属夹杂 112
3.6.2金属夹杂 113
3.7氧化膜 114
3.7.1宏观组织特征 114
3.7.2显微组织特征 114
3.7.3形成机理 115
3.7.4氧化膜防止措施 115
3.7.5氧化膜对制品性能的影响 116
3.8白亮点 116
3.8.1宏观组织特征 116
3.8.2显微组织特征 117
3.8.3形成机理 117
3.8.4白亮点防止措施 117
3.8.5白亮点对制品性能的影响 117
3.9白斑 117
3.9.1白斑的组织特征 117
3.9.2形成机理 118
3.9.3防止措施 118
3.9.4白斑对制品性能的影响 118
3.10光亮晶粒 119
3.10.1宏观组织特征 119
3.10.2显微组织特征 119
3.10.3形成机理 120
3.10.4防止措施 120
3.10.5光亮晶粒对制品性能的影响 120
3.11羽毛状晶 120
3.11.1羽毛状晶宏观组织特征 121
3.11.2羽毛晶显微组织特征 121
3.11.3羽毛晶形成机理 121
3.11.4羽毛晶防止措施 122
3.11.5羽毛晶对制品性能的影响 122
3.12粗大晶粒 122
3.12.1宏观组织特征 122
3.12.2显微组织特征 123
3.12.3形成机理 123
3.12.4粗大晶粒防止措施 123
3.12.5粗大晶粒对制品性能的影响 123
3.13晶层分裂 124
3.13.1宏观组织特征 124
3.13.2显微组织特征 125
3.13.3晶层分裂形成机理 125
3.13.4防止措施 125
3.13.5晶层分裂对制品性能的影响 125
3.14粗大金属化合物 126
3.14.1宏观组织特征 126
3.14.2显微组织特征 127
3.14.3形成机理 127
3.14.4防止措施 128
3.14.5粗大金属化合物对制品性能的影响 128
3.15 裂纹 128
3.15.1冷裂纹 129
3.15.2热裂纹 130
3.15.3中心裂纹 131
3.15.4环状裂纹 132
3.15.5放射状裂纹 132
3.15.6表面裂纹 133
3.15.7横向裂纹 133
3.15.8底部裂纹 133
3.15.9浇口裂纹 134
3.15.10晶间裂纹 134
3.15.11侧面裂纹 134
3.16冷隔 135
3.16.1宏观组织特征 135
3.16.2显微组织特征 135
3.16.3形成机理 135
3.16.4防止措施 136
3.16.5冷隔对制品性能的影响 136
3.17断流冷隔 136
3.18竹节 136
3.19拉痕和拉裂 137
3.19.1组织特征 137
3.19.2形成机理 137
3.19.3防止措施 137
3.19.4拉痕和拉裂对制品性能的影响 138
3.20竖道皱褶 138
3.21弯曲 139
3.21.1形成原因及防止措施 139
3.21.2对制品性能的影响 139
3.22偏心 139
3.22.1形成原因及防止措施 139
3.22.2对制品性能的影响 139
3.23尺寸不符 139
3.24周期性波纹 140
3.25枞树组织 140
3.25.1枞树组织的宏观组织特征 140
3.25.2枞树组织的显微组织特征 141
3.25.3枞树组织的形成机理 141
3.25.4枞树组织的防止措施 141
3.26表面气泡 141
3.26.1宏观组织特征 141
3.26.2显微组织特征 141
3.26.3形成机理 142
3.26.4表面气泡防止措施 143
3.26.5表面气泡对制品性能的影响 143
4铝合金管、棒、型、线材缺陷分析与质量控制 144
4.1挤压工序的主要缺陷分析及质量控制方法 144
4.1.1缩尾 144
4.1.2粗晶环 146
4.1.3成层 148
4.1.4焊合不良 149
4.1.5挤压裂纹 150
4.1.6气泡 151
4.1.7起皮 152
4.1.8划伤 152
4.1.9磕碰伤 153
4.1.10擦伤 154
4.1.11模痕 155
4.1.12扭拧、弯曲、波浪 155
4.1.13硬弯 156
4.1.14麻面(表面粗糙) 157
4.1.15 金属压入 158
4.1.16非金属压入 159
4.1.17表面腐蚀 159
4.1.18橘皮 160
4.1.19凹凸不平 161
4.1.20振纹 161
4.1.21夹杂 162
4.1.22水痕 162
4.1.23间隙(平面间隙) 163
4.1.24壁厚不均 163
4.1.25扩(并)口 164
4.1.26矫直痕 165
4.1.27停车痕、瞬间印痕、咬痕 165
4.1.28内表面擦伤 166
4.1.29力学性能不合格 167
4.1.30铝合金热挤压无缝管材(厚壁管、异形管)常见缺陷分析 167
4.2铝合金管材冷轧工序主要缺陷分析及质量控制方法 169
4.2.1压坑(或金属压入) 169
4.2.2裂口、裂纹 170
4.2.3耳子 171
4.2.4飞边 172
4.2.5内表面波浪 173
4.2.6孔型啃伤 174
4.2.7棱子 174
4.2.8横向壁厚不均 174
4.2.9纵向壁厚不均 175
4.2.10壁厚超差 176
4.2.11管材椭圆 176
4.2.12表面圆环 176
4.2.13外表面波浪 177
4.2.14表面划伤、擦伤 178
4.3铝合金管、棒、线材冷拔工序主要缺陷分析与质量控制 178
4.3.1铝合金管材冷拔时的主要缺陷分析和质量控制 179
4.3.2铝合金棒、线材冷拔工序常见的缺陷及防止方法 180
4.4铝合金管、棒、型、线材的质量检测与质量控制 181
4.4.1概述 181
4.4.2挤压工序检验与质量控制 182
4.4.3管、棒、型、线材组织性能检验取样规定与审查处理 189
4.4.4挤压材成品检查与质量控制 192
5铝合金板、带、箔材缺陷分析与质量控制 193
5.1铝合金铸轧制品缺陷分析与质量控制 193
5.1.1夹杂 193
5.1.2热带 194
5.1.3气道 195
5.1.4偏析 196
5.1.5粗大晶粒 197
5.1.6板形 198
5.1.7裂纹 200
5.1.8粘辊 201
5.1.9表面条纹 202
5.2铝合金热轧制品的缺陷分析与质量控制 203
5.2.1铝合金热轧制品的质量控制 203
5.2.2铝合金热轧工序常见缺陷与控制 206
5.3铝合金中厚板的缺陷分析与质量控制 214
5.3.1铝合金中厚板的主要缺陷分析 214
5.3.2铝合金热轧中厚板材的检验与质量控制 224
5.4铝合金冷轧板带材的缺陷分析与质量控制 234
5.4.1铝合金冷轧板带材的缺陷分析 234
5.4.2铝合金冷轧板、带材的质量控制 248
5.5铝箔的主要缺陷及质量控制 251
5.5.1铝箔的质量控制 251
5.5.2箔材主要缺陷分析 252
6铝合金锻件的缺陷分析与质量控制 262
6.1铝合金锻件缺陷分析 262
6.1.1铝合金锻件缺陷分类 262
6.1.2铝合金锻件原材料引起的锻件缺陷及控制 263
6.1.3锻造过程中缺陷的产生原因及预防措施 266
6.1.4加热及热处理类缺陷及控制 277
6.1.5其他工序产生的缺陷及控制 280
6.2铝合金锻件质量检验的内容和方法 284
6.3铝合金锻件检验及质量控制 286
6.3.1锻件设计过程中的质量控制 286
6.3.2锻造坯料的质量检验和控制 288
6.3.3备料工序检验与质量控制 290
6.3.4生产工艺编制过程的质量控制 291
6.3.5锻造前加热工序的检验与质量控制 292
6.3.6锻模的检验及质量控制 294
6.3.7锻造过程各工序的检验与质量控制 300
6.3.8模锻件切边、洗修及淬火前工序检验与质量控制 302
6.3.9热处理工序检验与质量控制 304
6.3.10组织、性能检验和取样规定及审查处理 310
6.3.11锻件成品检验与质量控制 314
6.3.12技术文件的控制 319
7铝合金加工材热处理、精整和检查工序的缺陷分析与质量控制 320
7.1常见的缺陷(废品)或问题及防止的方法 320
7.1.1热处理过程中常见的缺陷(废品)及控制方法 320
7.1.2制品精整矫直工序中常见的缺陷及防止与控制措施 326
7.1.3检查工序常出现的质量问题及控制方法 332
7.2质量控制举例(以铝合金热轧中厚板为例) 334
7.2.1中厚板热处理工序检验与质量控制 334
7.2.2中厚板精整工序检验与质量控制 336
7.2.3中厚板材成品验收工序检验与质量控制 341
7.2.4中厚板材组织性能检验取样规定与审查处理 345
7.2.5中厚板板材成品检查程序 347
8其他铝合金加工材料的缺陷分析与质量控制举例 348
8.1铝及铝基合金粉材的主要缺陷及质量控制 348
8.1.1铝及铝基合金粉材的生产工艺流程 348
8.1.2粉材废品(缺陷)分类及产生原因与控制方法 349
8.2铝及铝基合金粉材的检查与质量控制 354
8.2.1粉材的检查规则 354
8.2.2粉材取样规定 354
8.2.3粉材检测内容与方法 355
8.3铝及铝合金挤压材表面处理过程出现的缺陷分析与质量控制 359
8.3.1机械磨光、抛光处理中常出现的缺陷及控制对策 359
8.3.2铝型材化学抛光与电化学抛光处理中常见缺陷及控制对策 360
8.3.3铝型材阳极氧化着色产品的主要缺陷分析与对策 363
8.3.4电泳涂装发生的缺陷 377
8.3.5铝合金建筑型材静电粉末涂装常见缺陷及质量控制 382
8.3.6液相静电喷涂涂层常见缺陷分析及控制措施 386
参考文献 388
- 《继电保护精益化评价异常缺陷处理手册 智能变电站》国家电力调度控制中心组编 2018
- 《基于形状记忆合金的自复位抗震钢结构:材料、构件与体系》王伟 2020
- 《董事会成员特征与内部控制缺陷研究》鲁昱著 2019
- 《不同磁性合金的磁场干摩擦机理及特性》魏永辉 2019
- 《翦伯赞全集 第10卷 中外历史年表 主编》翦伯赞著 2008
- 《粘贴碳纤维复合材料改善焊接接头和含缺陷钢板的疲劳性能研究》余倩倩 2014
- 《海岸带经济与管理》朱坚真,王锋主编;徐小怡,刘汉威,何时都副主编;朱坚真,王锋,徐小怡,刘汉斌,何时都,毛小敏,秦运巧等编著;张登义,鹿守本顾问 2013
- 《茄果类蔬菜科学施肥》张菊平,赵要尊,熊法亭编著 2013
- 《工业射线检测影像识别与评定》侯若明主编 2013
- 《集成电路芯片封装技术 第2版》李可为编著 2013
- 《指向核心素养 北京十一学校名师教学设计 英语 七年级 上 配人教版》周志英总主编 2019
- 《北京生态环境保护》《北京环境保护丛书》编委会编著 2018
- 《指向核心素养 北京十一学校名师教学设计 英语 九年级 上 配人教版》周志英总主编 2019
- 《高等院校旅游专业系列教材 旅游企业岗位培训系列教材 新编北京导游英语》杨昆,鄢莉,谭明华 2019
- 《中国十大出版家》王震,贺越明著 1991
- 《近代民营出版机构的英语函授教育 以“商务、中华、开明”函授学校为个案 1915年-1946年版》丁伟 2017
- 《新工业时代 世界级工业家张毓强和他的“新石头记”》秦朔 2019
- 《智能制造高技能人才培养规划丛书 ABB工业机器人虚拟仿真教程》(中国)工控帮教研组 2019
- 《陶瓷工业节能减排技术丛书 陶瓷工业节能减排与污染综合治理》罗民华著 2017
- 《全国职业院校工业机器人技术专业规划教材 工业机器人现场编程》(中国)项万明 2019