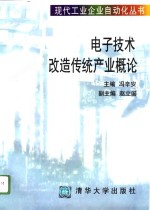
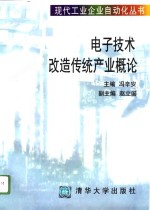
电子技术改造传统产业概论PDF电子书下载
- 电子书积分:11 积分如何计算积分?
- 作 者:冯辛安主编
- 出 版 社:北京:清华大学出版社
- 出版年份:1996
- ISBN:7302022178
- 页数:288 页
第1章 综述 1
1.1 微电子技术产生的技术背景 1
1.2 微电子技术改造传统产业 2
1.3 微电子技术改造传统产业的总体目标和基本内容 3
1.3.1 产品结构的调整和机电一体化 4
1.3.2 CAD/CAE/CAM技术的应用 5
1.3.3 对传统落后的生产装备的改造 6
1.3.4 计算机辅助管理 7
1.3.5 设计、工艺、生产与管理信息的一体化 8
1.3.6 企业职工技术素质的提高 9
1.4 微电子技术改造传统产业的指导思想 9
第2章 传感与检测技术及其应用 12
2.1 概述 12
2.1.1 传感器的定义与概念 12
2.1.2 传感器在工程领域的地位与作用 12
2.1.3 传感器在高新科技领域的应用 13
2.1.4 传感器与人们的日常生活 13
2.2 机电类传感器的基本原理与特点 14
2.2.1 传感器的分类 14
2.2.2 几何量传感器 14
2.2.3 力学量传感器 15
2.2.4 热力学传感器 18
2.2.5 光学量传感器 19
2.2.6 数字式传感器 23
2.3 变换电路与测试系统 25
2.3.1 变换电路 25
2.3.2 测试系统 26
2.4 传感器的发展与市场预测 29
2.4.1 国外传感器发展动向 29
2.4.2 国内传感器发展现状与90年代市场预测 32
第3章 电力电子技术及其应用 34
3.1 电力电子技术概述 34
3.1.1 定义 34
3.1.2 发展简史 35
3.2 电力半导体器件 36
3.2.1 二极管 36
3.2.2 晶闸管(SCR) 38
3.2.3 双极型功率晶体管(GTR) 41
3.2.4 新一代电力电子器件 42
3.3 电力电子技术应用基础线路 45
3.3.1 整流电路 46
3.3.2 晶闸管交流开关与交流调压器 49
3.3.3 直流斩波器和逆变器 50
3.4 电力电子技术与传统产业改造 53
3.4.1 概况 53
3.4.2 电力电子技术与节能 53
3.4.3 电力电子技术与节材 58
3.4.4 电力电子技术与机电一体化 60
第4章 数字控制及可编程序控制器技术 70
4.1 数控技术概述 70
4.1.1 数控技术发展历史的回顾 70
4.1.2 数控加工系统的基本组成、工作原理及特点 71
4.1.3 数控加工几种典型的分类方法 72
4.1.4 数控技术发展方向 74
4.1.5 我国数控系统及伺服系统的现状 75
4.2 数控系统主要控制软件 80
4.2.1 概述 80
4.2.2 插补运算的主要方法及其基本原理 81
4.2.3 进给速度控制 86
4.2.4 输入数据处理 86
4.3 数字控制的开环控制系统 89
4.3.1 概述 89
4.3.2 步进电机的工作原理及主要特性 89
4.3.3 步进电机的选择 91
4.3.4 步进电机的控制 92
4.3.5 步进电机的驱动电源 93
4.4 数字控制的闭环控制系统 94
4.4.1 数控系统中常用的位置检测装置 95
4.4.2 伺服电机 97
4.4.3 闭环伺服系统的几种主要形式 98
4.5 机床数控系统实例分析 101
4.5.1 机床数控改造应注意的几个问题 101
4.5.2 JWK系列数控装置 102
4.5.3 FANUC7M数控系统 108
4.6 可编程序控制器概述 112
4.6.1 概述 112
4.6.2 可编程序控制器的特点 113
4.6.3 PLC应用场合 114
4.6.4 国内外PLC的发展情况 114
4.7 PLC的基本组成及工作原理 116
4.7.1 PLC的基本组成 116
4.7.2 工作原理 117
4.7.3 PLC的结构型式 118
4.7.4 几种常用的可编程序控制器的性能 119
4.8 可编程序控制器编程方法及编程步骤 120
4.8.1 编程方法 120
4.8.2 编程步骤 121
4.9 可编程序控制器使用要点 123
4.9.1 如何选择可编程序控制器的机型 123
4.9.2 输入/输出点数量估算 123
4.9.3 内存容量的估算 124
4.9.4 抗干扰的一些措施 124
第5章 CAD/CAM一体化技术 125
5.1 概述 125
5.1.1 CAD/CAM一体化技术的定义 125
5.1.2 传统的生产过程 126
5.1.3 CAD/CAM所涉及的内容 127
5.1.4 CAD/CAM技术的产生、发展和现状 127
5.2 CAD/CAM的硬件系统 130
5.2.1 CAD/CAM硬件系统的组成与特点 130
5.2.2 计算机 131
5.2.3 图形显示系统 134
5.2.4 图形输入装置 134
5.2.5 外存储器 136
5.2.6 图形输出装置 136
5.2.7 计算机网络 137
5.2.8 CAD/CAM硬件系统正确选型的基本原则 137
5.3 CAD/CAM的支撑软件系统 139
5.3.1 CAD/CAM软件系统的分类 139
5.3.2 操作系统 139
5.3.3 数据库及其管理系统 143
5.3.4 图形支撑软件系统 145
5.3.5 CAD/CAM支撑软件系统选购要点 153
5.4 成组技术 154
5.4.1 成组技术的基本原理 154
5.4.2 零件分类成组的方法 155
5.5 CAD应用软件的开发 157
5.5.1 开发CAD应用软件应遵循的原则 157
5.5.2 参数化CAD 158
5.5.3 成组CAD 159
5.5.4 交互式CAD 160
5.5.5 智能化CAD 161
5.5.6 图形录入方法 162
5.6 计算机辅助工艺规程编制(CAPP)应用软件的开发 163
5.6.1 检索式CAPP 163
5.6.2 生成式CAPP 164
5.6.3 混合式CAPP 166
5.7 计算机辅助质量系统(CAQ) 166
5.7.1 计算机辅助质量保证(CAQA) 166
5.7.2 计算机辅助质量控制(CAQC) 168
第6章 机器人技术及其应用 170
6.1 概述 170
6.1.1 机器人的定义 170
6.1.2 机器人技术的发展 170
6.1.3 机器人应用可带来的效益 172
6.1.4 我国机器人技术的发展 172
6.2 机器人的组成与分类 173
6.2.1 机器人的组成 173
6.2.2 机器人的坐标系和自由度 173
6.2.3 机器人的分类 175
6.3 机器人的驱动和传动机构 176
6.3.1 机器人的驱动 176
6.3.2 机器人的传动机构 176
6.4 机器人的控制 177
6.4.1 “示教再现”控制方式 177
6.4.2 数字控制方式 178
6.4.3 位姿控制 178
6.4.4 力及顺应控制 179
6.4.5 自适应控制 179
6.5 机器人的传感器 180
6.5.1 机器人传感器的分类 180
6.5.2 机器人的触觉 180
6.5.3 机器人的视觉 181
6.6 机器人及其应用 182
6.6.1 毛坯生产 182
6.6.2 零件生产 183
6.6.3 处理作业 183
6.6.4 装配作业 185
6.6.5 搬运作业 186
第7章 计算机过程控制系统 188
7.1 微机过程控制技术概述 188
7.1.1 微机过程控制的基本概念 188
7.1.2 微机过程控制系统的组成 189
7.1.3 微机控制系统的分类 192
7.1.4 计算机控制系统发展简史 193
7.1.5 机电企业微机监测与控制系统的应用 194
7.2 微机控制系统设计 195
7.2.1 系统设计的基本要求 195
7.2.2 控制系统总体方案的确定 195
7.2.3 微型计算机的选择 197
7.2.4 控制算法的选用 198
7.2.5 微机控制系统的硬件设计 198
7.2.6 微机控制系统的应用软件设计 199
7.2.7 微机控制系统的调试 200
7.3 直接数字控制系统及控制规律 201
7.3.1 直接控制系统的工作原理 201
7.3.2 比例-积分-微分(PID)控制算法 202
7.3.3 专家系统在过程控制中的应用初步 203
7.3.4 模糊控制原理及其在工业中的应用 207
7.4 集散控制系统(DCS)简介 211
7.4.1 集散控制系统的概念 212
7.4.2 设计思想与特点 212
7.4.3 集散控制系统的硬件组成与功能 213
7.4.4 集散控制系统的软件 214
7.4.5 集散控制系统的通信技术 216
7.4.6 集散控制系统的发展概况 218
第8章 设备状态监测与故障诊断技术 222
8.1 概述 222
8.1.1 加强现代工业生产设备维修管理工作的重要意义 222
8.1.2 设备状态监测与故障诊断是现代维修管理制度的基础 222
8.1.3 设备状态监测与故障诊断的目的和内容 223
8.1.4 设备状态监测与故障诊断过程和方法的分类 223
8.1.5 设备状态监测与故障诊断的应用与发展 224
8.2 设备状态监测常用的基础技术 225
8.2.1 振动与噪声监测技术 225
8.2.2 超声监测技术 226
8.2.3 声发射(AE)诊断技术 228
8.2.4 红外监测技术 228
8.2.5 油污染分析监测诊断技术 228
8.2.6 功率监控技术 230
8.2.7 涡流诊断技术 230
8.3 设备状态与故障的诊断与预报 230
8.3.1 设备状态与故障的诊断方法 230
8.3.2 设备状态与故障的预报方法 232
8.4 设备状态监测与故障诊断的应用 233
8.4.1 应用的一般情况 233
8.4.2 滚动轴承的监测与诊断 234
8.4.3 齿轮故障的诊断 234
8.4.4 大型旋转机械的监测与诊断 235
第9章 计算机辅助生产管理系统 237
9.1 生产计划与管理 237
9.1.1 生产计划与管理在企业中的地位和任务 237
9.1.2 传统生产计划与管理工作存在的问题 237
9.1.3 计算机管理信息系统(MIS) 238
9.2 企业生产计划管理 240
9.2.1 企业生产计划管理的层次和内容 240
9.2.2 物料需求计划(MRP) 241
9.2.3 MRP的计算模型 244
9.2.4 多产品的MRP 246
9.2.5 MRP的批量规则 246
9.3 车间作业计划的编制与实施 247
9.3.1 车间作业管理的要求和任务 247
9.3.2 作业排序的优化 248
9.4 制造资源计划系统(MRP-Ⅱ) 249
9.4.1 从MRP到MRP-Ⅱ 249
9.4.2 RP-Ⅱ系统的典型功能组成 250
9.4.3 MRP-Ⅱ系统的软硬件配置 252
9.4.4 MRP-Ⅱ系统的实施 254
第10章 柔性自动化制造技术 256
10.1 概述 256
10.1.1 柔性自动化制造技术的基本形式 256
10.1.2 柔性自动化方案的选择 257
10.1.3 FMS的现状和各国的特点 257
10.2 柔性制造单元(FMC)和柔性制造系统(FMS) 259
10.2.1 FMC和FMS的组成 259
10.2.2 典型的柔性制造系统 260
10.2.3 面向FMC和FMS的机床的特点 262
10.2.4 工件流系统 263
10.2.5 刀具流系统 263
10.2.6 MS的信息流 266
10.2.7 作业计划管理与控制 267
10.2.8 制造过程的协调控制 267
10.2.9 加工过程监控和故障诊断 270
10.3 独立制造岛 271
10.3.1 技术构思 271
10.3.2 系统的功能和结构 273
10.3.3 生产组织原则的变革 274
10.4 计算机集成制造系统(CIMS) 275
10.4.1 CIMS的提出 275
10.4.2 CIMS的定义 276
10.4.3 CIMS的基本构成 277
10.4.4 CIMS的效益及应用对象 279
10.4.5 CIMS的实施 281
10.4.6 我国CIMS的发展策略 285
参考文献 287
- 《电子测量与仪器》人力资源和社会保障部教材办公室组织编写 2009
- 《钒产业技术及应用》高峰,彭清静,华骏主编 2019
- 《现代水泥技术发展与应用论文集》天津水泥工业设计研究院有限公司编 2019
- 《全国高等中医药行业“十三五”创新教材 中医药学概论》翟华强 2019
- 《异质性条件下技术创新最优市场结构研究 以中国高技术产业为例》千慧雄 2019
- 《Prometheus技术秘笈》百里燊 2019
- 《少儿电子琴入门教程 双色图解版》灌木文化 2019
- 《中央财政支持提升专业服务产业发展能力项目水利工程专业课程建设成果 设施农业工程技术》赵英编 2018
- 《药剂学实验操作技术》刘芳,高森主编 2019
- 《林下养蜂技术》罗文华,黄勇,刘佳霖主编 2017
- 《大学计算机实验指导及习题解答》曹成志,宋长龙 2019
- 《指向核心素养 北京十一学校名师教学设计 英语 七年级 上 配人教版》周志英总主编 2019
- 《大学生心理健康与人生发展》王琳责任编辑;(中国)肖宇 2019
- 《大学英语四级考试全真试题 标准模拟 四级》汪开虎主编 2012
- 《大学英语教学的跨文化交际视角研究与创新发展》许丽云,刘枫,尚利明著 2020
- 《北京生态环境保护》《北京环境保护丛书》编委会编著 2018
- 《复旦大学新闻学院教授学术丛书 新闻实务随想录》刘海贵 2019
- 《大学英语综合教程 1》王佃春,骆敏主编 2015
- 《大学物理简明教程 下 第2版》施卫主编 2020
- 《指向核心素养 北京十一学校名师教学设计 英语 九年级 上 配人教版》周志英总主编 2019