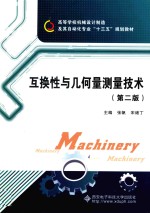
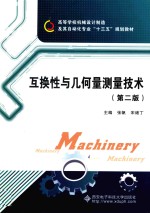
互换性与几何量测量技术 第2版PDF电子书下载
- 电子书积分:12 积分如何计算积分?
- 作 者:张帆著
- 出 版 社:西安:西安电子科技大学出版社
- 出版年份:2017
- ISBN:9787560645810
- 页数:349 页
第1章 绪论 1
1.1 本课程的研究对象、任务及基本特点 1
1.1.1 本课程的研究对象 1
1.1.2 本课程的任务 2
1.1.3 本课程的基本特点 2
1.2 互换性 3
1.2.1 互换性的概念 3
1.2.2 互换性的分类 4
1.2.3 互换性的作用 5
1.2.4 互换性的实现 6
1.3 标准化与优先数系 6
1.3.1 标准 6
1.3.2 标准化 8
1.3.3 优先数系和优先数 9
1.4 极限与配合标准以及检测技术的发展 12
1.4.1 极限与配合标准的发展概况 12
1.4.2 检测技术的发展概况 13
习题1 14
第2章 测量技术基础 15
2.1 概述 15
2.2 基准与量值传递 15
2.3 计量器具和测量方法 17
2.3.1 计量器具和测量方法的分类 17
2.3.2 计量器具和测量方法的常用术语 18
2.4 测量误差和数据处理 19
2.4.1 测量误差的基本概念 19
2.4.2 测量误差的来源 20
2.4.3 测量误差的分类和特性 21
2.4.4 测量精度 24
2.5 等精度测量列的数据处理 25
2.5.1 系统误差、随机误差和粗大误差的处理 25
2.5.2 测量列中综合误差的数据处理 28
2.6 计量器具的选择 32
2.6.1 计量器具的选择原则 32
2.6.2 光滑极限量规 32
2.6.3 光滑工件尺寸的检验 36
习题2 41
第3章 尺寸公差与圆柱结合的互换性 43
3.1 圆柱结合的使用要求 43
3.2 基本术语及定义 44
3.2.1 孔与轴的定义 44
3.2.2 有关尺寸的术语与定义 45
3.2.3 有关尺寸偏差与公差的术语和定义 46
3.2.4 有关配合的术语和定义 49
3.3 标准公差系列 54
3.3.1 标准公差因子 55
3.3.2 标准公差等级 56
3.3.3 尺寸分段 57
3.4 基本偏差系列 59
3.4.1 基本偏差代号及其特点 59
3.4.2 孔和轴的基本偏差 61
3.4.3 极限与配合的表示及其应用举例 65
3.5 圆柱结合的尺寸精度设计 69
3.5.1 极限与配合标准的适用条件 69
3.5.2 配合制的选用 70
3.5.3 标准公差等级的选用 71
3.5.4 配合的选用 73
3.5.5 线性尺寸的未注公差的选用 86
3.6 尺寸精度的检测 88
3.6.1 用通用计量器具测量 88
3.6.2 用光滑极限量规检验 95
习题3 99
第4章 形状和位置公差与检测 103
4.1 概述 103
4.1.1 零件的形位误差及其对零件使用性能的影响 103
4.1.2 形位公差的研究对象 104
4.1.3 形位公差的项目和符号 106
4.2 形位公差在图样上的表示方法 107
4.2.1 形位公差框格和基准代号 107
4.2.2 被测要素的标注方法 109
4.2.3 基准要素的标注方法 111
4.2.4 特殊表示方法 114
4.3 形位公差带 116
4.3.1 形位公差的含义和形位公差带的特征 116
4.3.2 形状公差带 118
4.3.3 轮廓度公差带 120
4.3.4 基准 121
4.3.5 定向公差带 123
4.3.6 定位公差带 128
4.3.7 跳动公差带 133
4.4 公差原则与公差要求 136
4.4.1 有关公差原则的术语及定义 137
4.4.2 独立原则 141
4.4.3 包容要求 142
4.4.4 最大实体要求 145
4.4.5 最小实体要求 153
4.4.6 可逆要求 159
4.5 形位公差的选用 163
4.5.1 形位公差特征项目的选用 163
4.5.2 公差原则和公差要求的选用 166
4.5.3 基准要素的选用 167
4.5.4 形位公差值的选用 170
4.5.5 形位公差选用和标注的实例 176
4.6 形位误差及其检测 178
4.6.1 形状误差的评定 178
4.6.2 位置误差的评定 191
4.6.3 形位误差的检测原则 199
习题4 201
第5章 表面粗糙度与检测 209
5.1 表面粗糙度的基本概念 209
5.1.1 表面粗糙度的定义 209
5.1.2 表面粗糙度对机械零件使用性能的影响 209
5.2 表面粗糙度的评定 211
5.2.1 基本术语 211
5.2.2 评定参数 213
5.3 表面粗糙度的参数值及其选用 215
5.3.1 表面粗糙度的参数值 215
5.3.2 表面粗糙度的选用 216
5.4 表面粗糙度的符号和代号及其注法 222
5.4.1 表面粗糙度的符号 222
5.4.2 表面粗糙度的代号及其注法 222
5.4.3 表面粗糙度的图样标注 225
5.5 表面粗糙度的检测 226
习题5 230
第6章 滚动轴承与孔、轴配合的互换性 232
6.1 滚动轴承的组成、分类及代号 232
6.2 滚动轴承的公差等级及其应用 236
6.2.1 滚动轴承的公差等级 236
6.2.2 滚动轴承的应用 239
6.3 滚动轴承内径与外径的公差带及其特点 239
6.3.1 滚动轴承内径和外径公差的规定(GB/T 307.1—94) 239
6.3.2 滚动轴承平均直径公差带的特点 241
6.4 滚动轴承与孔、轴结合时配合的选用 243
6.4.1 滚动轴承与轴颈、外壳孔配合的选用依据 243
6.4.2 轴颈和外壳孔几何精度的确定 246
习题6 252
第7章 螺纹结合的互换性与检测 254
7.1 螺纹结合的基本概念 254
7.1.1 螺纹的种类 254
7.1.2 螺纹结合的使用要求 254
7.1.3 普通螺纹的基本牙型及主要参数 255
7.2 影响螺纹互换性的因素 259
7.2.1 中径偏差的影响 259
7.2.2 螺距偏差的影响 260
7.2.3 牙侧角偏差的影响 261
7.2.4 螺纹作用中径和螺纹中径合格性的判断原则 263
7.3 普通螺纹公差 264
7.3.1 普通螺纹公差带 265
7.3.2 螺纹的旋合长度与公差精度等级 267
7.3.3 保证配合性质的其他技术要求 268
7.3.4 螺纹公差与配合的选用 268
7.3.5 螺纹的标记 269
7.4 普通螺纹精度的检测 271
7.4.1 单项测量 271
7.4.2 综合检验 272
习题7 273
第8章 渐开线圆柱齿轮传动的互换性与检测 275
8.1 齿轮传动的使用要求 275
8.2 影响渐开线圆柱齿轮传动质量的因素 277
8.2.1 影响传递运动准确性的因素 277
8.2.2 影响齿轮传动平稳性的因素 280
8.2.3 影响载荷分布均匀性的因素 282
8.2.4 影响齿轮副侧隙的因素 283
8.3 评定齿轮精度的偏差项目及齿轮侧隙参数 284
8.3.1 评定齿轮精度的必检偏差项目及齿轮侧隙参数 284
8.3.2 评定齿轮精度的可选用偏差项目 290
8.4 渐开线圆柱齿轮的精度标准 295
8.4.1 精度等级 295
8.4.2 齿轮各项偏差的计算公式及允许值 296
8.4.3 齿轮精度等级在图样上的标注 299
8.5 圆柱齿轮偏差的选用 300
8.5.1 齿轮精度等级的选用 300
8.5.2 最小侧隙和齿厚偏差的确定 302
8.5.3 齿轮偏差项目的确定 305
8.5.4 齿轮副和齿轮坯公差的确定 306
8.5.5 齿轮偏差选用示例 310
8.6 齿轮精度检测 314
8.6.1 齿轮径向跳动的测量 314
8.6.2 齿距的测量 314
8.6.3 齿廓偏差的测量 316
8.6.4 齿向和螺旋线偏差的测量 317
8.6.5 公法线长度的测量 318
8.6.6 齿厚的测量 318
8.6.7 单面啮合综合测量 319
8.6.8 双面啮合综合测量 320
习题8 320
第9章 尺寸链基础 322
9.1 尺寸链的基本概念 322
9.1.1 尺寸链的定义 322
9.1.2 尺寸链的构成 322
9.1.3 尺寸链的特征 324
9.1.4 尺寸链的种类 325
9.1.5 尺寸链图 326
9.1.6 尺寸链的作用 327
9.2 尺寸链的解算 328
9.2.1 极值法解尺寸链 328
9.2.2 概率法解尺寸链 336
9.2.3 尺寸链的其他解法 344
习题9 346
参考文献 348
- 《电子测量与仪器》人力资源和社会保障部教材办公室组织编写 2009
- 《钒产业技术及应用》高峰,彭清静,华骏主编 2019
- 《现代水泥技术发展与应用论文集》天津水泥工业设计研究院有限公司编 2019
- 《异质性条件下技术创新最优市场结构研究 以中国高技术产业为例》千慧雄 2019
- 《Prometheus技术秘笈》百里燊 2019
- 《中央财政支持提升专业服务产业发展能力项目水利工程专业课程建设成果 设施农业工程技术》赵英编 2018
- 《药剂学实验操作技术》刘芳,高森主编 2019
- 《林下养蜂技术》罗文华,黄勇,刘佳霖主编 2017
- 《脱硝运行技术1000问》朱国宇编 2019
- 《催化剂制备过程技术》韩勇责任编辑;(中国)张继光 2019
- 《中风偏瘫 脑萎缩 痴呆 最新治疗原则与方法》孙作东著 2004
- 《水面舰艇编队作战运筹分析》谭安胜著 2009
- 《王蒙文集 新版 35 评点《红楼梦》 上》王蒙著 2020
- 《TED说话的力量 世界优秀演讲者的口才秘诀》(坦桑)阿卡什·P.卡里亚著 2019
- 《燕堂夜话》蒋忠和著 2019
- 《经久》静水边著 2019
- 《魔法销售台词》(美)埃尔默·惠勒著 2019
- 《微表情密码》(波)卡西亚·韦佐夫斯基,(波)帕特里克·韦佐夫斯基著 2019
- 《看书琐记与作文秘诀》鲁迅著 2019
- 《酒国》莫言著 2019