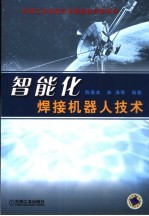
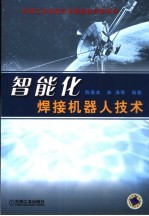
智能化焊接机器人技术PDF电子书下载
- 电子书积分:12 积分如何计算积分?
- 作 者:陈善本,林涛等编著
- 出 版 社:北京:机械工业出版社
- 出版年份:2006
- ISBN:7111180224
- 页数:303 页
第1章 绪论 1
1.1 智能机器人的技术范畴 1
1.1.1 机器人的分类 2
1.1.2 智能机器人技术的研究领域 3
1.2 焊接机器人与机器人焊接技术的发展现状 4
1.2.1 焊接机器人的分类 5
1.2.2 目前焊接机器人的特点 6
1.3 机器人焊接智能化技术范畴 7
1.4 焊接机器人智能化的主要问题 7
1.4.1 智能机器人体系结构 8
1.4.2 机器人焊接任务自主规划与离线编程 9
1.4.3 焊接机器人初始焊位视觉识别与焊缝跟踪 10
1.4.4 机器人焊接熔池动态过程的视觉传感、建模与智能控制 11
1.4.5 智能化机器人焊接柔性制造单元/系统 13
1.4.6 焊接机器人系统网络化与远程控制 14
参考文献 15
第2章 智能焊接机器人的系统构成 19
2.1 引言 19
2.2 智能焊接机器人的基本功能 19
2.3 智能焊接机器人的主要子系统功能 20
2.3.1 基于视觉传感的初始焊位识别与导引子系统 20
2.3.2 基于视觉传感的焊缝跟踪子系统 21
2.3.3 基于视觉传感的焊缝熔透实时控制子系统 22
2.3.4 焊接机器人离线编程与仿真子系统 22
2.3.5 机器人焊接知识库子系统 22
2.4 智能焊接机器人系统的分层递阶智能结构 23
2.5 智能焊接机器人系统的硬件构成 25
2.6 智能焊接机器人系统的软件构成 26
2.7 本章小结 27
参考文献 28
第3章 机器人焊接的初始焊接位置的视觉识别 29
3.1 引言 29
3.2 模板匹配法初始焊接位置的视觉识别 30
3.2.1 模板匹配的基本原理 30
3.2.2 焊缝区域的识别 32
3.2.3 动态变区域模板匹配 34
3.2.4 数字图像处理技术 37
3.2.5 初始焊接位置的确定 37
3.3 图像特征跟踪算法研究 39
3.3.1 图像特征定义及其跟踪算法研究概述 40
3.3.2 一种改进的SSD图像特征跟踪算法 43
3.3.3 图像特征跟踪算法实验 45
3.4 本章小结 46
参考文献 47
第4章 基于视觉信息的机器人焊接初始焊接位置导引 48
4.1 引言 48
4.2 基于主动单目立体视觉初始焊接位置的导引 48
4.2.1 视觉系统的标定 48
4.2.2 焊接机器人的手眼关系标定 53
4.2.3 焊接机器人的立体视觉模型 54
4.2.4 初始焊接位置的空间定位 56
4.2.5 初始焊接位置的导引 58
4.3 基于视觉伺服的初始焊接位置导引 62
4.3.1 动态估算图像雅可比矩阵的无标定视觉伺服控制方法 62
4.3.2 最大条件数法对无标定视觉伺服控制方法的改进 64
4.3.3 初始焊位导引控制算法的系统实验验证 68
4.4 本章小结 79
参考文献 79
第5章 焊接工件与焊缝曲线的视觉识别计算 81
5.1 引言 81
5.2 焊缝边缘特征提取 82
5.2.1 基于Zernike矩亚像素边缘提取的改进算法 82
5.2.2 基于Zernike矩的直线提取算法 88
5.2.3 焊缝边缘提取系统的设计 89
5.3 弧焊机器人手眼关系标定和摄像机标定 91
5.3.1 摄像机光心的标定 91
5.3.2 弧焊机器人手眼关系的标定 92
5.3.3 标定实验 93
5.4 弧焊机器人立体视觉模型分析 94
5.4.1 模型的几何原理 95
5.4.2 模型的可视范围 96
5.4.3 模型误差 98
5.5 获取焊缝空间位置信息的匹配算法 99
5.5.1 直线的整体匹配技术 99
5.5.2 基于极线的立体匹配 101
5.5.3 匹配方法 102
5.6 获取焊缝空间位置信息实验 104
5.6.1 弧焊机器人焊缝空间位置信息获取系统硬件组成 104
5.6.2 实验结果 105
5.7 本章小结 108
参考文献 109
第6章 基于视觉信息的机器人焊接的自主焊缝跟踪 110
6.1 引言 110
6.1.1 焊缝跟踪过程中使用的传感器 110
6.1.2 机器人视觉焊缝跟踪发展现状 112
6.2 机器视觉及其图像处理方法 113
6.3 LAIWR系统伺服双目视觉传感器设计 114
6.4 非起弧条件下的焊缝轨迹规划和摄像机的取像位置规划 116
6.4.1 试验装置及焊缝轨迹规划方法 116
6.4.2 焊缝图像处理的基本过程 117
6.4.3 标定和特征提取 118
6.4.4 机器人的控制策略 120
6.4.5 焊缝轨迹规划和摄像机取像角度规划的试验结果 123
6.5 起弧条件下焊缝视觉跟踪 124
6.6 本章小结 126
参考文献 126
第7章 机器人焊接过程熔池动态特征参数的提取 128
7.1 引言 128
7.2 焊接熔池动态过程视觉传感系统设计 130
7.2.1 熔池正反面视觉传感光路系统 130
7.2.2 熔池正反面同时同幅图像获取 131
7.2.3 熔池正反面典型图像 134
7.3 铝合金脉冲GTAW熔池二维视觉信息提取 134
7.3.1 熔池图像分类 135
7.3.2 铝合金GTAW熔池图像数据特征分析 136
7.3.3 非退化图像处理 136
7.3.4 退化图像复原 139
7.3.5 完整的图像处理流程 140
7.4 脉冲GTAW熔池表面三维信息提取 141
7.4.1 从阴影恢复形状方法的比较 141
7.4.2 熔池表面反射图建模 142
7.4.3 反射图方程的求解 146
7.5 熔池表面高度的计算及验证 152
7.5.1 低碳钢典型熔池表面高度计算结果及试验验证 153
7.5.2 不锈钢典型熔池表面高度计算结果及试验验证 156
7.5.3 铝合金典型熔池表面高度计算结果及试验验证 159
7.6 智能机器人铝合金脉冲GTAW过程熔池图像传感与特征参数提取 163
7.6.1 智能机器人系统中图像获取与处理 163
7.6.2 观测方向变化对熔池特征参数获取的影响 164
7.7 本章小结 165
参考文献 166
第8章 弧焊熔池动态过程的知识建模方法 167
8.1 引言 167
8.2 基于粗糙集理论的知识建模方法 168
8.2.1 知识模型的概念 168
8.2.2 粗糙集建模方法的主要步骤 169
8.2.3 粗糙集建模方法的关键算法 175
8.3 开环系统铝合金脉冲TIG焊动态过程建模 178
8.3.1 焊接知识模型的获得 178
8.3.2 焊接知识模型的验证 180
8.4 闭环系统铝合金脉冲TIG焊动态过程建模 182
8.4.1 PID控制器作用下的知识建模 182
8.4.2 最小方差自适应控制器作用下的知识建模 185
8.4.3 开环和闭环情况下的知识模型比较 187
8.5 本章小结 187
参考文献 188
第9章 机器人焊接熔池动态特征的实时控制方法 189
9.1 引言 189
9.2 焊接熔池动态过程与焊缝成形的实时控制方法 189
9.2.1 焊接熔池动态过程的模糊控制方法 189
9.2.2 焊接熔池动态过程的人工神经网络控制方法 190
9.2.3 焊接熔池动态过程的专家系统等多种控制方法结合应用 190
9.3 铝合金脉冲GTAW熔池动态过程与焊缝成形实时控制 191
9.3.1 铝合金脉冲GTAW焊接过程时变模型在线辨识 191
9.3.2 铝合金脉冲GTAW背面熔宽PID控制 192
9.3.3 铝合金脉冲GTAW焊接动态过程自适应控制 197
9.4 基于视觉传感的机器人焊接熔池与焊缝成形实时控制 205
9.4.1 基于视觉传感的机器人焊接过程控制系统 205
9.4.2 机器人焊接动态过程控制方案 208
9.4.3 机器人脉冲GTAW熔池动态过程实时控制验证试验 211
9.5 本章小结 216
参考文献 216
第10章 智能化焊接机器人系统集成与通信管理 219
10.1 引言 219
10.2 智能化焊接机器人系统集成 219
10.2.1 焊接加工过程信息流特征描述 220
10.2.2 系统集成通信的硬件实现 221
10.2.3 系统集成通信规范定义及流程 221
10.2.4 基于分级递阶结构的智能化焊接机器人系统集成 229
10.3 中央监控管理平台 229
10.4 系统集成控制实验 232
10.4.1 实验工艺条件 232
10.4.2 智能化焊接机器人初始焊接位置导引实验 232
10.4.3 智能化焊接机器人焊缝视觉自动跟踪实验 232
10.4.4 自适应神经网络——PID熔透控制实验 233
10.5 本章小结 233
参考文献 233
第11章 智能焊接机器人柔性加工系统的Petri网建模与控制 234
11.1 引言 234
11.2 柔性制造系统Petri网模型的基本概念 235
11.2.1 Petri网简介 235
11.2.2 Petri网定义 235
11.3 智能焊接机器人柔性加工单元WFMC的WAPN模型 236
11.3.1 智能焊接机器人柔性加工单元特点 236
11.3.2 WFMC自动Petri网建模 237
11.4 局部自主智能焊接机器人系统的WTCPN模型 243
11.4.1 硬件系统 243
11.4.2 系统WTCPN模型 244
11.4.3 模型性能分析 246
11.5 基于Petri网模型的WFMC和LAIWR系统的调度与控制 248
11.5.1 智能化焊接弧焊机器人单元WFMC系统模型的调度控制 248
11.5.2 局部自主智能焊接机器人系统LAIWR的调度控制 248
11.5.3 基于LAIWR为核心的三机器人PN模型及控制 250
11.6 WTCPN模型系统和MTCPN模型系统仿真 253
11.7 本章小结 254
参考文献 255
第12章 焊接柔性制造系统的多智能体协调控制 257
12.1 引言 257
12.2 多智能体系统及其协调协作技术 257
12.2.1 智能体与多智能体系统 257
12.2.2 智能体模型及多智能体系统结构 258
12.2.3 多智能体的协作 260
12.2.4 多智能体的联合意图 261
12.2.5 基于时间约束联合意图的协作模型 261
12.2.6 多智能体技术在柔性制造系统中的应用 262
12.3 基于多智能体协作技术的焊接柔性制造单元系统 262
12.3.1 焊接柔性制造单元焊接生产过程的任务描述 262
12.3.2 焊接柔性制造单元多智能体控制系统的结构 264
12.3.3 焊接柔性制造单元多智能体协作任务规划及分配过程 267
12.3.4 焊接柔性制造单元多智能体协作任务求解过程 267
12.3.5 焊接柔性制造单元多智能体监控系统的实现 269
12.4 基于多智能体系统的焊接柔性制造单元系统的实现 273
12.4.1 基于多智能体协作控制的激光焊缝跟踪控制 274
12.4.2 基于多智能体协作控制的焊接熔池熔透控制 274
12.4.3 基于多智能体协作控制的多机器人协调运动轨迹控制 276
12.5 本章小结 276
参考文献 277
第13章 基于网络的机器人焊接系统远程控制技术 279
13.1 引言 279
13.2 基于CORBA-CGI的LAIWR机器人远程控制 279
13.2.1 基于CORBA-CGI的LAIWR远程控制的原理 279
13.2.2 基于CORBA-CGI的LAIWR机器人远程控制硬件系统配置 279
13.2.3 基于CORBA-CGI的LAIWR远程控制软件系统结构及开发 281
13.3 基于CLI-IGRIP-IWRSVR的LAIWR远程控制 283
13.3.1 基于CLI-IGRIP-IWRSVR的LAIWR远程控制原理 283
13.3.2 基于CLI-IGRIP-IWRSVR的LAIWR远程控制硬件系统配置 285
13.3.3 基于CLI-IGRIP-IWRSVR的LAIWR远程控制运动通道组件开发 285
13.4 焊接机器人远程控制实验 287
13.5 远程控制方法的多机器人系统扩展 289
13.6 网络传输时延特性的分析及解决办法 291
13.6.1 延时及其不确定性产生的原因分析 291
13.6.2 减少时延和提高实时性的措施 291
13.7 两种远程控制方法的比较 292
13.8 焊接机器人远程监控管理功能 293
13.9 本章小结 293
参考文献 293
第14章 智能化焊接机器人关键技术应用实例 295
14.1 引言 295
14.2 背景和需求 295
14.3 应用实例 297
14.4 应用前景 301
参考文献 301
结束语 302
- 《智能制造高技能人才培养规划丛书 ABB工业机器人虚拟仿真教程》(中国)工控帮教研组 2019
- 《智能时代的教育智慧》魏忠著 2019
- 《全国职业院校工业机器人技术专业规划教材 工业机器人现场编程》(中国)项万明 2019
- 《STEM教育丛书 麦昆机器人和Micro:bit图形化编程》张弛责任编辑;(中国)陈宝杰,沙靓雯 2019
- 《全国职业院校工业机器人技术专业规划教材 工业机器人技术基础》(中国)陶守成,周平 2019
- 《AI智能时代》成旺坤编著 2019
- 《人工智能概论》张广渊,周风余著 2019
- 《ROS机器人编程与SLAM算法解析指南》陶满礼 2020
- 《工业机器人技术基础》甘宏波,黄玲芝主编 2019
- 《人工智能入门》范瑞峰,顾小清主编 2019
- 《断陷湖盆比较沉积学与油气储层》赵永胜等著 1996
- 《市政工程基础》杨岚编著 2009
- 《家畜百宝 猪、牛、羊、鸡的综合利用》山西省商业厅组织技术处编著 1959
- 《《道德经》200句》崇贤书院编著 2018
- 《高级英语阅读与听说教程》刘秀梅编著 2019
- 《计算机网络与通信基础》谢雨飞,田启川编著 2019
- 《看图自学吉他弹唱教程》陈飞编著 2019
- 《法语词汇认知联想记忆法》刘莲编著 2020
- 《培智学校义务教育实验教科书教师教学用书 生活适应 二年级 上》人民教育出版社,课程教材研究所,特殊教育课程教材研究中心编著 2019
- 《国家社科基金项目申报规范 技巧与案例 第3版 2020》文传浩,夏宇编著 2019
- 《指向核心素养 北京十一学校名师教学设计 英语 七年级 上 配人教版》周志英总主编 2019
- 《北京生态环境保护》《北京环境保护丛书》编委会编著 2018
- 《高等教育双机械基础课程系列教材 高等学校教材 机械设计课程设计手册 第5版》吴宗泽,罗圣国,高志,李威 2018
- 《指向核心素养 北京十一学校名师教学设计 英语 九年级 上 配人教版》周志英总主编 2019
- 《高等院校旅游专业系列教材 旅游企业岗位培训系列教材 新编北京导游英语》杨昆,鄢莉,谭明华 2019
- 《中国十大出版家》王震,贺越明著 1991
- 《近代民营出版机构的英语函授教育 以“商务、中华、开明”函授学校为个案 1915年-1946年版》丁伟 2017
- 《新工业时代 世界级工业家张毓强和他的“新石头记”》秦朔 2019
- 《智能制造高技能人才培养规划丛书 ABB工业机器人虚拟仿真教程》(中国)工控帮教研组 2019
- 《AutoCAD机械设计实例精解 2019中文版》北京兆迪科技有限公司编著 2019