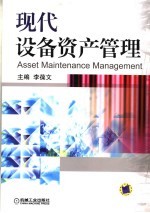
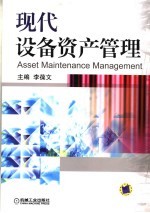
现代设备资产管理PDF电子书下载
- 电子书积分:14 积分如何计算积分?
- 作 者:李葆文主编
- 出 版 社:北京:机械工业出版社
- 出版年份:2006
- ISBN:7111184181
- 页数:439 页
目录 1
前言 1
第1章 设备管理概述 1
1.1 设备与设备管理 1
1.设备 1
2.现代设备管理 3
1.2 我国的设备管理体制 7
1.设备管理的发展历史 7
2.我国设备管理的发展 8
3.我国现行的设备管理制度 9
4.贯彻实施《“九五”全国设备管理工作纲要》 12
5.新设备管理条例修订和最新管理动态 13
1.3 设备的资产管理 14
1.固定资产 15
2.设备的分类、编号和登记 16
3.设备资产管理的基础资料 18
4.设备资产的变动管理 23
1.4 设备管理规章制度和考核指标 28
1.设备管理规章制度 28
2.设备管理中的统计工作 29
3.设备管理与维修的指标体系 30
第1章思考题 33
2.1 设备前期管理概述 34
1.设备前期管理的主要内容和总体工作程序 34
第2章 设备前期管理 34
2.设备前期管理的职责分工 35
2.2 设备的规划与选型 37
1.设备的规划 37
2.设备的选型 39
2.3 设备订货合同管理 46
1.设备前期管理中的合同谈判 47
2.合同的执行 48
2.招投标程序 50
2.4 设备招投标管理 50
1.招标的分类 50
3.组织招标机构 51
4.编制招标文件 52
2.5 设备的验收、安装调试及使用的初期管理 53
1.设备的验收 54
2.设备的安装 56
3.设备使用初期管理 58
2.6 设备前期管理案例 60
1.规划失误是最严重的浪费 60
2.博采众长,组合成线的思考 61
4.招投标程序中的问题及思考 62
3.规划选型中应注意的综合性问题 62
5.上海宝钢设备前期管理经验 63
第2章思考题 70
第3章 设备使用与维护管理 71
3.1 设备使用管理 71
1.合理使用设备的前提条件 71
2.设备使用与维护制度 74
3.设备的合理使用和性能发挥 76
3.2 设备维护管理 80
1.设备的维护保养制度 80
2.设备的区域维护 83
3.精密、大型、稀有、关键及重点设备的维护 84
4.设备维护基础工作 85
3.3 生产现场的5S/6S管理 87
1.6S的定义和宗旨 88
2.6S的具体内容 88
3.6S之间的关系 92
4.6S的实施步骤 93
5.实施6S的具体方法 94
6.5S/6S小结 96
第3章思考题 98
1.磨损原理 99
4.1 磨损 99
第4章 设备润滑管理 99
2.机械零件典型磨损过程 102
3.影响磨损的主要因素 103
4.2 润滑原理 105
1.润滑的作用 105
2.润滑的分类 106
3.润滑方式 107
4.润滑机理 108
4.3 润滑剂的分类 114
1.液体润滑剂 114
2.润滑脂 115
4.气体润滑剂 116
3.固体润滑剂 116
5.各类润滑剂的性能比较 117
4.4 润滑剂的选用 117
1.选用润滑剂应考虑的因素 117
2.润滑剂的选用原则 118
4.5 润滑管理 119
1.润滑管理的目的和内容 119
2.润滑管理目标 119
3.润滑管理机构 120
4.润滑管理的实施 120
5.制订并实施设备润滑管理制度 127
6.润滑泄漏治理 128
7.计算机辅助润滑管理 129
4.6 企业润滑管理经验介绍 130
1.精密加工机床润滑系统的监控 130
2.纺织设备的润滑管理 131
3.柴油机运行过程中的润滑管理 132
4.哈尔滨轴承集团设备润滑管理 133
5.胜利油田现河采油厂润滑管理 134
第4章思考题 136
1.备件 137
2.备件分类原则 137
5.1 备件的基本概念 137
第5章 设备备件管理 137
3.备件的储备条件 138
5.2 备件管理的定义和目的 139
1.备件管理的定义 139
2.备件管理的目的 139
3.备件管理模式选择 140
5.3 备件管理的内容 142
1.备件技术管理 142
2.备件计划管理 146
3.备件库存管理 148
4.备件经济管理 153
1.备件的ABC分类原则 156
5.4 备件的ABC管理 156
2.备件ABC管理对策 157
5.5 备件管理创新 158
1.备件的3A管理模型 158
2.备件管理创新方法 166
5.6 备件管理信息系统 169
1.备件编码 169
2.总体流程设计 172
第5章思考题 173
2.故障分类 174
1.设备故障 174
6.1 设备故障及故障分类 174
第6章 设备状态与故障管理 174
3.设备故障的原因和模式 175
6.2 设备的可靠性和故障规律 179
1.设备可靠度 179
2.设备的故障分布规律 179
6.3 设备故障统计与分析 182
1.设备故障的收集 182
2.设备故障的存储和统计 185
3.设备故障分析方法 185
6.4 设备点检管理 186
2.点检准备 187
1.点检分类和点检作业表 187
3.点检实施 188
4.点检管理 189
6.5 设备状态监测管理 195
1.积极应用状态监测技术 195
2.状态监测的主要技术和支撑 196
3.状态监测的十大手段 196
4.主要监测技术介绍 197
5.状态监测管理 202
6.6 设备诊断与分析 203
1.状态监测与诊断技术的选择 203
2.设备诊断分析方法——诊断工具箱 204
6.7 设备安全与事故管理 210
1.设备事故的分类 210
2.设备事故的分析 211
3.设备事故的处理 211
4.设备安全管理规范与流程 211
第6章思考题 215
第7章 设备维修管理 216
7.1 设备维修管理概述 216
1.目标和方针 216
2.设备维修的一般步骤 216
2.与故障特征、起因相关的维修策略 217
1.与设备役龄相关的维修策略 217
7.2 设备维修策略与模式设计 217
3.流程设备组合维修策略 218
4.维修策略优化和模式设计 222
7.3 设备维修计划 224
1.编制维修计划的基本准则 224
2.设备维修计划的制定 225
3.维修计划内容 228
4.维修计划的编制和执行 229
5.维修计划实施控制 230
2.设备维修的信息管理 231
1.设备维修现场的6S管理 231
7.4 设备维修工程管理 231
3.外委合同化维修管理 232
4.网络计划技术在设备维修中的应用 232
7.5 设备维修和修复技术简介 235
1.表面修复技术 235
2.金属腐蚀与防护涂层技术 237
3.工业清洗技术 238
4.焊接修复技术 239
5.不停车带压密封技术 239
第7章思考题 241
1.设备的磨损 242
8.1 设备的磨损与补偿 242
第8章 设备更新的技术经济分析 242
2.设备的实体性补偿与寿命 246
8.2 设备的折旧 248
1.设备折旧的意义和计提的依据 248
2.直线折旧法 249
3.加速折旧法 249
8.3 设备的大修理及其技术经济分析 251
1.设备大修理概述 251
2.设备大修理的经济评价 253
8.4 设备更新及其技术经济分析 256
1.设备更新 256
2.设备原型更新的决策方法 258
3.出现新设备条件下的更新决策方法 260
4.用设备占有总净现值确定的更新决策方法 263
8.5 设备现代化改装及其技术经济分析 264
1.设备现代化改装的概念和意义 264
2.最低总费用法 266
8.6 设备技术改造 268
1.设备技术改造的意义 268
2.设备技术改造的可能性及其基本方向 270
3.设备技术改造可行性分析 271
第8章思考题 272
1.设备维修的技术经济定额 273
第9章 设备的经济管理 273
9.1 设备维修费用的管理 273
2.维修费用的计划与管理 276
3.降低维修费用的主要途径 279
9.2 设备租赁 281
1.设备租赁的基本概念 281
2.设备租赁的分类 281
3.设备租赁的意义 281
4.设备租赁的经济性分析 282
9.3 设备管理的全面经济核算 283
1.设备管理全面经济核算的意义 283
5.设备租赁的经济核算 283
2.设备管理经济核算内容和体系 284
3.设备部门的经济核算 285
第9章思考题 288
第10章 企业动力与能源管理 289
10.1 企业动力设备管理概述 289
1.动力设备管理的重要性 289
2.动力设备管理的范围 289
3.动力设备的特点 290
4.动力设备管理的主要任务 291
10.2 动力系统的运行管理 292
1.动力设备安全运行要求 292
5.动力管理中应注意的几个关系 292
2.动力设备事故的防范和处理 293
3.动力设备的状态管理 294
10.3 动力设备的维修管理 295
1.动力设备维修的特点 295
2.动力设备维修的类别 296
3.动力设备修理的周期结构 298
4.动力设备维修定额管理 298
10.4 动力设备的经济管理 299
1.动力设备经济管理的目标 299
6.动力设备的诊断技术 299
5.动力设备维修计划的管理 299
2.动能的经济核算 300
3.动力部门经济活动分析 301
10.5 典型动力设备管理介绍 301
1.锅炉 301
2.压力容器 303
10.6 企业能源管理与节能 305
1.能源概念 306
2.能源管理 306
3.树立节约能源的思想 308
10.7 企业能源管理经验 309
1.广泛开展节能教育活动,提高员工节能意识 309
3.强化节能技术,挖潜增效 310
2.建立节能机制,强化能源管理力度 310
第10章思考题 311
第11章 设备管理的组织形式与绩效评估 312
11.1 设备管理的组织机构 312
1.设备管理组织机构的设置原则 312
2.组织管理理念 313
3.设置设备管理组织机构的影响因素 313
4.设备管理的领导体制与组织形式 314
5.组织机构形式 315
6.组织机构重组与变革 318
1.设备管理评价指标的系统思考 322
11.2 设备管理绩效评估 322
2.设备管理绩效评价指标 324
3.企业全部设备系统评价原则 327
11.3 塑造高绩效的组织 328
第11章思考题 330
第12章 设备资产管理信息系统 331
12.1 计算机辅助设备维护管理系统(CMMS) 331
1.设备综合管理的基本要点 331
2.面向企业特点和解决的问题 332
3.计算机辅助设备维护管理系统功能流程 333
4.实施过程注意环节 334
1.EAM的发展沿革 335
12.2 企业资产管理信息系统(EAM) 335
2.EAM的理论基础 337
3.EAM的构成及特点 338
4.EAM系统的实施 339
5.EAM的系统目标和经济效益预期 341
12.3 企业资产管理信息系统举例 343
1.Maximo Enterprise 343
2.HD-EAM 348
3.Datastream 7i 350
4.Insite EE 352
第12章思考题 354
1.预知维修和状态维修的定义 355
第13章 国际设备管理发展趋势 355
13.1 从预知维修到状态维修 355
2.状态维修的制度分级 356
3.状态维修技术 357
13.2 以利用率为中心的维修 357
1.定义及分类 357
2.维修规划的分析内容 358
3.维修规划编制流程 359
13.3 全面计划质量维修 360
1.全面计划质量维修 360
2.TPQM维修职能的十要素 361
3.TPQM实施过程——PDCA循环 362
13.4 适应性维修 363
1.适应性维修的定义 363
2.适应性维修的总目标 363
3.维修方式的确定流程 364
13.5 可靠性维修 366
1.可靠性维修的基本概念 366
2.从预防维修到主动维修 367
3.主动维修技术 368
4.三种维修制度的平衡 368
2.RCM的应用原理 369
13.6 以可靠性为中心的维修 369
1.以可靠性为中心的维修的基本概念 369
3.RCM管理和维修策略 371
4.RCM管理的总体框架 372
5.RCM的分析逻辑 373
6.预防维修大纲 373
13.7 风险维修 374
1.风险维修概述 374
2.风险分析 374
3.风险维修的几个重要概念 374
4.风险检查和风险维修 375
6.风险分析应用效果 376
5.维修程序 376
13.8 人的可靠性管理 377
1.SRK模型 378
2.人类失误分层模型 378
3.人的可靠性管理的重要性及要点 379
13.9 设备管理与企业文化 380
1.世界级维修的概念 380
2.设备管理的内势和外势强化功能 380
3.设备管理组织的修炼 381
13.10 设备知识资产管理 382
1.知识管理理念 382
2.资产知识管理——未来维修管理 384
3.设备知识管理流程 385
4.知识资产管理范畴 385
13.11 绿色维修——环境、安全、可持续发展 387
1.维修——基于预防的可持续性发展 387
2.联合国关于“可持续性”的定义 387
13.12 维修理论基础——热力学第二定律的应用 390
1.热力学第二定律的启示 390
2.故障过程——系统无组织过程 391
3.热力学第二定律的应用 391
第13章思考题 392
1.战后日本设备管理的发展 394
第14章 从TPM到TnPM 394
14.1 TPM管理体系 394
2.TPM给企业带来的效益 396
3.TPM定义和特点 397
4.TPM的5S活动 398
5.TPM自主维修的渐进过程 398
6.TPM的组织推进 403
7.从OEE到TEEP 406
8.TPM在世界的影响和推广 409
9.TPM的发展 409
1.从TPM到TnPM 413
14.2 TnPM管理体系 413
2.TnPM核心和要素 415
3.五个“六”架构 418
4.实施关键和推进流程 421
5.设备预防维护体系(SOON流程) 423
6.员工未来能力持续成长(FROG模型) 429
7.五阶评估体系 432
8.TnPM与其他标准化的对接 435
9.TnPM管理体系总体框架 436
10.TnPM推进八大忌 437
第14章思考题 438
参考文献 439
- 《管理信息系统习题集》郭晓军 2016
- 《MBA大师.2020年MBAMPAMPAcc管理类联考专用辅导教材 数学考点精讲》(中国)董璞 2019
- 《信息系统安全技术管理策略 信息安全经济学视角》赵柳榕著 2020
- 《卓有成效的管理者 中英文双语版》(美)彼得·德鲁克许是祥译;那国毅审校 2019
- 《危险化学品经营单位主要负责人和安全生产管理人员安全培训教材》李隆庭,徐一星主编 2012
- 《管理运筹学》韩伯棠主编 2019
- 《ESG指标管理与信息披露指南》管竹笋,林波,代奕波主编 2019
- 《战略情报 情报人员、管理者和用户手册》(澳)唐·麦克道尔(Don McDowell)著 2019
- 《穿越数据的迷宫 数据管理执行指南》Laura Sebastian-Coleman 2020
- 《风险管理与保险》(中国)粟芳 2019
- 《指向核心素养 北京十一学校名师教学设计 英语 七年级 上 配人教版》周志英总主编 2019
- 《北京生态环境保护》《北京环境保护丛书》编委会编著 2018
- 《高等教育双机械基础课程系列教材 高等学校教材 机械设计课程设计手册 第5版》吴宗泽,罗圣国,高志,李威 2018
- 《指向核心素养 北京十一学校名师教学设计 英语 九年级 上 配人教版》周志英总主编 2019
- 《高等院校旅游专业系列教材 旅游企业岗位培训系列教材 新编北京导游英语》杨昆,鄢莉,谭明华 2019
- 《中国十大出版家》王震,贺越明著 1991
- 《近代民营出版机构的英语函授教育 以“商务、中华、开明”函授学校为个案 1915年-1946年版》丁伟 2017
- 《新工业时代 世界级工业家张毓强和他的“新石头记”》秦朔 2019
- 《智能制造高技能人才培养规划丛书 ABB工业机器人虚拟仿真教程》(中国)工控帮教研组 2019
- 《AutoCAD机械设计实例精解 2019中文版》北京兆迪科技有限公司编著 2019