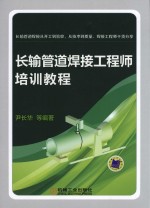
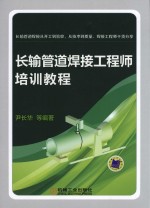
长输管道焊接工程师培训教程PDF电子书下载
- 电子书积分:11 积分如何计算积分?
- 作 者:尹长华编著
- 出 版 社:北京:机械工业出版社
- 出版年份:2016
- ISBN:7111548621
- 页数:254 页
第一章 长输管道施工工艺简介 1
第一节 长输管道施工工艺流程 1
第二节 施工准备 2
一、公共关系准备 2
二、人员准备 3
三、设备及物资准备 3
四、编制施工进度计划及对施工任务进行划分 3
五、技术准备 4
六、对施工地区的自然状况进行调查 4
七、营地建设 4
第三节 测量放线及作业带清理 5
一、接桩 5
二、补桩 5
三、测量放线及设立标志桩 5
四、移桩 6
五、施工作业带的清理 6
六、施工便道的修筑 6
第四节 管道的组装焊接 7
一、布管 7
二、钢管的组装 7
三、钢管的焊接 7
四、表面的清理及外观检查 8
五、焊接接头的无损检测 9
六、焊缝的返修 9
第五节 管道的防腐补口 9
一、金属腐蚀的基本原理和分类 9
二、埋地管道的腐蚀 10
三、防腐前对钢管表面的处理 10
四、管道防腐的常用涂料 11
五、防腐涂层的主要特性 11
六、管道防腐补口的一般步骤 11
七、管道防腐的一般要求 11
第六节 管沟的开挖、管道的下沟回填及地貌恢复 12
一、管沟的开挖 12
二、管道的下沟 12
三、管道的回填及地貌的恢复 12
第七节 压力试验及通球扫线 12
一、压力试验 12
二、通球扫线 13
第二章 长输管道焊接方法与技术 14
第一节 长输管道工程常用焊接方法 14
一、焊条电弧焊 15
二、手工钨极氩弧焊 17
三、自保护药芯焊丝半自动焊 18
四、STT技术气体保护实心焊丝半自动焊 20
五、CMT技术熔化极气体保护半自动焊 21
六、RMD技术熔化极气体保护半自动焊 22
七、管道自动焊 23
第二节 未来长输管道焊接技术展望 31
一、自保护药芯焊丝自动焊技术 31
二、单弧双丝焊接技术 32
三、激光/电弧复合焊技术 34
四、多焊嘴自动焊外焊技术 35
五、管道视觉焊接系统 36
六、搅拌摩擦焊技术 38
七、其他焊接技术 40
第三章 长输管道工程用材料 42
第一节 管道用材 42
一、管道工程的发展趋势及其对管线钢的要求 42
二、管线用钢 43
三、管线钢的发展趋势 47
四、管道工程常用材料 49
第二节 焊接材料 52
一、焊接材料分类 52
二、管道常用焊接材料 52
三、焊接材料牌号、型号 57
四、焊接材料质量管理 67
五、长输管道用焊接材料选用原则 70
第四章 管线钢焊接性分析 74
第一节 焊接性的概念 74
第二节 管线钢焊接性分析方法 75
一、利用管线钢的化学成分分析 75
二、利用管线钢的CCT图或SHCCT图分析 79
三、利用最高硬度HVmax公式法进行分析 81
四、利用管线钢焊接性试验方法分析 82
第三节 典型焊接性试验方法介绍 84
一、斜Y形坡口焊接裂纹试验法 84
二、插销试验 86
三、焊接热模拟试验 88
四、横向可调拘束裂纹试验法 89
五、微型剪切试验法 90
六、压板对接(FISCO)焊接裂纹试验法 92
七、焊接热影响区最高硬度试验法 93
八、其他焊接性试验方法 94
第四节 管线钢的焊接性问题表征 95
一、焊缝中的气孔 95
二、夹杂 97
三、热裂纹 98
四、冷裂纹 102
五、再热裂纹 104
六、应力腐蚀裂纹 105
七、氢致裂纹 106
八、焊接热影响区的性能变化 108
第五章 长输管道工程焊接工艺及工艺评定 112
第一节 国内外长输管道工程常用焊接工艺 112
第二节 长输管道环焊接头焊接工艺评定 122
一、焊接工艺评定的目的及要求 122
二、焊接工艺评定程序 122
三、焊接作业工艺文件编制 126
第三节 长输管道工程焊接工艺评定执行标准 127
第四节 国内外长输管道焊接施工及验收标准对比分析 128
第六章 长输管道工程焊工培训考试及管理 141
第一节 焊工培训 141
一、学历教育 141
二、对焊接专业毕业生的培训 141
三、对社会青年的焊工培训 144
四、对在职焊工的培训 147
第二节 焊工考试 149
一、焊工等级证考试 149
二、焊工安全证考试 150
三、焊工资格证考试 150
四、焊工上岗证考试 161
第三节 焊工管理 165
一、焊工资格证管理 165
二、焊工档案管理 165
第七章 长输管道工程常见缺陷成因及控制 167
第一节 焊接缺陷的危害 167
第二节 常见缺陷的成因及控制 167
一、裂纹 167
二、未焊透 169
三、边缘及层间未熔合 170
四、夹渣 170
五、气孔 171
六、咬边 172
七、背面凹陷(内凹) 173
八、焊瘤 173
九、弧坑 173
十、电弧擦伤 174
十一、焊缝尺寸不符合要求 174
十二、夹钨 175
十三、烧穿 175
十四、飞溅 175
第八章 长输管道工程焊接质量检验 177
第一节 焊缝外观及尺寸检验 177
一、焊缝的目视检验 177
二、对接焊缝尺寸的检验 178
第二节 管道的射线检测 179
一、射线检测的基本原理及特点 179
二、通用射线检测设备 180
三、管道爬行器 181
四、射线照相法 183
第三节 管道的超声波检测 189
一、超声波的发生及其性质 189
二、超声波探头的种类 191
三、试块 192
四、超声波检测原理 194
五、超声波检测方法的分类 195
六、检测仪的调节 197
七、缺陷位置的测定 197
八、缺陷大小的测定 199
九、中厚板对接焊缝超声波检测 200
十、管道的全自动超声波检测(AUT) 201
第四节 焊缝的强度和严密性试验 206
一、一般规定 206
二、清管、测径 207
三、水压试验 207
四、气压试验 208
第五节 环焊接头破坏性试验 209
一、焊接接头抗应力腐蚀(SSC)试验 209
二、焊接接头抗氢致裂纹(HIC)试验 210
第九章 射线照相底片评定 213
第一节 评片工作的基本要求 213
一、底片质量要求 213
二、环境设备条件要求 215
三、评片人员要求 216
第二节 底片影像分析 216
一、焊接缺陷影像 217
二、常见伪缺陷影像及识别方法 218
三、表面几何影像的识别 219
四、底片影像分析要点 220
第三节 焊接接头的质量等级评定 222
一、质量分级规定 222
二、射线照相检验记录与报告 223
第四节 典型缺陷的射线底片影像 223
第十章 长输管道工程现场焊接质量控制 231
第一节 焊接质量控制体系文件的建立与实施 231
一、焊接质量控制体系文件建立要求 231
二、焊接质量控制体系文件构建 232
第二节 现场焊接质量控制 235
一、焊接工艺评定及焊接工艺规程 236
二、施工组织设计(施工方案)中焊接质量控制 237
三、现场焊接质量控制人员、设备的管理 237
四、现场焊接材料的管理 238
五、焊工上岗资格管理 240
六、焊接技术交底 240
七、现场焊接过程控制 241
八、焊后质量检查 242
第三节 现场焊接质量控制资料构建 243
一、资料整理的完整性 243
二、记录填写的符合性 244
三、资料生成的真实性 244
四、焊接质量控制交工资料 245
附录 246
附录A 焊接工艺评定报告参考范例 246
附录B 焊接工艺规程参考范例 250
参考文献 254
- 《市政工程基础》杨岚编著 2009
- 《高级英语阅读与听说教程》刘秀梅编著 2019
- 《看图自学吉他弹唱教程》陈飞编著 2019
- 《激光加工实训技能指导理实一体化教程 下》王秀军,徐永红主编;刘波,刘克生副主编 2017
- 《AutoCAD 2019 循序渐进教程》雷焕平,吴昌松,陈兴奎主编 2019
- 《少儿电子琴入门教程 双色图解版》灌木文化 2019
- 《工程静力学》王科盛主编 2019
- 《中央财政支持提升专业服务产业发展能力项目水利工程专业课程建设成果 设施农业工程技术》赵英编 2018
- 《Photoshop CC 2018基础教程》温培利,付华编著 2019
- 《剑桥国际英语写作教程 段落写作》(美)吉尔·辛格尔顿(Jill Shingleton)编著 2019
- 《市政工程基础》杨岚编著 2009
- 《家畜百宝 猪、牛、羊、鸡的综合利用》山西省商业厅组织技术处编著 1959
- 《《道德经》200句》崇贤书院编著 2018
- 《高级英语阅读与听说教程》刘秀梅编著 2019
- 《计算机网络与通信基础》谢雨飞,田启川编著 2019
- 《看图自学吉他弹唱教程》陈飞编著 2019
- 《法语词汇认知联想记忆法》刘莲编著 2020
- 《培智学校义务教育实验教科书教师教学用书 生活适应 二年级 上》人民教育出版社,课程教材研究所,特殊教育课程教材研究中心编著 2019
- 《国家社科基金项目申报规范 技巧与案例 第3版 2020》文传浩,夏宇编著 2019
- 《流体力学》张扬军,彭杰,诸葛伟林编著 2019
- 《指向核心素养 北京十一学校名师教学设计 英语 七年级 上 配人教版》周志英总主编 2019
- 《北京生态环境保护》《北京环境保护丛书》编委会编著 2018
- 《高等教育双机械基础课程系列教材 高等学校教材 机械设计课程设计手册 第5版》吴宗泽,罗圣国,高志,李威 2018
- 《指向核心素养 北京十一学校名师教学设计 英语 九年级 上 配人教版》周志英总主编 2019
- 《高等院校旅游专业系列教材 旅游企业岗位培训系列教材 新编北京导游英语》杨昆,鄢莉,谭明华 2019
- 《中国十大出版家》王震,贺越明著 1991
- 《近代民营出版机构的英语函授教育 以“商务、中华、开明”函授学校为个案 1915年-1946年版》丁伟 2017
- 《新工业时代 世界级工业家张毓强和他的“新石头记”》秦朔 2019
- 《智能制造高技能人才培养规划丛书 ABB工业机器人虚拟仿真教程》(中国)工控帮教研组 2019
- 《AutoCAD机械设计实例精解 2019中文版》北京兆迪科技有限公司编著 2019