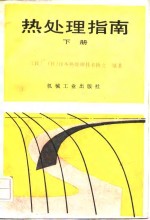
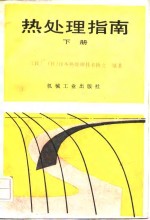
热处理指南 下PDF电子书下载
- 电子书积分:12 积分如何计算积分?
- 作 者:日本热处理技术协会编著;刘文泉等译
- 出 版 社:北京:机械工业出版社
- 出版年份:1987
- ISBN:15033·6573
- 页数:309 页
目录 1
1 钢材的强度和热处理 3
1.1 钢材的强度及其强化方法 3
(1)何谓钢材的强度 3
(2)使钢材进一步强化的方法 6
1.2 钢材的固溶强化 7
1.3 钢材的晶粒细化强化 9
(1)霍尔-佩奇关系 9
(2)细化铁素体晶粒的方法 10
1)细化相变前的奥氏体晶粒 10
2)增大铁素体晶粒的形核率 10
1.4 钢材的相变强化 11
(1)正火强化 11
3)阻止铁素体晶粒的长大 11
(2)淬火回火强化 12
1)保证钢完全淬火的两种方法 12
2)理想临界直径表示钢材的淬透性 14
3)两相区淬火可获得优异的韧性 16
1.5 析出强化和弥散强化 16
1.6 钢材的冷加工强化 19
(1)冷加工为什么能使钢材强化 19
(2)积极利用冷加工强化的实例 19
1)奥氏体型不锈钢 19
2)高锰钢 19
3)琴钢丝 20
(3)冷加工可以提高疲劳强度 21
1.7 钢材的形变热处理强化 21
(2)过冷奥氏体形变热处理强化 22
(1)在稳定奥氏体区进行的形变热处理 22
(3)马氏体时效钢的形变热处理 23
(4)马氏体相变过程中的形变 23
(5)铁素体-珠光体相变过程中的形变 23
(6)珠光体的形变强化 24
(7)控制轧制-控制冷却强化 24
1.8 钢材的可强化限度 27
1.9 在钢材选择和热处理上需要特别注意的问题 29
(1)钢材的不均匀性 29
(2)钢件的质量效应 29
(3)时效 31
(4)低温特性 31
(5)高温特性 32
(1)软钢与机器结构用钢 33
1.10 机器结构用钢的强度和热处理 33
(2)机器结构用碳素钢 35
(3)机器结构用合金钢 37
(4)渗碳钢 39
(5)渗氮钢 40
1.11 其他结构用钢的强度和热处理 42
(1)焊接结构用高强度钢 42
1)50kgf/mm2级钢 42
2)60kgf/mm2级钢 43
3)70~100kgf/mm2级钢 45
(2)耐大气腐蚀用钢 46
(3)低温压力容器用钢 46
(4)中常温压力容器用钢 47
(5)高温压力容器用钢 49
(6)超高强度钢 51
1.12 特殊用途钢的强度和热处理 53
(1)轴承钢 53
(2)弹簧钢 54
(3)工具钢 54
1)碳素工具钢 54
2)合金工具钢 55
3)高速钢 56
4)高锰钢 58
1.13 不锈钢的强度和热处理 59
(1)马氏体型不锈钢 59
(2)铁素体型不锈钢 61
(4)奥氏体-铁素体型不锈钢 62
(3)奥氏体型不锈钢 62
(5)析出硬化型不锈钢 63
1.14 耐热钢的强度和热处理 64
钢材的韧性和热处理 67
2.1 何谓韧性 67
(1)影响韧性的各种因素 67
(2)断裂韧性值 67
2.2 退火、正火改善韧性 71
2.3 淬火回火提高韧性 72
(1)淬火温度的影响 72
(2)淬火冷却速度的影响 74
(3)回火温度的影响 77
(4)淬火时效造成的脆化 78
2.4 低温回火脆性造成的韧性降低 79
(1)化学成分的影响 80
2.5 高温回火脆性造成的韧性降低 80
(2)组织、强度的影响 83
(3)回火冷却速度的影响 83
(4)回火脆性的机理 86
(5)预防回火脆性的措施 87
(6)与回火脆性有关的几个问题 88
2.6 晶粒度对韧性的影响 89
2.7 组织对韧性的影响 93
2.8 合金元素对韧性的影响 98
(1)含碳量的影响 98
(2)含锰量的影响 100
(3)含硅量的影响 101
(4)含镍量的影响 101
(6)含钼量的影响 102
(5)含铬量的影响 102
(7)磷、硫的影响 103
(8)杂质元素的影响 103
2.9 冷、热加工和韧性 104
(1)热加工引起的韧性提高 104
(2)冷加工引起的韧性降低 105
(3)加工各向异性引起的韧性降低 106
2.10 工具钢的韧性和热处理 106
(1)基体的韧性 107
(2)回火和残余奥氏体的影响 107
(3)碳化物的影响 110
2.11 特殊热处理和钢的韧性 110
(1)控制轧制改善韧性 110
(2)铁素体-奥氏体两相区淬火改善韧性 113
(3)等温淬火、形变热处理改善韧性 114
(4)消除应力退火引起的韧性降低 116
(5)长时间加热引起的韧性降低 118
(6)环境脆化和热处理 119
2.12 渗碳钢的韧性和热处理 120
(1)渗碳层的韧性 120
(2)合金元素对渗碳层韧性的影响 121
(3)通过急热处理法改善渗碳层的韧性 122
2.13 渗氮钢的韧性和热处理 123
2.14 高频淬火、火焰淬火和韧性 123
3 耐疲劳性和热处理 126
3.1 普通热处理和耐疲劳性 126
(1)普通热处理的残余应力对耐疲劳性的影响较小 126
(2)非金属夹杂物降低材料的疲劳强度 126
(3)疲劳强度随零件尺寸的增大而降低 128
(4)缺口降低零件的疲劳强度 129
3.2 高频淬火和耐疲劳性 130
(1)残余应力产生的机理 131
(2)可以同时提高表面硬度和疲劳强度 132
(3)残余应力可以抑制裂纹的扩展 134
(4)高频淬火有最适宜的淬火条件 136
(5)电力机车驱动齿轮的试验实例 138
3.3 渗碳硬化和渗氮处理与耐疲劳性 143
(1)应力梯度各有特征 143
(2)残余应力分布的类型与高频淬火相同 144
(3)渗碳层深度要适当 145
(4)渗氮不能大幅度提高疲劳强度 146
4.1 用热处理方法改善耐磨性的三项基本事项 151
(1)尽量减小摩擦面上的残余应力 151
4 耐磨性和热处理 151
(2)硬度是改善耐磨性的重要因素 153
(3)在摩擦面上形成非金属覆膜可以提高耐磨性 155
4.2 残余应力和耐磨性 156
(1)在强韧铸铁中存在有残余加工应力 157
(2)要消除铸造应力可在550℃以上退火 157
(3)为了改善耐磨性也可在500℃左右退火 159
(4)回火处理时残余应力的松弛 162
4.3 铸铁的淬火硬化和耐磨性 163
(1)含钛共晶石墨铸铁有一个最佳回火温度 163
(2)分级淬火的合金铸铁具有优异的耐磨性 167
4.4 利用淬火硬化提高耐磨性的方法 169
(1)渗碳、碳氮共渗时应选择较低的淬火温度 169
(2)高频淬火有一个最佳回火温度 172
(1)渗硼处理时单相Fe2B具有优异的耐磨性 177
4.5 利用非金属硬化层提高耐磨性的方法 177
(2)碳化物被覆处理和耐磨性 182
1)各种碳化物的硬度 183
2)熔盐法碳化物扩散渗透处理 183
3)利用化学气相沉积法(CVD法)可获得1.5 μm以上的碳化物覆层 184
4)利用物理气相沉积法(PVD法)进行碳化物被覆处理时工模具的变形很小 185
(3)渗氮处理的耐磨性取决于表面硬度和对粘着的抑制作用 188
4.6 利用非金属化合物层抑制粘着作用的表面处理方法 192
(1)加氧渗氮处理有抑制粘定和熔着的作用 192
(2)碳氮氧共渗处理优于气体软氮化和盐浴渗氮吗? 197
(3)渗硫和硫氮共渗处理 199
1)电解渗硫处理在渗碳硬化后特别有效 200
2)硫氮共渗处理能抵抗严重的摩擦条件 202
(4)提高耐磨性的氧化处理只需处理两摩擦面中的一方 210
4.7 贝氏体钢板的耐磨性 214
4.8 结束语 218
5 耐蚀性和热处理 223
5.1 不锈钢的种类和热处理 223
5.2 不锈钢的耐蚀性和热处理 225
(1)马氏体型不锈钢 226
(2)铁素体型不锈钢 226
(3)奥氏体型不锈钢 228
(4)奥氏体-铁素体型复相不锈钢 228
5.3 局部腐蚀和热处理 228
(1)晶间腐蚀 229
(2)点腐蚀及其预防措施 234
5.4 应力腐蚀开裂和热处理 237
5.5 镍基合金 241
(1)何谓延滞断裂 245
6.1 延滞断裂现象 245
6 延滞断裂和热处理 245
(2)腐蚀反应和延滞断裂机理 246
6.2 延滞断裂的试验方法 248
6.3 热处理对低合金钢延滞断裂特性的影响 251
(1)回火温度的影响 251
(2)奥氏体晶粒度的影响 254
(3)等温转变处理的影响 255
(4)脱碳和渗碳的影响 256
6.4 工业上的延滞断裂现象和预防措施 258
(1)高强度螺栓的延滞断裂 258
(2)超高强度钢的延滞断裂 261
(3)焊区延滞断裂 262
(4)钢的氢致开裂和硫化物腐蚀开裂 264
(1)疲劳试验方法 267
7 材料试验和检验 267
7.1 疲劳试验 267
(2)疲劳极限和抗拉强度 270
7.2 磨损试验 271
(1)什么是磨损 271
(2)磨损试验机 273
(3)磨损量的测量方法 276
(4)根据失重求磨损量的方法 280
(5)根据磨痕大小求磨损量的方法 282
(6)测量磨损量的其他方法 282
(7)精确磨损量的求法 283
7.3 组织试验 287
(1)宏观组织试验 287
(2)利用金属显微镜进行的组织试验 288
7.4 物理试验 289
(1)特征X射线 290
(2)EPMA 291
(3)电子显微镜 294
(4)X射线衍射 295
(5)应力测定法 296
7.5 无损检验 296
(1)渗透探伤试验 296
(2)磁粉探伤试验 297
(3)其他无损检验法 297
7.6 其他试验和检验 297
(1)现场的试验和检验 297
(2)其他试验和检验 302
索引 304
- 《钒产业技术及应用》高峰,彭清静,华骏主编 2019
- 《近代旅游指南汇刊二编 16》王强主编 2017
- 《现代水泥技术发展与应用论文集》天津水泥工业设计研究院有限公司编 2019
- 《异质性条件下技术创新最优市场结构研究 以中国高技术产业为例》千慧雄 2019
- 《甘肃省档案馆指南》甘肃省档案馆编 2018
- 《Prometheus技术秘笈》百里燊 2019
- 《中央财政支持提升专业服务产业发展能力项目水利工程专业课程建设成果 设施农业工程技术》赵英编 2018
- 《药剂学实验操作技术》刘芳,高森主编 2019
- 《林下养蜂技术》罗文华,黄勇,刘佳霖主编 2017
- 《脱硝运行技术1000问》朱国宇编 2019
- 《家畜百宝 猪、牛、羊、鸡的综合利用》山西省商业厅组织技术处编著 1959
- 《市政工程基础》杨岚编著 2009
- 《《道德经》200句》崇贤书院编著 2018
- 《高级英语阅读与听说教程》刘秀梅编著 2019
- 《计算机网络与通信基础》谢雨飞,田启川编著 2019
- 《看图自学吉他弹唱教程》陈飞编著 2019
- 《法语词汇认知联想记忆法》刘莲编著 2020
- 《培智学校义务教育实验教科书教师教学用书 生活适应 二年级 上》人民教育出版社,课程教材研究所,特殊教育课程教材研究中心编著 2019
- 《国家社科基金项目申报规范 技巧与案例 第3版 2020》文传浩,夏宇编著 2019
- 《流体力学》张扬军,彭杰,诸葛伟林编著 2019
- 《指向核心素养 北京十一学校名师教学设计 英语 七年级 上 配人教版》周志英总主编 2019
- 《北京生态环境保护》《北京环境保护丛书》编委会编著 2018
- 《高等教育双机械基础课程系列教材 高等学校教材 机械设计课程设计手册 第5版》吴宗泽,罗圣国,高志,李威 2018
- 《指向核心素养 北京十一学校名师教学设计 英语 九年级 上 配人教版》周志英总主编 2019
- 《高等院校旅游专业系列教材 旅游企业岗位培训系列教材 新编北京导游英语》杨昆,鄢莉,谭明华 2019
- 《中国十大出版家》王震,贺越明著 1991
- 《近代民营出版机构的英语函授教育 以“商务、中华、开明”函授学校为个案 1915年-1946年版》丁伟 2017
- 《新工业时代 世界级工业家张毓强和他的“新石头记”》秦朔 2019
- 《智能制造高技能人才培养规划丛书 ABB工业机器人虚拟仿真教程》(中国)工控帮教研组 2019
- 《AutoCAD机械设计实例精解 2019中文版》北京兆迪科技有限公司编著 2019