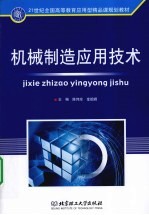
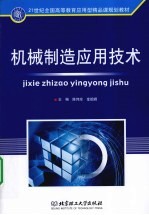
机械制造应用技术PDF电子书下载
- 电子书积分:11 积分如何计算积分?
- 作 者:陈伟珍,金祖峰主编
- 出 版 社:北京:北京理工大学出版社
- 出版年份:2009
- ISBN:9787564026202
- 页数:272 页
任务一 认识机床 1
1.1 项目任务书 1
1.2 机械制造技术的相关知识 2
1.2.1 机械制造业的地位和作用 2
1.2.2 机械制造业的发展方向 2
1.2.3 本课程的主要内容及学习要求 2
1.3 金属切削机床分类及型号 3
1.3.1 机床的分类 3
1.3.2 机床型号的组成 4
1.4 金属切削原理 5
1.4.1 工件表面的成形方法 5
1.4.2 切削运动 7
1.4.3 工件表面 8
1.4.4 切屑的形成与积屑瘤 8
1.4.5 切削力和切削功率 10
1.4.6 切削热和切削温度 12
1.5 拓展知识——传动系统 13
1.5.1 机床传动系统的组成 13
1.5.2 机床传动原理 13
1.5.3 传动系统分析 14
任务二 夹具的使用、拆装和设计 16
2.1 项目任务书 16
2.2 机床夹具的作用、组成 16
2.2.1 机床夹具的作用 17
2.2.2 机床夹具的组成 17
2.2.3 机床夹具的分类 18
2.3 基准及工件的安装方式 19
2.3.1 定位基准选择的原则 19
2.3.2 安装方式 21
2.4 工件的定位和定位元件 22
2.4.1 概述 22
2.4.2 六点定位原理 22
2.4.3 工件定位的几种情况 23
2.4.4 常用定位元件 24
2.4.5 常用定位元件及其限制的自由度 25
2.4.6 定位元件的应用 27
2.5 定位误差的分析与计算 31
2.5.1 加工误差的组成 31
2.5.2 定位误差产生的原因 32
2.5.3 定位误差的计算 33
2.5.4 定位误差的计算实例 34
2.6 夹紧装置及夹具动力装置 36
2.6.1 夹紧装置组成 36
2.6.2 常见夹紧机构 37
2.6.3 夹紧力的确定 40
2.6.4 夹具动力装置 41
2.7 夹具设计 43
2.7.1 夹具设计的方法和步骤 43
2.7.2 专用夹具设计实例 44
2.8 拓展知识——数控机床夹具 46
任务三 轴类零件的加工 49
3.1 项目任务书 49
3.2 轴类零件加工的相关知识 50
3.2.1 轴类零件的功用和结构特点 50
3.2.2 轴类零件的技术要求 52
3.2.3 轴类零件的材料、毛坯及热处理 53
3.3 车削加工方法及装备 55
3.3.1 车床 55
3.3.2 常用的装夹方式 68
3.4 外圆表面其他常用加工方法及装备 70
3.4.1 外圆表面磨削加工 70
3.4.2 外圆表面精密加工 80
3.5 机械加工基础 84
3.5.1 生产过程与工艺过程 84
3.5.2 生产类型及工艺特点 86
3.5.3 工艺规程的制定 88
3.5.4 工艺规程的编制 91
3.5.5 加工余量及工序尺寸的确定 94
3.5.6 时间定额的确定 96
3.5.7 工艺过程的技术经济分析 97
3.6 轴类零件加工实践 99
3.6.1 确定加工方案、选择加工设备及工装设备 99
3.6.2 划分加工阶段 101
3.6.3 制定加工工艺过程 101
3.7 拓展知识——车圆锥面 103
任务四 零件加工质量的分析与检测 105
4.1 项目任务书 105
4.2 精度测量的相关知识 106
4.2.1 尺寸测量的方法 106
4.2.2 形位误差检测的方法 109
4.2.3 表面粗糙度测量的方法 110
4.3 加工误差分析 111
4.3.1 加工误差种类 111
4.3.2 加工误差的统计分析法 112
4.3.3 加工精度的概念 117
4.3.4 加工精度获得的方法 118
4.3.5 影响机械加工精度的因素 119
4.3.6 提高加工精度的途径 133
4.3.7 机械加工表面质量 135
4.4 拓展知识——无损探伤 141
任务五 套筒类零件的加工 143
5.1 项目任务书 143
5.2 套筒类零件加工的相关知识 144
5.2.1 套筒类零件的功用和结构特点 144
5.2.2 套筒类零件的技术要求 144
5.2.3 套筒类零件的材料、毛坯及热处理 145
5.3 内孔表面常用的加工方法及装备 145
5.3.1 内孔表面钻削加工 145
5.3.2 内孔表面镗削加工 149
5.3.3 内孔表面拉削加工 153
5.3.4 内孔表面的精密加工 154
5.4 常用的装夹方式 156
5.4.1 套筒类零件常用的装夹方式 156
5.4.2 钻床夹具的分类及其结构形式 158
5.4.3 钻床夹具设计要点 160
5.5 工艺尺寸链计算 164
5.5.1 尺寸链定义和组成 164
5.5.2 尺寸链的计算方法 165
5.5.3 工艺尺寸链的应用 168
5.6 套筒类零件的加工实践 170
5.6.1 确定加工方案、选择加工设备及工装设备 171
5.6.2 划分加工阶段 172
5.6.3 制定加工工艺过程 172
5.7 拓展知识——深孔钻 174
任务六 盘类零件加工 176
6.1 项目任务书 176
6.2 盘类零件加工的相关知识 177
6.2.1 盘类零件的结构特点及工艺性分析 177
6.2.2 盘类零件的技术要求 178
6.2.3 盘类零件的材料、毛坯及热处理 178
6.3 常用的装夹方式 178
6.3.1 基准分析 178
6.3.2 安装方案 178
6.4 盘类零件的加工实践 179
6.4.1 零件图分析 179
6.4.2 选择毛坯 179
6.4.3 选择定位基准 179
6.4.4 确定加工方案 180
6.4.5 拟订工艺路线 180
6.4.6 确定工序尺寸 180
6.4.7 选择加工设备和工艺装备 181
6.4.8 填写工艺文件 181
6.5 拓展知识——螺纹车削 182
6.5.1 螺纹车削实践 182
6.5.2 螺纹的检测 185
任务七 齿轮零件的加工 187
7.1 项目任务书 187
7.2 齿轮加工的相关知识 188
7.2.1 圆柱齿轮的功用和结构特点 188
7.2.2 圆柱齿轮的技术要求 188
7.2.3 齿轮常用的材料、毛坯及热处理 189
7.3 齿轮加工常用的方法及装备 189
7.3.1 成形加工 190
7.3.2 滚齿加工 190
7.3.3 插齿加工 193
7.3.4 剃齿加工简介 195
7.3.5 珩齿加工简介 197
7.3.6 磨齿加工简介 197
7.3.7 齿形加工方案 198
7.4 常用的装夹方式 199
7.4.1 滚齿、插齿装夹方式 199
7.4.2 剃齿、珩齿装夹方式 200
7.4.3 齿轮轴的装夹 201
7.5 齿轮零件的加工实践 201
7.5.1 确定加工方案、选择加工设备及工装设备 202
7.5.2 划分加工阶段 202
7.5.3 制定加工工艺过程 202
7.6 拓展知识——齿形精度检测方法 204
任务八 箱体类零件的加工 207
8.1 项目任务书 207
8.2 箱体类零件加工的相关知识 208
8.2.1 箱体的功用和结构特点 208
8.2.2 箱体的技术要求 209
8.2.3 箱体常用的材料、毛坯及热处理 210
8.3 箱体表面常用的加工方法及装备 210
8.3.1 铣削加工 210
8.3.2 刨削加工 216
8.3.3 磨削加工简介 218
8.3.4 光整加工简介 219
8.4 箱体零件常用的安装方式 220
8.4.1 常用的装夹方式 220
8.4.2 铣床夹具的分类及其结构形式 221
8.4.3 铣床夹具设计要点 223
8.5 箱体类零件的加工实践 224
8.5.1 确定加工方案、选择加工设备及工装设备 224
8.5.2 划分加工阶段 224
8.5.3 制定加工工艺过程 224
8.6 拓展知识——箱体零件的测量 227
任务九 设备的拆装 230
9.1 项目任务书 230
9.2 机械装配的相关知识 230
9.2.1 装配的一般流程 230
9.2.2 装配的基本作业 231
9.2.3 机械装配的装配单元及组织形式 233
9.2.4 装配的方法 235
9.2.5 装配工艺规程的制定 243
9.3 减速器拆装实践 246
9.3.1 减速器的结构 246
9.3.2 减速器装配的主要技术要求 247
9.3.3 减速器的拆卸 247
9.3.4 减速器的装配工艺过程 247
9.4 拓展知识——轴承的装拆方法 248
9.4.1 滚动轴承的装配 248
任务十 特种加工技术的应用 252
10.1 项目任务书 252
10.2 特种加工的相关知识 253
10.2.1 电火花加工 254
10.2.2 电火花线切割加工 255
10.2.3 电化学加工 256
10.2.4 超声波加工 258
10.2.5 激光加工 259
10.3 电火花线切割加工实践 260
10.3.1 零件工艺分析 260
10.3.2 工艺参数的选择 260
10.3.3 工件的装夹与调整 261
10.3.4 加工设备 263
10.3.5 操作步骤及内容 263
10.4 拓展知识——现代制造技术的概况 264
10.4.1 现代制造技术的定义 264
10.4.2 计算机辅助工艺设计 265
10.4.3 计算机集成制造系统 268
参考文献 272
- 《钒产业技术及应用》高峰,彭清静,华骏主编 2019
- 《现代水泥技术发展与应用论文集》天津水泥工业设计研究院有限公司编 2019
- 《异质性条件下技术创新最优市场结构研究 以中国高技术产业为例》千慧雄 2019
- 《Prometheus技术秘笈》百里燊 2019
- 《英汉翻译理论的多维阐释及应用剖析》常瑞娟著 2019
- 《中国制造业绿色供应链发展研究报告》中国电子信息产业发展研究院 2019
- 《中央财政支持提升专业服务产业发展能力项目水利工程专业课程建设成果 设施农业工程技术》赵英编 2018
- 《药剂学实验操作技术》刘芳,高森主编 2019
- 《林下养蜂技术》罗文华,黄勇,刘佳霖主编 2017
- 《脱硝运行技术1000问》朱国宇编 2019
- 《大学计算机实验指导及习题解答》曹成志,宋长龙 2019
- 《指向核心素养 北京十一学校名师教学设计 英语 七年级 上 配人教版》周志英总主编 2019
- 《大学生心理健康与人生发展》王琳责任编辑;(中国)肖宇 2019
- 《大学英语四级考试全真试题 标准模拟 四级》汪开虎主编 2012
- 《大学英语教学的跨文化交际视角研究与创新发展》许丽云,刘枫,尚利明著 2020
- 《北京生态环境保护》《北京环境保护丛书》编委会编著 2018
- 《复旦大学新闻学院教授学术丛书 新闻实务随想录》刘海贵 2019
- 《大学英语综合教程 1》王佃春,骆敏主编 2015
- 《大学物理简明教程 下 第2版》施卫主编 2020
- 《指向核心素养 北京十一学校名师教学设计 英语 九年级 上 配人教版》周志英总主编 2019