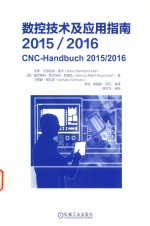
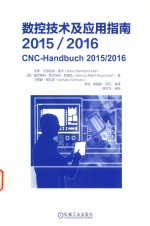
数控技术及应用指南 2015-2016PDF电子书下载
- 电子书积分:16 积分如何计算积分?
- 作 者:汉斯·贝恩哈特·基夫,赫尔穆特·阿尔伯特·罗施瓦著;林松等译
- 出 版 社:北京:机械工业出版社
- 出版年份:2017
- ISBN:9787111565826
- 页数:521 页
第1章 数控技术导论 1
1.1 数控加工的发展历史 3
1.1.1 第二次世界大战后初期 3
1.1.2 机床行业的重建 3
1.1.3 东德的机床工业 4
1.1.4 全球机床行业的发展变化 5
1.1.5 具有代表性的新型数控机床 5
1.1.6 日本的影响 6
1.1.7 德国危机 6
1.1.8 原因及影响 7
1.1.9 柔性制造系统 7
1.1.10 2009年世界经济危机 8
1.1.11 形势及展望 9
1.1.12 结论 10
1.2 数控技术的发展里程碑 12
1.3 数控技术和计算机数控技术 15
1.3.1 通向NC的途径 15
1.3.2 硬件 16
1.3.3 软件 16
1.3.4 控制类型 17
1.3.5 数控轴 19
1.3.6 可编程序控制器 20
1.3.7 适配单元 20
1.3.8 计算机技术和数控技术 20
1.3.9 NC程序和编程 22
1.3.10 数据输入 24
1.3.11 数控系统的操作 24
1.3.12 小结 27
1.3.13 本节要点 28
第2章 CNC机床的功能 29
2.1 位置信息 31
2.1.1 引言 31
2.1.2 轴的标识 31
2.1.3 位置控制回路 33
2.1.4 位置的测量 35
2.1.5 补偿 44
2.1.6 本节要点 52
2.2 辅助功能 53
2.2.1 说明 53
2.2.2 换刀功能 53
2.2.3 车床的换刀功能 54
2.2.4 铣床和加工中心的换刀功能 54
2.2.5 刀具的识别 56
2.2.6 工件的更换 57
2.2.7 主轴的变速功能 60
2.2.8 进给速度功能 60
2.2.9 小结 60
2.2.10 本节要点 61
2.3 数控功能 62
2.3.1 定义 62
2.3.2 CNC系统的基本功能 62
2.3.3 CNC系统的特殊功能 66
2.3.4 防碰撞功能 68
2.3.5 数控机床集成的安全理念 73
2.3.6 数控显示 83
2.3.7 数控系统的用户界面扩展 84
2.3.8 开放式数控系统 86
2.3.9 成本评估 88
2.3.10 现代数控系统的优点 90
2.3.11 小结 90
2.3.12 本节要点 91
2.4 可编程序控制器 93
2.4.1 定义 93
2.4.2 PLC的发展历史 93
2.4.3 PLC的组成和工作原理 93
2.4.4 数据总线和现场总线 95
2.4.5 PLC的优点 99
2.4.6 PLC的编程和文档语言 100
2.4.7 PLC程序 101
2.4.8 程序存储器 101
2.4.9 PLC、CNC和PC集成 102
2.4.10 PLC的选择标准 104
2.4.11 小结 104
2.4.12 CNC和PLC的列表比较 104
2.4.13 本节要点 104
2.5 CNC系统对机床组件的影响 108
2.5.1 机床配置 108
2.5.2 床身 109
2.5.3 导轨 110
2.5.4 机床外罩 110
2.5.5 冷却系统 111
2.5.6 排屑系统 111
2.5.7 小结 111
2.5.8 本节要点 111
第3章 CNC机床的电气驱动系统 113
3.1 CNC机床的进给驱动系统 115
3.1.1 进给驱动系统的要求 116
3.1.2 进给驱动的类型 116
3.1.3 直线电动机的种类 121
3.1.4 直线电动机驱动的优缺点 122
3.1.5 驱动控制器和CNC系统的连接 123
3.1.6 测量传感器 124
3.1.7 小结 125
3.1.8 本节要点 126
3.2 CNC机床的主轴驱动系统 127
3.2.1 主轴驱动系统的要求 127
3.2.2 主轴驱动的类型 128
3.2.3 主轴驱动系统的结构形式 128
3.2.4 交流同步电动机驱动模式 130
3.2.5 同步电动机驱动的优缺点 131
3.2.6 本节要点 131
3.3 面向过程的机床驱动系统设计 133
3.3.1 系统划分 133
3.3.2 加工工艺的出发点 134
3.3.3 能效均衡 135
3.3.4 机床驱动系统的结构 136
3.3.5 进给驱动系统的静态设计和动态设计 137
3.3.6 直线电动机驱动 140
3.3.7 根据工艺参数拟订驱动方案 140
3.3.8 机床设计的普遍性和特殊性 142
3.3.9 基于工艺参数的机床进给驱动系统的设计方案拟订 143
3.3.10 机床的系统性考虑 144
3.3.11 小结 146
3.3.12 本节要点 146
3.4 基于工艺参数的主轴机械设计 148
3.4.1 电动机选择 148
3.4.2 轴承选择 148
3.4.3 润滑介质选择 149
3.4.4 加工工艺选择 149
3.4.5 本节要点 152
第4章 数控机床的类型 153
4.1 数控机床 155
4.1.1 加工中心和数控铣床 155
4.1.2 数控车床 160
4.1.3 数控磨床 165
4.1.4 数控齿轮加工机床 170
4.1.5 数控钻床和镗床 176
4.1.6 数控锯床 178
4.1.7 激光加工设备 180
4.1.8 冲压机床和冲剪机床 185
4.1.9 弯管机床 188
4.1.10 数控电火花加工机床 190
4.1.11 电子束机床 192
4.1.12 水切割机床 193
4.1.13 复合机床 195
4.1.14 测量和检验设备 202
4.1.15 小结 204
4.1.16 本节要点 205
4.2 增材制造 206
4.2.1 引言 206
4.2.2 定义 207
4.2.3 工艺流程 208
4.2.4 增材制造工艺的分类 210
4.2.5 几种重要的叠层制造工艺 211
4.2.6 小结 218
4.2.7 本节要点 218
4.3 柔性制造系统 220
4.3.1 定义 220
4.3.2 柔性制造岛 221
4.3.3 柔性制造单元 222
4.3.4 柔性制造系统的技术特征 224
4.3.5 柔性制造系统的应用准则 225
4.3.6 加工策略 227
4.3.7 设备选型及布局 228
4.3.8 工件运输系统 228
4.3.9 适用于柔性制造系统的CNC系统 235
4.3.10 柔性制造系统的主机 236
4.3.11 柔性制造系统的经济优势 238
4.3.12 柔性制造系统规划中的问题与风险 239
4.3.13 柔性和复杂性 241
4.3.14 柔性制造系统的仿真 241
4.3.15 生产计划系统 243
4.3.16 小结 244
4.3.17 本节要点 244
4.4 工业机器人及其操纵技术 246
4.4.1 引言 246
4.4.2 工业机器人的定义 246
4.4.3 工业机器人的组成 247
4.4.4 工业机器人的机械学/运动学结构 248
4.4.5 夹持器或末端执行器 249
4.4.6 控制器 249
4.4.7 机器人的安全技术 252
4.4.8 编程 253
4.4.9 传感器 255
4.4.10 工业机器人的应用案例 256
4.4.11 工业机器人的应用准则 258
4.4.12 工业机器人和数控机床的比较 259
4.4.13 小结与展望 259
4.4.14 本节要点 260
4.5 高能效经济型生产 261
4.5.1 引言 261
4.5.2 能效的定义 261
4.5.3 车间 261
4.5.4 机床群 261
4.5.5 加工中心的节能特征 262
4.5.6 数控程序的节能措施 263
4.5.7 机床制造商的节能潜力 263
4.5.8 用户的节能潜力 263
4.5.9 无功电流补偿 265
4.5.10 小结 267
4.5.11 展望 267
4.5.12 本节要点 267
第5章 数控加工刀具 269
5.1 刀具的结构 271
5.1.1 引言 271
5.1.2 技术要求 271
5.1.3 刀具的分类 273
5.1.4 机床端刀具夹头 277
5.1.5 模块化刀具系统 280
5.1.6 可调刀具 281
5.1.7 螺纹铣削 283
5.1.8 专用刀具 285
5.1.9 刀具的选择 289
5.1.10 本节要点 290
5.2 刀具的管理 291
5.2.1 引言 291
5.2.2 刀具管理的评估 292
5.2.3 技术规范 292
5.2.4 解决方案的评定 293
5.2.5 刀具管理的引入 293
5.2.6 组成 293
5.2.7 集成 293
5.2.8 刀具的识别 294
5.2.9 刀具的查询 295
5.2.10 刀具的分类 295
5.2.11 刀具部件 295
5.2.12 刀具的总成 296
5.2.13 刀具列表 297
5.2.14 工序 297
5.2.15 刀具的预调 298
5.2.16 刀具的物流 299
5.2.17 刀具的电子识别 300
5.2.18 小结 305
5.2.19 本节要点 305
5.3 在线工件测量和过程控制 307
5.3.1 引言 307
5.3.2 过程控制的切入点 307
5.3.3 工件和刀具测量系统的应用范围 308
5.3.4 机床的工件测量系统 310
5.3.5 本节要点 315
5.4 基于激光技术的刀具监控 316
5.4.1 引言 316
5.4.2 破损检测 316
5.4.3 单切削刃的检测 317
5.4.4 高速切削刀具的测量 317
5.4.5 组合式激光测量系统 318
5.4.6 面向过程的孔测头 319
5.4.7 主动可调刀具系统 319
5.4.8 机电一体化刀具系统 319
5.4.9 闭环过程链 322
5.4.10 小结 323
5.4.11 本节要点 323
第6章 NC加工程序及编程 325
6.1 NC加工程序 327
6.1.1 定义 328
6.1.2 NC加工程序的结构 328
6.1.3 程序的组成、语法和语义 329
6.1.4 辅助功能(M指令) 330
6.1.5 位置信息 331
6.1.6 准备功能(G指令) 332
6.1.7 加工循环 335
6.1.8 零点和参考点 338
6.1.9 坐标转换 341
6.1.10 刀具补偿 342
6.1.11 DXF文件转换 344
6.1.12 三维图形 345
6.1.13 小结 347
6.1.14 本节要点 347
6.2 数控机床的编程 349
6.2.1 数控编程的定义 349
6.2.2 编程方法 349
6.2.3 基于CAM的数控切削加工策略 354
6.2.4 图形辅助编程 357
6.2.5 合适的编程系统的选择 358
6.2.6 小结 359
6.2.7 本节要点 360
6.3 数控编程系统 361
6.3.1 引言 361
6.3.2 变化中的加工方法 361
6.3.3 根据应用范围确定优先级 363
6.3.4 不同来源的数据输入 364
6.3.5 现代NC编程系统(CAM)的功能范围 364
6.3.6 高级数据模型 364
6.3.7 面向CAM的几何元素处理 364
6.3.8 侧重高效加工策略 365
6.3.9 自适应加工 366
6.3.10 三维模型提供更多信息 366
6.3.11 三维接口 367
6.3.12 特征技术的创新 367
6.3.13 NC编程的自动化 368
6.3.14 刀具 370
6.3.15 装夹方案及顺序的确定 370
6.3.16 仿真的重要性 372
6.3.17 后置处理器 372
6.3.18 生成的数据及其与机床的接口 372
6.3.19 小结 372
6.3.20 本节要点 372
6.4 加工仿真 374
6.4.1 引言 374
6.4.2 系统的定性区分 374
6.4.3 仿真场景的组件 376
6.4.4 NC仿真流程 379
6.4.5 集成仿真系统 380
6.4.6 应用领域 381
6.4.7 小结 383
6.4.8 本节要点 384
第7章 从企业信息化到工业4.0 385
7.1 直接数字控制或分布式数字控制 387
7.1.1 定义 387
7.1.2 DNC的任务 387
7.1.3 DNC系统的应用准则 387
7.1.4 与CNC控制器的数据通信 388
7.1.5 程序的访问调用技术 389
7.1.6 目前可提供的DNC系统 389
7.1.7 用于DNC的网络技术 390
7.1.8 网络应用的优点 391
7.1.9 NC加工程序的管理 391
7.1.10 DNC的优点 394
7.1.11 DNC的成本和经济性 395
7.1.12 DNC的现状和发展趋势 395
7.1.13 小结 396
7.1.14 本节要点 396
7.2 局域网(LAN) 398
7.2.1 引言 398
7.2.2 局域网 399
7.2.3 信息的定义 399
7.2.4 局域网的特征与属性 400
7.2.5 网桥和网关 404
7.2.6 局域网的选择标准 405
7.2.7 接口 405
7.2.8 小结 408
7.2.9 本节要点 409
7.3 数字化产品的研发和制造:从CAD、CAM到PLM 410
7.3.1 引言 410
7.3.2 概念和发展史 410
7.3.3 数字化产品研发 414
7.3.4 数字化制造 418
7.3.5 小结 421
7.3.6 本节要点 422
7.4 工业4.0 423
7.4.1 基础 423
7.4.2 工业4.0的核心元素 424
7.4.3 制造业中的工业4.0 426
7.4.4 制造执行系统是工业4.0的重要组件 427
7.4.5 工业4.0的挑战与风险 428
7.5 全过程链在牙科制造业中的应用 429
7.5.1 引言 429
7.5.2 医疗器械法规的影响 429
7.5.3 变化中的牙科制造业 429
7.5.4 牙科制造业对信息流的要求 431
7.5.5 牙科制造业的全过程信息系统 433
7.5.6 本节要点 434
第8章 附录 437
8.1 准则、标准和建议 439
8.1.1 VDI准则 439
8.1.2 VDI/NCG准则 441
8.1.3 德国工业标准(DIN) 442
8.2 NC专业词汇 446
8.3 关键词索引 495
8.4 推荐的NC文献 518
- 《钒产业技术及应用》高峰,彭清静,华骏主编 2019
- 《近代旅游指南汇刊二编 16》王强主编 2017
- 《现代水泥技术发展与应用论文集》天津水泥工业设计研究院有限公司编 2019
- 《异质性条件下技术创新最优市场结构研究 以中国高技术产业为例》千慧雄 2019
- 《甘肃省档案馆指南》甘肃省档案馆编 2018
- 《Prometheus技术秘笈》百里燊 2019
- 《英汉翻译理论的多维阐释及应用剖析》常瑞娟著 2019
- 《中央财政支持提升专业服务产业发展能力项目水利工程专业课程建设成果 设施农业工程技术》赵英编 2018
- 《药剂学实验操作技术》刘芳,高森主编 2019
- 《林下养蜂技术》罗文华,黄勇,刘佳霖主编 2017
- 《社会学与人类生活 社会问题解析 第11版》(美)James M. Henslin(詹姆斯·M. 汉斯林) 2019
- 《难民革命》马克·恩格尔哈特 2019
- 《国际声乐舞台咏叹调必选 次女高音》玛莎·格哈特原版翻译 2019
- 《静默之地》(美)约翰·哈特著;崔玲译 2019
- 《隐形冠军 未来全球化的先锋 原书第2版》张帆,吴君,刘惠宇,刘银远译;(德国)赫尔曼·西蒙,杨一安 2019
- 《超译黑塞 痛苦和悲伤都是欢喜》赫尔曼·黑塞,白取春彦著 2020
- 《风湿病》(德)斯特凡·塞尔;(德)斯特凡·雷哈特 2019
- 《老鼠、虱子和历史》(美)汉斯·辛瑟尔(HansZinsser)著 2019
- 《国际声乐舞台咏叹调必选 男高音》玛莎·格哈特原版翻译 2019
- 《国际声乐舞台咏叹调必选 女高音》玛莎·格哈特原版翻译 2019
- 《指向核心素养 北京十一学校名师教学设计 英语 七年级 上 配人教版》周志英总主编 2019
- 《北京生态环境保护》《北京环境保护丛书》编委会编著 2018
- 《高等教育双机械基础课程系列教材 高等学校教材 机械设计课程设计手册 第5版》吴宗泽,罗圣国,高志,李威 2018
- 《指向核心素养 北京十一学校名师教学设计 英语 九年级 上 配人教版》周志英总主编 2019
- 《高等院校旅游专业系列教材 旅游企业岗位培训系列教材 新编北京导游英语》杨昆,鄢莉,谭明华 2019
- 《中国十大出版家》王震,贺越明著 1991
- 《近代民营出版机构的英语函授教育 以“商务、中华、开明”函授学校为个案 1915年-1946年版》丁伟 2017
- 《新工业时代 世界级工业家张毓强和他的“新石头记”》秦朔 2019
- 《智能制造高技能人才培养规划丛书 ABB工业机器人虚拟仿真教程》(中国)工控帮教研组 2019
- 《AutoCAD机械设计实例精解 2019中文版》北京兆迪科技有限公司编著 2019