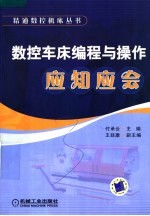
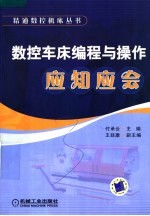
数控车床编程与操作应知应会PDF电子书下载
- 电子书积分:13 积分如何计算积分?
- 作 者:付承云主编;王廷康副主编
- 出 版 社:北京:机械工业出版社
- 出版年份:2007
- ISBN:711120297X
- 页数:377 页
第1章 预备知识 1
1.1 数控车床的种类及其功能 1
1.1.1 数控车床的分类 1
前言 1
1.1.2 数控车床的功能部件 2
1.2 数控车床采用的数控系统的配置 4
1.2.1 FANUC 0i系统 4
1.2.2 SIEMENS 802D系统 4
1.2.3 可编程控制器 5
1.2.4 伺服驱动系统 6
1.3 数控车床机械结构的配置 9
1.3.1 传动系统机械结构简化 9
1.3.2 机床导轨的特点 10
1.3.3 4工位刀架 12
1.4.2 运动方向的确定 14
1.4 数控车床坐标系的建立 14
1.4.1 坐标系确定的原则 14
1.4.3 前置刀架与后置刀架 15
1.4.4 车削中心与旋转轴的命名 16
1.4.5 坐标系中点的概念 16
1.4.6 数控车床FANUC 0系统中的四个坐标系 18
第2章 CKA6150数控车床(系统FANUC 0—TD)的编程与操作 20
2.1 FANUC 0—TD系统的编程基本知识 20
2.1.1 程序编制的方法 20
2.1.2 程序的格式 21
2.1.3 准备功能G代码、辅助功能M代码 23
2.2 编程指令的介绍 28
2.2.1 快速定位(G00) 28
2.2.2 直线插补(G01) 29
2.2.3 圆弧插补(G02、G03) 30
2.2.4 暂停(G04) 32
2.2.5 自动返回参考点(G28) 33
2.2.6 返回参考点检测(G27) 34
2.2.7 公制与英制(G21、G20) 34
2.2.8 螺纹切削(G32) 34
2.2.9 刀具半径补偿功能(G40、G41、G42) 35
2.2.10 设定工件坐标系(G50) 39
2.2.11 第一工件坐标系~第六工件坐标系(G54~G59) 39
2.2.12 外径内径单一车削循环 40
2.2.13 端面切削循环(G94) 42
2.3 CKA6150数控车床的布局及技术参数 43
2.4 操作面板的按钮设置及其使用方法 45
2.4.1 系统操作面板的组成及其使用方法 45
2.4.2 机床操作面板的组成及其使用方法 47
2.5.2 手动操作机床 50
2.5.1 开机方法 50
2.5 机床的操作和实用对刀方法及刀补的应用 50
2.5.3 程序的编辑 52
2.5.4 程序的运行 53
2.5.5 实用对刀方法及刀补的应用 53
2.6 编程举例 56
2.6.1 轴类零件的加工举例 56
2.6.2 盘类零件的加工举例 59
第3章 CL—20数控车床(系统FANUC 0i—T)的编程与操作 64
3.1 FANUC 0i—T系统的功能特点 64
3.2 指令说明 64
3.2.1 变螺距螺纹的切削(G34) 64
3.2.2 等螺距螺纹的切削(G32) 65
3.2.3 粗车多重固定循环(G71) 66
3.2.4 端面多重固定循环(G72) 68
3.2.5 仿形切削循环(G73) 69
3.2.7 端面深孔钻削(G74) 71
3.2.6 精加工循环(G70) 71
3.2.8 外径切槽循环(G75) 72
3.2.9 螺纹切削复合循环(G76) 74
3.2.10 可编程参数输入(G10) 75
3.2.11 局部坐标系指令(G52) 76
3.3 CL—20数控车床的布局及规格 77
3.4 操作面板的使用方法 80
3.5 实用对刀方法及刀补的应用 86
3.6 编程举例 88
3.6.1 例1:轴类零件 88
3.6.2 例2:盘套类零件 91
3.6.3 例3:加工综合零件 94
第4章 CKA6150数控车床(系统SINUMERIK 802D)的编程与操作 100
4.1 SINUMERIK 802D系统的编程基本知识 100
4.2.2 直线插补(G1) 101
4.2.1 快速移动(G0) 101
4.2 功能指令介绍 101
4.2.3 顺时针圆弧插补(G2) 102
4.2.4 逆时针圆弧插补(G3) 102
4.2.5 通过中间点进行圆弧插补(CIP) 102
4.2.6 切线过渡圆弧(CT) 102
4.2.7 恒螺距螺纹切削(G33) 102
4.2.8 返回固定点(G75) 104
4.2.9 回参考点(G74) 104
4.2.10 暂停(G4) 104
4.2.11 主轴转速极限(G25、G26) 105
4.2.12 恒定切削速度(G96、G97) 105
4.2.13 倒圆、倒角 106
4.2.14 刀具和刀具补偿 106
4.2.15 刀具半径补偿指令(G41、G42) 110
4.2.16 取消刀尖半径补偿(G40) 111
4.2.17 拐角特性(G450、G451) 112
4.2.18 绝对和增量位置 113
4.2.19 轮廓定义编程 114
4.2.20 计算参数R 115
4.2.21 程序跳转 116
4.2.22 有条件跳转 117
4.2.23 子程序 120
4.2.24 可编程的零点偏置(G158) 121
4.2.25 调用加工循环 126
4.3 操作面板的使用方法 126
4.4 对刀方法及刀补的应用 134
4.5 程序的输入及修改 140
4.6 编程举例 143
4.6.1 棒料加工锥形 143
4.6.2 棒料加工螺纹 144
4.6.3 棒料加工圆弧 146
5.1 大森Ⅲ(R2J50L)系统的编程基本知识 151
第5章 CL—20数控车床(系统大森Ⅲ:R2J50L)的编程与操作 151
5.2 功能指令介绍 152
5.2.1 直线插补(G01) 152
5.2.2 圆弧插补(G02、G03) 154
5.2.3 延时(G04)非模态指令 154
5.2.4 倒角(G11)模态指令 155
5.2.5 倒圆角(G12)模态指令 156
5.2.6 英制/米制(G20/G21) 157
5.2.7 圆弧插补的半径编程(G22、G23) 157
5.2.8 参考点检查(G27) 158
5.2.9 自动返回参考点(G28) 158
5.2.10 从参考点返回(G29) 159
5.2.11 第二参考点的返回(G30) 159
5.2.12 螺纹切削、连续螺纹切削(G32) 160
5.2.13 多头螺纹切削(G32) 162
5.2.14 变螺距螺纹的切削(G34) 163
5.2.15 刀具半径补偿(G40、G41、G42) 164
5.2.16 车外圆循环(G90) 165
5.2.17 车螺纹循环(G92) 165
5.2.18 车端面循环(G94) 167
5.2.19 表面恒速度控制(G96、G97) 169
5.2.20 分进给与转进给(G98、G99)模态指令 169
5.2.21 车外圆重复循环(G71) 169
5.2.22 车端面重复循环(G72) 170
5.2.23 仿形重复循环(G73) 170
5.2.24 精车循环(G70) 171
5.2.25 Z轴啄钻(G74) 171
5.2.26 X轴切槽(G75) 172
5.2.27 自动螺纹切削(G76) 173
5.3 操作面板的使用方法 174
5.4 大森Ⅲ(R2J50L)对刀方式 180
5.5.1 加工外圆、端面及内孔 181
5.5 编程举例 181
5.5.2 车外圆 184
5.5.3 车削100mm长度上各部分尺寸 187
第6章 CKA6150数控车床(系统ASINA 205—T)的编程与操作 191
6.1 ASINA 205-T系统的编程 191
6.1.1 编程说明 191
6.1.2 G代码一览表 191
6.1.3 自动加减速概念 193
6.2 准备功能G指令 194
6.2.1 快速定位(G00) 194
6.2.2 直线插补(G01) 194
6.2.3 圆弧插补(G02/G03) 194
6.2.4 暂停(G04) 195
6.2.5 米制与英制(G21/G20) 195
6.2.9 螺纹切削(G33) 196
6.2.8 返回机械原点(G28) 196
6.2.7 设定位置复归(G27、G92) 196
6.2.6 返回加工原点(G26) 196
6.2.10 刀尖半径补偿指令(G41、G42) 197
6.2.11 返回刀具交换位置(G50) 198
6.2.12 加工坐标系设定取消(G53) 198
6.2.13 绝对值指令/增量值指令(G90/G91) 199
6.2.14 坐标系设定/主轴最高转速的设定(G92) 200
6.2.15 每分钟进给/每转进给(G94/G95) 201
6.2.16 恒线速控制/恒线速控制取消(转数一定)(G96/G97) 201
6.2.17 倒圆/倒角(R/C) 201
6.2.18 内、外径及锥面单一切削固定循环(G77) 203
6.2.19 直螺纹/锥螺纹单一切削固定循环(G78) 204
6.2.20 端面/锥面单一切削固定循环(G79) 204
6.2.21 精车循环(G70) 206
6.2.22 外圆(轴向)切削复合循环(G71) 206
6.2.23 端面(径向)切削复合循环(G72) 207
6.2.24 轮廓切削复合循环(G73) 208
6.2.25 螺纹切削复合循环(G76) 209
6.3 操作面板的使用方法 211
6.3.1 系统操作面板说明 211
6.3.2 机床操作面板说明 212
6.3.3 操作方式 212
6.4 系统对刀及刀补参数 220
6.4.1 系统对刀方式 220
6.4.2 刀补参数方式操作 221
6.4.3 刀补参数的说明 222
6.5 编程举例 223
6.5.1 轴类零件 223
6.5.2 盘类零件 225
7.2.1 G准备功能 230
7.2 功能指令介绍 230
7.1 FAGOR 8025T系统的编程基本知识 230
第7章 CKA6763数控车床(系统FAGOR 8025T)的编程与操作 230
7.2.2 M辅助功能 259
7.2.3 T刀具程序设计 260
7.2.4 S主轴速度程序设计 260
7.2.5 F进给率程序设计 261
7.3 操作面板的使用方法 261
7.4 机床操作方法及对刀方式 263
7.5 编程举例 266
第8章 数控车床CSK6136—1(系统DTMSYSTEM 5T)的编程与操作 273
8.1 DTMSYSTEM 5T基本知识 273
8.2 指令功能 274
8.2.1 字符 274
8.2.3 主轴转速代码S功能 275
8.2.2 进给速度F代码功能 275
8.2.4 刀具代码T功能 276
8.2.5 准备代码G功能 276
8.2.6 辅助代码M功能 277
8.2.7 地址码L功能 278
8.2.8 地址码P功能 279
8.2.9 R代码指令功能 280
8.2.10 N代码功能 282
8.2.11 坐标X、Z、U、W、R代码功能 282
8.3 操作面板的使用方法 283
8.3.1 系统显示及编程面板 283
8.3.2 系统操作面板 284
8.3.3 进给及主轴保持旋钮 287
8.3.4 手动进给键 288
8.3.5 程序启动键 288
8.4 对刀方法及应用 288
8.5.1 棒料外轮廓、槽加工 293
8.5 编程举例 293
8.5.2 棒料槽、螺纹、外圆加工 294
8.5.3 棒料外圆、槽、圆弧、螺纹加工 298
第9章 数控车床CAK6140(系统FANUC)的编程举例 304
9.1 综合试件之一(45钢棒料端面、内孔、外轮廓、槽、螺纹加工) 304
9.2 综合试件之二(45钢棒料端面、外圆、锥面、内孔、槽加工) 307
9.3 综合试件之三(45钢棒料端面、锥面、外圆、内孔、内孔阶梯面、槽加工) 310
9.4 综合试件之四(45钢棒料端面、外轮廓、槽、螺纹加工) 313
9.5 综合试件之五(45钢棒料外轮廓、槽、螺纹加工) 316
第10章 数控车床CSK6136—1(系统SINUMERIK 802S/C)的编程举例 319
10.1 综合试件之一(45钢工件外轮廓、槽、螺纹、内孔、内孔槽加工) 319
10.2 综合试件之二(黄铜工件外轮廓、端面、槽、螺纹加工) 324
10.3 综合试件之三(铝合金件端面、外轮廓、V型槽、空刀槽、螺纹加工) 332
10.4 综合试件之四(45钢阶梯轴外轮廓加工) 335
10.5 综合试件之五(45钢短阶梯轴外轮廓加工) 339
10.6 综合试件之六(45钢工件端面、倒角、锥面、槽、螺纹加工) 341
11.1 综合试件之一(40Cr工件轮廓、螺纹加工) 345
第11章 数控车床CSK6136(系统GSK 980TA)的编程举例 345
11.2 综合试件之二(HT200套筒件外圆、槽、内孔加工) 348
11.3 综合试件之三(HT200薄壁套件外圆、槽、内孔加工) 350
11.4 综合试件之四(45钢工件外圆、槽加工) 353
11.5 综合试件之五(45钢工件外圆、内孔加工) 355
11.6 综合试件之六(45钢工件外轮廓、槽加工) 356
第12章 数控车床故障诊断与排除 359
12.1 电气系统的布局及机床电气原理 359
12.1.1 电气系统的布局 359
12.1.2 机床电气原理 361
12.2 数控机床日常检查与维护 365
12.3 故障的查找与排除 368
12.3.1 故障的种类 368
12.3.2 常见故障查找方法 370
12.3.3 故障维修12例 371
参考文献 377
- 《编匠心集》陈昕著 1996
- 《全宋笔记 第8编 10》朱易安,复璇琮,周常林,戴建国主编 2017
- 《民法婚姻家庭亲属编立法研究》杨遂全著 2018
- 《乐都县志 第10编 附录编》乐都县志编纂委员会 1985
- 《乐都县志 第3编 修订稿》乐都县志编纂委员会 1985
- 《光栅尺支架夹具设计及数控加工》张方阳 2019
- 《数控机床主轴系统在线动平衡技术》王展 2020
- 《儒藏 精华编162册 史部传纪类》北京大学《儒藏》编纂与研究中心编 2019
- 《儒藏 96 精华编》北京大学《儒藏》编纂与研究中心编 2018
- 《儒藏 精华编四一册》北京大学《儒藏》编纂与研究中心编 2018
- 《指向核心素养 北京十一学校名师教学设计 英语 七年级 上 配人教版》周志英总主编 2019
- 《北京生态环境保护》《北京环境保护丛书》编委会编著 2018
- 《高等教育双机械基础课程系列教材 高等学校教材 机械设计课程设计手册 第5版》吴宗泽,罗圣国,高志,李威 2018
- 《指向核心素养 北京十一学校名师教学设计 英语 九年级 上 配人教版》周志英总主编 2019
- 《高等院校旅游专业系列教材 旅游企业岗位培训系列教材 新编北京导游英语》杨昆,鄢莉,谭明华 2019
- 《中国十大出版家》王震,贺越明著 1991
- 《近代民营出版机构的英语函授教育 以“商务、中华、开明”函授学校为个案 1915年-1946年版》丁伟 2017
- 《新工业时代 世界级工业家张毓强和他的“新石头记”》秦朔 2019
- 《智能制造高技能人才培养规划丛书 ABB工业机器人虚拟仿真教程》(中国)工控帮教研组 2019
- 《AutoCAD机械设计实例精解 2019中文版》北京兆迪科技有限公司编著 2019