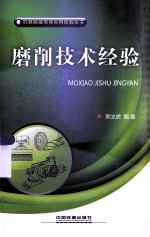
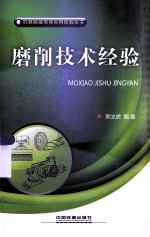
磨削技术经验PDF电子书下载
- 电子书积分:10 积分如何计算积分?
- 作 者:郑文虎编著
- 出 版 社:北京:中国铁道出版社
- 出版年份:2014
- ISBN:9787113181161
- 页数:238 页
第一章 磨削工艺 1
第一节 外圆磨削 1
1.重视中心孔对轴类工件磨削的影响 1
2.修研中心孔的方法 2
3.用双顶尖装夹工件时应注意的问题 3
4.用三爪或四爪卡盘装夹工件应注意的问题 3
5.用卡盘和顶尖装夹工件注意的问题 5
6.磨削时工件速度vw的选择 5
7.磨削深度的选择 6
8.纵向进给量的选择 7
9.台阶轴端面的磨削方法 7
10.磨削轴类工件磨床的调整 9
11.磨削外圆时防止烧伤的办法 10
12.磨削外圆时螺旋纹的防止方法 11
13.磨削外圆时防止椭圆的方法 11
14.磨削外圆时防止直波纹的方法 11
15.磨削轴时台阶端面问题的防止 12
16.磨削台阶轴外圆防止同轴度误差大的方法 12
17.磨削外圆时工件表面粗糙度值大的解决方法 13
18.磨削细长轴时易产生的问题防止方法 13
19.用Z形板拨动工件通磨轴外圆 14
20.磨削轴类工件步骤的选择原则 14
第二节 内圆磨削 16
1.砂轮直径的选择 16
2.砂轮宽度的选择 17
3.砂轮粒度和硬度的选择 17
4.对砂轴接长轴的要求 18
5.砂轮与接长轴的紧固方法 18
6.用三爪自定心卡盘装夹和找正工件 20
7.用四爪单动卡盘装夹和找正工件 22
8.用卡盘和中心架装夹和找正工件 22
9.用法兰盘和压板装夹工件磨内孔 23
10.用花盘装夹工件 24
11.内孔纵向磨削法 25
12.内孔横向磨削法 28
13.修整砂轮的方法 29
14.内孔磨削用量的选择 30
15.保证套类工件相互位置精度的方法 31
16.防止工件变形的措施 32
17.磨削内孔时工件表面产生直波纹的防止方法 33
18.磨削内孔时工件表面出现螺旋纹的防止方法 33
19.磨削内孔时工件表面产生划伤的防止方法 34
20.磨削内孔时工件表面产生烧伤的防止方法 34
21.磨削内孔时工件圆度超差的防止方法 34
22.磨削内孔时工件产生喇叭形的防止方法 35
23.磨削内孔时圆柱度达不到要求的防止方法 35
24.采用法兰盘或花盘装夹磨内孔工件端面与孔不垂直的防止方法 36
25.磨削小孔时的砂轮装夹方法 36
26.小砂轮的夹紧方法 36
27.干磨橡胶轴承内孔 37
28.用电镀金刚石或立方氮化硼砂轮磨小孔 37
29.提高内圆磨削效率的方法 37
第三节 圆锥工件的磨削 38
1.磨削外圆锥面时工件的装夹方法 38
2.磨削内圆锥面时工件的装夹方法 38
3.外圆锥面的磨削方法 40
4.内圆锥面的磨削方法 43
5.锥度(或角度)的检验 44
6.圆锥尺寸的检测 46
7.圆锥尺寸的控制方法 49
8.磨削圆锥面时锥度不准确的防止方法 52
9.磨削圆锥面时母线不直的防止方法 52
10.磨削圆锥内孔时圆度不好的防止方法 53
11.修磨活顶尖60°锥面的方法 55
第四节 平面磨削 56
1.平面的磨削方法 56
2.平面磨削时砂轮的选择 58
3.磨削平面时工件的装夹 59
4.磨削平面时的方法 60
5.磨削平面时磨削用量的选择 61
6.小尺寸薄壁环形工件的磨削 62
7.宽工件平面的磨削 63
8.垂直平面的磨削 64
9.磨削斜面的方法 67
10.台阶平面的磨削 70
11.磨削直角槽平面的方法 72
12.磨削平面时工件表面产生波纹的防止方法 72
13.磨削平面时出现划伤的防止方法 72
14.磨削平面时工件表面出现直线痕迹的防止方法 73
15.磨削平面时几何误差大的防止方法 73
16.磨削平面时工件表面烧伤的防止方法 74
17.平面磨削时应注意的问题 74
第五节 无心磨削 74
1.无心外圆磨削的基本原理 74
2.无心外圆磨削的方法 76
3.无心外圆磨削磨床的调整 78
4.在无心磨床上磨削圆柱销 84
5.在无心磨床上磨削圆锥体 85
6.在无心磨床上磨削细长轴 87
7.无心磨削时工件产生不圆的防止方法 88
8.无心磨削时工件产生多边形的防止方法 88
9.无心磨削时工件表面振痕的防止方法 89
10.无心磨削时工件圆柱度超差的防止方法 89
11.无心磨削时工件中间大两端小的防止方法 90
12.无心磨削时工件中间小两端大的防止方法 90
13.无心磨削时工件产生螺旋线的防止方法 90
14.无心磨削时工件前部多磨去一小块的防止方法 91
15.无心磨削时直线度超差的防止方法 91
16.无心磨削时工件表面产生烧伤的防止方法 91
17.无心磨削时工件后部被切去一条的防止方法 92
18.无心磨削时工件表面粗糙度值大的防止方法 92
19.无心磨削时工件尺寸分散的防止方法 92
第六节 刀具的磨削 93
1.直齿铰刀的磨削 93
2.圆柱螺旋齿铣刀的磨削 96
3.交错三面刃铣刀的磨削 99
4.锥柄立铣刀的磨削 100
5.盘形插齿刀前刀面的磨削 104
6.锥度铰刀的磨削 106
7.小模数齿轮滚刀的磨削 108
8.拉刀前刀面的磨削 110
9.刃磨刀具时砂轮的选择 112
10.刃磨刀具的注意事项 115
第七节 典型工件的磨削 115
1.细长轴的磨削 115
2.空心细长轴的磨削 118
3.薄片工件的磨削 119
4.外球面的磨削 120
5.内球面的磨削 121
6.大直径球面副的磨削 121
7.高精度大型辊面的磨削 124
8.人造金刚石刀具的磨削 125
9.球面轴承的磨削 126
10.R2 000 mm内圆弧面的磨削 126
11.梯形螺纹丝杠的磨削 128
12.双头蜗杆的磨削 130
13.圆弧板的磨削 133
第二章 难磨材料的磨削 135
第一节 基本概念 135
1.难磨材料的划分 135
2.难磨材料的磨削特点 136
3.改善难磨材料的措施 137
第二节 难磨材料的磨削 140
1.铜、铝合金的磨削 140
2.不锈钢的磨削 141
3.高温合金的磨削 142
4.钛合金的磨削 145
5.采用浸渗润滑剂的砂轮磨削钛合金 147
6.软橡胶的磨削 148
7.磁钢的磨削 149
8.热喷涂(焊)材料的磨削 150
9.工程陶瓷的磨削 151
10.高强度钢和超高强度钢的磨削 153
11.高钒高速钢的磨削 154
12.硬质合金的磨削 155
第三章 珩磨与研磨 157
第一节 珩磨加工 157
1.珩磨加工的特点 157
2.珩磨加工的原理 158
3.珩磨头的结构形式 158
4.珩磨用油石宽度和数量的选择 160
5.珩磨用油石长度的选择 161
6.珩磨油石磨料的选择 161
7.珩磨油石粒度的选择 163
8.珩磨油石硬度的选择 163
9.珩磨油石结合剂的选择 163
10.珩磨油石组织和浓度的选择 164
11.珩磨油石在油石座上的固定方法 164
12.珩磨油石的修整方法 165
13.珩磨液的选择 166
14.珩磨速度和切削交叉角的选择 167
15.珩磨油石工作压力的选择 168
16.珩磨时定量进给速度的选择 169
17.珩磨时工作行程的调整 170
18.珩磨余量的选择 171
19.珩磨前对工件的要求 171
20.珩磨工件常出现的缺陷和消除措施 172
21.轮式珩磨的原理和特点 173
22.轮式珩磨头的结构形式 174
23.珩磨轮尺寸的选择 176
24.珩磨轮特性的选择 177
25.珩磨轮的制造 177
26.珩磨轮的修整 178
27.轮式珩磨工艺参数的选择 178
28.轮式珩磨的珩磨液 179
29.消除轮式珩磨缺陷的方法 179
第二节 研磨加工 179
1.研磨和研磨的特点 179
2.研磨可加工的材料和形状 180
3.研磨的方法划分 181
4.研磨的原理 181
5.研磨能达到的加工精度 183
6.研磨剂的磨料选择 184
7.研磨剂的磨料粒度选择 185
8.研磨液的选择 185
9.研磨用辅助填料的选择 186
10.研磨剂的配制 187
11.金刚石研磨膏及使用注意的问题 187
12.研具的作用和要求 188
13.研具材料及选用 189
14.平面研具的设计 189
15.圆柱面研具的设计 190
16.研磨时工件保持架的设计 192
17.确定研磨运动轨迹的原则 192
18.平面研磨运动轨迹形式和特点 193
19.研磨压力、速度和余量的选择 196
20.平板研具的研平的方法 197
21.研磨圆盘的校平方法 198
22.研磨平板压砂的方法 199
23.研磨中工件的换位 199
24.双面研磨机研磨圆柱形工件的方法 199
25.量块的研磨 201
26.半球体的研磨 202
27.整球体的研磨 202
28.多齿分度盘的研磨 203
第四章 先进的现代磨削 205
1.高速磨削 205
2.深切缓进给强力磨削 206
3.恒压力磨削 211
4.宽砂轮磨削 212
5.多砂轮磨削 215
6.成形磨削 217
7.砂带磨削 219
8.电解磨削 225
9.镜面磨削 231
10.砂轮电解镜面磨削 236
参考文献 238
- 《钒产业技术及应用》高峰,彭清静,华骏主编 2019
- 《现代水泥技术发展与应用论文集》天津水泥工业设计研究院有限公司编 2019
- 《异质性条件下技术创新最优市场结构研究 以中国高技术产业为例》千慧雄 2019
- 《Prometheus技术秘笈》百里燊 2019
- 《中央财政支持提升专业服务产业发展能力项目水利工程专业课程建设成果 设施农业工程技术》赵英编 2018
- 《药剂学实验操作技术》刘芳,高森主编 2019
- 《林下养蜂技术》罗文华,黄勇,刘佳霖主编 2017
- 《脱硝运行技术1000问》朱国宇编 2019
- 《催化剂制备过程技术》韩勇责任编辑;(中国)张继光 2019
- 《信息系统安全技术管理策略 信息安全经济学视角》赵柳榕著 2020
- 《市政工程基础》杨岚编著 2009
- 《家畜百宝 猪、牛、羊、鸡的综合利用》山西省商业厅组织技术处编著 1959
- 《《道德经》200句》崇贤书院编著 2018
- 《高级英语阅读与听说教程》刘秀梅编著 2019
- 《计算机网络与通信基础》谢雨飞,田启川编著 2019
- 《走出人格陷阱》郑晓斌,徐樟责编;武志红 2020
- 《看图自学吉他弹唱教程》陈飞编著 2019
- 《法语词汇认知联想记忆法》刘莲编著 2020
- 《培智学校义务教育实验教科书教师教学用书 生活适应 二年级 上》人民教育出版社,课程教材研究所,特殊教育课程教材研究中心编著 2019
- 《国家社科基金项目申报规范 技巧与案例 第3版 2020》文传浩,夏宇编著 2019
- 《中国当代乡土小说文库 本乡本土》(中国)刘玉堂 2019
- 《异质性条件下技术创新最优市场结构研究 以中国高技术产业为例》千慧雄 2019
- 《中国铁路人 第三届现实主义网络文学征文大赛一等奖》恒传录著 2019
- 《莼江曲谱 2 中国昆曲博物馆藏稀见昆剧手抄曲谱汇编之一》郭腊梅主编;孙伊婷副主编;孙文明,孙伊婷编委;中国昆曲博物馆编 2018
- 《中国制造业绿色供应链发展研究报告》中国电子信息产业发展研究院 2019
- 《中国陈设艺术史》赵囡囡著 2019
- 《指向核心素养 北京十一学校名师教学设计 英语 七年级 上 配人教版》周志英总主编 2019
- 《《走近科学》精选丛书 中国UFO悬案调查》郭之文 2019
- 《清至民国中国西北戏剧经典唱段汇辑 第8卷》孔令纪 2018
- 《北京生态环境保护》《北京环境保护丛书》编委会编著 2018