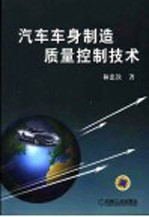
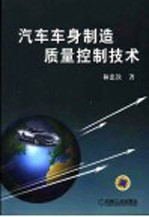
汽车车身制造质量控制技术PDF电子书下载
- 电子书积分:11 积分如何计算积分?
- 作 者:林忠钦著
- 出 版 社:北京:机械工业出版社
- 出版年份:2005
- ISBN:7111158563
- 页数:256 页
第1章 绪论 1
1.1 引言 1
1.2 面向制造过程的车身尺寸偏差控制 2
1.2.1 传统的工序控制的缺陷与在线检测 2
1.2.2 基于偏差诊断的车身尺寸偏差控制 4
1.2.3 基于自适应补偿的车身装配偏差控制 5
1.3 面向设计的车身装配尺寸偏差控制 6
1.3.1 夹具的优化设计 6
1.3.2 车身装配偏差分析与综合 7
1.4 基于偏差流理论的车身装配尺寸偏差控制的系统模型 9
1.5 现代车身制造质量控制体系框架 10
参考文献 10
第2章 白车身制造质量检测与评价方法 13
2.1 引言 13
2.2 基于功能尺寸的白车身制造质量检测方法 13
2.2.1 车身统一基准系统(RPS) 13
2.2.2 白车身检测的功能尺寸系统定义 14
2.2.3 白车身检测的功能尺寸系统构成与作用机制 15
2.2.4 应用实例 18
2.3 基于曲率特征的覆盖件检测规划 21
2.3.1 采样规划原理 22
2.3.2 算法实现 23
2.4 白车身制造过程的统计质量评价 24
2.4.1 制造过程的离线检测 24
2.4.2 白车身制造质量连续改进指数(CII) 29
2.4.3 小样本检测条件下CII指数的计算 30
2.4.4 小样本检测条件下合格率的计算 37
2.5 本章小结 41
参考文献 41
第3章 基于数值模拟的薄板冲压成形质量控制 44
3.1 引言 44
3.2 薄板冲压成形仿真系统 45
3.2.1 计算机软硬件平台 47
3.2.2 体系结构中的关键环节 47
3.3 冲压回弹分析 48
3.3.1 汽车零件的变形及其回弹 48
3.3.2 回弹的影响因素 51
3.3.3 回弹的常用计算方法 52
3.3.4 回弹预测的增量有限元法 55
3.3.5 基于一步模拟的回弹预测方法 59
3.4 回弹控制与补偿方法研究 62
3.4.1 基于变压边力的大弯曲件回弹控制方法 62
3.4.2 基于回弹预测的小曲率件模具型面设计 68
3.5 本章小结 73
参考文献 74
第4章 白车身点焊质量控制方法研究 80
4.1 引言 80
4.2 轿车车身电阻点焊熔核长大过程有限元仿真研究 80
4.2.1 点焊装配的分类 80
4.2.2 电阻点焊过程计算模型 81
4.2.3 点焊过程控制方程组 81
4.2.4 点焊过程有限元模拟 83
4.2.5 电阻点焊热过程对零件变形影响研究 85
4.2.6 试验研究 91
4.3 轿车车身电阻点焊装配过程偏差机理及其仿真的研究 93
4.3.1 车身装配的特点 93
4.3.2 轿车车身装配偏差定义 95
4.3.3 偏差传播的几何分析 95
4.3.4 轿车车身零件多点装配过程偏差有限元仿真 99
4.3.5 应用实例 103
4.4 本章小结 108
参考文献 108
第5章 柔性薄板焊装夹具的优化设计方法 110
5.1 引言 110
5.2 基于CBD的焊装夹具概念设计 111
5.2.1 焊装夹具设计实例相似度 112
5.2.2 焊装夹具设计实例的索引和检索 113
5.2.3 焊装夹具设计实例的修改和存储 116
5.3 面向N-2-1定位的薄板焊装夹具优化设计方法 117
5.3.1 多种群自适应模拟退火-遗传算法 118
5.3.2 多种群自适应模拟退火-遗传算法(SAMGA)算法结构研究 119
5.3.3 基于MATLAB和FEMLAB的SAMGA优化算法工具包 122
5.3.4 焊装夹具的定位误差 123
5.3.5 考虑定位误差时的“N-2-1”定位原理 123
5.4 车身薄板焊装夹具虚拟设计系统 125
5.4.1 车身焊装夹具虚拟设计体系 125
5.4.2 车身焊装夹具虚拟设计系统 129
5.5 应用实例 134
5.5.1 车门内板结构及其装配过程 134
5.5.2 车门内板焊装夹具概念设计 136
5.5.3 车门内板焊装夹具结构设计 137
5.5.4 车门内板焊装夹具优化设计 138
5.6 本章小结 141
参考文献 142
第6章 柔性薄板冲压件检具设计方法 145
6.1 引言 145
6.2 车身检具选型设计方法 145
6.2.1 车身检具设计过程 146
6.2.2 车身检具的特点及其分类 147
6.2.3 车身覆盖件检测特征 148
6.2.4 基于检测特征的车身检具选型设计研究 149
6.2.5 车身检具选型设计应用举例 154
6.3 车身检具结构设计方法 154
6.3.1 车身检具结构特征 155
6.3.2 车身检具特征映射 159
6.3.3 车身检具特征映射系统结构 163
6.3.4 车身检具特征映射功能的实现方法 167
6.3.5 应用举例 168
6.4 柔性薄板冲压件检具优化设计 169
6.4.1 关于柔性零件——检具的基本假设 169
6.4.2 检具的有限元优化分析模型 170
6.4.3 柔性件检具优化设计方法—基于知识的遗传算法 172
6.5 基于ANSYS的薄板冲压件检具优化设计 183
6.5.1 基于APDL的遗传算法优化技术 183
6.5.2 基于知识的遗传算法计算模块 184
6.5.3 ANSYS环境下柔性零件检具优化设计的程序结构 185
6.6 应用实例 186
6.7 本章小结 189
参考文献 190
第7章 基于知识的车身装配尺寸偏差源快速诊断方法 192
7.1 引言 192
7.2 小样本检测数据的处理分析与尺寸控制方法 193
7.2.1 小样本采样条件下相关分析与主成分分析 193
7.2.2 基于多维时间序列分析的车身装配过程预测 194
7.2.3 车身装配过程尺寸控制的系统流程 198
7.3 N-2-1焊装夹具定位失效模型与故障模式匹配方法 199
7.3.1 车身焊装夹具的定位方案与假想失效模式 200
7.3.2 夹具定位单元与测点的几何关系 201
7.3.3 焊接夹具误差样本模型的建立 203
7.3.4 模型参数的确定 208
7.3.5 夹具误差样本模型中的诊断向量与主成分之间的关系 209
7.3.6 夹具故障模式匹配的映射程序 210
7.3.7 基于蒙特卡罗模拟的模型验证 212
7.4 基于知识的车身装配尺寸偏差源诊断系统构造 214
7.4.1 系统结构 214
7.4.2 产品和工艺过程知识库 215
7.4.3 问题识别 219
7.4.4 问题分析 221
7.4.5 误差源定位 222
7.5 本章小结 224
参考文献 224
第8章 轿车车身制造质量控制系统研究应用实例 226
8.1 引言 226
8.2 白车身装配工艺系统 226
8.3 白车身装配过程偏差源智能诊断系统软件 230
8.3.1 软件总体结构 230
8.3.2 主要模块功能和界面 230
8.4 案例分析实例 234
8.4.1 某轿车后围板尺寸波动诊断实例 235
8.4.2 某三厢车前围尺寸偏差及波动案例研究 241
8.4.3 某轿车前翼子板钻孔工位钻孔波动案例 251
- 《中国制造业绿色供应链发展研究报告》中国电子信息产业发展研究院 2019
- 《高含硫气藏开发腐蚀控制技术与实践》唐永帆,张强 2018
- 《智能制造高技能人才培养规划丛书 ABB工业机器人虚拟仿真教程》(中国)工控帮教研组 2019
- 《钢铁行业污染特征与全过程控制技术研究》周长波等 2019
- 《生活垃圾焚烧飞灰中典型污染物控制技术》朱芬芬等编著 2019
- 《海河干流水环境质量与经济发展模式研究》于航白景峰,张春意 2019
- 《玉米淀粉绿色精益制造 新工艺、新设备、新理念》佟毅 2018
- 《钢铁烧结烟气多污染物过程控制原理与新技术》甘敏,范晓慧著 2019
- 《大众汽车维修资料全书 2008-2018款车型》瑞佩尔主编 2019
- 《真菌毒素控制集成解决方案 第二届MycoKey国际真菌毒素大会论文集》冯洁 2018
- 《九型人格 认识自我看懂他人》申屠增群责编;林忠儒,黎得如 2020
- 《清代易学史 上》林忠军,张沛,赵中国等著 2018
- 《我的河山 抗日正面战场全纪实 人物》陈钦著 2013
- 《剑胆琴心 辛亥先锋秋瑾》耿彦钦著 2012
- 《勃列日涅夫时代》(俄)姆列钦著;王尊贤译 2013
- 《桑塔纳轿车使用与维修》林忠等编著 2000
- 《龙脉寻踪 中华远古文明疑辨录 3》仓林忠著 2010
- 《舞台艺术摄影技巧漫谈》周文钦著 2012
- 《译林百家》符家钦著 2003
- 《怪屋》郑允钦著 1995
- 《指向核心素养 北京十一学校名师教学设计 英语 七年级 上 配人教版》周志英总主编 2019
- 《北京生态环境保护》《北京环境保护丛书》编委会编著 2018
- 《高等教育双机械基础课程系列教材 高等学校教材 机械设计课程设计手册 第5版》吴宗泽,罗圣国,高志,李威 2018
- 《指向核心素养 北京十一学校名师教学设计 英语 九年级 上 配人教版》周志英总主编 2019
- 《高等院校旅游专业系列教材 旅游企业岗位培训系列教材 新编北京导游英语》杨昆,鄢莉,谭明华 2019
- 《中国十大出版家》王震,贺越明著 1991
- 《近代民营出版机构的英语函授教育 以“商务、中华、开明”函授学校为个案 1915年-1946年版》丁伟 2017
- 《新工业时代 世界级工业家张毓强和他的“新石头记”》秦朔 2019
- 《智能制造高技能人才培养规划丛书 ABB工业机器人虚拟仿真教程》(中国)工控帮教研组 2019
- 《AutoCAD机械设计实例精解 2019中文版》北京兆迪科技有限公司编著 2019