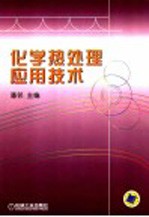
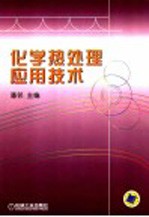
化学热处理应用技术PDF电子书下载
- 电子书积分:14 积分如何计算积分?
- 作 者:潘邻主编;吴懿平,林峰,夏春怀,陶锡麒,温浚沂,詹汉明编写
- 出 版 社:北京:机械工业出版社
- 出版年份:2004
- ISBN:7111146417
- 页数:419 页
1.1 化学热处理的基本过程 1
1.1.1 渗剂的分解 1
第1章 化学热处理基础 1
1.1.2 活性原子在工件表面的吸收过程 4
1.1.3 化学热处理中的扩散过程 6
1.2 扩散层的形成规律 11
1.2.1 扩散层的形成过程及扩散层组织 11
1.2.2 温度和时间对扩散层深度的影响 12
1.3.1 新材料研制 14
1.3.2 改变化学热处理的工艺过程控制 14
1.3 加速化学热处理过程的途径 14
1.3.3 多元共渗 15
1.3.4 催渗技术 15
1.4 化学热处理后渗层的性能评估 16
1.5 化学热处理分类 18
参考文献 19
第2章 渗碳及碳氮共渗 20
2.1 钢的渗碳 20
2.1.1 渗碳原理 20
2.1.2 常用渗碳钢及其预处理 23
2.1.3 气体渗碳 30
2.1.4 液体渗碳、固体渗碳及其他渗碳方法 42
2.1.5 渗碳后的热处理 48
2.1.6 渗碳层的组织和性能 54
2.1.7 渗碳件质量检查 59
2.1.8 渗碳件常见缺陷及防止措施 63
2.1.9 应用实例 67
2.2 钢的碳氮共渗 70
2.2.1 碳氮共渗原理 70
2.2.2 碳氮共渗用钢及其热处理 71
2.2.3 气体碳氮共渗 74
2.2.4 液体碳氮共渗 78
2.2.5 碳氮共渗件的力学性能 80
2.2.6 碳氮共渗件的质量检查与缺陷分析 84
2.2.7 应用实例 89
参考文献 95
第3章 渗氮及其多元共渗 96
3.1 渗氮及其多元共渗原理 96
3.1.1 渗氮及其多元共渗的发展、目的及意义 96
3.1.2 渗氮原理 97
3.1.3 氮碳共渗原理 100
3.1.4 盐浴硫氮碳共渗原理 102
3.2 渗氮及其多元共渗设备 103
3.2.1 气体渗氮及其多元共渗设备 103
3.2.2 盐浴氮碳共渗及硫氮碳共渗炉 104
3.3 渗氮及多元共渗用钢及其预处理 105
3.4.1 渗氮介质 108
3.4 渗氮 108
3.4.2 气体渗氮工艺参数及操作过程 109
3.4.3 结构钢与工具钢的渗氮 110
3.4.4 不锈钢与耐热钢的渗氮 113
3.4.5 铸铁的渗氮 115
3.4.6 非渗氮部位的保护 115
3.4.7 其他渗氮方法 116
3.5 氮碳共渗 118
3.5.1 气体氮碳共渗 118
3.5.2 盐浴氮碳共渗 120
3.5.3 固体氮碳共渗 122
3.6.1 氧氮共渗 123
3.5.4 奥氏体氮碳共渗 123
3.6 含氮多元共渗 123
3.6.2 硫氮共渗 124
3.6.3 硫氮碳共渗 124
3.6.4 QPQ处理 126
3.6.5 盐浴氮碳钒共渗 126
3.7 渗氮及其多元共渗层的组织与性能 127
3.7.1 气体渗氮层的组织与性能 127
3.7.2 氮碳共渗层的组织与性能 134
3.7.3 其他多元共渗层的组织与性能 136
3.8 渗氮及其多元共渗常见缺陷及预防措施 139
3.8.1 气体渗氮常见缺陷产生原因及预防措施 139
3.8.2 氮碳共渗常见缺陷产生原因及预防措施 140
3.8.3 硫氮碳共渗常见缺陷产生原因及预防措施 141
3.9 应用实例 141
3.9.1 气体渗氮 141
3.9.2 真空脉冲渗氮 142
3.9.3 预氧化快速气体渗氮 143
3.9.4 盐浴硫氮碳共渗 143
3.9.5 气体氮碳共渗 145
3.9.6 加压气体氮碳共渗 145
3.9.7 QPQ处理 145
参考文献 145
4.1.1 渗硼工艺 147
4.1 渗硼 147
第4章 渗硼和渗金属 147
4.1.2 钢铁件的渗硼工艺及特点 151
4.1.3 其他金属渗硼 157
4.2 渗硅 159
4.2.1 渗硅工艺 159
4.2.2 渗硅的影响因素 162
4.2.3 渗硅层的组织和性能 163
4.3 渗铬、钒、铌、钛 165
4.3.1 渗金属工艺方法 166
4.3.2 渗金属层的组织 171
4.3.3 渗金属层的性能 174
4.3.4 渗金属层的质量检验、常见缺陷及防止措施 177
4.4.1 工艺方法 178
4.4 渗锌和渗铝 178
4.4.2 渗层的组织和性能 181
4.4.3 渗锌、渗铝工件的质量检测、常见缺陷及防止措施 185
4.5 多元共渗和复合渗 185
4.5.1 硼铝共渗 185
4.5.2 硼铬共渗 187
4.5.3 硼硅共渗 189
4.5.4 铬铝共渗 189
4.6 渗硼和渗金属应用实例 190
参考文献 197
5.1.1 辉光放电 198
5.1 离子化学热处理基础 198
第5章 离子化学热处理 198
5.1.2 离子化学热处理原理 201
5.2 离子化学热处理设备及操作过程 203
5.2.1 离子化学热处理设备概述 203
5.2.2 离子化学热处理设备电气控制系统 204
5.2.3 真空炉体及配套系统 218
5.2.4 离子化学热处理设备的维护及常见故障排除 225
5.3 离子渗氮及氮碳共渗 227
5.3.1 离子渗氮炉及其基本操作过程 227
5.3.2 离子渗氮工艺 229
5.3.3 离子渗氮层的组织与性能 236
5.3.4 离子氮碳共渗 245
5.3.5 钛及钛合金离子渗氮 248
5.3.6 稀土催渗离子渗氮技术 249
5.4 离子渗碳及碳氮共渗 251
5.4.1 离子渗碳设备及其基本操作过程 251
5.4.2 离子渗碳工艺 252
5.4.3 离子碳氮共渗 253
5.5 离子渗硫及含硫介质的多元共渗 254
5.5.1 低温离子渗硫 254
5.5.2 离子硫氮共渗及离子硫氮碳共渗 255
5.5.3 离子渗硫及其多元共渗层的组织与性能 257
5.6.1 双层辉光离子渗金属 259
5.6 离子渗金属 259
5.6.2 其他离子渗金属方法 260
5.7 离子渗硼 261
5.8 离子化学热处理应用实例 262
参考文献 266
第6章 化学热处理件的质量检测方法 267
6.1 原材料化学成分分析 267
6.1.1 钢的化学分析方法 267
6.1.2 钢的火花检验 269
6.1.3 光谱分析 271
6.2 渗层金相组织检验的目的和试样 272
6.2.1 金相检验的目的 272
6.2.3 金相试样的制备 273
6.2.2 金相试样的制备要求 273
6.3 渗层微观组织及成分分析方法 280
6.3.1 光学金相显微镜 280
6.3.2 高温金相显微镜 282
6.3.3 电子显微镜 283
6.4 力学性能试验 285
6.4.1 硬度试验 285
6.4.2 静拉伸试验 291
6.4.3 压缩、弯曲及扭转试验 293
6.4.4 冲击试验 295
6.4.5 疲劳试验 297
6.4.6 接触疲劳 299
6.4.7 金属的摩擦与磨损 301
6.5 金属腐蚀试验 304
6.5.1 金属腐蚀的分类 304
6.5.2 金属腐蚀的评定方法 305
6.6 无损检测 306
6.6.1 内部缺陷检测 306
6.6.2 表层缺陷检测 309
6.6.3 材质与热处理质量的无损检测 311
参考文献 313
第7章 其他表面改性技术 314
7.1 气相沉积技术 314
7.1.1 概述 314
7.1.2 物理气相沉积 315
7.1.3 化学气相沉积 329
7.1.4 气相沉积技术的工业应用 335
7.2 离子注入技术 339
7.2.1 离子注入技术的原理与特点 339
7.2.2 离子注入装置 340
7.2.3 离子注入技术在微电子中的应用 342
7.2.4 离子注入技术在机械工业中的应用 344
7.2.5 离子注入技术在生物和医疗方面的应用 346
7.2.6 离子注入新技术 347
7.3 热浸镀技术 350
7.3.1 概述 350
7.3.2 热浸镀锌 353
7.3.3 热浸镀铝 370
7.3.4 热浸镀锡 376
7.3.5 热浸镀铅 380
7.4 激光熔覆及激光表面合金化技术 382
7.4.1 激光表面改性基础 382
7.4.2 激光熔覆 388
7.4.3 激光表面合金化 400
参考文献 403
附录 405
附录A 常用硬度值换算表 405
附录B 国内外化学热处理常用钢钢号对照表 411
附录C 热处理金相组织检查常用侵蚀剂 415
附录D 我国现行化学热处理相关标准目录 418
- 《钒产业技术及应用》高峰,彭清静,华骏主编 2019
- 《现代水泥技术发展与应用论文集》天津水泥工业设计研究院有限公司编 2019
- 《异质性条件下技术创新最优市场结构研究 以中国高技术产业为例》千慧雄 2019
- 《Prometheus技术秘笈》百里燊 2019
- 《英汉翻译理论的多维阐释及应用剖析》常瑞娟著 2019
- 《中央财政支持提升专业服务产业发展能力项目水利工程专业课程建设成果 设施农业工程技术》赵英编 2018
- 《药剂学实验操作技术》刘芳,高森主编 2019
- 《林下养蜂技术》罗文华,黄勇,刘佳霖主编 2017
- 《脱硝运行技术1000问》朱国宇编 2019
- 《催化剂制备过程技术》韩勇责任编辑;(中国)张继光 2019
- 《指向核心素养 北京十一学校名师教学设计 英语 七年级 上 配人教版》周志英总主编 2019
- 《北京生态环境保护》《北京环境保护丛书》编委会编著 2018
- 《高等教育双机械基础课程系列教材 高等学校教材 机械设计课程设计手册 第5版》吴宗泽,罗圣国,高志,李威 2018
- 《指向核心素养 北京十一学校名师教学设计 英语 九年级 上 配人教版》周志英总主编 2019
- 《高等院校旅游专业系列教材 旅游企业岗位培训系列教材 新编北京导游英语》杨昆,鄢莉,谭明华 2019
- 《中国十大出版家》王震,贺越明著 1991
- 《近代民营出版机构的英语函授教育 以“商务、中华、开明”函授学校为个案 1915年-1946年版》丁伟 2017
- 《新工业时代 世界级工业家张毓强和他的“新石头记”》秦朔 2019
- 《智能制造高技能人才培养规划丛书 ABB工业机器人虚拟仿真教程》(中国)工控帮教研组 2019
- 《AutoCAD机械设计实例精解 2019中文版》北京兆迪科技有限公司编著 2019