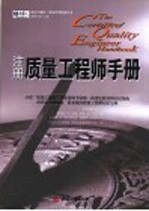
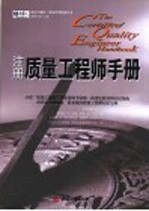
注册质量工程师手册PDF电子书下载
- 电子书积分:16 积分如何计算积分?
- 作 者:(美)唐纳德·W.本堡(Don Benbow)等著;克劳士比中国学院·克劳士比管理顾问中心译
- 出 版 社:北京:中国城市出版社
- 出版年份:2003
- ISBN:7507415120
- 页数:515 页
· 写在前面 2
· 图表目录 2
第一部分 质量领导者 2
目录 2
· 序言 2
第1章 质量领导 2
· 编著者致谢 2
1.1 引言和范围 3
1.2 知识体系大纲 3
1.3.1 方针展开 3
1.3 改进质量的管理系统 3
1.3.2 目标设定 4
1.3.3 策划和进度安排 5
第一部分 5
表1.1 设立目标的“聪明法”S.M.A.R.T.W.A.Y 5
图表目录 5
图1.1.b 计划实施进度表 6
图1.1.a 行动计划 6
1.3.4 项目管理 7
表1.2 某典型项目策划的结果 8
图1.2 工作分解结构(部分) 10
图1.3 甘特图 11
图1.4 关键路径法(CPM)图 12
1.3.5 质量信息系统 13
1.4 领导原则和技巧 14
1.4.1 开发、建立和组织团队 14
图1.5 互相联系的团队结构 15
1.4.2 领导质量创新活动 18
1.5.1 团队环境中的促进者角色和责任 19
1.5 促进原则和技巧 19
1.5.2 意见处理和决策制订 22
图1.6 名义群体技术评分表 23
图1.7 多轮投票法 24
1.6 本章总结 25
第2章 质量管理 26
2.1.1 引言和范围 27
2.1.2 道德困境 27
2.1 职业品行和ASQ职业道德守则 27
2.2 培训 29
2.2.1 引言和范围 29
2.1.3 道德小结 29
图2.1 教育与培训 30
图2.2 宗师们的语录 30
2.2.2 对培训知识的需要 31
2.2.3 需要分析 31
图2.3 基本沟通模型 32
2.2.4 计划制订 33
图2.4 ANSI/ASQC Z1.11-1996培训模型 34
图2.5 培训循环图 35
2.2.5 教材准备 35
2.2.6 有效性测定 36
图2.6 评价层次 36
2.2.7 培训小结 37
2.3.1 引言和范围 38
2.3.2 质量经济学 38
2.3 质量成本 38
2.3.3 质量成本系统的目标 39
2.3.4 质量成本的管理 40
表2.1 按类别划分的质量成本要素 41
2.3.5 质量成本类别 41
2.3.6 实施 43
2.3.8 质量成本总结和分析 44
2.3.7 质量成本资料搜集 44
2.3.10 使用质量成本 45
2.3.9 质量成本报告 45
2.3.11 质量改进和削减质量成本 46
2.3.12 质量成本小结 47
2.4.2 质量的好处 48
2.4 质量哲学和方法 48
2.4.1 引言和范围 48
2.4.3 质量的历史 49
2.4.4 菲利浦·B·克劳士比(Philip B.Crosby) 50
2.4.5 W·爱德华兹·戴明(W.Edwards Deming) 50
表2.2 戴明的14要点 51
2.4.6 乔治·D·爱德华兹(George D.Edwards) 52
2.4.7 阿曼德·V·费根堡姆(Amand V.Feigenbaum) 53
2.4.8 石川馨(Kaoru Ishikawa) 54
2.4.9 约瑟夫·M·朱兰(Joseph M.Juran) 54
2.4.10 沃尔特·A·休哈特(Walter A.Shewhart) 55
2.4.11 田口玄一(Genichi Taguchi) 56
2.4.13 质量哲学和方法小结 57
2.4.12 质量的定义 57
2.5.2 知识体系大纲(第Ⅰ节部分H小节) 59
2.5.3 顾客需要和期望 59
2.5 顾客关系、期望、需要和满意 59
2.5.1 引言和范围 59
2.5.4 质量功能展开(QFD) 60
图2.7 QFD图:某文件处理过程的质量屋 61
图2.8 输入—输出要求矩阵 62
图2.9 轿车门的质量屋 63
表2.3 对顾客价值的看法 64
2.5.5 顾客驱动的质量 64
2.5.6 顾客关系、期望、需要和满意小结 65
2.6.1 引言和范围 66
2.6 供应商关系和管理方法论 66
2.6.2 采购标准和规范 66
2.6.3 调查、审核与检验 67
2.6.4 供应商关系和管理方法论小结 73
2.7 本章总结 73
第二部分 质量策划、实施和控制 78
第3章 质量体系建立、实施和验证 78
3.2 知识体系大纲 79
3.3 质量体系的要素 79
3.1 引言和范围 79
第二部分 80
图3.1 产品生命周期和质量体系要素 80
3.3.1 质量体系的文件管理 82
图3.2 质量手册和文件的层次 82
3.4 ANSI/ISO/ASQ Q 9000-2000 83
3.5 质量体系实施 85
图3.3 体系实施和改进循环 86
3.7.1 审核目标 87
3.6 国内和国际标准 87
3.7 质量审核 87
3.7.2 质量审核的类型 88
3.7.3 角色和责任 88
3.7.4 策划和执行 89
3.7.5 审核报告和跟踪审核 90
3.8 本章总结 91
第4章 质量策划 92
4.1 引言和范围 93
4.2 知识体系大纲 93
图4.1 最佳质量成本模型 94
4.3 战略质量策划 95
图4.2 战略质量计划的有效性测试 96
4.4 战术质量策划 98
图4.3 策划与执行 98
图4.4 产品质量策划时间表 99
4.5 先期的质量策划原则 100
4.5.1 第1阶段:计划和定义 101
图4.5 在质量策划中使用展开表 101
4.5.2 第2阶段:产品设计和开发 102
4.5.3 第3阶段:过程设计和开发 105
图4.6 控制计划样例:第1页 108
图4.7 控制计划样例:第2页 109
4.5.4 第4阶段:产品和过程确认 110
图4.8 狩野质量模型 112
4.6 市场研究和质量工程 112
4.7 本章总结 113
第5章 材料控制 115
5.2 知识体系大纲 116
5.3 分类管理 116
5.1 引言和范围 116
5.4 材料的标识 117
5.4.1 标识的原则 117
5.4.2 例行手续 117
5.5.1 样品真实可靠性 118
5.5.2 批次控制 118
5.5 保持产品的真实可靠性 118
5.5.3 变更控制 119
5.5.4 结构控制 119
5.6.1 原理 120
5.6 可追溯性 120
5.6.2 要考虑的因素 121
5.7 处置 122
5.7.1 材料评审委员会 122
表5.1 关于原材料评审委员会工作的标准 123
5.7.2 产品召回 123
5.8 本章总结 124
第6章 检验、测试和接收抽样 125
6.3 检验 126
6.1 引言和范围 126
6.2 知识体系大纲 126
6.3.1 检验的用途 127
6.3.2 质量特性 127
6.3.3 缺陷分类 128
6.4 抽样检验与百分之百检验 129
6.4.2 检验员培训 130
6.4.1 检验员资格 130
6.4.3 检验绩效中的人为因素 131
6.4.4 检验计划编制 132
6.5 试验 133
6.6 接收抽样 134
6.5.1 非破坏检验(NDT)技术 134
6.6.2 操作特性(OC)曲线 135
6.6.1 逐批保护与平均质量保护 135
图6.1 操作特性(OC)曲线 136
6.6.3 计数接收抽样 137
图6.2 平均检出质量曲线,当N=∞,n=50,c=3时 138
图6.3 当接收数(c)保持恒定时,对变化样本大小(n)的(OC)曲线的影响 140
图6.4 当样本大小(n)保持恒定时,变化接收数(c)的影响 140
图6.5 当接收数(c)和样本大小(n)保持恒定时,变化批量(N)的影响 141
图6.6 对样本大小等于批量10%的抽样方案的操作特性曲线 142
6.6.4 计数抽样方案的类型 142
图6.7 对n1=75,c1=0,r1=3,n2=75,c 2=3,R2=3的二次抽样方案的OC曲线 144
图6.8 二次抽样方案的平均检出质量曲线 144
图6.9 二次抽样方案的平均抽样个数曲线 146
6.7.1 检验水平 147
6.7 ANSI/ASQC Z1.4-1993 147
图6.10 对正常、加严和放宽检验的操控准则 148
6.8 道奇·罗米格——抽样表 150
6.9 计量抽样方案 151
图6.11 ANSI/ASQC Z 1.9—1993的结构和组织 152
6.10 ANSI/ASQC Z1.9-1993 152
6.10.1 变异性未知——极差法 153
6.10.2 变异性未知——标准偏差法 154
6.11 序贯抽样方案 155
图6.12 某序贯抽样方案的判定范围 156
6.12 连续抽样方案 157
6.12.1 连续抽样方案的类型 158
6.13 计量抽样方案的其他方法 160
6.13.1 标准偏差为已知时的计量方案 160
6.13.2 给定α和β值时的样本大小 161
6.14 本章总结 163
图6.13 ANSI/ASQCZ1.4-1993表8:放宽检验的限制数表 164
图6.14 ANSI/ASQC Z 1.4-1993表1:样本大小代码字母检验表 165
图6.15 ANSI/ASQC Z 1.4-1993表2-A:正常检验的一次抽样方案 166
图6.16 ANSI/ASQC Z 1.4-1993表3-A:正常检验的二次抽样方案 167
图6.17 ANSI/ASQC Z 1.4-1993表4-A:正常检验的多次抽样方案 168
图6.18 ANSI/ASQC Z 1.9-1993表A-2:样本大小代码字母表 170
图6.19 ANSI/ASQC Z 1.9-1993表C-1:基于变异性未知(单倍规格限—表1)的正常和加严检验方案的主表 171
图6.20 ANSI/ASQC Z 1.9-1993表B-5:使用标准偏差法估算批百分不合格率表 172
图6.21 ANSI/ASQC Z 1.9-1993表B-3:基于变异性未知(双倍规格限和表2—单倍规格限)的正常和加严检验方案的主表 173
第三部分 技术系统 176
第7章 测量系统 176
7.3 测量的来龙去脉 177
7.1 引言和范围 177
7.2 知识体系大纲 177
7.4 测量的标准 178
7.5 关于标准 178
7.5.1 基本单位的定义 179
第三部分 179
表7.1 国际系统的基本单位 179
图7.1 标准按级别的分类 179
表7.2 SI基本单位定义 180
图7.2 SI单位及名称间关系 181
7.5.2 物理制品 182
7.5.3 书面标准 182
7.6 测量过程 182
7.6.1 一般特性 182
7.6.2 测量系统 183
7.7 测量的基本概念 185
7.7.1 测量误差 185
图7.3 影响测量过程的因素 186
7.7.4 灵敏度和可读性 187
7.7.2 准确度 187
7.7.3 精度 187
7.7.6 对准确度和精度的需要 188
7.7.7 重复性和再现性 188
7.7.5 一致性 188
7.7.8 准确度的评估 189
7.7.10 测量保证 191
7.7.9 溯源性 191
7.8 校准 192
7.8.1 校准控制系统 192
7.9 制造业中的尺寸测量和标准 193
7.9.1 控制产品质量 194
7.10.1 测量标准 195
7.11.1 长度和角度测量 195
7.11 测量技术 195
7.10 尺寸测量 195
表7.3 工业长度和角度测量的典型标准和仪器 196
7.12 测量仪器的选择 197
7.12.3 布局和定位装置 198
7.12.2 角度测量仪器 198
7.12.1 基本线性测量仪器 198
7.12.4 量具 199
7.12.5 千分表 199
7.13 表面质量测量 199
7.12.6 比较仪 199
7.12.7 块规 199
图7.4 ISO/R468表面粗糙度参数 200
7.13.1 表面的数值估算 200
图7.5 表面粗糙度的其他参数 201
7.13.2 测量的触针系统 201
7.14 圆度的测量 202
7.14.1 什么是“不圆度” 202
7.14.2测量方法 203
图7.6 圆度测量仪器的两种类型:(a)台面旋转(b)工件旋转 203
图7.7 选定中心的四种方法 204
7.15 量具重复性和再现性 205
7.15.1 零件对零件的偏差 206
7.15.2 总偏差 207
7.16 尺寸和公差 208
7.16.1 几何公差 209
图7.8 某些几何允许公差符号 209
7.17.1 坐标测量仪的分类 210
7.17 坐标测量仪 210
图7.9 坐标测量仪分类 212
7.17.2 影响仪器性能的因素 213
7.18 本章总结 214
第8章 可靠性和维修性工程 217
8.1 引言和范围 218
8.2 知识体系大纲 219
8.3 可靠性定义和估算 219
表8.1 某些时间间隔中的故障数 220
表8.2 风险率、概率密度函数和可靠性 221
图8.1 不同时间的风险率×? 221
图8.2 不同时间的概率密度函数×? 222
图8.3 不同时间的可靠性函数 222
8.4 故障模式 222
图8.4 不同时间的分布函数 223
图8.5 普通故障率模型(浴盆曲线) 223
图8.6 恒定故障率的概率密度函数 224
图8.7 恒定故障率的可靠性函数 224
8.4.1 恒定故障率 224
图8.8 带有不同形状和标度参数的威布尔模型的概率密度函数 225
8.4.2 降低或提高故障率 225
图8.9 带有不同形状和标度参数的威布尔模型的风险率函数 226
8.4.3 平均故障寿命和平均残余寿命 226
8.5 系统可靠性 227
图8.10 典型的串联系统 227
8.5.1 串联系统 227
图8.11 典型的并联系统 228
8.5.2 并联系统 228
8.7 潜在故障模式的识别 229
8.7.1 环境压力屏蔽(ESS) 229
8.6 可靠性故障分析和报告 229
8.7.2 故障树分析(FTA) 230
8.8 维修性 232
图8.12 简单故障树 232
8.9 本章总结 234
第9章 故障模式和影响分析 235
9.2 知识体系大纲 236
9.3.1 为FMEA选择标准 236
9.1 引言和范围 236
9.3 理解FMEA 236
9.3.2 策划FMEA 237
9.3.5 FMEA的输入 238
9.3.4 FMEA团队成员 238
9.3.3 单个责任点的建立 238
9.3.8 FMEA的基本步骤 239
9.3.6 FMEA和其它质量工具 239
9.3.7 FMEA的输出 239
9.3.9 与各个潜在故障有关的风险的量化 240
9.3.10 风险的组成 240
9.3.11 根据风险序数(RPN)采取行动 241
9.3.12 我们要对故障模式或其原因评分吗 242
9.3.13 当质量工程师遇到FMEA 242
9.3.14 FMEA设计和过程 243
图9.1 FMEA空白设计表格 244
图9.2 FMEA空白过程表格 245
表9.1 FMEA设计严酷度判别标准 247
表9.3 FMEA设计发生频度判别标准 248
表9.2 FMEA过程严酷度判别标准 248
表9.5 FMEA设计可检测度判别标准 249
表9.4 FMEA过程发生频度判别标准 249
表9.6 FMEA过程可检测度判别标准 250
9.3.15 对采取纠正措施的最后说明 251
9.3.16 评估危险程度 251
9.3.17 使用FMEA要注意的一件事 252
9.4 本章总结 252
9.3.18 设计和处理FMEA的实例 252
图9.3 FMEA设计实例 254
图9.4 FMEA过程实例 254
第四部分 解决问题 258
第10章 解决问题与质量改进 258
10.2 知识体系大纲 259
10.1 引言和范围 259
10.3 方法 260
10.3.1 改善(Kaizen) 260
10.3.2 PDSA循环 261
图10.1 基本的“计划——实施——研究——处理”循环 261
第四部分 261
10.3.3 过程再造 262
10.4 解决问题的方法 262
图10.2 问题解决的7个阶段 262
10.4.1 第1阶段:识别机会(问题识别) 263
10.4.2 第2阶段:分析当前的过程 264
10.4.3 第3阶段:制定最佳解决方案(纠正) 266
10.4.4 第4阶段:实施变革 267
10.4.6 第6阶段:将解决方案标准化(再发生控制) 268
10.4.5 第5阶段:研究结果 268
10.4.7 第7阶段:计划将来(有效性评估) 269
表10.1 波纹焊接过程的控制计划 269
表10.2 过程鉴定检查表 269
10.5 预防措施 270
10.5.2 培训 270
10.5.3 防错 270
10.5.1 改进的机会 270
10.5.4 验证预防措施的有效性 271
10.6 克服质量改进的障碍 272
10.7 本章总结 274
第11章 传统的解决问题工具 275
11.1 引言和范围 276
11.2 知识体系大纲 276
11.3.1 流程图 277
11.3 理解图表工具 277
图11.1 流程图的4个主要符号 278
11.3.2 检查表 279
图11.2 回归分析法 279
图11.3 通过检查表作帕累托图 280
11.3.3 直方图 281
11.3.4 帕累托图 282
图11.4 通过检查表作帕累托图 282
图11.5 通过检查表作帕累托图 283
11.3.5 因果图 284
图11.6 因果图/模块 285
图11.7 因果图:公共汽车安全差异 286
11.3.7 连线图 286
11.3.6 控制图 286
图11.8 连线图 287
11.3.8 散布图 288
图11.9 散布图确定的5种可能关系 288
图11.10 培训时间(与)误差 289
表11.1 数据图 289
11.4 本章总结 290
第12章 解决问题和质量改进——管理和策划工具 291
12.1 引言和范围 292
12.2 知识体系大纲 293
12.3.1 亲和图 294
12.3 质量工具 294
图12.1 学生焦点小组亲和图 295
12.3.2 关联图(相关图) 295
图12.2 存货支持子过程关联图 297
12.3.3 树图 297
图12.3 简化的存货断供故障树 298
图12.4 局部制造成本改进目标树 299
12.3.4 过程决策程序图 300
图12.5 验收/贮存/供货子过程的PDPC 302
表12.1 验收/贮存/供货PDPC的问题、可能的根本原因和一般影响结论 303
12.3.5 矩阵图 303
图12.6 质量功能展开矩阵图 304
12.3.6 优先顺序矩阵 305
表12.2 存货支持改进过程的活动、顺序和持续时间 306
12.3.7 活动网络图法(活动网络图和箭条图) 306
图12.7 简化的CPM进度网络——存货支持改进实施 307
表12.3 存货支持改进计划进度安排细节 308
12.3.8 过程示意图 309
图12.8 企业层次的过程示意图 311
图12.9 形象化替代方案——改进了的子过程示意图/PDPC 312
12.3.9 过程价值链(PVC)图 312
图12.10 普通的生产系统过程价值链图 313
12.3.10 标杆学习 314
图12.11 标杆学习和创造性思维 315
12.4 本章总结 317
第五部分 统计工具 321
第13章 概率和统计学简介 321
13.2 知识体系大纲 322
13.3 描述性统计学——数据分析的图表方法 322
13.3.1 频率分布图、描点图和直方图 322
13.1 引言和范围 322
第五部分 323
图13.1 频率分布、描点图和直方图 323
13.3.3 干叶图、百分比图和方框散点图 324
图13.2 累积频率分布图 324
13.3.2 累积频率分布 324
图13.5 方框散点图 325
图13.3 茎叶图 325
图13.4 柱线图 325
图13.6 多重方框散点图实例 326
13.4.2 数据类型 327
13.4 测量标度 327
13.4.1 自动化测量 327
13.4.5 正态概率曲线图 328
13.4.4 数据编码 328
13.4.3 数据准确度和真实可靠性 328
图13.7 根据正态概率对非正态数据作概率图 329
13.4.6 威布尔曲线图 329
13.5 概率简介 330
图13.8 威布尔概率曲线 331
13.5.1 中心极限定理 335
13.5.2 均值的抽样分布 336
13.6 概率分布 336
13.6.1 离散型分布 336
图13.9 正态曲线实例 338
13.6.2 连续变量的分布 338
图13.10 正态密度函数 339
表13.1 某些分布的公式、均值和方差 341
13.7 本章总结 342
第14章 统计判定 343
14.2 知识体系大纲 344
14.1 引言和范围 344
14.3 点估计和置信区间 344
14.3.1 假设和稳健性 346
14.5 假设检验 348
14.4 统计容许区间 348
14.6.1 单因子方差分析 355
14.6 方差分析(ANOVA) 355
14.6.2 双因子方差分析 358
14.6.4 分析研究 364
14.6.3 枚举研究 364
14.6.5 统计显著性与实际显著性 364
14.7 为变量间关系建立模型 365
14.7.1 线性回归 365
图14.1 散点图 365
图14.2 r值示意图 367
14.7.3 归和相关推论 368
14.7.2 多元线性回归 368
14.8 错误类型和功效 369
14.8.1 操作特性(OC)曲线 370
图14.3 操作特性曲线 371
图14.4 AQL=1.5%的方案的理想操作特性曲线 371
图14.5 OC曲线 372
14.9 本章总结 372
第15章 试验设计 373
15.1 引言和范围 374
15.2 知识体系大纲 374
15.3.1 变异性问题:如何降低噪音 375
15.3.2 稀缺资源问题:最大限度地利用资金 375
15.3 预先考虑 375
15.3.3 管理支持问题 376
15.4 试验策略 376
15.5.1 选择要研究哪些因子 378
15.5 第一阶段:过程分析 378
15.5.2 选择响应 379
表15.1 裁判打分转换为标准分 380
15.5.3 决定是否汇总计算原始响应 380
15.5.4 确定试验是否应该分块试验 381
15.5.5 选择最合适的教学模型 382
图15.1 两个不同的双因子试验结果的轮廓图 383
15.6 第二阶段:选择设计方案 385
15.6.1 设计特性 385
图15.2 拉丁方设计 386
15.6.2 设计类型 387
图15.3 某个2×2全部因子设计 387
表15.2 二个水平全部因子试验中因子数目是怎样影响试验次数的 388
图15.4 ?因子设计的半分数,有的作者称其为?设计,因为它有?试验 389
15.7 第三阶段:完成试验 389
15.8 第四阶段:分析试验数据 390
图15.5 结果统计及方框图 391
表15.3 上下班交通时间试验的全部40个结果列表 391
图15.6 新旧两条路线的方框图 392
图15.7 喷射模塑试验的散点图 392
图15.8 上下班交通时间的影响图和置信区间 393
图15.9 对时间影响和路影响的95%置信区间 393
表15.4 适用模型系数,变换时间实例 394
15.8.1 系数和方差分析表 394
表15.5 上下班交通时间例题的方差分析 395
图15.10 喷射模塑实例中文的变异来源 395
15.8.2 简化模型的优点 396
15.9 第五阶段:得出结论 396
15.9.1 对比 396
15.9.2 预测 397
表15.6 每分钟行驶速度对比 397
图15.11 每分钟行驶速度对比 397
15.9.3 评价影响 398
15.9.4 建立一个损失函数(效用函数) 398
图15.12 上下班交通时间的预测和95%的累积置信区间 398
15.10 第六阶段:跟踪和下一步计划 399
表15.7 因子的最小损失和最佳值 399
15.9.5 使用损失函数和模型进行最优化 399
15.11.2 多因子设计 400
15.10.1 验证研究 400
15.11 设计分类 400
15.11.1 单因子设计 400
图15.13 某个23全部因子设计数据收集表 401
图15.14 包括试验平均次数的23全部因子数据收集表 402
15.11.3 主影响 402
图15.15 23的半分数 403
15.12 本章总结 404
第16章 统计过程控制 405
16.3 管理者的角色和职责 406
16.2 知识体系大纲 406
16.1 引言和范围 406
16.3.1 过程分析 407
16.4 控制图的基本原理通论 408
16.4.1 决策准备 410
图16.1 控制图选择的决策树 411
16.4.2 变量控制图 411
图16.2 ?—R控制图 412
图16.3 某巧克力制造过程的传送带 413
图16.4 控制图(作图表示均值和极差,以确定过程是否稳定) 414
16.4.3 属性控制图 416
表16.1 移动平均数据 416
表16.2 np控制图数据 420
表16.3 c控制图数据(每平方米材料缺陷数) 421
图16.5 np控制图实例 421
图16.6 c控制图实例 422
表16.4 u控制图数据 423
图16.7 u控制图实例 424
16.4.4 过程能力指数 427
16.5 本章总结 429
16.4.5 过程绩效指数 429
第17章 六西格玛的实施 430
17.1 六西格玛需求评估 432
表17.1 六西格玛需求检查表 432
17.2 作为经营战略的六西格玛 433
17.3 实施六西格玛 434
17.3.1 选择1:实施六西格玛项目或创新活动 434
17.3.2 选择2:创建一个六西格玛基本结构 435
图17.1 西格玛质量水平的含义 436
17.4 六西格玛度量 436
图17.3 六西格玛界限内中心无位移的正态分布,只有十亿分之二的装置不能满足规格要求 437
图17.2 正态分布曲线表明三西格玛和六西格玛参数的符合性 437
图17.4 不合格率仅百万分之3.4时,偏移1.5个σ产生的影响 438
图17.5 缺陷率(ppm)与西格玛——质量水平 438
图17.6 六西格玛尺度和实施战略 440
17.5 维持和沟通变革 441
17.6 本章总结 441
附录1:美国质量协会职业道德守则 444
第六部分 附录 444
附录2:ASQ—CQE知识体系大纲 446
附录3:马尔科姆·鲍德里奇国家质量奖 455
附录4:ANSI/ISO/ASQ Q9000系列标准 457
附录5:控制界限公式 461
附录6:控制图常数 462
附录7:至少99%总体的统计公差因子(“K——值”) 463
附录8:标准正态分布 464
附录9:选定Z值右侧标准正态曲线下的面积 466
附录10:F分布F.90 468
附录11:F分布F.95 471
附录12:F分布F.99 474
附录13:二项分布 477
附录14:x2分布 479
附录15:指数分布 481
附录16:泊松分布 483
附录17:中位数层号 485
附录18:正态分数 486
附录19:t分布值 488
附录20:精选国家和国际质量体系标准 490
附录21:参考读物 493
克劳士比中国学院 509
后记 515
- 《市政工程基础》杨岚编著 2009
- 《管理信息系统习题集》郭晓军 2016
- 《MBA大师.2020年MBAMPAMPAcc管理类联考专用辅导教材 数学考点精讲》(中国)董璞 2019
- 《工程静力学》王科盛主编 2019
- 《中央财政支持提升专业服务产业发展能力项目水利工程专业课程建设成果 设施农业工程技术》赵英编 2018
- 《信息系统安全技术管理策略 信息安全经济学视角》赵柳榕著 2020
- 《Maya 2018完全实战技术手册》来阳编著 2019
- 《化学反应工程》许志美主编 2019
- 《卓有成效的管理者 中英文双语版》(美)彼得·德鲁克许是祥译;那国毅审校 2019
- 《危险化学品经营单位主要负责人和安全生产管理人员安全培训教材》李隆庭,徐一星主编 2012
- 《SQL与关系数据库理论》(美)戴特(C.J.Date) 2019
- 《魔法销售台词》(美)埃尔默·惠勒著 2019
- 《看漫画学钢琴 技巧 3》高宁译;(日)川崎美雪 2019
- 《优势谈判 15周年经典版》(美)罗杰·道森 2018
- 《社会学与人类生活 社会问题解析 第11版》(美)James M. Henslin(詹姆斯·M. 汉斯林) 2019
- 《海明威书信集:1917-1961 下》(美)海明威(Ernest Hemingway)著;潘小松译 2019
- 《古代巴比伦》(英)莱昂纳德·W.金著 2019
- 《迁徙 默温自选诗集 上》(美)W.S.默温著;伽禾译 2020
- 《上帝的孤独者 下 托马斯·沃尔夫短篇小说集》(美)托马斯·沃尔夫著;刘积源译 2017
- 《巴黎永远没个完》(美)海明威著 2017
- 《中国当代乡土小说文库 本乡本土》(中国)刘玉堂 2019
- 《异质性条件下技术创新最优市场结构研究 以中国高技术产业为例》千慧雄 2019
- 《中国铁路人 第三届现实主义网络文学征文大赛一等奖》恒传录著 2019
- 《莼江曲谱 2 中国昆曲博物馆藏稀见昆剧手抄曲谱汇编之一》郭腊梅主编;孙伊婷副主编;孙文明,孙伊婷编委;中国昆曲博物馆编 2018
- 《中国制造业绿色供应链发展研究报告》中国电子信息产业发展研究院 2019
- 《中国陈设艺术史》赵囡囡著 2019
- 《指向核心素养 北京十一学校名师教学设计 英语 七年级 上 配人教版》周志英总主编 2019
- 《《走近科学》精选丛书 中国UFO悬案调查》郭之文 2019
- 《清至民国中国西北戏剧经典唱段汇辑 第8卷》孔令纪 2018
- 《北京生态环境保护》《北京环境保护丛书》编委会编著 2018