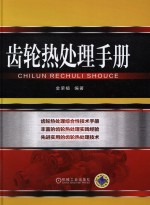
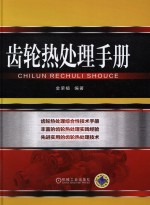
齿轮热处理手册PDF电子书下载
- 电子书积分:17 积分如何计算积分?
- 作 者:金荣植编著
- 出 版 社:北京:机械工业出版社
- 出版年份:2015
- ISBN:9787111507598
- 页数:600 页
第1章 齿轮材料及其热处理 1
1.1 齿轮类别及其性能要求 1
1.1.1 齿轮的类别 1
1.1.2 齿轮(材料)的性能要求 2
1.2 齿轮材料及其热处理的选择 2
1.2.1 齿轮用钢铁材料的选择 3
1.2.2 常用齿轮钢材及其力学性能 5
1.2.3 典型齿轮材料及其热处理 9
1.2.4 铸铁齿轮材料及其热处理 22
1.2.5 齿轮用铸钢及其热处理 27
1.2.6 齿轮用非铁金属合金 30
1.2.7 齿轮用粉末冶金材料及其热处理 35
第2章 齿轮热处理常用设备和工艺材料 37
2.1 齿轮热处理常用设备 37
2.1.1 齿轮热处理常用生产设备 38
2.1.2 齿轮热处理检测设备及仪器 50
2.2 齿轮热处理用工艺材料 53
2.2.1 热处理生产用材料及其分类 53
2.2.2 金属热处理保护涂料及其分类 54
2.2.3 齿轮热处理用淬火冷却介质 54
2.2.4 齿轮淬火冷却用盐浴、碱浴的配方及使用温度 61
第3章 齿轮的整体热处理技术 63
3.1 齿轮的退火与正火技术 63
3.1.1 齿轮的退火技术 64
3.1.2 齿轮的正火技术 69
3.1.3 齿轮毛坯的等温正火技术 74
3.1.4 齿轮的锻造余热正火工艺 77
3.1.5 齿轮的退火、正火热处理实例 77
3.2 齿轮的整体淬火、回火技术 78
3.2.1 齿轮的淬火技术 79
3.2.2 齿轮的回火工艺 86
3.2.3 冷处理 89
3.2.4 齿轮的整体淬火、回火技术应用实例 90
第4章 齿轮的调质热处理技术 91
4.1 常用调质齿轮钢材及其热处理 91
4.1.1 调质钢的分类 91
4.1.2 国内外调质钢材 91
4.1.3 调质齿轮常用钢材与用途 92
4.1.4 常用调质齿轮钢截面与力学性能 92
4.1.5 调质齿轮的硬度选配 94
4.1.6 齿轮钢材调质硬度与硬化层深度的确定 94
4.2 齿轮的调质热处理 98
4.2.1 调质齿轮钢材的预备热处理 98
4.2.2 齿轮的调质热处理工艺 99
4.3 球墨铸铁齿轮的调质处理工艺 104
4.4 大齿轮调质工艺设计 105
4.5 大模数齿轮的开齿调质工艺 108
4.6 焊接齿轮的调质处理工艺 108
4.7 齿轮调质热处理的实例 109
第5章 齿轮的化学热处理技术 112
5.1 齿轮的渗碳热处理技术 112
5.1.1 齿轮渗碳工艺的分类与典型加工流程 112
5.1.2 齿轮的渗碳热处理技术参数 113
5.1.3 齿轮的渗碳工艺参数的选择与控制 116
5.1.4 齿轮的气体渗碳工艺 117
5.1.5 常用结构钢齿轮的渗碳淬火、回火热处理规范 131
5.1.6 齿轮渗碳后常用热处理工艺、特点及适用范围 132
5.1.7 齿轮经渗碳(碳氮共渗)后的热处理 133
5.1.8 齿轮的固体渗碳技术 134
5.1.9 齿轮的液体渗碳技术 138
5.1.10 齿轮的高温渗碳技术 140
5.1.11 大型齿轮的渗碳热处理技术 142
5.1.12 大型焊接齿轮渗碳淬火技术 147
5.1.13 齿轮的防渗技术及防渗涂料的清理方法 149
5.2 齿轮的碳氮共渗技术 153
5.2.1 齿轮的气体碳氮共渗工艺 153
5.2.2 典型齿轮的碳氮共渗技术应用实例 159
5.2.3 碳氮共渗后的热处理方法 161
5.3 齿轮的渗氮及氮碳共渗技术 162
5.3.1 齿轮的渗氮技术 162
5.3.2 齿轮的气体氮碳共渗技术 176
5.3.3 齿轮的离子(气体)氮碳共渗技术 179
5.3.4 齿轮的盐浴氮碳共渗技术 180
5.3.5 齿轮的氮碳共渗技术应用实例 181
第6章 齿轮的表面淬火技术 183
6.1 表面淬火技术概述 183
6.2 齿轮的火焰淬火技术 184
6.3 齿轮的感应淬火技术 189
6.3.1 感应淬火方法的分类 189
6.3.2 感应加热齿轮常用钢铁材料与用途 189
6.3.3 感应加热设备的选择 190
6.3.4 齿轮的感应淬火工艺 190
6.3.5 齿轮的高频感应淬火技术 206
6.3.6 齿轮的中频感应淬火技术 209
6.3.7 齿轮的埋液感应淬火技术 214
6.3.8 齿轮超高频脉冲和大功率脉冲感应淬火工艺 217
6.3.9 国内外大模数齿轮感应淬火设备与工艺 218
6.3.10 齿轮感应淬火的屏蔽技术 218
6.3.11 齿轮的高、中频感应器及喷水器 219
6.3.12 感应淬火机床的基本参数的选取 228
6.3.13 主动齿轮尾部螺纹的感应软化处理技术 229
6.3.14 齿轮感应淬火技术应用实例 230
6.3.15 齿条的高频感应电阻加热表面淬火技术 231
第7章 先进的齿轮热处理技术 233
7.1 齿轮的激光热处理技术 233
7.1.1 激光淬火及其特点和应用 233
7.1.2 齿轮激光淬火技术应用实例 239
7.2 齿轮的稀土化学热处理技术 239
7.2.1 生产现场化学热处理用稀土催渗剂的配制 240
7.2.2 稀土渗碳(碳氮共渗)工艺 241
7.2.3 齿轮的稀土渗碳(碳氮共渗)技术应用实例 242
7.2.4 稀土气体渗氮技术 243
7.2.5 齿轮的BH催渗技术 245
7.3 先进的齿轮感应热处理技术 246
7.3.1 齿轮双频感应淬火技术 246
7.3.2 齿轮的同时双频感应淬火技术(SDF法) 248
7.3.3 单频整体冲击加热淬火技术 249
7.3.4 低淬透性钢齿轮的感应淬火技术 250
7.3.5 齿轮渗碳后感应淬火、感应渗碳及渗氮技术 252
7.3.6 先进的齿轮感应热处理技术应用实例 253
7.3.7 新的模压式感应淬火技术 254
7.3.8 国外先进齿轮感应热处理技术与应用 256
7.4 齿轮的真空热处理技术 257
7.4.1 齿轮的真空淬火技术 257
7.4.2 齿轮的真空渗碳技术 259
7.4.3 齿轮真空渗碳技术应用实例 263
7.4.4 齿轮的离子渗碳技术 264
7.4.5 齿轮的真空热处理实例 266
7.4.6 齿轮的低压真空渗碳与高压气体淬火技术 267
7.4.7 齿轮的离子渗氮技术 269
7.4.8 齿轮离子渗氮技术应用实例 276
7.4.9 活性屏离子渗氮技术 277
7.4.10 齿轮的低真空变压快速化学热处理技术 279
7.5 齿轮的真空及超声波清洗技术 280
7.6 齿轮的先进计算机模拟与智能控制和精密热处理技术 281
7.7 齿轮的其他先进热处理技术 285
7.7.1 一种全新的HybridCarb渗碳方法 285
7.7.2 齿轮的微波热处理技术 286
第8章 齿轮热处理质量控制与检验 289
8.1 齿轮热处理质量控制要求 289
8.2 齿轮的材料热处理质量控制与疲劳强度等级 289
8.2.1 齿轮用钢冶金质量的检验项目及技术要求 289
8.2.2 齿轮材料热处理质量等级的选择 290
8.2.3 齿轮的材料热处理质量控制和疲劳强度 290
8.3 齿轮的一般热处理检验 301
8.3.1 齿轮脱碳、过热的检验 301
8.3.2 齿轮锻件的主要检验项目及内容 302
8.4 齿轮退火与正火的质量检验 302
8.5 齿轮整体淬火与回火的质量检验 303
8.6 齿轮调质处理的质量检验 304
8.7 齿轮渗碳热处理的质量检验 307
8.8 齿轮碳氮共渗的质量检验 312
8.9 齿轮气体渗氮、离子渗氮及氮碳共渗的质量检验 313
8.10 齿轮感应淬火的质量检验 318
8.11 齿轮火焰淬火的质量检验 323
8.12 齿轮热处理畸变与裂纹的检测 324
8.12.1 齿轮热处理畸变的检测 324
8.12.2 齿轮热处理裂纹的检测 324
8.13 齿轮的台架疲劳寿命试验 326
8.13.1 汽车弧齿锥齿轮技术要求及其疲劳寿命试验要求 326
8.13.2 载货汽车驱动桥总成试验机及其技术参数、特点 327
8.13.3 13t载货汽车单级减速器驱动桥总成疲劳试验 328
8.13.4 齿轮弯曲疲劳试验 328
8.13.5 齿轮接触疲劳性能试验的实例 328
8.14 齿轮硬度检验 329
8.14.1 经不同工艺热处理后的零件表面硬度测试方法及选用原则 329
8.14.2 常用硬度测试方法的适用范围 329
8.14.3 不同硬化层深度和硬度测量方法选用原则 330
8.14.4 硬度符号与表示及举例说明 330
第9章 齿轮热处理常见缺陷与对策 332
9.1 齿轮热处理加热、冷却与力学性能缺陷与对策 332
9.1.1 齿轮热处理加热缺陷与对策 332
9.1.2 齿轮热处理冷却缺陷与对策 336
9.1.3 齿轮热处理力学性能缺陷与对策 337
9.1.4 防止齿轮热处理加热、冷却缺陷的实例 339
9.2 齿轮的整体热处理缺陷与对策 339
9.2.1 齿轮的退火、正火缺陷与对策 339
9.2.2 齿轮的整体淬火、回火缺陷与对策 342
9.2.3 中碳钢和中碳合金钢齿轮整体淬火、回火硬度缺陷与对策 344
9.2.4 中碳钢和中碳合金钢齿轮淬火、回火金相组织缺陷与对策 346
9.2.5 中碳钢和中碳合金钢齿轮淬硬层缺陷与对策 348
9.2.6 中碳钢和中碳合金钢齿轮淬火、回火其他缺陷与对策 348
9.2.7 中碳钢和中碳合金钢齿轮淬火畸变与对策 348
9.2.8 中碳钢和中碳合金钢齿轮淬火裂纹与对策 349
9.3 齿轮调质处理缺陷与对策 350
9.3.1 齿轮调质处理常见缺陷与对策 350
9.3.2 防止齿轮调质处理缺陷的实例 352
9.4 齿轮的化学热处理缺陷与对策 353
9.4.1 齿轮的渗碳(碳氮共渗)热处理缺陷与对策 353
9.4.2 齿轮的渗氮(氮碳共渗)热处理缺陷与对策 376
9.4.3 齿轮的离子渗氮缺陷与对策 385
9.4.4 齿轮的气体氮碳共渗缺陷与对策 388
9.5 齿轮的感应热处理缺陷与对策 391
9.5.1 齿轮的感应淬火硬度缺陷与对策 391
9.5.2 感应淬火齿轮表面硬度过高或过低原因与对策 394
9.5.3 齿轮的感应淬火表面硬度不均原因与对策 395
9.5.4 齿轮的感应淬火显微组织缺陷与对策 396
9.5.5 齿轮的感应淬火硬化层缺陷与对策 396
9.5.6 感应淬火齿轮其他热处理缺陷与对策 398
9.5.7 齿轮感应热处理缺陷对策的实例 400
第10章 齿轮的热处理畸变、裂纹与控制技术 402
10.1 影响齿轮热处理畸变的因素 402
10.2 齿轮的整体热处理畸变控制技术 404
10.2.1 轴类齿轮的热处理畸变控制技术 404
10.2.2 环、套类齿轮的热处理畸变控制技术 406
10.3 齿轮的化学热处理畸变与控制技术 407
10.3.1 齿轮的渗碳(碳氮共渗)热处理畸变与控制技术 407
10.3.2 齿轮的渗氮(氮碳共渗)热处理畸变与控制技术 433
10.4 齿轮的感应热处理畸变与控制技术 437
10.4.1 减小与控制齿轮感应淬火畸变的措施 437
10.4.2 齿轮的高频感应淬火畸变与控制技术 442
10.4.3 齿轮的中频感应淬火畸变与控制技术 448
10.5 减小与控制齿轮热处理畸变的方法与措施 450
10.5.1 合理选材和正确设计 451
10.5.2 优化锻造 455
10.5.3 采用预备热处理 456
10.5.4 消除机械加工残余应力 458
10.5.5 冷、热加工配合 459
10.5.6 合理选择装炉及支撑方式 463
10.5.7 减小热应力 464
10.5.8 合理选择淬火冷却介质及淬火方式 468
10.5.9 改进热处理工艺与齿轮材料 471
10.5.10 采用淬火压床淬火 474
10.5.11 采用镶嵌补偿法 478
10.5.12 采用先进的热处理工艺与装备 479
10.6 齿轮热处理畸变的校正技术 482
10.6.1 齿轮热处理畸变的校正方法 482
10.6.2 轴类齿轮热处理畸变的矫直技术 483
10.6.3 环、套类齿轮热处理畸变的校正技术 485
10.6.4 齿轮热处理畸变的校正技术应用实例 489
10.6.5 齿轮齿形畸变的校正技术 492
10.7 齿轮的热处理裂纹与对策 494
10.7.1 热处理裂纹的分类、类型与特征 494
10.7.2 淬火裂纹的特点及其与非淬火裂纹的区别 496
10.7.3 形成齿轮淬火裂纹的影响因素 497
10.7.4 防止齿轮形成裂纹的方法与措施 498
10.7.5 防止齿轮形成裂纹的实例 501
10.7.6 防止齿轮淬火裂纹的其他方法 502
10.7.7 调质齿轮淬火裂纹形成原因与对策 503
10.7.8 防止调质齿轮淬火裂纹的实例 504
10.7.9 齿轮的感应淬火裂纹与对策 505
10.7.10 齿轮的化学热处理裂纹与对策 514
10.7.11 齿轮的喷丸(抛丸)处理裂纹形成原因与对策 519
10.7.12 齿轮的磨削裂纹与对策 520
第11章 齿轮的失效分析与对策 525
11.1 齿轮的服役条件与失效形式 525
11.1.1 齿轮的服役条件 525
11.1.2 齿轮的失效形式 525
11.2 齿轮的接触及弯曲疲劳失效原因、形式及其影响因素 527
11.3 齿面的失效与对策 527
11.3.1 齿面磨损与对策 528
11.3.2 齿面塑性变形与对策 529
11.3.3 齿面胶合与对策 529
11.3.4 齿面点蚀与对策 530
11.3.5 齿轮硬化层剥落与对策 531
11.4 齿轮断裂与对策 532
11.5 齿轮的其他失效与对策 533
11.5.1 齿轮轮齿崩齿与对策 533
11.5.2 齿轮轮齿的末端损坏与对策 533
11.6 齿轮轮齿常见失效模式的特征、原因及对策 534
11.7 防止齿轮早期失效的实例 536
11.8 中重型载货汽车弧齿锥齿轮失效与对策 538
11.8.1 因主、从动弧齿锥齿轮制造问题造成失效的原因与对策 538
11.8.2 因主、从动弧齿锥齿轮装配及使用问题造成失效的原因与对策 540
第12章 提高齿轮性能与寿命的途径 544
12.1 齿轮的强度设计 544
12.2 齿轮延寿与提高性能的途径 545
12.2.1 高精度长寿命渗碳齿轮对钢材的要求 545
12.2.2 采用新型钢材提高重型载货汽车驱动桥弧齿锥齿轮性能与寿命 546
12.2.3 提高载货汽车变速器齿轮性能与寿命的途径 547
12.2.4 提高重型载货汽车驱动桥弧齿锥齿轮性能与疲劳寿命的途径 549
12.2.5 通过增加渗层深度或提高心部强度方法提高齿轮渗层接触疲劳剥落抗力 550
12.2.6 采用稀土渗碳技术提高齿轮性能与使用寿命 551
12.2.7 选用合适的低温化学热处理工艺提高齿轮的疲劳强度 551
12.2.8 采用喷丸强化技术提高渗碳齿轮疲劳强度 552
12.2.9 齿轮的其他延寿热处理技术 554
12.2.10 感应淬火齿轮使用寿命低的原因与对策 556
第13章 典型齿轮热处理及其实例 558
13.1 机床齿轮热处理及其实例 558
13.1.1 机床齿轮的热处理 558
13.1.2 机床齿轮的热处理典型实例 559
13.2 车辆齿轮热处理及其实例 560
13.2.1 车辆齿轮的热处理 560
13.2.2 车辆齿轮的热处理典型实例 561
13.3 能源装备齿轮热处理及其实例 563
13.3.1 风电齿轮热处理及其实例 563
13.3.2 火电及其他发电装备齿轮热处理及其实例 565
13.4 航空齿轮热处理及其实例 566
13.4.1 航空齿轮的热处理 566
13.4.2 航空齿轮的热处理典型实例 567
13.5 轨道交通装备齿轮热处理及其实例 568
13.5.1 轨道交通装备齿轮的热处理 568
13.5.2 轨道交通装备齿轮的热处理典型实例 568
13.6 冶金、矿山、石油化工及建材设备齿轮热处理及其实例 569
13.6.1 冶金、矿山、石油化工及建材设备齿轮的热处理 569
13.6.2 冶金、矿山、石油化工及建材设备齿轮的热处理典型实例 569
13.7 船舶与海洋工程装备齿轮热处理及其实例 573
13.7.1 船舶与海洋工程装备齿轮的热处理 573
13.7.2 船舶与海洋工程装备齿轮的热处理典型实例 573
13.8 液压齿轮泵齿轮热处理及其实例 574
13.8.1 液压齿轮泵齿轮的热处理 574
13.8.2 液压齿轮泵齿轮的热处理典型实例 574
附录 576
附录A 齿轮用钢热处理工艺参数 576
附录B 齿轮渗碳钢末端淬透性(CGMA001-1:2012) 583
附录C 国内外常用结构钢对照表 584
附录D 齿轮热处理相关标准目录 586
参考文献 590
- 《Maya 2018完全实战技术手册》来阳编著 2019
- 《大数据Hadoop 3.X分布式处理实战》吴章勇,杨强 2020
- 《高等教育双机械基础课程系列教材 高等学校教材 机械设计课程设计手册 第5版》吴宗泽,罗圣国,高志,李威 2018
- 《慢性呼吸系统疾病物理治疗工作手册》(荷)瑞克·考斯林克(RikGosselink) 2020
- 《战略情报 情报人员、管理者和用户手册》(澳)唐·麦克道尔(Don McDowell)著 2019
- 《实用内科手册》黄清,阮浩航主编 2016
- 《基层医疗卫生机构安全用药手册》黎月玲,熊慧瑜 2019
- 《同仁眼科手册系列 同仁儿童眼病手册》付晶编 2018
- 《环境噪声监测实用手册》中国环境监测总站编 2018
- 《高度关注物质(SVHC)毒性手册 上》顾爱华主编 2019
- 《市政工程基础》杨岚编著 2009
- 《家畜百宝 猪、牛、羊、鸡的综合利用》山西省商业厅组织技术处编著 1959
- 《《道德经》200句》崇贤书院编著 2018
- 《高级英语阅读与听说教程》刘秀梅编著 2019
- 《计算机网络与通信基础》谢雨飞,田启川编著 2019
- 《看图自学吉他弹唱教程》陈飞编著 2019
- 《法语词汇认知联想记忆法》刘莲编著 2020
- 《培智学校义务教育实验教科书教师教学用书 生活适应 二年级 上》人民教育出版社,课程教材研究所,特殊教育课程教材研究中心编著 2019
- 《国家社科基金项目申报规范 技巧与案例 第3版 2020》文传浩,夏宇编著 2019
- 《流体力学》张扬军,彭杰,诸葛伟林编著 2019
- 《指向核心素养 北京十一学校名师教学设计 英语 七年级 上 配人教版》周志英总主编 2019
- 《北京生态环境保护》《北京环境保护丛书》编委会编著 2018
- 《高等教育双机械基础课程系列教材 高等学校教材 机械设计课程设计手册 第5版》吴宗泽,罗圣国,高志,李威 2018
- 《指向核心素养 北京十一学校名师教学设计 英语 九年级 上 配人教版》周志英总主编 2019
- 《高等院校旅游专业系列教材 旅游企业岗位培训系列教材 新编北京导游英语》杨昆,鄢莉,谭明华 2019
- 《中国十大出版家》王震,贺越明著 1991
- 《近代民营出版机构的英语函授教育 以“商务、中华、开明”函授学校为个案 1915年-1946年版》丁伟 2017
- 《新工业时代 世界级工业家张毓强和他的“新石头记”》秦朔 2019
- 《智能制造高技能人才培养规划丛书 ABB工业机器人虚拟仿真教程》(中国)工控帮教研组 2019
- 《AutoCAD机械设计实例精解 2019中文版》北京兆迪科技有限公司编著 2019