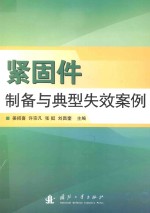
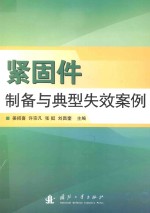
紧固件制备与典型失效案例PDF电子书下载
- 电子书积分:17 积分如何计算积分?
- 作 者:姜招喜,计宗凡,张挺,刘昌奎主编
- 出 版 社:北京:国防工业出版社
- 出版年份:2015
- ISBN:9787118102161
- 页数:560 页
第一篇 紧固件的标准、制造工艺、试验与材料应用 3
第一章 紧固件的标准、加工制造与特种工艺 3
1.1 概述 3
1.2 紧固件的标准体系 5
1.2.1 紧固件的标准 6
1.2.2 紧固件的标准化 6
1.2.3 紧固件标准的分类 6
1.2.4 紧固件标准的技术要求 7
1.2.5 紧固件标准体系的应用 9
1.3 紧固件常用基础技术标准目录 9
1.4 紧固件的加工制造 10
1.4.1 紧固件的分类、结构特点与工作条件 10
1.4.2 紧固件的加工制造 11
1.5 紧固件的特种工艺 17
1.5.1 特种紧固件的特种工艺 18
1.5.2 常用紧固件的特种工艺 19
第二章 紧固件的理化检测 21
2.1 紧固件的机械性能检测 21
2.1.1 特种紧固件的机械性能 22
2.1.2 常用紧固件机械性能 29
2.1.3 紧固件的硬度与性能 31
2.2 紧固件的金相试验检测 31
2.2.1 金相试样的加工制备 31
2.2.2 特种紧固件的金相检测 33
2.2.3 常用紧固件的金相检测 36
2.3 紧固件的化学分析 36
2.3.1 特种紧固件原材料化学分析 36
2.3.2 特种紧固件氢含量分析 38
2.3.3 常用紧固件原材料化学元素分析 39
第三章 紧固件用材简介 42
3.1 特种紧固件采用的材料 42
3.1.1 高温合金 42
3.1.2 不锈钢 45
3.1.3 合金结构钢与碳素结构钢 45
3.1.4 钛合金 46
3.1.5 铝合金 47
3.1.6 铜合金 48
3.2 常用紧固件冷镦专用丝材 49
3.3 特种紧固件主要材料牌号 49
3.4 常用紧固件材料牌号 50
第二篇 紧固件金相组织图谱与热处理工艺 55
第四章 紧固件的金相组织 55
4.1 金相试验中常见的组织 55
4.1.1 钢中常见金相组织的定义 55
4.1.2 钢中常见金相组织的形貌特征 56
4.2 钢铁材料的热处理与组织转变 61
4.2.1 钢在加热时的组织转变 61
4.2.2 钢在冷却时的组织转变 62
4.3 钢铁材料不同热处理状态下的金相组织 65
4.3.1 工业纯铁退火 65
4.3.2 碳钢退火 66
4.3.3 T8钢正火(退火) 68
4.3.4 碳钢淬火 68
4.3.5 65Mn钢不同温度等温淬火 70
4.3.6 碳钢、合金钢淬火回火 71
4.3.7 不锈钢固溶处理 72
4.4 钢铁材料化学热处理后的的金相组织 73
4.4.1 15钢的渗碳后退火 73
4.4.2 40Cr钢软氮化 73
第五章 紧固件螺栓的金相组织与热处理工艺 74
5.1 特种紧固件螺栓的金相组织与热处理工艺 74
5.1.1 结构钢螺栓 74
5.1.2 不锈钢螺栓 76
5.1.3 高温合金螺栓 78
5.1.4 钛合金螺栓 83
5.1.5 铝合金螺栓 84
5.2 常用紧固件螺栓的金相组织与热处理工艺 86
5.2.1 碳素钢螺栓 87
5.2.2 合金结构钢螺栓 88
5.3 特种紧固件螺栓常用原材料的金相组织 91
5.3.1 结构钢螺栓原材料 91
5.3.2 不锈钢螺栓原材料 93
5.3.3 高温合金螺栓原材料 94
5.3.4 钛合金螺栓原材料 98
5.3.5 铝合金螺栓原材料 99
5.3.6 铜合金螺栓原材料 100
5.4 常用紧固件螺栓原材料的金相组织 100
第六章 特种紧固件成品和半成品的金相组织与热处理工艺 102
6.1 结构钢紧固件成品和半成品的金相组织与热处理工艺 102
6.1.1 38Cr钢丝套 102
6.1.2 20A钢螺栓(大)、30CrMnSi钢沉头螺栓半成品 102
6.1.3 40CrNiMo钢异形螺母(12角螺母)成品 104
6.1.4 30CrMnSi钢镀锌螺栓、30CrMnSi钢自锁螺母 105
6.1.5 65Si2MnWA钢压弹簧圈 105
6.1.6 ML18钢螺母成品、ML18钢螺母未热处理半成品、20钢锁片 106
6.1.7 30CrMnSiNi2钢六角螺栓和沉头螺栓 108
6.1.8 ML16CrSiNi钢长托板螺母、镀锌四角托板螺母、两角小托板螺母 109
6.1.9 30CrMnSiA钢高锁螺栓成品及半成品 110
6.1.10 40CrNiMoA钢收口螺母 111
6.2 不锈钢紧固件成品和半成品的金相组织与热处理工艺 112
6.2.1 1Cr11Ni2W2MoV不锈钢螺母 112
6.2.2 1Cr12Ni2WMoVNb不锈钢半成品、成品螺栓 113
6.2.3 1Cr12Ni3MoVN不锈钢螺母 114
6.2.4 1Cr11Ni2W2MoV不锈钢圆柱销 114
6.2.5 1Cr11Ni2W2MoV不锈钢螺母热处理 115
6.3 高温合金紧固件成品和半成品金相组织与热处理工艺 116
6.3.1 A286合金十二角螺栓 116
6.3.2 GH2132合金半成品(固溶热处理)螺栓 117
6.3.3 GH2132合金螺母 118
6.3.4 GH2132合金六角螺母 118
6.3.5 GH4169合金十二角、六角半成品(固溶处理)螺栓 119
6.3.6 GH4169合金十二角螺栓 120
6.3.7 GH2696合金螺母 121
6.3.8 A286合金托板螺母 121
6.4 铝合金紧固件成品及半成品的金相组织与热处理工艺 122
6.4.1 7C04合金紧固件 122
6.4.2 2A01合金铆钉 123
6.4.3 2A01合金空心铆钉 124
6.4.4 7075高强合金螺栓 125
6.4.5 2A10合金铆钉 125
6.4.6 2A10合金高锁螺母 126
6.4.7 2A10合金高锁螺母、2A09合金套管 127
6.5 铜合金紧固件金相组织 127
6.5.1 H62螺栓 127
6.5.2 HPb59-1合金螺母 128
6.6 特种紧固件及材料常用的相关热处理技术文件 129
第三篇 紧固件的缺陷与断口形貌 133
第七章 紧固件的宏观缺陷与断口形貌 133
7.1 紧固件原材料问题造成裂纹 133
7.2 紧固件淬火裂纹 139
7.3 紧固件因加工工艺或安装不当造成的开裂及缺陷 143
7.4 紧固件因装配应力过大造成的裂纹 147
7.5 紧固件脆性断裂 151
7.6 紧固件疲劳断裂 157
7.7 紧固件应力腐蚀开裂 160
第八章 紧固件常见缺陷的金相形貌 162
8.1 紧固件原材料显微缺陷 162
8.2 紧固件常见夹杂物缺陷 173
8.3 紧固件的热处理缺陷 175
8.4 成形工艺不当造成的缺陷 189
8.5 紧固件的金相低倍缺陷 196
第九章 紧固件断口扫描电镜形貌 200
9.1 紧固件疲劳断裂断口 200
9.2 紧固件螺栓(钉)氢脆断口 210
9.3 紧固件热处理缺陷造成断裂的断口 221
9.4 装配应力过大断裂的断口 225
9.5 应力腐蚀断裂断口 228
9.6 机加工艺缺陷造成断裂的断口 229
9.7 高温合金螺栓早期断裂断口 230
第四篇 紧固件的失效分析与预防 235
第十章 紧固件的失效分析与预防 235
10.1 紧固件的受力分析 235
10.1.1 螺栓的拉伸与扭转应力分析 235
10.1.2 螺栓疲劳应力分析 236
10.1.3 螺栓和螺母紧固时的受力分析 237
10.2 紧固件失效的基本类型及特征 237
10.2.1 紧固件塑性变形断裂及特征 237
10.2.2 紧固件脆性断裂及特征 237
10.2.3 紧固件疲劳断裂及特征 238
10.2.4 紧固件氢脆断裂及特征 238
10.3 紧固件失效的原因分析 239
10.3.1 材料性能低引起的紧固件失效 239
10.3.2 装配力过大导致失效 240
10.3.3 选材不当导致失效 240
10.3.4 机械加工工艺不当导致失效 241
10.3.5 热处理工艺不当导致失效 241
10.3.6 表面处理工艺不当导致失效 242
10.4 紧固件常见的制造工艺缺陷 242
10.4.1 紧固件因原材料缺陷原因造成的产品缺陷 242
10.4.2 紧固件成形工艺与加工工艺不当造成缺陷 244
10.4.3 热处理工艺不当造成的产品缺陷 245
10.4.4 表面处理工艺不当造成的产品缺陷 246
10.5 紧固件的失效分析方法 246
10.6 预防紧固件失效的方法与技术措施 248
10.6.1 预防紧固件失效的方法 248
10.6.2 预防紧固件失效的技术措施 249
第五篇 紧固件常见典型失效案例分析 255
第十一章 紧固件疲劳断裂失效案例 255
11.1 塔吊固定螺栓断裂 255
11.2 夹子弹簧疲劳断裂 259
11.3 40Cr钢固定螺栓断裂 262
11.4 10.9 级40Cr钢轮毂螺栓断裂 266
11.5 40Cr钢六角头螺栓断裂 270
11.6 塔吊基础40Cr钢高强度螺栓断裂 274
11.7 35CrMo钢车轮毂螺栓断裂 278
11.8 40Cr钢差速器紧固螺栓断裂 284
11.9 42CrMo钢双头螺栓断裂 288
11.10 40Cr钢齿轮箱端盖螺栓断裂 292
11.11 55CrSi钢传动阀弹簧断裂 294
11.12 电梯扶手45钢驱动轴断裂 300
11.13 35CrMo钢动车底座六方螺栓断裂 306
11.14 45钢发电车螺栓断裂 310
11.15 某矿机35CrMo钢双头螺栓断裂 316
11.16 40Cr钢连杆与连杆螺栓断裂 320
11.17 SCM435钢皮带张紧轮螺栓断裂 327
11.18 SAE 9254钢弹簧断裂 331
11.19 40Cr钢转向臂下端轴断裂 339
第十二章 紧固件氢脆断裂失效案例 345
12.1 40Cr钢高强度内六角圆柱螺栓断裂 345
12.2 65Mn钢弹性垫圈开裂 348
12.3 12.9级ML40Cr钢内六角螺栓断裂 352
12.4 发动机底座40Cr钢六角头螺栓断裂 355
12.5 SAE 1022钢自挤螺钉断裂 359
12.6 10.9级20MnTiB钢螺栓断裂 363
12.7 汽车推力杆20MnTiB钢螺栓断裂 366
12.8 汽车支架20MnTiB钢螺栓断裂 370
12.9 10B21钢压铆螺钉断裂 373
12.10 三角牙六角头10B21钢螺栓断裂 376
第十三章 热处理缺陷造成的紧固件断裂失效案例 380
13.1 SWRCH35K钢六角头螺栓断裂 380
13.2 40Cr钢六角头螺栓断裂 383
13.3 SWRCH35K六角电镀螺栓断裂 387
13.4 45钢六角螺母开裂失效 391
13.5 20MnTiB钢内六角圆柱头螺钉断裂 395
13.6 SWRCH35K钢螺栓头部弧形裂纹 399
13.7 65Mn钢鞍形弹簧垫圈断裂 403
13.8 60Si2Mn钢波形垫圈断裂 406
13.9 35钢内六角圆柱头螺钉安装断裂 408
13.10 40Cr钢六角头螺栓安装断裂 412
13.11 SWRCH35K钢六角头螺栓断裂 415
13.12 风电10级45钢螺母开裂 418
13.13 齿轮箱25钢螺栓断裂 422
13.14 35CrMo钢螺栓断裂 425
第十四章 制造工艺不当造成紧固件失效的案例 430
14.1 50CrV钢盘形弹簧安装断裂 430
14.2 SWRCH45K钢四方螺母表面开裂 434
14.3 ML35钢螺栓头部裂纹缺陷 437
14.4 42CrMo钢热镦六方大螺栓头下圆角处裂纹缺陷 439
14.5 35钢卡箍裂纹缺陷 444
14.6 ML08AlCK钢大扁头方颈螺栓断裂 446
14.7 35钢六角头带垫螺栓螺纹处的疑似裂纹 448
14.8 40Cr钢六角头螺栓头杆连接处断裂 450
14.9 挖掘机履带SCM435钢螺栓断裂 454
14.10 AISI1022A钢盘头螺钉断裂 458
14.11 45钢启动爪螺栓断裂 460
14.12 40Cr钢热锻螺栓滚丝开裂 463
第十五章 紧固件因装配不当造成的断裂失效案例 467
15.1 SCM435钢圆柱头螺钉断裂 467
15.2 40Cr钢六角头螺栓断裂 469
15.3 35CrMo钢六角头螺栓断裂 471
15.4 40Cr钢轴承调隙螺栓断裂 473
15.5 Q195钢焊钉使用过程中断裂 478
第十六章 紧固件原材料缺陷造成的失效案例 483
16.1 35K钢法兰面螺母冷镦开裂 483
16.2 ASTM194钢六角螺母安装开裂 485
16.3 35CrMo钢内六角圆柱头螺栓杆部裂纹 487
16.4 40Cr钢螺杆表面纵向裂纹 490
16.5 40Cr钢大扁头方颈螺栓头部裂纹 493
16.6 35K钢圆头方颈螺栓表面严重脱碳 497
16.7 SWRCH35K钢六角法兰面螺栓冷镦开裂 500
16.8 42CrMo钢螺栓使用中断裂 503
16.9 1Cr11Ni2W2MoV不锈钢螺母表面裂纹 507
16.10 35K钢螺钉安装断裂 513
附录1 紧固件常用基础技术与质量控制标准目录 516
附录2 紧固件材料热处理工艺规范与材料技术条件 521
附录3 紧固件及材料的金相组织常用浸蚀试剂与方法 544
附录4 紧固件及材料强度与硬度常用换算表 548
附录5 常用金属材料的中外牌号对照表 552
附录6 紧固件相关名称的中英文对照表 558
参考文献 560
- 《催化剂制备过程技术》韩勇责任编辑;(中国)张继光 2019
- 《大气中典型二恶英类物质的氧化降解机理研究》张晨曦 2017
- 《生活垃圾焚烧飞灰中典型污染物控制技术》朱芬芬等编著 2019
- 《典型地区居民汞、镉、砷、铅、铬环境总暴露研究报告》中国环境科学研究院著 2018
- 《德国联邦法院典型判例研究丛书 德国联邦最高法院典型判例研究 专利法篇》孙东育,王珊责任编辑;(中国)赵晓鹏 2019
- 《GIS设备典型故障案例及分析》国网宁夏电力有限公司电力科学研究院编 2019
- 《磁性核壳结构吸波材料构建与制备》刘渊,陈桂明,王炜著 2019
- 《姜黄素 功能制备及应用研究》马自超,陈文田,李海霞著 2020
- 《钢铁行业温室气体排放典型企业减排机会指南》杨宏伟,郭敏晓著 2018
- 《生物质活性炭催化剂的制备及脱硫应用》宁平,李凯,宋辛著 2019
- 《指向核心素养 北京十一学校名师教学设计 英语 七年级 上 配人教版》周志英总主编 2019
- 《北京生态环境保护》《北京环境保护丛书》编委会编著 2018
- 《指向核心素养 北京十一学校名师教学设计 英语 九年级 上 配人教版》周志英总主编 2019
- 《抗战三部曲 国防诗歌集》蒲风著 1937
- 《高等院校旅游专业系列教材 旅游企业岗位培训系列教材 新编北京导游英语》杨昆,鄢莉,谭明华 2019
- 《中国十大出版家》王震,贺越明著 1991
- 《近代民营出版机构的英语函授教育 以“商务、中华、开明”函授学校为个案 1915年-1946年版》丁伟 2017
- 《新工业时代 世界级工业家张毓强和他的“新石头记”》秦朔 2019
- 《智能制造高技能人才培养规划丛书 ABB工业机器人虚拟仿真教程》(中国)工控帮教研组 2019
- 《陶瓷工业节能减排技术丛书 陶瓷工业节能减排与污染综合治理》罗民华著 2017